In this article
The air we breathe is not always clean and safe. Certain work activities can produce hazardous substances that can contaminate the air and then be breathed in by workers and others in the vicinity. Oxygen levels can also fall dangerously low when working in some types of areas, such as confined spaces.
The inhalation of hazardous substances and oxygen depletion can have many adverse health effects (acute and chronic). In some cases, it can result in disabling ill health and even fatalities.
The Health and Safety Executive’s (HSE) latest statistics highlight the seriousness of the problem and found that:
- 13,000 deaths each year are estimated to be linked to past exposure at work, primarily to chemicals or dust.
- 12,000 lung disease deaths each year are estimated to be linked to past exposures at work, which included:
– Chronic obstructive pulmonary disease (COPD).
– Non-asbestos-related lung cancer.
– Asbestos-related lung cancer.
– Mesothelioma.
– Other lung diseases. - 17,000 estimated annual new cases of self-reported breathing or lung problems were caused or made worse by work.
Respiratory protective equipment (RPE) protects workers from inhaling hazardous substances and being exposed to low oxygen levels. In this article, you will look at RPE in further detail, the types, and selection. You will also look at the different respiratory hazards to which workers could be exposed.
What is RPE?
HSG53 (Respiratory protective equipment at work: A practical guide) definition of RPE is:
“A particular type of personal protective equipment (PPE) designed to protect the wearer from breathing in harmful substances or from oxygen-deficient atmospheres when other controls are either not possible or insufficient on their own.”
Workers can be exposed to many different airborne hazardous substances, and the risk will depend on the work activities and environment. Whether RPE is worn will depend on the risk assessment findings and whether other precautions can prevent and control exposure, e.g. engineering controls.
Some examples of industries/work where RPE may be used are (this list is not exhaustive):
- Construction – Workers in the construction industry can be exposed to many different airborne contaminants, e.g. asbestos and silica from concrete.
- Agriculture – Agricultural workers can be exposed to airborne hazardous substances, such as grain dust, pesticide and herbicide spraying, poultry dust and fungal spores.
- Healthcare – Those working in healthcare can be exposed to biological agents, e.g. viruses, transmitted via the air. They also use different chemicals and drugs that can become airborne.
- Woodworking – Workers working in woodworking can be exposed to wood dust. However, this should be controlled by other means first, e.g. extraction.
- Tradesmen – Those who are self-employed and do jobs such as plastering, carpentry, building works and insulation installation can be exposed to many hazardous substances, e.g. asbestos, plaster, insulation fibres and cement.
- Paint spraying – Workers who spray paint, e.g. on vehicles, can be exposed to different chemicals, such as solvents.
- Confined space work – Anyone working in a confined space can be exposed to hazardous substances, and there is also a risk of oxygen depletion.
It can also include animal workers, bakers, solderers, welders and engineers. Any jobs where individuals are at risk of exposure to airborne hazardous substances will need to consider the use of RPE in their risk assessments.
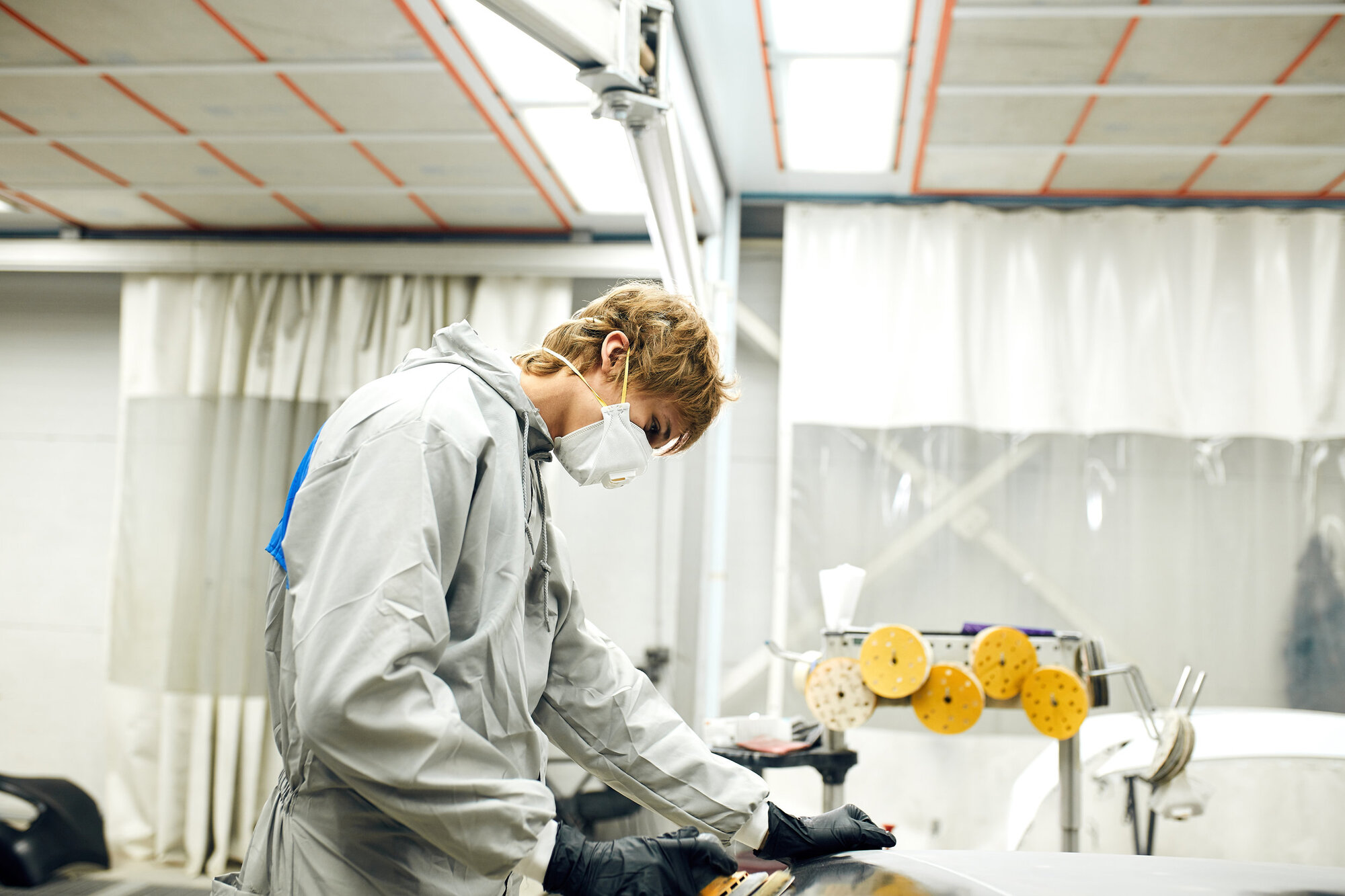
Applicable laws
General legislation will apply to the risk of exposure to hazardous substances and low oxygen environments, e.g. the Health and Safety at Work etc. Act 1974 and the Management of Health and Safety at Work Regulations 1999 require employers to provide and maintain a safe working environment.
The main law relating to airborne contaminants and RPE is the Control of Substances Hazardous to Health Regulations 2002. There may be other applicable laws relating to specific hazardous substances and work activities, e.g. asbestos, lead, ionising radiation and confined spaces.
The Personal Protective Equipment at Work Regulations 1992 may also apply if the RPE is not covered by COSHH or other specific legislation.
Controlling respiratory hazards
A respiratory hazard is something with the potential to cause harm to the respiratory system, as it can be inhaled through the nose and mouth, into the lungs, and can cause damage.
Some examples of respiratory hazards include:
- Dust, e.g. concrete, stone, wood, grain, flour, asbestos and animal dander.
- Smoke, e.g. surgical.
- Fume, e.g. welding, lead and engine exhaust fumes.
- Gas, e.g. carbon dioxide and nitrogen that displace oxygen. Some gases are also toxic, such as carbon monoxide and chlorine.
- Mist, e.g. oils, cutting fluids and acid.
- Fine sprays, e.g. paints and pesticides.
- Vapour, e.g. solvents.
- Biological agents, e.g. spores, parasites and microorganisms.
- Fibres, e.g. asbestos and fibreglass insulation.
- Working in areas where oxygen levels can be low, e.g. working in confined spaces, such as a sewer or tank.
Inhalation is a common route of entry for hazardous substances. The likelihood of inhaling a substance will depend on the form, e.g. dust, fume, mist and vapour are easily inhaled. The particle size also affects the risk of inhalation. The smaller the particle, the easier it will be to inhale it deep into the lungs, and the more damage it will cause.
Once hazardous substances have been inhaled, it can cause effects such as:
- Respiratory cancers, including lung, nasal and mesothelioma.
- Chronic obstructive pulmonary disease (COPD).
- Respiratory irritation.
- Occupational asthma.
- Pneumoconiosis, e.g. silicosis and asbestosis.
- Diffuse pleural thickening and pleural plaques.
- Allergic alveolitis and byssinosis.
- Damage to other organs and the nervous system.
Exposure can result in short-term effects. However, if a person is exposed to certain hazardous substances over time, it can cause life-changing debilitating symptoms and, in some cases, death.
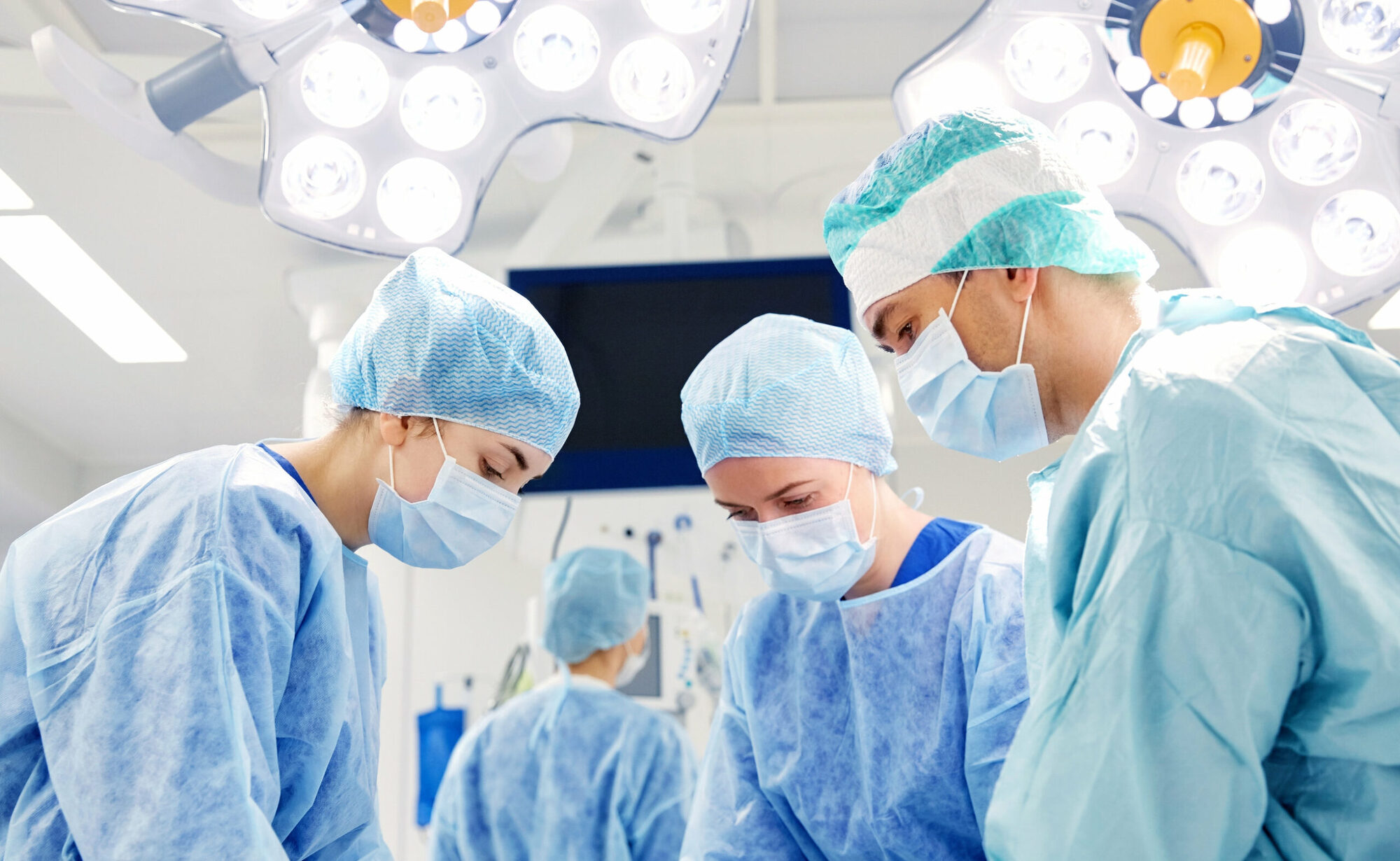
What are the different types of RPE?
There are two main types of RPE, which are:
- Respirators (air purifying) – Also known as filtering devices. They remove contaminants from the air using filters and can be powered or non-powered.
- Breathing apparatus – This type of RPE provides an independent supply of air to the wearer, e.g. from a cylinder or compressor. Typically used in confined spaces when there is a risk of oxygen depletion.
Respirators and breathing apparatus are divided into two main groups:
Tight-fitting face pieces
- Also known as masks.
- There needs to be a tight seal on the wearer’s face.
- Can be powered, non-powered or breathing apparatus.
- The wearer must be face-fit tested.
Loose-fitting face pieces
- Clean air is provided to the wearer.
- Can be powered or breathing apparatus.
- Examples are hoods, helmets, visors, blouses and suits.
There are two basic types of RPE filters, which are:
- Particle – Protects against particles, such as dust.
- Gas/vapour – Protects against gas and vapour, such as solvents.
For RPE to be effective, the correct filters must be used, i.e. those for particles will not protect against gas/vapour and vice versa, although there are combination filters available that can protect against both. These filters should not be used where there is a risk of oxygen deficiency.
Wearers must change the filters frequently for the RPE to offer maximum protection. The manufacturer should provide instructions on when and how to change RPE filters. Some also have expiry dates marked on the actual filter.
There are colour codes on some RPE filters to indicate the level of protection and the substances it protects against, e.g. P = particles (white). There are also classes, e.g. 1 (low), 2 (medium) & 3 (high), which is the capacity of the specified contaminant the filters can hold. Appendix 2 in HSG53 has further guidance on filters.
Respirators | |
Half masks | Can be disposable or reusable.Covers the mouth and nose.Filters can be particle or gas/vapour.Filters will need to be changed for some reusable masks. |
Full face mask | Reusable masks.Covers the mouth, nose and eyes.Filters can be particle or gas/vapour.Filters will need to be changed. |
Powered | Reusable masks or hoods/helmets.Covers the mouth, nose and eyes or head (hoods & helmets).Attached to a motor power pack.Filters can be particle or gas/vapour.Filters will need to be changed. |
Breathing apparatus | |
Fresh air hose | Relies on a supply of clean fresh air and is not under pressure.A hose that delivers air via mechanical means such as a fan or by a worker breathing naturally.Can be used for particles and gas/vapour. |
Constant flow airline | A hose delivers a constant supply of clean air from a compressor, a cylinder or a mobile compressed air unit.Can be used for particles and gas/vapour. |
Demand valve | A hose delivers a supply of clean air from a compressor, a cylinder or a mobile compressed air unit when the worker breathes in (on demand).Can be used for particles and gas/vapour. |
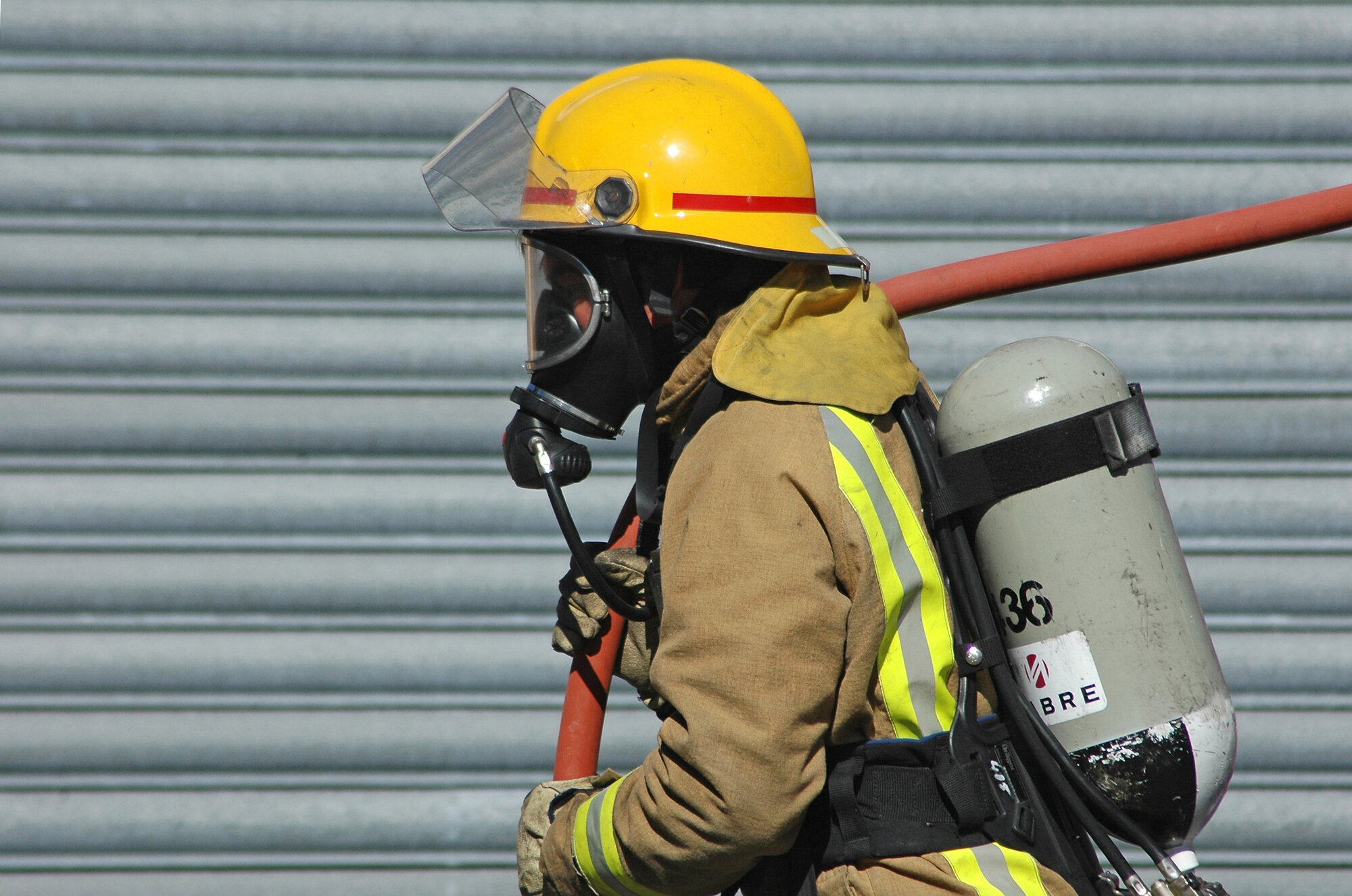
Selecting the right RPE
Before deciding on RPE, other control measures should be considered. There are principles of good control practice in the Control of Substances Hazardous to Health Regulations 2002 that should be used when deciding on precautions.
As RPE is classed as personal protective equipment (PPE), it only protects the user. It can be less effective than other control measures, so it is the final control option. Where practicable, employers should be looking at collective methods of control that protect everyone at risk of exposure and not just individuals. For example, eliminating or substituting hazardous substances and engineering controls, such as enclosures and extraction.
It is a legal requirement to carry out a risk assessment under the COSHH Regulations. The assessment must justify why RPE is needed and why the risk cannot be controlled by other means.
It may be necessary for the following circumstances:
- If there is still a risk of inhaling airborne contaminants despite other control measures being in place, such as local exhaust ventilation.
- If there is a sudden failure of control measures.
- If exposure to airborne contaminants is short-term or infrequent and it is not practical to use other control measures, e.g. for a spill or maintenance.
- If employers are in the process of implementing other control measures.
- In the event of an emergency , i.e. to safely exit an area and for emergency work or rescue purposes.
If the risk assessment identifies that RPE is required, it should be adequate and suitable, which means:
- It must be the right type for the hazard(s) that workers are exposed to and must reduce exposure to a level that protects the user’s health.
- It must be the right type for the user, activity and environment. It should not create additional risks and hinder work.
When assessing and selecting RPE, the following needs to be considered:
- The type of hazardous substances and concentration in the air.
- The environment that RPE will be used in, e.g. respirators must never be used if there is a risk of oxygen deficiency.
- The form of the substances, e.g. dust, vapour or mist.
- The work activities being conducted.
- Individual factors, e.g. facial differences, glasses and any medical conditions.
- Whether workers will have to wear other PPE or if anything could interfere with the RPE or communication.
It is important to consult employees and their representatives in the selection process. Not only is this legally required, but RPE will also be more effective at protecting workers if they are involved.
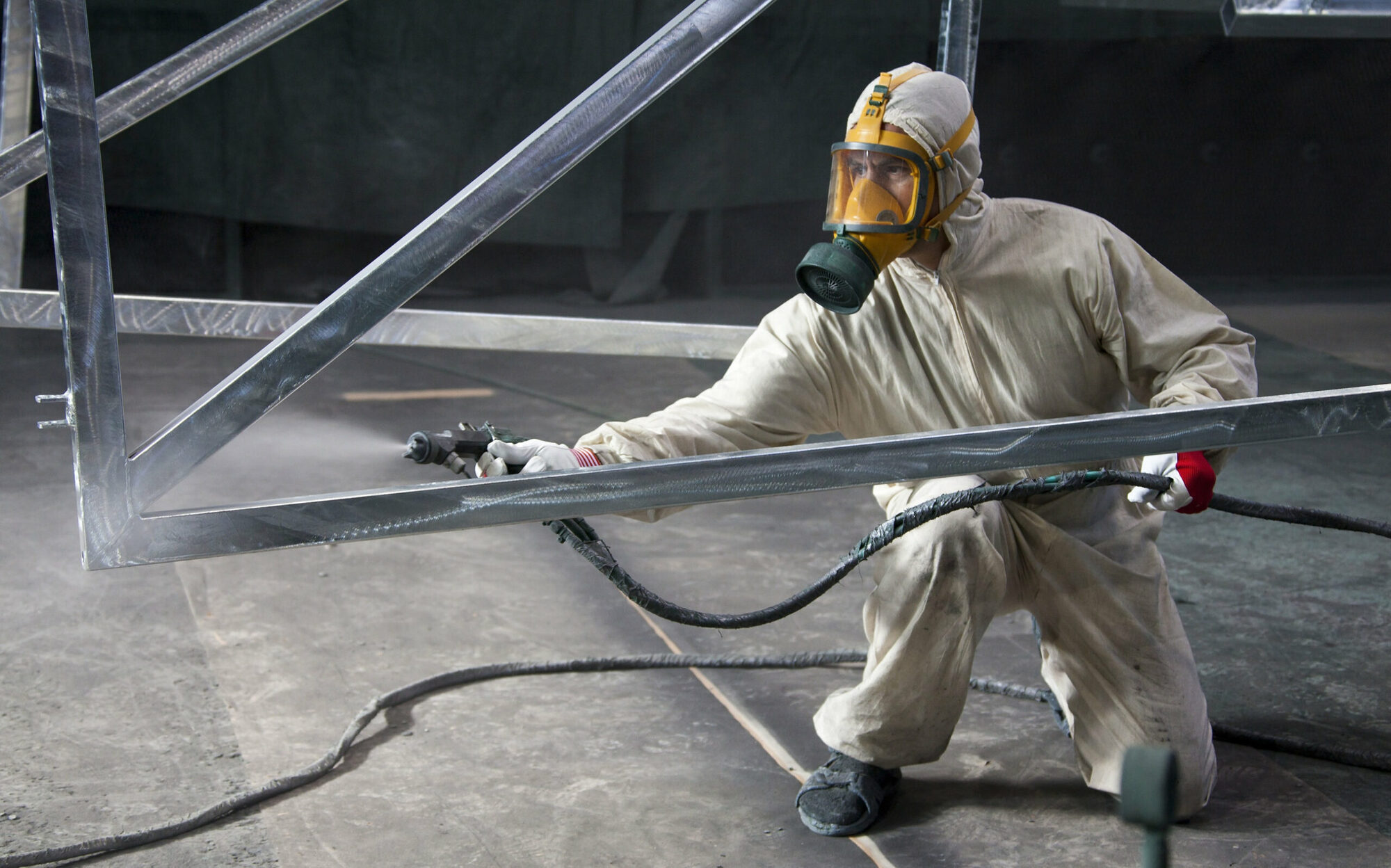
Assigned Protection Factor (APF)
The Assigned Protection Factor (APF) must be taken into account when selecting RPE. The APF is a number rating given by manufacturers that indicates the amount of protection different types of RPE provide. The ratings available are 4, 10, 20, 40, 200 or 2000, and the APF must be high enough to protect the wearer.
To identify what APF is required, the following should be checked:
- Safety data sheets (SDSs).
- Advice in COSHH essentials.
- Workplace exposure limits (WELs).
If the APF is not available, this is where it can get slightly tricky. The APF will need to be calculated using the WEL. RPE manufacturers and suppliers may advise on how to do this, and the HSE guidance HSG53 also provides advice.
Further help
To help employers and wearers select the correct RPE, the HSE recommends using:
- Health and safety guidance, such as HSG53 ((Respiratory protective equipment at work: A practical guide). There is a flow chart on page 12 that can help with the selection of adequate and suitable RPE.
- The Healthy Working Lives RPE selector tool.
- COSHH essentials guidance sheets.
RPE manufacturers and suppliers can also help select the right RPE, and some may even help with the risk assessment.
Other things to consider
There are other things to consider when selecting RPE and after the selection process, such as:
- The RPE selected must be suitable for the hazardous substances, environment and task.
- The RPE selected must fit the wearer and be compatible with other types of PPE.
- RPE must be of good quality and compliant with relevant national and international standards, e.g. CE marking and EN standards.
- Face-fit testing is required for every type of tight-fitting RPE used.
- When using breathing apparatus, the air should be clean and safe to breathe.
- Workers must be informed and trained on how to use RPE, and its use should be supervised.
- RPE should be maintained and stored in accordance with the manufacturer’s instructions.
- Damaged or used RPE must be disposed of safely and responsibly.
Summary
Employers must look at other options before deciding on RPE as a control and, if it is used, it must be adequate and suitable. Not wearing the correct RPE can result in ill health, and in some environments, such as confined spaces, it can be lethal to workers if there is toxic gases or oxygen depletion.
RPE selection can be somewhat of a minefield, particularly for smaller companies and self-employed workers without the correct expertise. The HSE and RPE manufacturers/suppliers have a wealth of information and guidance. They can help duty holders and RPE wearers understand the law and what they need to do.
Our respiratory systems are highly sensitive and are susceptible to damage, particularly when exposed to hazardous substances over time. It is, therefore, crucial that workers are protected from exposure to airborne contaminants.