In this article
Abrasive wheels are used across a range of industries for heavy-duty tasks such as grinding or cutting hard materials, for example metal or concrete. They are made up of abrasive particles that are bonded together using organic or inorganic bonded materials.
The HSE states that accident statistics indicate that almost half of all accidents associated with abrasive wheels can be attributed to an unsafe system of work or operator error. To reduce the chance of an accident or injury occurring, training is essential for anyone carrying out work with them.
Training should cover all aspects of working with abrasive wheels including how to handle and store them correctly. Incorrect handling techniques and poor storage can damage and degrade abrasive wheels, making them more likely to break during use and cause injury.
Storage Guidelines
Abrasive wheels need to be stored safely in an organised workspace. They are best stored in segmented storage units, featuring racks, drawers or compartments where the wheels can be grouped by their type, similar to the image here.
- Storage units should be solid and of sound structure
- Most plain and tapered wheels are best supported on their edges or on a central support
- Wheels that are placed on their side should have support in the form of cradles so they cannot roll out
- Safeguards should be in place so wheels don’t fall over
- Abrasive wheels should be stored in temperature controlled rooms away from excessive heat, moisture or extreme cold
- Cylinder wheels and large, straight cup wheels can be stacked on the flat side with corrugated cardboard (or a similar cushioning material) between them
- The edges of the wheels should fit into the storage rack and not protrude out
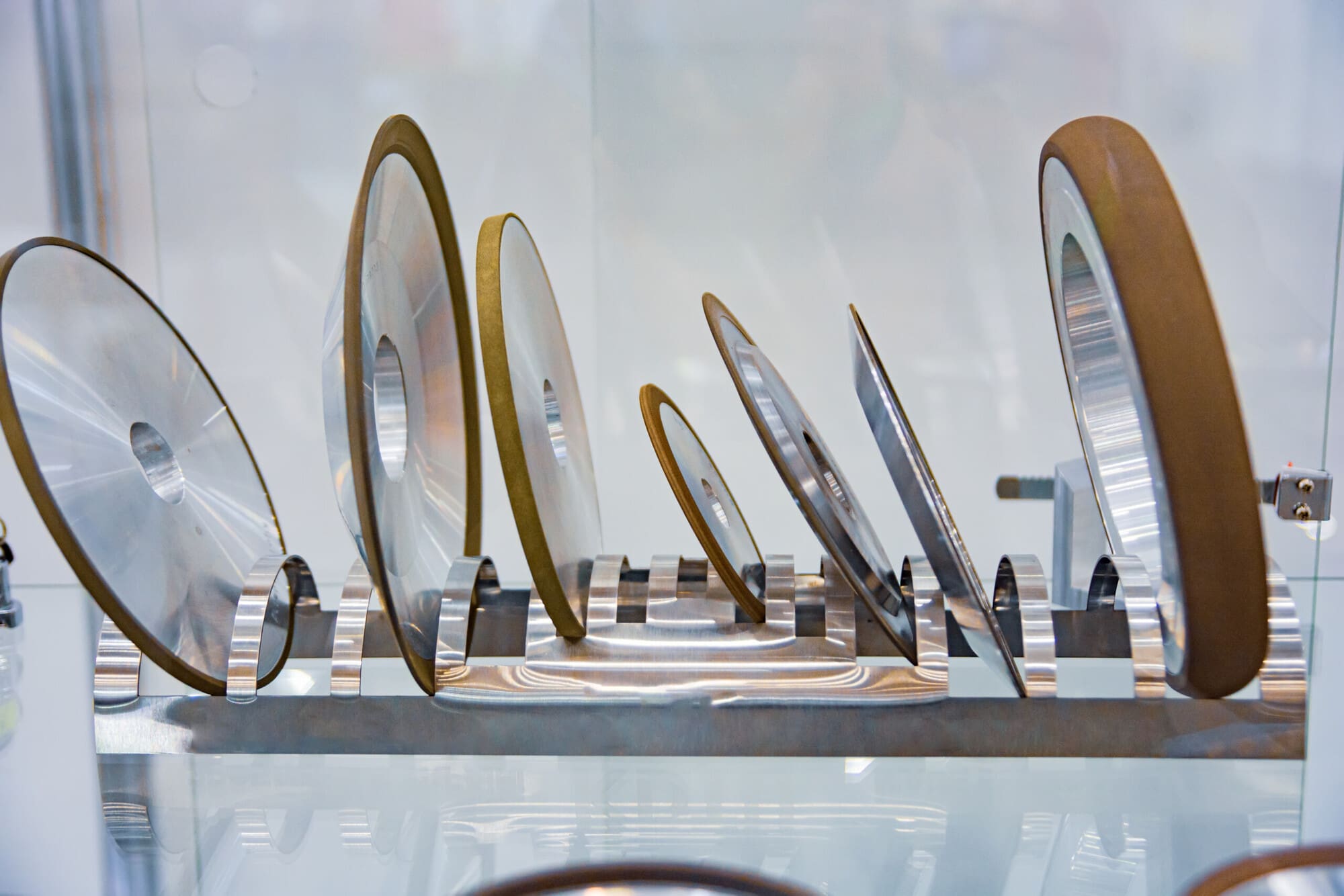
Additional storage guidelines for storing and selecting abrasive wheels from storage:
- Mark wheels with the date of receipt and use a rotation system so older wheels are used before newer wheels
- If a wheel has been in stock for more than 3 years you need to contact the manufacturer to check its current viability
- When putting away or taking out a wheel, keep in mind correct manual handling techniques at work to minimise the risk of injury
- Keep all stockrooms and storage areas clean, tidy and free from hazards
- Always move and work safely in storage areas to avoid slips, trips and falls or bumping into the units
- Ensure storage areas for abrasive wheels are dry and well lit
Handling and Transportation
When abrasive wheels are damaged or weakened, they can break or burst whilst they are being rotated at extreme speeds. This can result in severe injuries. It is vital that abrasive wheels are handled safely and with care at each step in the supply chain including:
- Manufacture
- Packing
- Transportation
- Delivery
- Destination
The risk of breakage exists for all types of abrasive wheels. It makes financial sense for all businesses that make or use abrasive wheels to keep breakages to a minimum. This means exercising care at all stages from design, to wheel manufacture and testing, to adopting appropriate safety measures once the abrasive wheel reaches its end user.
All abrasive wheels can be fragile and should be handled with care:
- Do not handle abrasive wheels roughly
- Never stack heavy items (such as castings or tools) on top of abrasive wheels
- Avoid rolling the wheels (if you have to do this because the wheel is large then you must only do so on a soft, resilient floor surface)
- Use trucks or suitable conveyors to move wheels around if they are too heavy to be carried by hand
- Take care when stacking wheels on trucks and do not leave them vulnerable to toppling over
- Never drop or toss handheld machines onto the ground as this could damage the wheel
- Take special care with wheels that are already mounted between flanges
Inspection and Maintenance
Manufacturers of abrasive wheels are expected to take all necessary steps to supply wheels that are fit for purpose and safe to use, which includes performing speed tests. It is also important for everyone in the supply chain to take responsibility for following any safety guidelines and regulations.
All abrasive wheels are relatively fragile and must be handled, stacked and transported with care to ensure they reach their destination in optimum condition.
Abrasive wheels should be carefully inspected for any issues on delivery and any that are not up to standard should be discarded and refunded by the company who provided them:
- Wheels should be unpackaged carefully on arrival
- They should be cleaned with a brush and visually examined for any damage that may have occurred in transit
- The soundness of the wheels can be checked with a ‘ring test’ by tapping on the wheel with a light, non-metallic object (not suitable for all wheels, for example 100mm diameter or less, plugs and cones, mounted wheels)
- Heavy wheels can be supported on a clean, hard surface for the ring test
- Light wheels should be suspended carefully from their hole or by using a finger or a small pin
- Fit and proper wheels should emit a metallic ring – if the wheel sounds dead, for example due to cracking, it should not be used
- You can compare the ring sound to others of the same size and specification of wheels if you are unsure
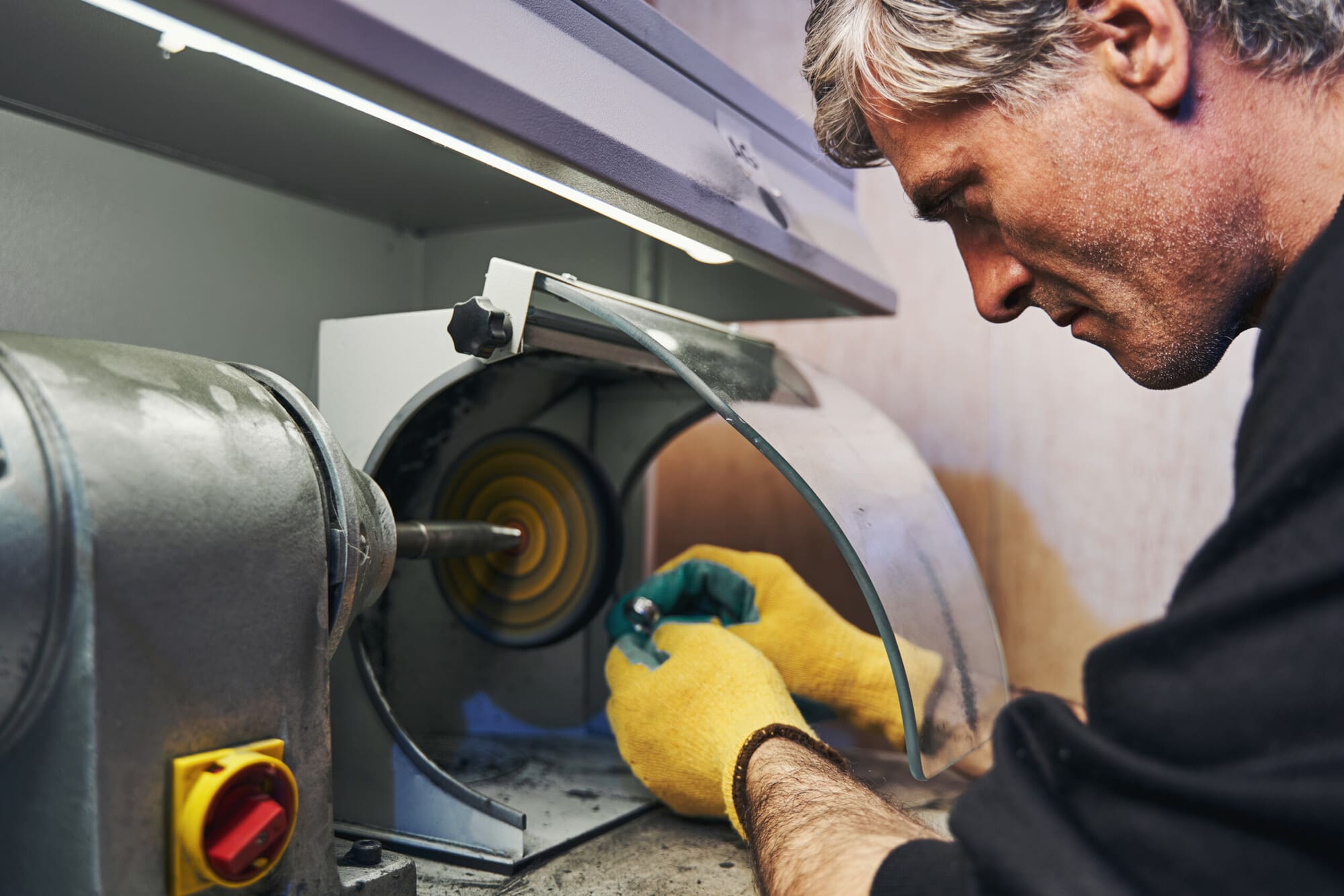
Personal Protective Equipment (PPE)
The best way to prevent accidents involving abrasive wheels is to ensure that only competent people are working with them. If you are employing people who use abrasive wheels you should also conduct a risk assessment specifically for this activity.
A risk assessment is a structured way to assess how dangerous a task might be and what measures need to be put in place to prevent or manage hazards.
A risk assessment follows these basic steps:
- Identify hazards
- Assess the risks
- Control the risks
- Record your findings
- Review your controls
A key component of reducing harm and protecting workers from hazards is to provide them with suitable personal protective equipment (PPE). PPE should be safe, clean and fit for purpose.
PPE that should be worn if you are working with an abrasive wheel, includes:
- Eye protection to protect the eyes against flying debris from abrasive and metallic particles
- Face masks to avoid dust or particle inhalation
- Adequate head protection to protect the head from wheel fragments or debris
- Protective gloves to minimise the severity of a hand or finger injury
- Protective footwear to reduce the chance of injury to the foot or toes, or minimise the severity of the injury if injury occurs
You should also avoid wearing loose clothing (such as ties, baggy sleeves etc) that can get caught in machinery. For abrasive wheel work, including heavy-duty cutting and grinding tasks, it is best to wear suitable overalls. Fireproof clothing can provide some safeguarding against ignition from rogue sparks or magnesium particles.
Legal and Regulatory Compliance
The Health and Safety at Work Act 1974 is the primary piece of legislation that relates to overall occupational health and safety.
Key legislation that specifically covers abrasive wheel usage includes:
The Provision and Use of Work Equipment Regulations 1998 (PUWER)
The PUWER outline that all workplace equipment should not pose an undue risk to workers. The PUWER also set out various statutes that should be followed in order to keep workers safe. All machinery associated with abrasive wheels should be well maintained, fit for use and regularly inspected, as well as periodically tested.
Additionally, employers have a duty to provide adequate protective equipment to workers under:
The Personal Protective Equipment at Work Regulations 1992
Users of abrasive wheels may also be exposed to additional hazards from vibrations, noise and breathing in hazardous particles which are covered under the following legislation:
- The Control of Vibration at Work Regulations 2005
- The Control of Noise at Work Regulations 2005
- The Control of Substances Hazardous to Health (COSHH)
If there is an accident and the employer is found to be at fault, the results of legal proceedings can include large fines or prison time. You will also incur serious reputational damage. Your business will likely suffer financially, from loss of productivity and money, whilst investigations are conducted and operations have to cease.
As an employer, it is important to show that you have been compliant and taken reasonable measures to keep workers and the general public safe. Doing so safeguards you and protects others:
- Conduct appropriate risk assessments
- Understand legislation and legal requirements
- Practise good record keeping
- Be responsible and lead by example
- Perform checks on equipment, work areas, storage areas and operations
- Provide appropriate storage units or storage bins to store abrasive wheels
- Provide trucks or conveyors to move heavy wheels that can’t be carried safely
Poor organisation and improper storage can contribute to abrasive wheel damage and breakage. It is essential that areas where stock is held are regularly inspected for hazards or unsafe working conditions, just like you would inspect electrical equipment.
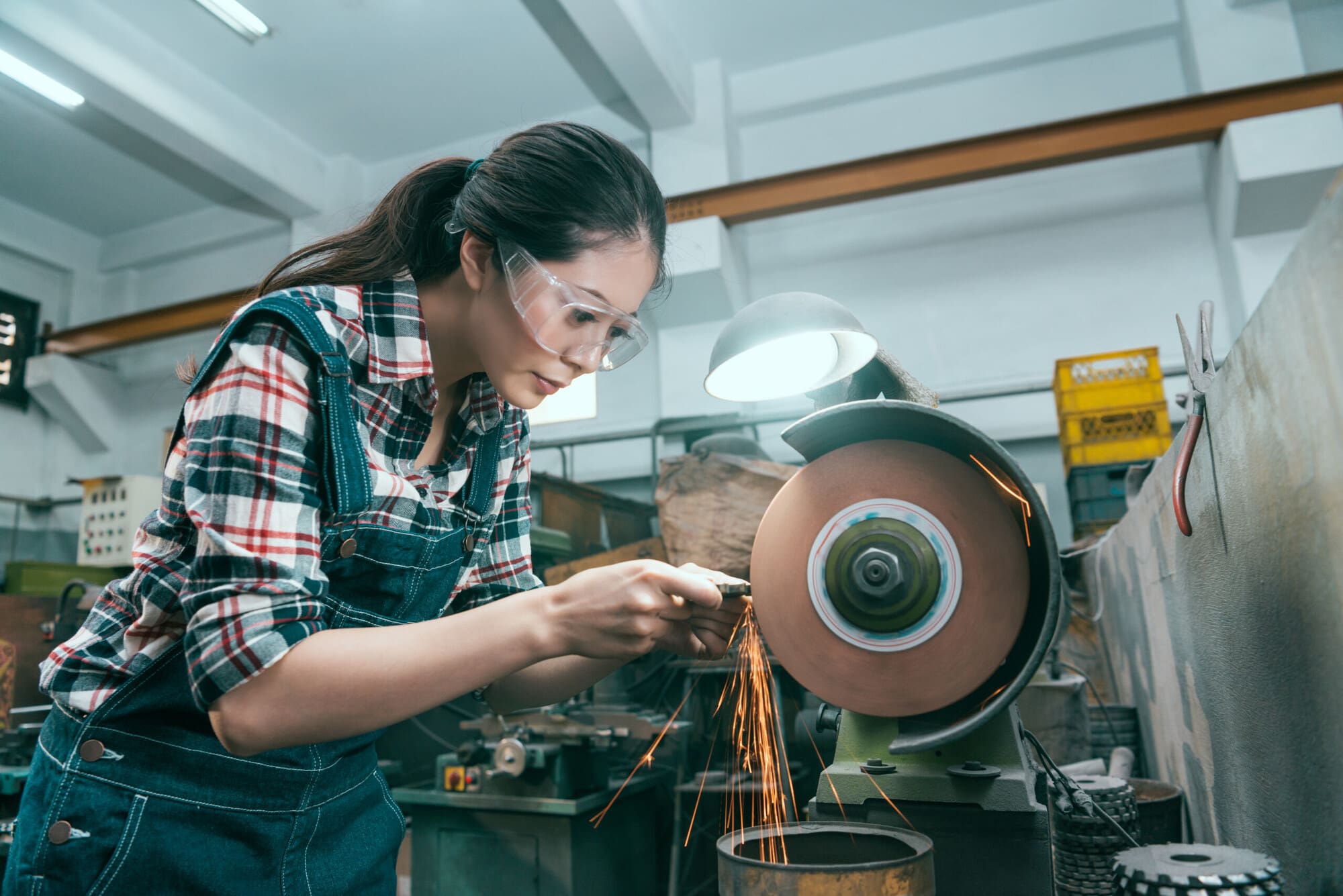
Training and Certification
HSE guidelines dictate that abrasive wheels should only be handled and used by someone who has been deemed competent and is trained to do so.
Comprehensive training should include the safe storage, handling and use of abrasive wheels. Emphasis should be on practical training.
Abrasive wheel awareness training courses should minimally cover the following in relation to how to handle and store abrasive wheels:
- How abrasive wheels should be stored, handled and moved around
- The dangers of improper handling and storage
- The importance of good housekeeping in storage and work areas
In terms of handling and storage, it should be stressed to anyone attending training that the consequences of failing to store or handle an abrasive wheel correctly could be catastrophic if the wheel becomes weakened or damaged and an accident occurs. Emphasis should be on practical scenarios that show both what to do and what not to do. Include pictures, diagrams or videos of proper handling methods and how appropriate storage areas should look.
Additionally, abrasive wheel training should cover the following key aspects:
Hazards and precautions:
- The hazards and risks that can arise from using abrasive wheels
- Precautions that should be taken
Understanding abrasive wheels:
- Methods of marking abrasive wheels (this should cover their size, type, restrictions of use, expiry date and maximum operating speed)
- Methods for inspecting and testing abrasive wheels for damage
Assembly and component parts:
- Explanation of any components that are used with abrasive wheels (such as flanges, blotters, wheel bushes, nuts)
- How to assemble abrasive wheels correctly (ensuring they are properly balanced and fit for purpose)
- Dressing an abrasive wheel (removing material from the cutting surface)
The role of PPE:
- What PPE should be worn
- How to use personal protective equipment (PPE)
Using the abrasive wheel:
- Safe mounting of abrasive wheels
- Safe usage of abrasive wheels
Training records should be kept that state the attendee’s name, signature and the date they received their training. It is a good idea to conduct refresher training on the subject periodically.
You may want to cover more than the basics in your training sessions, such as:
- How to carefully unpack, clean and examine a new wheel
- How to reject a damaged wheel and what the manufacturer should do
- Performing a ‘ring test’ and which types of wheels are unsuitable for this test
- Statistics on abrasive wheel accidents and injuries
- First aid basics
Anyone who is being instructed in the use of abrasive wheels should also be taught the potential risks and implications if they are not stored, handled or used correctly. Many people misunderstand the life-changing injuries that can occur as a result of wheel bursting, wheel breakage or from rogue sparks. These include:
- Cuts and damage to the skin
- Eye damage
- Digit amputation
- Serious head and facial injuries
- Burns
During training you should reiterate the types of injuries associated with abrasive wheel accidents and the role that handling or storing abrasive wheels in an unsafe way can have in such accidents. Workers should be made aware of the role everyone has to play; for example, if they handle a wheel carelessly and drop it, they are putting their colleagues at risk down the line if the wheel gets cracked and no one notices the damage and the wheel ends up in use.
Workers should also be given information on how to report accidents and how to get immediate medical help.
Training and certification on the safe use of abrasive wheels should only be delivered by someone who is sufficiently skilled and competent to do so.
Our CPD accredited Abrasive Wheels training course is made up of six units and provides an overview of how to assess and manage the risks of working with abrasive wheels, as well as tips for if an emergency situation arises.