In this article
Confined spaces can be found across various industries, playing a critical role in numerous operational processes. These spaces, characterised by their limited entry and exit points and not designed for continuous occupancy, can be found in a myriad of environments such as manufacturing plants, construction sites, shipyards, and even in municipal infrastructures like sewers and water treatment facilities.
In the industrial sector, confined spaces might include tanks, silos, pipelines and storage bins. In the construction industry, workers often encounter confined spaces in trenches, tunnels and manholes. Similarly, in the agricultural sector, grain bins and silos are common examples. The maritime industry also frequently deals with confined spaces in the form of ship holds and ballast tanks.
Despite their prevalence and necessity, confined spaces pose significant risks to worker safety. The restricted nature of these areas can lead to hazardous atmospheric conditions such as oxygen deficiency, toxic gas accumulation or combustible dust concentrations. Additionally, the physical configuration of confined spaces can complicate emergency response efforts, making rescue operations particularly challenging and dangerous. Workers in confined spaces are also at risk of physical injuries due to cramped working conditions, slips, trips, falls, or being struck by equipment.
The combination of these hazards means that stringent safety measures and comprehensive training for workers is vital. Understanding the nature of confined spaces and the associated risks is crucial for the development of effective safety protocols and emergency preparedness plans, ensuring that workers can perform their duties safely in these challenging environments.
People are killed or seriously injured in the UK each year working in confined spaces across a range of industries, including mining, sewage and working on the docks. Those killed in accidents include people working within the confined space and those people attempting a rescue operation from confined spaces without the proper equipment or training.
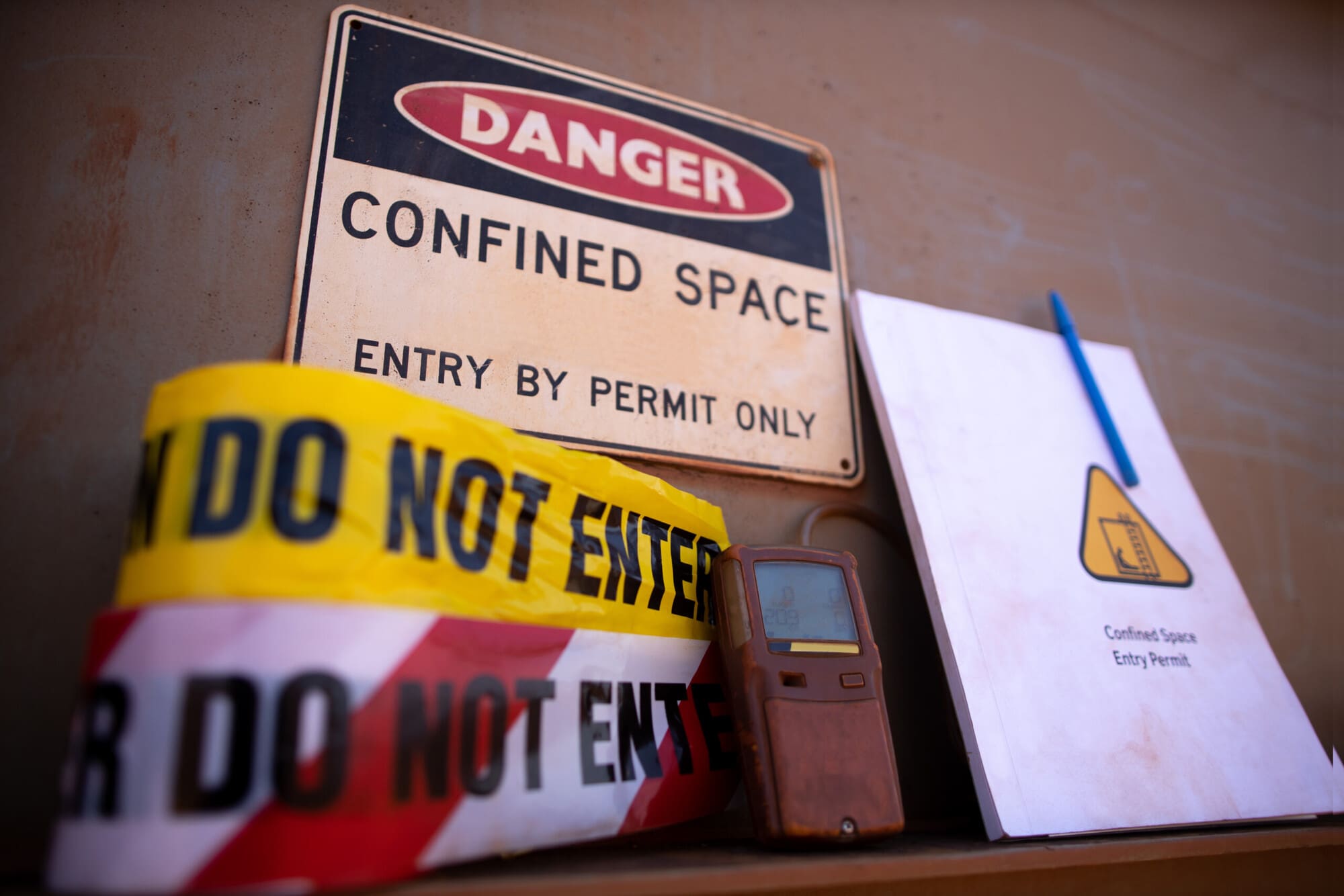
Defining Confined Spaces
A confined space is a specific type of work environment with distinct characteristics that pose unique challenges and hazards to workers. The defining characteristics of a confined space include:
- Limited entry and exit points – confined spaces have restricted means for entry and exit, which can complicate emergency escape and rescue operations. These limited openings may require special entry and exit procedures, often involving ladders or narrow passages.
- Inadequate ventilation – the natural ventilation in confined spaces is often poor, leading to the potential accumulation of hazardous substances. This lack of adequate airflow can cause dangerous atmospheres due to the build-up of toxic gases, lack of oxygen, or flammable vapours.
- Potential atmospheric hazards – confined spaces can contain or produce hazardous atmospheres, which may include oxygen deficiency. These are oxygen levels below 19.5% which can impair physical and mental functioning and can be fatal. Oxygen enrichment is oxygen levels that are above 23.5%, which can increase the risk of fire and explosion. Toxic gases and vapours include the presence of substances such as carbon monoxide, hydrogen sulphide, or other chemicals that can cause poisoning or respiratory problems. Flammable gases and vapours include the presence of substances that can create a risk of explosion or fire.
- Not designed for continuous occupancy – these spaces are not intended for continuous worker occupancy. They are usually designed for occasional access for maintenance, repair, cleaning, inspection or similar activities.
Confined spaces may contain other hazards such as unguarded machinery, exposed live wires, extreme temperatures, or loose materials that can pose risks to workers.
Examples of confined spaces include:
- Storage tanks – including chemical tanks, water tanks and fuel tanks.
- Vessels – pressure vessels, reactors and boilers.
- Ducts and HVAC systems – including air ducts and exhaust ducts.
- Pipelines – sewage pipes, water pipes, gas pipelines.
- Vaults – including electrical vaults and utility vaults.
- Crawl spaces – these are areas under floors or in attics.
- Hoppers – these are used in industrial processes for holding and dispensing materials.
- Utility tunnels – underground tunnels for utilities such as steam, water or electrical lines.
- Bunkers – storage bunkers for materials like coal, sand or grains.
- Septic tanks – used for waste disposal.
- Boiler rooms – rooms where boilers are housed, often cramped and poorly ventilated.
- Ship holds – cargo holds in ships.
- Trenches – deep excavations for laying pipes and cables.
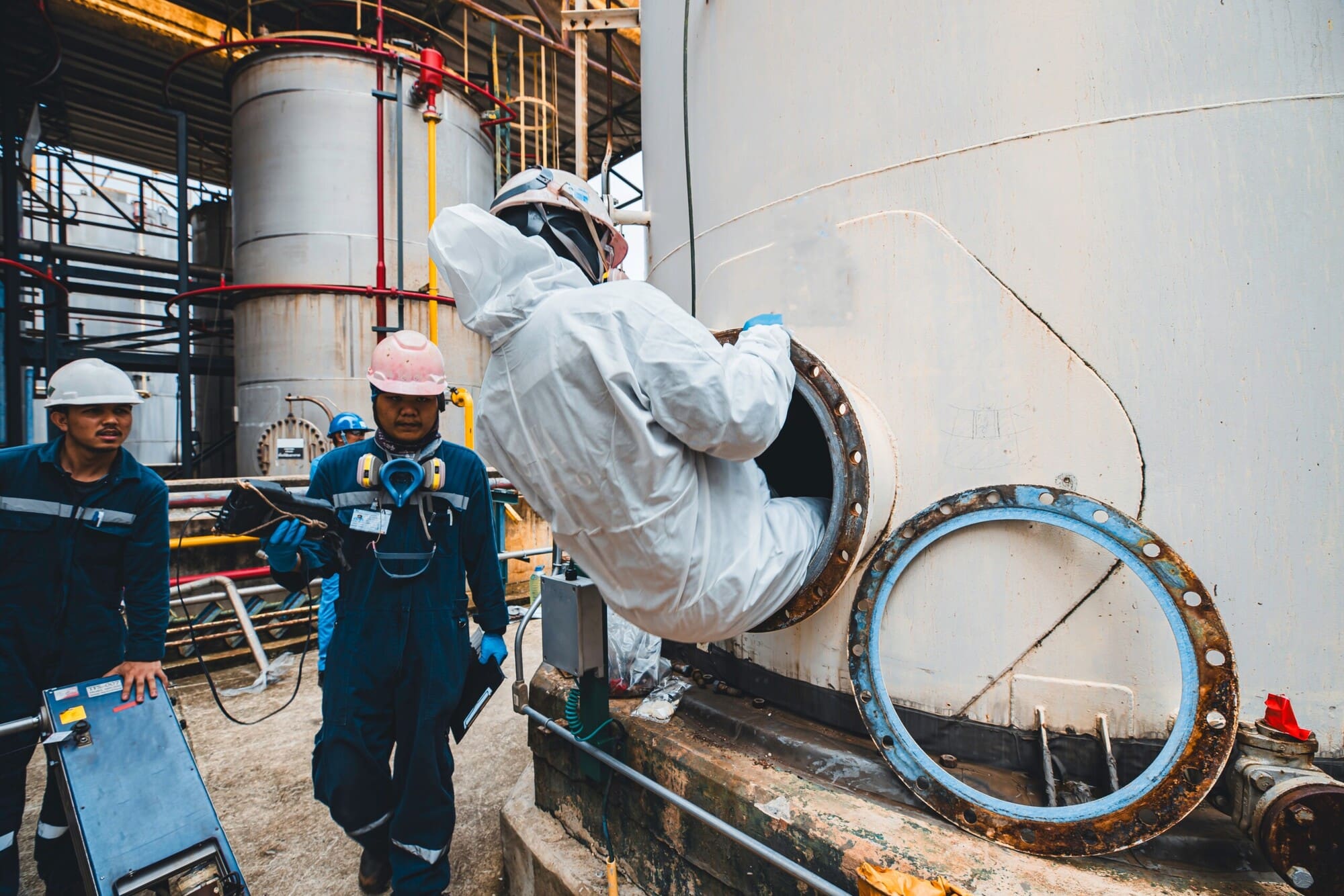
Risks Associated with Confined Spaces
Confined spaces present numerous risks and hazards that can endanger the health and safety of individuals working within them. These hazards can be broadly categorised into atmospheric, physical and psychological hazards. Understanding these risks is crucial for effective safety management and prevention measures.
Atmospheric hazards
- Oxygen deficiency – this can result from the consumption of oxygen by chemical reactions, e.g. rusting, displacement by other gases, or biological processes, such as fermentation. Symptoms of oxygen deficiency include dizziness, shortness of breath, confusion, loss of consciousness and, in severe cases, death.
- Toxic gases, e.g. hydrogen sulphide, carbon monoxide, ammonia and methane – exposure to toxic gases can cause a range of health issues from mild irritation to severe poisoning, respiratory failure and death. Hydrogen sulphide, for instance, can cause rapid unconsciousness and death at high concentrations.
- Flammable vapours, e.g. methane, propane and gasoline vapours – flammable vapours can form explosive mixtures with air, posing fire and explosion risks. A spark or static discharge can ignite these vapours, leading to catastrophic consequences.
Physical hazards
Engulfment can occur in environments like grain bins, sand, gravel or other loose materials. Engulfment can lead to suffocation, crushing injuries and death as the individual is buried and pressure from the material prevents breathing. Entrapment occurs when a person is trapped in machinery, between objects or in narrow passages. It can result in injuries or death due to compression, inability to escape or delays in rescue efforts. Slippery surfaces, unguarded edges, uneven flooring, and the confined nature itself can cause people to have falls. Falls can lead to fractures, head injuries and other serious trauma. The confined space complicates rescue operations, increasing the risk of prolonged entrapment and further injury.
Psychological hazards
These include claustrophobia which is a fear of confined or enclosed spaces. Individuals may experience intense anxiety, panic attacks, sweating, rapid heartbeat and difficulty breathing. This can impair their ability to function safely and effectively within the space. Panic can be triggered by the confined nature of the space, lack of visibility or a sudden hazardous event, for example gas release or equipment failure. Panic can lead to irrational behaviour and compromised decision-making, which can potentially exacerbate the situation. In extreme cases, it can cause the person to hyperventilate, freeze or attempt dangerous escape manoeuvres.
There have been several real-life incidents and accidents caused by inadequate safety measures in confined spaces including:
- DuPont La Porte Incident (2014) in Texas, USA – a release of nearly 24,000 pounds of methyl mercaptan, a highly toxic chemical, occurred at a DuPont plant. Four workers died due to toxic exposure as a result of inadequate maintenance procedures and insufficient training on confined space entry protocols. Investigations revealed lapses in safety culture and emergency response readiness.
- Humboldt Wedag Coal Mill Explosion (2009) in Tuen Mun, Hong Kong – workers were inside a coal mill conducting maintenance when an explosion occurred. There was an ignition of coal dust due to insufficient cleaning and poor ventilation in the confined space. Three workers were killed and the investigation pointed to failures in ensuring a safe atmosphere before entry.
- City of Tampa Sewer Deaths (2006) in Tampa, Florida, USA – two workers entered a sewer to retrieve a piece of equipment and were overcome by hydrogen sulphide gas due to there being a lack of proper atmospheric testing and inadequate use of PPE. Both workers died and the incident underscored the importance of gas detection and PPE in confined space work.
- Valero Refinery Hydrogen Sulphide Leak (2006) in Delaware City, Delaware, USA – a hydrogen sulphide leak occurred in a confined space at a Valero refinery due to inadequate maintenance and failure to detect and control the hazardous atmosphere. One worker died and several others were injured. The company faced significant fines and was required to implement stricter safety protocols.
- Teesside Refinery Incident (2013) in Teeside, UK – two workers died after being exposed to a release of hydrogen sulphide gas at a refinery. An investigation found that there were inadequate gas detection and ventilation systems, and failure to adhere to confined space entry protocols. The company was fined £1.2 million for health and safety breaches.
- Longannet Power Station Incident (2000) Fife, UK – three workers died due to asphyxiation while working in a poorly ventilated underground duct. An investigation found that there had been a lack of proper ventilation and failure to conduct a proper risk assessment. The power station operator faced significant fines and implemented stricter safety protocols.
These incidents highlight the critical importance of comprehensive safety measures, including proper training, atmospheric testing, use of PPE, emergency preparedness, and adherence to safety regulations, in order to prevent tragedies in confined spaces.
Safety Protocols and Procedures
In these kinds of environments various safety measures should be taken, including:
- Oxygen levels should be regularly measured, and the detection of toxic and flammable gases using the appropriate sensors before and during entry into the space should be a priority.
- Forced air ventilation should be used to ensure a continuous supply of fresh air and to remove contaminants from the confined space.
- Personal Protective Equipment (PPE) such as respirators, gas detectors and harnesses should be used.
- Train workers on the specific hazards of confined spaces, emergency procedures and the use of safety equipment. Inadequate training creates dangerous work environments, particularly when working in a high-risk environment.
- Develop and practise rescue plans, ensuring that rescuers are equipped and trained to respond to confined space emergencies.
- Implement a permit system to control entry into confined spaces, ensuring that all safety checks and preparations are completed before entry.
- Complete a risk assessment, which should be used to identify, evaluate and manage potential risks. The process should aim to minimise or mitigate these risks by implementing appropriate safety measures.
Understanding and addressing the various risks associated with confined spaces through comprehensive safety protocols, proper equipment and thorough training is essential to protect workers and prevent accidents.
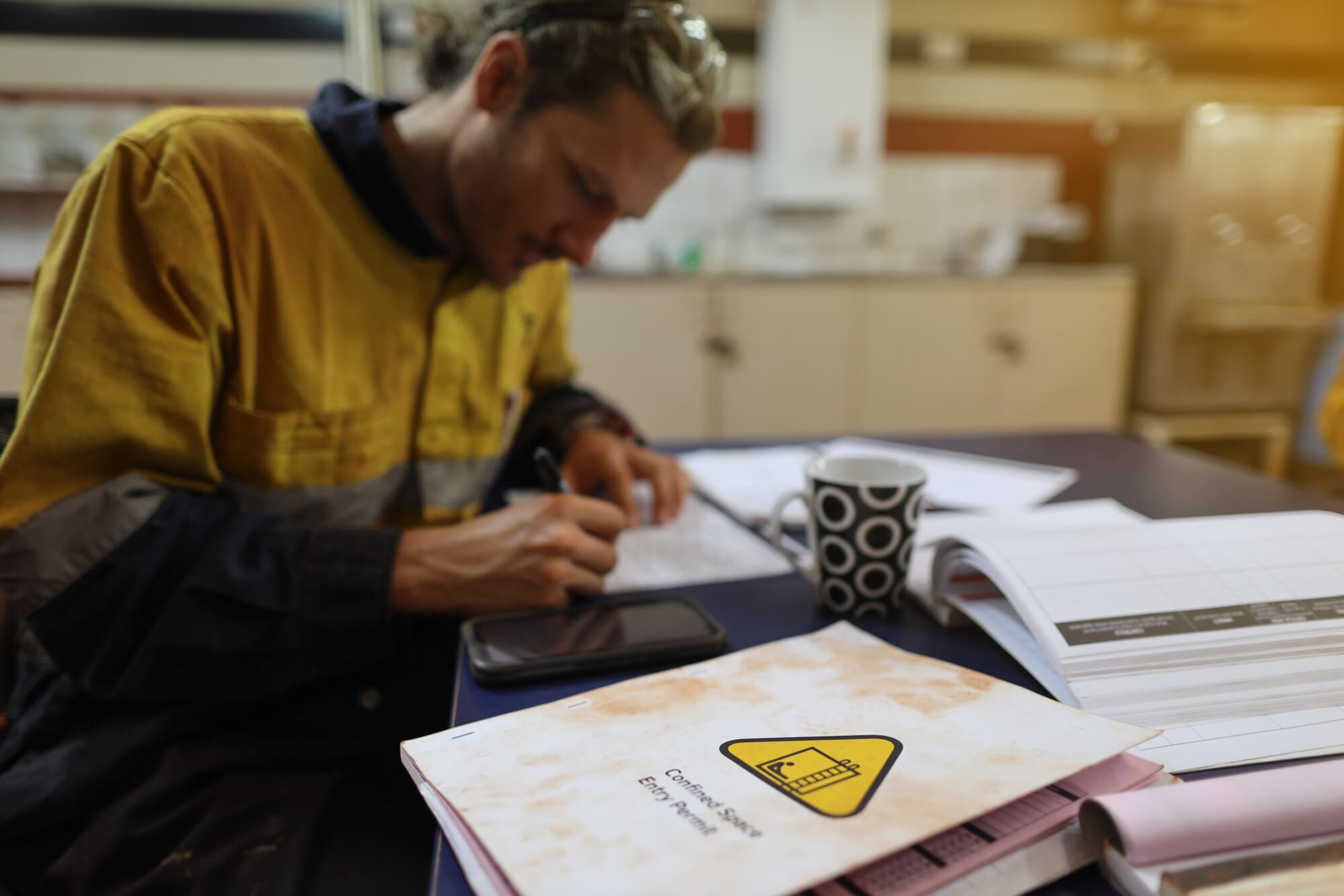
Regulatory Compliance
In the UK, the primary legislation covering safety in confined spaces is the Confined Spaces Regulations 1997. These regulations are designed to protect workers from risks associated with working in confined spaces. Key points include:
- Risk assessment – employers must carry out a risk assessment to identify hazards and evaluate the risks associated with confined spaces.
- Avoidance of entry – where possible, work in confined spaces should be avoided.
- Safe systems of work – if entry is necessary, a safe system of work must be implemented, which includes adequate training for workers, proper supervision, and ensuring appropriate equipment is available and is used correctly.
- Emergency procedures – emergency arrangements must be in place, including rescue plans and equipment.
In addition to the Confined Spaces Regulations 1997, several other pieces of legislation and guidance are relevant, including:
- Health and Safety at Work etc. Act 1974 (HSWA) – this Act places a general duty on employers to ensure, so far as is reasonably practicable, the health, safety and welfare of all employees.
- Management of Health and Safety at Work Regulations 1999 (MHSWR) – these regulations require employers to conduct suitable and sufficient risk assessments and to implement preventive and protective measures based on these assessments.
- Personal Protective Equipment at Work Regulations 1992 (PPEWR) – these regulations require employers to provide suitable personal protective equipment to employees where risks cannot be adequately controlled by other means.
- Provision and Use of Work Equipment Regulations 1998 (PUWER) – these regulations require that equipment provided for use at work is suitable for the intended use, safe for use, and properly maintained.
- Control of Substances Hazardous to Health Regulations 2002 (COSHH) – these regulations require employers to control substances that are hazardous to health, which can be particularly relevant in confined spaces where hazardous atmospheres might develop.
The Health and Safety Executive (HSE) also provides extensive guidance on working safely in confined spaces, including the Approved Code of Practice (ACOP) and guidance document L101, “Safe Work in Confined Spaces”, which elaborates on the requirements and practical measures for compliance with the Confined Spaces Regulations 1997.
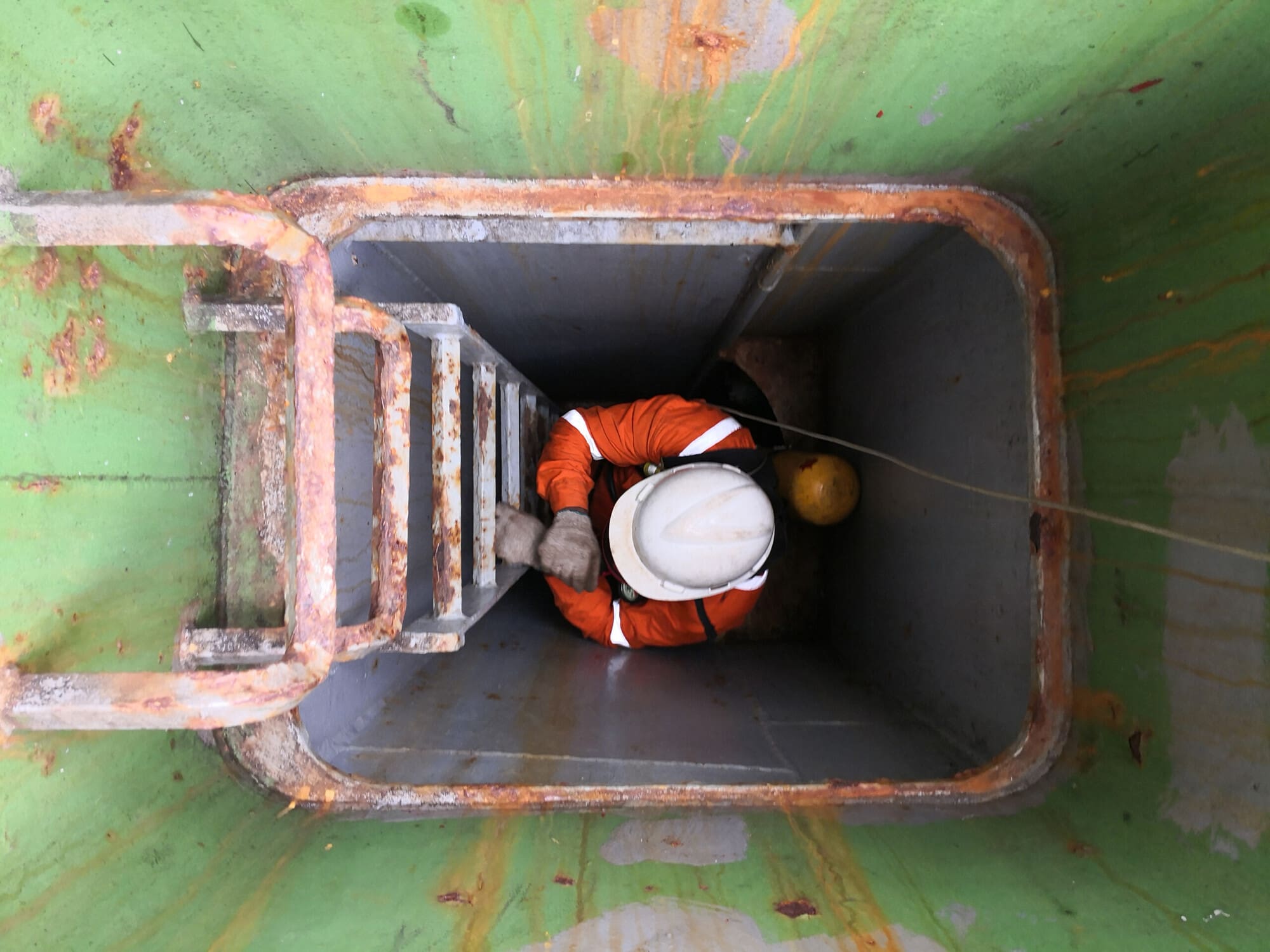
Conclusion
Confined spaces, by their very nature, present unique challenges and hazards that require meticulous attention and proactive management. The risks associated with these environments, such as limited access, poor ventilation and potential exposure to toxic substances, underscore the importance of rigorous safety protocols and comprehensive training for all personnel involved. Implementing robust entry procedures, continuous monitoring and emergency preparedness plans is crucial to safeguarding the health and well-being of workers. By fostering a culture of safety and adhering to regulatory guidelines, organisations can mitigate the inherent dangers of confined spaces, ensuring that tasks are completed efficiently and, most importantly, safely. As industries evolve and new hazards emerge, continuous education and adaptation will remain pivotal in protecting those who operate within these challenging yet essential environments.