In this article
Abrasive wheels are commonly used across a range of industries, including in construction, metalworking and manufacturing. There are different types of abrasive wheels that are designed for different uses. Some are made for heavy duty tasks such as cutting and grinding hard materials, while others are suited to precision tasks such as finishing, shaping, sharpening and refining.
Abrasive wheels are cutting tools that consist of abrasive particles that are bonded together using organic or inorganic materials.
- Organic bonding materials include rubber, shellac, resin
- Inorganic bonding materials include sodium silicate, magnesium oxychloride, metal
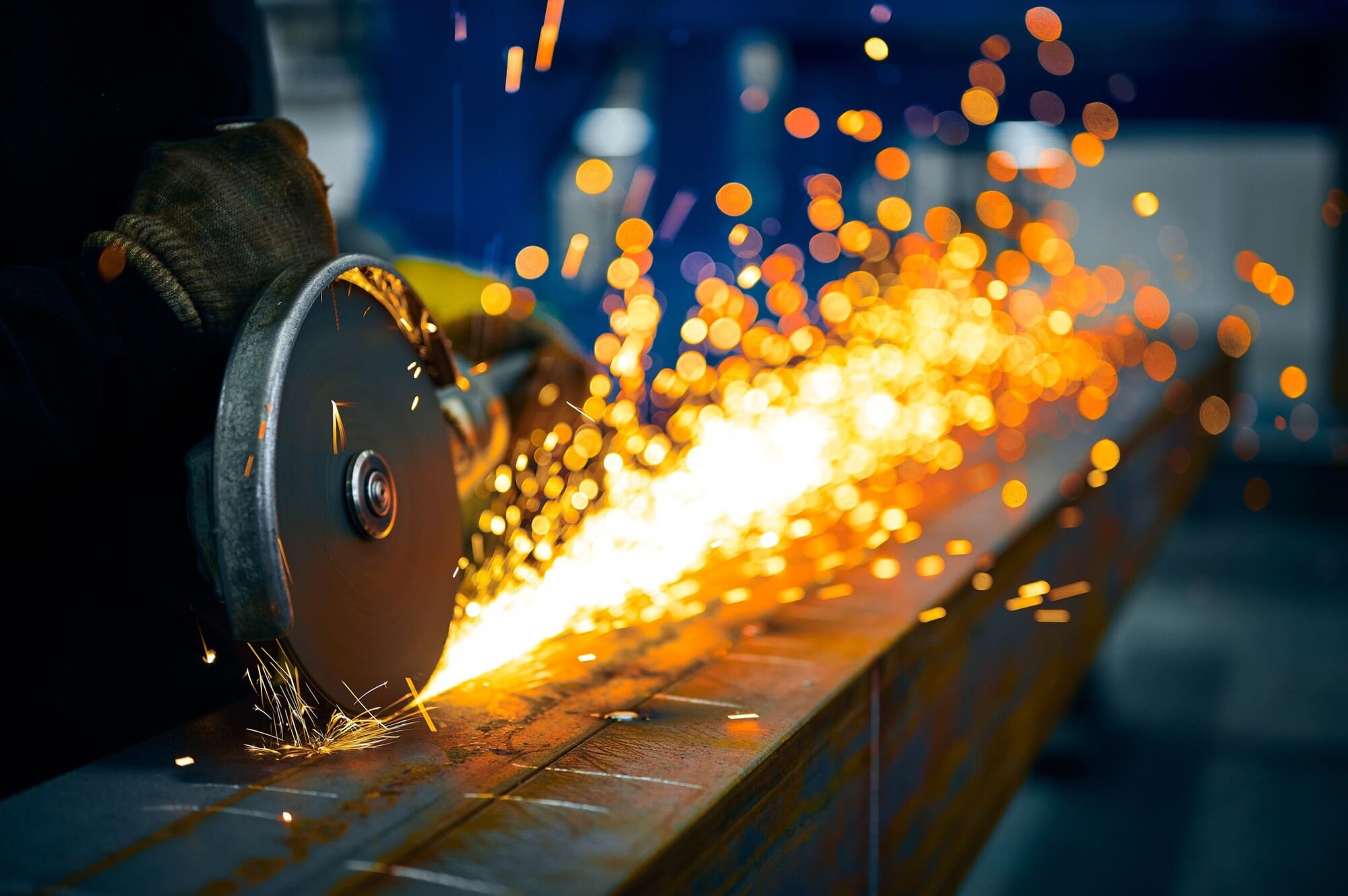
There are several common forms of abrasive wheels:
- Straight wheels
- Cylinder wheels
- Tapered wheels
- Straight cup wheels
- Dish wheels
- Saucer wheels
They are made from abrasive grains including aluminium oxide, silicon carbide, cubic boron nitride and diamond. The type of material used for the abrasive grain correlates to the hardness of the material it grinds.
Grinding wheels are attached to machines such as grinders or saws. They rotate at high speeds to grind or cut through hard materials. An abrasive flap wheel is an abrasive wheel that is mounted onto a power tool, for example a drill. A cutting wheel is thinner than a grinding wheel and used in metalworking or fabrication. Rather than being designed to remove high amounts of hard material, they are designed to make a precise cut (often at a 90-degree angle).
Applications
Abrasive wheels are used in both pedestal (fixed) and handheld (portable) machines. You will be familiar with abrasive wheels if your work involves machines such as:
- Angle grinders
- Belt grinders
- Bench grinders
- Jig grinders
- Cylindrical grinders
- Surface grinders
- Tool and cutter grinders
Angle grinders
Angle grinders (sometimes referred to as side grinders or disc grinders) are handheld tools that can be used to cut or polish materials. Favoured by both professionals on construction sites and DIY enthusiasts, their portable nature makes them suitable for use on metal, stone, tile or concrete.
Belt grinders
Belt grinders are usually used in metalworking or woodworking to finish or polish materials. They feature a belt coated in an abrasive material that is run over the surface of another material that is capable of removing large amounts of material in a short space of time.
Bench grinders
Bench grinders are mounted to a tabletop and feature two different abrasive wheels on each side. They are useful in multiple scenarios, including grinding, shaping or finishing metal parts. Bench grinders may also be used to sharpen or grind tools such as drill bits and lawnmower blades.
Cylindrical grinders
Cylindrical grinders are used to shape the exterior of objects with a central axis of rotation, such as precision rods, tubes and bearing races.
Jig grinders
Jig grinders are precise machines that are selected for jobs that require a high level of accuracy, such as grinding holes or complex shapes in metal parts. They provide high accuracy and a fine finish.
Surface grinders
Surface grinders are generally used to finish surfaces or remove large amounts of material from them. They can grind large areas (such as tabletops) making them completely flat.
Tool and cutter grinders
Tool and cutter grinders are used to sharpen tool bits, milling cutters, drills and a range of other specialised tools to ensure they remain sharp and in top condition for professional use.
You may also use abrasive wheels if your work involves:
- Table saws
- Chop saws
- Petrol cut-off saws
Properties and Characteristics
Abrasive wheels are used for a range of purposes including cutting, grinding, finishing surfaces, making shapes or sharpening tools. The type of wheel you select will depend on the job you need it to do and the machinery you are trained to operate. If you are unsure of the specifics of using abrasive wheels, consider signing up to our Abrasive Wheel Awareness training course here.
All wheels must feature specific markings that show important information to the user. This includes:
- Trademark and test records
- Restrictions of use
- Expiry date (all organic bonded wheels for handheld machines have an expiry date 3 years from the date they were manufactured)
- Speed strip
- Dimensions in mm
- Specification mark
- Code number
- Maximum permissible speed and ISO Type No (Shape)
- Mounting instruction
- All wheels are required to have the speed marked clearly in RPM
Other information should include
- Sizes – Diameter, Bore and Thickness
- Supplier Name – Accountability
- Usage – Stone or Metal (Steel)
- British Standard Marking
They must conform to the British Standard (BS EN 12413 and BS ISO 525) system for marking.
When selecting a wheel, you must consider the necessary characteristics you require. Full details are given in Clause 5.5 of BS ISO 525: 1999:
- Abrasive grain – this means the abrasive materials used to construct the wheel
- Size of the grain/grit – larger sizes of grain cut faster and produce a rougher finish. For precision tasks a smaller grain is needed. Sizes are expressed in numbers from 4 (very coarse) to 1200 (very fine)
- Wheel grade – wheels are graded as hard or soft (using the letters A to Z)
- Structure – how porous the wheel is
- Bond type – the bonding material used to stick the abrasive particles together
Safety Considerations
Accidents involving abrasive wheels are all too common. Hazards associated with the use of abrasive wheels include cuts and eye damage from flying shards or sparks, as well as health problems from dust inhalation, noise and vibrations.
According to the Health and Safety Executive (HSE), there are over 5,000 accidents each year related to angle grinders alone. An angle grinder is a type of handheld abrasive wheel, ranked by ROSPA as the third most dangerous tool due to its prevalence in accidents.
All employers have a duty to keep workers safe. If you are employing people who work with abrasive wheels, or any dangerous equipment, you must be aware of all relevant legislation that might affect you. We will cover the legislation that relates to the use of abrasive wheels later in the article.
To keep everyone safe and reduce hazards, employers have to undertake a risk assessment for using abrasive wheels. They may also need to conduct an Environmental Risk Assessment and take steps to mitigate damage to the environment (including the landscape, local animals and the general population) such as:
- Proactive measures to mitigate/minimise damage associated with noise, vibrations, debris or dust
- Having fire safety procedures in place
- Setting out clear procedures for safe disposal of spent wheels or used cutting fluids
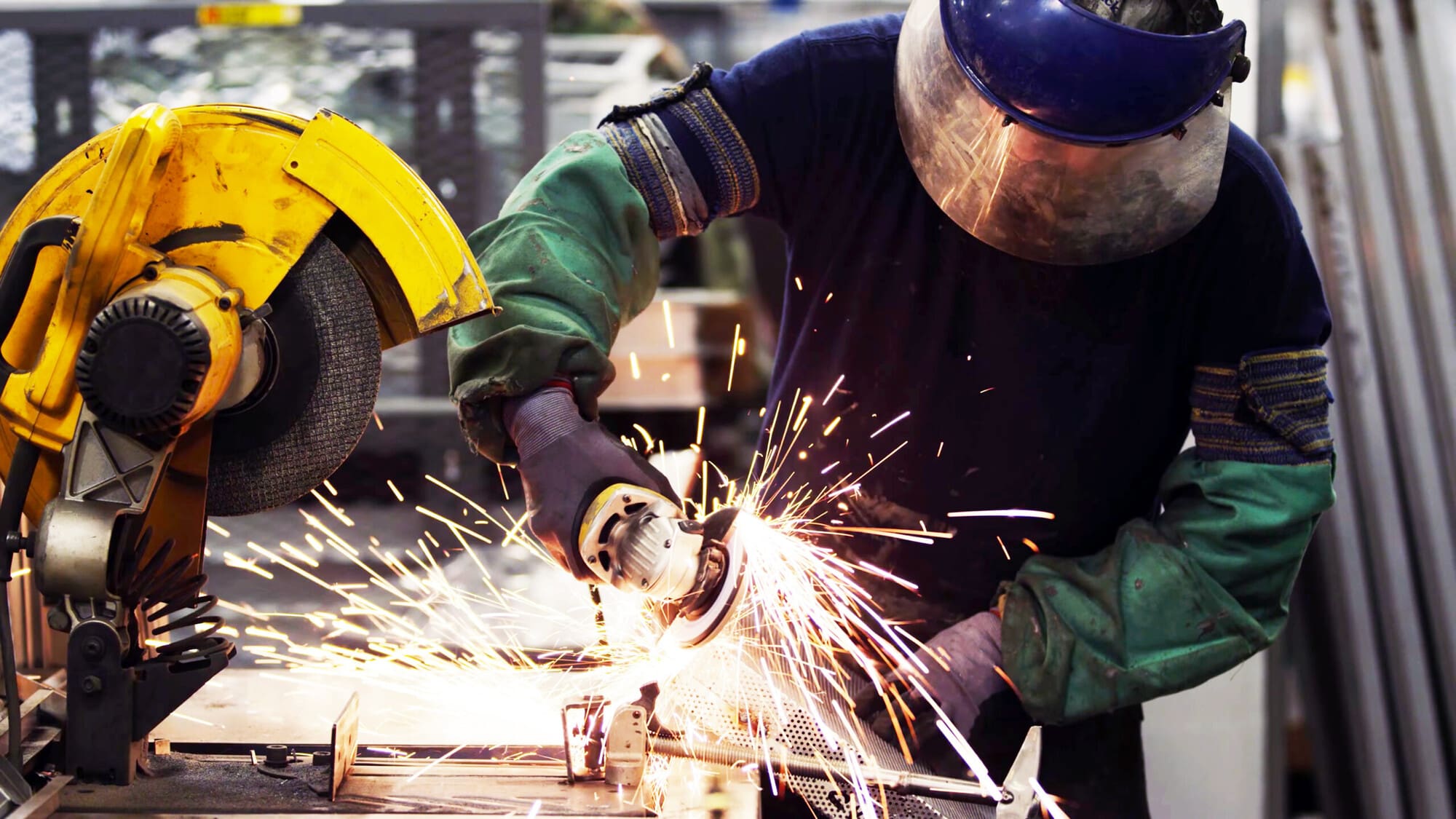
Some steps you can take to reduce the risks to workers using abrasive wheels include:
- Make sure everyone working with abrasive wheels has completed comprehensive training
- Only allow competent people to use abrasive wheels
- Work in a clean and tidy environment, free from flammable materials, to reduce the risk of fire caused by flying sparks or debris
- Provide personal protective equipment (PPE) (including eye protection, dust masks, gloves)
- Conduct regular fire training and provide appropriate fire extinguishers
- Use, handle and store abrasive wheels properly to reduce chances of damage or breakage
- Have at least one first-aider on site and provide instruction to everyone on what to do if an accident or incident occurs
Sparks and dust made up of certain particles (in particular magnesium) are capable of causing fires. Steps should be taken to ensure fire safety and minimise the chance of a fire occurring during (and after) abrasive wheel use, including:
- Good housekeeping – ensuring a clean, tidy and organised workspace free of clutter, dust and ignition sources
- Using extraction systems
- Keeping the work area free from ignition sources (open flames etc)
- Using fireproof PPE
According to the HSE guidelines, many people working with abrasive wheels underestimate the dangers of incorrect mounting. When a wheel isn’t mounted correctly the risk of it bursting during operation is significantly increased.
Many abrasive wheel accidents would be prevented:
- If people were fully aware of the hazards associated with improper mounting
- Understood the correct method of assembly
It is essential that training reiterates the importance of correct mounting and that anyone working with abrasive wheels has the knowledge, resources and time to set up their workstation correctly. If in doubt, always ask.
If an accident does occur, it needs to be fully investigated. Near misses should also be recorded as they can provide warnings about risks or hazards before an incident occurs.
Wheel Selection
When working with abrasive wheels, it is vital that you select the correct wheel for the task in hand. Using the wrong wheel or misusing equipment are some of the leading causes of abrasive wheel accidents in the UK.
As a general guide, soft wheels are preferred on hard materials and hard wheels are preferred for working with softer materials.
- Vitrified wheels made with inorganic bonds are good for precision grinding tasks because they hold their shape, but they require dressing. They have a strong structure but are brittle.
- Cured wheels made with organic bonds tend to be tough and shock resistant. They are self-dressing and suitable for non-precision tasks, for example fettling and cutting off.
Straight Wheels (Type 1)
- Straight wheels are flat and circular with a hole in the centre for mounting
- Made from abrasive materials, aluminium oxide, silica carbide
- Often found on bench grinders
- The grinding edge is straight and parallel to the axis of the wheel
- Used in grinding operations that require a flat smooth finish
Cylinder Wheels (Type 2)
- Large hollow wheels with a cylindrical shape
- Can be used in high volume grinding tasks to remove material or provide finishing
- Provide flat surfaces
- Often used in horizontal or spindle grinders
Tapered Wheels (Type 4)
- Similar to straight wheels except they are not flat
- The edge tapers meaning you can grind with precision at different angles
- Can be used for grinding contoured surfaces due to their shape
Straight Cup Wheels (Type 6)
- Named for the fact their shape mimics that of a cup (flat base with raised edges/vertical sides)
- The grinding surface is the base of the cup
- Suitable for use in smaller workpieces, such as grinding smooth, flat surfaces
- Can be used to sharpen tools and give them a flat edge
Dish Wheels (Type 12)
- Have a flat centre and are shaped like a shallow dish
- Usually used in jig grinding and cutter grinding operations
- Used in tasks where the unique, concave shape of the dish wheel is helpful
Saucer Wheels (Type 13)
- Similar to the dish wheel but flatter
- Ideal for grinding in corners or tight spaces
You can view images of the above wheels on the HSE website.
When selecting an abrasive wheel, you must consider the characteristics required and only use one that is suitable for the task in hand. Also ensure correct handling, mounting and safe use of the abrasive wheel during operation.
Maintenance and Inspection
Abrasive wheels should be inspected for damage or excessive wear before each usage. You should also know how to read the wheel markings as this will help you select the correct wheel for the job you need to do.
All abrasive wheels can be fragile and will not stand up to rough handling. To avoid chipping, breakage or cracking:
- Handle abrasive wheels with care (a simple drop or bump can cause damage)
- Do not stack lots of wheels on top of one another or place heavy tools or castings on them
- Never roll the wheels to transport them (if this is unavoidable it must only be done on a soft, resilient floor surface)
- Use trucks or suitable conveyors to move large, heavy wheels that cannot be transported by hand
Additionally, abrasive wheels should be stored correctly, ideally in a segmented storage unit.
Abrasive wheels are used in conjunction with high powered machinery. It is essential that routine inspections are carried out on a regular basis to:
- Check for electrical faults or malfunctions
- Ensure machinery is working properly
- Account for all of the component parts
- Check for any hazards (such as damage or deterioration of cable anchoring devices, plug pins, casings or brush gears)
- Make sure work areas are neat and organised
- Make sure all tools have original instructions from the manufacturer
Any broken or unsafe equipment must be removed and not used until it has been replaced or repaired professionally.
- For 110-volt machines, the HSE recommends weekly safety checks, visual inspections and a combined inspection and test to be carried out every three months.
- For 240-volt machines, users should carry out daily safety checks, weekly formal visual inspections and combined tests before first time use, then every month thereafter.
Safety checks must be carried out by a person who is competent to do so.
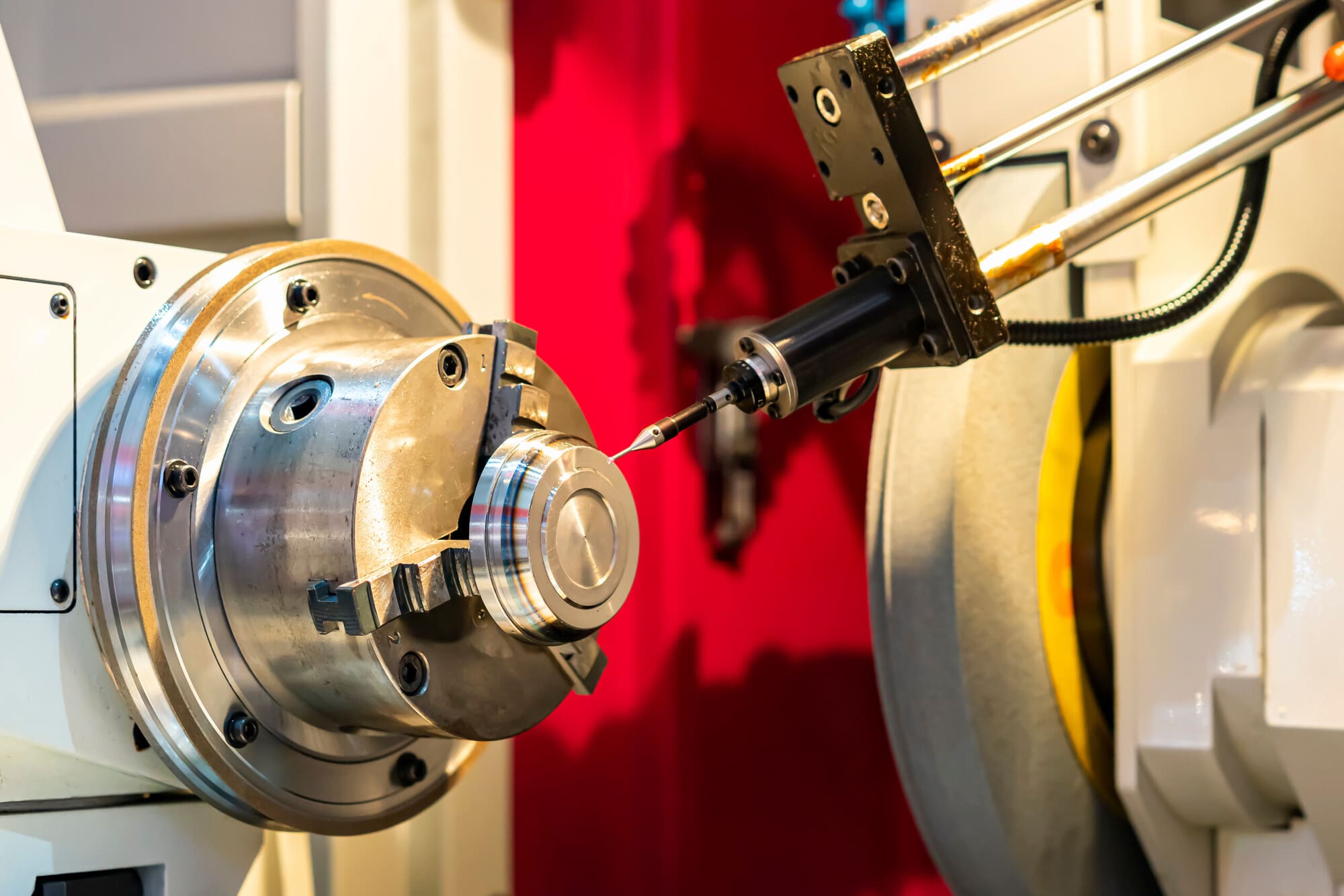
Legal and Regulatory Framework
Legislation relating to abrasive wheels includes the:
Health and Safety at Work Act 1974
This is the primary piece of legislation that relates to all occupational health and safety.
Key legislation that specifically covers abrasive wheel usage includes:
The Provision and Use of Work Equipment Regulations 1998 (PUWER)
The PUWER dictate that workplace equipment should not pose an undue risk to workers. The regulations set out guidance and rules to follow in order to protect the health and safety of people at work.
Additionally, employers have a duty to provide adequate protective equipment to workers under:
The Personal Protective Equipment at Work Regulations 1992
Users of abrasive wheels may also be exposed to additional hazards from vibrations, noise and breathing in hazardous particles, which are covered under the following legislation:
- The Control of Vibration at Work Regulations 2005
- The Control of Noise at Work Regulations 2005
- The Control of Substances Hazardous to Health (COSHH)
There can be significant consequences for failing to comply with legislation or failing to protect workers who are handling potentially dangerous tools and machinery such as abrasive wheels. It is vital that employers are familiar with the law as it relates to them, are providing adequate training and PPE and are taking steps to reduce harm from occurring.