In this article
A confined area is an enclosed space where there is a risk of death or serious injury from hazardous substances or dangerous conditions. Work in a confined space can pose a number of hazards as a result of restricted ability for movement, or potentially hazardous substances and/or atmospheres, including a higher than normal risk of fire, explosion, flood or asphyxiation.
Under the Confined Spaces Regulations 1997, a confined space can be any space of an enclosed nature, for example a space with limited openings where there is a risk of death or serious injury from hazardous substances or dangerous conditions, such as explosive atmospheres, poisoning or lack of oxygen etc. Some types of confined spaces include, but are not limited to:
- Storage tanks and vessels such as grain silos, bulk tanks etc.
- Enclosed drains and sewerage systems
- Open topped pits, chambers and vats such as a vehicle inspection pit in a workshop or garage
- Open topped chambers, chimneys and flues
- Combustion chambers in furnaces etc.
- Ductwork and ventilation shafts
- Hatchways, manholes and access shafts
- Lift shafts
- Plant and boiler rooms
- Controlled temperature stores
- Unventilated or poorly ventilated rooms or areas such as basements or cellars, roof and floor voids
- Industrial plant or machinery entered for maintenance or inspection purposes, for example laundry equipment such as large-scale washing and drying machines; ovens, kilns and drying plant; frozen or chilled storage areas such as chillers, freezers, and cold stores; combustion chambers and incinerators; fuel tanks etc.
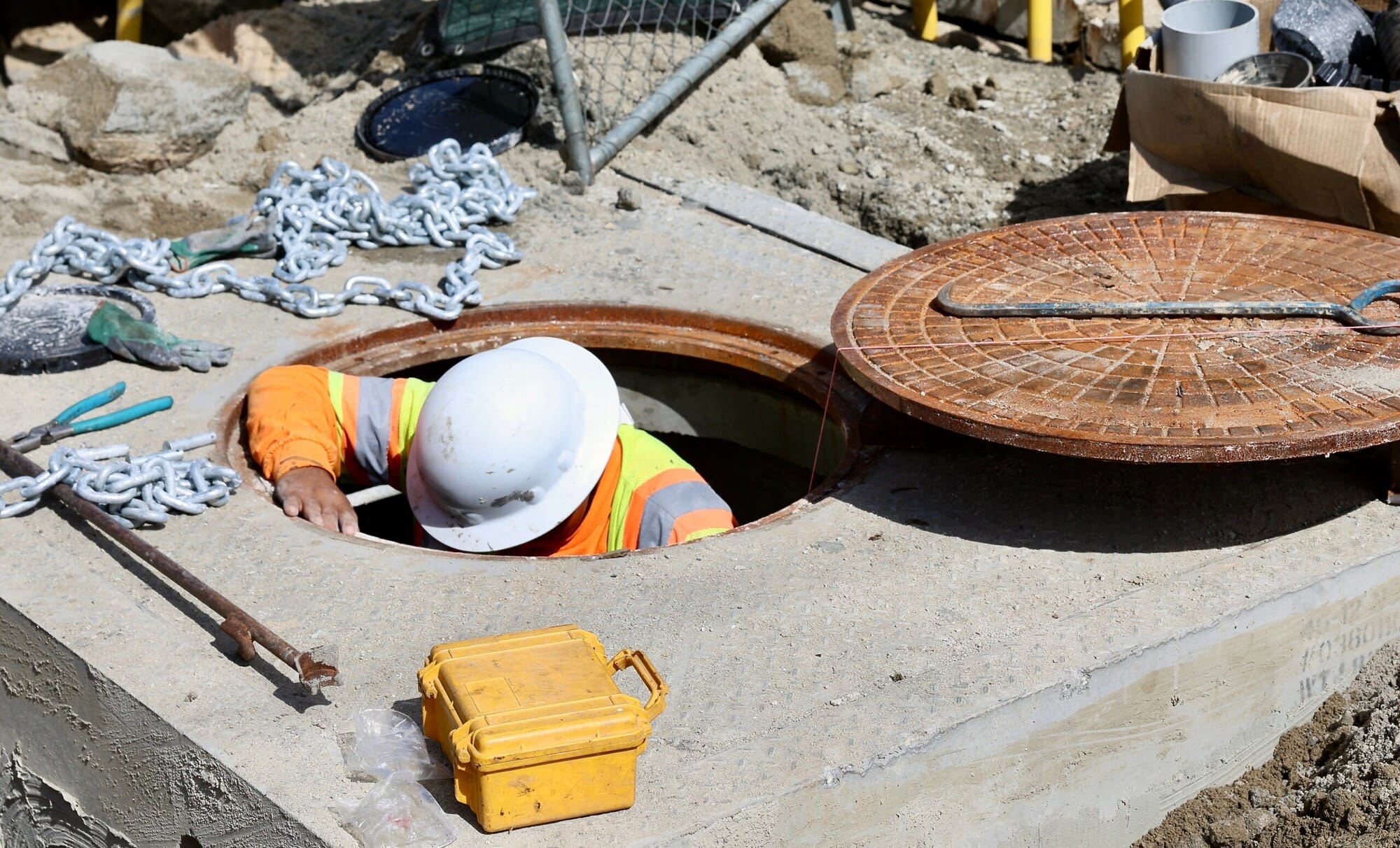
Confined spaces are present in most industries and workplaces. Some places are not ordinarily considered a confined space, but may become one when work is carried out, or during their construction, fabrication or subsequent modification.
When working in confined spaces, it is crucial to test the air and monitor the atmosphere to keep everyone safe. The RIDDOR fatal injury statistics from 2016/17 to 2020/21 show that 24 working people died as a result of drowning or asphyxiation in confined spaces and 134 workers were killed by being trapped by something collapsing or overturning; this includes trench collapse.
In confined space work, understanding and monitoring air quality and gas levels becomes paramount for ensuring the safety and well-being of workers, as the air around them may be quite different from the air outside. They may not know that they are in a life-threatening atmosphere, as colourless, odourless and tasteless gases may be present. These can be introduced into the atmosphere of a confined space through, for example:
- The use of cutting, burning and welding equipment
- The use of diesel-powered vehicles or equipment
- Leaking oxygen cylinders
- The oxidisation of metals
- Changes in weather conditions
These gases can mix with air to form a mixture that can explode, irritate, poison or asphyxiate workers.
In this article we will explore the importance of air quality monitoring in confined areas and its implications for worker health and safety.
Identifying Atmospheric Hazards
The air around us is also known as the atmosphere. It is colourless, odourless and tasteless and comprises approximately:
- 21% oxygen
- 78% nitrogen
- 0.9% argon
- 0.04% carbon dioxide and trace gases
Air quality in a confined space can quickly become compromised. Natural ventilation is not usually sufficient to maintain breathable air quality. In addition, air conditions in the confined space can change as work is performed. Performing hot work such as grinding can release particles into the air and decrease oxygen supply. The substances brought into the space for the work can also affect air quality.
A confined space risk assessment is a systematic process of identifying, evaluating and controlling the hazards associated with working in confined spaces. The risk assessment process, irrespective of the type of risk, involves a five-step process:
Step 1 – Identify the hazards or threats – these are things that could reasonably be expected to cause harm, and they will depend upon what type of risk is being assessed.
Step 2 – Decide who or what might be harmed and how – be clear about who or what might be harmed by each hazard or threat, as this helps to identify the best way of managing the risk.
Step 3 – Evaluate the risks and decide on precautions – can the risk be eliminated or what needs to be done to control the risk so that harm is unlikely?
Step 4 – Record the findings and implement them – a risk assessment report and implementation plan will enable everyone in the organisation to understand the risks and control measures that have been put in place. It is also important to keep this record in the event of compliance inspections.
Step 5 – Review the assessment and update if necessary – managing risk is an ongoing process that is triggered when changes affect the workplace. These changes may include, but are not limited to:
- Workforce changes
- Changing work practices, procedures or the work environment
- Purchasing new or used equipment or using new substances
- Planning to improve efficiency or reduce costs
- New information about the workplace risks becomes available
- Responding to concerns raised by employees, workers, contractors, clients, visitors or others at the workplace
Risk assessment is simply a careful examination of what could cause harm, i.e. a hazard or a threat, to someone or something, and requires making a judgement on the risk severity, so that the organisation can weigh up whether they have taken enough precautions to either eliminate or mitigate the risk, or whether they should do more to prevent harm.
A hazard or threat is anything that may cause harm. A risk is the chance, high, medium or low, that someone or something could be harmed by these and other hazards or threats, together with an indication of how serious the harm could be. There is a simple formula used:
Risk Severity = the probability of a risk materialising X the impact of a risk on, for example, the business, employee(s), client(s) and/or stakeholder(s) interests.
Probability is the likelihood that the risk might happen, and may be understood as:
- Low (Level 1) – a reasonably informed person would think it very unlikely this risk would materialise in the foreseeable future.
- Medium (Level 2) – a reasonably informed person would think there is a significant possibility this risk would materialise in the foreseeable future.
- High (Level 3) – a reasonably informed person would think there is a very significant or even likely possibility the risk would materialise in the foreseeable future.
Impact may be understood as:
- Low (Level 1) – any impact on the organisation as a business, its employees, workers, contractors, clients or stakeholders is minimal having regard to the importance of interests affected, impairment of function and duration. Typically, the impact is isolated and short-lived.
- Medium (Level 2) – any impact on the organisation as a business, its employees, workers, contractors, clients or stakeholders is significant having regard to the importance of interests affected, impairment of function and duration. Typically, the impact is limited to one function or group, but there is a material operational impact and the effects may continue.
- High (Level 3) – any impact on the organisation as a business, its employees, workers, contractors, clients or stakeholders is severe having regard to the importance of interests affected, impairment of function and duration. Typically, the impact impairs a critical function and/or has a systemic impact and the effects may be long-lasting or permanent.
Regular assessments of the conditions within and around the confined space should take place to identify, for example, what gases are or could be present, and to also assess which gases are potentially not present, such as a lack of oxygen. Carrying out an assessment of the risks to health and safety ensures that workers won’t be exposed to a risk, and if there is a risk, to make sure that it is controlled at an acceptable level.
In the case of identifying atmospheric hazards, hazardous atmospheres inside of a confined space are those that expose workers to the risk of incapacitation, injury, acute illness or death. The risk assessment process involves identifying potential hazards, such as toxic gases, lack of oxygen, extreme temperatures, or the risk of engulfment. Poor air quality and hazards posed by asphyxiates and toxic gases are some of the most common and deadly hazards faced in a confined space. Common causes include:
- Oxygen deficiency – the normal volume of oxygen in ambient air is approximately 21%. When the oxygen content is lower than normal air, for example when it is intentionally lowered for special applications, the resulting gas is called hypoxic air or low oxygen air. An asphyxiating or suffocating and therefore inadequate atmosphere is one which contains less than 19.5% oxygen. This is normally the pre-set alarm level for environmental monitors. Low levels of oxygen can be the result of open flame operations, such as welding, cutting or brazing, or natural phenomena present in swampy areas, sewers or landfills. Some materials, such as charcoal may absorb oxygen or consume it in their chemical reactions, such as rusting. In some cases, some gases, such as nitrogen, helium or carbon dioxide, have been intentionally used to purge an environment before work can be completed, and in doing so displacing oxygen.
- Flammable gases, vapours, and mists with more than 10% of its lower explosive limit (LEL) – flammable or combustible gas build-up in a confined space can lead to the most dangerous of situations. It doesn’t take long for a combustible gas, such as methane, to build up in a small confined area. Combine that with the right oxygen levels and all you need is a spark to cause a catastrophic explosion.
- Airborne combustible dust at a concentration that meets or exceeds its LEL – dust explosions occur when combustible dust is present, forms a dust cloud in an enclosed environment, and is exposed to oxygen and an ignition source. The explosion occurs as a result of the rapid burning of the dust cloud, which creates a rapid pressure rise in the enclosed area or confined space. A dust pile that may burn while an ignition source is being applied, then go out immediately or shortly after the ignition source is removed, can become lethally explosive when scattered and suspended in the air.
- Toxic gases – the most common toxic gases found in confined spaces are Volatile Organic Compounds (ppm VOC), Carbon Monoxide (ppm CO) and Nitrogen Dioxide (ppm NO2). They are usually the by-product of operations such as painting and gas or diesel generators. When found in excess, workers can experience acute issues like headaches, confusion and unconsciousness. Even at lower levels, workers can experience longer-term health effects.
There are many ways that you can mitigate the risks associated with working in confined spaces, including but not limited to:
- Avoiding the need for entry to the confined space – consideration should be given to carrying out the work without entry into the confined space, for example carrying out inspections of ducts via remote-controlled cameras, or installing closed-circuit television to monitor conditions within a confined space without having to enter, or cleaning tanks by using water jets and tools with long handles from outside the contained space.
- Having a safe system of work (SSOW) – this is a formal procedure that results from a systematic examination of a task in order to identify all the hazards. It defines safe methods to ensure that hazards are eliminated or risks are reduced to acceptable levels. This system includes the procedures, people, equipment, and materials that contribute to the execution of a task. These include procedures for entering and exiting the space, communication methods, use of tools and equipment, and emergency response.
- Having a Permit to Work (PTW) system – this is a formal written system and is required where there is a reasonably foreseeable risk of serious injury in entering or working in the confined space. The PTW procedure is an extension of the safe system to work, not a replacement for it. The use of a PTW system does not, by itself, make the job safe. It supports the SSOW, providing a ready means of recording findings and authorisations required to proceed with the entry. It also contains information on results of the gas testing, and other information that may be required during an emergency and which, when the job is completed, can also provide historical information on original entry conditions.
- All work in confined spaces should be carried out by a minimum of two persons. One person should act as the safety person and remain at the entrance to the confined space throughout the work. An adequate communication system must be in place and should enable communication between those inside the confined space and those outside, and to be able to summon help in case of emergency.
- Personal Protective Equipment (PPE) such as respiratory protection plays a crucial role in reducing the risks associated with air quality when working in confined spaces.
- Some confined spaces require mechanical ventilation to provide sufficient fresh air to replace the oxygen that is being used up by people working in the space, and to dilute and remove gas, fume or vapour produced by the work.
- Cleaning and removing residues in confined spaces can significantly reduce the risks associated with working in these environments.
- Workers must have adequate training and experience in the particular work involved to be competent to work safely in a confined space. Training standards must be appropriate to the task, and to the individual’s roles and responsibilities, so that work can be carried out safely. Where the risk assessment indicates that properly trained individuals can work for periods without supervision, checks should be made that they are competent to follow the established safe system of work and have been provided with adequate information and instruction about the work to be done.
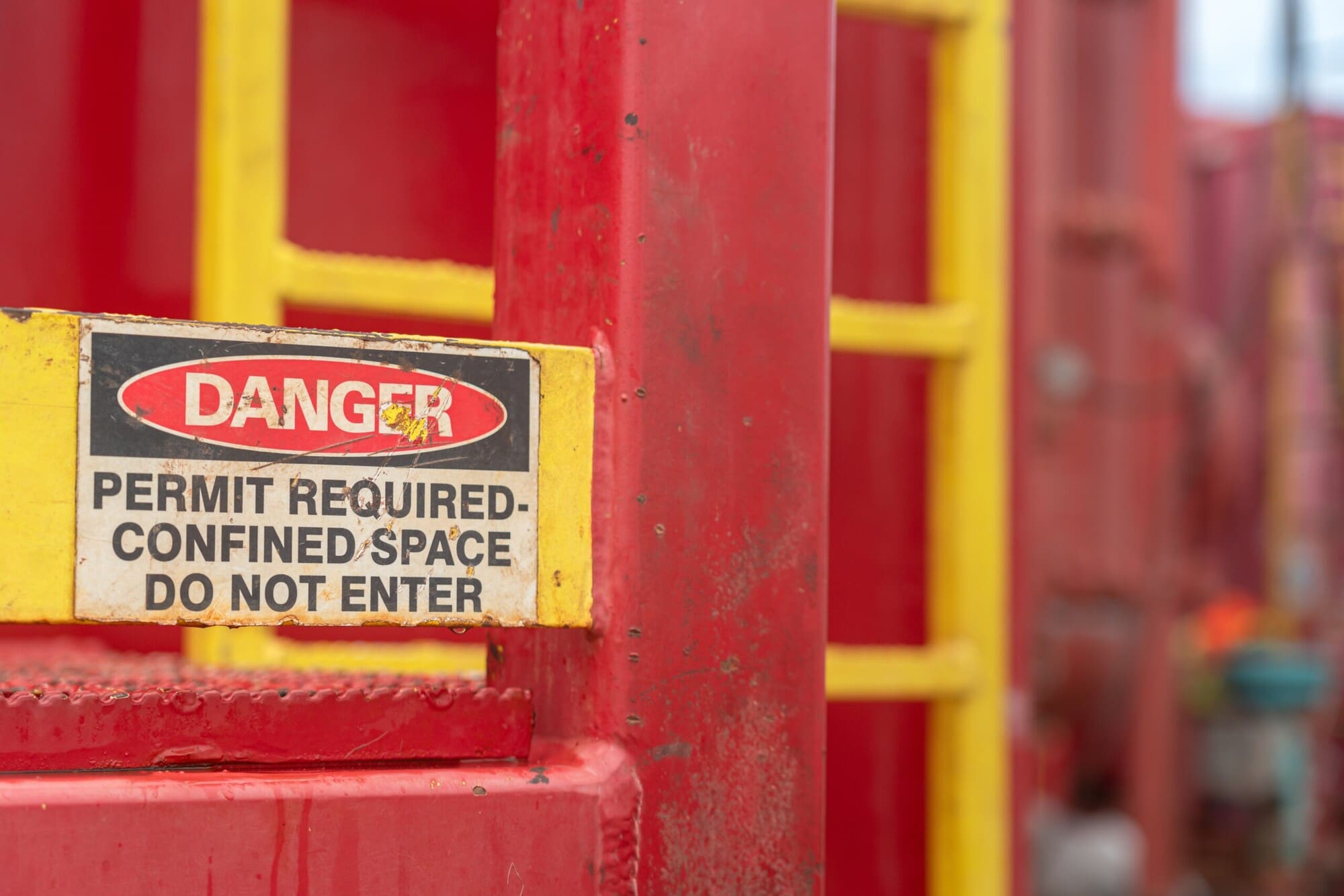
Prior to entry, the atmosphere within a confined space should be tested to check the oxygen concentration or for the presence of hazardous gas, fume or vapour. Regular or continuous monitoring might be needed while work is being carried out in a confined space if there is a possibility that the atmosphere may deteriorate during this time. Testing equipment must be suitably calibrated and well maintained. Wherever possible, tests should be carried out without entering the confined space, for example by using instruments with long handles. The tests should be carried out only by people who:
- Are competent
- Understand what constitutes a safe atmosphere to work in
- Have received training regarding the risks
- Are able to interpret the results
- Have the authority to allow them to take appropriate action as a result of the testing.
Testing should also be carried out where knowledge of the confined space indicates that the atmosphere might be contaminated, for example from information about its previous contents or chemicals used in a previous activity in the space, or to any extent unsafe to breathe, or where any doubt exists as to the condition of the atmosphere. Testing should also be carried out if the atmosphere was known to be contaminated previously, was ventilated as a consequence, and needed to be tested to check the result. Where the assessment has identified the presence or possible presence of flammable or toxic gases or vapours, there may be a need to purge the gas or vapour from the confined space.
Preventing Accidents and Health Risks
When working in confined spaces, it is crucial to test the air and monitor the atmosphere to keep everyone safe. Regularly monitoring the air quality helps detect any changes that might indicate the presence of harmful gases or lack of oxygen, allowing employers and/or employees to take necessary actions to protect themselves and their workforce, and to limit time inside the confined space if needed.
The main dangers associated with working in confined spaces include:
- Asphyxiation from a lack of oxygen, for example from the presence of a contaminant, a chemical reaction, or displacement of oxygen in the atmosphere etc.
- Inhalation of poisonous gases, dusts, fumes or vapours, for example from contents that are present and can build up over time, are disturbed or those that enter the space from connecting pipes, residues left in tanks, vessels etc. or remaining on internal surfaces which can still give off gas, fume or vapour if not cleaned properly.
- Drowning in liquids and solids which are present or can suddenly fill the space, for example free flowing solids such as grain that has partially solidified or bridged in silos which then collapse unexpectedly when walked on.
- Fire and explosions, for example from flammable vapours, excess oxygen, hot work, high concentrations of dust etc.
- Overheating from the hot conditions inside the confined space, leading to a dangerous increase in body temperature.
The effects that a reduced oxygen content, or the presence of toxic gases, dusts, fumes or vapours, can have on workers include:
- Dizziness
- Shortness of breath
- Increased heart and respiration rate
- Diminished concentration and reasoning
- Ability and awareness to make recovery decisions highly impaired
- Nausea
- Vomiting
- Muscular incapacity
- Rapid loss of consciousness
- Death
Many who have been involved in incidents and accidents in confined spaces may suffer long-term effects including Post-Traumatic Stress Disorder (PTSD).
In July 2004, the Health and Safety Executive (HSE) issued an urgent warning following a spate of deaths involving confined spaces, which happened in quick succession over four months. In one incident three workers on a farm near Thetford, Norfolk, died as a result of being overcome by carbon dioxide while working in a slurry tank. A fourth worker, who was also overcome by fumes, was rescued from the tank.
In Hereford, two workers died while working in a pit used in manufacturing and associated with a high-pressure special atmosphere furnace. The workers died due to lack of oxygen. Two months earlier, a worker in West Thurrock, Essex, died during an incident which occurred as he welded the inside of a petrol tanker.
Prior to entering a confined space, the air must be tested and monitored. This includes checking:
- The proper levels of oxygen
- That no combustible gases are present
- That toxic gases are below the permissible working limits
When testing and monitoring, samples need to be taken of the air at the top, middle and bottom of the confined space as the gases and vapours will vary in concentration. Depending on the density of the gas, you may find highly concentrated levels at the top or very bottom of the workspace, and you must sample the air at a distance from the opening to the confined space. This is because the air from outside will give you a false sense of adequate oxygen presence.
To carry out these atmospheric tests requires monitoring equipment to be in good working order. Where necessary, it must be calibrated and tested at least in accordance with the manufacturer’s recommendations, or in line with some other schedule that may differ from the manufacturer’s requirements, such as that identified from the findings of the risk assessment. Testing and calibration should be included in daily operator checks, where identified as necessary.
The advancement in technology has led to the integration of internet-connected devices and systems into emergency management and response. The adoption of AI-based solutions for confined space monitoring represents a significant advancement in industrial safety across the construction, manufacturing, oil and gas and mining sectors. By providing continuous, real-time surveillance, predictive analytics, and data-driven insights, AI enhances the ability to detect and respond to hazards, ensuring a safer working environment.
Real-time alerts have emerged as a game-changer for enhancing worker safety. By delivering critical information instantaneously, they play a crucial role in preventing accidents, ensuring swift responses to potential dangers, and cultivating a proactive safety culture. Real-time monitoring and analysis of air quality and exhaust emissions gives an accurate record of exposure levels which can be mapped to workflow patterns and machinery operations and movements in order to identify specific pollution sources.
Compliance with Safety Regulations
In the UK, there are specific duties and responsibilities for the employer and employees regarding health and safety when working within confined spaces under the following Acts and Regulations:
- Health and Safety at Work etc. Act 1974 (HASAWA) – this requires employers to ensure the health and safety of all employees and anyone who may be affected by their work, including any and all visitors to any part of the employer’s premises. This includes taking steps to control confined spaces risks. Employees must not endanger themselves or others and must use any safety equipment provided. Manufacturers and suppliers of equipment such as, but not limited to, PPE, have a duty to ensure that their products are safe. They must also provide adequate information about appropriate use.
- Management of Health and Safety at Work Regulations 1999 – these build on the HASAWA and include duties on employers to assess risks and where necessary take action to safeguard health and safety.
- Confined Spaces Regulations 1997 – the regulations place duties on employers, the self- employed and any person who controls the work of others, for example Health and Safety managers, facilities managers or building owners who may contract others to work in confined spaces, to the extent they control the work. It requires that work is undertaken safely and that the risks presented by confined spaces are adequately controlled. The regulations have an accompanying Approved Code of Practice (HSE L101) that has special legal status and contains further detail on the requirements for managing work in confined spaces. HSE L101 Regulation 4 Work in Confined Spaces, specifically details requirements for testing/monitoring the atmosphere.
- Personal Protective Equipment at Work Regulations 1992 and Personal Protective Equipment Regulations 2002 – the main requirement of the PPE at Work Regulations is that personal protective equipment is to be supplied and used at work wherever there are risks to health and safety that cannot be adequately controlled in other ways.
The following regulations apply to confined spaces within machinery:
- Provision and Use of Work Equipment Regulations 1998 (PUWER) – the regulations require that equipment is safe, suitable, maintained, inspected and installed correctly. PUWER also requires that equipment is used only by competent people when it is safe to do so.
- Workplace (Health, Safety and Welfare) Regulations 1992 – these regulations place duties on employers in respect of all workplaces, or any premises used as a place of work, under their control.
Legislation covering enclosed spaces on sea-going vessels includes:
Merchant Shipping and Fishing Vessels (Entry into Enclosed Spaces) Regulations 2022 and Code of Safe Working Practices for Merchant Seafarers COSWP, Ch 4 (Emergency Drills and Procedures) and Ch 15 (Entering Dangerous (Enclosed) Spaces).
The Occupational Safety and Health Administration (OSHA) is a regulatory agency of the United States Department of Labor (sic). OSHA 1910.146 has set standards that employers and employees must follow when working in confined spaces. OSHA provides a few requirements that employees should know when it comes to highlighting the hazards associated with any confined space. They should understand the following hazards that could be present such as:
- Toxic atmospheres that cause various acute health effects.
- Oxygen deficiency environments that displace air by another gas.
- Oxygen enrichment environments that can result in an increased risk of fire or explosion.
- Flammable atmospheres that can present a risk of explosion or a suspension of combustible dust in air.
- Flowing liquid that can cause drowning, suffocation, burns or injury.
- Excessive heat that can increase the risk of heat stroke or cause an employee to heat collapse from heat stress.
In the European Union (EU), the European Agency for Safety and Health at Work (EU-OSHA) is the EU equivalent of the UK Health and Safety Executive (HSE). The EU has not introduced any legislation specifically relating to work in confined spaces, with the exception of temporary or mobile construction sites. EU Directive 92/57/EEC sets the measures for protecting workers’ health and safety when working in confined spaces in temporary or mobile construction sites. It covers risk assessment, control measures and training requirements.
Failure to comply with the regulations can result in enforcement action, including improvement notices, prohibition notices, or prosecutions. Non-compliance can lead to significant fines or other legal consequences. Below are examples of compliance breaches that led to fatalities or injuries to workers in combined spaces.
In December 2016, worker Nathan Walker was instructed by managers at Greenfeeds Limited in Leicester to clean a slurry tanker containing semi-liquid pig feed by entering the tank and using a pressure washer to clear the residue. On entering the tank, Mr Walker was overcome by the fumes and quickly became unconscious. His colleague Gavin Rawson attempted to assist him but also became unconscious due to the carbon dioxide inside the tanker. Both workers drowned and were very sadly pronounced dead at the scene.
Greenfeeds Limited was found guilty of corporate manslaughter, on the basis that the two deaths were caused by gross failings in the management of the organisation, including a failure to respond to concerns raised by staff about the dangerous practice of entering the slurry tankers. The organisation was fined £2 million. Greenfeeds Limited was also found guilty of an offence contrary to section 2 of the Health and Safety at Work Act 1974 (HSWA 1974), having failed to take all reasonably practicable steps to ensure the health, safety and welfare of its employees. One of the directors, Gillian Leivers, was found guilty on a personal basis of gross negligence manslaughter. Transport manager Stewart Brown was handed a twelve-month suspended sentence for breaching section 7(a) of the HSWA 1974, having failed to take reasonable care for the health and safety of Nathan Walker and Gavin Rawson through his actions and omissions as an employee.
On 29 August 2017, three workers were conducting preparatory work in a sewer for the Thames Tideway Tunnel at East Greenwich, which is controlled by Thames Water Utilities Limited (Thames Water). The workers were engulfed when a 150-year-old cast iron gate failed, carrying them along the sewer. The three workers suffered minor physical injuries but have been mentally affected. One worker suffers from long-term traumatic stress and has been forced to continue working in his specialised career. HSE found that Thames Water failed to properly coordinate work activities. The permission and authorisation system had been “fragmented”, it said. Thames Water Utilities Limited pleaded guilty to breaching Regulation 3(1)(b) of the Confined Spaces Regulations 1997 and was fined £300,000 with costs of £16,419.
Kettering General Hospital NHS Foundation Trust was fined £480,000 after an employee lost consciousness and suffered a brain injury while unblocking a drain. The man was discovered in a manhole on the hospital site by other staff members on 1 February 2022. He was rescued by Northamptonshire Fire and Rescue Service and treated in hospital for acute sulphate intoxication. This resulted in a traumatic brain injury and ongoing issues with memory loss and nerve damage.
A Health and Safety Executive (HSE) investigation found that Kettering General Hospital NHS Foundation Trust had failed to identify the manhole as a confined space, and had not carried out a proper risk assessment of the activity. The Trust failed to prevent employees from entering confined spaces at the site, says HSE, and did not identify a safe system for clearing blocked drains.
The average fine for breach of health and safety law in 2017/18 was £147,000, with total fines exceeding £72 million. Even if a business can weather such significant financial penalties, the reputational impact can be a cost from which some businesses may never recover.
Promoting Worker Health and Well-being
Ensuring the health and safety of every employee on a day-to-day basis is, and should be, a top priority to every business. Workers who feel protected by effective occupational health and safety management are healthier, more motivated, and ultimately more productive at work. Health and safety policies and risk management plans encourage workers’ commitment to safety and they have a positive impact on their attitudes towards work in general.
Proactive safety management of air quality monitoring which involves inspections, regular testing and monitoring, ongoing training, near-miss reporting and active supervision will all form part of a proactive safety management structure. This will create a positive safety culture throughout the business, help to prevent accidents from occurring, and improve overall well-being and health and safety.
There are also cost benefits to proactively managing air quality safety. According to Asthma + Lung UK, lung conditions cost the UK economy a staggering £188 billion a year, with £9.6 billion direct costs to the NHS. Indirect costs associated with lost productivity from people requiring time off work for their own health, or to care for a loved one, amounts to £4.2 billion.
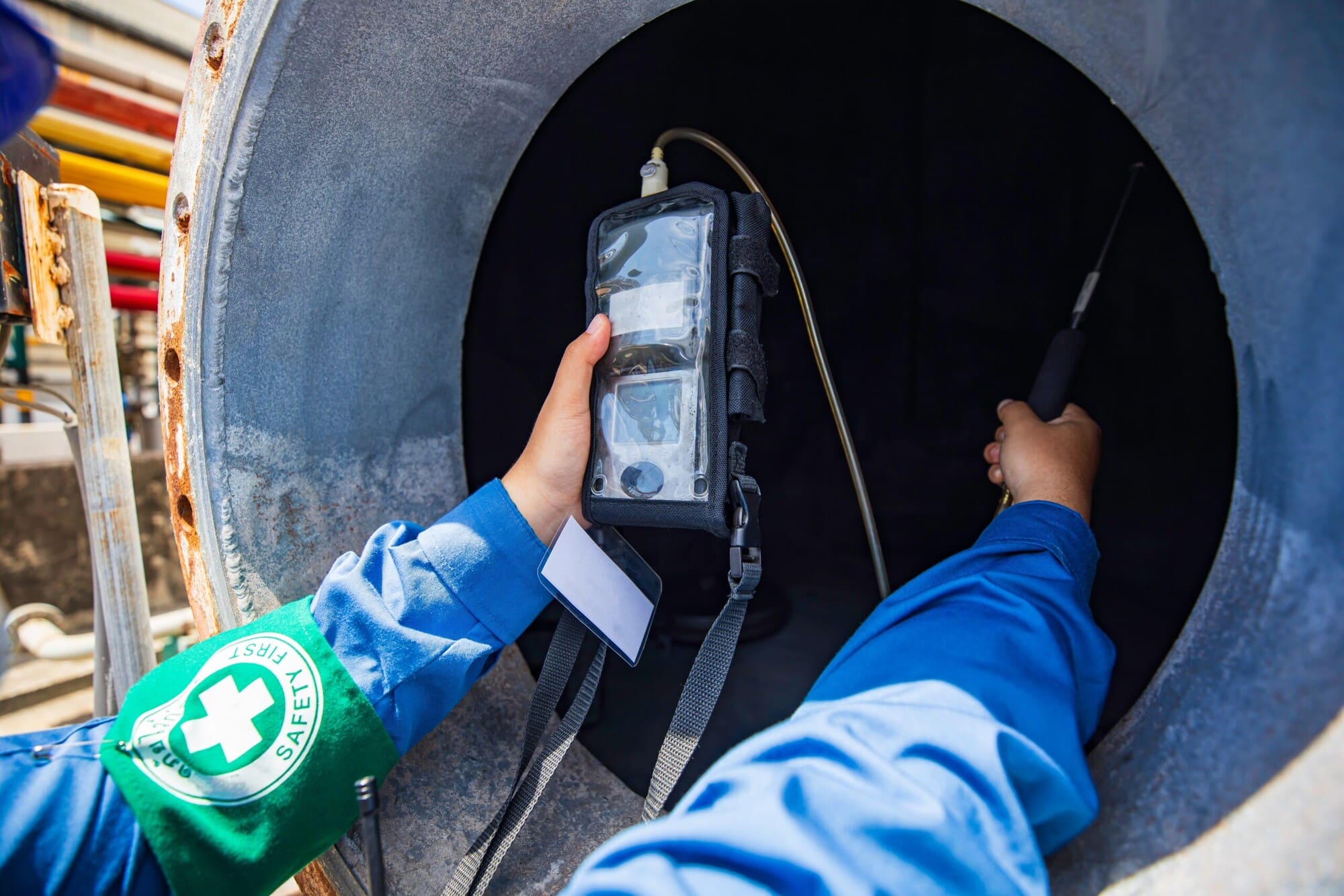
Conclusion
Many workplaces contain spaces that are considered to be ‘confined’ because their configuration, or hazards within them, hinder or present risks to the activities of any employees who must enter into, work in and exit from them.
There are specific statutory responsibilities for the employer to ensure that it provides a safe working environment in any confined space by ensuring that potential hazards are identified, a suitable and sufficient risk assessment is carried out, a safe system of work is developed and managed, and ensuring all necessary precautions, equipment and emergency procedures are taken.
There are also specific statutory responsibilities for workers to ensure that they comply with policies, procedures, safe ways of working developed through risk assessment, and any requirements of a permit to work set out by the employer to safeguard them from harm when working in confined spaces.
In this article we have looked at the importance of carrying out robust risk assessments in order to identify, assess, eliminate and/or mitigate risks associated with working in confined spaces. We have also highlighted above some very clear examples of where the HSE have investigated and prosecuted employers for not prioritising air quality safety in confined spaces, and the dire implications that these incidents had for the workers involved.
By following the risk assessment process and implementing control measures, employers can reduce the risks associated with confined spaces and create a safer working environment.