In this article
Abrasive wheels are a commonly used tool in the construction trades. A wide range of tools utilise abrasive products to perform cutting, grinding and sanding operations and a very common format is a rotating abrasive wheel, which can be used on both handheld and bench-mounted tools.
Machines and tools incorporating abrasive wheels include:
- Angle grinders – handheld power tools used for cutting, grinding and polishing various materials, including metal, concrete and stone.
- Bench grinders – stationary machines used for grinding, sharpening or shaping metal objects.
- Cut-off saws – power tools used to make precise cuts in various materials, such as metal, wood and masonry.
Although a common piece of equipment across the UK, abrasive wheels can pose significant health hazards and are a leading cause of injury in the workplace. The Royal Society for the Prevention of Accidents (ROSPA) Accident Surveillance Systems data ranked angle grinders as the third most dangerous tools, with 5,400 injuries recorded annually.
Training and competence
The Abrasive Wheels Regulations (1970) were replaced by the Provision and Use of Work Equipment Regulations (1998) (PUWER), placing a greater emphasis on training, and widening the scope of those who need to be trained. Under PUWER, those who operate abrasive wheels must have sufficient training. PUWER regulations state that:
“Every employer should ensure that all persons who use work equipment have received adequate training for purposes of health and safety, including training in the methods which may be adopted when using the work equipment, any risks which such use may entail and precautions to be taken.
“Every employer should ensure that any of his employees who supervises or manages the use of work equipment has received adequate training for purposes of health and safety, including training in the methods which may be adopted when using the work equipment, any risks which such use may entail and precautions to be taken.”
Information about accredited training providers can be obtained from the British Abrasives Federation (BAF). BAF are the recognised UK accrediting training body for the safe use of professional abrasives in HSE document HSG17. Abrasive wheel training usually comprises, but is not limited to:
- The basics in abrasive wheel health and safety awareness
- Hazards and risk control measures
- Health and safety legislation
- Personal Protective Equipment (PPE)
- Types of abrasive wheel machines and their safe use, including mounting, use and maintenance of abrasive wheels
- A practical assessment on abrasive wheel safe use
The aim of abrasive wheels training is to ensure that operators are working safely with abrasive wheels so that they can recognise the risks and know which control measures are needed to prevent injury and ill health to themselves and to others.
Training providers usually provide a certificate of attendance, not competence, so the employer is required to assess and record competence in the workplace. The certificate issued should refer to the type of machine the individual was trained to use and be kept on file by the employer, as they will be asked to produce these should any HSE inspections or investigations take place.
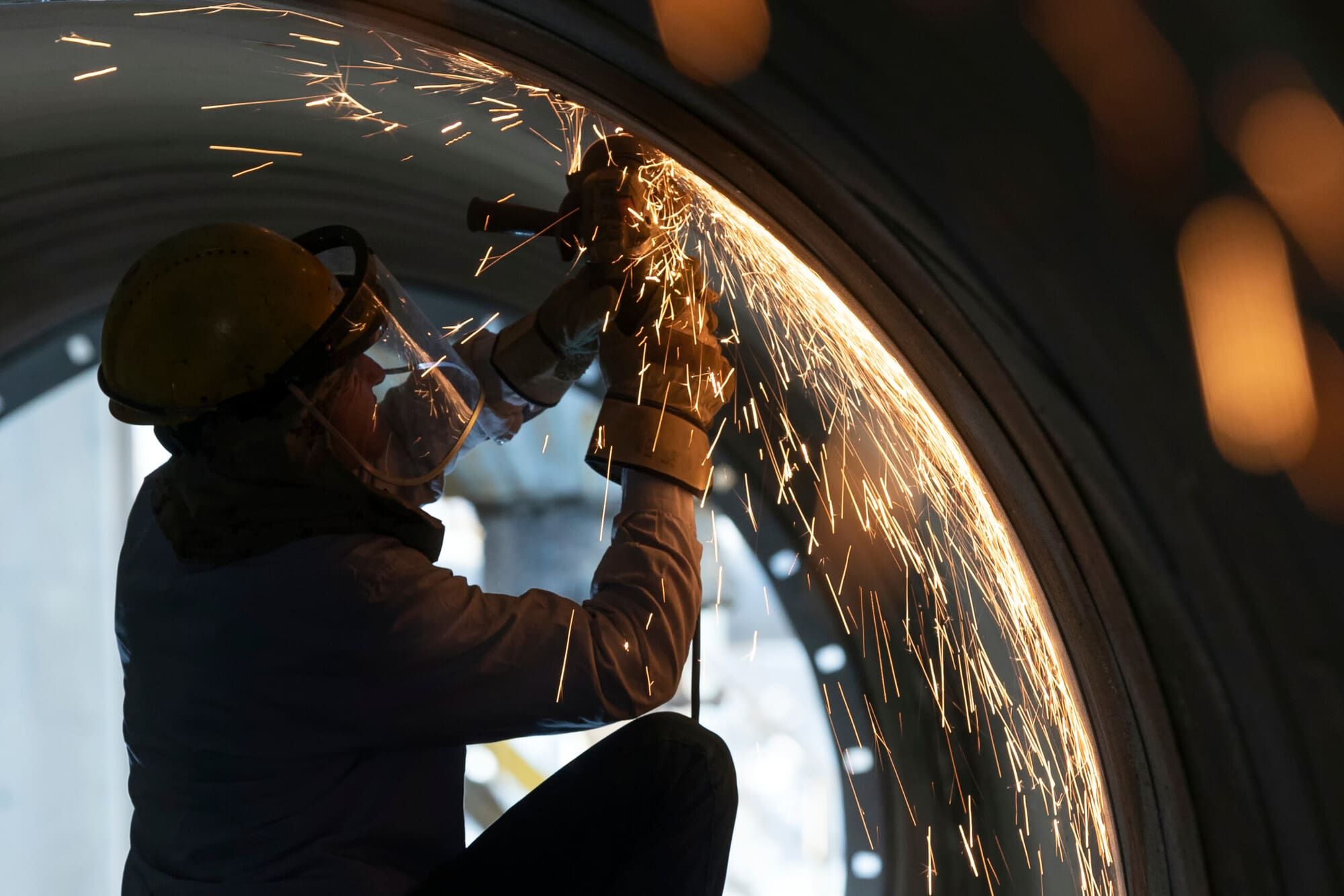
Selection of the right wheel
An abrasive wheel is a wheel, cup or cone consisting of abrasive particles bonded together with various substances. The two main types of bonding agent are inorganic and organic.
Inorganic bonds are generally fired in a furnace to give the bond a hard, strong but brittle structure. These wheels are used for precision grinding applications as they hold their shape, but require dressing. Dressing means removing the very outer surface of the wheel so that a new sharp surface can be exposed.
Organic bonds are not fired but are cured at low temperature. Such wheels are tough, shock-resistant and self-dressing, and are most suited to non-precision applications, for example fettling and cutting off.
Choosing the right abrasive wheel for any given project is perhaps the most important part of the process because choosing the wrong abrasive wheel for your material might lead to, for example, workpiece and/or machine damage resulting from running the wrong wheel or grinding process. An abrasive wheel specification is a combination of grain type, grit size, hardness, porosity and bond.
The abrasive wheel that you choose needs to be made of stronger material than the material that you are processing in order to have an impact. Wheel selection is dependent on the kind of material to be ground and the type of grinding operation. The eight important factors that need to be considered in the selection of an abrasive wheel are:
- Material to be ground and its hardness – the type of material to be ground determines the selection of abrasives, its grit size and grade. Aluminium oxide abrasives are ideal for grinding hard or high tensile materials such as alloy steel, high speed steel, annealed malleable iron and other ferrous metals. Silicon carbide abrasives are excellent for grinding or cutting low tensile strength materials such as cast iron, bronze, aluminium, copper and other non-metallic materials. Finer grit wheels are required for hard and brittle materials; coarser grit wheels are ideal for soft and ductile materials.
- Stock removal and surface finish – the amount of stock removal and the degree of surface finish required also depends on the abrasive size and the type of bond. When an operation demands high stock removal rates, as in fettling, coarse grit wheels are used. In contrast, fine grit wheels are ideally suited to achieve extremely close surface tolerances and fine geometrical finish. Resinoid, rubber or shellac bonded wheels are usually recommended for operations that require fine finishes.
- The grinding process – wet or dry – during dry grinding with vitrified wheels, in order to minimise the heat generated, soft grade wheels should be used. These can be at least one or two grades softer than the ones chosen for wet grinding operations. In wet grinding applications, where coolants reduce the heat, harder grade wheels can be used.
- Peripheral speed of the wheel – the speed at which the grinding edge of the wheel passes the work surface is called the Peripheral Speed of the wheel. This is a very important factor in grinding wheel selection. The maximum operating speed for standard vitrified wheels can be up to 60 m/s. This is indicated on the blotter or on the face of the wheel. Organically bonded wheels (resinoid, rubber or shellac) are used for most applications where the required speed rate is up to 48 m/s. Higher speeds for reinforced products can go up to 100 m/s. Reducing the wheel speed reduces the wheel hardness.
- The area of grinding contact – large or small – the area of grinding contact influences the selection of wheel grade and grit size. As far as wheel grade is concerned, it is normal practice to use soft grade wheels where the area of grinding contact is large and harder grade wheels where the area of grinding contact is small. In surface grinding, for instance, where the area of grinding is large, coarser grit, open structure wheels are recommended. Conversely, fine grit, closer structure wheels are ideal for use in narrower and close precision areas of contact, as in cylindrical grinding operations.
- The grinding application – severity of a grinding operation can be due to various factors such as the pressure of shock loads, heavy in-feeds, high work speeds and traverse rates and intermittent grinding contact. Hence, for wheel selection, the grinding operation influences the choice of abrasive type, grade and even type of bond. The greater the severity of the grinding operation, the harder the grade of wheel required and the tougher the abrasive that should be used. For example, for severe grinding operations, like snagging, a tough abrasive is required. Medium and soft grade wheels are ideally suited for precision grinding jobs.
- Condition of the grinding machine – it is very important that all grinding machines are in good condition and must be installed or fixed on flat and strong foundations.
- The type of grinding machine – the type of wheel and grinding operation defines the type of machine to be used, therefore the correct choice of the wheel for the application and the machine is essential.
Wheels to BS EN 12413 and BS ISO 525 standards will be marked to indicate specific restrictions for use, which are:
- RE1 Not permitted for handheld machines and manually guided grinding
- RE2 Not permitted for handheld cutting off machines
- RE3 Not permitted for wet grinding. Abrasive product only suitable for dry grinding
- RE4 Only permitted for totally enclosed working area
- RE6 Not permitted for face grinding
Inspection and maintenance
The Provision and Use of Work Equipment Regulations Act 1998 (PUWER) require that abrasive wheels are kept in good condition and are safe to use. All machinery and tools that contain abrasive wheels must be regularly maintained and inspected by a competent, trained individual.
It is necessary to carry out routine checks, regular inspections and preventive maintenance that includes daily/weekly service checks, formal visual inspections and combined inspections and tests before first-time use and then every month. Any tool found to be in an unserviceable or unsafe condition must be withdrawn from use until defects have been rectified by a person competent to carry out this class of work.
Abrasive wheels should also be inspected to make sure they have not been damaged while being moved or stored. This can be quickly accomplished through visual inspection and the ring test. To perform the ring test, gently tap a dry clean wheel with a light, non-metallic tool, for example a screwdriver handle or a wooden mallet. If the wheel is in good working condition, the tap should produce a clear ping noise. If it makes a thud sound, the wheel is damaged and should not be used.
Abrasive wheels with inorganic bonds will require regular dressing. Just as with any cutting tool, an abrasive wheel dulls after repeated use. If an abrasive wheel is not dressed, it will not cut as effectively or as precisely. This can result in poor-quality work and may also endanger the safety of both the operator and anyone in the near vicinity. Dressing gets rid of any old, dull grains and removes any clogs or excess amounts of bonding material.
Electrically powered hand tools must have portable appliance tests (PATs) which identify electrical safety faults.
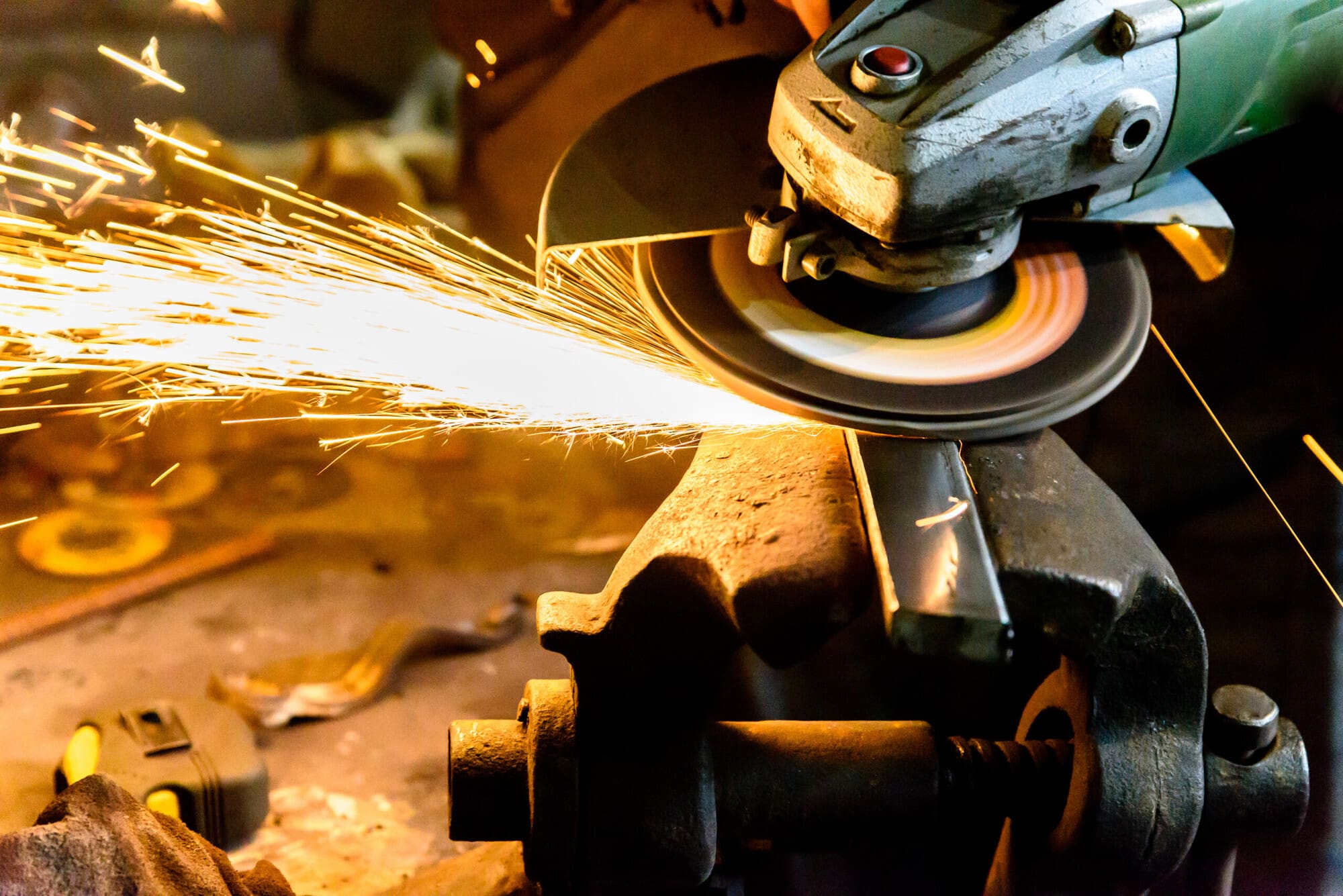
Personal protective equipment (PPE)
It is crucially important that anyone operating abrasive wheels should be wearing the appropriate personal protective equipment (PPE). This is part of the basic safety procedures, and it is important for the operator’s safety as well as the safety of those working around them. Appropriate PPE for operating abrasive wheels includes:
- Hearing protection – this should be worn based on the sound level and duration of the task. The noise volume will vary depending on the abrasive accessory that the operator is using and the type of material the grinder is being used on.
- Eye and face protection – eye protection, such as safety glasses or goggles, is especially important when grinding. The speed at which angle grinders can propel small particles is much faster and farther than hand tools. Certain power tools may require using a face shield in addition to safety glasses or goggles. For example, a face shield is suggested while using a grinder due to the amount of hot metal particles generated. A face shield is considered a secondary form of eye protection and should always be used in conjunction with a primary form of protection, i.e. safety glasses or goggles. Protective masks should be worn to prevent inhaling substances such as dust etc.
- Hand protection – gloves are required when the task produces sharp particles or the materials become hot. Gloves should be well-fitted while providing good dexterity and the best possible protection against cut, abrasion and heat. Vibration-resistant properties are also of benefit.
- Body protection – sparks are a sign that the grinding wheel is doing its job; however, they present a safety hazard. Operators should cover their skin with a fire retardant (FR) jacket or well-fitting, flame-resistant clothing to protect against burns and cuts from the spark stream or the surfaces of the workpiece. Do not wear loose clothing or allow any clothing to flap, such as sleeves, when operating a hand grinder. Severe damage can occur if the grinding disc gets tangled in clothing
- Safety footwear – these help to protect the feet from potential occupational hazards such as falling objects, sharp objects, electrical dangers, slipping, and more.
Safe operating techniques
Abrasive wheel operators must receive relevant training on how to safely operate an abrasive wheel. The training must be specific to the type of abrasive wheel and the tasks being undertaken. Safe operating techniques include:
- Appropriate personal protective equipment must be used.
- A guard of adequate strength should be provided, where practicable, to achieve the following:
– contain wheel fragments in the event of fracture
– reduce the likelihood of the operator coming into contact with the wheel
– protect the wheel against inadvertent damage
– prevent an oversized wheel from being fitted. - The guard must be fabricated from a material of adequate strength to withstand the impact force of any ejected wheel fragments.
- The guard should enclose the wheel to the greatest possible extent, keeping the opening as small as possible. Adjustable hoods or tongues may also be incorporated into the guard to compensate for the increased exposure as the wheel wears down.
- When a guard is constructed from several component parts, the fasteners should be of adequate strength to prevent separation of the guard in the event of wheel failure. This also applies to any fasteners used to anchor the guard to the machine frame.
- New or re-fitted wheels should be trial run at full operating speed for at least one minute before the workpiece is applied. During the trial run everyone should stand clear.
- Excessive vibration usually indicates that the wheel is out of round. Such wheels should not be used until they have been balanced by dressing. Wheels which cannot be balanced by dressing should be removed.
- Never force the wheel by exerting excessive pressure on it. The wheel characteristics – that is, its abrasive, grit size, grade and porosity – govern its cutting power.
- Never grind on the side of the wheel unless permitted by the wheel manufacturer. Most wheels are designed for grinding on the outer (peripheral) surface only.
- Ensure the work rest, where fitted, is adjusted as close to the wheel as practicable and securely fixed in position. The gap between the wheel and work rest should be maintained at less than 2mm as the wheel wears down.
- Never impact the wheel with tools or the workpiece. Contact with the wheel should be made by exerting gradual, even pressure.
- Care should be exercised when handling and storing abrasive wheels to prevent damage. All abrasive wheels are fragile, though some are more susceptible to damage than others. Appropriate precautions include:
– handle wheels carefully to prevent dropping or bumping them together
– do not roll wheels
– use suitable plant which provides adequate support to transport large wheels.
- Abrasive wheels should be stored in an area that is dry and not subject to large changes in temperature. Some bonded abrasives may be affected by excess humidity, dampness and extreme temperatures.
- The wheels should be stored in suitable racks and located as near as practicable to the grinding location but remain protected from traffic or excessive vibration.
- Wheels may be stored horizontally on a flat surface or suspended vertically from pegs through the centre hole of the wheel. Guidance should be obtained from the manufacturer to determine the most appropriate method of storage, especially for thin wheels.
Do not under any circumstances use an abrasive wheel which has been subject to impact or damage, or which fails any form of your initial inspection. It is also important to mount abrasive wheels which do not match the fittings or speed of any machine that you are likely to be using.
Emergency procedures
Having a wheel crash while it is on a machine can be a rather unsettling event, so knowing what to do in this situation can make it a little less stressful:
- A cracked or damaged wheel should not be used. In the event of a wheel breakage, the wheel manufacturer and the machine supplier should be notified immediately.
- Wheel breakage should be investigated by the operator to determine and correct the cause. Corrections of adverse conditions should only be made following a complete investigation and recommendation by all parties concerned. This will help determine the cause of the breakage so that a recurrence of the trouble can be prevented.
- After a wheel breakage, the machine should immediately be removed from service until it is thoroughly inspected and/or repaired. The inspection should be made by a qualified person. All of the elements that affect safety such as guards, flanges, spindles and the operating speed of the machine should be returned to their original condition or replaced before the machine is put back in use.
When operating abrasive wheels, the main hazards arise from the ejection of pieces of the wheel or workpiece, contact with the wheel, and trapping of fingers between the wheel and work rest. Severe friction burns, crushed fingers and loss of eyesight are common injuries arising from accidents which occur when using abrasive wheels.
Should accidents and injuries occur, the injured person should in the first instance receive emergency treatment from the workplace first-aider who can assess whether there is a need to call the emergency services.
It is a statutory requirement that all workplace accidents are recorded. Certain types of incidents and injuries need to be reported to the Health and Safety Executive (HSE). The Reporting of Injuries, Diseases and Dangerous Occurrences Regulations (RIDDOR) is a piece of health and safety legislation that provides a structured approach to the way health and safety incidents are reported by employers.
RIDDOR applies to every workplace and puts duties on employers, the self-employed and people in control of work premises, that is the Responsible Person, to report and keep records of:
- Work-related accidents which cause death
- Work-related accidents which cause certain serious injuries, i.e. reportable injuries
- Diagnosed cases of certain industrial diseases
- Certain dangerous occurrences, i.e. incidents with the potential to cause harm.
Reporting accidents allows the enforcing authorities, including the Health and Safety Executive (HSE) and local authorities, to monitor accident trends, identify how risks arise and investigate serious accidents. They can then target their work to provide specific guidance and advice about how to avoid work-related deaths, injuries and ill health.
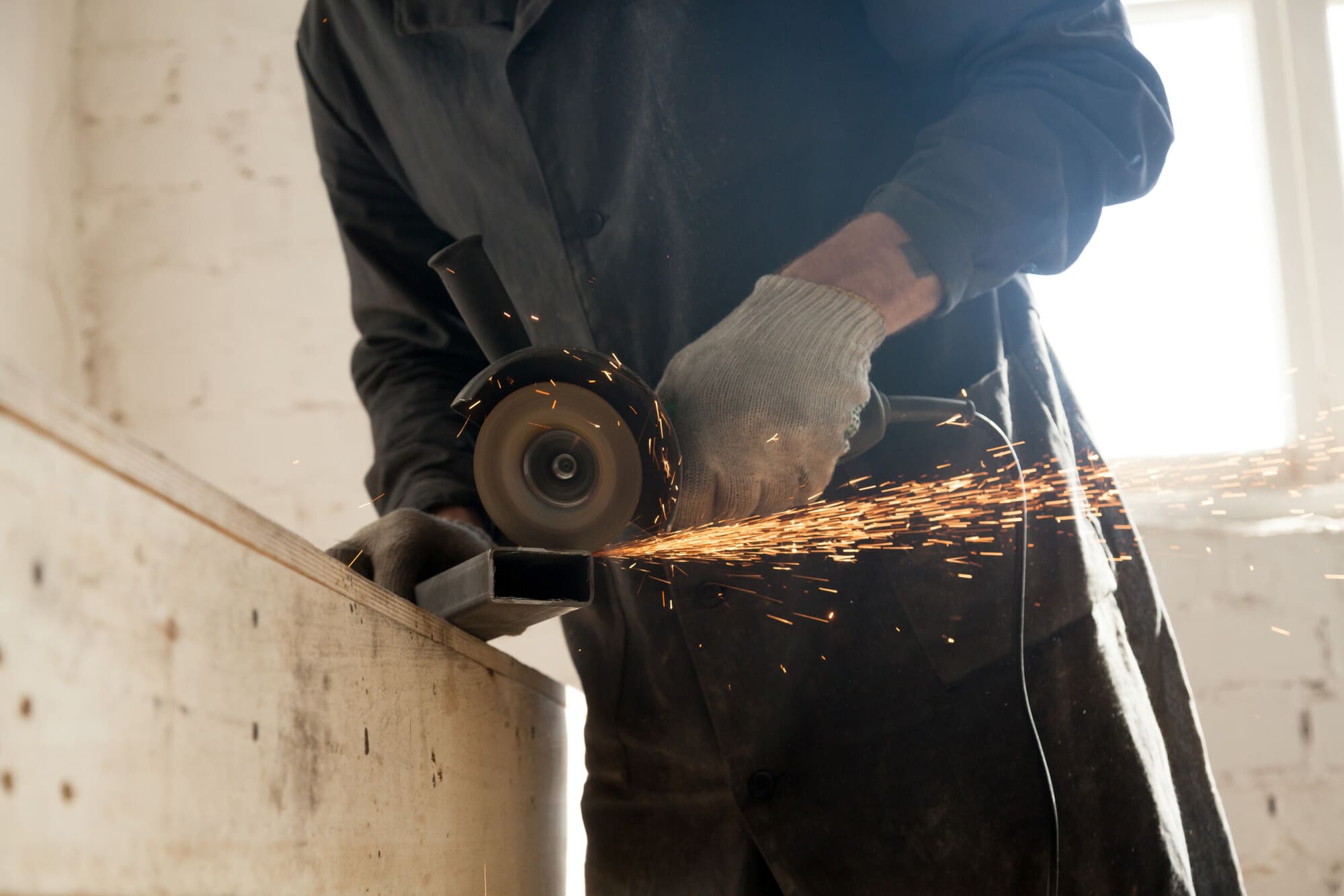
Legal compliance
The use of abrasive wheels in Scotland, England and Wales is regulated by the Provision and Use of Work Equipment Regulations Act 1998 (PUWER). These regulations replaced the previous 1992 PUWER regulations which in turn were introduced to replace the Abrasive Wheels Regulations 1970. PUWER is overseen and enforced by the Health and Safety Executive (HSE).
PUWER exists to protect workers from unsafe machinery such as abrasive wheels and other work equipment. The PUWER regulations require risks to people’s health and safety from any equipment that they use in the course of their work to be prevented or controlled. In other words, that work equipment is maintained safe for use, in a safe condition and suitable for the intended use. Further examples of uses of work equipment which are covered by the PUWER regulations include:
- Installing
- Starting or stopping
- Maintaining
- Servicing
- Repairing
- Modifying
- Cleaning
- Transporting
To comply with the PUWER regulations an employer who owns, operates or has control over work equipment, such as abrasive wheels, has a duty to control any risks by:
- Ensuring that work equipment is suitable for use, and used for the purpose and conditions in which it is intended to be used.
- Properly installing any fixed work equipment or machinery, including ensuring that any safeguards are in place.
- Producing a safe system of work for using and maintaining machinery and work equipment.
- Ensuring that, where necessary, work equipment is regularly inspected by a suitably competent person so it continues to be safe for use.
- Maintaining work equipment in good condition.
- Ensuring that people using, supervising or managing equipment are provided with appropriate information and training on use and safety.
- Taking account of working conditions and health and safety risks when selecting work equipment, for example flooring conditions, stairs and space.
- Keeping appropriate records.
PUWER builds on the general duty of the Health and Safety at Work Act 1974 (HSWA) to ensure, so far as is reasonably practicable, the health, safety and welfare of employees, and on the specific duty of the Management of Health & Safety at Work Regulations 1999 (MHSWR) to assess and control risks.
Other relevant legislative requirements or regulations that also apply to the use of abrasive wheels include:
- Manual Handling Operations Regulations 1992 (MHOR) – these regulations set out a clear ranking of measures for dealing with risks from manual handling.
- The Personal Protective Equipment Regulations 1992 – these regulations mandate that employers must provide adequate personal protective equipment (PPE) to employees. On 6 April 2022 the Personal Protective Equipment at Work (Amendment) Regulations 2022 (PPER 2022) came into force. They amended the 1992 Regulations (PPER 1992).
- Control of Substances Hazardous to Health Regulations (COSHH) – COSHH regulations outline what employers and employees must do to control substances that are hazardous to health.
- The Reporting of Injuries, Diseases and Dangerous Occurrences Regulations 2013 (RIDDOR) places a legal duty on employers, self-employed people and people in control of premises to report when there has been an accident which caused an injury, an accident that was work-related or the injury is of a type which is reportable.
- Control of Noise at Work Regulations 2002 – this legislation is designed to ensure that workers’ hearing is protected from high levels of noise in the workplace.
- Electricity at Work Regulations 1989 – these regulations apply to every employer and self-employed person in a workplace, and every employee, who must co-operate with their employer.
Manufacturers of abrasive wheels also have legal duties placed on them, under the Health and Safety Act 1974 (HASWA), and the Supply of Machinery (Safety) Regulations 2008. This legislation requires that equipment is only supplied that has been tested as safe under the specific conditions it is intended to be used in.
Final thoughts
By implementing prevention methods, ensuring that operators and supervisors are adequately trained and competent, and complying with legal requirements, employers can help maintain a safe work environment and minimise the risk of accidents and injuries associated with the use of abrasive wheels and power tools incorporating abrasive wheels in UK workplaces.