In this article
Working in confined spaces poses high risks of accidents, injuries and even death. In the UK in 2021/2022, there were 35 workplace deaths due to falling from heights; falling within a confined space adds extra dimensions to that hazard. In addition to falling, workers can be struck by objects or bump into walls and obstacles. Depending on the space’s location and use, they may suffer from oxygen deficiency or be overcome by toxic or suffocating gases and vapours. In some cases, there are risks of drowning in liquid or being buried by solid materials. Hazardous chemicals, fires and explosions, as well as extremes of heat or cold, are further possibilities.
The RIDDOR (Reporting of Injuries, Diseases and Dangerous Occurrences Regulations) fatal injury statistics from 2016/17 to 2020/21 show that 24 working people died as a result of drowning or asphyxiation in confined spaces and 134 workers were killed by being trapped by something collapsing or overturning, which includes trench collapse.
This is why it is critically important that employers and workers comply with legal regulations and why employers must ensure that all workers who work in confined spaces are adequately trained for the work that they are undertaking, and the environment that they are working in.
Definition and Characteristics of Confined Spaces
The Health and Safety Executive (HSE) definition of a confined space is: “Any place, including any chamber, tank, vat, silo, pit, trench, pipe, sewer, flue, well or other similar space in which, by virtue of its enclosed nature, there arises a reasonably foreseeable specified risk.”
Under the Confined Spaces Regulations 1997, a confined space can be any space of an enclosed nature, for example a space with limited openings where there is a risk of death or serious injury from hazardous substances or dangerous conditions, such as explosive atmospheres, poisoning or lack of oxygen etc. Such environments can expose individuals to numerous risks to their health and safety. Some types of confined spaces include but are not limited to:
- Combustion chambers in furnaces etc.
- Controlled temperature stores
- Ductwork and ventilation shafts
- Enclosed drains and sewerage systems
- Hatchways, manholes and access shafts
- Industrial plant or machinery entered for maintenance or inspection purposes, e.g. laundry equipment such as large-scale washing and drying machines; ovens, kilns and drying plant; frozen or chilled storage areas such as chillers, freezers and cold stores; combustion chambers and incinerators; fuel tanks etc.
- Lift shafts
- Open-topped chambers, chimneys and flues
- Open-topped pits, chambers and vats such as a vehicle inspection pit in a workshop or garage
- Plant and boiler rooms
- Storage tanks and vessels such as grain silos, bulk tanks etc.
- Unventilated or poorly ventilated rooms or areas such as basements or cellars, roof and floor voids
Confined spaces are present in most industries and workplaces. Some places are not ordinarily considered a confined space but may become one when work is carried out, or during their construction, fabrication or subsequent modification.
There are several characteristics that define a confined space, including:
- The space is large enough to permit a worker to enter
- The space has limited openings for entry and exit
- The space is not designed for continuous occupancy
- The space is partially or completely enclosed
- The space has the potential for a hazard to be present such as:
Lack of oxygen / poor ventilation – Oxygen can be removed from the atmosphere within a confined space through naturally occurring reactions. A reaction between certain soils and the oxygen, or groundwater and chalk or limestone, can produce carbon dioxide which displaces oxygen. Rust forming inside tanks can also create a lack of oxygen.
Gases, fumes and vapours – Poisonous gases and fumes can build up within confined spaces, especially where there is a lack of ventilation. Deadly gases can leak into the confined space, e.g. through a burst gas pipe or from contaminated land. Or they may be created from the work being carried out, such as welding, adhesives or paint fumes. Without extraction or ventilation, these gases and fumes can create a toxic atmosphere within the confined space.
Flooding – Liquids can quickly flood the confined space, particularly in drainage or sewer work, trapping and potentially drowning those within. Solids can also flood confined spaces, e.g. in trench collapses, with those within the trench at the risk of being trapped or buried. Confined spaces can be small, so flooding can occur in a matter of seconds, leaving no time to escape.
Dust – Dust can build up within confined spaces, either naturally occurring or through the activity being carried out, e.g. drilling or grinding. Excessive dust inhalation causes respiratory problems, and hazardous dust can be fatal. Dust build-up can also increase fire/explosion risk, especially where there is a lack of ventilation.
Fire and explosions – Flammable vapours, liquids, gases and dust within the confined space can all increase the risk of fire and explosions. The risk is increased further when any hot works or tools which can spark are used within the confined space.
Temperature – Strenuous construction work, hot works or naturally occurring hot conditions can lead to a dangerous increase in body temperature. This can quickly become a problem within confined spaces that are hard to escape from at the best of times. Heat can rapidly rise due to the enclosed nature of a confined space. This can lead to heatstroke, exhaustion and collapse.
Access restrictions – Confined spaces are also dangerous because they can be difficult to access. This makes escape difficult and also hinders any emergency rescue. Once you are inside a confined space, there may not be a quick or easy way out. So it is important to know that work can be carried out safely before you enter, and that emergency arrangements are in place.
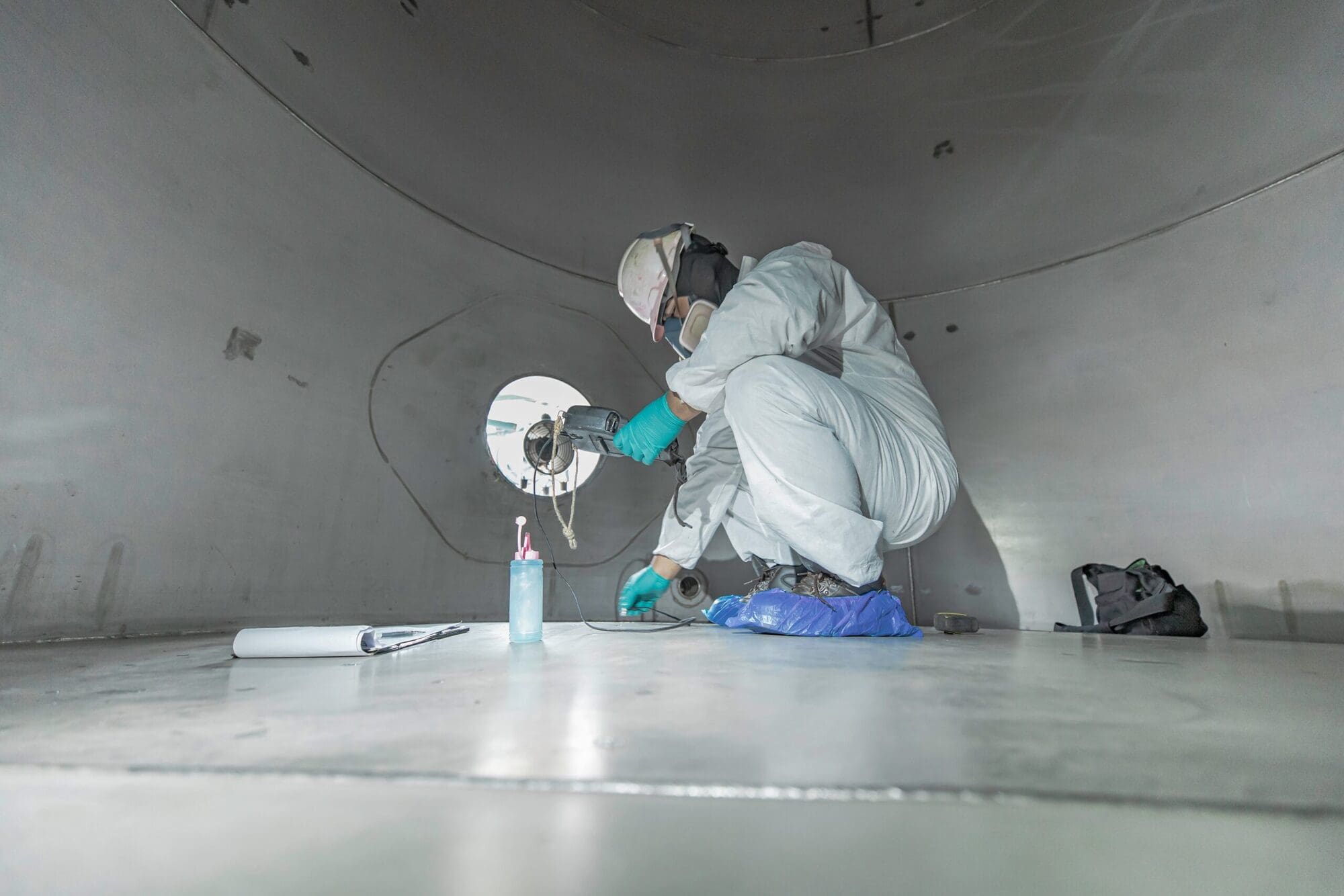
Legal Framework
The UK has strict requirements for identifying and managing confined spaces. These laws and regulations mandate employers to assess risks and ensure the safety of workers. Failure to comply can result in severe penalties, legal action and reputational damage.
Confined Spaces Regulations 1997
The regulations place duties on employers, the self-employed, and any person who controls the work of others, e.g. Health and Safety managers, facilities managers or building owners who may contract others to work in confined spaces, to the extent they control the work. It requires that work is undertaken safely and that the risks presented by confined spaces are adequately controlled. The regulations have an accompanying Approved Code of Practice (HSE L101) that has special legal status and contains further details on the requirements for managing work in confined spaces. HSE L101 Regulation 4 Work in Confined Spaces specifically details requirements for testing/monitoring the atmosphere.
Health and Safety at Work etc. Act 1974 (HSWA)
This requires employers to ensure the health and safety of all employees and anyone who may be affected by their work, including any and all visitors to any part of the employer’s premises. This includes taking steps to control confined spaces risks. Employees must not endanger themselves or others and must use any safety equipment provided. Manufacturers and suppliers of equipment such as but not limited to PPE, have a duty to ensure that their products are safe. They must also provide adequate information about appropriate use.
Management of Health and Safety at WorkRegulations 1999
These build on the HSWA and include duties on employers to assess risks and where necessary take action to safeguard health and safety.
Personal Protective Equipment at Work Regulations 1992
The main requirement of the PPE at Work Regulations is that personal protective equipment is to be supplied and used at work wherever there are risks to health and safety that cannot be adequately controlled in other ways.
The following regulations apply to confined spaces within machinery:
Provision and Use of Work Equipment Regulations 1998 (PUWER)
The regulations require that equipment is safe, suitable, maintained, inspected and installed correctly. PUWER also requires that equipment is used only by competent people when it is safe to do so.
Workplace (Health, Safety and Welfare) Regulations 1992
These regulations place duties on employers in respect of all workplaces, or any premises used as a place of work, under their control.
Legislation covering enclosed spaces on sea-going vessels includes:
- Merchant Shipping and Fishing Vessels (Entry into Enclosed Spaces) Regulations 2022 and Code of Safe Working Practices for Merchant Seafarers (COSWP) 2021, Ch 4 (Emergency Drills and Procedures) and Ch 15 (Entering Dangerous (Enclosed) Spaces).
In EU countries, there is no EU legislation specifically relating to work in confined spaces. However, the Framework Council Directive 89/391/EEC of June 1989 covers all aspects of safety and health at a workplace. It places a duty on employers to consider the specific characteristics of every workplace. Some European countries do have their own local confined space regulations. The PPE used for such work is covered by EU-wide regulations, which are also adopted by the EU state members and the UK.
In the US, the Occupational Safety and Health Administration (OSHA) is a regulatory agency of the United States Department of Labor (sic). OSHA 1910.146 has set standards that employers and employees must follow when working in confined spaces. OSHA provides a few requirements that employees should know when it comes to highlighting the hazards associated with any confined space. They should understand the following hazards that could be present such as:
- Toxic atmospheres that cause various acute health effects
- Oxygen deficiency environments that displace air by another gas
- Oxygen enrichment environments that can result in an increased risk of fire or explosion
- Flammable atmospheres that can present a risk of explosion or a suspension of combustible dust in air
- Flowing liquid that can cause drowning, suffocation, burns or injury
- Excessive heat that can increase the risk of heat stroke or cause an employee to heat collapse from heat stress

Training Requirements
The Health and Safety Executive (HSE) mandates that all workers involved in confined space work must receive adequate training. An employer as a minimum MUST make employees aware of the dangers of working in a confined space and provide adequate training on the legal requirements, foreseeable risks, and a wide range of safety procedures. Employers must also carry out a risk assessment that details a safe system of work and ensure that workers are trained with practical skills to ensure that they are fully prepared to manage the risks associated with confined spaces. The Confined Spaces Regulations 1997 and guidance from the Health and Safety Executive (HSE) set out the key components that should be included in this training, and include:
- Understanding the risks
- Safe systems of work
- Using safety equipment including the use of PPE
- Rescue procedures
- First aid
Workers need to understand the common hazards and risks associated with confined spaces, and how to implement control measures to either eliminate the hazard or reduce the risk to an acceptable level.
They need to have a clear understanding of safe entry and exit procedures, including the importance of checking the environment before entering, continuous monitoring during the work, and fully understanding when to exit immediately, such as if the atmosphere becomes unsafe or if a dangerous condition arises. They must understand how to use permit-to-work systems, which provide a formal authorisation process for working in confined spaces.
Training for the use of safety equipment and PPE should cover how to use portable gas detection devices to measure oxygen levels and detect the presence of harmful gases. They should know the acceptable limits for oxygen levels (19.5% to 23.5%) and other gases, and understand the risks if these thresholds are breached. They should also know the procedures for continuous atmospheric monitoring throughout the work, especially if conditions can change rapidly.
Training should cover the correct selection, use and maintenance of PPE such as helmets, harnesses, gloves and protective clothing. For some workers, training in the use of respirators or self-contained breathing apparatus (SCBA) may be required such as in areas where the air is unsafe to breathe.
Workers need to understand the specifics of the emergency plan which every confined space operation must have, including designated roles and available equipment for rescue. They should also be trained on how to use and maintain emergency equipment such as harnesses, lifelines, and hoists, especially for rescue operations. This aspect of working in confined spaces training should be practical and include the opportunity to practise such things as confined space entry, work and emergency scenarios so that workers can apply theory to practice in a safe environment to prepare them for the work environment.
It is essential that workers in confined spaces have basic first aid training so that they are able to provide initial support until professional emergency help arrives. First aid training certificates must be updated every 3 years; however, the HSE recommends a refresher course every year.
Communication and team working is an important aspect of working in confined spaces. Effective communication can be difficult in confined spaces so workers should be trained in using reliable communication systems. Everyone in the team should understand their role and how to work together to ensure safety.
In confined space working, the roles of supervisors and rescue teams carry immense responsibility, as they are critical to ensuring safe operations, proper oversight and effective emergency responses. Training for these roles must be compliant with UK regulations, including the Confined Spaces Regulations 1997 and guidance from the Health and Safety Executive (HSE), and should include:
- A thorough understanding of all legal responsibilities and regulatory compliance including any additional regulations relevant to their specific industry, such as construction or utilities.
- Supervisors must be trained in how to document incidents, near misses and safety checks, ensuring compliance with legal reporting requirements.
- The training must cover specific risk assessment, the practical implementation of control measures, and risk management, including how to monitor conditions continuously and adjust control measures if necessary to maintain a safe environment.
- Supervisors and rescue teams must be competent in using gas detectors to assess the presence of hazardous gases and ensure safe oxygen levels (19.5%-23.5%).
- Supervisors must be trained to manage permit-to-work systems, ensuring that no one enters a confined space without proper authorisation, safety checks and a rescue plan in place. They must also be trained to create tailored rescue plans for each confined space scenario. Rescue teams should be trained and equipped to respond quickly and safely to these rescue plans.
- Training for rescue teams must include the proper use of specialist rescue equipment, such as tripod winches, rescue lines, breathing apparatus and stretchers and should involve practical exercises that simulate confined space emergencies.
- Supervisors and rescue teams must be trained to be proficient in selecting appropriate PPE based on the specific risks, the use of breathing apparatus, and ensuring that PPE is correctly maintained, inspected before use, and properly stored to prevent malfunctions during critical operations as the safety of workers will depend upon their competence.
- Communication is an important aspect of training for supervisors and rescue teams and must include how to communicate with workers and with external emergency services and provide accurate information during a crisis.
- First aid training for supervisors and rescue teams should go beyond basic first aid training and should include how to manage injuries that are common in confined space incidents. Rescue teams should also be trained on cardiopulmonary resuscitation (CPR) and safe techniques for moving injured individuals, especially when confined spaces make access and movement difficult.
Supervisors and rescue teams will need to take part in regular refresher training and practical exercises to ensure continued competency in this high-risk area of work.
Awarding bodies such as City and Guilds offer Confined Spaces qualifications at levels 2, 3 and 4. Level 2 and 3 qualifications are for anyone entering a confined space. This could be to carry out work, work as an entry controller / top person supporting entry or conducting emergency rescue and recovery. The level 4 qualification is for those who plan and manage work in confined spaces.
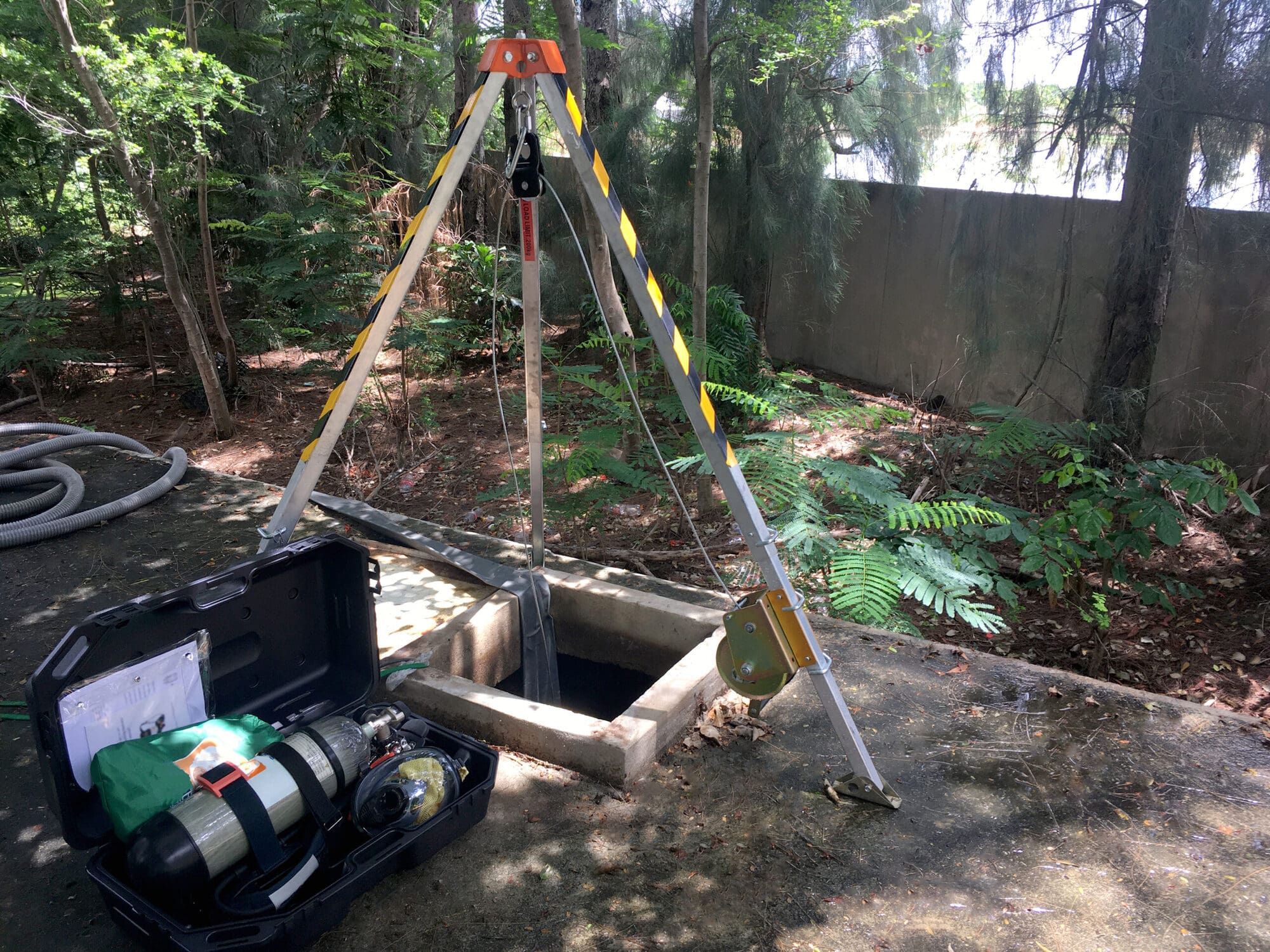
Case Studies and Examples
In November 2016, Carlsberg was in the process of upgrading the refrigeration system, a key element of the brewing process at its main UK brewery in Northampton. Part of the work being done involved the removal of the refrigeration system’s old compressor. It was during the removal of the compressor that there was an uncontrolled release of ammonia gas, which killed David Chandler and seriously injured David Beak. It also resulted in another 20 people requiring medical assistance, including some members of the emergency rescue team. The HSE was notified of the incident the same day and immediately began a joint investigation alongside the police.
Although the investigation was quite complex, the reasons for the incident were actually quite simple and it essentially came down to inadequate isolation. At Birmingham Crown Court, Carlsberg Supply Company UK Ltd, which was summonsed under its new company name of Carlsberg Marston’s Brewing Company, pleaded guilty to charges under sections 2(1) and 3(1) of the Health and Safety at Work Act, and regulation 3(1) of the Management of Health and Safety at Work Regulations. The company was fined £3 million with costs of £90,000.
The incident led to increased scrutiny of safety standards in the food and beverage industry regarding chemical use in confined spaces.
The tragic deaths of two workers involved in cleaning tankers resulted in Greenfeeds Ltd receiving a seven-figure fine and senior managers received substantial custodial sentences and disqualification. In a six-week trial, the jury found that there was no safe method of work for cleaning the tanker. The only method implemented was to have one person entering the tank with a power washer while another acted as a spotter and held the hose pipe. There was no method statement for getting someone out of the tanker, despite there being no ladder inside to climb out, and no proper risk assessment in place. Employees received no training, no personal protective equipment and no warning of the risks. There was not even a basic record of when an employee entered a tanker to clean it. Staff had previously expressed concerns about the dangers of the cleaning method but had been ignored and there was no named health and safety officer at the company.
Greenfeeds Ltd pleaded guilty to failing to discharge their duties under section 2(1) Health and Safety at Work Act etc 1974 (“HSWA”) due to a failure to ensure, so far as is reasonably practicable, the health, safety and welfare at work of its employees. The company was also found guilty of two counts of corporate manslaughter and fined a total of £2 million.
Gillian Leivers, who worked as the office and accounts manager and oversaw the day-to-day running of the site, was found guilty of two counts of gross negligence manslaughter. She was also found guilty of breach of section 2(1) HSWA by virtue of section 37(1) in that the offence by the company was committed with her consent or connivance of, or attributable to her neglect. She was sentenced to a total of 13 years imprisonment and disqualified for being a company director for a period of 15 years.
Ian Lievers, director of Greenfeeds Ltd, was also found guilty of breach of section 2(1) HSWA by virtue of section 37(1) of the Act. He was sentenced to 20 months imprisonment and disqualified from being a company director for a period of 10 years.
Stewart Brown, the firm’s transport manager, was found guilty under section 7(1) HSWA in that being an employee at work, he failed to take reasonable care for the health and safety of others who might be affected by his acts or omissions at work. He was also charged with two counts of gross negligence manslaughter but found not guilty of either count. He was sentenced to one-year imprisonment suspended for two years.
Greenfeeds Ltd’s breaches were severe and their consequences fatal. Although the facts are extreme, they highlight the importance of getting the basics right for even the most routine of tasks. Working in confined spaces of tanks and tankers is part of everyday work in the waste and agricultural sector and it is essential that risk assessments are regularly reviewed, that regulations are complied with and that all workers are adequately trained for the roles that they are performing and the environments that they are working in.
Implementing Safety Measures
The Management of Health and Safety at Work Regulations requires employers to carry out a suitable and sufficient assessment of the risks from all work activities, including work in confined spaces, for the purpose of deciding what measures are necessary for safety. The risk assessment must be carried out before anyone enters the confined space. The risk assessment should follow the HSE five-step process and include:
- The task to be carried out inside the confined space.
- The working environment – including the actual confined space and the area around it.
- Working materials and tools that are to be used and/or taken inside the confined space, including the method of getting the equipment into the confined space and its suitability for the working environment, e.g. in flammable atmospheres you may need explosion protection equipment to prevent sparks.
- The suitability of those carrying out the task, ensuring both physical, such as mobility, size etc., and mental considerations, such as claustrophobia, perception of risk etc., are considered.
- Arrangements for emergency rescue – all employers must have procedures as you cannot simply rely on the emergency services, they may take too long to arrive. You must, however, have procedures for alerting them such as who will call them etc.
The Confined Spaces Regulations 1997 and guidance from the Health and Safety Executive (HSE) emphasise that effective communication and monitoring systems are critical for ensuring the safety of workers in confined spaces. Best practice and compliance with these regulations include:
- Establishing and using a clear and standardised communication method, such as radios, hand signals, or pre-arranged verbal commands, depending on the environment, and setting specific, clear signals for emergencies that every worker must know.
- Ensuring that workers inside a confined space remain in continuous contact with a designated safety attendant or supervisor outside the space and appointing a safety attendant responsible for maintaining communication with workers inside the confined space, keeping records of entry/exit, and raising the alarm in case of an emergency.
- Ensuring that all workers involved in the confined space operation, including supervisors, attendants and workers, participate in a pre-entry briefing detailing hazards, risks, procedures, roles and emergency procedures.
- Ensuring the use of continuous atmospheric monitors to detect hazards such as low oxygen levels, toxic gases etc. and ensuring real-time readings are communicated both to workers inside the confined space and the safety attendant outside.
- Ensuring that supervisors and safety attendants regularly review and update the permit-to-work, particularly if conditions inside the confined space change.
A specific rescue plan must be developed for each confined space operation. This plan should detail:
- The roles and responsibilities of each team member during a rescue
- Communication protocols to signal and manage the rescue process
- Entry and exit points, particularly if alternative escape routes are needed
- Steps to handle specific emergencies such as atmospheric contamination, worker collapse, or entrapment
Employers should ensure that workers, supervisors and rescue teams know the emergency procedures and emergency communication process set out in the specific rescue plan, including how to signal for immediate help, evacuate workers, and contact external emergency services if needed. Essential and appropriate rescue equipment must always be available and workers must be adequately trained to use the equipment. This includes:
- Breathing Apparatus (BA)
- Retrieval Systems
- Ventilation Equipment
- Atmospheric Monitoring Devices
- Lighting and Communication Tools
- First Aid Kits
All rescue equipment and rescue personnel must be well maintained and immediately available at the site where confined space work is taking place. Equipment should be stored near the entry point for rapid deployment during an emergency.
Compliance Audits and Inspections
Risk assessments, communication and monitoring protocols, permit-to-work systems, safety procedures and rescue plans, and training are ‘living documents and practices’ and as such require regular reviews, audits and inspections to ensure relevance and compliance with legal regulations and safety standards. They also demonstrate due diligence by the employer.
Non-compliance can have devastating consequences for worker safety, and can lead to heavy fines, legal action or even the closure of operations, as seen in the examples highlighted earlier in this article. Regular audits and inspections help to identify:
- Any new or additional hazards and risks to health and safety
- Any defects in equipment and verify that it is available and operational for when it is needed
- Areas where processes can be improved, enhanced or changed
- Gaps in training requirements and/or update requirements
- Non-compliance issues and enable employers to rectify these before they lead to accidents or regulatory enforcement
Regular audits and inspections reinforce a safety-first mindset and adhere to safety protocols within the workforce ensuring compliance in working practices.
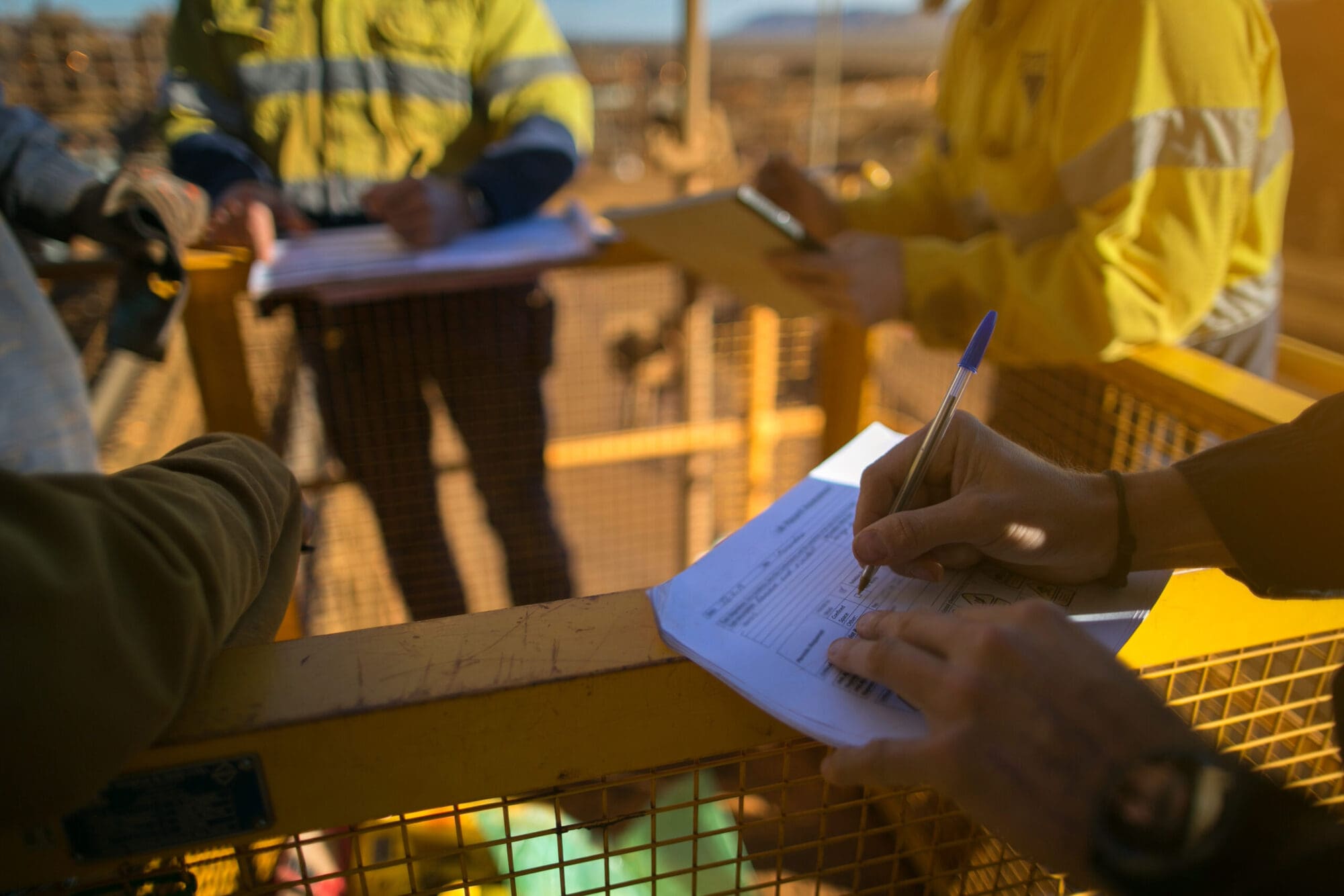
Future Trends and Challenges
Through the incorporation of remote, robotics and artificial intelligence (AI), new technology is facilitating comprehensive inspection, maintenance and operations within confined spaces, mitigating risks to individuals.
Advances in gas detection and monitoring systems are a critical technological development. These systems continuously monitor the atmosphere within confined spaces, detecting the presence of hazardous gases or insufficient oxygen levels. They can alert operators in real time, allowing for immediate action to be taken to mitigate any identified risks. This continuous monitoring ensures that the environment remains safe throughout the entire duration of the work.
Drones are already being used to negate the need to have employees working at height in a range of circumstances. Drones can increase efficiency and productivity as well as enhance safety. The price of drones has come down substantially; however, in many instances, employers will need to bring in drone operatives if they don’t have the skills in-house, which adds to the expense, but overall the technology is now genuinely affordable to most businesses.
Effective communication is crucial during confined space operations. Technological tools such as wireless communication devices and wearable technology have greatly improved the ability of teams to stay in contact. Workers can now use hands-free communication devices that integrate with their personal protective equipment (PPE), allowing for seamless communication with team members and supervisors outside the confined space. Wearable technology will continue to evolve, providing workers with real-time health monitoring and hazard alerts. Smart PPE will integrate sensors that monitor vital signs and environmental conditions, ensuring that workers remain safe and healthy during confined space operations. Additionally, real-time data sharing through cloud-based platforms enables better coordination and decision-making. Supervisors and safety officers can monitor operations remotely, accessing live data and video feeds. This connectivity ensures that any issues can be promptly addressed, and the overall safety of the operation is maintained.
Predictive analytics can also be employed to anticipate potential risks based on historical data. By analysing factors such as environmental conditions, equipment performance, and worker behaviour, predictive models can forecast potential hazards and recommend proactive measures to prevent accidents.
Virtual reality (VR) and augmented reality (AR) are being used to improve health and safety training. Through VR and AR, trainees can experience various scenarios they might encounter in real-life confined spaces. The idea is to make the scenario as realistic as possible and allow trainees to be fully immersed in the action, improving their readiness and confidence when performing actual confined space entries. Use will help to prevent accidents and therefore prevent downtime on sites.
The integration of artificial intelligence (AI) and machine learning is expected to further enhance safety and efficiency. AI-powered robots and drones will become more autonomous and capable of performing complex tasks with minimal human intervention.
Conclusion
In this article we have examined the importance of legal regulation compliance and adequate training in mitigating risks associated with confined space work. As we have seen, staying compliant and protecting workers goes beyond just meeting the legal requirements. It involves ongoing, relevant training for all workers and regular up-to-date information on regulations and guidelines especially if changes are made. Communication and collaboration between all stakeholders involved with confined space work is also a crucial aspect of ensuring compliance with regulations and for maintaining a safe working environment. This includes timely information sharing particularly following audits, inspections and accidents or near misses as this helps to inform the development of best practice.
Working in confined spaces is one of the most dangerous occupations in the world; however, a deep knowledge of and compliance with the regulations, guidelines and best working practices can help to mitigate the risks and make the working environment safer.