In this article
Equipment has improved efficiency in the workplace. It enables workers to complete tasks more quickly and accurately than they would if doing them manually. In fact, some jobs would not be possible without work equipment. Despite its usefulness, it can introduce a risk of injuries and ill health in the workplace.
Numerous workplace accidents have occurred over the years. Some have resulted in serious injuries and even fatalities. According to the latest HSE statistics, 123 workers died in work-related accidents; the main causes were falls from a height, being struck by a moving vehicle or a moving object, contact with moving machinery or being trapped by something overturning/collapsing.
Many non-fatal injuries occurred; 565,000 working people sustained an injury at work, according to the Labour Force Survey, and there were 61,713 RIDDOR reported injuries to employees. Also, 1.8 million workers reported suffering from work-related ill health (new or long-standing).
The HSE statistics demonstrate that there have been many fatalities, non-fatal injuries and reports of ill health relating to equipment at work. It highlights the importance of having health and safety laws relating to the provision and use of equipment to protect everyone at work from the risks.
The main health and safety law on work equipment is PUWER. These regulations ensure that any equipment provided and used at work is without risks to health and safety, regardless of what it is, its age, condition or origin.
This article will cover what PUWER is, the main requirements and to whom the regulations apply. It will also look at the equipment covered under PUWER and why duty holders should use a PUWER checklist to help them comply with the law.
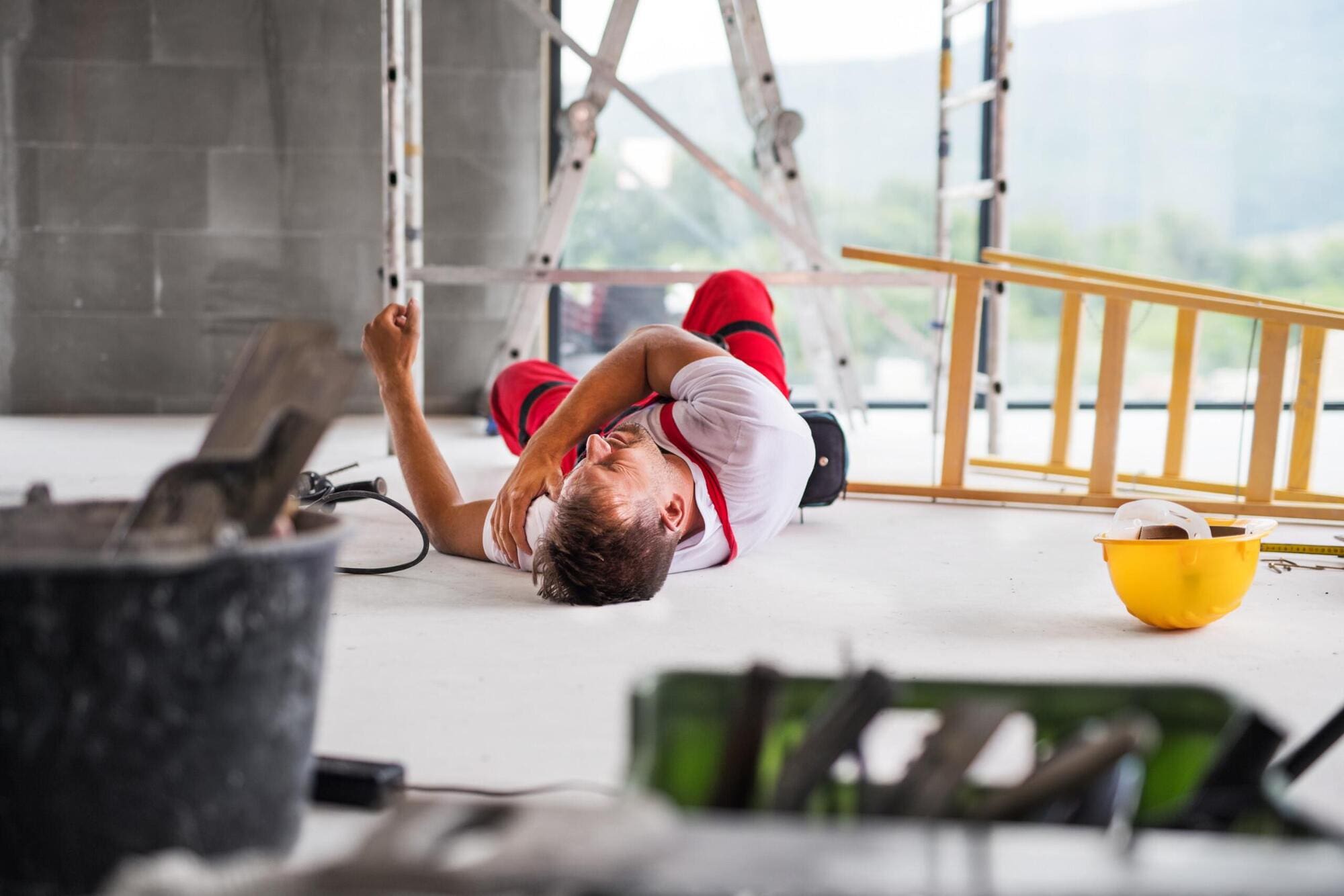
What is PUWER?
PUWER is an acronym for the following:
- Provision and;
- Use of;
- Work;
- Equipment;
- Regulations.
These regulations are sometimes known as just PUWER, PUWER 1998 or PUWER 98, and came into force on 5th December 1998. They are made under the Health and Safety at Work, etc. Act 1974 (HSWA).
PUWER first came out in 1992 as one of the ‘six-pack’ regulations, i.e. it was one of six health and safety regulations introduced in the 1990s in response to a set of European Union (EU) Directives.
The EU significantly influenced health and safety legislation in the United Kingdom (UK). As a previous member state, the UK adopted numerous directives and regulations. Some laws applied directly, and others were incorporated into national laws. Even though the UK has left the EU, PUWER 98 remains unchanged, as it was already a national law.
What are the main requirements of PUWER?
PUWER requires that any equipment provided for use at work must be:
- Suitable for the intended use.
- Safe for use, maintained in a safe condition, and inspected to ensure it is correctly installed and without health and safety risks.
- Used only by individuals who have had adequate information, instruction and training.
- Accompanied by appropriate health and safety measures, such as protective devices and controls. These will usually include guarding, emergency stop devices, adequate means of isolation from sources of energy, clearly visible markings and warning devices.
- Used in line with specific requirements, e.g. for mobile work equipment and power presses.
There are additional requirements for some types of work equipment. For example, lifting equipment must also comply with the Lifting Operations and Lifting Equipment Regulations 1998 (LOLER).
The HSE has further guidance on PUWER here.
To whom do the PUWER regulations apply?
Anyone who owns, operates or controls work equipment will have duties under PUWER.
The regulations apply to the following:
- Employers (individuals, partnerships or companies) – Have duties under PUWER when providing equipment for use at work. It also applies when equipment is used by employees and the self-employed working for the business.
- Self-employed workers – Have duties under PUWER when providing equipment for work or using it at work.
- People who have control of work equipment – This will apply to:
– Those who provide work equipment for use in the workplace but do not control its use or the premises where it is used, e.g. hire companies.
– Offshore owners, operators and contractors.
– Those who have control of non-domestic premises and provide work equipment used by other people at work.
– Owners of multi-occupied buildings where equipment is used by occupants, e.g. a passenger lift.
– Those who have control of work equipment in construction, e.g. the main contractor.
– Those employed to supervise or manage the use of equipment. - Employees – Do not have specific duties under PUWER but do have responsibilities under general health and safety legislation.
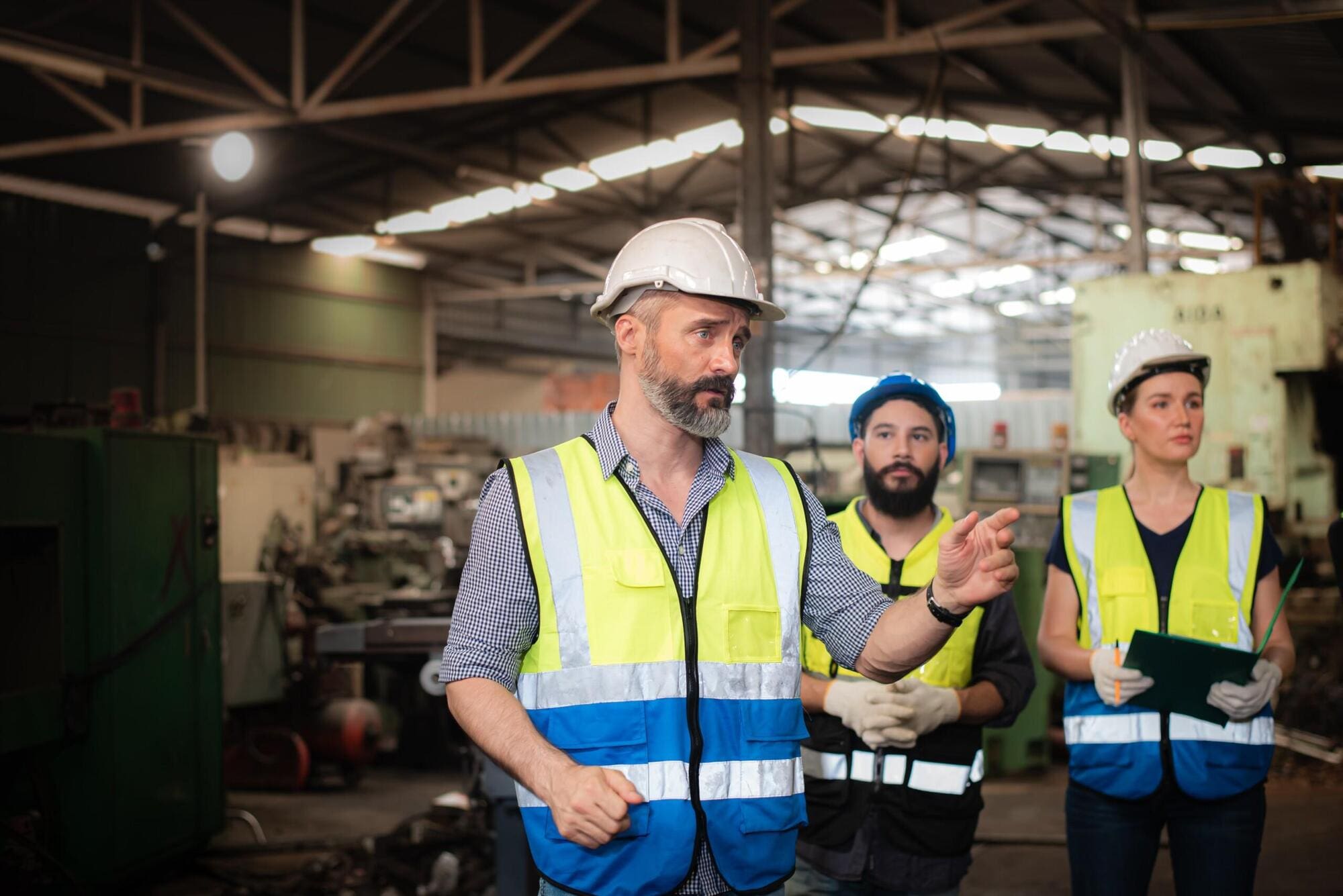
What common equipment is covered by PUWER?
PUWER applies to equipment provided for use at work.
The HSE defines work equipment as:
“Any machinery, appliance, apparatus, tool or installation for use at work (whether exclusively or not). This includes equipment which employees provide for their own use at work.”
PUWER covers a wide range of new, existing, second-hand and leased work equipment, including that owned and provided by employees. It also includes various activities such as starting, stopping, using, cleaning, transporting, repairing, modifying, servicing and maintaining equipment.
PUWER covers a wide range of different types of work equipment, and some examples are in the table below (this list is not exhaustive).
Machinery | · Mobile plant (dumper trucks, excavators and tractors).· Motor vehicles.· Conveyors.· Hand-held machines (mowers).· Fixed machines (power presses, lathes and drilling machines). |
Appliances | · Kitchen appliances (microwaves, toasters, fridges, freezers, dishwashers and kettles).· Computers.· Office equipment (photocopiers, shredders and laminators). |
Lifting equipment | · Hoists.· Slings.· Lift trucks.· Mobile elevated working platforms (MEWPs).· Passenger lifts.· Bath lifts. |
Apparatus | · Laboratory equipment, such as Bunsen burners.· Medical equipment.· Personal protective equipment (PPE). |
Tools | · Power tools, such as drills, abrasive wheels and circular saws.· Hand tools, such as hammers, saws, knives, screwdrivers and axes. |
Installations | · Production lines (robotic lines).· Electrical installations (wiring and equipment).· Emergency equipment (fire detection and water suppression).· Air conditioning units.· Heating and plumbing systems. |
Other equipment | · Ladders.· Podiums.· Scaffolding.· Pressure washers.· Welding equipment. |
What equipment is not covered by PUWER?
PUWER does not include the following, as it is not classed as work equipment:
- Livestock and other animals.
- Substances, such as acids and alkalis.
- Structural items, such as walls, stairs and fences.
- Privately owned vehicles.
PUWER does not cover equipment used by the public, e.g. compressed air for tyres or a DIY car wash at a fuel station. However, there are still duties to the public under general health and safety legislation (e.g. HSWA).
There are instances where PUWER will apply, but other laws will take precedence. For example, specific road traffic legislation will need to be complied with where vehicles are used on public roads or in public places.
PUWER checklist
PUWER is a detailed regulation, and there are a lot of requirements that duty holders need to meet to comply with the law. Although not legally required, they should use a PUWER checklist to help them ensure their equipment is compliant.
There are many benefits, such as:
- It keeps them on the right side of the law.
- It acts as a prompt to avoid missing something important.
- It can help a business improve its risk assessment and procedures if anything is missing or inaccurate.
- It can assist with deciding on the type and frequency of inspections.
- It can reduce the risk of work equipment-related accidents, injuries and ill health.
- It provides recorded evidence to enforcement authorities that the business is taking its legal obligations seriously.
We have a generic PUWER checklist that duty holders can use and modify to suit their specific circumstances.
Individuals carrying out a check should be competent, i.e. have the knowledge, skills and experience of the work equipment and PUWER.
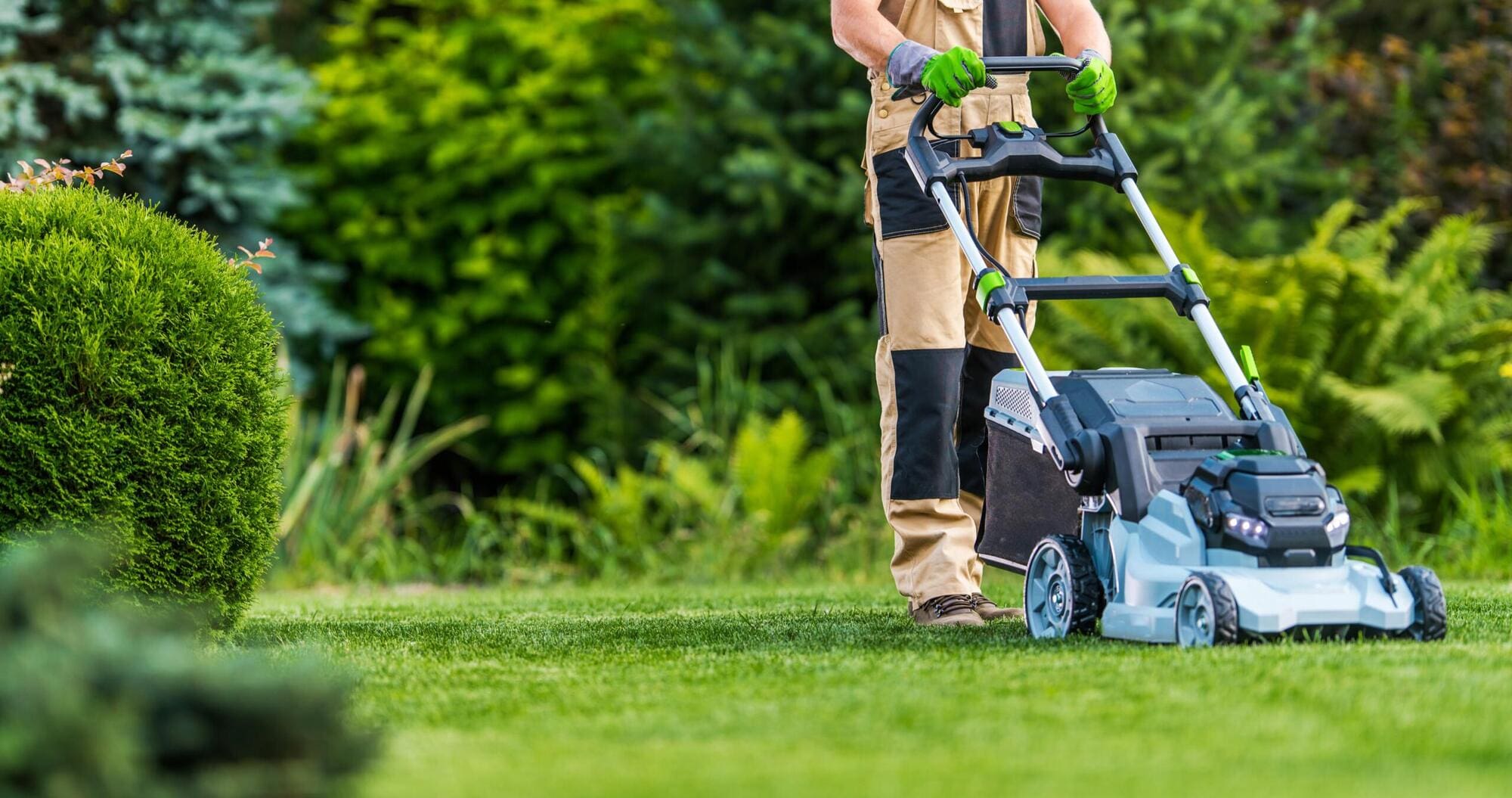
Summary
Work equipment can introduce many hazards into the workplace, potentially putting employees and others at serious risk of injury, ill health and even death. Therefore, it is essential that employers and other duty holders comply with PUWER and put the necessary measures in place to prevent, reduce or control the risks associated with work equipment.
Despite PUWER being law, some companies are still non-compliant. The Building Safety Group (BSG) has reported a 40% increase in PUWER equipment breaches occurring on construction sites during the first half of 2021. Non-compliance with the law can have serious consequences for duty holders.
Using a PUWER checklist can help employers, and other duty holders, comply with the law and keep their employees and others safe and healthy. After all, businesses’ main aim is to be profitable, and PUWER-related accidents can be costly, especially if there is a fatality or severe injury on site.