In this article
PPE in Preventing Accidents
Personal protective equipment (PPE) is equipment that is worn to prevent accidents and injuries in hazardous working environments. PPE serves as a physical barrier between the worker and potential hazards associated with abrasive wheel operations.
Abrasive wheels are used within multiple industries, such as manufacturing, construction, metalwork, fabrication and woodworking. The wheels are covered in particles, such as grit, that are bonded with organic or inorganic substances, such as resin, and can be used to grind, shape, cut, sharpen, polish and finish metallic objects. Abrasive wheels can be fitted to portable, handheld machines or fixed grinding machines to modify or prepare different surfaces.
There are many potential risks and hazards associated with abrasive wheel operations, such as:
- Risk of eye injuries – One of the most significant dangers in abrasive wheel operations is the risk of eye injuries due to flying debris, particles or sparks that are generated during cutting, grinding or polishing. Without adequate eye protection such as safety glasses or face shields, workers are at risk of eye irritation, lacerations or more severe injuries that can lead to permanent vision loss.
- Potential for hand and arm injuries – Handling abrasive wheels exposes workers to the risk of hand and arm injuries from contact with rotating machinery, abrasive materials or sharp edges. Without proper hand and arm protection such as gloves, workers could suffer cuts, abrasions, punctures or burns when using abrasive wheels. Additionally, vibrations from the machinery can lead to hand-arm vibration (HAV) syndrome which can cause permanent numbness, pain, tingling, muscle weakening or carpel tunnel syndrome.
- Respiratory hazards – The dust and particulate matter produced during abrasive wheel operations can pose respiratory hazards if they are inhaled. Inhaling dust or fumes from dry grinding and prolonged exposure to airborne contaminants may lead to respiratory illnesses or lung diseases or could worsen any pre-existing respiratory conditions. Workers must wear appropriate respiratory protection such as dust masks or respirators to prevent the inhalation of harmful airborne particles.
- Noise-induced hearing loss – Abrasive wheel operations often generate high levels of noise, which can exceed safe exposure limits and cause hearing damage over time. Without proper ear protection such as earplugs or earmuffs, workers are at risk of noise-induced hearing loss, tinnitus or other hearing problems associated with prolonged exposure to loud noises.
- Risk of injuries from kickbacks – Incorrectly using or not maintaining abrasive wheels can lead to kickbacks, where the wheel suddenly jerks or kicks back towards the operator. Kickbacks can result in serious injuries such as lacerations, fractures or even amputations if the operator’s hands or body are in the path of the rotating wheel.
- Risk of fire or explosion – Abrasive wheel operations involving flammable materials or in environments with combustible dust pose a risk of fire or explosion if sparks ignite the combustible materials. Proper maintenance, ventilation and control measures are essential to minimise the risk of fire and explosion hazards in abrasive wheel operations.
- Machine hazards – Operating abrasive wheel machinery such as grinders, cut-off saws or polishing machines without proper training or supervision can expose workers to various machine hazards, including entanglement, crushing or electrical hazards. Safeguarding measures such as machine guards, lockout procedures and regular equipment maintenance are essential to prevent accidents and injuries.
PPE is essential for protecting workers during abrasive wheel operations, ensuring the health and safety of everyone in the workplace and ensuring compliance with health and safety laws and regulations.
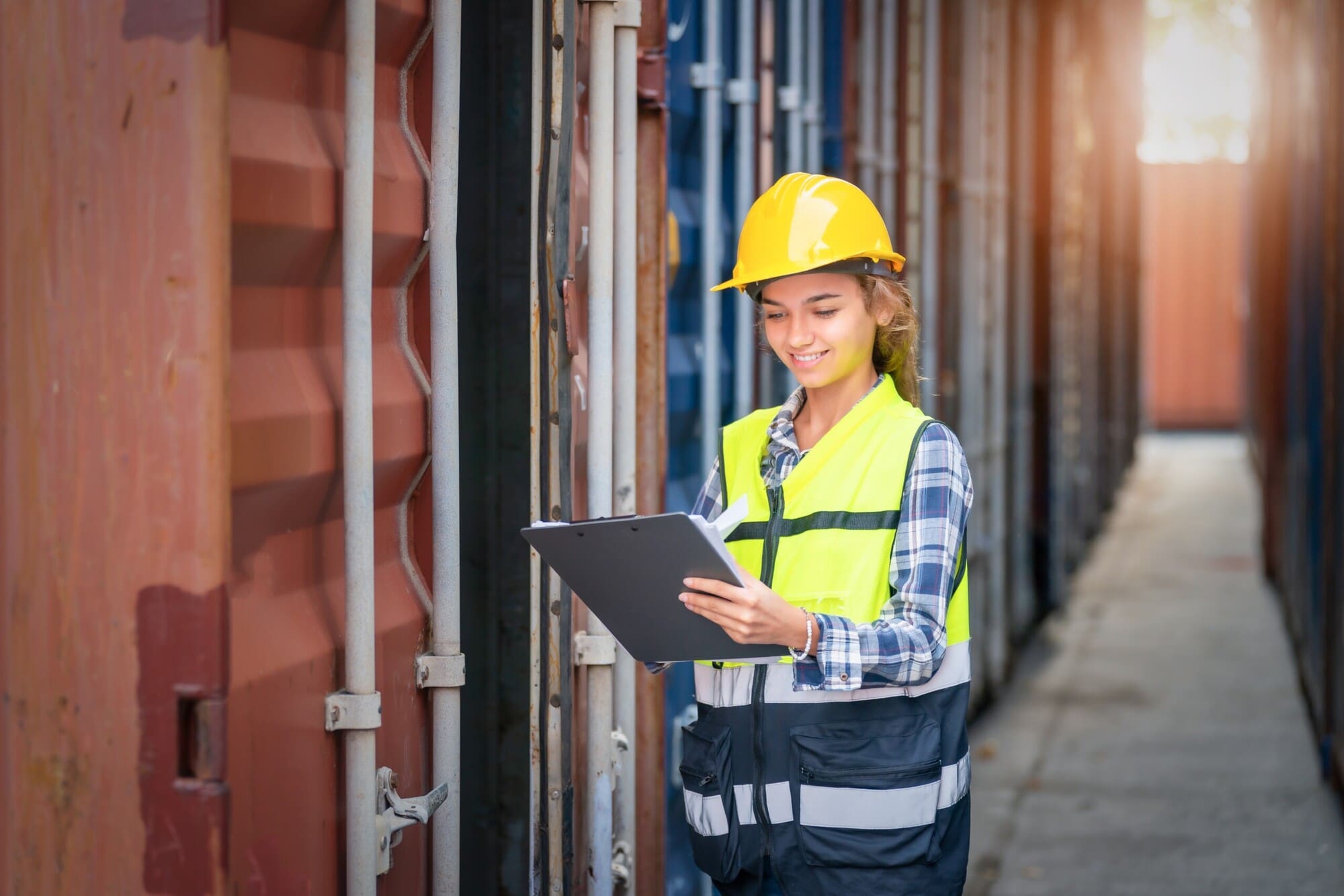
Understanding PPE
In abrasive wheel operations, where workers are exposed to various hazards such as flying debris, dust, noise and potential contact with rotating machinery, several types of PPE are necessary to ensure worker safety.
Different types of PPE are available, depending on the type of work you are engaging in and the part of your body that requires protection.
The most common types of PPE are:
- Eye protection.
- Hand and arm protection.
- Respiratory protection.
- Hearing protection.
- Head protection.
- Foot protection.
- Ear protection.
- Full body protection.
These types of PPE are essential for safeguarding workers against the hazards associated with abrasive wheel operations.
As well as other safety protocols for working with abrasive wheels, PPE can help to prevent accidents, injuries, illnesses and even death for people involved in abrasive wheel operations.
Some ways PPE can protect abrasive wheel operators include:
- Protection from impact and flying debris – In abrasive wheel operations, workers are exposed to the risk of flying debris and particles generated by the grinding or cutting process. PPE such as safety glasses and face shields create a barrier that shields the eyes and face from impact and flying debris, reducing the likelihood of eye injuries, lacerations and facial trauma.
- Protection from cuts, abrasions and burns – Abrasive wheels pose a significant risk of cuts, abrasions and burns to the hands and arms of workers. Gloves provide a protective layer that helps prevent direct contact with abrasive materials and rotating machinery, which reduces the risk of injuries.
- Respiratory protection from dust and particulate matter – Dust and particulate matter generated during abrasive wheel operations can pose respiratory hazards if inhaled. Respiratory PPE such as dust masks and respirators filter out airborne contaminants, safeguard the respiratory system and help to prevent respiratory illnesses and long-term health problems.
- Reducing noise-induced hearing loss – The noise generated by abrasive wheel operations can exceed safe levels and lead to hearing damage over time. Ear protection devices, such as earplugs and earmuffs, help to reduce exposure to loud noises, protect workers from noise-induced hearing loss and maintain auditory health.
- Prevention of skin injuries and contamination – In some abrasive wheel operations, workers may be exposed to abrasive materials, chemicals or other hazards that can cause skin injuries or contamination. Full body protection, such as coveralls or aprons, creates a barrier that shields the skin from harmful substances and reduces the risk of skin injuries and chemical exposure.
- Protection from wheel contact – Contact with an abrasive wheel can result in serious injury. Wheel contact can occur if hair, clothing or other loose items (such as a lanyard or necklace) get caught in the wheel or drawn into the machinery. PPE can be worn over your clothing or hair to prevent injuries.
- Enhanced visibility and awareness – Certain types of PPE, such as high-visibility clothing, can improve worker visibility and awareness in the workplace and reduce the risk of collisions and accidents involving moving machinery or vehicles.
PPE for Eye Protection
Eye protection is particularly important when working with abrasive wheels because of the significant risks posed by flying debris, particles and sparks generated during grinding, cutting or polishing operations. Without appropriate eye protection, workers are vulnerable to a number of eye injuries, including abrasions, lacerations, contusions and even permanent vision loss. Abrasive wheel operations involve high-speed rotation and friction which can cause materials to break apart or dislodge. This can result in projectiles that can penetrate the eye or cause damage upon impact. Additionally, sparks produced during the process can pose a hazard if they come into contact with any part of your body, including your eyes. Wearing appropriate eye protection is essential to safeguard workers’ eyesight and prevent potentially life-altering injuries.
There are several types of PPE for eye protection that can be used when working with abrasive wheels, including:
- Safety glasses – Safety glasses are a fundamental form of eye protection used in abrasive wheel operations. They are designed to provide basic coverage and impact resistance against flying debris, particles and small objects. Safety glasses have durable frames and lenses made from materials such as polycarbonate, which offer high impact resistance and optical clarity. Some safety glasses also feature side shields to provide additional protection from peripheral hazards. Safety glasses are lightweight, comfortable to wear and suitable for most abrasive wheel applications where the risk of eye injuries is moderate.
- Safety goggles – Safety goggles offer enhanced protection compared to safety glasses, particularly against hazards that may enter from the sides, top or bottom of the eyewear. They provide a seal around the eyes, preventing debris, dust or liquids from reaching the eyes from various angles. Safety goggles have a flexible frame with indirect ventilation to minimise fogging while still maintaining airflow. They are suitable for more demanding abrasive wheel operations where there is a higher risk of splashes, chemical exposure or larger projectiles.
- Face shields – Face shields provide comprehensive coverage for the entire face and neck area, offering maximum protection against flying debris, sparks and chemical splashes. They consist of a transparent visor made from impact-resistant materials such as polycarbonate or acrylic, mounted on a headgear frame for support. Face shields are ideal for abrasive wheel operations involving large wheels, heavy-duty cutting or tasks where the risk of severe facial injuries is high. They can be worn alone or over safety glasses or goggles for added protection.
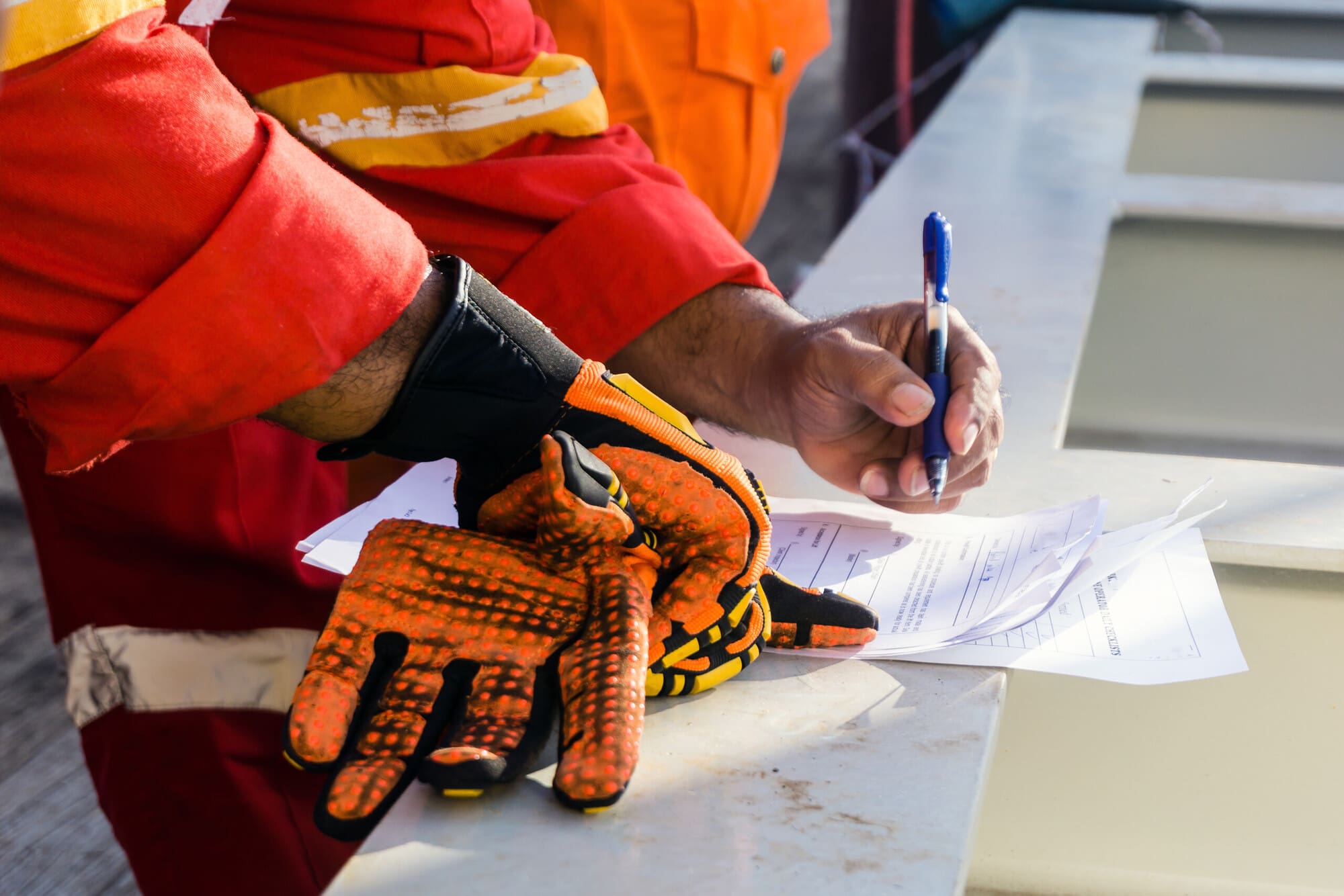
Hand and Arm Protection
Gloves play a critical role in protecting the hands and arms of individuals handling abrasive wheels. In abrasive wheel operations, workers are exposed to various hazards such as sharp edges, abrasive materials, high temperatures and rotating machinery. Gloves provide a protective barrier that helps prevent cuts, abrasions, punctures, burns and other injuries that may occur during the handling, operation or maintenance of abrasive wheels. Additionally, gloves offer insulation against heat and vibration, which can improve comfort and reduce fatigue during prolonged use.
Some of the glove options for workers handling abrasive wheels include:
- Leather gloves – Leather gloves are a popular choice for abrasive wheel operations because of their durability, abrasion resistance and thermal protection. They provide excellent grip and dexterity which allows workers to handle abrasive wheels and equipment with precision. Leather gloves come in various thicknesses and designs, including split leather, full-grain leather and pigskin leather, with each option offering different levels of protection and flexibility based on the specific requirements of the task.
- Kevlar gloves – Kevlar gloves are known for their strength, cut resistance and heat resistance. They are popular for handling abrasive wheels in high-risk environments. Kevlar is a synthetic aramid fibre that offers superior protection against cuts, punctures and abrasions while still maintaining flexibility and comfort. Kevlar gloves are lightweight and breathable and allow for extended wear without compromising dexterity or tactile sensitivity.
- Nitrile gloves – Nitrile gloves are commonly used in abrasive wheel operations where chemical resistance is required. Nitrile is a synthetic rubber compound that provides excellent resistance to oils, solvents, acids and other chemicals commonly encountered in industrial settings. Nitrile gloves offer good puncture resistance and durability while maintaining tactile sensitivity and grip, making them suitable for handling abrasive wheels and chemical agents simultaneously.
- Impact-resistant gloves – Impact-resistant gloves are designed to provide additional protection against blunt force impacts, crush injuries and vibrations associated with abrasive wheel operations. These gloves feature padded palms, reinforced knuckles and impact-absorbing materials such as gel or foam to minimise the risk of hand and arm injuries from accidental impacts or tool strikes. Impact-resistant gloves are ideal for tasks involving heavy-duty cutting, grinding or handling large abrasive wheels.
- Heat-resistant gloves – Heat-resistant gloves are recommended to protect workers from burns and thermal injuries if they are handling abrasive wheels at high temperatures. These gloves are typically made from heat-resistant materials such as leather, Kevlar or aluminised fabric and are capable of withstanding high temperatures without melting or degrading. Heat-resistant gloves provide insulation and thermal protection and allow workers to handle hot abrasive wheels and materials safely.
Respiratory Protection
Respiratory protection is essential in environments where dust or particulate matter is generated, such as in abrasive wheel operations. During these operations, the grinding, cutting or polishing of materials can produce airborne contaminants, including fine dust particles and hazardous chemicals. Inhaling these airborne pollutants can lead to respiratory issues, lung diseases and long-term health problems. Providing adequate respiratory protection is essential for safeguarding the health and well-being of workers in these environments.
Some of the respiratory PPE available include:
- Dust masks – Dust masks, also known as particulate respirators, are lightweight, disposable masks designed to filter out airborne particles. They provide basic protection against non-toxic dust, pollen and other solid particulates but may not offer sufficient protection against fine particles or hazardous substances. Dust masks are typically made up of multiple layers of filter material, such as polypropylene or fibreglass, and feature a flexible nose piece and elastic ear loops for a secure fit. They are available in various shapes, sizes and filtration levels, ranging from N95 to P100, with higher numbers indicating higher filtration efficiency.
- Half-face respirators – Half-face respirators cover the nose and mouth and provide more substantial respiratory protection compared to dust masks. They feature replaceable cartridges or filters that capture airborne contaminants, including dust, fumes and vapours. Half-face respirators are reusable and offer better sealing around the face, providing a tighter fit and enhanced protection against particulate matter and certain chemicals. They are commonly used in environments where moderate to high levels of respiratory protection are required, such as in abrasive wheel operations involving hazardous materials or airborne contaminants.
- Full-face respirators – Full-face respirators provide the highest level of respiratory protection by covering the entire face, including the eyes, nose and mouth. They feature a clear visor or lens that offers unobstructed vision and protects the eyes from airborne hazards. Full-face respirators are equipped with replaceable cartridges or filters that effectively filter out particulates, gases, vapours and other contaminants. They are suitable for use in environments where there is a risk of exposure to toxic chemicals, gases or particulate matter, such as in abrasive wheel operations involving hazardous materials or confined spaces.
- Powered air-purifying respirators (PAPRs) – PAPRs are advanced respiratory protection devices that use a battery-powered fan to draw air through filters and deliver clean, filtered air to the wearer. PAPRs offer a higher level of comfort and protection compared to traditional respirators, as they provide a constant supply of fresh air and reduce breathing resistance. They are ideal for use in environments where prolonged exposure to airborne contaminants is expected, such as in abrasive wheel operations involving high concentrations of dust, fumes or chemical vapours.
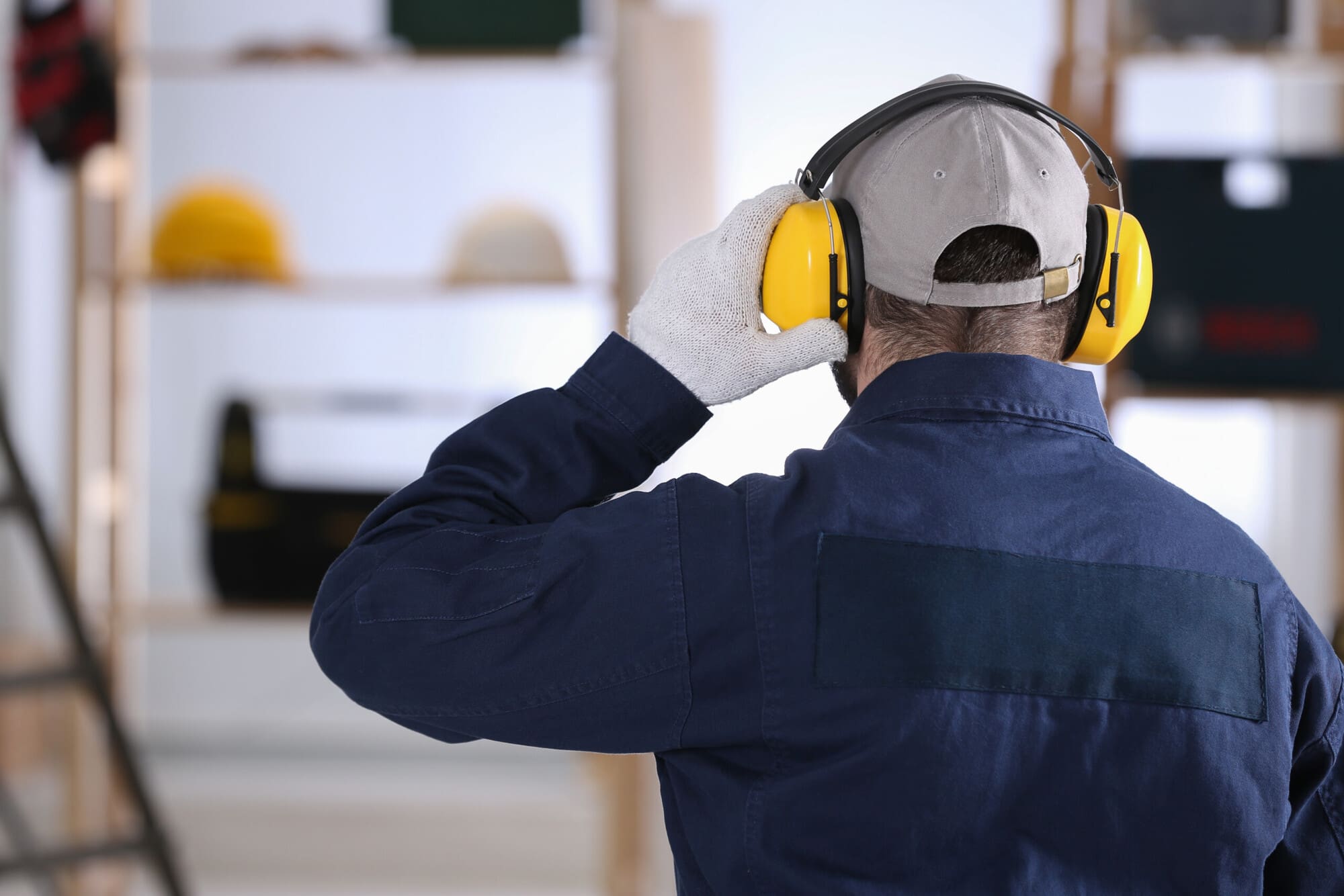
Hearing Protection
Abrasive wheel operations often involve machinery that generates high levels of noise. The noise is typically produced by the rotation of abrasive wheels, the operation of grinding or cutting equipment and the interaction between the abrasive material and the workpiece. The intensity and duration of noise exposure in abrasive wheel operations can vary depending on factors such as the type of machinery used, the materials being processed and the specific tasks being performed.
Prolonged exposure to high levels of noise can lead to various adverse effects on workers’ hearing health. These effects can include:
- Noise-induced hearing loss (NIHL) – Exposure to loud noises over time can damage the delicate structures of the inner ear, leading to permanent hearing loss. This condition, known as noise-induced hearing loss (NIHL), typically develops gradually and may go unnoticed until it is too late and significant hearing damage has occurred.
- Tinnitus – Tinnitus is a common symptom of noise exposure characterised by ringing, buzzing or other phantom noises in the ears. It can be temporary or persistent and may significantly impact a person’s quality of life and cause sleep disturbances, difficulties concentrating and emotional distress.
- Hyperacusis – Hyperacusis is a condition characterised by increased sensitivity to everyday sounds, making them seem louder than they actually are. It can result from prolonged exposure to loud noises and can significantly affect an individual’s ability to tolerate sound.
- Communication difficulties – High levels of noise can interfere with verbal communication, making it challenging for workers to communicate effectively with each other or hear important warnings or signals in the workplace. This can increase the risk of accidents and injuries due to miscommunication or failure to hear safety alerts.
Ear protection, such as earplugs or earmuffs, is essential for reducing the risk of noise-induced hearing loss and other adverse effects of noise exposure in abrasive wheel operations. Ear protection can help to prevent hearing loss, tinnitus and other ear-related problems by creating a physical barrier to reduce the amount of noise that reaches the inner ear.
Ensuring workers have appropriate ear protection also ensures compliance with safety regulations. Many occupational health and safety regulations require employers to provide ear protection to workers exposed to high levels of noise in the workplace. Providing earplugs or earmuffs not only helps protect workers’ hearing health but also ensures compliance with regulatory requirements and reduces the risk of penalties or fines for non-compliance.
Full Body Protection
Full body protection can help to ensure the health, safety and well-being of workers in abrasive wheel operations. These forms of PPE provide complete coverage to workers’ bodies and offer protection against various hazards that are present in the work environment.
There are four different levels of full body protection PPE: Levels A, B, C and D, with Level A offering the most protection and Level D offering the least protection. Full body protection can include:
- Coveralls.
- Aprons.
- A respirator.
- A hat or helmet.
- Goggles or safety glasses.
- Gloves.
- Appropriate boots.
Full body protection can protect workers from abrasive materials that can cause skin irritation, abrasions or cuts upon contact. In some abrasive wheel operations, workers may be exposed to chemicals, solvents or other hazardous substances that can cause skin irritation, burns or chemical burns. Coveralls or aprons made from chemical-resistant materials provide protection against chemical splashes or spills and reduce the risk of skin exposure and contamination.
During abrasive wheel operations, the friction and heat generated by the grinding or cutting process can pose a risk of burns or thermal injuries to exposed skin. Coveralls or aprons made from flame-resistant or heat-resistant materials offer protection against heat and sparks, minimise the risk of burns and ensure worker safety in high-temperature environments.
Full body protection can also help to prevent workers’ clothing from being contaminated by abrasive dust, particles or other contaminants present in the work environment. Providing an additional layer of protection over regular clothing, coveralls or aprons can prevent clothing from becoming damaged or contaminated during abrasive wheel operations and can ensure worker comfort and hygiene.
Some coveralls or aprons come in high-visibility colours or reflective designs to improve worker visibility in the workplace. Enhanced visibility is particularly important in environments where there is a risk of collisions, entanglement or other accidents involving moving machinery or vehicles as they can help to prevent accidents and injuries.
Full body protection is a popular PPE option when working with abrasive wheels. It is particularly recommended in the following circumstances:
- When working with abrasive materials that can cause skin irritation, abrasions or cuts, you may require comprehensive coverage to protect the body from injuries.
- When handling chemicals, solvents or other hazardous substances that pose a risk of skin exposure, you may need chemical-resistant clothing to prevent contact with the skin and contamination.
- When operating in high-temperature environments where the risk of burns or thermal injuries is present, you may require flame-resistant or heat-resistant clothing to provide protection against heat and sparks.
- When working in environments where there is a risk of clothing contamination with abrasive dust, particles or other contaminants, you may need to wear coveralls or aprons to minimise contamination and maintain worker hygiene.
- When working in low-visibility conditions or areas with increased risk of accidents, you may require high-visibility coveralls or aprons to enhance worker visibility and ensure safety in the workplace.
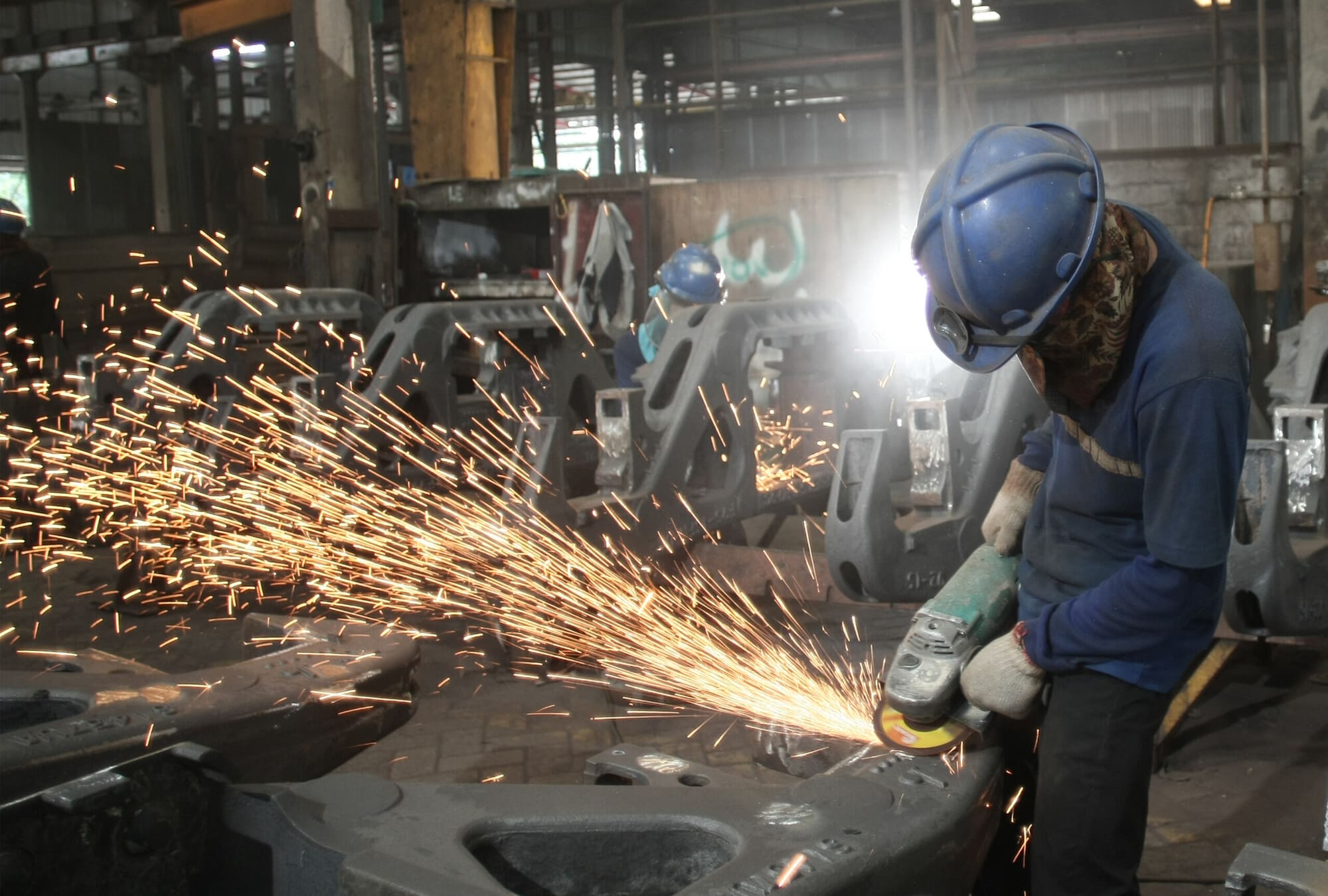
Proper Fit and Maintenance
Choosing PPE that fits correctly and comfortably can help to ensure it is effective in providing protection and promoting worker safety. PPE that fits properly forms a barrier between the wearer and any workplace hazards and ensures adequate protection against injuries or exposure. Ill-fitting PPE may leave gaps which allow hazards to enter and jeopardise the safety of the worker.
Comfortable PPE also encourages compliance and reduces the likelihood of workers removing or adjusting it improperly, which could compromise their safety. Uncomfortable or poorly fitting PPE can cause discomfort and irritation and can lead to distraction and decreased productivity. Properly fitted PPE allows for ease of movement and dexterity. This allows workers to perform tasks safely and efficiently. PPE that restricts movement may increase the risk of accidents or injuries due to impaired performance.
Ill-fitting PPE can exert pressure or cause chafing on the skin, leading to skin irritation, blisters or skin infections. PPE that fits properly can minimise the risk of skin problems and promote overall comfort and well-being. PPE should be available in various sizes and with adjustable features to accommodate individual differences, such as different heights and weights. Because of differences in body shape, male and female workers may also require different PPE. Customised or adjustable PPE ensures a better fit and comfort for each worker and can help to improve protection and safety.
Regular inspection, maintenance and replacement of PPE are essential to ensure it continues to be effective in providing protection and maintaining worker safety. Regular inspection allows you to detect any damage, wear or deterioration that may compromise the safety and integrity of the PPE. Damaged or worn-out PPE may not provide adequate protection and could increase the risk of injuries or exposure to hazards.
Routine maintenance and care can extend the lifespan of PPE, reduce the frequency of replacements and lower the overall cost. Regular inspection and maintenance help identify minor issues early on, prevent them from worsening and prolong the usable life of PPE. Establishing a system for regular inspection, maintenance and replacement of PPE promotes accountability and responsibility among workers and employers for ensuring workplace safety. It emphasises the importance of proper care and maintenance of PPE as part of a comprehensive safety programme.
Training and Education
Training and education in PPE awareness and usage are important elements of workplace safety programmes. Training and education can be beneficial in the following ways:
Encourages correct use
Training and education provide workers with the knowledge and skills they need to correctly choose, use and maintain PPE. Proper usage ensures that PPE effectively protects workers from workplace hazards and reduces the risk of injuries or exposure.
Improves awareness
Training increases awareness among workers about the potential hazards present in the workplace and the importance of using PPE to reduce these risks. By understanding the hazards they may encounter and the protective measures available, workers are more likely to use PPE consistently and appropriately.
Improves compliance
Educating workers on the importance of PPE usage and the consequences of non-compliance encourages them to adhere to safety protocols and policies. When workers understand the rationale behind PPE requirements and the potential risks of not using PPE, they are more likely to comply with safety guidelines.
Reduces accidents and injuries
Properly trained workers are better equipped to identify hazards, assess risks and take appropriate safety precautions, including using PPE. Training reduces the likelihood of accidents and injuries by empowering workers to recognise and respond to potential dangers effectively.
Creates a culture of safety
Training and education contribute to the development of a strong safety culture within the workplace, where safety is prioritised and valued by all employees. By investing in training initiatives, employers demonstrate their commitment to protecting the health and well-being of their workforce, which helps to create a culture of safety awareness and responsibility.
Increases confidence and competence
Training builds confidence and competence among workers in using PPE correctly and can lead to increased job satisfaction and morale. When workers feel confident in their ability to protect themselves from workplace hazards, they are more likely to approach their tasks with a sense of security and peace of mind.
Ensures compliance with regulations
- Occupational health and safety regulations require employers to provide training on PPE awareness and usage to employees. Some of the key regulations you should be aware of when working with abrasive wheels include:
- The Abrasive Wheels Regulations 1970.
- Provision and Use of Work Equipment Regulations (PUWER) 1998.
- Health and Safety at Work etc Act 1974.
- Control of Substances Hazardous to Health (COSHH) 2002 (as amended).
- The Personal Protective Equipment at Work (Amendment) Regulations 2022.
- The Management of Health and Safety at Work Regulations 1999.
- Under these regulations, employers must ensure that anyone operating abrasive wheels has sufficient training, including training on the correct usage of abrasive wheels, the potential risks and any precautions that should be taken. Compliance with these regulations ensures legal compliance and helps avoid potential fines or penalties for non-compliance.