What is manual handling?
In this article
Did you know that:
- 1 in 3 workplace accidents are caused by manual handling?
- A staggering 300,000 people in the UK suffer from back pain due to manual handling accidents, according to UNISON?
- The Health and Safety Executive (HSE) reported that 38.8 million working days were lost in 2019/2020 as a result of workplace illness or injury?
- 11.6 million working days are lost specifically as a result of work-related musculoskeletal disorders?
These figures demonstrate that not only is correctly following manual handling procedures vital to the health and safety of workers, but also how incorrect manual handling can have a detrimental financial effect and an overall negative impact on productivity.
So what is manual handling? Manual handling is defined as the transporting or supporting of a load by hand or bodily force. This could include lifting, putting down, pushing, pulling, carrying, manoeuvring or transporting the load. The load could be an object, a person or an animal.
Manual handling is an essential health and safety concern in the workplace. Although not all types of manual handling are considered hazardous, most workers, jobs and employment sectors have some form of manual handling as part of their job role. This means that all employers and employees in the UK should be aware of manual handling regulations.
Hazardous manual handling can result in the development of musculoskeletal disorders. These can occur because of heavy manual labour, repetitive handling, the exacerbation of previous or existing injuries, awkward positioning, and the use of incorrect, or incorrectly using, equipment.
Musculoskeletal disorders are the most common injury that occurs as a result of manual handling. Musculoskeletal disorders include upper limb or neck disorders, lower limb disorders, back injuries or pain, and damage to joints or other tissue in the body.
Other common injuries that can occur as a result of manual handling include:
- Sprains.
- Strained or pulled muscles.
- Prolapsed discs.
- Hernias.
- Crushed limbs.
- Cuts and abrasions.
- Broken or fractured bones.
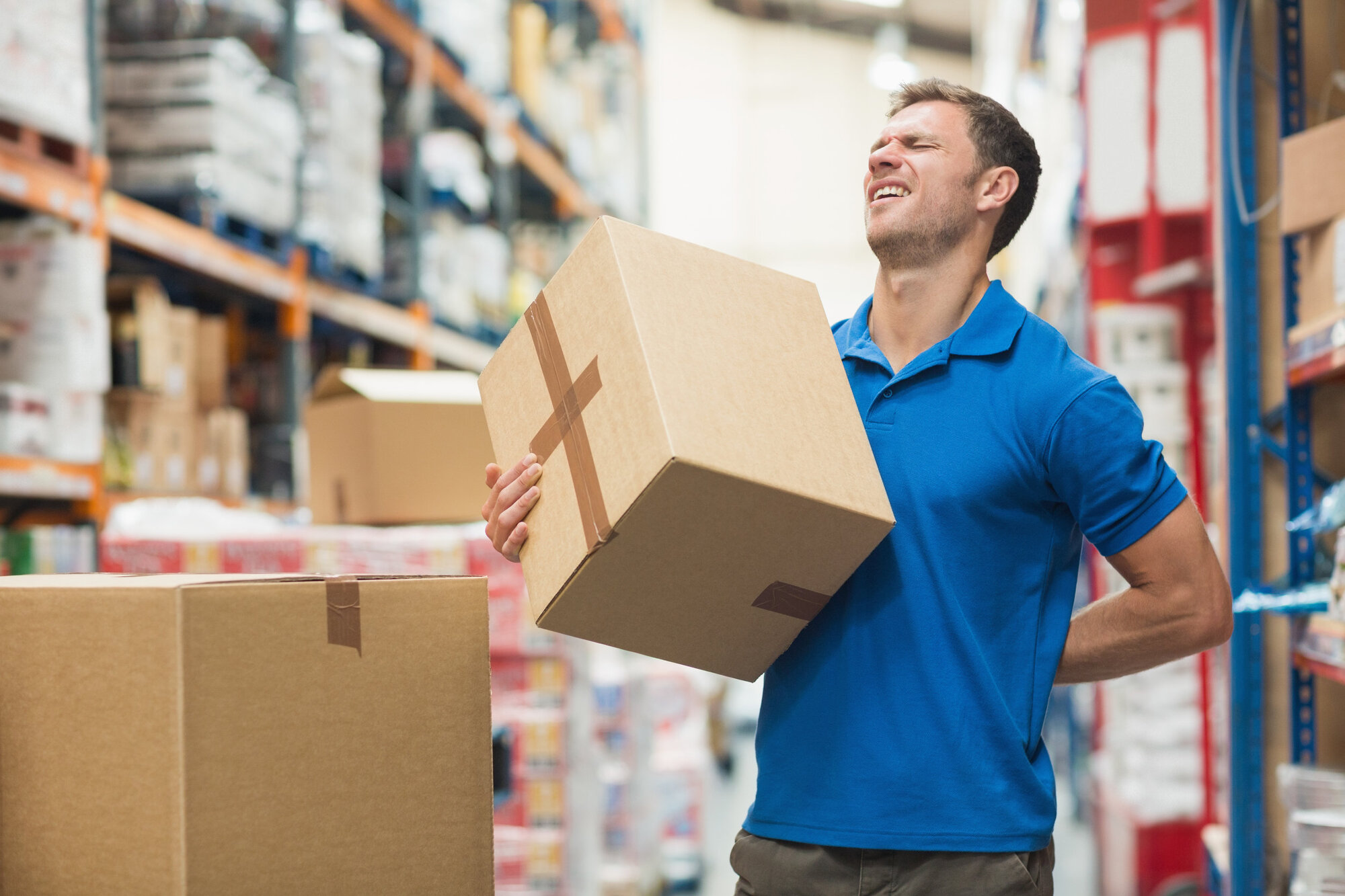
Manual handling operations
Manual handling operations are any tasks, activities or responsibilities in the workplace that involve manual handling. Manual handling operations include a range of tasks, and are not limited to tasks such as lifting, pushing and carrying. Manual handling in the workplace could also include repetitive tasks such as typing, assembling, cleaning, packing, making deliveries, operating machinery or equipment, and handling or restraining animals.
Manual handling operations occur in all types of workplaces and industries, including building sites, factories, hospitals, care homes, schools, farms and shops.
Being aware of manual handling operations helps employers to identify which manual handling activities or operations are potentially hazardous. This can help employers and employees to ensure incorrect manual handling does not occur in the workplace.
There are some basic manual handling principles that can be followed to reduce the risks associated with manual handling operations. These principles may be most relevant to manual handling tasks such as lifting, carrying and transporting.
1. Plan
There are several ways you can plan manual handling to ensure you are reducing the risk to the lowest possible level. If you are lifting, carrying, manoeuvring or transporting a load, use a weight guide to determine how much weight you are able to carry and how to distribute this weight.
Although there are no legal weight limits for manual handling, there are suggested guidelines for the safe maximum weight that should be lifted for employees. For more information on manual handling weight limits, consult our knowledge base. You can also plan your route, making sure there are no obstacles, and calculate the amount of time the task will take.
2. Position/Posture
Ensuring the correct position before handling a load can help reduce the risk of injury. You should place your feet shoulder-width apart and, where possible, grasp the load with both hands. If the load is being picked up from the floor, you should lower yourself towards the ground. Ensure you grasp the load firmly and use your leg muscles to lift the load into a standing position. Injuries are most likely to occur when your arms are extended, or the load is positioned at high or low levels.
3. Technique
When holding the load, it is important to keep your back straight, carry the load with straight arms, keep the load close to your body and keep your head up and positioned straight forward.
4. Clothing
It is important to wear clothing that is suitable to the task and will not obstruct or cause any risk to the handler. Appropriate footwear may also be an important consideration.
5. Placement
Putting the load down can cause injuries. The load should never be dropped or put down with force, nor should the handler make quick movements. The load should be lowered in the same way that it was picked up, ensuring the correct posture and technique are followed.
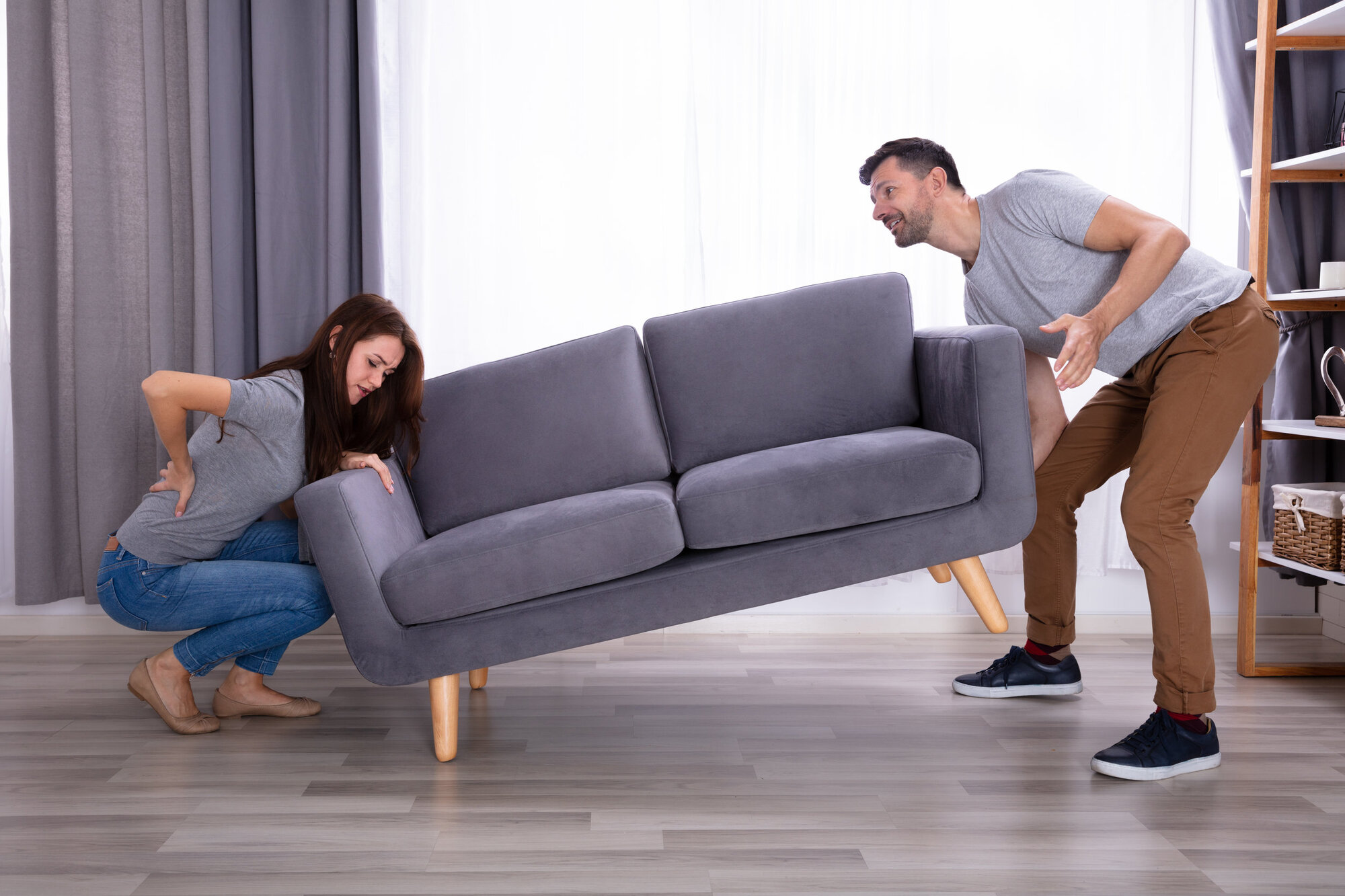
What are the Manual Handling Operations Regulations 1992?
The Manual Handling Operations Regulations 1992 (MHOR) are guidance designed for employers, managers and safety representatives. They explain how to avoid, assess and reduce the risk of injury from manual handling. The guidance was amended by the Health and Safety Regulations in 2002.
The MHOR set out clear guidelines on how to deal with risks associated with manual handling. These guidelines are organised into a ranking of measures for dealing with risks.
1. Avoid hazardous manual handling operations when reasonably practicable.
2. Assess any hazardous manual handling operations that cannot be avoided.
3. Reduce the risk of injury as much as is reasonably practicable.
The Manual Handling Operations Regulations aim to reduce both the incidence and the prevalence of musculoskeletal disorders that arise from manual handling operations.
Under the MHOR, considerations must be given to the:
- Task.
- Individual.
- Load.
- Environment.
This is known as TILE.
The duties and responsibilities, in respect of employees, fall to the employer. In other words, the employer is responsible for the health and safety of their employees concerning manual handling. If an individual is self-employed, they are responsible for their own safety. The MHOR do not require employers to be responsible for other individuals associated with the workplace, for example volunteers.
The Manual Handling Operations Guide does not apply to any risks associated with manual handling operations where the load is hazardous. For example, if the load that is being manually handled contains a toxic substance, this would not fall under manual handling regulations.
The MHOR state that a worker may be at risk of a manual handling injury if:
- They are physically unsuited to carrying out the task or operation.
- They are wearing unsuitable clothing, footwear or other personal effects.
- They do not have adequate and appropriate training and knowledge relevant to the task.
The Manual Handling Operations Guide states an important difference regarding when equipment is considered as a load. A tool or machine that is being used for its normal purpose is not considered a load. However, if the tool or machine is being carried, lifted or handled in another way, such as being unloaded from a vehicle, then it is considered to be a load and manual handling regulations must be adhered to.
What is the purpose of the Manual Handling Operations Regulations 1992?
The Manual Handling Operations Regulations 1992 were designed to as far as possible remove or minimise the risks associated with manual handling operations. The MHOR set out duties to help ensure safety for a wide range of manual handling operations. They aim to prevent injury to workers undertaking manual handling tasks.
The MHOR explicitly state what employers are required to do to manage the health and safety of their employees during manual handling tasks.
By making manual handling regulations a legal duty, this ensures that all employers in the UK are legally required to reduce the risks associated with manual handling tasks and follow regulations and procedures at all times.
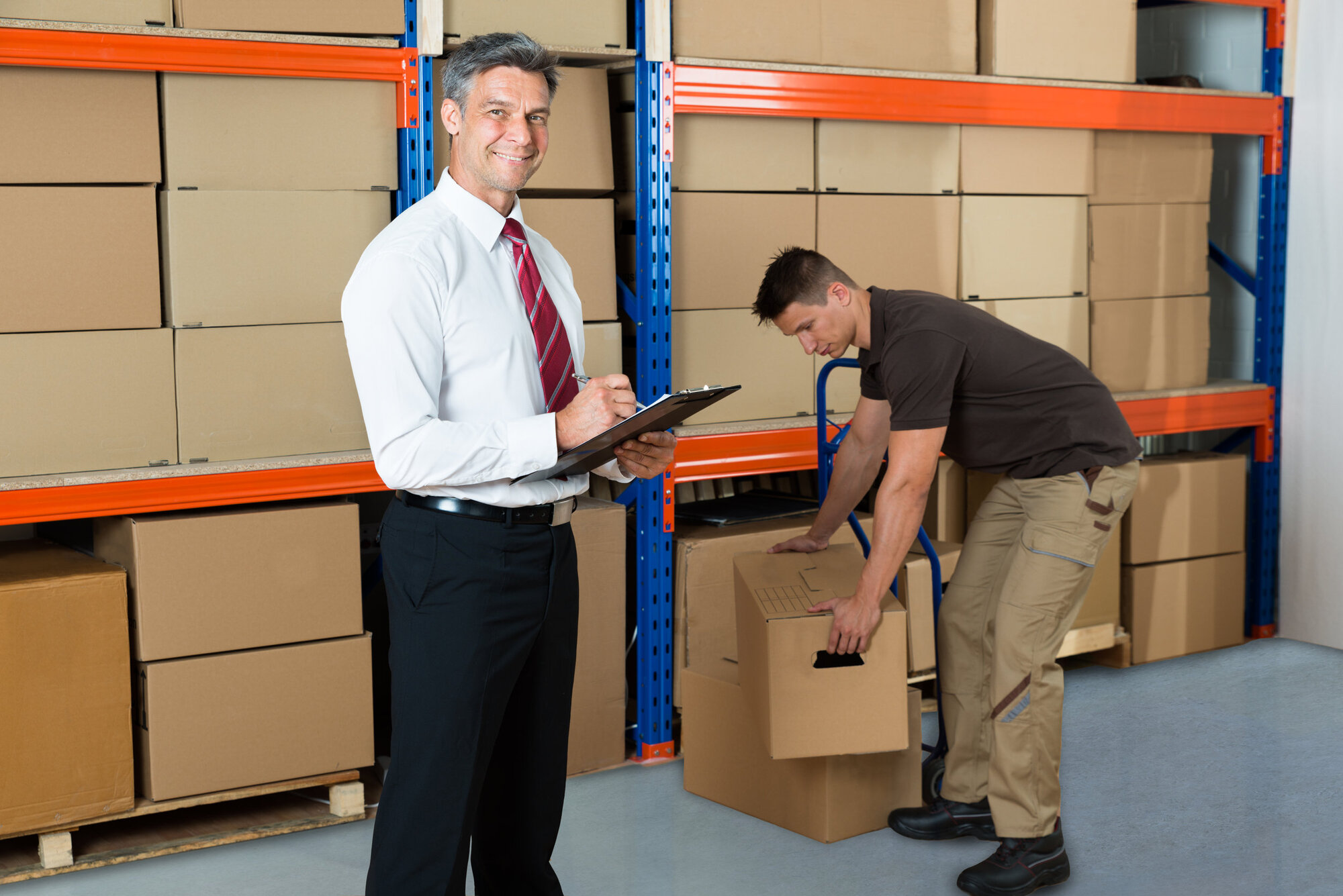
Other relevant legislation
As well as the Manual Handling Operations Regulations 1992, some other important pieces of legislation may be relevant to manual handling operations. Employers should ensure they are aware of and are complying with all relevant legislation to ensure the safety of their employees. Failure to follow regulations, or a serious breach in regulations, could result in a large fine or even a custodial sentence.
Legislation that may be relevant to manual handling activities includes:
- Health and Safety at Work etc Act 1974 – This includes guidance on complying with health and safety law. It is the primary legislation covering occupational health and safety in the UK. It includes the health and safety duties of employers, employees and self-employed individuals.
- The Management of Health and Safety at Work Regulations 1999 – This was introduced to reinforce the Health and Safety at Work etc. Act 1974. It includes explicit outlines of how employers should manage the health and safety of the workplace. It specifically focuses on the employer’s duty to conduct risk assessments.
- Provision and Use of Work Equipment Regulations 1998 – This is commonly known as PUWER. It focuses on the safe use of work equipment and provides regulations for employers, managers and other individuals who have a responsibility for the safe use of work equipment.
- Lifting Operations and Lifting Equipment Regulations 1998 – This is commonly known as LOLER and is built on the requirements of PUWER. It applies to lifting equipment.
What are the employees’ duties under the Manual Handling Regulations?
Under the manual handling regulations, employees also have health and safety duties that they must adhere to. This is to ensure the safety of themselves, and other people.
Some regulations employees should adhere to are:
- Follow all health and safety protocols and appropriate systems of work.
- Make proper use of health and safety equipment.
- Use all equipment safely and correctly and in accordance with any training, instruction and guidelines.
- Report any defects in equipment, systems or practices.
- Co-operate with their employer on all health and safety matters.
- Inform their employer if any manual handling operations are potentially risky or hazardous.
- Inform their employer of any shortcomings or flaws in any health and safety procedures or equipment.
- Inform their employer of any illness, injury or another factor that may increase their risk of injury or illness from manual handling tasks.
- Inform their employer if they believe the risk assessment is no longer valid or accurate.
- Ensure that none of their activities put other people at risk.
- Attend training if their employer or workplace requires them to.
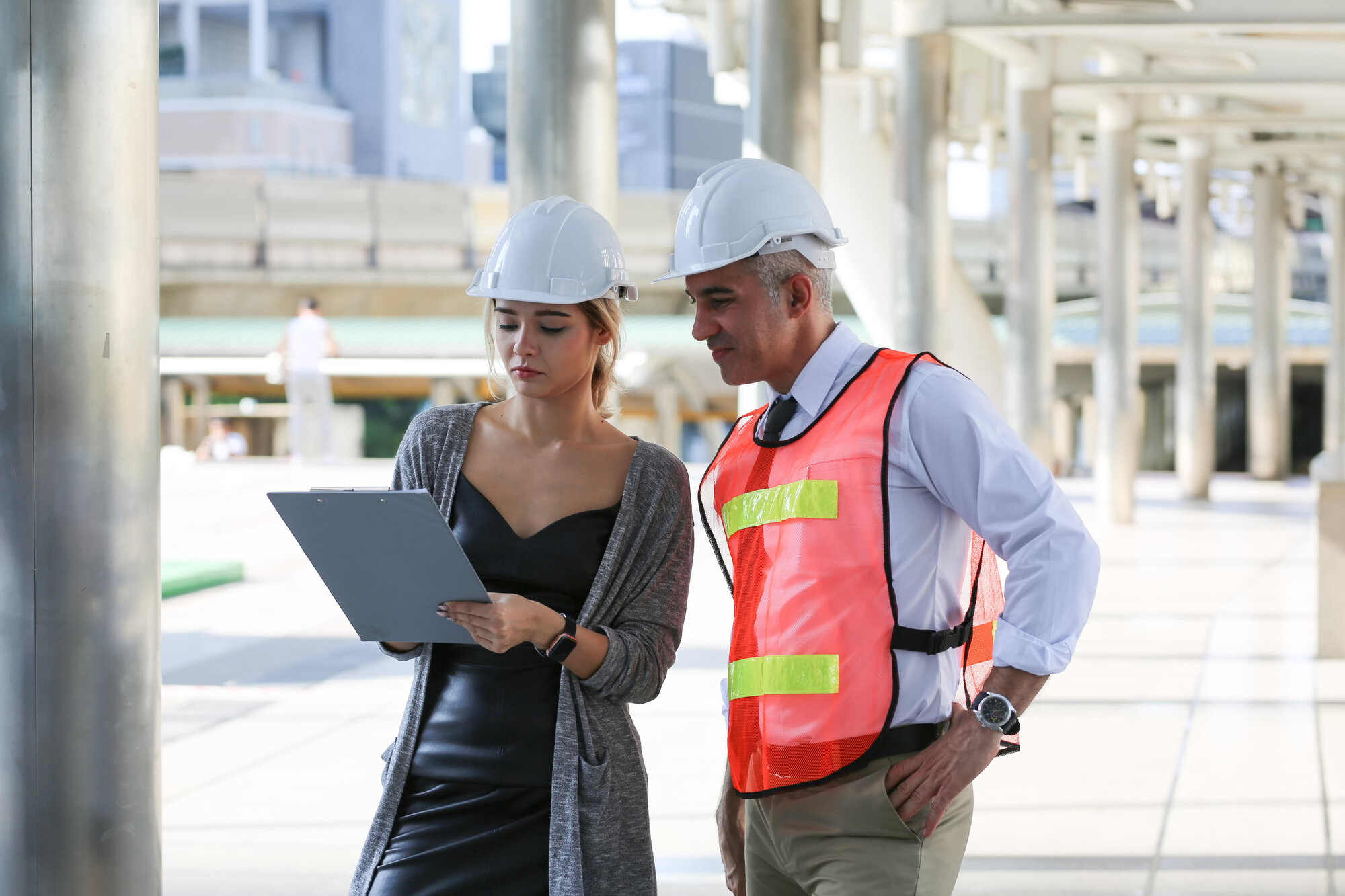
What are the employers’ duties under the Manual Handling Regulations?
Employers must protect their employees from the risk of injury or ill health that occurs as a result of hazardous manual handling tasks.
The Manual Handling Operations Regulations 1992 set out three duties of employers:
1. The employer should avoid the need for employees to undertake any manual handling operations at work which involve a risk of injury, where this is reasonably practicable.
2. If the above point is not possible, the employer should make a suitable and sufficient assessment of the operation which cannot be avoided.
3. The employer should take appropriate steps to reduce the risk of injury during such operations, to the lowest level that is reasonably practicable.
When the employer is considering if a manual handling operation has a risk of injury, the employer must determine appropriate risk reduction measures. When doing this, the employer must consider the employee’s clothing, footwear and personal effects to ensure they are suitable. They should also take into consideration the knowledge and training that the employee has and whether the person was determined to be at risk when a Management of Health and Safety Regulations (1999) risk assessment was completed.
If some workers are deemed to be more at risk than others, it is important that the employer takes their individual requirements into account.
Workers who may be deemed higher risk include:
- Expectant or new mothers.
- Those with disabilities that may affect their ability to do a task.
- Older workers.
- Those returning to work with a previous manual handling injury or musculoskeletal disorder.
- Individuals with a limited understanding of English.
- New, inexperienced or temporary workers.
Conducting risk assessments is an essential part of the employer’s duties. Depending on the type of operation or activity the employee is engaging in, a generic or specific risk assessment may be required.
Operations that have a greater risk of injury will require a more detailed assessment. It is important to ensure that the risk assessment is suitable and sufficient. Any risk reduction methods that are identified should be implemented as soon as possible.
When conducting the risk assessment, employers should consider the risks that arise from:
- The task or activity.
- The load.
- The working environment.
- The capacity of the individual.
- Any equipment or handling aids that are employed.
- The duration and frequency of the task.
Employers will have to use their own judgement when deciding the presence and degree of risk. Employers must also determine the appropriate measures and actions that should be put into place to reduce the level of risk involved.
Employers who have five or more employees are legally required to record the findings of the risk assessments.
General risk assessments for manual handling tasks will need to be updated at a regular, pre-determined time, such as annually. They will also need to be updated if an accident or injury occurs or if additional hazards are identified.