In this article
What is manual handling?
Manual handling refers to transporting or supporting a ‘load’ using bodily force.
A load may be an object, a person or an animal.
Manual handling includes actions such as lifting, lowering, pushing, pulling, supporting, restraining or carrying.
Manual handling is required during a range of activities both in and out of the workplace. If the nature of your work requires you to do manual handling tasks, your employer has a duty of care to provide a safe working environment and to protect your health and safety as far as practicable.
Across most sectors, manual handling is necessary to some degree, however, in some workplaces manual handling procedures are required more frequently or are considered ‘high risk’ operations.
Sectors where manual handling is common include:
- Construction
- Manufacturing
- Health and Social Care
- Logistics/ transport of goods
Examples of manual handling in the workplace include:
- Stacking pallets in a warehouse
- Turning or moving a bedridden patient in a care home
- Lifting an animal onto the examination table at a vet surgery
- Pushing cages of linen in a hotel
- Unloading boxes from a delivery van
- Rolling casks of ale into a pub cellar
Consequences of poor manual handling may include bodily injuries such as:
- Musculoskeletal disorders
- Strains and sprains
- Pulled muscles
- Broken bones
- Crushed hands or feet
Injuries from manual handling can cause people pain, inflammation and significant amounts of stress and upset.
Poor manual handling can delay tasks being completed, reduce productivity and cause employees to lose workdays due to injuries, which has an economic impact on both employees and employers.
Incorrect manual handling techniques can also result in accidents, damage and breakages to items in the load.
Manual handling plays a role in more than 20% of workplace injuries and is one of the leading causes of musculoskeletal disorders (MSDs) in the UK. MSDs accounted for almost one third (32%) of instances of work-related ill health in 2023/24, leading to 7.8 million working days being lost.
One of the most common parts of the body to hurt when doing a manual handling task is the back. Each year millions of workdays are lost due to back pain, which has a significant impact on workplace productivity and profit margins. Careful manual handling reduces the chances of workers being injured or developing conditions relating to workplace ill-health.
Manual handling becomes a problem when it is hazardous because it is done in an improper way, is poorly planned or otherwise puts people at risk. Manual handling legislation sets out guidance for employers and employees to follow to ensure that manual handling in the workplace does not pose an undue hazard that puts people at risk. By following the guidelines set out in legislation, the risk of injuries, accidents or financial losses due to manual handling will be significantly decreased.
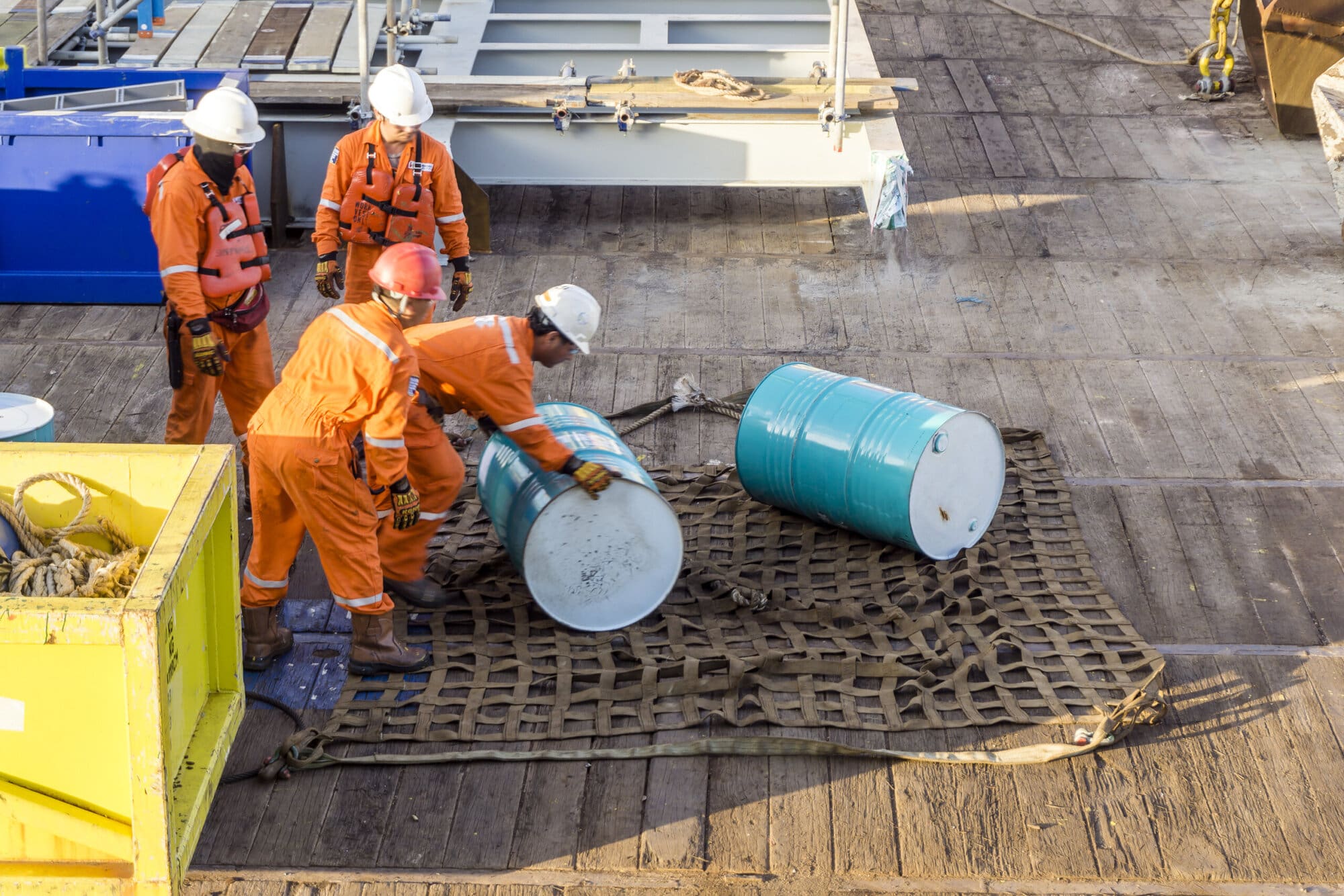
Manual Handling Regulations Legislations
Key manual handling legislation includes:
- Manual Handling Operation Regulation 1992 – as amended by the Health and Safety (Miscellaneous Amendments) Regulations 2002
This legislation sets out duties for both employers and employees and explains how to avoid, assess and reduce the risk of injury from manual handling.
Additional important legislation includes:
- The Health and Safety at Work Act 1974
- The Health and Safety at Work Regulations 1999
The Health and Safety at Work Regulations 1999 sets out the minimum requirements for employers. These regulations require employers to:
- Identify hazards that could cause injury or illness to people within the workplace
- Assess the likelihood that someone will be harmed and how seriously (the risks)
- Decide what action needs to be taken to remove the hazards or, when this is not possible, to reduce the risks (controls)
The law does not set out safe weight limits when it comes to handling loads, although the HSE provides guidelines on safe limits. Thes guidelines are based on assumptions about the lifting capacity for men and women and will not necessarily apply to all workers.
The HSE guidelines state:
- The maximum weight limit for men is 25 kg (55 lbs)
- The maximum weight limit for women is 16 kg (35 lbs)
These weight limits refer to loads that are held close to the body at around waist height. The HSE has different weight limits for handling at shoulder, elbow or lower leg height.
Employers should not expect their employees to handle more weight than they safely can and employees should always work safely within their own capabilities and not overstretch themselves.
If employers are providing equipment in the workplace to assist workers with manual handling duties, they have a duty to provide health and safety information and ensure equipment is safe fit for purpose. Key legislation that covers the safety of workplace equipment includes:
- Provision and Use of Work Equipment Regulations 1998 (PUWER)
- The Lifting Operations and Lifting Equipment Regulations 1998 (LOLER)
PUWER builds on legislation already set out in the Health and Safety at Work Act and stresses the duty on employers to protect workplace health, safety and welfare.
LOLER places duties on people who own, operate or have control over lifting equipment.
Duties as an employee
Under section 7 of the Health and Safety at Work Act, employees have a duty to take reasonable care of their own health and safety and the health and safety of others.
Additionally, employees should:
- Work cooperatively with managers or employers
- Make use of equipment that is provided for them (for example machinery or mechanical aids) and to use it appropriately and as instructed
- Follow safe systems of work
- Take care that their work activities do not out others at risk
- Report any accidents, injuries or near misses
Good housekeeping plays an important role in manual handling. Areas that are cluttered, untidy or otherwise unsafe pose a hazard to people who are carrying out manual handling tasks. To avoid accidents, including slips, trips and falls, employees should work together as a team to ensure:
- Walkways and corridors are clear and free from tripping hazards
- Stock rooms are kept tidy, including removing and disposing of any cardboard, packaging and empty pallets
- Spillages are mopped up and cleaned immediately, with appropriate signage put out to warn others that floors may be slippery or wet
- Everyone takes responsibility for keeping the workplace clean, tidy and free from unnecessary hazards
It is vital that employees engage with any training that they are given on manual handling and take steps to avoid unsafe working practices. Additionally, they should report any unsafe work or hazards that they see. Employees should reasonably expect that their employer will protect them at work, however employees must also take some responsibility for their own health and safety and avoid complacency or taking necessary risks.
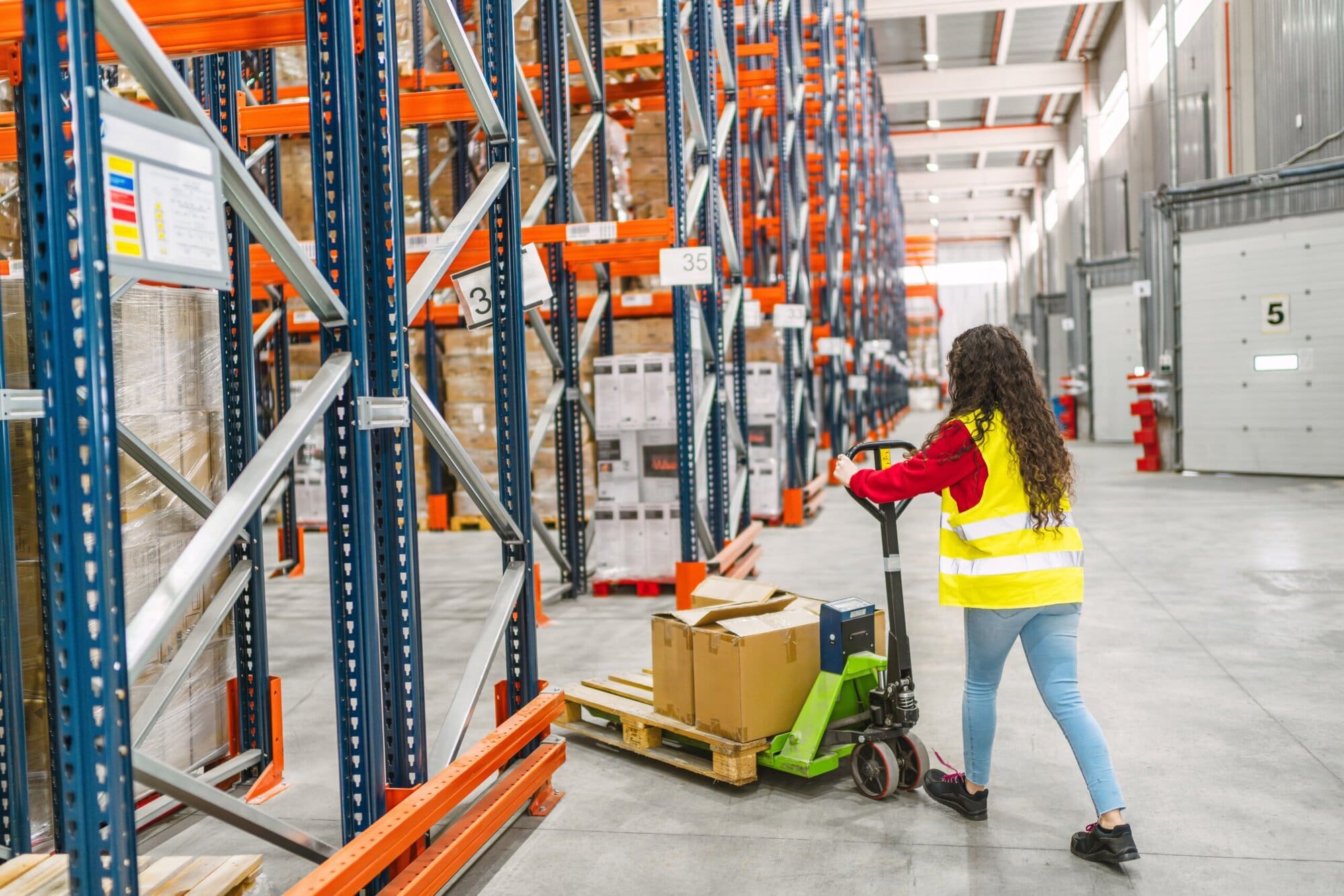
Duties as an employer
Employers have a duty to look after the health and safety of their workers in order to protect them from harm due to workplace activities. Manual handling regulations require employers to:
- Find ways to avoid hazardous manual handling where possible
- Identify and assess risks that may arise from manual handling
- Take steps to reduce the risks as far as reasonably practicable
Employers must act in line with any law and legislation on manual handling and should keep clear, organised records to prove that they have been compliant. This includes training records and the proof of any risk assessments.
Risk assessments
Employers should consider the management of manual handling as part of their wider responsibilities for health and safety at work. They will need to conduct a risk assessment for manual handling tasks.
A risk assessment is a structured process that is used to identify hazards, assess risks and put controls in place to minimise the chance of harm occurring.
Risk assessments should only be conducted by a competent person, for example a manager or health and safety professional.
The basic steps of a risk assessment include:
- Identify the hazards
- Assess the risks and decide who may be harmed and how
- Control the risks
- Record your findings
- Monitor and review
In any organisation with more than five employees, the findings of any risk assessment must be recorded in writing.
Records of risk assessments should be detailed and include:
- Dates of risk assessments
- The findings (risks)
- Controls already in place
- Controls that need to be put in place (including timeframes)
- How often findings will be reviewed
- Details of monitoring and review processes
Risks from manual handling may arise from physical factors such as:
- The task in hand
- The load
- The working environment
- An individual’s capacity
- How work is organised and/or allocated
- How repetitive manual handling tasks are
- The pace, frequency and duration of work
- Availability of handling equipment or handling aids
In addition to physical factors, the likelihood of a person being injured can be influenced by psychosocial factors during manual handling, for example:
- How stressed or tired workers feel
- How tight deadlines are
- To what extent they have control over their work and working methods
To improve workplace wellbeing, it is important for employers to consider both physical and psychological factors when assessing risks and deciding what controls need to be put into place.
Employers can use the MAC tool to identify high risk workplace manual handling activities. The MAC tool can help employers with understanding, identifying and categorising levels of risk using a numerical and colour coded system.
Employers also need to complete additional risk assessments for vulnerable workers, for example new and expectant mothers, disabled workers or people returning to work following a workplace injury.
Reducing risks
Eliminating the need for manual handling completely is always better than putting controls in place, however this is often impossible. If manual handling is a necessary part of daily activities in the workplace, employers have a responsibility to make sure they can prove that they have taken steps to reduce the risks as far as practicable.
Steps to take to reduce risks from manual handling may include:
- Breaking loads down into smaller parts to make them lighter and easier to grasp
- Changing the systems of work so more people work on tasks, loads have to be carried shorter distances, less twisting movements are needed, or reducing the need to move loads from the floor to above shoulder height
- Improving the work environment including providing better lighting, more space or safer flooring
- Ensuring workers have access to adequate resources and help
Additionally, employers should:
- Routinely observe manual handling operations to ensure activities are being carried out safely and as instructed
- Encourage employees to report near misses (an unsafe incident where no one was harmed but they could have been)
- Collect feedback from workers to check how they feel about manual handling and workplace safety
Using mechanical aids and making use of technology and automation reduces the need for manual handling using bodily force and, in some cases, can eliminate manual handling completely.
Mechanical aids that assist with manual handling include:
- Trollies
- Hoists
- Wheelbarrows
- Conveyor belts
- Lift trucks
If employers provide mechanical aids to help workers with manual handling it is essential that they provide training in how to properly use them as any workplace equipment can introduce new risks to workers.
Lifting equipment is covered under The Lifting Operations and Lifting Equipment Regulations 1998 (LOLER) regulations and most workplace equipment is also covered under Provision and Use of Work Equipment Regulations 1998 (PUWER) regulations. PUWER regulations require employers to provide their workers with equipment that is safe to use and fit for purpose.
PUWER regulations highlight essential safety information for employes on workplace equipment, for example:
- Correct installation of workplace equipment
- Providing equipment that is fit for purpose and only used for its intended purpose
- Regular inspection and maintenance
- Proper training in safe use of workplace equipment
- How to report hazards
- The importance of good record keeping
Regulation 8(2) of LOLER defines a lifting operation as ‘an operation concerned with the lifting or lowering of a load’. A ‘load’ is the item or items being lifted, which may be an object, animal or person.
Under LOLER regulations:
- Lifting equipment must be fit for purpose and of adequate strength and stability
- Lifting equipment should be installed or fixed in a way that reduces the risk of a load falling or otherwise injuring someone due to coming loose
- All lifting equipment must be clearly marked with information on ‘safe working loads’ (SWL) – the maximum weight that the equipment can safely lift
- There are additional regulations and requirements for equipment that is used to lift people, including more regular safety inspections, to reduce the chance of someone being injured during lifts
Additionally, LOLER sets out guidelines for the planning, organisation and operation of lifting exercises and states that all operations involving lifting equipment must be:
- Properly planned and undertaken by someone competent
- Appropriately supervised
- Conducted in a way that is as safe as possible
Benefits of controlling risks
There are multiple benefits for employers who control the risks of manual handling including:
- Improved productivity within the workforce
- Reduction in retraining costs
- Reducing company liability
- Reducing instances of injury/ ill health to workers
- Improved business reputation
In addition to conducting a thorough risk assessment and putting appropriate controls in place to protect workers, employers should also ensure that their employees have received appropriate guidance and training in manual handling.
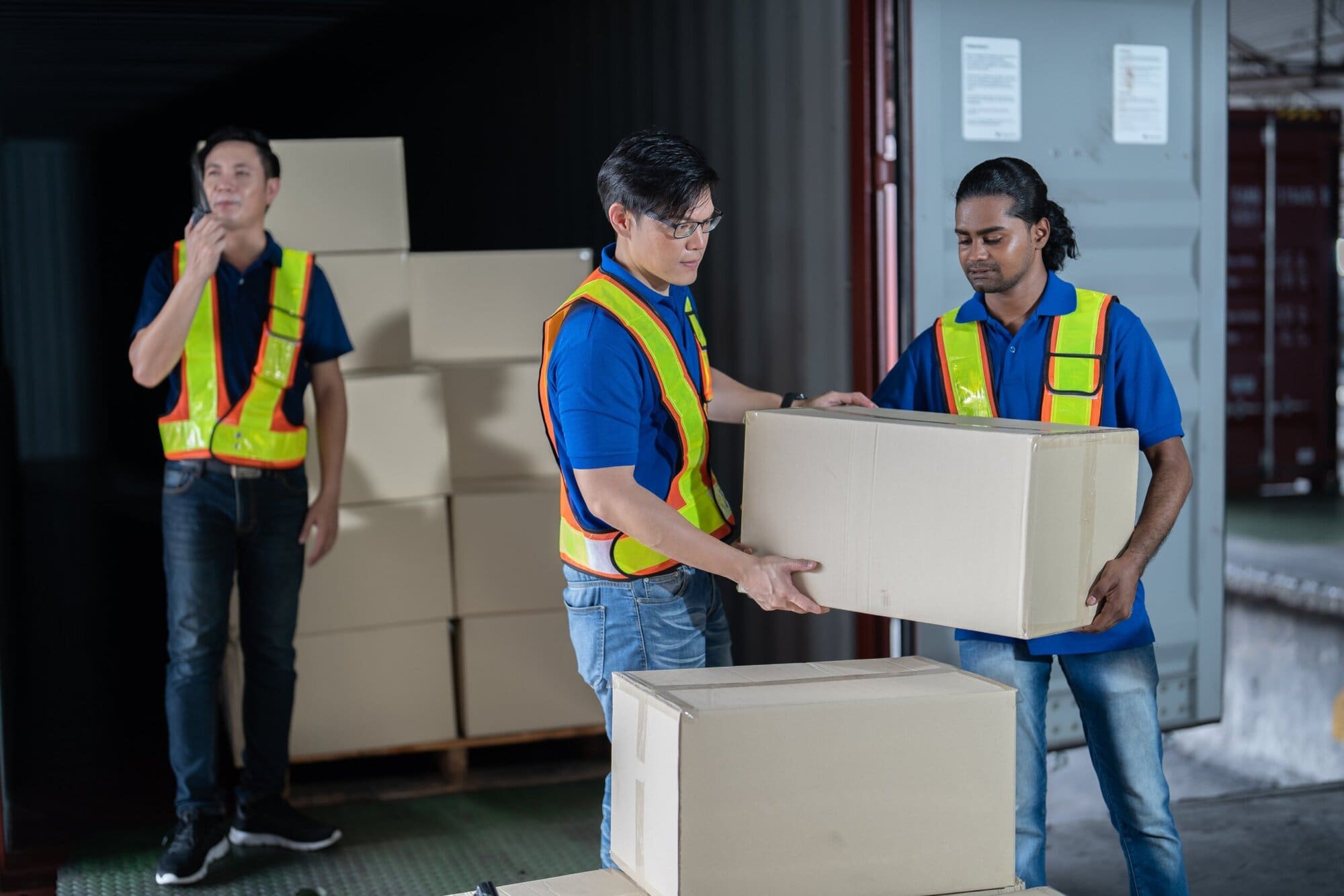
Providing guidance and training
It is essential that employees are provided with proper guidance and training in manual handling prior to undertaking such activities. Training teaches workers how to work safely and competently and will reduce the risk of accidents or injuries occurring.
Effective guidance and training in manual handling should include:
- A definition of manual handling
- Examples of manual handling (including safe lifting, safe pushing and pulling, safe carrying)
- Safe postures for manual handling
- How to work safely (including how to use lifting and handling aids)
- What to avoid when manual handling
- The risks of poor manual handling
- An overview of manual handling regulations and legislation
Training should be relevant to the nature of the work involved and suitable for the individuals undertaking training with special considerations for migrant workers who may have English as a second language, workers with disabilities or very young workers.
Effective training programs should be engaging and interesting, preferably with a mixture of classroom style learning and hands-on exercises. Practical components allow trainers to observe trainees and advise them on anything they are doing wrong which can help them avoid slipping into bad habits. Additionally, after any workplace training, there should be some mechanism to check everyone’s understanding, such as a quiz or short exam.
Providing manual handling training and education should only ever be used in conjunction with other controls, such as redesigning tasks or providing mechanical aids. Training alone is never a sufficient control for manual handling.
Training courses should always be given to new employees and refresher training provided periodically. Additionally, training should always be done when there are significant changes to the methods used at work, a skills gap has been identified (for example after an incident or near miss) or when new legislation is passed. Evidence of who has attended training needs to be kept and stored safely in case it needs to be checked later on.