In this article
Manufacturing processes often involve chemicals, solvents, dust, fumes and vapours that can be harmful if inhaled, ingested, or if they come into contact with the skin. Examples include welding fumes, asbestos and industrial chemicals.
Prolonged exposure to hazardous substances can lead to chronic conditions such as respiratory diseases, skin conditions, cancer and reproductive issues.
The Control of Substances Hazardous to Health (COSHH) Regulations are a critical framework designed to protect workers from the harmful effects of exposure to hazardous substances. In manufacturing units, the use of chemicals, solvents, dust and other potentially harmful materials is common.
The implementation of COSHH standards is essential for ensuring a safe and compliant working environment. Proper adherence to COSHH Regulations not only helps mitigate health risks but also supports the overall productivity and sustainability of manufacturing operations.
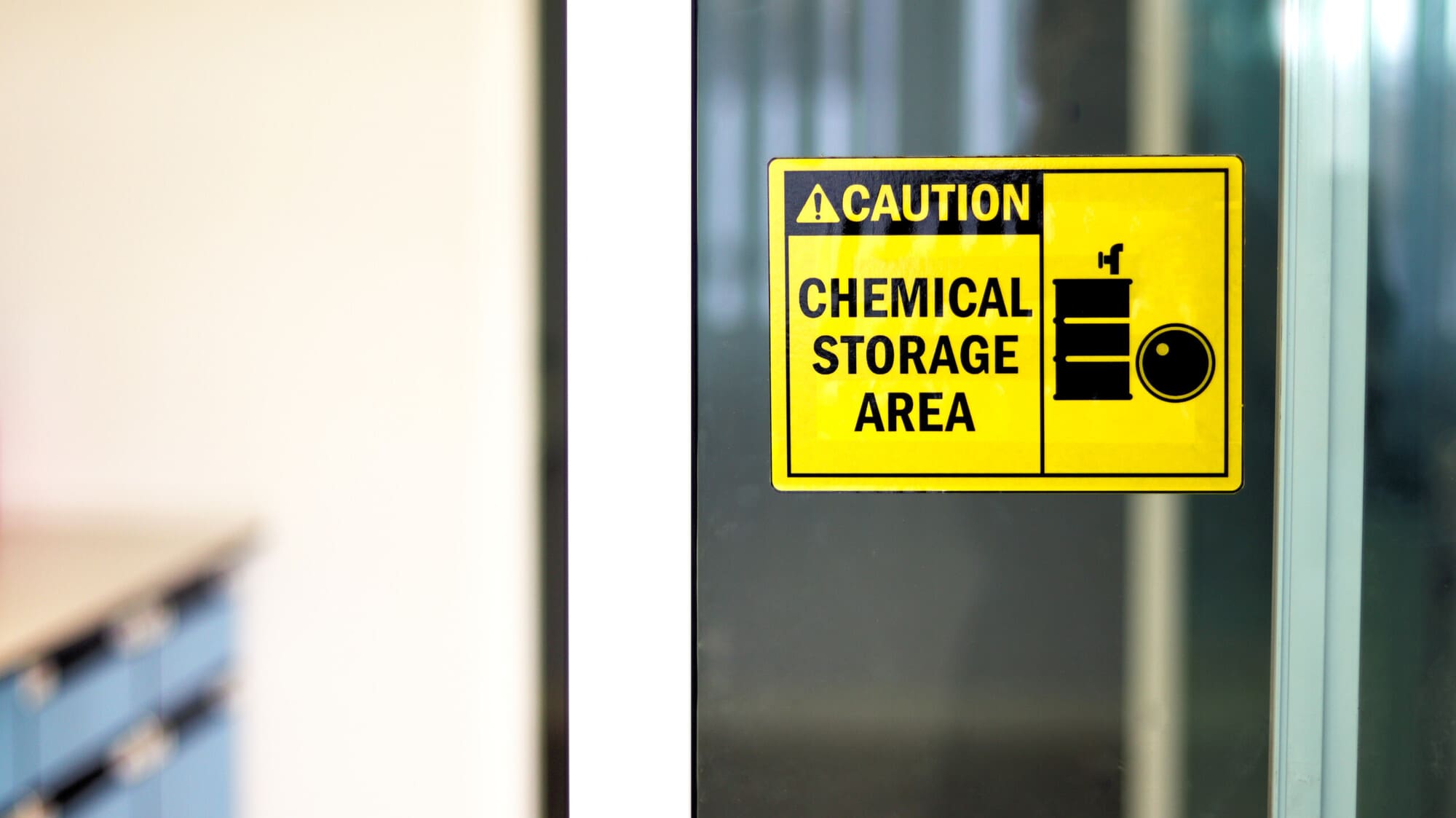
Case Study Overview
The subject of this case study is SkyeZ Manufacturing Ltd, a mid-sized UK-based company specialising in the production of industrial machinery. Established in 1998, the company has grown to employ over 500 workers across multiple departments, including metalworking, assembly, painting and maintenance. The company’s commitment to quality and innovation has helped it secure a strong position in its sector, but as operations expanded, so did the need to manage potential health risks associated with hazardous substances.
SkyeZ Manufacturing operates within the metal fabrication and engineering sector, producing heavy-duty machinery for industries such as construction, mining and automotive. This sector requires the use of various chemicals, solvents and materials, which present potential health hazards to employees. The company routinely handles substances like welding fumes, cutting oils, degreasers and paints, some of which contain harmful chemicals such as lead, chromium and volatile organic compounds (VOCs).
Within SkyeZ Manufacturing, hazardous substances are handled in several processes:
- Welding and metal cutting – exposing workers to fumes containing hazardous particulates and gases.
- Surface treatment and painting – requiring the use of chemicals, including solvents and metal cleaning agents.
- Machinery maintenance – involving lubricants and oils that may contain carcinogens or other harmful substances.
With such a diverse array of potential hazards, implementing COSHH standards was crucial for ensuring worker safety and regulatory compliance.
Implementation of COSHH Standards
Risk Assessment
A risk assessment in manufacturing is a systematic process used to identify, evaluate and prioritise potential risks associated with manufacturing operations. The goal is to minimise or eliminate the likelihood of accidents, failures or disruptions that could affect safety, quality or productivity. The process helps ensure a safer working environment, compliance with regulatory requirements, and overall operational efficiency.
To comply with COSHH Regulations, SkyeZ Manufacturing initiated a comprehensive risk assessment to identify all hazardous substances present in its operations. This process involved several key steps:
Inventory of hazardous substances
The company catalogued all chemicals and substances used in its processes. Each substance was evaluated based on its safety data sheets (SDS), which provide detailed information on health risks and safe handling procedures.
Health risk evaluation
The risk to workers’ health was assessed by analysing how substances were used and the likelihood of exposure. Factors considered included frequency and duration of exposure, routes of exposure (inhalation, skin contact and ingestion), the concentration and toxicity of the substances, worker groups at risk, and risk grading. SkyeZ used a grading system to classify risks based on the severity of health outcomes, e.g. respiratory diseases or skin conditions, and the likelihood of exposure. High-risk areas were prioritised for intervention.
Control Measures
Control measures are actions or strategies implemented to manage, reduce or eliminate risks or hazards. The effectiveness of control measures depends on proper implementation and regular review to adapt to new risks or changes in the environment.
Once risks were identified, SkyeZ Manufacturing implemented a series of control measures designed to minimise exposure to hazardous substances. The approach followed the hierarchy of control principle, focusing on the most effective methods first. Engineering controls were physical changes to the workplace or processes aimed to reduce exposure at the source. Examples include:
- Ventilation systems – local exhaust ventilation (LEV) systems were installed in welding and metal cutting areas to capture fumes at the source, preventing workers from inhaling dangerous particulates.
- Closed systems – solvent use in painting and cleaning processes was shifted to closed systems, minimising evaporation and airborne VOCs.
- Automated machinery – in some high-risk operations, manual processes were replaced with automated or remote-controlled systems to limit direct worker exposure.
- Administrative controls – these included changes to work practices and operational procedures.
- Workplace scheduling – tasks that involved hazardous substances were scheduled during times when fewer workers were present to minimise potential exposure.
- Work area zoning – designated “hazard zones” were created, limiting access to areas where hazardous substances were being used or produced.
- Safe work procedures – standard operating procedures (SOPs) were developed for each hazardous process, specifying how substances should be handled and stored safely.
- Personal Protective Equipment (PPE) – where risks could not be fully eliminated by engineering or administrative controls, PPE was provided to employees. This included Respiratory Protective Equipment (RPE); high-efficiency masks and respirators were distributed to workers in welding, painting and chemical-handling areas. Workers handling chemicals were provided with chemical-resistant suits, gloves and eye protection. The company established protocols for the regular inspection and replacement of PPE to ensure it was effective.
Training and Education
Training is crucial in manufacturing for several reasons:
- Safety – proper training ensures that employees are aware of safety protocols and how to handle equipment safely, which reduces the risk of accidents and injuries.
- Efficiency – well-trained workers can operate machinery and complete tasks more effectively, leading to higher productivity and better use of resources.
- Quality control – training helps employees understand quality standards and procedures, which helps maintain product consistency and meet customer expectations.
- Adaptability – manufacturing processes and technologies are constantly evolving. Training helps employees stay up to date with new systems, tools and methods, allowing them to adapt quickly.
- Employee retention – investing in training demonstrates a commitment to employee development, which can improve job satisfaction and reduce turnover.
- Compliance – training ensures that employees are aware of and adhere to regulatory and industry standards, helping avoid legal issues and fines.
Training was a core component of SkyeZ Manufacturing’s COSHH implementation strategy. The company developed and delivered a series of training programmes to ensure that workers were well informed about the risks they faced and how to mitigate them.
All employees received mandatory training on COSHH Regulations, including understanding the hazards associated with the substances they worked with and how to read safety data sheets.
Workers were trained in the proper use and disposal of hazardous substances, with hands-on demonstrations and simulations. Employees were also provided with instructions on how to correctly wear, maintain and store personal protective equipment. This training emphasised the importance of consistent use and the risks of non-compliance.
Refresher courses were scheduled regularly to keep workers up to date on new safety practices, emerging risks and changes in COSHH Regulations.
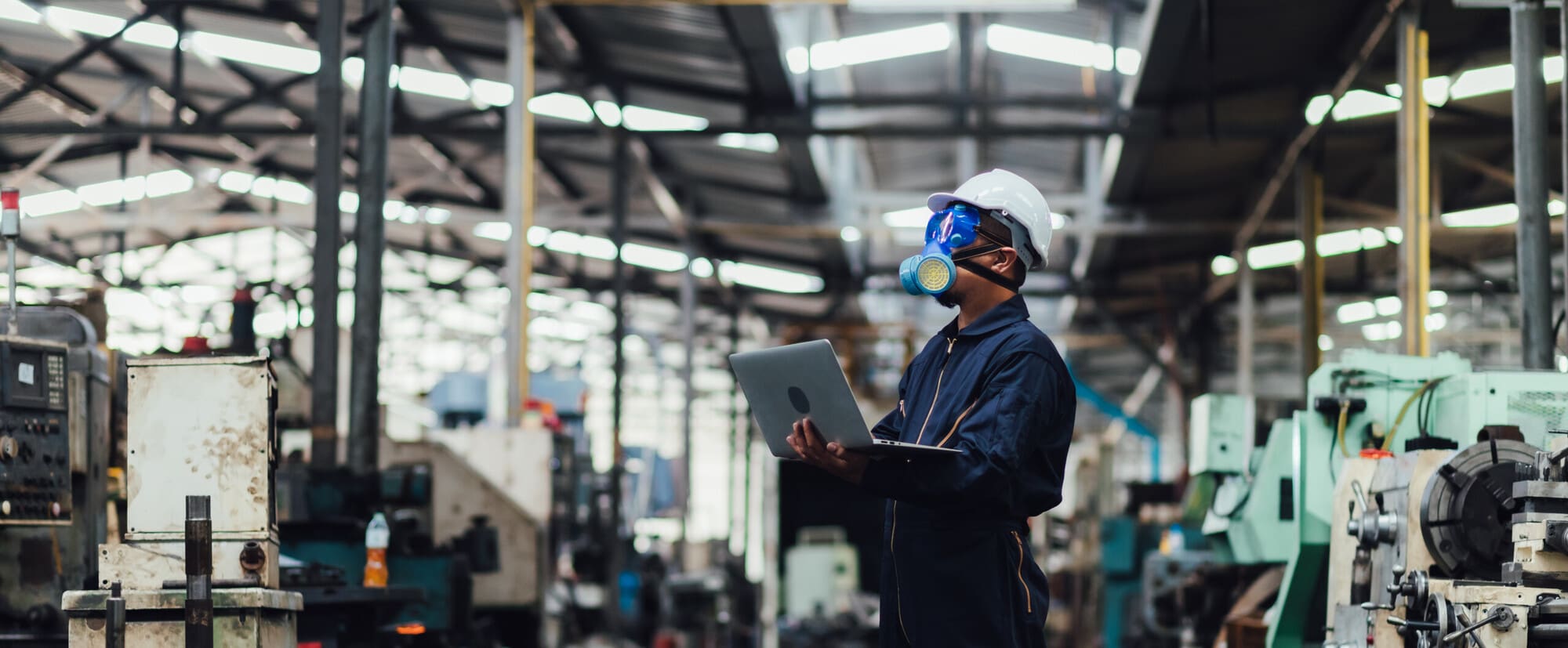
Monitoring and Review
Ensuring that COSHH standards are met helps to comply with legal requirements. This compliance protects organisations from legal repercussions and potential fines.
Regular reviews help to minimise the risk of exposure to hazardous substances, safeguarding the health and safety of employees. This can prevent accidents, illnesses and long-term health issues related to exposure. Continuous monitoring allows for the identification and mitigation of potential hazards before they result in incidents. This proactive approach helps manage risks effectively.
Monitoring helps to identify areas where controls may be insufficient or outdated. This enables organisations to make necessary improvements and adapt to new safety standards or changes in regulations. By regularly reviewing procedures and controls, organisations can prevent incidents related to hazardous substances, reducing the likelihood of accidents and ensuring a safer working environment.
Monitoring and reviewing can highlight the need for additional training or awareness among employees regarding the safe handling and use of hazardous substances. It is important to keep up-to-date records of compliance and monitoring, demonstrating adherence to COSHH Regulations and for auditing purposes.
SkyeZ Manufacturing implemented a robust monitoring system to ensure ongoing compliance with COSHH standards and evaluate the effectiveness of control measures. This process included:
- Routine inspections – safety officers conducted regular inspections of work areas to ensure that engineering controls, administrative measures and PPE were being used properly.
- Air quality monitoring – the company invested in air quality monitoring systems to continuously assess levels of airborne contaminants such as welding fumes and VOCs.
- Health surveillance – workers exposed to hazardous substances were enrolled in a health surveillance programme, which included regular medical examinations and monitoring for signs of occupational illnesses.
- Annual COSHH review – management held annual reviews to assess the effectiveness of COSHH implementation, making adjustments to control measures as necessary and incorporating employee feedback.
Benefits and Outcomes
Improved Safety
The implementation of COSHH standards at SkyeZ Manufacturing has significantly improved workplace safety. Since adopting these measures, the company has reported a 40% reduction in workplace incidents related to hazardous substances.
The introduction of advanced engineering controls, coupled with rigorous safety protocols, has minimised exposure to harmful fumes, chemicals and dust, creating a safer environment for workers across all departments.
Regulatory Compliance
By fully aligning its operations with COSHH Regulations, SkyeZ Manufacturing has ensured compliance with UK health and safety laws. This has allowed the company to avoid legal penalties and maintain a positive relationship with regulators. The company’s commitment to health and safety has also been recognised with several industry safety certifications.
If a manufacturing company does not comply with Control of Substances Hazardous to Health (COSHH) standards, several negative consequences can occur:
- Legal penalties – the company could face legal action from regulatory bodies, such as the Health and Safety Executive (HSE). This could result in fines, sanctions or even criminal charges, depending on the severity of the non-compliance.
- Health risks – employees may be exposed to hazardous substances, which can lead to health issues such as respiratory problems, skin conditions or other serious illnesses. Non-compliance increases the risk of accidents and long-term health problems.
- Workplace accidents – improper handling of hazardous substances can result in workplace accidents, which could lead to injuries, damage to property or even fatalities.
- Reputational damage – a company’s reputation can suffer if it is known for failing to comply with health and safety standards. This can affect relationships with clients, customers and potential employees.
- Increased insurance costs – non-compliance can lead to higher insurance premiums or difficulties obtaining insurance coverage.
- Operational disruptions – investigations, legal proceedings or accidents resulting from non-compliance can disrupt normal operations and affect productivity.
- Loss of certification or contracts – non-compliance may result in the loss of certifications required for certain contracts or industries, impacting the company’s ability to do business.
Employee Engagement
The implementation of COSHH standards has had a positive impact on employee morale and engagement. Workers report feeling safer and more valued in their roles, knowing that their employer is taking significant steps to protect their health. This has contributed to a culture of safety within the company, with employees more actively participating in safety programmes and initiatives.
Challenges and Solutions
Initial Challenges
During the initial phase of implementation, SkyeZ Manufacturing faced several challenges:
- Resistance to change – some workers were hesitant to adopt new safety procedures and use PPE consistently, citing discomfort or inconvenience.
- High costs – installing engineering controls and upgrading ventilation systems required significant financial investment.
- Complex risk assessment – identifying and evaluating the wide range of hazardous substances used across various departments was a time-consuming and complex task.
Solutions
SkyeZ Manufacturing overcame these challenges through a combination of strategic planning and stakeholder engagement.
The company launched an employee engagement programme to foster a culture of safety, encouraging workers to provide feedback on the COSHH measures and participate in decision-making processes related to safety. To manage costs, the company adopted a phased approach to implementing expensive engineering controls, starting with high-risk areas and expanding over time.
The company worked with external health and safety consultants to streamline the risk assessment process and ensure all hazards were accurately identified.
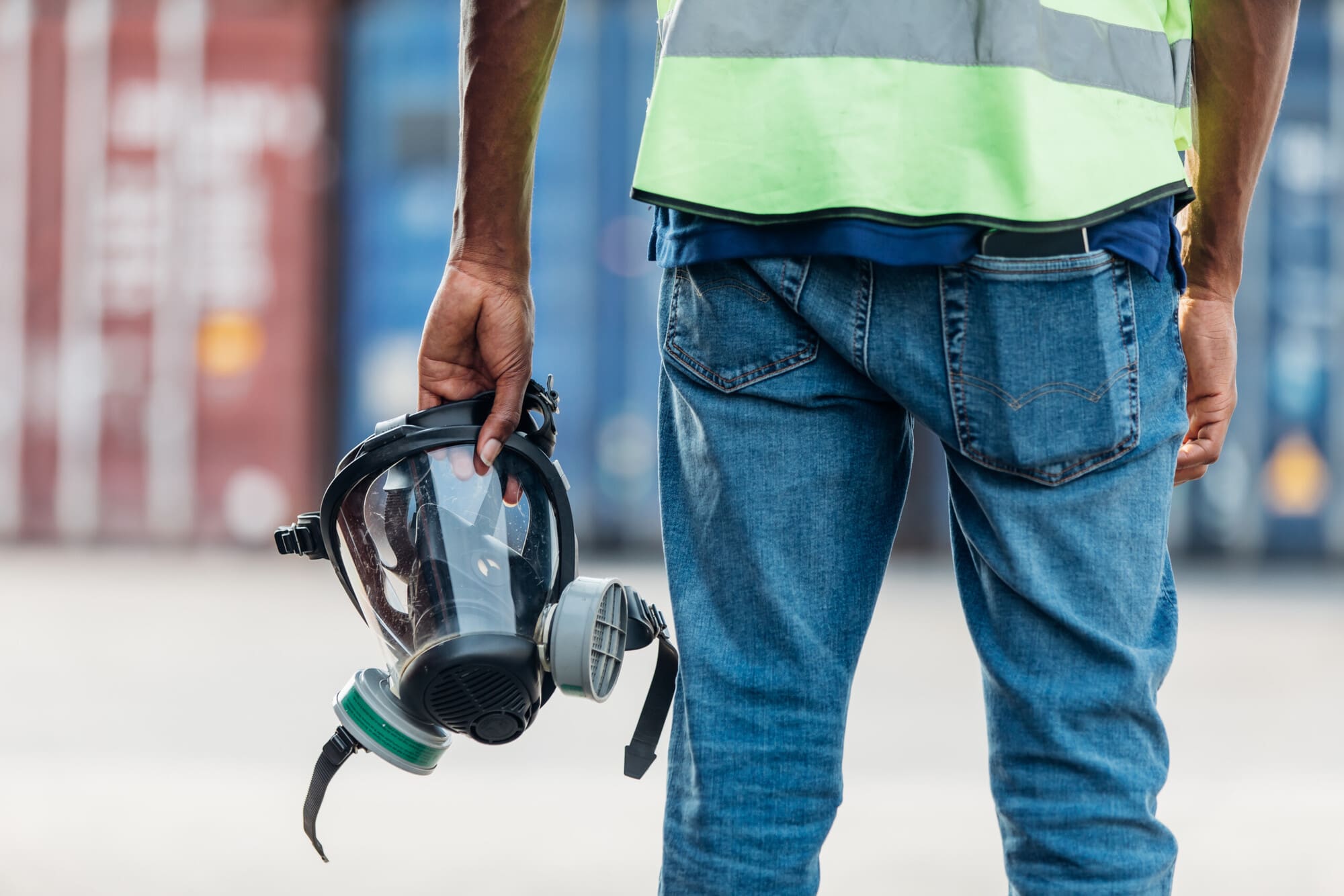
Conclusion
Implementing COSHH standards in manufacturing units is vital for ensuring the safety and well-being of employees and maintaining a compliant and efficient working environment. By identifying hazardous substances, assessing risks and enforcing preventive control measures, manufacturing units can significantly reduce workplace incidents and long-term health issues. Proper training, regular monitoring and continuous improvement of safety protocols are key to sustaining these standards.
Ultimately, adherence to COSHH Regulations not only protects workers but also enhances operational efficiency, productivity and legal compliance within the industry.