In this article
Workplace safety is an important concern for employers and employees alike. According to the Health and Safety Executive (HSE), 561,000 people sustained a non-fatal injury at work in 2023 and 138 people were killed in work-related accidents. One of the most important aspects of maintaining a safe working environment is the effective management of hazardous substances. The Control of Substances Hazardous to Health (COSHH) regulations are designed to address this need.
COSHH provides a comprehensive framework to help organisations identify, assess and control the risks associated with hazardous substances. These regulations are essential because they aim to protect the health and well-being of employees and prevent workplace illnesses and injuries that can arise from exposure to harmful chemicals, dust, fumes and biological agents.
Effective management of hazardous substances under COSHH not only ensures compliance with legal requirements but also promotes a culture of safety within the workplace. By implementing COSHH regulations, employers can significantly reduce the risk of occupational diseases, increase employee morale and maintain a productive and healthy workforce. Understanding and adhering to these regulations is essential for any organisation that uses or generates potentially hazardous substances, making COSHH a vital component of the overall workplace safety strategy.
What is COSHH?
The Control of Substances Hazardous to Health (COSHH) is a set of regulations established in the UK to manage the risks associated with hazardous substances in the workplace. COSHH aims to protect workers from health problems caused by exposure to these substances by providing a framework for identifying, assessing and controlling their risks.
The primary purpose of COSHH is to ensure that employers take the necessary steps to prevent or reduce workers’ exposure to hazardous substances, thereby minimising the likelihood of occupational illnesses and injuries. This includes substances that are used directly in work processes, as well as those that may be generated as by-products or wastes.
Employers have several legal obligations under COSHH to control exposure to hazardous substances. These obligations include:
Conducting risk assessments
Employers must conduct thorough risk assessments to identify potential hazards associated with substances used or produced in the workplace. This involves understanding the properties of the substances, the ways in which employees may be exposed and the potential health risks.
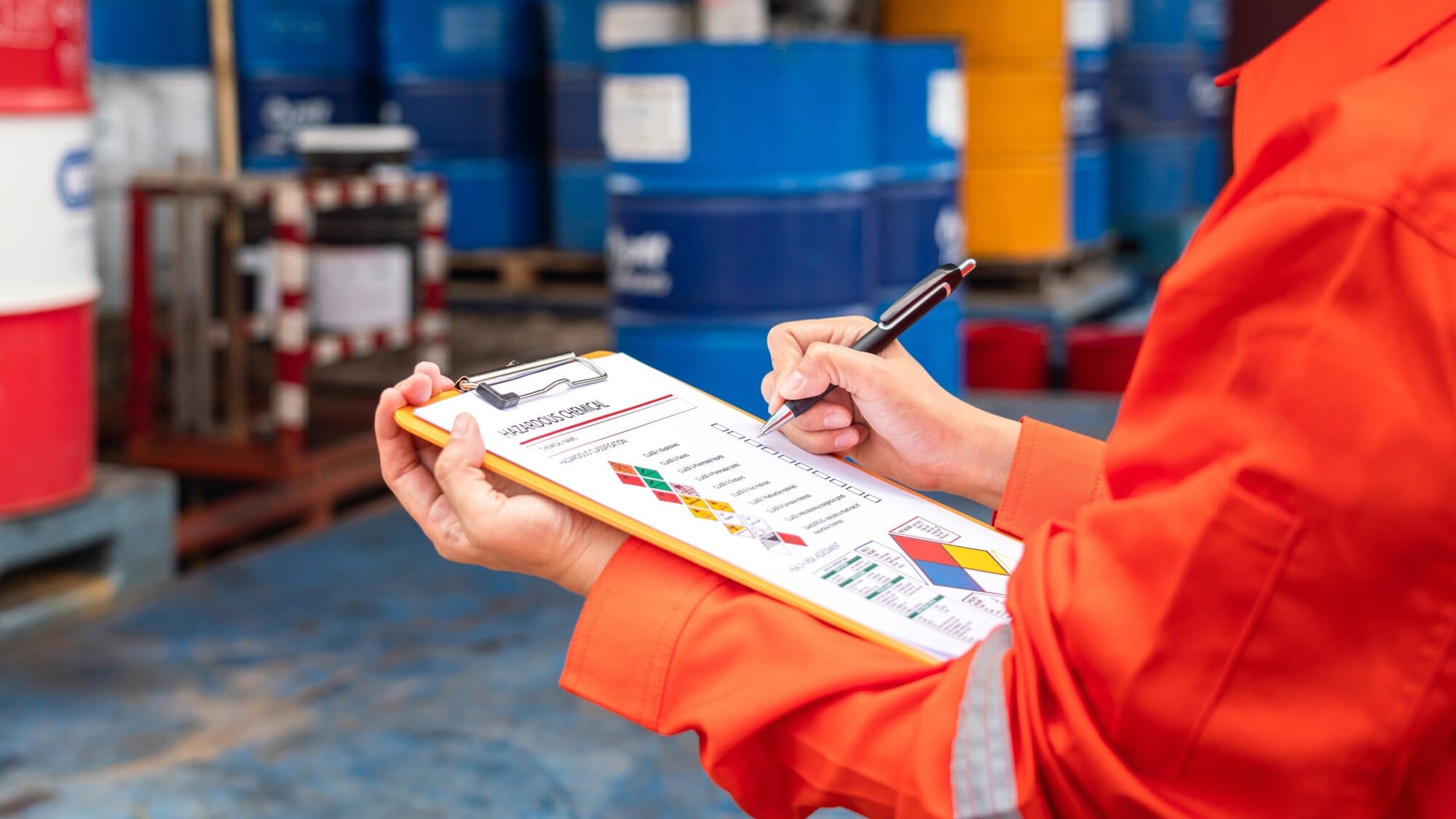
Implementing control measures
Based on the findings of the risk assessments, employers must implement appropriate control measures to either eliminate the hazard or reduce exposure to safe levels. These measures follow a hierarchy of controls:
- Substitution: Replacing hazardous substances with less harmful alternatives.
- Engineering controls: Using equipment or processes to reduce exposure, such as ventilation systems or enclosures.
- Administrative controls: Implementing procedures and practices to minimise exposure, such as providing safe handling instructions and restricting access to high-risk areas.
- Personal protective equipment (PPE): Providing employees with appropriate protective gear, such as gloves, masks or eye protection.
Providing information and training
Employers are required to inform employees about the risks associated with hazardous substances and train them on safe handling practices, use of control measures and emergency procedures. This ensures that employees understand the hazards and know how to protect themselves effectively.
Monitoring and health surveillance
Regular monitoring of the workplace environment and health surveillance of employees may be necessary to ensure that control measures are effective and that employees are not experiencing adverse health effects.
Maintaining records
Employers must keep detailed records of risk assessments, control measures, training and health surveillance activities. These records should be accessible to employees and relevant authorities.
Reviewing and updating
COSHH regulations require that risk assessments and control measures be reviewed and updated regularly, particularly when there are changes in work processes, new substances are introduced or there is evidence that current controls are not effective.
By fulfilling these legal obligations, employers can create a safer working environment, protect the health of their employees and ensure compliance with COSHH regulations. This proactive approach to managing hazardous substances is essential for maintaining workplace safety and minimising the risk of occupational health issues.
Understanding Hazardous Substances
Hazardous substances are materials that can pose a risk to health or safety if they are not properly managed. These substances can exist in various forms, including solids, liquids, gases, dusts, fumes and biological agents. The risks associated with hazardous substances depend on their properties, the extent of exposure and the ways in which they are used or generated in the workplace.
Hazardous substances can be natural or artificial and can take many forms, including:
Chemicals and products containing chemicals
Chemicals can include industrial chemicals, such as those used in manufacturing, cleaning and maintenance processes and household chemicals commonly found in workplaces such as offices, schools and retail environments. Examples of chemicals include solvents, acids, alkalis, cleaning agents and disinfectants and they can commonly be found in cleaning products, petrol, oil and paint.
Fumes
Fumes can be generated from a variety of activities in the workplace. Metal fumes, e.g. from lead, cadmium and zinc, can be generated during activities such as welding, cutting or soldering. Chemical fumes are typically emitted during chemical reactions or chemical processes, e.g. plastic manufacturing or chemical laboratories.
Dust
Another common hazardous substance is dust. Mineral dust is produced from activities such as mining, quarrying and construction. Examples include silica dust from sand, stone and concrete. Organic dust, such as flour dust, wood dust and grain dust, can be found in industries such as agriculture and food processing.
Gases and vapours
Industrial gases are used in a variety of industrial processes. Commonly found industrial gases are ammonia, chlorine and carbon monoxide. Solvent vapours are released from volatile solvents used in painting, cleaning and manufacturing. This can include vapours from benzene, xylene and toluene.
Nanomaterials
Nanomaterials are engineered nanoparticles that are produced by nanotechnology. They are extremely small particles used in advanced manufacturing and research and have a minimum of one external dimension that measures less than 100 nanometres. Examples include carbon nanotubes and nanosilver.
Biological agents
Biological agents can be microorganisms, including bacteria, fungi and other pathogens that can cause infections. Some common examples are Legionella, E. coli and hepatitis viruses. Microorganisms can occur naturally in the environment or can be transmitted from humans, animals and parasites. Biological agents can also include allergens that can cause allergic reactions.
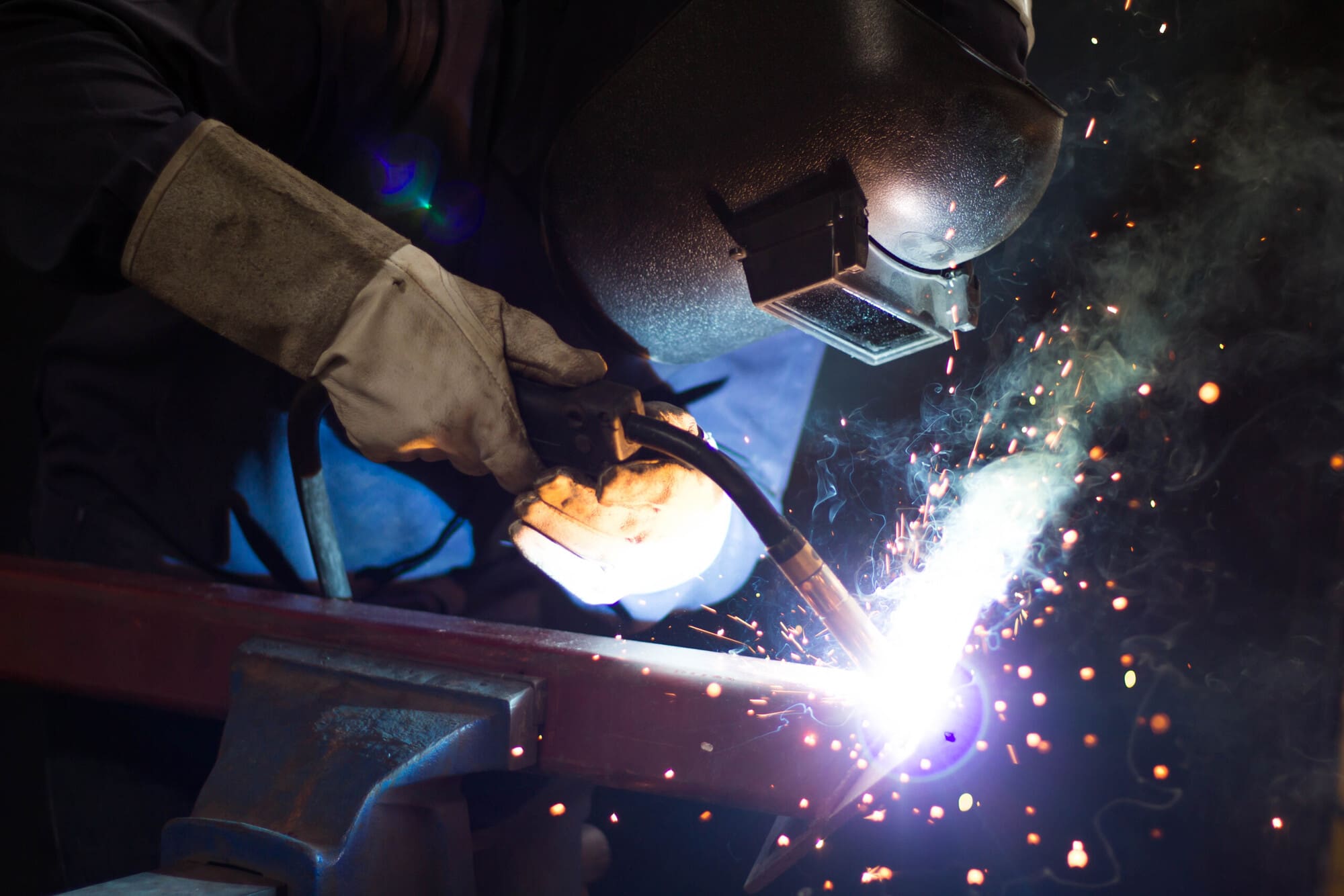
Exposure to hazardous substances can lead to a range of health issues, varying in severity depending on the type and concentration of the substance, duration of exposure and the susceptibility of the individual. Potential health risks include:
Respiratory issues
Exposure to hazardous substances can result in several respiratory issues, such as:
- Asthma: Asthma can be caused by exposure to dust, fumes and certain chemicals. People who already have asthma may also experience asthma attacks.
- Chronic Obstructive Pulmonary Disease (COPD): COPD is linked to long-term exposure to dust and fumes.
- Lung cancer: Exposure to carcinogenic substances like asbestos and certain chemical fumes is associated with lung cancer.
Respiratory issues may be more likely to occur if hazardous substances are inhaled.
Skin conditions
Hazardous substances can result in a number of skin conditions, including:
- Dermatitis: Resulting from contact with irritants such as cleaning agents or solvents.
- Chemical burns: Caused by exposure to strong acids or alkalis.
Allergic reactions
Exposure to allergens can result in an allergic reaction that can range from mild to severe. Allergic reactions can include:
- Allergic rhinitis: Triggered by inhalation of dust or biological agents.
- Anaphylaxis: Anaphylaxis is a severe, potentially life-threatening allergic reaction to certain biological agents.
Toxic effects
Many different toxic effects can occur as a result of exposure to hazardous substances and can include:
- Organ damage: Chemicals like solvents and heavy metals can cause toxicity that affects internal organs including the liver, kidney or nervous system. Toxicity can also result in neurological damage.
- Reproductive harm: Certain substances can affect reproductive health and can lead to birth defects or fertility issues.
- Eye damage: Eye damage can range from eye irritation to severe damage and loss of vision.
Infections
Infections are caused by exposure to biological agents, such as bacteria and viruses and can lead to diseases such as tuberculosis, hepatitis or influenza.
Understanding the nature of hazardous substances and their associated health risks is essential for implementing effective control measures and ensuring workplace safety. By recognising these dangers, employers and employees can work together to minimise exposure and protect health.
Responsibilities Under COSHH
Under the COSHH regulations, employers are required to conduct thorough risk assessments to identify hazardous substances and evaluate the risks associated with their use. This involves:
- Identifying hazardous substances: As part of the identification process, all chemicals, dust, fumes, gases and biological agents used or produced in the workplace must be identified and recorded.
- Assessing exposure: Workplaces are required to determine how, when and where employees might be exposed to these substances. This includes evaluating the duration, frequency and intensity of exposure.
- Evaluating health risks: Understanding the potential health effects of exposure requires workplaces to consider factors such as toxicity, routes of entry (e.g. inhalation, skin contact and ingestion) and susceptible populations (e.g. pregnant workers).
Based on the risk assessment findings, employers must implement appropriate control measures to prevent or minimise employee exposure to hazardous substances.
Employers must ensure that employees are well-informed and adequately trained about the hazards they may encounter and the measures in place to protect them. This includes providing them with detailed information about hazardous substances, including safety data sheets (SDS) and appropriate labelling and signage. Employers must also give clear instructions on safe handling, storage and disposal of hazardous substances.
It is also recommended to conduct regular training sessions to educate employees on recognising hazards and understanding risks, the proper use and maintenance of control measures, including PPE, safe work practices and emergency procedures, first aid and incident reporting.
Regular monitoring and review of control measures are essential to ensure their continued effectiveness and to make necessary adjustments. Employers must:
- Monitor exposure levels: This includes conducting air sampling, biological monitoring and other relevant tests to measure employees’ exposure to hazardous substances.
- Implement health surveillance: Employers must implement health surveillance programmes for employees at risk, such as regular medical examinations and health checks.
- Review control measures: It is necessary to periodically review risk assessments and control measures to ensure they remain effective. This review should also occur whenever there are changes in processes or substances used or if new information about a substance’s hazards becomes available.
- Maintain record-keeping: Workplaces are required to maintain accurate records of risk assessments, control measures, monitoring results and health surveillance data. These records should be accessible to employees and regulatory authorities.
By fulfilling these responsibilities, employers can create a safer working environment, reduce the risk of occupational illnesses and injuries and comply with COSHH regulations. This proactive approach to managing hazardous substances is necessary to protect employees’ health and ensure workplace safety.
Key Components of COSHH Assessments
The first step in the COSHH assessment process is to identify all hazardous substances that are used or generated in the workplace. To do this, it is recommended to create an inventory that lists all the chemicals, materials and substances that are present in the workplace. This includes substances used in production, maintenance, cleaning and any other work processes.
Employers should also review the safety data sheets (SDS) provided by suppliers to understand the properties and hazards of each substance. It is also necessary to identify any hazardous substances that may be produced as by-products or waste during work processes, such as fumes, dust or residues.
Once the hazardous substances are identified, the next step is to evaluate the risks associated with their use. This involves:
- Assessing exposure scenarios: It is necessary to determine how employees might be exposed to each substance, considering factors like inhalation, skin contact, ingestion and eye exposure.
- Estimating exposure levels: Employers should evaluate the intensity, frequency and duration of exposure. This may involve air monitoring, sampling and analysis.
- Understanding health effects: It is necessary to review the potential health effects of each substance, including acute and chronic effects, such as irritation, sensitisation, toxicity, carcinogenicity and reproductive harm.
- Identifying vulnerable workers: Consider any employees who may be more susceptible to certain substances, such as pregnant women, young workers or those with pre-existing health conditions.
After evaluating the risks, appropriate control measures must be implemented to eliminate or minimise exposure. These measures follow the hierarchy of controls:
Substitution
Replace hazardous substances with less harmful alternatives where possible. For example, using a water-based paint instead of a solvent-based one.
Engineering controls
Implement physical controls to reduce exposure. Examples include:
- Ventilation systems: This could include installing local exhaust ventilation (LEV) to capture and remove airborne contaminants at the source.
- Enclosures and isolation: Use closed systems or isolating processes to prevent exposure.
Administrative controls
Change work practices and procedures to reduce risks. Examples include:
- Safe work procedures: Develop and enforce procedures for the safe handling, storage and disposal of hazardous substances.
- Work schedules: Organise work to minimise the number of employees exposed and the duration of exposure.
- Training and education: Provide ongoing training and information to employees about the hazards and control measures.
Personal Protective Equipment (PPE)
Provide and ensure the proper use of PPE when other controls are insufficient to reduce exposure to safe levels. Examples include:
- Respirators: For protection against inhalation of hazardous substances.
- Gloves and protective clothing: To prevent skin contact.
- Safety goggles: To protect the eyes from splashes and fumes.
The final step in the COSHH assessment process is to document the findings and ensure they are accessible to employees. It is necessary for employers to document the details of the risk assessments, including identified hazards, evaluation of risks and implemented control measures. They should also ensure that the risk assessment records are easily accessible to all employees. This may involve keeping digital records on a shared drive or physical copies in a central location.
Employers must also inform employees about the findings of the risk assessments and the control measures in place. This can be done through safety meetings, training sessions and posting information in common areas. Regular reviews and updates to the risk assessments and control measures are required, especially when there are changes in work processes, new substances are introduced or if there is evidence that current controls are not effective.
By following these key components of COSHH assessments, employers can effectively manage hazardous substances in the workplace, ensure the health and safety of their employees and maintain compliance with regulatory requirements.
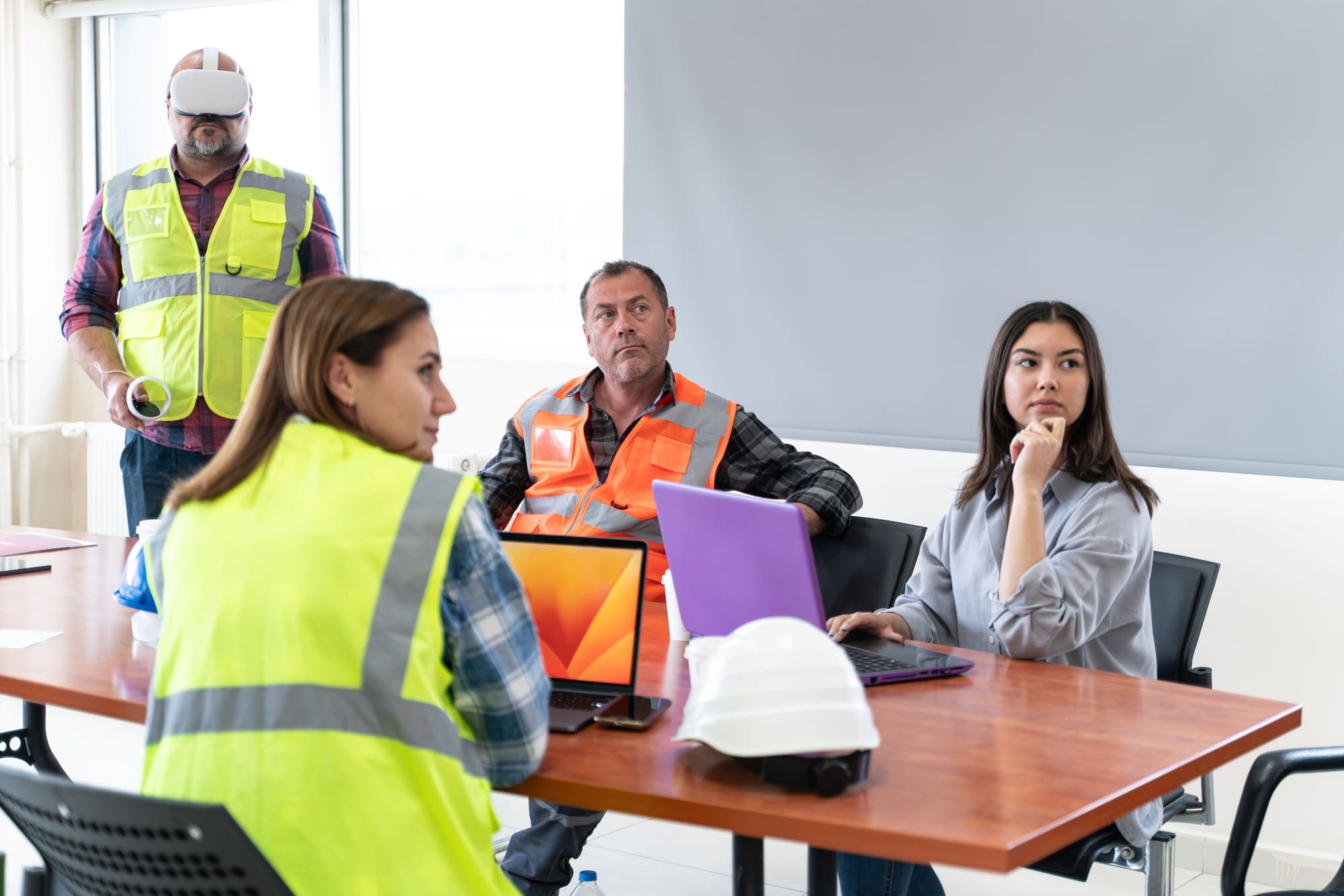
Importance of COSHH in Promoting Safety
Adhering to the COSHH regulations is essential for creating a safe and healthy workplace. The benefits of following COSHH guidelines extend beyond compliance and significantly impact both employees and the organisation as a whole.
There are many possible benefits to COSHH, including:
Reduces the risk of occupational illnesses and injuries
By effectively managing and controlling exposure to hazardous substances, there is likely to be a reduction in occupational illnesses and injuries caused by hazardous substances. By effectively managing and controlling exposure to hazardous substances, employers can prevent acute health issues, including immediate health problems such as chemical burns, respiratory distress and skin irritations and lower the risk of long-term health issues, such as occupational asthma, dermatitis, lung cancer and neurological disorders. COSHH can improve employees’ general health and well-being by reducing their exposure to harmful agents which can result in fewer sick days and better overall productivity.
Improved workplace safety culture and morale
Implementing COSHH regulations can create a positive safety culture within the workplace which can significantly improve employee morale. This cultural shift can be achieved by:
- Demonstrating commitment to safety: Showing employees that their health and safety are a top priority can increase their trust and confidence in the organisation.
- Encouraging participation: Involving employees in safety assessments and training can boost their engagement and commitment to maintaining a safe working environment.
- Improving communication: Promoting open communication about health and safety issues can lead to quicker identification and resolution of potential hazards.
- Increasing job satisfaction: Creating a safer work environment can lead to higher job satisfaction, reduced staff turnover and better recruitment and retention of talent.
Compliance with legal requirements
Adhering to COSHH regulations is not only beneficial for health and safety but is also a legal requirement. Compliance with these regulations helps organisations to:
- Avoid legal penalties: Compliance with COSHH prevents businesses and employers from receiving fines, sanctions and other legal consequences that can arise from non-compliance with health and safety laws.
- Reduce legal liabilities: Adhering to regulations minimises the risk of legal action from employees who might suffer from work-related illnesses or injuries due to inadequate control measures.
- Maintain reputation: Compliance protects the organisation’s reputation by demonstrating a commitment to legal and ethical standards in health and safety practices.
- Ensure operational continuity: Compliance helps employers avoid disruptions to business operations that can result from workplace accidents, health investigations or enforcement actions.
Training and Awareness
Training and awareness are critical components of the COSHH regulations. Proper training ensures that employees are knowledgeable about the hazardous substances they may encounter in the workplace and understand how to handle these substances safely. This not only protects the health and safety of employees but also enhances overall workplace safety and compliance with legal requirements.
As part of a COSHH training programme, employees need to learn how to recognise hazardous substances and the associated risks. This includes being able to read and understand labels, safety data sheets (SDS) and hazard symbols. Training should also cover the specific risks associated with each hazardous substance, including short-term and long-term health effects. Employees should understand how these substances can enter the body (e.g., inhalation, ingestion and skin contact) and the symptoms of exposure. Employees should know where hazardous substances are stored and used within the workplace. This knowledge helps them to avoid accidental exposure and to take necessary precautions when working in these areas.
Training must also cover understanding control measures and safe working practices and should emphasise the hierarchy of controls, which includes elimination, substitution, engineering controls, administrative controls and personal protective equipment (PPE). Employees should understand the rationale behind each control measure and how it reduces risk. Employees must be trained on the correct use, maintenance and limitations of personal protective equipment. This includes how to properly fit and wear PPE, as well as how to inspect it for damage.
Training should include safe handling, storage and disposal procedures for hazardous substances. This helps prevent accidental spills, leaks and other incidents. Employees should be taught safe working practices specific to their roles, such as proper ventilation techniques, use of fume hoods and safe methods for mixing and transferring chemicals.
Another important aspect of COSHH training programmes is emergency response. Employees must be trained on the specific emergency procedures for dealing with hazardous substance incidents, such as spills, leaks and accidental exposure. This includes knowing the location of emergency equipment (e.g. eyewash stations and spill kits) and how to use it. Training should cover the workplace’s evacuation procedures in the event of a serious incident involving hazardous substances. Employees need to know the designated evacuation routes and assembly points.
Employees should be familiar with the first aid measures for exposure to hazardous substances, such as flushing eyes with water, washing skin and administering first aid for inhalation or ingestion. Training should also cover when and how to seek medical attention. Additionally, employees must know the protocol for reporting incidents involving hazardous substances. This includes who to notify, what information to provide and how to document the incident.
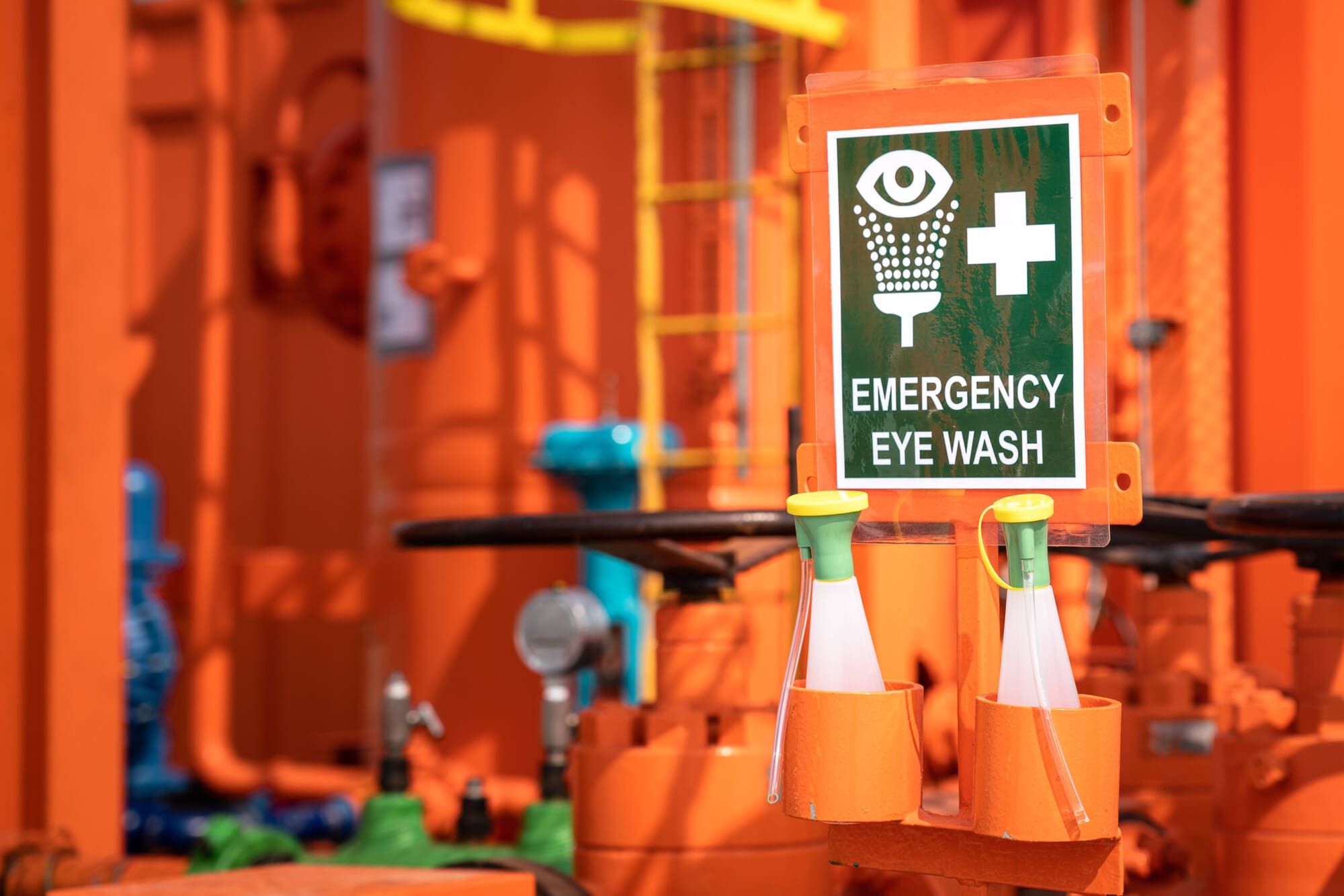
Case Studies
Case Study 1: Manufacturing Industry – Reducing Exposure to Solvent
A manufacturing company specialising in automotive parts used solvents extensively in their cleaning and degreasing processes. Employees reported frequent headaches, dizziness and respiratory issues, which were traced back to solvent exposure.
To comply with COSHH regulations, the company undertook a detailed risk assessment to identify the hazardous solvents involved and evaluate the levels of exposure. Based on the findings, the company implemented several key measures. Where possible, hazardous solvents were substituted with less harmful, water-based cleaning agents. Additionally, local exhaust ventilation systems were installed at workstations to capture solvent fumes directly at the source. Work processes were adjusted to reduce the duration of exposure and employees were rotated between tasks to minimise time spent in high-exposure areas. Personal protective equipment (PPE), including gloves and respirators, was provided and training on their proper use was conducted.
The implementation of these measures led to a significant reduction in reports of headaches, dizziness and respiratory issues among employees. The company achieved compliance with COSHH regulations and improved its overall safety record. This proactive approach also resulted in increased employee satisfaction and morale, demonstrating the benefits of effective COSHH management.
Case Study 2: Construction Industry – Managing Silica Dust
A construction company engaged in road and building projects faced serious challenges with silica dust exposure, particularly from cutting, drilling and grinding concrete and stone. Silica dust posed a significant health risk to workers, necessitating a robust response to manage these hazards.
The company conducted thorough risk assessments to identify tasks generating high levels of silica dust and evaluated the associated exposure risks. To address these risks, the company explored alternative materials with lower silica content, though complete substitution was not always possible. Engineering controls were introduced, including wet-cutting techniques to reduce dust generation and on-tool extraction systems to capture dust at the source. Work schedules were adjusted to limit the duration workers spent on high-risk tasks and regular breaks were incorporated to further reduce continuous exposure. PPE, including high-efficiency respiratory protective equipment, was provided with training on its proper use and maintenance.
The implementation of these control measures led to a significant reduction in airborne silica dust and a corresponding decrease in respiratory complaints and long-term health risks among workers. The company maintained compliance with COSHH regulations and avoided potential fines and legal issues. Additionally, the company’s commitment to worker safety enhanced its reputation within the industry and among potential clients.
Case Study 3: Laboratory Environment – Controlling Biological Hazards
In a research laboratory dealing with various biological agents, including bacteria and viruses, there was a need to manage the risks associated with these hazardous substances to ensure the safety of laboratory personnel.
The laboratory started by conducting a detailed risk assessment to identify all biological agents used and evaluate the associated risks, such as infection and allergic reactions. To address these risks, biological safety cabinets (BSCs) were installed to provide containment when handling pathogens. Advanced ventilation systems were also implemented to ensure proper air filtration and reduce the risk of airborne contaminants.
Strict protocols were established for the handling and disposal of biological agents, with regular audits and inspections to ensure compliance. Personnel were provided with appropriate PPE, including gloves, lab coats, face shields and respirators and received mandatory training on the correct use of this equipment. Additionally, regular health check-ups and immunisations were offered to employees to ensure early detection and prevention of potential infections.
These measures resulted in enhanced safety and minimised exposure to hazardous biological agents. Regular health surveillance and immunisations contributed to the early detection and prevention of infections, ensuring the well-being of laboratory personnel. The laboratory maintained full compliance with COSHH regulations, met the industry standards and avoided legal repercussions. Effective management of biological hazards also ensured uninterrupted research activities and created a culture of safety within the laboratory.
Conclusion
The COSHH regulations play a pivotal role in ensuring workplace safety and protecting employees’ health. By mandating the systematic identification, assessment and management of hazardous substances, COSHH helps prevent a wide range of occupational illnesses and injuries. The primary goal of COSHH is to safeguard employees from the harmful effects of substances that could potentially lead to serious health issues, from acute reactions, including chemical burns, to chronic conditions, such as respiratory diseases or cancer.
Adhering to COSHH regulations has numerous benefits, including a significant reduction in workplace accidents and health complaints, improved safety culture and compliance with legal requirements, thus avoiding fines and legal liabilities. These regulations help create a safer work environment where employees can perform their duties without undue risk to their health, ultimately enhancing overall productivity and job satisfaction.
Ensuring workplace safety through COSHH is not a one-time effort but an ongoing commitment. Regular monitoring and reviewing of control measures are essential to adapt to changes in the workplace environment, new substances and evolving regulations. Continuous improvement of COSHH practices, informed by feedback, incident reports and advances in safety technology, is important for maintaining a safe and healthy workplace.
An effective COSHH management system is dynamic and responsive, integrating regular updates, training and revisions of safety protocols. This ongoing vigilance ensures that safety standards are not only met but exceeded and creates a culture of proactive safety and continual improvement. COSHH regulations are fundamental to maintaining workplace safety and protecting the health of employees. The commitment to regularly reviewing and enhancing COSHH practices is essential for creating a safe working environment and ensuring the well-being of all employees.