In this article
LOLER stands for the Lifting Operations and Lifting Equipment Regulations 1998. It is a set of UK health and safety regulations designed to ensure the safe use of lifting equipment in workplaces. These regulations are essential for protecting employees, contractors, and the public from the risks associated with lifting operations.
LOLER applies across various industries, from construction and manufacturing to healthcare and logistics, wherever lifting equipment is used. By focusing on proper inspection, maintenance, and safe operating practices, LOLER helps minimise accidents and injuries.
It was introduced to improve safety standards for lifting equipment and operations in the workplace. It was implemented in response to accidents and fatalities caused by poor maintenance, inadequate inspection, and unsafe use of lifting equipment.
Before LOLER, there were frequent accidents involving lifting equipment due to poor maintenance and lack of proper procedures. Existing laws, such as the Health and Safety at Work Act 1974 covered general workplace safety but lacked specific rules on lifting operations. LOLER ensured all lifting operations were properly planned, supervised, and carried out safely. It aligned with European health and safety laws, particularly the EU Work Equipment Directive.
LOLER was part of a broader effort to reduce injuries and fatalities related to lifting operations, ensuring equipment was fit for purpose and used correctly. It remains a key regulation in industries such as construction, manufacturing, and warehousing.
LOLER regulations explained
The Lifting Operations and Lifting Equipment Regulations (LOLER) 1998 is a critical piece of legislation designed to ensure the safe use of lifting equipment in the workplace. Enforced under the Health and Safety at Work Act 1974, LOLER places responsibilities on employers, self-employed individuals, and those in control of lifting equipment to ensure that operations are planned, supervised, and executed safely.
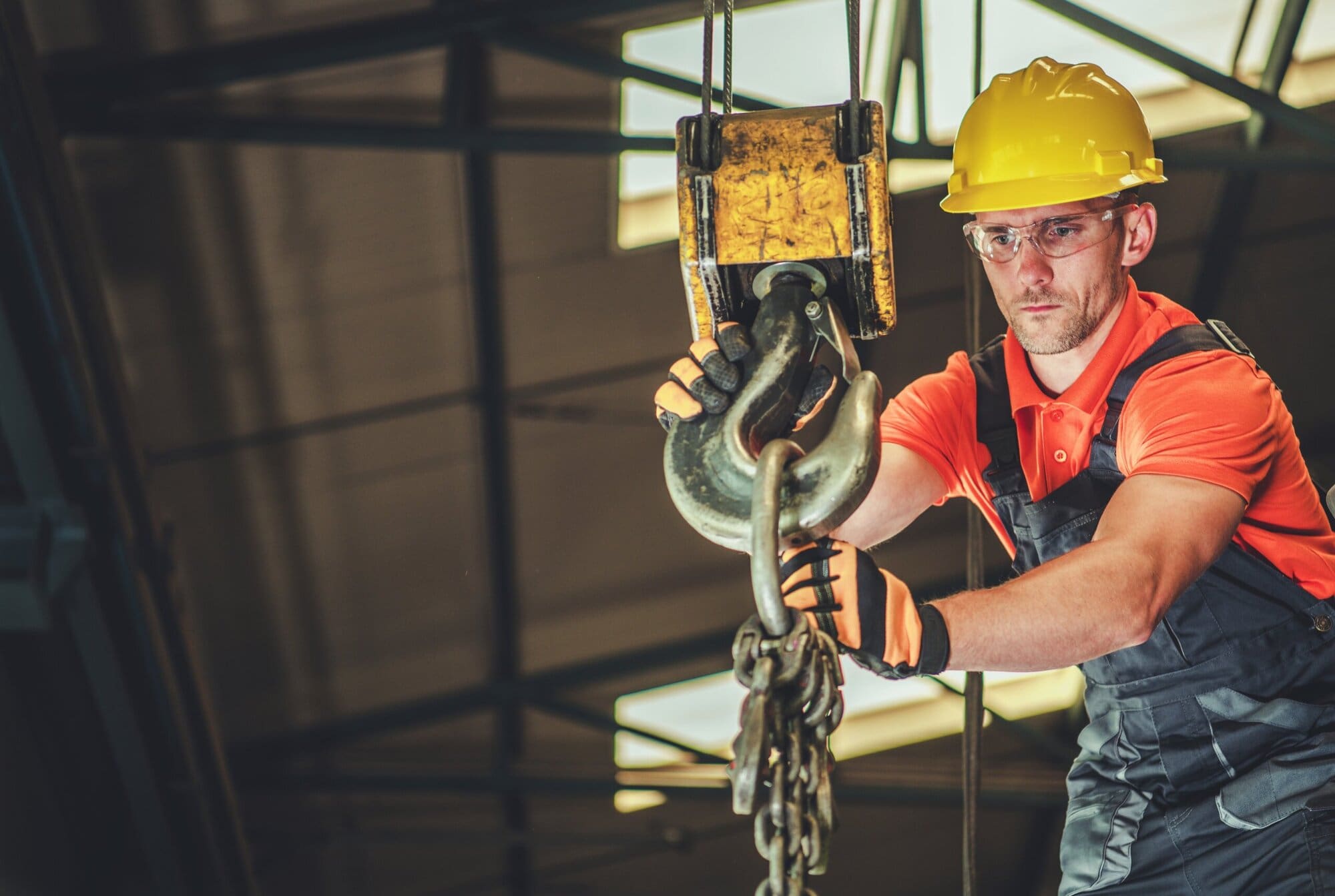
Key elements of LOLER include:
- Ensuring equipment suitability – lifting equipment must be appropriate for the task and safe for use.
- Competent personnel – operations involving lifting must be conducted by trained and competent individuals. Inadequately trained employees create dangerous work environments.
- Regular inspections – equipment must be examined by a qualified person at specified intervals. Regular inspections help identify hazards before they cause harm, reducing workplace injuries and fatalities.
- Clear markings – lifting equipment must display safe working loads (SWL) and any other necessary information.
- Minimising risk – lifting activities must be planned to prevent accidents, including load falling or equipment failure.
LOLER regulations are designed to reduce the risks associated with lifting operations and ensure that equipment is used correctly, safely, and maintained properly. LOLER aims to prevent workplace accidents and injuries related to lifting operations. Lifting equipment, such as cranes, hoists, lifts, forklifts, and even slings and chains, poses significant risks if not used properly. LOLER ensures that:
- The equipment is strong and stable enough for the intended use.
- Lifting operations are properly planned and supervised.
- Loads are safely secured to prevent falls or swinging.
By enforcing these measures, LOLER reduces the likelihood of serious incidents, including fatalities.
LOLER places legal obligations on employers, self-employed individuals, and those in control of lifting equipment. Compliance with these regulations is mandatory under UK law, and failure to adhere can lead to:
- Legal action and fines from the Health and Safety Executive (HSE).
- Increased liability in the event of an accident.
- Criminal prosecution if negligence leads to injury or death.
Employers have a duty of care to protect their workers, and LOLER provides clear guidelines to ensure safety is a priority.
Lifting equipment undergoes significant wear and tear due to constant use, making regular inspections and maintenance essential. LOLER mandates that:
- Equipment must be inspected by a competent person at regular intervals, typically every six or twelve months, depending on the equipment and its use.
- Any identified defects must be reported immediately and addressed before further use.
- Employers must maintain records of all inspections and maintenance work.
These requirements help identify potential hazards before they lead to equipment failure, accidents, or costly downtime.
LOLER requires that all lifting operations are:
- Properly planned by a competent person.
- Adequately supervised to ensure safe execution.
- Carried out safely to minimise risks.
Proper planning and organisation reduce workplace disruptions, increase efficiency, and ensure that lifting activities are performed without unnecessary risks.
LOLER not only safeguards employees who operate or work around lifting equipment but also protects the public and anyone who may be nearby. Poorly managed lifting operations can result in dropped loads, collapsing cranes, or runaway forklifts, endangering bystanders. By enforcing strict regulations, LOLER minimises these risks.
Non-compliance with LOLER can lead to severe financial and reputational consequences for businesses, including:
- Compensation claims from injured workers.
- Increased insurance premiums.
- Loss of business reputation due to unsafe practices.
LOLER works in conjunction with other health and safety regulations, such as:
- The Health and Safety at Work etc. Act 1974 – is the primary legislation governing workplace health and safety in the UK. It places a duty on employers to ensure, as far as is reasonably practicable, the health, safety, and welfare of their employees and others affected by their work activities. The key provisions include, providing a safe working environment, adequate training, risk assessments, and appropriate safety measures, placing a duty on employees to take reasonable care of their own and others’ safety and comply with workplace safety policies. Employers must identify and mitigate workplace hazards and ensure access to facilities such as toilets, drinking water, and first aid. The Health and Safety Executive enforces the Act through inspections, investigations, and prosecutions. The Act applies to all workplaces, including offices, factories, construction sites, and public spaces. Non-compliance can lead to legal action, fines, or imprisonment.
- PUWER – this is a UK regulation designed to ensure that work equipment is safe to use and properly maintained. It applies to employers, the self-employed, and those responsible for work equipment. The key requirements of PUWER 1998 include ensuring that equipment must be appropriate for the task and used in suitable conditions, regular inspections and servicing to keep equipment safe, ensures that workers must be adequately trained to use equipment safely, safety measures for equipment including having clear safety signs and warnings and sets out that equipment should be used in a safe environment to minimise risks. PUWER applies to all workplaces where equipment is used, including factories, construction sites, offices, and farms. It complements other health and safety laws, such as the Health and Safety at Work Act 1974, ensuring that work equipment does not pose risks to users or others. The legislation covers all work equipment, including lifting devices.
- The Management of Health and Safety at Work Regulations 1999 – is a key piece of UK legislation that builds on the Health and Safety at Work etc. Act 1974, requires employers to proactively manage health and safety risks in the workplace. The key requirements are that employers must assess workplace risks to employees and others who may be affected, employers must implement measures to eliminate or reduce risks, suitable management systems must be in place, employers must appoint competent individuals to assist in health and safety management, employees must receive adequate health and safety training, employers and self-employed individuals must work together where necessary, there should be additional protections for young workers, new or expectant mothers, and temporary workers. The regulations are designed to create a structured approach to workplace health and safety, ensuring hazards are managed effectively.
By complying with LOLER, businesses also align with these broader health and safety obligations.
LOLER is a vital regulation that ensures lifting operations are conducted safely and efficiently. It protects workers, prevents equipment failures, reduces accidents, and ensures legal compliance. Adhering to LOLER not only safeguards lives but also prevents financial and reputational risks for businesses. Employers must take their responsibilities seriously, implementing proper training, maintenance, and supervision to create a safe working environment.
Failure to comply with LOLER can lead to serious legal and financial consequences, as well as risks to employee safety.
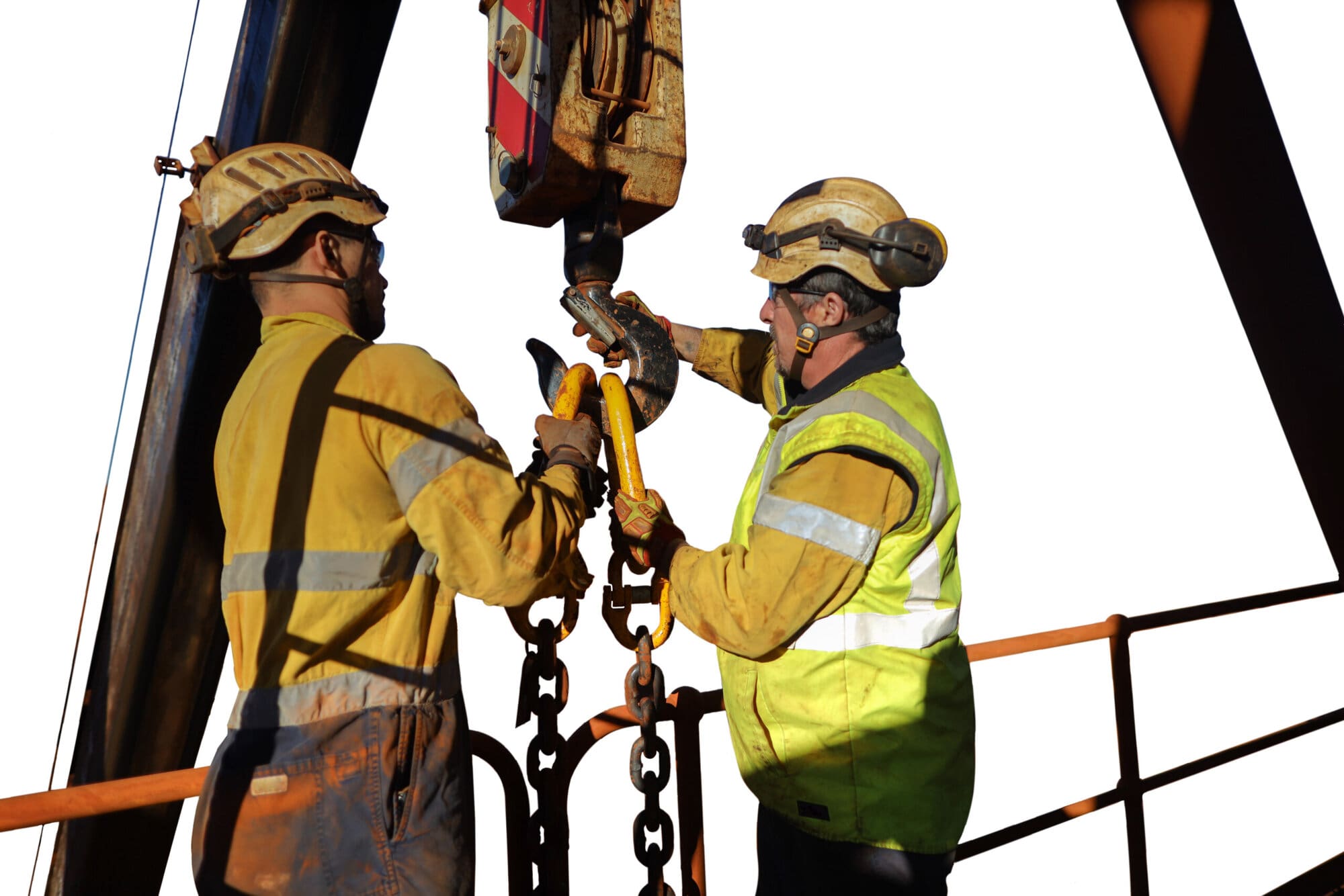
What equipment is LOLER relevant to?
LOLER applies to a wide range of lifting equipment used in workplaces. The regulations cover any equipment used for lifting or lowering loads, including attachments used for anchoring, fixing, or supporting the equipment. LOLER is relevant to:
Cranes and Hoists
- Mobile Cranes – Used in construction, industrial, and logistics sectors.
- Tower Cranes – Commonly used on construction sites for lifting heavy materials.
- Overhead Cranes – Installed in factories and warehouses for lifting and moving loads.
- Vehicle-Mounted Cranes – Found on lorries and other transport vehicles for loading/unloading.
- Gantry Cranes & Jib Cranes – Typically used in workshops and shipyards.
- Hoists & Winches – Including electric, manual, and hydraulic hoists for vertical lifting.
Forklifts and Telehandlers
- Forklift Trucks – Any forklift equipped with lifting attachments is covered.
- Tele handlers – Versatile machines used in construction and agriculture with lifting capabilities.
Passenger and Goods Lifts
- Passenger Lifts – If used for work purposes, for example, site lifts, and lifts in warehouses.
- Goods Lifts & Dumbwaiters – Used in catering, hotels, warehouses, and industrial settings.
- Construction Hoists – Used for lifting workers and materials on construction sites.
Access Equipment
- Mobile Elevated Work Platforms (MEWPs) – Includes cherry pickers, scissor lifts, and boom lifts.
- Suspended Access Equipment – Such as window cleaning cradles.
Lifting Accessories
- Chains, Ropes, and Slings – Including wire rope slings, webbing slings, and round slings.
- Shackles and Eyebolts – Used to secure loads to lifting equipment.
- Lifting Beams and Frames – Spreader beams and modular lifting frames.
- Magnets and Vacuum Lifters – Used for lifting sheets of metal, glass, or other materials.
Vehicle Lifting Equipment
- Vehicle Inspection Lifts – Used in garages and MOT testing centres.
- Trolley Jacks and Axle Stands – If used for lifting vehicles as part of work operations.
Agricultural and Forestry Equipment
- Tractor-Mounted Loaders – Including front-end loaders and bale handlers.
- Log Lifting Equipment – Such as grapple loaders and timber cranes.
Offshore and Marine Lifting Equipment
- Davit Cranes – Used for lifeboats and offshore lifting operations.
- Lifting Equipment on Ships and Oil Rigs – Includes deck cranes and lifting gear.
Theatre and Entertainment Industry Equipment
- Stage Lifts & Rigging Equipment – Used for lighting, sound, and stage scenery.
Other Workplace Lifting Equipment
- Patient Hoists – Used in healthcare for lifting and transferring patients.
- Workshop Lifts – Small cranes and lifting tables used in engineering workshops.
Exclusions from LOLER
- Escalators
- Equipment used exclusively for leisure or domestic purposes.
- Manually operated sack trucks and wheelbarrows.
- Standard passenger lifts used solely for non-work purposes.
Equipment provided for use by employees, even if hired or leased, must comply with LOLER regulations. In certain cases, equipment used for lifting people, such as passenger lifts, must meet stricter safety standards. If lifting equipment is used to handle hazardous materials, for example, barrels of chemicals or gas cylinders, both COSHH and LOLER may apply.
LOLER lifting regulations
LOLER specifies several essential requirements for lifting operations:
- Planning and supervision – every lifting operation must be planned by a competent person, ensuring all risks are assessed. Supervision must also be in place, especially for complex or high-risk tasks.
- Safe working loads (SWL) – all lifting equipment must clearly display its maximum load capacity. Overloading is strictly prohibited.
- Load stability – loads must be securely attached to prevent slipping or falling. The centre of gravity should be balanced.
- Routine maintenance – equipment must be maintained and repaired to prevent wear and tear from compromising safety.
Adhering to these principles not only ensures compliance but also minimises workplace accidents and equipment damage.
Carrying out LOLER inspections
Regular inspections, referred to as thorough examinations under LOLER, are a legal requirement to verify the safety and functionality of lifting equipment. These examinations should be carried out:
- Before first use – for new equipment or after installation.
- Regular intervals – typically every 6 months for equipment lifting people and every 12 months for other equipment. These intervals may vary based on risk assessments or manufacturer recommendations.
- Following exceptional circumstances – if an incident, damage, or environmental condition has impacted the equipment’s integrity.
- Inspections must be conducted by a competent person, often an independent examiner, to ensure an unbiased and thorough review. Records of these inspections must be maintained for future reference and compliance checks.
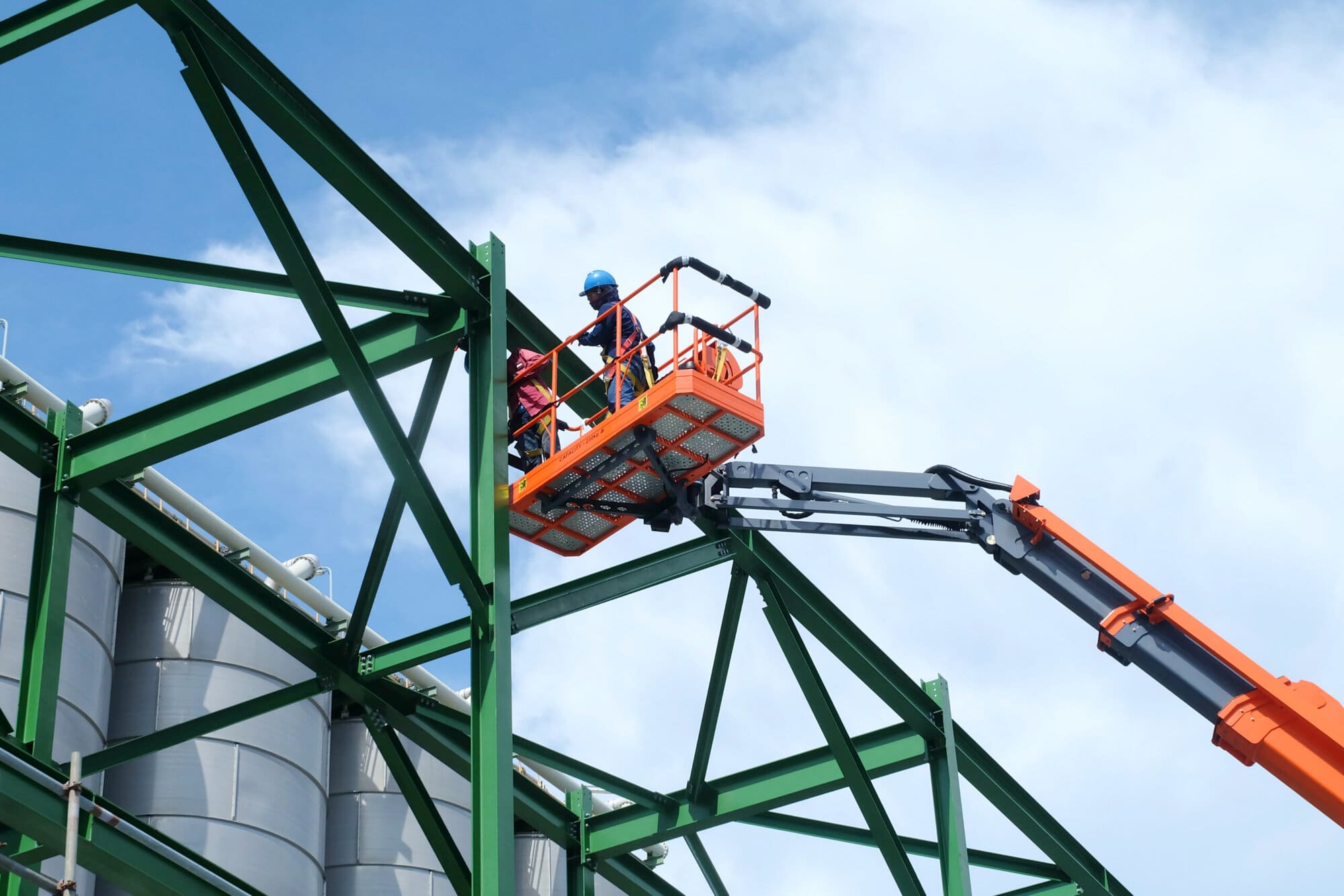
LOLER certificate
A LOLER certificate is a document provided following a thorough examination of lifting equipment. It indicates that the equipment complies with LOLER standards and is safe for use. While not explicitly named in the legislation, certificates are commonly issued by inspection bodies or competent persons as proof of compliance.
Key details on a LOLER certificate include:
- Description of the equipment.
- Date of the examination.
- Results of the inspection.
- Recommended date for the next examination.
- Name and qualifications of the examiner.
Employers must retain these certificates and make them available for inspections or audits.
LOLER inspection checklists
A well-structured inspection checklist is essential for ensuring compliance with LOLER. A typical checklist may include:
- Equipment identification – including serial number or unique identifier and manufacturer details.
- Visual inspection – this should check for signs of wear, corrosion, or damage and should include an inspection of load-bearing components and lifting accessories.
- Functionality tests – this should ensure mechanical components operate smoothly including testing emergency systems and brakes.
- Markings and documentation – this should verify safe working load labels and confirm that operating manuals and maintenance records are up-to-date.
- Operational checks – this should confirm load stability during lifts and assess whether controls respond correctly.
By maintaining and following an inspection checklist, businesses can ensure that lifting equipment remains compliant, reliable, and safe for use.
By adhering to LOLER regulations and implementing best practices for inspections and operations, organisations can not only meet their legal obligations but also foster a safer working environment for all employees.