In this article
Abrasive wheels are commonly used in construction, metalwork and manufacturing for cutting and grinding hard materials. They are used in both pedestal (fixed) and handheld (portable) machines. You will be familiar with abrasive wheels if you work with machines such as angle grinders, bench grinders, table saws, chop saws or petrol cut-off saws.
Abrasive wheels consist of abrasive particles that are bonded together using organic or inorganic materials. Some commonly used abrasives include ceramic alumina, zirconia alumina, aluminium oxide, white aluminium oxide and silicon carbide.
The grinding process creates significant amounts of friction between surfaces which results in a high temperature, sparks and debris which can pose a risk of fire. Additionally, the manufacture, use and disposal of abrasive wheels can have a negative impact on the environment.
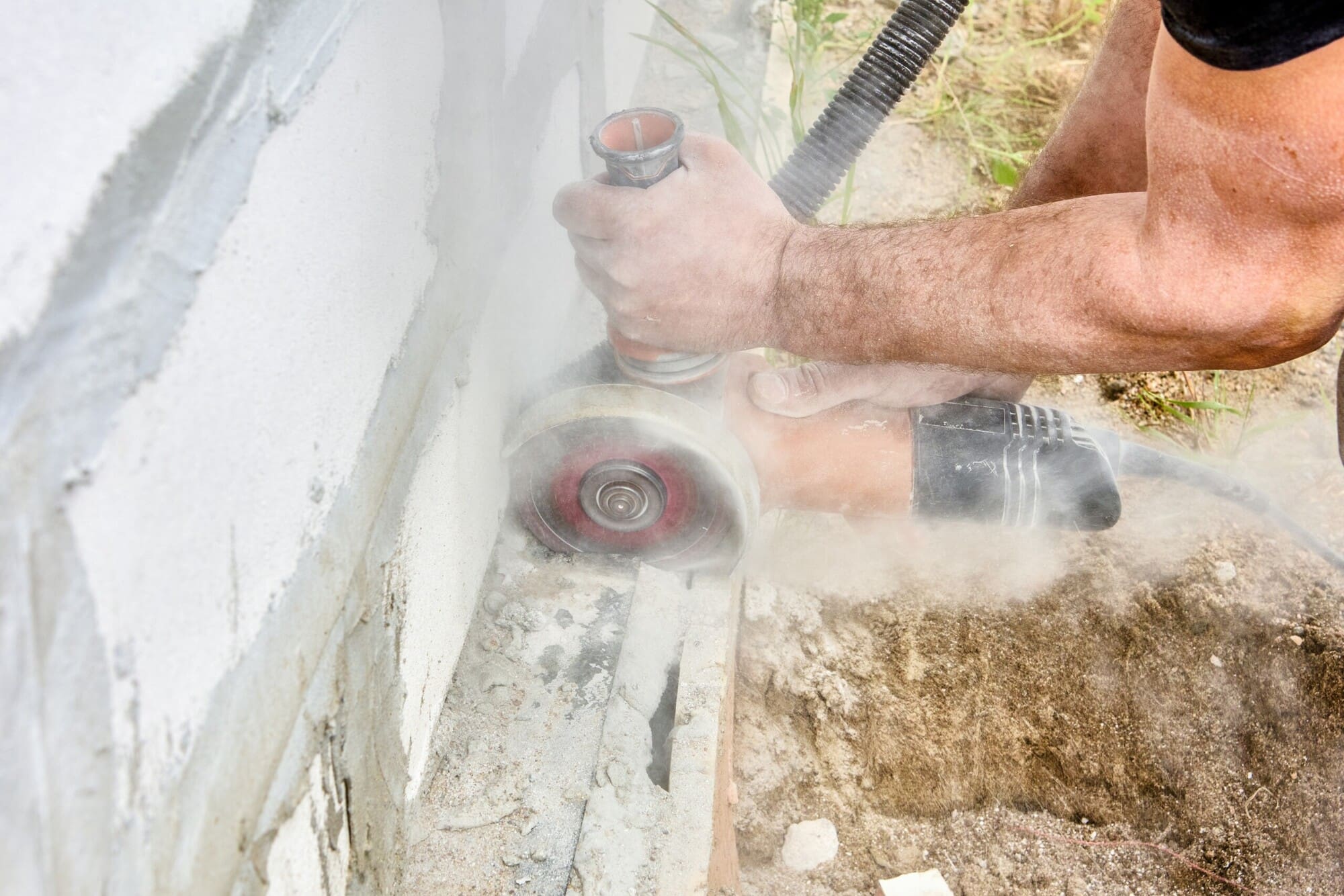
Environmental Concerns
Using abrasive wheels can result in various risks to the user and the environment such as:
- Noise pollution
- Disruption from vibrations
- Flying particles
- Disposal of spent or broken wheels
- Energy consumption
- Fires from sparks or electrical faults
- Use of potentially hazardous cutting fluids
Managing risk and reducing harm is key in the safe usage of abrasive wheels. These concerns should go beyond looking after workers/users and their immediate environment and should extend to concerns for the natural world.
Additional environmental concerns about abrasive wheels include the initial manufacturing process which may involve the depleting of important resources in order to gather the raw materials required to build the wheels. Some abrasive wheels are made using organic bonding agents such as resinoid, rubber and shellac.
Both manufacturing and utilising abrasive wheels requires significant power. This can result in excessive energy consumption and usage.
Stacking, rolling and mishandling abrasive wheels can lead to them cracking or weakening, meaning they are more likely to break during the grinding process. By handling and storing abrasive wheels safely and appropriately, you will prolong their life and reduce the need to:
- Buy new wheels – which has an environmental impact including the collection of raw materials, energy used in manufacturing, carbon footprint of transport costs etc
- Dispose of old wheels – abrasive wheels are classified as non-biodegradable waste, meaning they often end up languishing in landfill
- Reduce the chances of an accident or incident and the associated costs of treatment, clean up etc
Sustainable Practices
Disposing of waste materials safely and ethically is fundamental in reducing the environmental impact of using abrasive wheels.
Many companies resist adopting more sustainable practices because they worry about:
- Cost implications
- Compromising on efficiency
- Reducing output
- Disrupting their process by introducing a change
However, environmental awareness is increasingly becoming part of the cultural zeitgeist and sometimes it is necessary to embrace change and/or lead by example. You can also promote your commitment to the environment and sustainability in your marketing materials. This can improve your reputation, set you apart from competitors and attract new customers.
Five tips to keep up with best business practice in relation to sustainability:
- Understand relevant legislation to ensure compliance
- Review your methods regularly (including risk assessments and beyond) and make appropriate changes
- Keep up with advancements in technology or breakthroughs in research
- Consider environmentally friendly changes or alternatives
- Embrace change – the global abrasive wheel market is set to change – try not to get stuck in a fixed mindset that resists progress
When thinking about sustainability and reducing environmental impact, it is important to consider the full lifecycle of your manufacturing equipment, rather than just its day-to-day usage. This includes disposal options once your equipment is no longer fit for purpose.
Many companies send the waste from their grinding wheels and blast abrasive to landfill. This may be due to laziness, lack of understanding or lack of available alternatives. Used tools and equipment must always be disposed of safely; however, in some circumstances, they can also be repurposed or recycled. Whilst abrasive wheels are not technically hazardous, simply dumping them is bad for the environment and removes the opportunity for recycling the wheels and reusing the grains. There are a few companies out there that are able to recycle used abrasive wheels, so you should check if there is one in your area before opting for landfill.
Bonded vitrified wheels, for example, can be used for:
- Sandblasting
- Mortar in cement
The wheels can sometimes be crushed down and the grains used for new wheels, lapping/polishing compounds or pressure blasting.
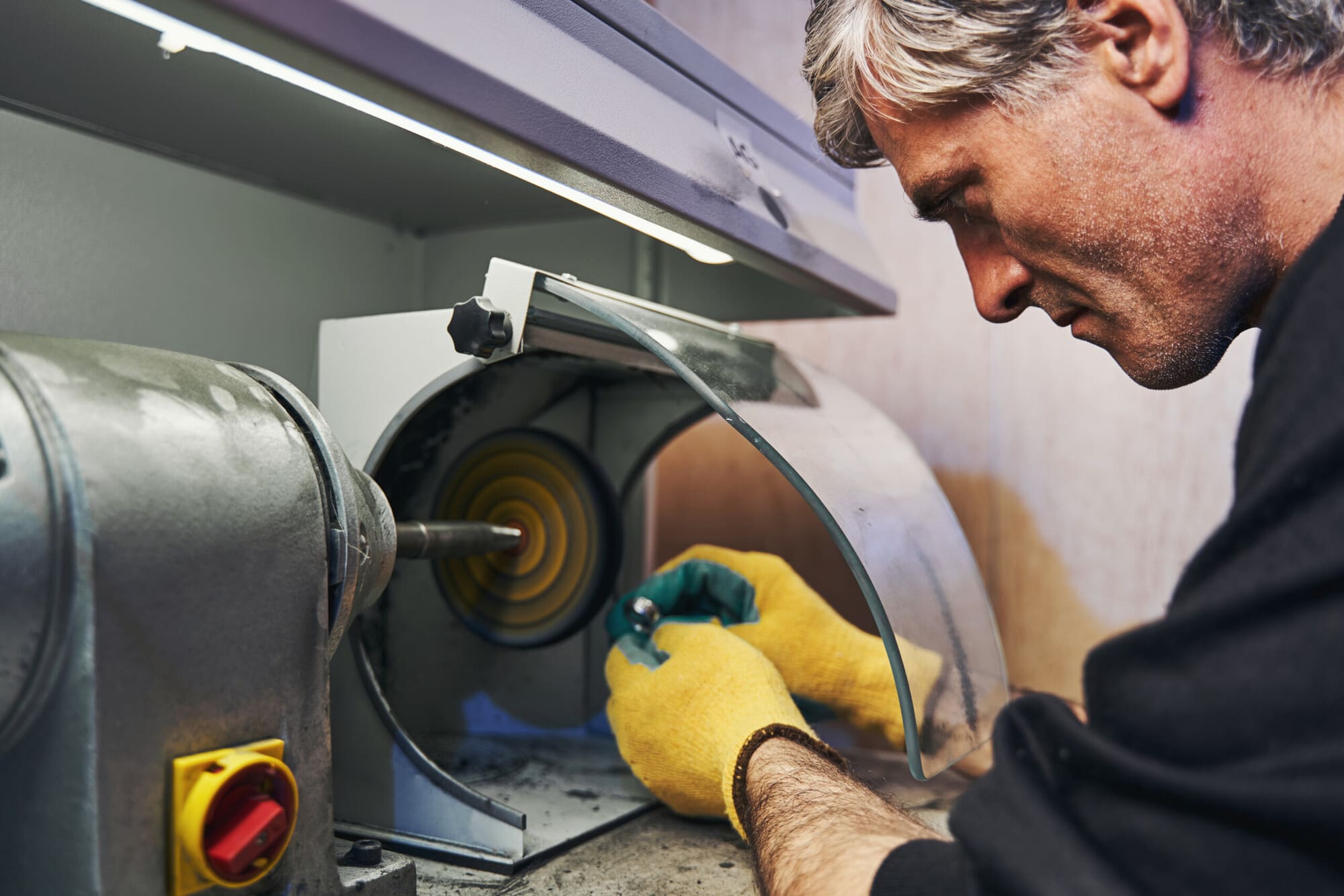
Regulations and Compliance
When considering the environmental impact of your business practices, in addition to understanding law and legislation, you may also want to think about any ethical and moral concerns.
These include:
- Promoting safe practices
- Ensuring workers are well trained and competent
- Knowing your supply chain and working alongside sustainable businesses
Previously, some wheels included asbestos in their core. The use of asbestos was completely banned in 1999 in the UK across all industries including construction, manufacturing and engineering due to severe health hazards associated with exposure to asbestos. This means that wheels containing asbestos are hazardous and are no longer allowed.
Using abrasive wheels can be extremely dangerous, especially if they are used incorrectly or unsafely or you select the wrong type of wheel for the job. It is important to provide comprehensive training, conduct a risk assessment and be compliant with any relevant regulations to reduce the chance of an accident or incident.
Accidents involving abrasive wheels are all too common. Hazards associated with using them include cuts and eye damage from flying shards or sparks, as well as health problems from dust inhalation, noise and vibrations. According to the Health and Safety Executive, there are over 5,000 accidents each year related to angle grinders alone. An angle grinder is a type of handheld abrasive wheel, ranked by ROSPA as the third most dangerous tool due to its prevalence in accidents.
Employers have a duty to keep workers safe. There are various pieces of legislation that relate to abrasive wheels, including the Health and Safety at Work Act 1974 which is the primary piece of legislation that relates to occupational health and safety.
Key legislation that specifically covers abrasive wheel usage includes:
The Provision and Use of Work Equipment Regulations 1998 (PUWER)
PUWER regulations dictate that workplace equipment should not pose an undue risk to workers. The regulations set out guidance and rules that should be followed to protect workers’ safety.
Additionally, employers have a duty to provide adequate protective equipment to workers under:
The Personal Protective Equipment at Work Regulations 1992
Users of abrasive wheels may also be exposed to additional hazards from vibrations, noise and breathing in hazardous particles, which are covered under the following legislation:
- The Control of Vibration at Work Regulations 2005
- The Control of Noise at Work Regulations 2005
- The Control of Substances Hazardous to Health (COSHH)
To keep everyone safe and reduce hazards you will need to undertake a risk assessment for using abrasive wheels. You may also need to conduct an Environmental Risk Assessment and take steps to mitigate damage to the environment (including the landscape, local animals and the general population) such as:
- Taking measures to minimise damage from noise, vibrations, debris or dust
- Having fire safety procedures in place
- Setting out clear procedures for safe disposal of spent wheels or used cutting fluids
- Making decisions around transportation / supply chain to keep traffic and emissions to a minimum
Some steps you can take to reduce the risks to the workers and the environment when using abrasive wheels include:
- Offering comprehensive training
- Only allowing competent people to use abrasive wheels
- Ensuring a clean and tidy environment, free from flammable materials, to reduce the risk of fire caused by rogue sparks
- Providing PPE
- Providing fire training and appropriate fire extinguishers
- Using, handling and storing abrasive wheels properly to reduce chances of damage/ breakage which creates unnecessary waste
- Adopting cleaner and greener workplace practices (recycling, commitments to renewable energy)
Eco-Friendly Abrasive Wheel Options
Some companies are now offering more environmentally friendly options for abrasive wheels. We will look at these in more detail in the next section.
As well as understanding what eco-friendly alternatives are available, there are other considerations to be made that can help your business to become greener and more sustainable, such as:
- Reducing your carbon footprint, including buying from local suppliers and purchasing in bulk to avoid unnecessary journeys.
- Understanding your supply chain and how they operate and choosing companies that align with your values regarding sustainability and the environment.
- Communicating with suppliers and clients about how you can all work more sustainably and reduce overall harm to the environment and natural world.
- Utilising technologies that might make it easier to be more sustainable or make greener decisions.
- Consider using ‘carbon offsetting’ in your business to reduce your impact on climate change.
- Recycling your old worn, used or cracked abrasive wheels by using a reputable company that offers this service.
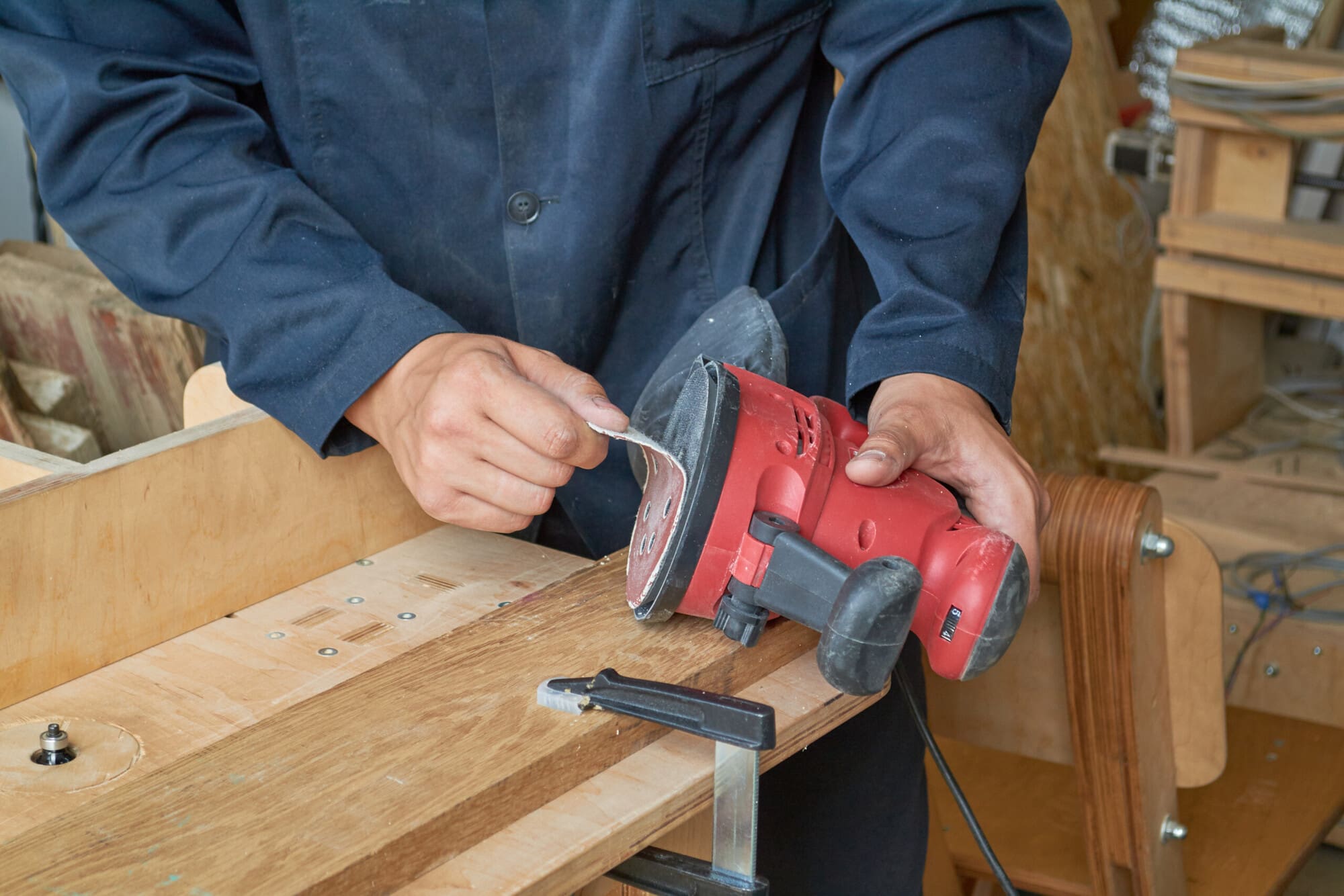
Innovation and Research
Sustainability is an increasing area of interest and concern within business, in particular manufacturing and construction industries which tend to produce significant CO2 emissions.
Research is ongoing into cleaner, greener practices relating to abrasive wheels including alternative methods and materials, addressing concerns around non-organic cutting fluids and improving efficiency to reduce energy consumption.
One key area that has yielded some of the most promising new practices to reduce the impact of abrasive wheel usage concerns disposal methods and opportunities for recycling old wheels or wheel scrap.
An Indian research paper published in 2020, for example, reported on the possibility of the recycling and reusing of grinding scrap as an alternative abrasive grain for the abrasive water jet machining (AWJM) process. Researchers considered the impact of recycling and repurposing abrasive wheel stubs more sustainably. It also looked into the possibility of reducing the need for garnet (a natural resource) in the process to redress the supply/ demand of the substance and stabilise the price of garnet, which currently fluctuates accordingly.
Their research concluded that converting industrial grinding wheel rejects into one of the resources for the abrasive water jet machining (AWJM) process would:
- Provide benefits to society and industry
- Minimise the need to deplete garnet resources so quickly
- Lower associated machining costs
Another significant innovation has been the rise in popularity of environmentally friendly cutting fluids used in the grinding process, in particular vegetable-based oils such as soybean oil. These oils can deliver effective lubrication whilst also:
- Reducing greenhouse gases (in comparison to traditional methods)
- Increasing worker safety (through reduced exposure to harmful substances)
- Reducing overall environmental impact
- Being more sustainable (when produced using renewable sources)
- Saving money (from longer fluid lifespan, increased tool life and reduced waste disposal costs)
Moving forward, the main benefits of adopting alternative cutting fluids include them being biodegradable, recyclable and containing no inorganic additives.
Research is also being conducted into the efficacy of water-based cutting fluids that would be kinder to the environment.
Conclusion
The best way to reduce risk is always to remove the hazard completely; however, for some jobs, abrasive wheels are necessary and cannot be eliminated. In such cases, it is important to consider how we can adopt new practices to reduce harm to the environment and operate more sustainably.
As new advancements are made in green technology, the options for green alternatives to abrasive wheels will expand. It is important to embrace these changes and invest in new and more sustainable business practices. As a business owner, you can take steps to decrease your carbon footprint and adopt ethical waste management procedures, whilst prioritising the safety of workers and balancing all of these against ensuring the continued efficiency of your business practices.