In this article
Abrasive wheels are a common piece of equipment; however, they can pose significant health hazards and are a leading cause of injury in the workplace in the UK. Due to the risks associated with using them, there are various abrasive wheels regulations that place legal duties on employers. A failure to comply means you will be in breach of the law and this can result in significant fines.
According to the Health and Safety Executive, 135 workers were killed in work-related accidents in 2022/23 and there were 60,645 employee non-fatal injuries reported by employers in 2022/23.
What is an Abrasive Wheel?
Abrasive wheels are tools used for cutting and grinding various materials. The wheels are made up of abrasive particles bonded together, and they come in a variety of shapes and sizes. They can be used in:
- Metalworking – abrasive wheels are extensively used in metal fabrication and manufacturing for tasks like cutting, grinding and polishing metal components.
- Construction – they are often used in construction for cutting and shaping concrete, tiles and other building materials.
- Woodwork – in woodworking, abrasive wheels can be used for shaping and smoothing wood surfaces.
As there are so many different abrasive wheels, they can be defined by their characteristics, which can include:
- The grade of the wheel.
- The structure of the wheel.
- The grit size.
- The coating or bonding substance used.
- The type of abrasive material used.
There are various types of abrasive wheels and the type of abrasive wheel chosen depends upon the specific task and the material being worked on. Some types of abrasive wheels include:
- Straight grinding wheels – these are used for surface grinding, cylindrical grinding and tool sharpening. They are available in various diameters and thicknesses.
- Cylinder wheels – these are similar to straight grinding wheels but have a longer width, making them suitable for grinding large surfaces.
- Tapered grinding wheels – these are used for gear grinding, thread grinding and other precision applications.
- Straight cup wheels – these are designed for tool and cutter grinding.
- Dish grinding wheels – these are shaped like a shallow dish and are used for grinding on the face of the wheel rather than the periphery.
- Diamond wheels – these utilise synthetic diamonds as the abrasive material. They are ideal for grinding hard materials such as carbides and ceramics.
- Cubic Boron Nitride wheels – these are suitable for grinding ferrous materials and high-speed steel.
- Flaring cup wheels – these are similar to straight cup wheels but have a flaring shape for increased surface contact.
- Saucer grinding wheels – these resemble a saucer shape and are used for grinding on the periphery.
- Mounted points – these are small, abrasive wheels mounted on a spindle for precision grinding in hard-to-reach areas.
- Cut-off wheels – these are thin, reinforced wheels used for cutting various materials, such as metal and concrete.
- Flap wheels – these consist of abrasive flaps arranged radially around a central hub. They are used for blending, deburring and finishing.
- Wire wheels – these consist of wire bristles and are used for cleaning, rust removal and surface preparation.
- Grinding cones and plugs – these are cone-shaped or plug-shaped grinding wheels for use in tight spaces and intricate shapes.
- Rubber bonded abrasives – these combine abrasive grains with rubber to form flexible wheels for polishing and finishing.
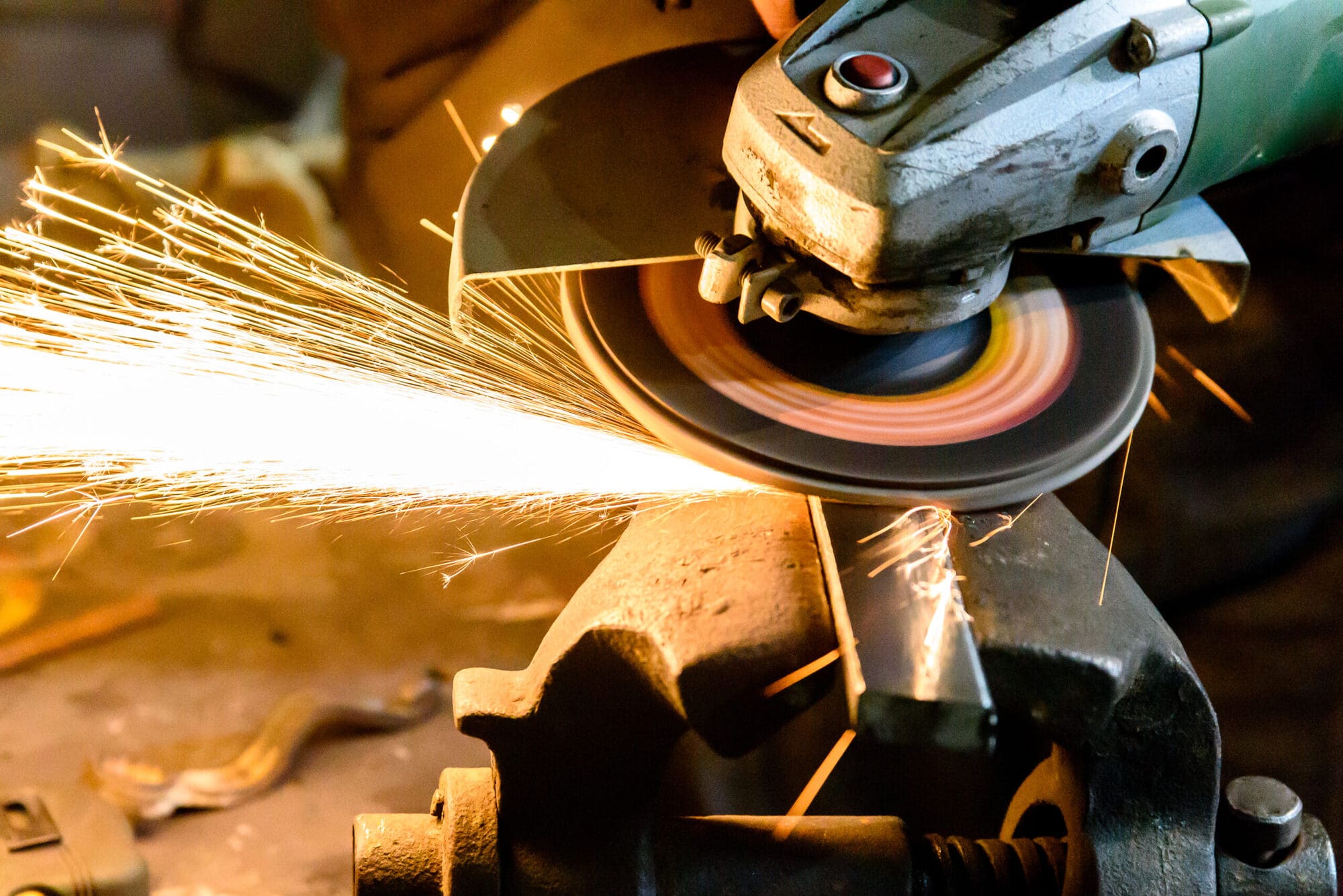
Hazards Associated with Abrasive Wheels
According to the Health and Safety Executive, almost half of accidents that involve an abrasive wheel are attributed to operator error or an unsafe work environment. There are around 5,000 injuries recorded each year by angle grinders alone. Abrasive wheels carry some of the most dangerous risks of any type of equipment used in the workplace and accidents involving abrasive wheels have the potential to cause life-changing injuries and even death.
Abrasive wheels are commonly used in various industries including construction sites, and, while they are essential tools, they can pose a number of hazards that can lead to serious injuries, therefore it is vital that proper precautions are taken. Some of the hazards associated with abrasive wheels include:
Eye injuries
Sparks, abrasive particles and debris can be thrown off during wheel operation, which can lead to eye injuries.
Contact with rotating parts
Workers may come into contact with the rotating parts of abrasive wheels during operation which can lead to injuries such as cuts, abrasions or, in some cases, more severe injuries if body parts are drawn into the machinery itself.
Dust and particles
Grinding and cutting operations create airborne dust and particles. Inhaling these particles can cause respiratory issues.
Issues due to noise and vibration
The high-speed rotation of abrasive wheels generates a loud noise and vigorous vibrations. Prolonged exposure to these can potentially lead to hearing loss and musculoskeletal disorders.
Wheel breakage
Abrasive wheels can break during operation, particularly if they are damaged or improperly put together. This can result in flying fragments that pose a significant risk.
Incorrect wheel selection
When using an abrasive wheel it is crucial to use the appropriate wheel for the material being worked on. Choosing the wrong type of abrasive wheel for a specific task can result in reduced efficiency, increased wear, and the potential for hazards to occur.
Abrasive wheels rotate between 6,000 and 15,000 rpm – should the tool come into contact with skin, the injuries can be devastating. Do not touch the wheel or apply excessive force during use.
Identifying Risks: Common Scenarios
There are some common risk scenarios when it comes to using abrasive wheels. These include:
Over-speeding
Operating the abrasive wheel at a speed higher than necessary can lead to wheel failure and potential injury. You should follow the manufacturer’s recommendations for operating speeds and use equipment with speed controls in order to prevent over-speeding.
Abrasive wheel breakage
Abrasive wheels can break during use, causing fragments to come loose. You should regularly inspect wheels for damage, and replace any that show signs of wear or damage. Use the appropriate wheel for the task.
Lack of personal protective equipment (PPE)
Failure to use appropriate PPE, such as safety glasses, gloves and hearing protection, can increase the risk of being injured. Prevention ensures that operators wear the necessary PPE for the specific task, as recommended by safety regulations and guidelines.
Poor handling and storage
Mishandling or improper storage of abrasive wheels can result in the tools becoming damaged, leading to potential hazards during use. You should store abrasive wheels in a dry, cool place away from direct sunlight.
Exposure to hazardous substances
The use of abrasive wheels may generate dust or fumes containing hazardous substances. You should use appropriate ventilation systems, respiratory protection, and other measures in order to minimise exposure to harmful substances.
Not using the tool correctly
Using the wrong tool or attachment with an abrasive wheel can result in accidents. You should only use tools and attachments that are compatible with the abrasive wheel and are recommended by the manufacturer.
Assessing Risks: Risk Evaluation Methods
Evaluating the risks associated with the use of abrasive wheels is vital in order to ensure a safe working environment for all. Employers and workers should follow established risk assessment methods in order to identify, assess and control any potential hazards. Workers should be aware of the hazards, how to reduce the risks and what to do in an emergency situation. Some general things to consider when conducting a risk evaluation for the use of abrasive wheels include:
- You should identify what the hazards are – this includes identifying all potential hazards associated with abrasive wheel use. These may include things like contact with the rotating abrasive wheel, flying debris, noise, vibration, dust and fumes.
- Assess the associated risks – a thorough risk assessment should be completed without cutting any corners. You should evaluate the likelihood and potential outcomes of each identified hazard. You should consider the frequency and duration of exposure and take into account the competence of operators and the adequacy of training that has been provided to them.
- Ensure the correct training has been provided and assess their competency levels – you should ensure that operators are adequately trained and they are competent in using abrasive wheels. They should also be provided with information on safe working practices and procedures.
- Review the existing controls that are in place – you should review the effectiveness of existing control measures. This should be done regularly. You should adjust or update the control measures as necessary.
- Have safe operating procedures in place – you should develop and implement safe operating procedures for the use of abrasive wheels. Workers should have access to these and they should understand the importance.
- Documentation – you should document the risk assessment process, including what the identified hazards are, what the risk levels are, and what control measures you have in place. You should always keep records of training, maintenance and inspections.
- Regularly review the existing risk assessment – regularly review and update the risk assessment, especially when there are changes in equipment, processes or personnel. There are many things that can change within a workplace and therefore it is important to ensure that the current risk assessment is still valid.
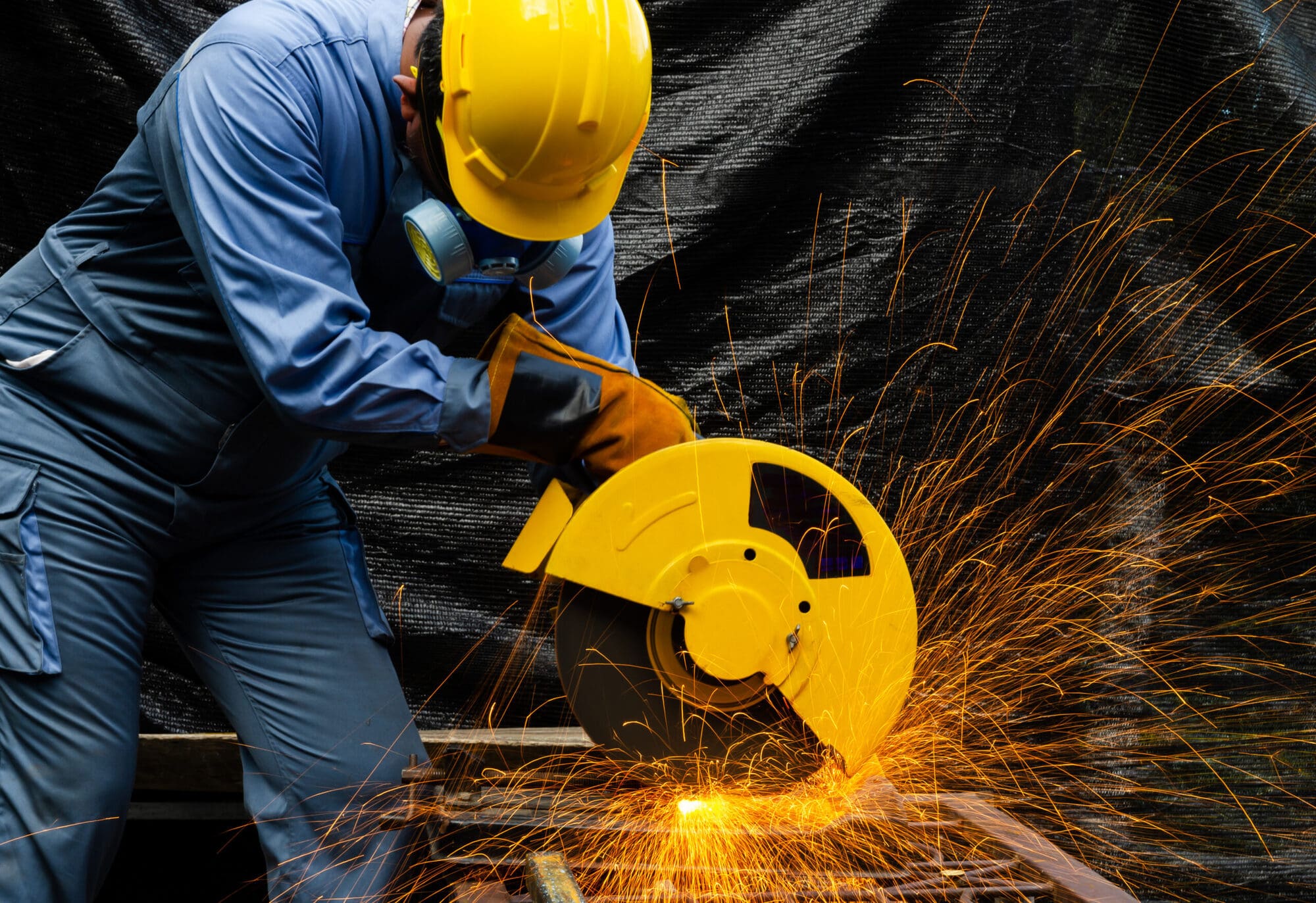
Controlling and Preventing Risks: Best Practices
It is the Provision and Use of Work Equipment Regulations Act 1998 (PUWER) that sets out abrasive wheels regulations. The regulations are intended to keep workers safe while using equipment and machinery. For further reading about what equipment is covered by PUWER, please see our knowledge base.
Protecting the public during construction projects is also important when thinking about preventing risks.
Taking preventative measures in order to minimise the risks associated with abrasive wheels is essential in order to protect workers and others who may be around when the abrasive wheel is in use. Some important things to consider are:
- Ensure there is effective training in place and that workers are competent – you should ensure that only trained and competent individuals are allowed to operate abrasive wheels. You should provide comprehensive training on the use, mounting and maintenance of abrasive wheels. Legal requirements mean that you can’t operate a machine with an abrasive wheel without being trained. Appropriate records of the training should be kept.
- Ensure regular inspection and maintenance of the equipment – you should ensure regular inspections of abrasive wheels for any signs of damage, wear or imbalance. You should ensure that the spindle speed of the machine matches the maximum operating speed of the abrasive wheel. You should replace damaged or worn wheels without delay.
- Selection of abrasive wheels – you should choose the right type of abrasive wheel for the specific task and material being worked on. You should check the manufacturer’s recommendations and specifications for the abrasive wheel before using it.
- Safe operating procedures – establish and enforce safe operating procedures for the use of abrasive wheels. You should always follow manufacturer guidelines and industry guidelines and best practices.
- Ensure workers have access to and are using the correct PPE (Personal Protective Equipment) – you should ensure that operators wear appropriate PPE, such as safety glasses or goggles, hearing protection and gloves. Face shields should also be used to protect against flying particles, especially during grinding operations.
- Ensure the work area is safe – keep the work area clean and free of clutter at all times in order to prevent tripping hazards. You should ensure proper lighting for better visibility during operation of the abrasive wheel. You should mark and secure the work area in order to prevent any unauthorised access.
- Handling and storage – you should handle abrasive wheels with care in order to prevent damage during transport and storage. You should store abrasive wheels in a dry and cool environment away from any direct sunlight.
- Emergency procedures – you should ensure that emergency procedures are in place, including first aid and the availability of emergency stop controls. Training should be provided on what to do in case of accidents or injuries occurring.
- Carry out regular risk assessments – conduct regular risk assessments in order to identify and address potential hazards that are associated with abrasive wheel use. An effective risk assessment is also crucial in order to identify significant danger to workers’ health and safety. It should evaluate the likelihood and potential consequences of these hazards, and should determine appropriate measures in order to mitigate or manage the risks.
Safety in the use of abrasive wheels can be found in the HSE regulations.