In this article
COSHH legislation outlines responsibilities for both employers and employees to ensure a safe working environment for everyone. Employers have the responsibility to educate and inform staff on how to complete tasks safely and to supply the correct equipment to do so. Employees have the responsibility to ensure that they conduct their daily tasks safely and don’t cause harm to themselves or others.
What is COSHH?
The Control of Substances Hazardous to Health (COSHH) Regulations 2002 are a set of legal directives that require employers to control those substances which present any kind of health risk in and around their workplace.
The control of substances part of COSHH includes any form of hazardous material, including:
- Biological agents such as bacteria and viruses.
- Dust.
- Fibres.
- Fumes.
- Gases.
- Liquids.
- Mists.
- Nano-particles.
- Solids.
- Vapours.
The hazardous to health part of COSHH includes damage to:
- Central nervous system.
- Eyes.
- Genes.
- Internal organs.
- Lungs.
- Mouth.
- Nose.
- Skin.
- The risk of injury due to combustion or explosion.
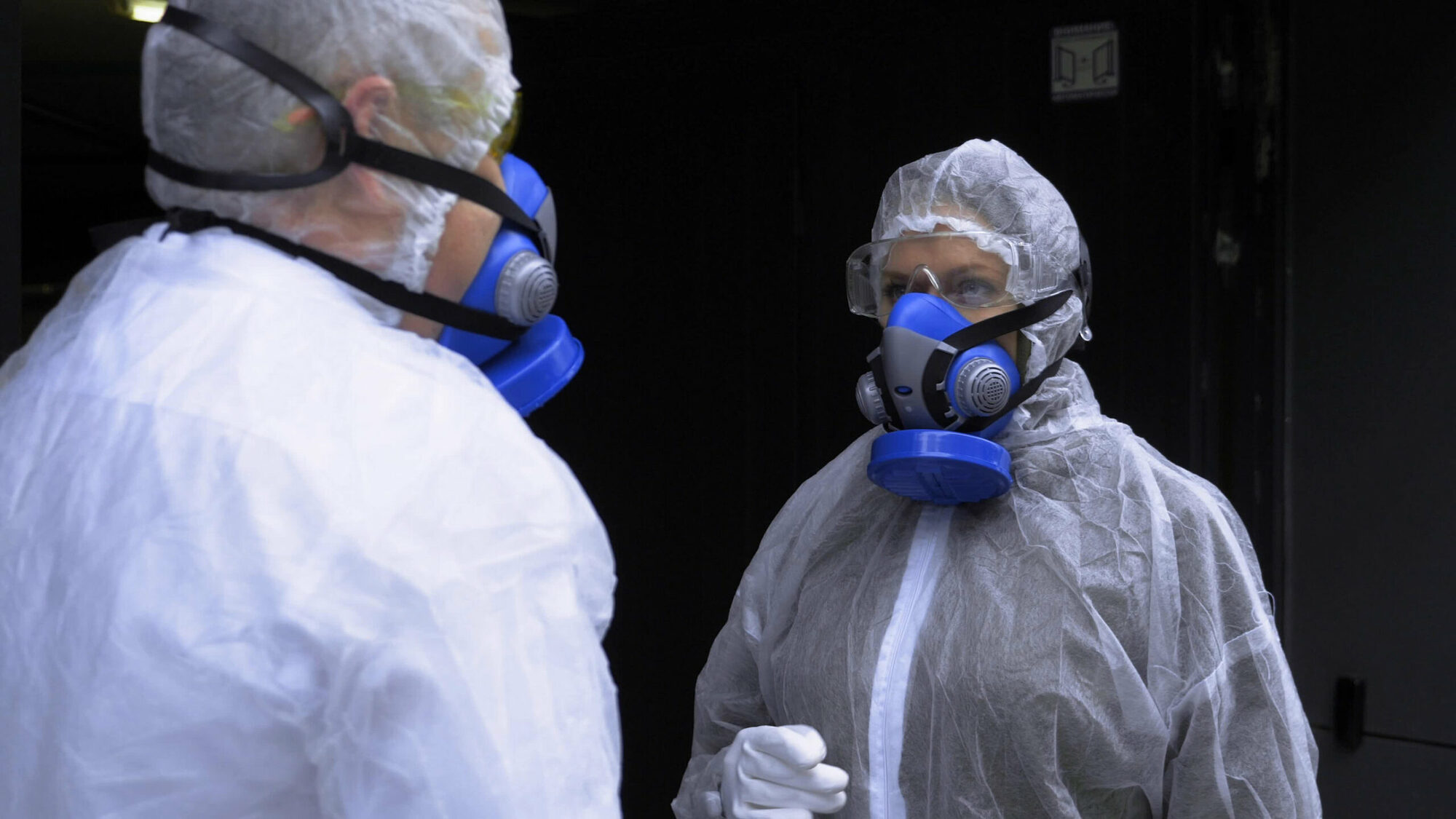
Employee responsibilities under COSHH?
As part of their legal obligations under the COSHH Regulations, employees should:
- Help their employers to create a safe working environment and abide by the regulations set in the workplace. Health and safety is all about preventing people from being harmed or becoming ill through work, so the workplace safety regulations, including COSHH, have been put in place for a very good reason, employee’s own and their colleagues’ safety.
- Follow the procedures and any control measures put into place by their employer to stop accidents and overexposure from any form of hazardous material which causes harm. Their responsibility as an employee, is to ensure that they use and abide by any and all control measures implemented in their workplace. They are obligated by law to protect themselves, and others, by following the proper procedures designed to minimise risk of exposure.
- Wear the correct personal protection equipment (PPE), such as but not limited to eye protection, noise protection and respiratory protection, and ensure that the PPE is stored correctly and returned to its correct storage facilities. They should also regularly check their PPE for any damage and replace when necessary. Returning the PPE that they use to its proper storage place ensures that it will not be damaged inadvertently. Tracking and storing their PPE in specific areas also allows their employer to ensure it is properly maintained and kept safe for them when they need it.
- Never refuse to use the PPE that their employer provides. An employee could needlessly endanger their own safety and it is a direct breach of the COSHH Regulations. Their employer has every right to discipline them, and the HSE has every right to prosecute them if they deem the employee’s actions dangerous.
- Remove any contaminated PPE and dispose of in a specified area, before interacting with people or taking in food or drink to minimise risks.
- Report any accidents, incidents, spillages or breakages of any form of hazardous material which causes harm immediately, correctly and accurately.
- Report inadequate or defective equipment and control measures immediately, correctly and accurately. The employer should be conducting regular equipment checks and maintenance, but it is entirely possible that their assessments missed something. When an employee spots a defect, they should immediately report it.
- Attend medical check-ups. Some workplaces provide medical check-ups to ensure their workers are safe while working with hazardous substances. If these are not provided by the employer, the employee should take responsibility to check up on their own health on a regular basis.
- Use any cleaning and showering facilities that are provided by their employers following their employer’s procedures. Cleaning and washing facilities are provided by employers and are designed specifically to remove the contamination from employees to ensure that any form of hazardous substances which causes harm is removed from the person and work area as soon as is practicable to minimise the risks. An employee may be covered in substances such as oil or dust and smelling of fumes at the end of their workday. It is important employees clean themselves thoroughly to ensure they do not contaminate locations they visit after work.
- Keep up to date with training provided. Under COSHH Regulations employers must provide COSHH training, information and updates; it is the employees’ responsibility to adhere to all training and information provided for them. As with personal protective equipment, the training and information given to them by their employer is designed specifically to keep them safe from harm when doing their job.
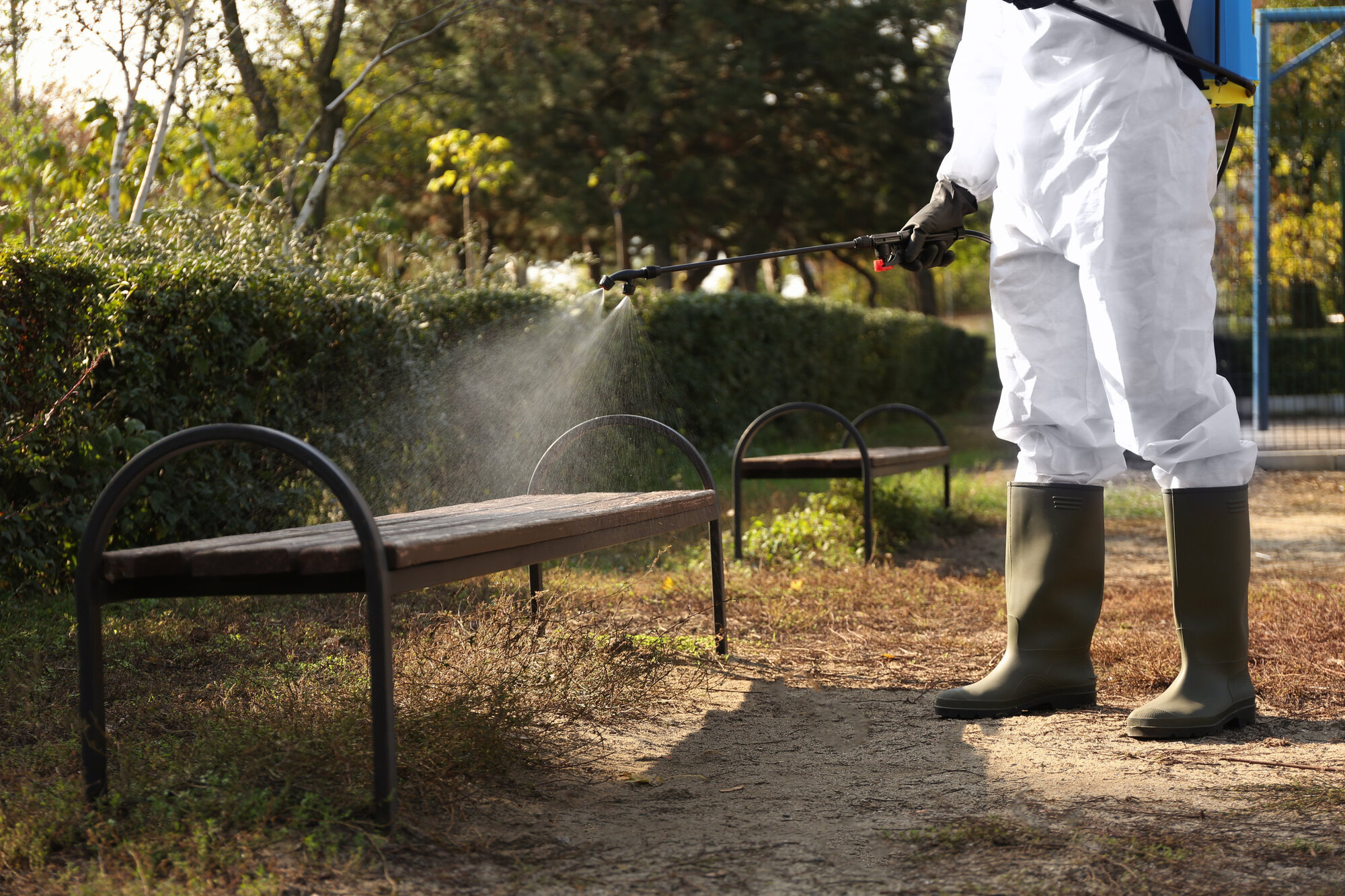
Who does the employee report to?
An employee may spend most of their time on the “shop floor”, with eyes on the hazards they work around. A very important part of COSHH safety is the reporting of incidents, near misses or new hazards. Employees are the best people to spot failures, and potentially new hazards, relating to the substances, equipment and control measures they use on a daily basis.
An employer should name someone to be in charge of checking and maintaining control measures under COSHH. Any incidents, near misses or new hazards identified by employees under COSHH should be reported to this person.
That designated person will have the responsibility to:
- Check that the process isn’t emitting uncontrolled contaminants.
- Check that the control equipment continues to work as it was designed to.
- Check that workers follow the right ways of working.
- Involve workers in developing control measures to make sure they are suitable for the way they carry out the work.
- Encourage workers to suggest improvements, and to report anything they think might be going wrong.
Who does COSHH apply to?
Depending on the industry or environment you work in, your business or organisation may require COSHH risk assessments to be done in your workplace in order to be legally compliant.
If you are not sure if you require COSHH risk assessments, consider the following factors:
- Do I work in an environment or industry which includes any hazardous substances?
- If so, how can these hazardous substances cause harm?
- How can I prevent or avoid the risk of harm happening in my workplace?
Preventing exposure to hazardous substances is always the most effective place to start when evaluating the safety of your workplace. If there is a means of using an alternative, safer substance rather than a hazardous substance, this is a good place to start.
This could include things such as using water-based as opposed to solvent-based products, or applying products using a brush as opposed to spraying them, which can cause them to spread in the air, increasing the chances of inhalation.
COSHH Regulations place a duty on an employer in regards to their employees. This also means the employer is responsible for protecting other people from hazardous substances in the workplace, whether they work there or not, such as visitors or the general public; any people who are on the premises where the work is being carried out.
Employees themselves have legal duties of care under COSHH Regulations as listed above. The COSHH Regulations also apply the same to self-employed people as they would to other employers.
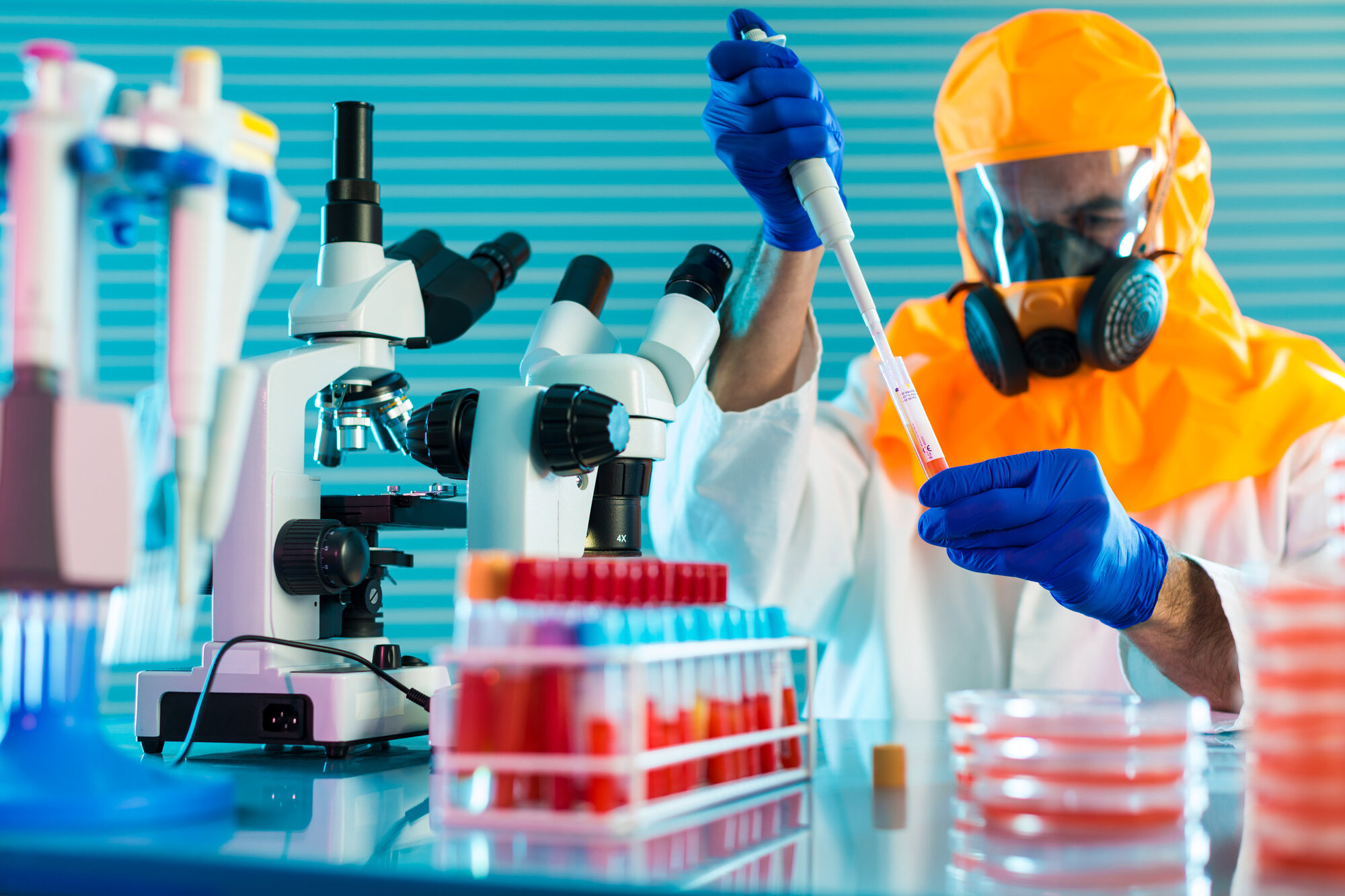
COSHH risk assessment
Far from being complicated, a COSHH risk assessment is a straightforward step-by-step process.
Step 1:
- Assess the risks to health arising from hazardous substances used in or created by your workplace activities. To assess the risks, you must:
– Identify the hazardous substances present in your workplace.
– Consider the risks these substances present to people’s health.
Step 2:
- Decide what precautions are needed. You must not carry out work which could expose your employees to hazardous substances without first considering the risks and the necessary precautions, and what else you need to do to comply with COSHH:
– Decide what precautions are needed to help you decide whether risks are significant, compare any controls you already use.
– Check that your control systems work and are effective.
– Consider whether the substance could be, for example, absorbed through the skin, inhaled, swallowed.
– What further action should be taken? If you decide that there are risks to health, you must take action to protect your employees’ and others’ health.
Step 3:
- Prevent or adequately control exposure. You must prevent your employees being exposed to hazardous substances. Where preventing exposure is not reasonably practicable, then you must adequately control it. The COSHH Regulations require you to prevent exposure to substances hazardous to health, if it is reasonably practicable to do so. You might:
– Change the process or activity so that the hazardous substance is not needed or generated.
– Replace it with a safer alternative.
– Use it in a safer form, for example use pellets instead of powder.
– Control exposure at source, for example local exhaust ventilation, and reduce to a minimum the number of employees exposed.
– Provide personal protective equipment, for example face masks, respirators, protective clothing, but only as a last resort.
– Use occupational exposure standards. An OES is set at a level that is not likely to damage the health of workers exposed to it, by inhalation, day after day, based on current scientific knowledge. For substances with an OES, you should reduce exposure to comply with that OES.
– Use maximum exposure limits. MELs are set for substances which may cause the most serious health effects such as cancer and occupational asthma, and for which it is not possible to set an OES. For substances with MELs you are required to reduce exposure so far as is reasonably practicable and, in any case, below the MEL.
– Consider skin absorption. Some substances can damage the skin itself while others can readily penetrate it, so you must consider the need to protect skin in deciding on control measures.
Step 4:
- Ensure that control measures are used and maintained properly and that safety procedures are followed. When:
– Using the controls, COSHH requires your employees to make proper use of control measures and to report defects.
– Maintaining controls, COSHH places specific duties on you to ensure that controls are kept in efficient working order and good repair.
Step 5:
- Monitor the exposure of employees to hazardous substances, if necessary. Under COSHH, you have to measure the concentration of hazardous substances in the air breathed in by workers where your assessment concludes that:
– There could be serious risks to health if control measures failed or deteriorated.
– Exposure limits might be exceeded.
– Control measures might not be working properly.
Step 6:
- Carry out appropriate health surveillance where your assessment has shown this is necessary or where COSHH sets specific requirements. COSHH requires you to carry out health surveillance in the following circumstances:
– Where an employee is exposed to one of the substances listed in Schedule 6 to COSHH.
– Where employees are exposed to a substance linked to a particular disease or adverse health effect and there is a reasonable likelihood under the conditions of the work of that disease or effect occurring and it is possible to detect the disease or health effect.
Step 7:
- Prepare plans and procedures to deal with accidents, incidents and emergencies involving hazardous substances, where necessary. This will apply where the work activity gives rise to a risk of an accident, incident or emergency involving exposure to a hazardous substance. In such circumstances, you must plan your response to an emergency involving hazardous substances before it happens.
Step 8:
- Ensure employees are properly informed, trained and supervised. COSHH requires you to provide your employees with suitable and sufficient information, instruction and training which should include:
– The names of substances they work with or could be exposed to and the risks created by such exposure, and access to any safety data sheets that apply to those substances.
– The main findings of your risk assessment.
– The precautions they should take to protect themselves and other employees.
– How to use personal protective equipment and clothing provided.
– Results of any exposure monitoring and health surveillance ensuring compliance with Data Protection.
– Emergency procedures which need to be followed.
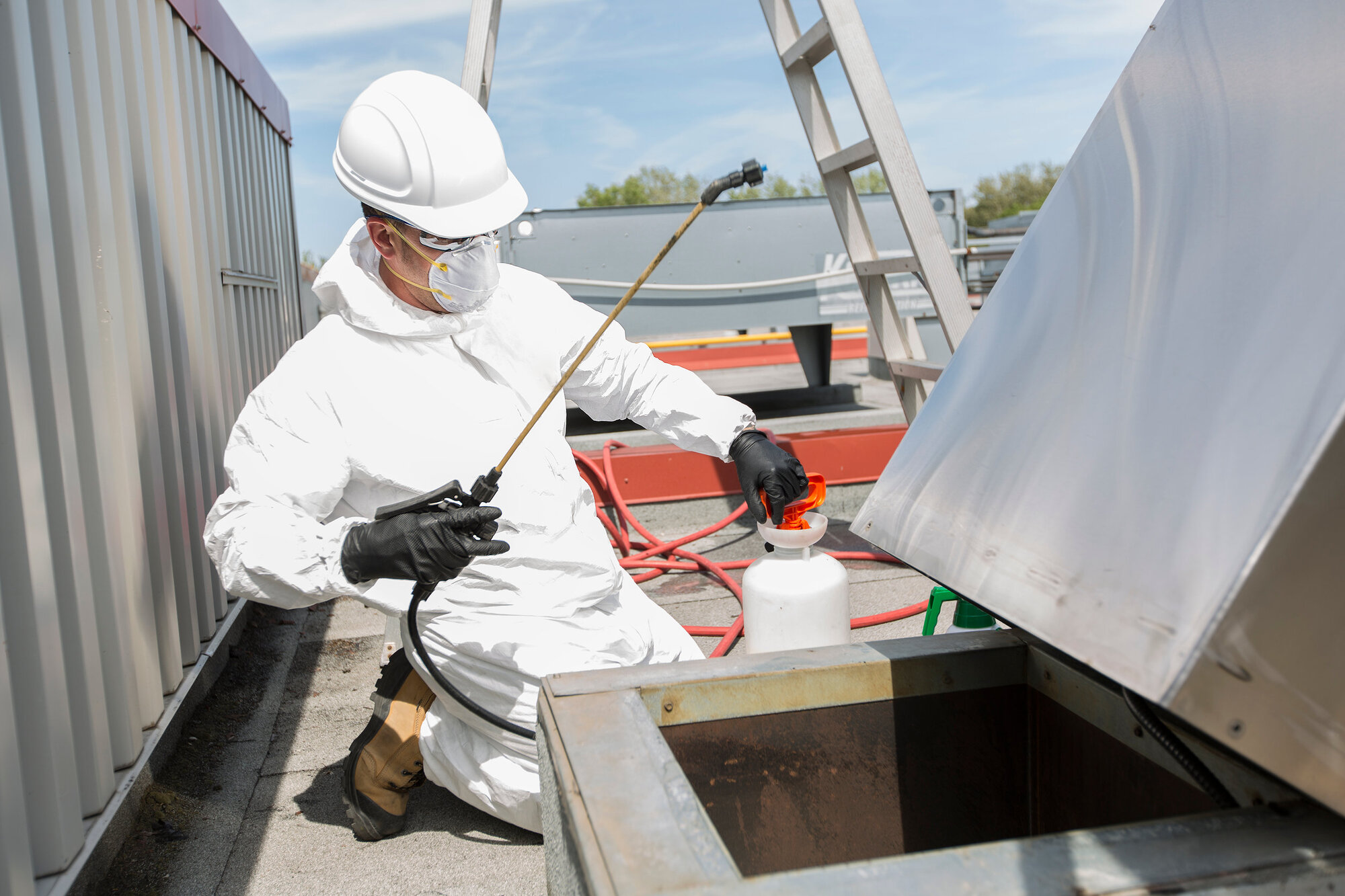
COSHH regulations and COSHH legislation
As we have seen previously, COSHH stands for ‘Control of Substances Hazardous to Health’ and is a set of regulations to protect employees from ill health when working with specific substances and materials. The COSHH legislation requires employers to identify and manage the hazards and risks from substances in a workplace.
Other legislation and regulations connected with COSHH are:
REACH and COSHH
REACH is a European Union regulation and stands for Registration, Evaluation, Authorisation and restriction of Chemicals. It came into force on 1 June 2007 and replaced a number of European Directives and regulations with a single system. COSHH and REACH work together and both require a risk assessment.
REACH was designed so that better information on the hazards of chemicals and how to use them safely will be passed down the supply chain by chemical manufacturers and importers through improved safety data sheets.
RIDDOR and COSHH
Whilst RIDDOR provides legislation on reporting incidents, COSHH focuses on controlling hazardous substances. Both work together to protect the health and safety of everyone entering the work environment, including employees and members of the public.
What happens if you don’t follow COSHH?
The COSHH Regulations are enforced by the Health and Safety Executive (HSE) who keep a constant watch on businesses to ensure they comply with COSHH legislation. Noncompliance with the regulations can result in prosecution as well as hefty fines.
If businesses fail to adequately control hazardous substances, employees or others may become ill or injured. Effects from hazardous substances range from mild eye irritation to chronic lung disease or, on occasions, death. This may result in lost productivity to businesses, leaving them liable to enforcement action, including prosecution under the COSHH Regulations, or result in civil claims from employees.
If any employee fails to adequately comply with the safety controls their employer has put in place, for example not wearing designated PPE or ignoring or circumventing safety training and instructions, they may be liable to disciplinary measures by their employer, possibly dismissal.
In serious breaches the employee may be liable to prosecution and being fined for noncompliance. Individuals can be imprisoned for breaches of health and safety law including COSHH, with sentences of up to six months in the magistrates’ courts and up to two years in the Crown Courts.
Even individuals that avoid a custodial sentence will have to live with the stigma of a criminal conviction, which could restrict their ability to work in certain industry sectors or to travel abroad.
Both employers AND employees can be prosecuted for breaches of COSHH Regulations under criminal law, sometimes simultaneously.
The Sentencing Council introduced new sentencing guidelines in 2016 that brought with them harsher penalties and fines available to the courts for organisations who do not manage health and safety matters effectively. In 2018/2019, the average health and safety fine rose to £150,000, the highest it has ever been, and a total of £54.5 million worth of fines were issued.
Case study from the Health and Safety Executive on noncompliance with COSHH Regulations:
“Workers at a company premises in Bristol were exposed to hazardous chemicals over a four-year period leading to the onset of a disease called ‘allergic contact dermatitis’. One employee suffered four years of his skin blistering, cracking, splitting and weeping because of this allergic dermatitis.
Two other employees also suffered the symptoms of allergic dermatitis, including fingers and hands becoming so badly swollen and blistered that one could not do up his shirt buttons without his fingers splitting open. All three employees had been working with photographic chemicals.
The company was fined a total of £100,000 and ordered to pay £30,000 costs. They were fined £30,000 for breaching the Health and Safety at Work etc. Act 1974, and £10,000 for six separate breaches of the Control of Substances Hazardous to Health (COSHH) Regulations for not making adequate risk assessments, not preventing or controlling exposure of employees to chemicals, and for not providing any ‘health surveillance’ of employees at-risk. They were also fined £10,000 for not reporting a case of allergic contact dermatitis.”
In conclusion
Health and safety should not only be a priority for every employing organisation but also for every employee. We all share a responsibility to use work practices that are as safe as possible, for our own safety and also for the safety of others.