In this article
Abrasive wheels are important in many industries and their use ranges from manufacturing and construction to maintenance and repair. These tools, however, bring about risks and hazards that demand strict safety protocol adherence. According to the Royal Society for the Prevention of Accidents (ROSPA), one specific type of abrasive wheel—angle grinders—was ranked third in the list of most dangerous tools. Most of these involved the wheel shattering. In this case study, we’ll look at two examples of success stories where organisations have implemented abrasive wheel safety measures with huge success. In looking at these stories, we aim to shed light on best practices and inspire others.
What is abrasive wheel safety?
Abrasive wheels are integral components of many industrial processes. They are used for grinding, cutting, polishing and sharpening. Industries like manufacturing, maintenance and construction use these constantly.
The wheels themselves are made of abrasive particles that are bonded together. When used improperly—and even properly—they come with risks that can have severe consequences, including death. This occurs due to wheel breakage, flying debris and being exposed to hazardous substances during grinding. Due to the risks, comprehensive safety measures are needed to protect workers and their equipment.
In the UK, the safe use of abrasive wheels comes under the Provision and Use of Work Equipment Regulations 1998 (PUWER). These regulations provide a legal framework for employers and employees working with abrasive wheels.
Within the regulations, proper training, regular inspections and the use of personal protective equipment (PPE) is mandated. This is in order to mitigate the risks associated with using these tools. Those who understand and adhere to these regulations are much less likely to come into problems.
The importance of training and awareness
Ensuring abrasive wheels are handled, used and maintained appropriately requires knowledge and awareness. Training is crucial as it equips workers with the skills to use the wheels while also teaching them how to mitigate the associated risks.
Comprehensive training will help workers identify the potential hazards associated with abrasive wheels. This will include:
- Recognising signs of wear and tear
- Understanding proper mounting procedures
- Understanding the limitations of each type of abrasive wheel.
Training must also include reference to regulations and their compliance. This isn’t just a legal obligation but a moral one; it ensures the safety and well-being of workers and fosters a culture of adherence to safety standards.
Well-trained workers are also much more efficient and know how to operate abrasive wheels more effectively. This leads to improved productivity and a reduction in downtime as there are fewer equipment failures. Proper training means abrasive wheels are also used only for their intended purpose. This prolongs their lifespan and reduces the frequency of replacements.
Above all else, a well-informed workforce is less susceptible to accidents and injuries. Training programmes reduce incidents because they teach the proper use of abrasive wheels but also because they instil a mindset of attentiveness and caution.
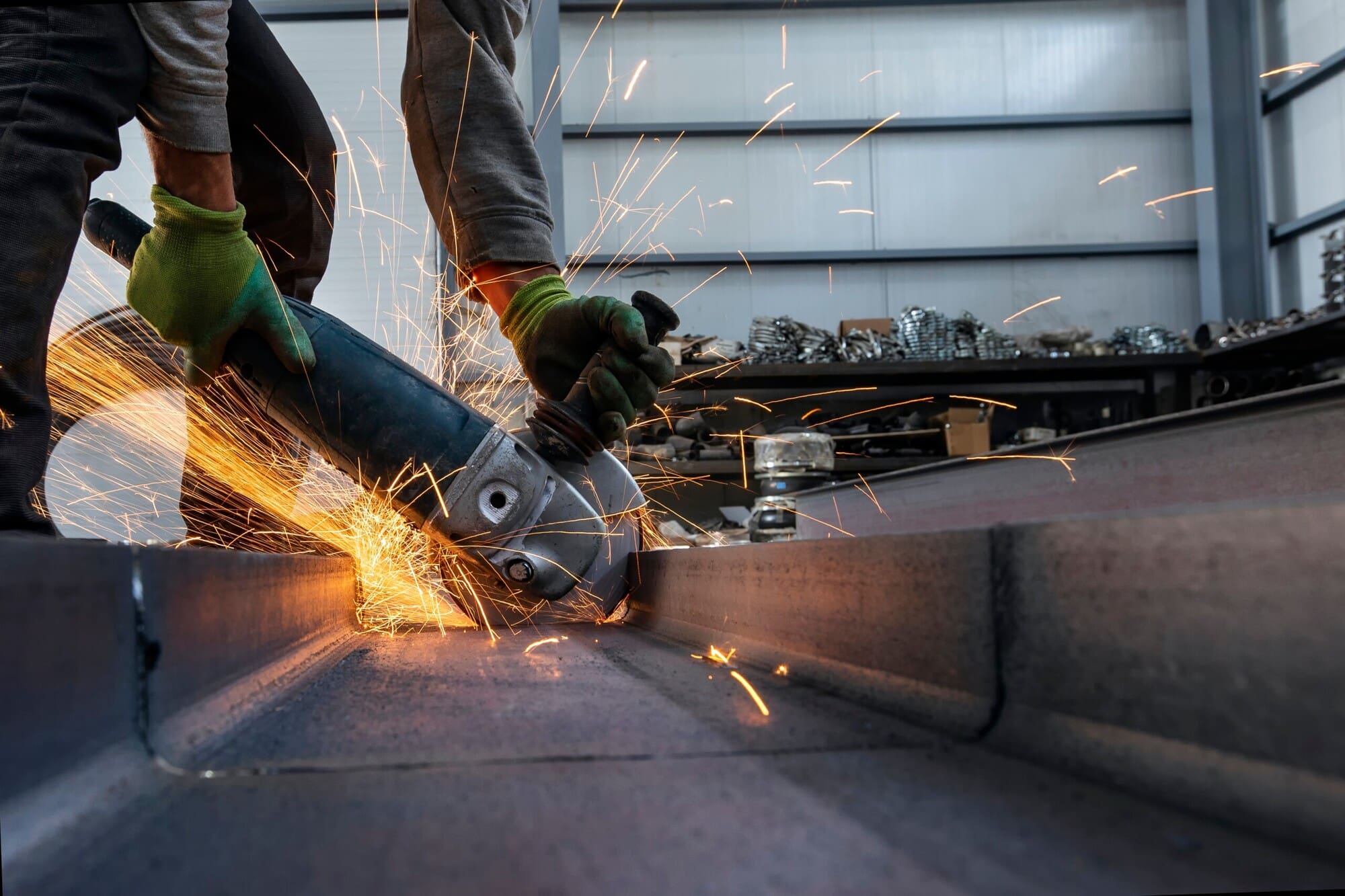
Case Study 1: Company X’s Safety Initiative
In its pursuit for a safer working environment, Company X became a frontrunner in robust abrasive wheel safety initiatives. This leading manufacturing firm recognised the inherent risks associated with abrasive wheel usage in their production processes. The company committed themselves to a comprehensive safety initiative that was aimed at enhancing the handling, operation and maintenance of abrasive wheels.
Approach
Company X began by conducting a detailed risk assessment of their current abrasive wheel operations. They identified all of the potential hazards and evaluated their existing safety protocols. They also revisited relevant regulations to ensure their full understanding. With this information fresh in their minds, they formulated a tailored approach that addressed the unique challenges of their operational environment.
Training programmes
At the centre of the company’s new safety initiative was a series of targeted training programmes. These were designed to educate employees of all levels, including those well-versed in abrasive wheel use. There were various aspects involved, which included:
- Hands-on training: This offered practical sessions to familiarise workers with the correct mounting, balancing and operation of abrasive wheels. Included in this was training on the proper adjustment of guards and how to select appropriate personal protective equipment (PPE). Workers were also trained on the limitations of different abrasive wheel types.
- Risk awareness workshops: Besides the practical training, Company X also organised workshops on risk awareness. The sessions focused on recognising signs of damage and wear. It reinforced the importance of regular equipment inspections to promote a culture of safety.
- Supervisor training: Supervisors had specialised training that allowed them to oversee and enforce safety procedures effectively. This included education on how to identify potential safety issues, conduct regular audits and guide workers.
As a result of the initiatives, Company X noted measurable improvements in various key areas over the following years:
Reduction in incidents
The targeted training programme and continued professional development (CPD) resulted in a significant reduction in incidents. Workers were more adept and proactive in identifying and addressing potential hazards, which led to a safer working environment.
Increased compliance
It was noted that there was an increase in compliance with safety regulations. Workers became more diligent in following protocols and less laissez-faire in attitude. Supervisors were more attuned to workers and ensured they kept up to date with guidelines.
Enhanced equipment longevity
Managers had expected to go through more abrasive wheels as workers erred on the side of caution and replaced worn wheels. However, the opposite happened. Proper handling and maintenance learned from training meant that wheels had a longer lifespan. Ultimately, this had the added bonus of cost savings for the company.
Improved confidence
Employees reported feeling more confident in their use of abrasive wheels. This translated into them being more proactive and working collaboratively to promote safety. Workers began reporting concerns and taking initiatives to suggest improvements.
Case Study 2: Training Centre’s Impact
Our second case study shifts the spotlight to a dedicated training centre that has played a pivotal role in abrasive wheel safety advancements. This centre has imparted knowledge and influenced industry practices across the country.
The AWSTC is a specialised institution committed to providing comprehensive safety training on the safe handling, operation and maintenance of abrasive wheels. The centre recognised a critical need for specialised education in this domain and has, therefore, become a leader in providing comprehensive training to workers using these tools.
Training methods
The AWSTC uses a multi-dimensional approach to its training. This has meant that a wide range of people have successfully trained here. The methods used include:
Interactive workshops
This provides a hands-on approach that simulates real-world scenarios. The workshops cover the correct mounting and balancing procedures of abrasive wheels and troubleshoot common issues as well as teach the crucial emergency response procedures. This practical approach has meant that participants grasp theory while developing their practical skills.
State-of-the-art simulations
Alongside practical training by trained leaders, the AWSTC is a leader in using cutting-edge simulations to create realistic scenarios. This allows trainees to practise in a controlled environment and in safety. The simulations include scenarios involving wheel breakages, guard use and emergency shutdown procedures. This is an immersive experience that allows users to explore the ‘what if’ scenarios in complete safety. This enhances their preparedness and decision-making skills for actual situations they might come across.
Comprehensive course material
Participants attending AWSTC courses receive in-depth materials covering the regulatory guidelines as well as best practices and the latest advancements. These takeaways are nicely presented to enable trainees to refer back to them regularly.
Facilities
The state-of-the-art centre is equipped with modern equipment. Trainees have the opportunity to try out the full range of abrasive wheels and grinders to enhance their familiarity with the different tools and their uses.
Instruction
All of this is given under the expertise of seasoned expert instructors who have deep theoretical knowledge as well as practical experience.
AWSTC’s impact
The AWSTC’s role in abrasive wheel training has been pioneering and is seen as the gold standard in the industry. Graduates of their programmes consistently exhibit heightened awareness of abrasive wheel safety. They are also more attuned to hazards and are proactive with safety measures.
As a result, companies report less downtime and fewer incidents, which they put down to the thorough training given by the AWSTC. The organisation’s reputation for excellence has meant it has received industry-wide recognition and awards for innovation in practice.
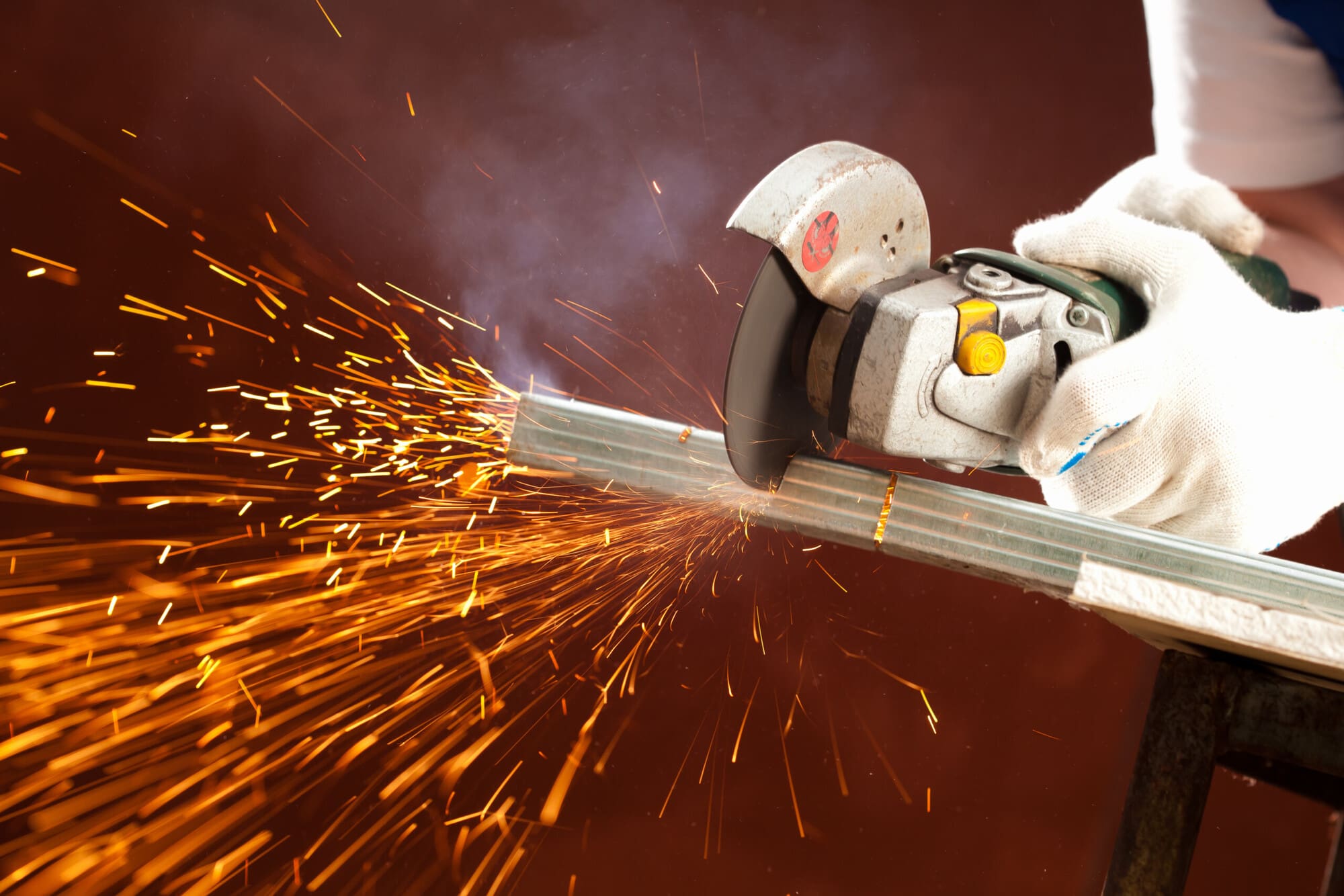
Measuring success and continuous improvement
Ensuring abrasive wheel safety success isn’t just about reducing or eliminating accidents. This also involves various other factors that contribute to an improved safer worker environment. Here are some of the ways in which managers and business owners measure success and improvement in abrasive wheel safety:
Accident reduction
Of course, the primary indicator of success has to be the noticeable reduction in incidents and accidents linked to abrasive wheel use. Tracking and recording incidents over time helps organisations to assess their safety initiatives and training. When there’s a declining trend, it becomes clear that implemented safety measures are working.
Regulatory compliance
Adherence to relevant safety regulations is critical for success. Monitoring and ensuring compliance with PUWER and abrasive wheel safety regulations shows a company is committed to meeting legal standards. Regular assessments, paper trails and audits can gauge whether an organisation is complying appropriately and help identify areas for improvement.
Training programme effectiveness
Assessing the impact of training can help determine its success. It is also important in determining how competent the workforce is in handling abrasive wheels. Metrics like the percentage of employees completing training and the scores on assessments provide insights into how effective training is.
Workplace culture
This is also integral to abrasive wheel safety. When there is a positive workplace culture that prioritises safety, we know that this is more likely to be a safer and more successful enterprise. Continued professional development should be a regular occurrence too. An engaged workforce that participates in safety initiatives is a sign of a workplace with safety being a shared value.
Equipment longevity
The condition of equipment and its lifespan can be linked to the success of training in maintenance and handling. When abrasive wheels are used appropriately and reach their expected lifespan, costs are lower. Monitoring these costs can reveal trends that indicate whether or not workers are handling and maintaining them properly.
Reporting of near misses
Near miss reporting is an important part of identifying potential hazards before an accident can occur. Having a low rate of near misses suggests that safety measures are working. Having a high rate of near miss reporting suggests that safety culture is respected, and employees are confident to share near miss situations without fearing reprisal.
Continuous improvement initiatives
Success in abrasive wheel safety is ongoing and is something that requires constant re-evaluation. Regular reviews are needed of safety protocols, risk assessments and reporting mechanisms.
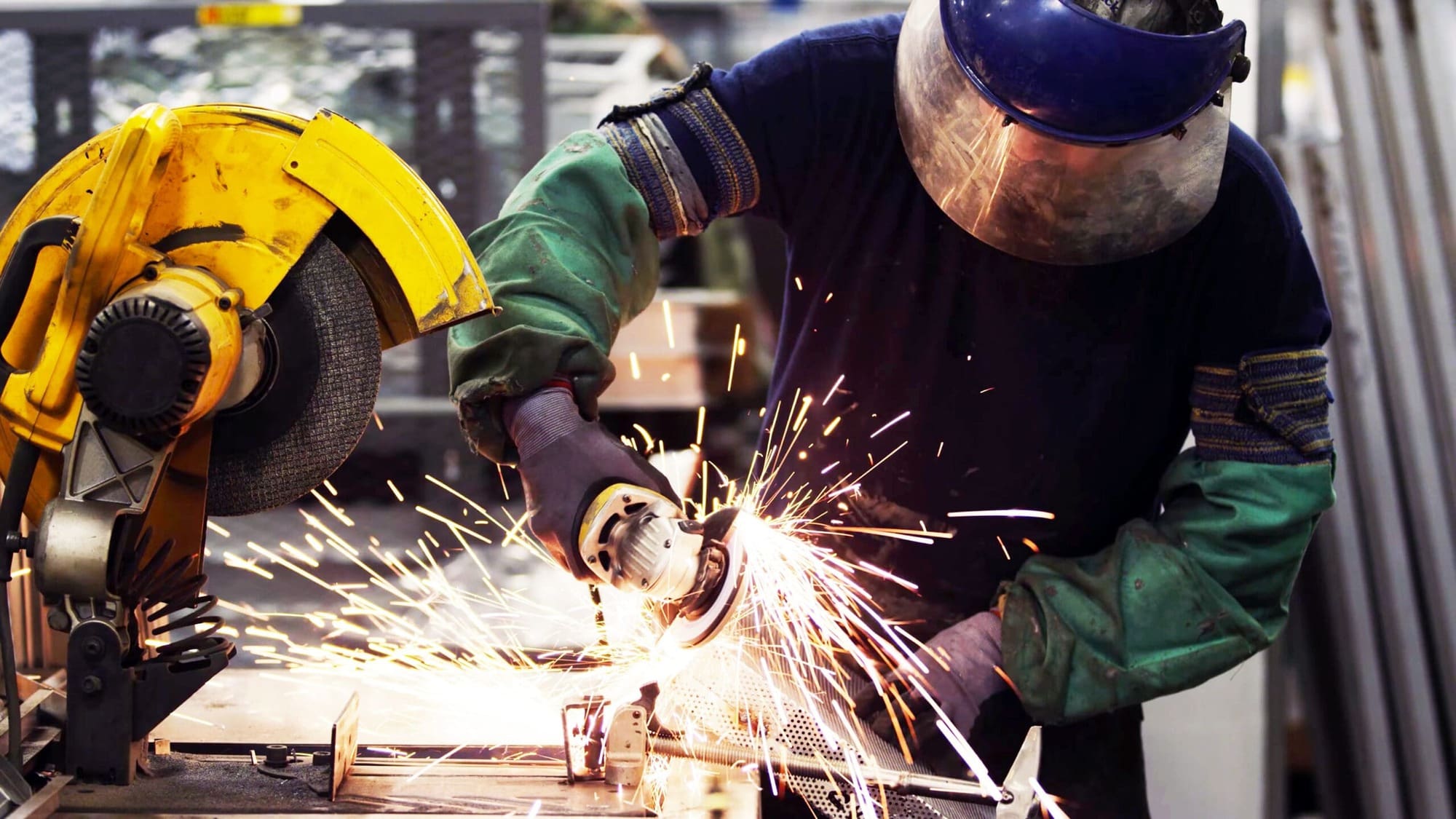
Inspiring industry-wide change
Success stories like those of Company X and the AWSTC are powerful. They can serve as inspiration for change in the wider industry. Abrasive wheel safety can and should be a collective responsibility of UK organisations.
These success stories:
- Showcase tangible results: They show that positive outcomes are achievable with the right approach to abrasive wheel safety. Sharing measurable results like these inspires other organisations to adopt similar strategies.
- Demonstrate best practices: These stories show proactive organisations that have robust training programmes, innovative approaches to equipment maintenance and proactive risk assessments. Organisations can learn from their experiences and adopt proven methods.
- Encourage collaboration and knowledge sharing: Industry-wide changes to safety are facilitated through knowledge sharing and collaboration. Many organisations in this industry see other organisations as direct competitors and so won’t collaborate fully. However, a culture of openness means that companies can elevate their safety standards collectively to benefit the entire industry.
- Empower employees as safety advocates: Case studies like these show how vital employees are in playing their part in safety. Well-informed employees can contribute to a safer workplace and be committed to preventing accidents and injuries.
To summarise, success stories act as beacons of inspiration. They can guide other companies towards the prioritisation of safety. When organisations work together collectively, they show that safety is more important than competing. And while they might not want to share customers, it’s perfectly possible to share safety successes to improve standards in the industry as a whole.