In this article
Abrasive materials are used in many situations and by many industries for various purposes. One of the most common types of abrasive materials used is sandpaper. Sandpaper is made from a paper or cloth backing with an abrasive material adhered to the surface. Another common type of abrasive material is abrasive wheels.
Abrasive wheels are designed for cutting and grinding hard materials such as metal and concrete. They are commonly found in workshops and industrial factories throughout the UK. One of the key advantages of abrasive wheels is their versatility. They can be used for a wide variety of tasks, such as shaping, cutting, grinding, sanding, polishing and cleaning, and are used in many industries such as construction, foundries and engineering generally. Abrasive wheels are also used outside of workplace settings, such as for DIY work at home.
Although abrasive wheels are relatively easy to use and to maintain, it won’t come as a surprise to learn that they can cause accidents. The Royal Society for the Prevention of Accidents (ROSPA) accident surveillance systems data ranked angle grinders, a type of abrasive wheel, as the third most dangerous tools, with 5,400 injuries recorded annually. The vast majority of these injuries are caused by a shattering of the abrasive wheel. A substantial number of these injuries were not occupational injuries. They often occurred when individuals were using this tool outside of a work context at home etc.; 44% of the patients treated were retired.
This is why anyone operating an abrasive wheel should be familiar with the equipment, undergo appropriate training, and recognise the hazards in order to use them safely.
What are abrasive wheels?
Abrasive wheels are precision tools with grains on the outer circumference which effectively create thousands of cutting points as the wheel spins. Put simply, abrasive wheels are revolving wheels, cylinders, discs or cones made of abrasive particles, which have been bonded together, using inorganic or organic substances. Inorganic bonds such as clay, glass, porcelain, sodium silicate, magnesium oxychloride or metal, are generally fired in a furnace to give the bond a hard, strong but brittle structure. These wheels are used for precision grinding applications as they hold their shape, but require dressing. Dressing an abrasive wheel means removing the very outer surface of the wheel so that a new sharp surface can be exposed. This is because over time the outer edge will blunt. Ways to dress the wheel depend on what the wheel is made of.
Organic bonds, for example resin, rubber and shellac, are not fired but are cured at low temperatures. Such wheels are tough, shock-resistant and self-dressing, and are most suited to non-precision applications, for example fettling and cutting off. Only organic-bonded wheels should be used for portable and handheld grinding machines. Those intended for cutting-off operations should additionally have some form of reinforcement, usually fibreglass.
Types of abrasive wheels
Abrasive wheels come in a large range of sizes and configurations, with each being suited to different tasks and functions such as grinding, finishing, cleaning, cutting, buffing etc. The main aspects of an abrasive wheel are:
- Grit size – this means the particle size of abrasive grains. The range is expressed by number, for example very coarse 4 to very fine 1200.
- Coating material bonding – this means the bonding material used in the wheel construction.
- Abrasive type – this means the type of abrasive used in wheel construction.
- Grade of the wheel – this represents the tenacity with which the bonding material holds the abrasive grain in a wheel. Wheels are graded as soft or hard according to their degree of tenacity. The grade scale is expressed in letters from A which is extremely soft to Z which is extremely hard.
- Wheel structure – this means the level of porosity in the wheel. The higher the number, the greater the level of porosity.
The Health and Safety Executive (HSE) lists 33 different types of abrasive wheels. In general, the most commonly used types of abrasive wheels are:
- Type 1 Straight Grinding Wheels – straight wheels are a common type of revolution found on pedestal or bench grinders. It is often also widely used for centreless and cylindrical surface grinding operations.
- Type 2 Cylinder or Wheel Ring – this type of wheel doesn’t have middle mounting support, but it sits on an extended and wide surface. They’re mainly utilised in horizontal or vertical spindle grinders for producing flat surfaces.
- Type 4 Tapered Grinding Wheels – a sharp emery wheel may be a straight wheel that tapers externally towards the wheel’s midpoint. A straight wheel with a sharp wheel is usually used for gear teeth, grinding threads, etc. In tapered cup wheels the sides taper outwards, providing extra strength and therefore accepting higher lateral loads. Both types are primarily used in tool and cutter grinding.
- Type 6 Straight Cup – this straight cup wheel is employed as an option for cup wheels in cutters and gear grinders. It has an additional radial grinding surface, which can be beneficial in some applications.
- Type 9 Segmented Wheels – grinding wheel segments are generally used to grind flat stock or flat surfaces within a workpiece for anything from heavy stock removal to precision grinding.
- Type 12 Dish Cup – this type of wheel is suitable for jug grinding and cutter grinding. It only cuts in crevices and slots because it features a skinny cup-style grinding.
- Type 13 Saucer Grinding Wheels – saucer grinding wheels are used for grinding twist drills and milling cutters. It is often particularly in demand in non-machining areas because the saw filers are employed by saucer wheels to take care of saw blades.
Abrasive wheels are used in two main types of machines, pedestal and portable. A pedestal grinder has a mounted wheel that sits within a pedestal. The pedestal is either bolted to the floor or sits on rubber feet. These types of grinders are often used to sharpen cutting tools and to work extremely hard materials. Portable grinders are handheld devices, such as angle grinders. They are widely used in metalworking and construction, as well as by the emergency services. The types of machines that are mostly associated with abrasive wheels are:
- Angle grinders – also known as disc grinders or side grinders, used to cut or polish hard materials
- Belt grinders – mounted tabletop grinders with two different types of grinding wheels on each side, which can sharpen tools and are used for roughing or finishing
- Cylindrical grinders – used to shape the exterior of rods, tubes or bearing races
- Jig grinders – heavy machines used for complex grinding and cutting work
- Table saws – sometimes called bench saws, these are used for cutting wood
- Chop saws – handheld tools used to make straight cuts in wood
- Petrol cut-off saws – handheld tools used to cut concrete, steel, stone, asphalt and other materials
Every wheel must adhere to the British Standard (BS EN 12413 and BS ISO 525) system for marking. Manufacturers mark all wheels with the type, size, specification and the maximum operating speed of the wheel. The fundamental markings that a wheel should have are:
- Trade Mark
- Test Record
- Restriction for Use
- Expiry Date
- Speed Stripe
- Dimensions in mm
- Specification Mark
- Code Number
- Maximum Operating Speed
- ISO Type No. (shape)
- Mounting Instruction
All organic-bonded wheels for handheld applications will bear a use-by date of three years from the date of manufacture. A code number should be marked on the wheel to indicate the source and manufacturing details of the wheel.
Wheels should be of the correct diameter and speed rating for the machine, and of the correct material and hardness for the tasks to be performed. Selecting the appropriate wheel for the job is equally important for efficient production and for safety.
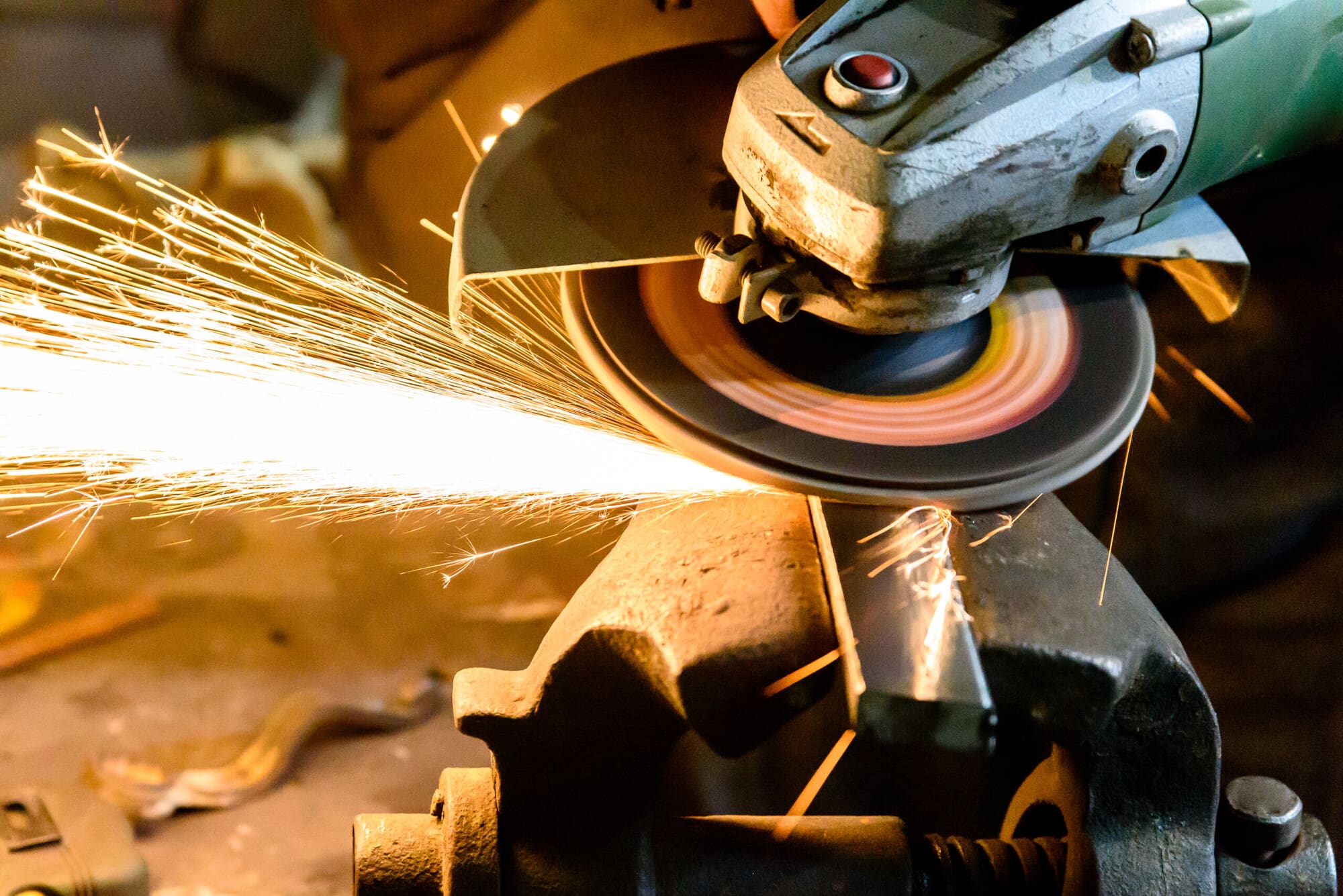
Components of abrasive wheels
The components of abrasive wheels, although similar, differ slightly between pedestal abrasive wheels and portable abrasive wheels such as angle grinders. The components for both are summarised below:
Pedestal abrasive wheels
The machine – the actual grinding machine must be a correctly manufactured piece of equipment. The abrasive wheel must be mounted on the machine for which it is intended. Do not use makeshift equipment. The machine must also be safe from all perspectives not just an abrasive wheels’ perspective.
The spindle – spindles must run true in their bearings and rotate freely, be long enough and sufficiently threaded to allow the nut to be fully engaged when the flanges and the abrasive wheel are fitted. When the wheel is secured by a single central spindle nut, the thread should be such that the nut direction of tightening is opposite to the rotation of the wheel to ensure the nut will not come loose as the wheel rotates, as stated in HSG 17. The thread should extend into the flange but not into the hole in the abrasive wheel. All pedestal grinding machines must have guards designed for the machine fitted before use.
Machine bearings – these must be maintained in good order and be free from defects and wear.
Flanges – these secure the abrasive wheel and should be a matched pair of equal diameter and at least 1/3 of the wheel diameter. The flanges must be recessed or undercut such that there is no pressure on the edge of the hole in the wheel. The driving flange is only to be secured by friction on bench-mounted machines of less than 560w; for all other machines the drive flange should be secured to the spindle by a key or similar. Flanges must be free of defects and the bearing surface free of burrs or defects.
Blotters – the blotter is used to distribute the clamping forces. Blotters are sometimes secured to the wheel but can be supplied loose. The blotter should be free from wrinkles or other defects. Certain types of wheels do not require a blotter. These are:
- Mounted wheels and points
- Abrasive discs with inserted nuts, or cylinders
- Plate mounted wheels
- Cylinder wheels mounted in chucks
- Rubber bonded cutting-off wheels 0.5mm or less in thickness; taper-sided wheels
- Wheels with threaded inserts
Wheel bushes – these are used to adapt the wheel hole diameter to that of the spindle. These should not come into contact with the flange. New bushes should be used if required when fitting a new wheel. Always use the correct bush for the wheel.
Portable abrasive wheels such as angle grinders
The machine – the actual grinding machine must be a correctly manufactured piece of equipment. The abrasive wheel must be mounted on the machine for which it is intended. Do not use makeshift equipment. The machine must also be safe from all perspectives not just an abrasive wheel perspective.
The spindle – spindles must run true in their bearings and rotate freely, and be undamaged, especially in respect of the threads. The threads should be undamaged for their full length. The base of the spindle should be matched to the bottom flange so the spindle seats correctly. The spindle should be long enough to allow the top flange to engage fully on the thread.
Machine bearings – these must be maintained in good order and be free from defects and wear.
Wheel lock mechanism – these secure the abrasive wheel and should be a matched pair which were supplied with the machine. The flanges must be recessed or undercut such that there is no pressure on the edge of the hole in the wheel. The undercut is shown. The top flange is different on both sides. This is to allow for the difference in thickness between cutting wheels that are thinner and grinding wheels which are thicker. Both have metal reinforced centres. Note that the top flange is threaded.
Safety precautions when working with abrasive wheels
Abrasive wheels carry some of the most dangerous risks of any type of equipment in the workplace and accidents involving abrasive wheels are often severe. The use of abrasives can create immediate safety hazards as well as long-term health hazards. If not properly managed and controlled, the routine use of abrasives can potentially create hazards from injury, airborne particles, noise and hard-arm vibration.
Rules and procedures should apply to the use of any abrasive wheels or grinding equipment owned or hired by a company and to work undertaken by employees, whether temporary, permanent or contractors. It should also apply to all operators, maintenance workers and other staff in order to minimise risk to themselves and all other persons working on, or visiting, the premises or site.
User inspection of both tool and task should be required. All tools that drive abrasive wheels need to be regularly examined.
Only authorised and trained persons should operate abrasive wheels. It is good practice to display a notice next to fixed wheels identifying who is authorised to use them. In some situations, for example where contractors share a workshop with employees, fixed abrasive wheels should be locked off to prevent unauthorised use.
The written, safe system of work should be incorporated into training programmes for operators and maintenance workers, with relevant parts incorporated into induction training for other staff, and instructions to contractors or other persons visiting the site, for example emergency procedures and first-aid arrangements.
For the wheel to be used, there has to be an area of it exposed to enable contact with the workpiece. However, it is important that this unprotected area of the wheel is kept to the smallest amount practicable. The following hierarchy of control measures in the Provision and Use of Work Equipment Regulations Act 1998 (PUWER) should be applied:
- Fixed guarding
- Moveable guarding, such as an interlocked guard or Perspex adjustable guard
- A means to keep the operative away from the danger, such as by the use of jigs or holders
- Procedural means of risk control, including adequate instruction, information and training
The measures are to be taken in order “to the extent that it is practicable to do so” before considering the next adequate measure. The guarding used to protect the operator from ejected particles will control some of the risk of contact with the wheel, but not all.
In the context of the use of an abrasive wheel, the written copy of the risk assessment should show that each of these means of risk control has been considered.
Abrasive wheels should be fit for purpose. Wheels to BS EN 12413 and BS ISO 525 standards will be marked to indicate specific restrictions for use, which are:
- RE1 Not permitted for handheld machines and manually guided grinding
- RE2 Not permitted for handheld cutting-off machines
- RE3 Not permitted for wet grinding. Abrasive product only suitable for dry grinding
- RE4 Only permitted for totally enclosed working area
- RE6 Not permitted for face grinding
They should only be operated with the correct type of tool and should not exceed the maximum operating speed. Examples of incorrect abrasive usage are:
- Over-speeding – doubling the speed increases wheel stress by four times, which increases the risk of the wheel bursting
- Incorrect mounting
- Used without proper machine guarding
- Lack of personal protective equipment
Poor storage or wheel selection, improper mounting, extreme out-of-balance conditions or speed, grinding machine defects, or misuse in the grinding operations are all factors that can result in wheel breakage or wheels becoming jammed and can cause the ejection of the broken wheel pieces created, throwing out pieces at high velocity in all directions, potentially causing serious injury.
Repairing the equipment also poses many risks to the person carrying out the maintenance and anyone using the machinery afterwards. Only those with the correct training should be performing repairs.
Adequately strong guards should cover as much of the wheel as practicable, as many ejected particles are likely to have sharp edges, be dangerously hot, and have a high energy of ejection. The extent to which the guard covers the wheel is likely to be greater with a fixed wheel rather than one that is used as a portable hand tool, such as an angle grinder.
Guards can be fixed in position or can be adjustable, and should ensure that the wheel is enclosed to the greatest extent possible, keeping the opening size minimised, by compensating for wheel wear. Protection against ejected material can be achieved by a properly constructed and adjusted transparent moveable guard; however, supervisors must enforce/encourage the use of the guards, and frequent inspection, cleaning and maintenance of the guards should be carried out.
Ejected materials can take many forms, including:
- Ground-off fragments of the workpiece
- Sparks – the heat generated from the friction of the wheel on the workpiece is likely to be sufficient to ignite even ferrous metals
- Small particles from the wheel that are broken off during the abrasive action on the workpiece
- Airborne particles – these are potentially hazardous to workers through contact with exposed skin or eyes, and especially by inhalation
In addition to the machine guards that protect the user against larger ejected pieces broken off from the wheel or the workpiece, it is necessary for users to wear eye protection as determined by a risk assessment. Eye protection complying with a relevant British Standard will protect against most of the smaller ejected particles such as dust.
Adequate and suitable respiratory protection should also be determined, based on a risk assessment including an evaluation of the level of exposure, occupational exposure limits, and on what the specific task and worker requirements are. The risk assessment should also take into account related processes which may include welding fume and/or gases used.
Dusts
There is a clear requirement under the Control of Substances Hazardous to Health Regulations (COSHH) 2002 for employers and the self-employed to assess and control the risks from dust exposure, and various workplace exposure limits exist. Often, natural ventilation is all that will be available to control exposure to dusts generated by abrasive wheels. If wet cutting is not possible, for example inside a building, then either fixed or on-tool extraction will be essential. There can be particular risks with concrete and masonry dusts, and consideration should be given to the possible need for the use of local exhaust ventilation or respiratory protective equipment (RPE). RPE should be used as a last resort. It is important that any local exhaust ventilation system is designed specifically for the task and the type of dust generated, that it is checked and serviced regularly, and that it undergoes statutory inspection/testing. Care also needs to be exercised if water is used as part of the process for dust dampening, to prevent slippery floors.
Noise
Regulations specify the level at which employers must enforce the use of hearing protection at 85dB, daily or weekly average exposure, and the level at which employers must assess the risk to workers’ health and provide them with information and training at 80dB. There is also a legal exposure limit value of 87dB, taking account of any reduction in exposure provided by hearing protection, above which workers must not be exposed. Normally, site signage will indicate the hearing protection zones.
Depending on the specific operation, noise levels can range from moderate to very high, reaching up to 120dB. Grinding, for example, can result in noise levels in the range of 97–105dB. Repeated daily personal noise exposure above LEP,d 85dB can lead to permanent hearing loss and tinnitus. The LEP,d is a worker’s daily exposure to noise at work normalised to an 8-hour day, taking into account the average levels of noise and the time spent in each area. Almost anyone working in a metal fabrication environment is likely to be exposed to harmful noise levels. In addition to protecting against the harmful effects of noise, it is vital to maintain situational awareness so that important warning signals can be heard such as fire alarms and moving vehicles, for example.
Hand-arm vibration (HAV)
Employers must assess their employees’ exposure to vibration and take steps as necessary to reduce exposure. The HSE’s vibration ready reckoner can be used to calculate how long it is permissible for an individual to operate each type of abrasive wheel or to carry out multiple operations that will expose them to the risk of Hand-Arm Vibration Syndrome (HAVS) within a defined period. Steps for reducing exposure to vibration include changing the equipment that is the source of the vibration, reducing the exposure time, and changing work methods. Health surveillance may be necessary. Anti-vibration mountings must be replaced at suitable periods not exceeding the manufacturer’s recommended intervals in order to reduce the risk of exposure to vibration. The risk of vibration-related injury is associated with tasks that require excessive bending of the wrists or time on tool. Prolonged exposure to vibration can cause damage to blood vessels, nerves and tendons in fingers, hands and wrists, leaving the sufferer with reduced sensitivity, strength and dexterity.
Fire or explosion
The choice of tool on which to mount an abrasive wheel should only be made after consideration of the environmental conditions of operation. Fire risk assessments take into account potential ignition sources, which would include sparks from ejected particles of steel potentially generated during the use of abrasive wheels, any fuels that might be present in the area where abrasive wheels are being used, for example packaging, and any high-risk sources of pure oxygen, for example oxyacetylene welding equipment. The risk is reduced by introducing prevention controls such as identifying a suitably inert area for abrasive wheel activity, and mitigation controls such as emergency procedures, firefighting equipment, and the provision of protected escape routes.
Where the risk is significant due to the presence of dangerous substances, for example flammable solvents or explosible dusts, Dangerous Substances and Explosive Atmospheres Regulations (DSEAR) assessments will have been completed to ensure the risk of fixed ignition sources, such as motors or lighting, are suitable. These assessments will also provide guidance for the conditions under which moveable ignition sources such as abrasive wheels can be used. Where the fire/explosion risk varies due to changes in the environment, employers may also need to implement the use of management procedures such as a hot work permit.
Electrical
Electrical risks to be considered arise from cutting power supplies or damage to machines which drive abrasive wheels. Tools which are part of the fixed installation will be inspected/tested during the periodic fixed electrical equipment to BS 7671. Electrically powered hand tools must have portable appliance tests (PATs) which identify electrical safety faults. However, users should also be trained to carry out visual inspection of the equipment before each use. Air-powered tools will need hose checks and governor speed checks. Petrol-driven tools must have engine maintenance, filter changes, etc. Engineers should use these maintenance/inspection opportunities to double-check that guards are secure, the tool is operating safely and on/off switches are reliable.
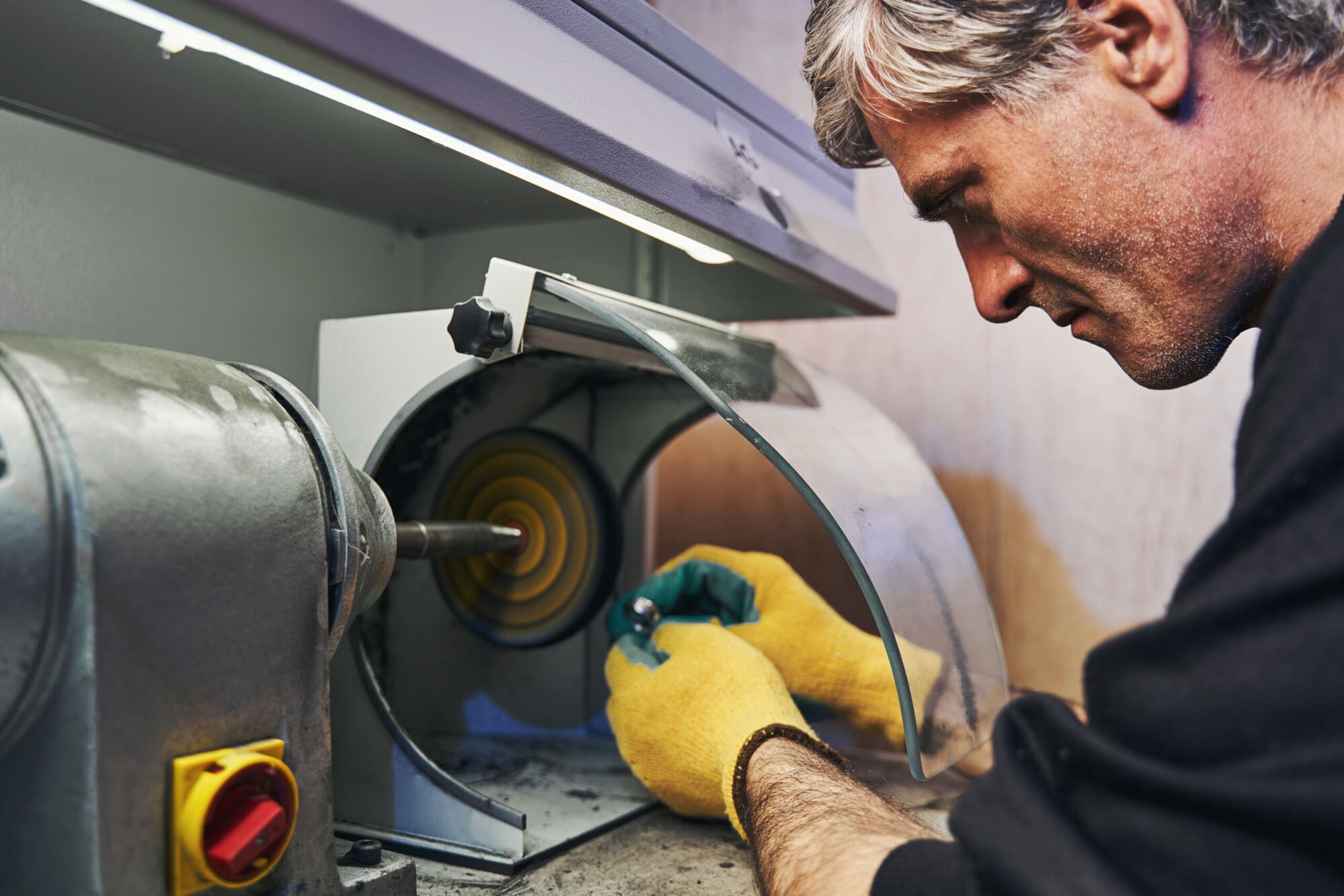
Handling, maintenance and storage of abrasive wheels
All abrasive wheels are fragile. Do not use a wheel if it is damaged or suspected of being damaged. When storing abrasive wheels, you should:
- Leave wheels that were shipped on a pallet stored as shipped until needed for use.
- Store wheels in racks or bins with dividers for different types of wheels and ensure easy access and less handling. When selecting the racks, bins, boxes or drawers for storage consider the size and type of wheels to be stored: for example, lay flat thin bonded wheels, and support larger wheels in racks. Always follow the manufacturer’s instructions.
- Place straight or tapered wheels on their end in a cradle or chocked position to prevent rolling or damage.
- Do not pile other items such as tools on top of wheels.
- Never store wheels near excessive heat or cold, in contact with water, oil or moisture, nor in drawers with loose tools. Store wheels in a dry area. Prevent the area from freezing temperatures and any temperature or humidity that causes condensation on the wheels.
- Keep the information from the manufacturer in the storage area, and available to the machine operator. Follow the manufacturer’s instructions for the length of time a wheel should be stored. Sort and store wheels so that older wheels can be selected first.
When handling abrasive wheels, you should:
- Handle the wheels carefully. Avoid dropping or bumping.
- Not roll a wheel on its edge.
- Transport wheels in containers designed to provide support for the wheels if they are too heavy to carry by hand.
Dressing abrasive wheels is important maintenance. It is also necessary to carry out routine checks, regular inspections and preventive maintenance that includes daily/weekly service checks, formal visual inspections and combined inspections and tests before first-time use and then every month. Any tool found to be in an unserviceable or unsafe condition must be withdrawn from use until defects have been rectified by a person competent to carry out this class of work.
Abrasive wheels training and knowledge
It is a legal requirement under the PUWER 98 regulation that specifiers, buyers and operators using abrasives are trained in their safe use. Requirements of the regulations include that the operative:
- Has a certificate of training
- Is deemed competent by their employer
Abrasive wheels training courses are offered by a variety of training providers, including by the CITB, the industry training board for the construction sector in England, Scotland and Wales. Training providers usually provide a certificate of attendance, not competence, so the employer is required to assess and record competence in the workplace. The certificate issued should refer to the type of machine the individual was trained to use.
Further information about accredited training providers can be obtained from the British Abrasives Federation (BAF). BAF are the recognised UK accrediting training body for the safe use of professional abrasives in HSE document HSG17. They also represent a range of abrasives manufacturers and distributors present in the UK, giving them a voice on the European and global abrasives stage.
There is no substitute for thorough practical training in all aspects of the mounting and the use of abrasive wheels. Any training programme should cover at least the following:
- Hazards and risks arising from the use of abrasive wheels and the precautions to be observed
- Methods of marking abrasive wheels with their type, size and maximum operating speed
- How to store, handle and transport abrasive wheels
- How to inspect and test abrasive wheels for damage
- The functions of all the components used with abrasive wheels such as flanges, blotters, bushes, nuts etc.
- How to assemble abrasive wheels correctly to make sure they are properly balanced and fit to use
- The proper method of dressing an abrasive wheel, i.e. removing dulled abrasive or other material from the cutting surface and/or removing material to correct any uneven wear of the wheel
- The correct adjustment of the work rest on pedestal or bench grinding machines
- The use of suitable personal protective equipment, for example eye and ear protection
It is recommended that a record of training in the safe mounting of abrasive wheels is kept, showing the trainee’s name and date of training.
Legal requirements and regulations
The use of abrasive wheels in Scotland, England and Wales is regulated by the Provision and Use of Work Equipment Regulations Act 1998 (PUWER). These regulations replaced the previous 1992 PUWER regulations which in turn were introduced to replace the Abrasive Wheels Regulations 1970. PUWER is overseen and enforced by the Health and Safety Executive (HSE).
PUWER exists to protect workers from unsafe machinery such as abrasive wheels and other work equipment. The PUWER regulations require risks to people’s health and safety from any equipment that they use in the course of their work, to be prevented or controlled. In other words, that work equipment is maintained safe for use, in a safe condition and suitable for the intended use. Further examples of uses of work equipment which are covered by the PUWER regulations include:
- Installing
- Starting or stopping
- Maintaining
- Servicing
- Repairing
- Modifying
- Cleaning
- Transporting
To comply with the PUWER regulations an employer who owns, operates or has control over work equipment such as abrasive wheels, has a duty to control any risks by:
- Ensuring that work equipment is suitable for use, and used for the purpose and conditions in which it is intended to be used
- Properly installing any fixed work equipment or machinery, including ensuring that any safeguards are in place
- Producing a safe system of work for using and maintaining machinery and work equipment
- Ensuring that, where necessary, work equipment is regularly inspected by a suitably competent person so it continues to be safe for use
- Maintaining work equipment in good condition
- Ensuring that people using, supervising or managing equipment are provided with appropriate information and training on use and safety
- Taking account of working conditions and health and safety risks when selecting work equipment, for example flooring conditions, stairs and space
- Keeping appropriate records
PUWER builds on the general duty of the Health and Safety at Work etc. Act 1974 (HSWA) to ensure, so far as is reasonably practicable, the health, safety and welfare of employees, and on the specific duty of the Management of Health & Safety at Work Regulations 1999 (MHSWR) to assess and control risks.
Other relevant legislative requirements or regulations that also apply to the use of abrasive wheels include:
- Manual Handling Operations Regulations 1992 (MHOR) – these regulations set out a clear ranking of measures for dealing with risks from manual handling.
- The Personal Protective Equipment Regulations 1992 – these regulations mandate that employers must provide adequate personal protective equipment (PPE) to employees. On 6 April 2022 the Personal Protective Equipment at Work (Amendment) Regulations 2022 (PPER 2022) came into force. They amend the 1992 Regulations (PPER 1992).
- Control of Substances Hazardous to Health Regulations (COSHH) – COSHH regulations outline what employers and employees must do to control substances that are hazardous to health.
- Control of Noise at Work Regulations 2002 – this legislation is designed to ensure that workers’ hearing is protected from high levels of noise in the workplace.
- Electricity at Work Regulations 1989 – these regulations apply to every employer and self-employed person in a workplace, and every employee, who must co-operate with their employer.
Manufacturers of abrasive wheels also have legal duties placed on them, under the Health and Safety Act 1974 (HASWA), and the Supply of Machinery (Safety) Regulations 2008. This legislation requires that equipment is only supplied that has been tested as safe under the specific conditions it is intended to be used in.
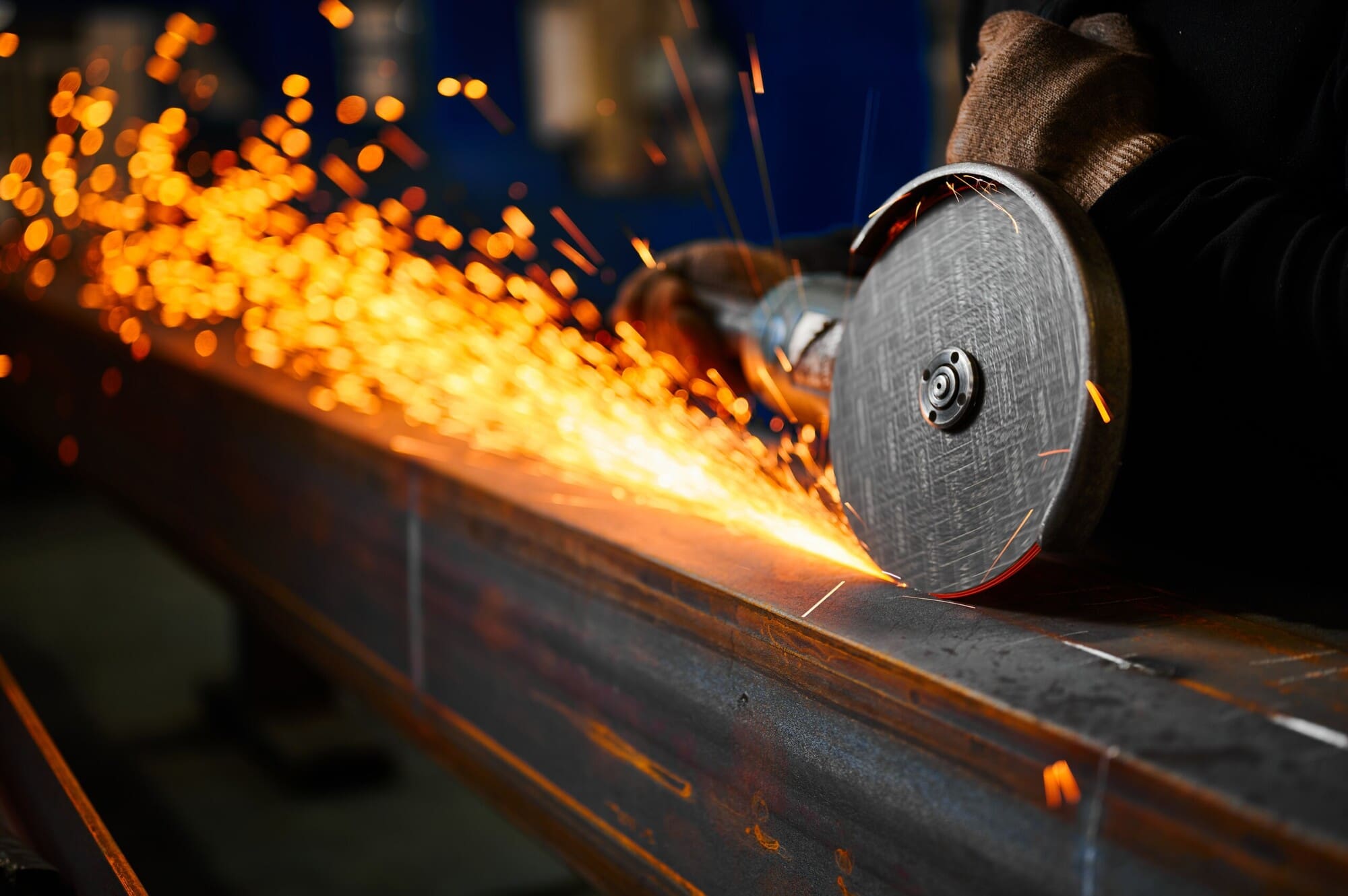
Final Thoughts
Nearly half of all accidents which result from abrasive wheels occur due to unsafe working practices and operator errors. If you work with abrasive wheels you should be fully trained and always follow strict Health and Safety practices to protect both yourself and others from harm.