In this article
What is manual handling?
Manual handling refers to moving, transporting or supporting a load either by hand or by using bodily force. A load may be an object, a person or an animal. Manual handling involves movements such as lifting, carrying, pushing, pulling or transporting a load from point A to point B.
Manual handling is required to some extent across a range of industries and job roles, as well as within the home. Examples of manual handling include turning a bedridden patient in a care home, stacking pallets in a warehouse, pushing cages of laundry in a hospital and operating heavy machinery on a farm.
More than one third of all workplace injuries are related to manual handling. Some manual handling injuries can affect people for the rest of their lives. When performing manual handling tasks, it is important to work safely and carefully to avoid hurting or injuring yourself.
Safely lifting
Steps for safely lifting loads include:
- Plan the lift, including where the load is going from and to and what route you will take
- Keep the load close to your waist with the heaviest side of the load closest to your body
- Maintain a good posture and a stable position
- Make sure that you have a good grip of the load
- Slightly bend your back, knees and hips at the start of the lift
- Keep your head up and look straight ahead not down whilst carrying/ lifting
- Use smooth movements rather than jerking
Additional tips for safe lifting include:
- Turning by moving your feet is better than trying to twist and lift at the same time
- Try to keep shoulders level
- Practice good housekeeping and ensure walkways are clear, tidy and free of debris that could cause a tripping hazard
- Consider using mechanical aids (such as a trolley or hoist) or other handling aids to help you
- Always ask for help when needed, a shared load is easier to manage
- Take breaks when needed and avoid over-exerting yourself
- Offer to pair up with another worker to share the load and practice good teamwork, especially if they look like they are struggling
To perform safe lifting, the following should be avoided:
- Don’t make jerking movements or snatch the load as this increases the chance of injury or dropping the load
- Never try to lift more than you can safely and easily manage
- Don’t twist your back or lean sideways during manual handling
- Avoid stooping or squatting
- Don’t bend from the waist – the power is in your legs
There are no legal weight limits for manual handling, although the HSE provides guidelines based on assumptions about the lifting capacity for men and women which suggests:
- The maximum weight limit for men is 25 kg (55 lbs)
- The maximum weight limit for women is 16 kg (35 lbs)
These weight limits refer to loads held close to the body at around waist height. There are different weight limits for handling at shoulder, elbow or lower leg height.
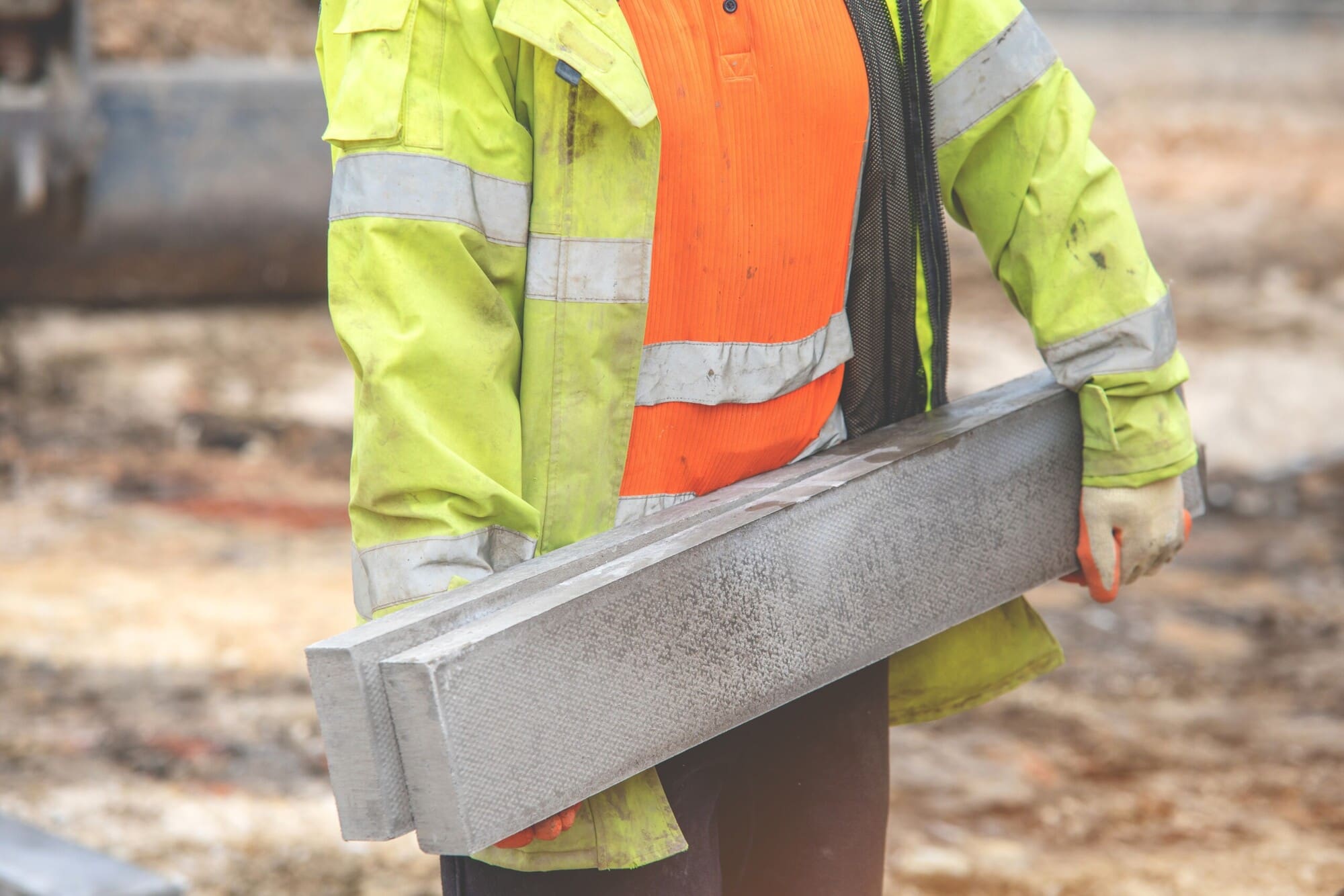
Safely pulling
In pulling and pushing operations, loads may be slid, rolled or moved on wheels. Examples include pushing large cages of laundry in a hotel or rolling cask beer into a pub cellar. If manual handling aids are being used to push or pull loads it is essential that they are in good working order, fit for purpose and only used by people who are trained to do so.
If you are an employer, you should investigate manual handling operations to determine their level of risk. When thinking about the safety of pushing and pulling operations, first observe the posture of the workers. Good postures include standing up straight with a straight back, looking forward.
Push/pull work is likely to pose a low risk to workers if:
- The majority of the force required will applied by the hands
- The torso is straight and not twisted
- The hands are between hip and shoulder height
- The distance that the load will be continually moved is no more than 20 metres
You can use the Risk Assessment for Pushing and Pulling (RAPP) tool, created by the HSE, to risk assess pushing and pulling operations. The tool can be used to identify high-risk pushing/ pulling practices within the workplace and to assess how effective control measures are.
The two different types of pushing/ pulling practices that can be assessed using the tool:
- Moving loads using wheeled equipment (such as trolleys, carts, cages or wheelbarrows)
- Moving loads without using wheels (for example rolling, dragging or sliding)
High risk pushing/ pulling operations may require a significant force (for example using a leaning posture). They may also incur extra risk factors such as constricted spaces, uneven floors, low light or sloping surfaces.
Potential risks from incorrect manual handling
Poor manual handling techniques can lead to accidents, injuries and instances of workplace ill-health. The effects of incorrect manual handling can be both short and long term.
Risks from incorrect manual handling include injuries to muscles, bones, joints and connective tissues that result in pain and swelling. Some of the most common health issues associated with poor manual handling techniques are:
- Musculoskeletal disorders (MSDs)
- Sprains, strains and pulled muscles
- Broken bones
- Crushed hands and feet
Musculoskeletal disorders (MSDs) are long term conditions that affect the muscles, bones, joints, nerves, tendons and ligaments. They are one of the most common physical ill health consequences of poor manual handling. MSDs accounted for almost one third (32%) of instances of work-related ill health in 2023/24, leading to 7.8 million working days being lost in the same year.
Additional health problems that may occur as a result of incorrect manual handling include:
- Back, neck and shoulder strains
- Tendinitis
- Carpal tunnel syndrome
- Slips, trips and falls
- Torn cartilage
Poor manual handling can also result in loads being dropped or damaged which leads to lost revenue and has an impact on productivity and the quality of service provided.
Posture for manual handling
Having a poor posture during manual handling can put additional stress on the body (especially the back). Good manual handling techniques require a solid posture with feet hip width apart and a neutral spine:
- Keep feet apart to maintain good balance
- Bend with the knees rather than the back
- Activate muscles to maintain a strong core
- Lift using your leg muscles
- Keep a neutral spine
- Avoid twisting your spine during lifting/ lowering
- Ensure that you have a good grip on the load
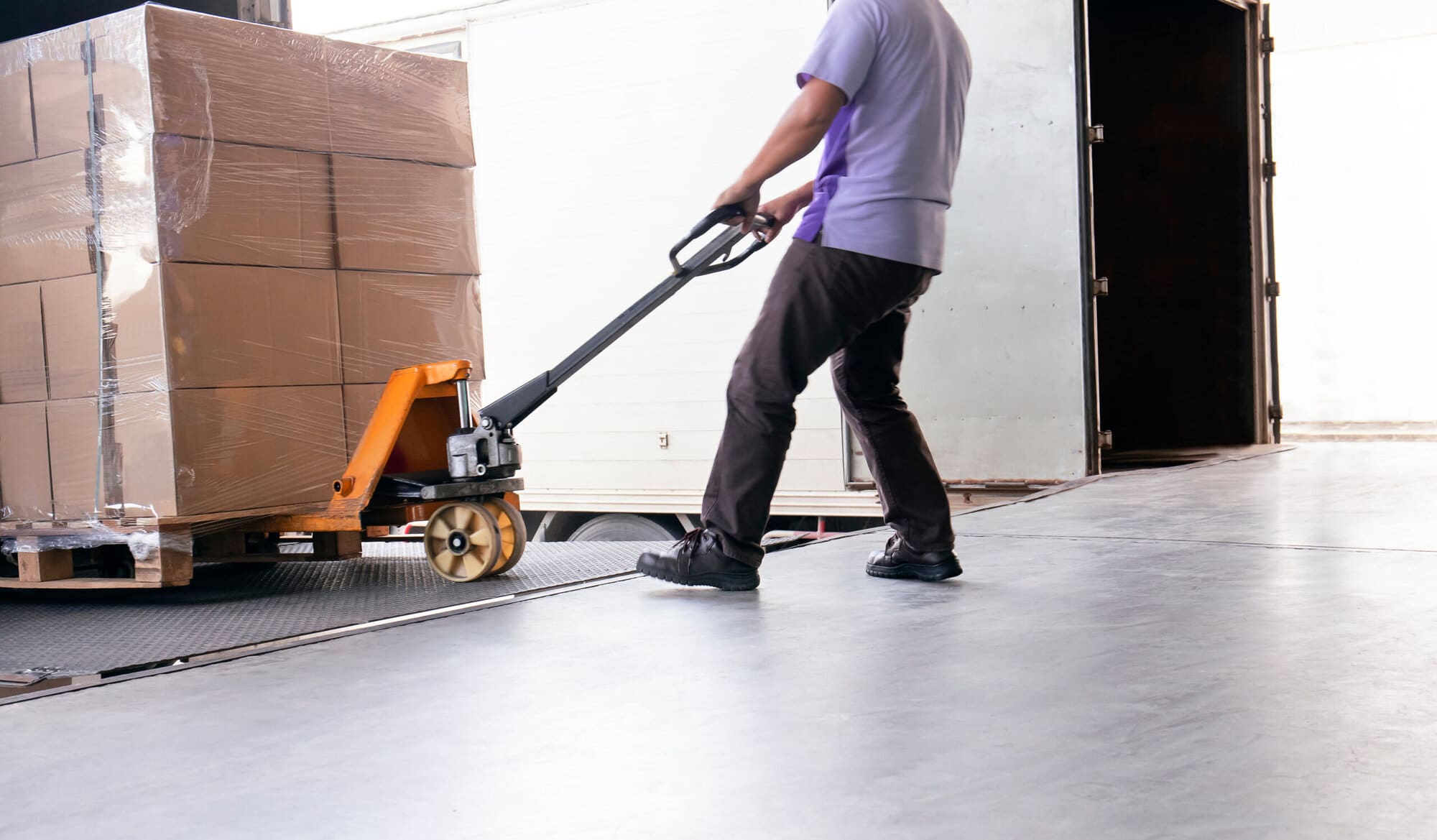
Following the above tips to keep a good posture whilst manual handling will protect your body and reduce the chances of an accident or injury occurring.
In addition to keeping a good posture, to minimise the chances of a slip, trip or fall during manual handling activities, try to wear low heeled footwear that is in good condition and has a good grip on the sole.
Risk assessments for manual handling
A risk assessment is a structured process that is used to identify hazards, assess risks and put controls in place to minimise the chance of harm.
Employers are required to take steps to protect their workers from harm as far as is reasonably practicable.
The Health and Safety at Work Regulations 1999 set out the minimum requirements for employers which include:
- Identifying hazards that could cause injury or illness to people within the workplace
- Assessing the likelihood that someone will be harmed and how seriously (the risks)
- Deciding what action needs to be taken to remove the hazards or, when this is not possible, to reduce the risks (the controls)
A risk assessment should only be done by a competent person; this could be a manager, supervisor or other competent person in the workplace. You can also appoint a health and safety professional to help you complete your risk assessments.
The basic steps of a risk assessment are:
- Identify the hazards
- Assess the risks
- Control the risks
- Record your findings
- Monitor and review
Risks from manual handling may arise from physical factors such as:
- The task at hand
- The load
- The working environment
- An individual’s capacity
- How work is organised and/or allocated
- How repetitive manual handling tasks are
- The pace, frequency and duration of work
- Availability of handling equipment or handling aids
In addition the physical aspects of the work and working environment, psychosocial factors can also influence the likelihood of a person being injured during manual handling. This includes factors such as how stressed or tired workers feel, how tight deadlines are and to what extent they have control over their work and working methods.
To improve workplace wellbeing, it is important for employers to consider both physical and psychological factors when assessing risks and deciding what controls need to be put into place.
Employers can use the MAC tool to identify high risk workplace manual handling activities. The MAC tool can help you to understand, identify and categorise levels of risk using a numerical and colour coded system.
Where possible, employers should try to involve the workforce in any risk assessments as they are at the forefront of operations and are ideally placed to spot unsafe working practices, notice risks and put forward ideas for practical solutions to control them.
Controls may include:
- Redesigning the task to minimise or remove the need for manual handling to take place
- Investing in new technology or automated solutions
- Making better use of mechanical or handling aids such as conveyors, hoists or trolleys
- Making loads easier to manage, for example, lighter or less bulky
- Ensuring flooring is even, dry and stable
- Providing comprehensive training in manual handling for all workers
Additional risks assessments may be needed for vulnerable workers for example new and expectant mothers, very young or elderly workers, temporary workers, migrant workers or people with disabilities/ health conditions.
Manual handling legislation
It is important to understand what the law says about manual handling at work in order to be compliant and uphold best practice.
The Health and Safety at Work Act 1974 and The Health and Safety at Work Regulations 1999 are key pieces of legislation that cover occupational health and safety. They outline employer responsibilities to assess risks and protect workers. In addition, employers must comply with Manual Handling Operations Regulations 1992 (as amended by the Health and Safety Miscellaneous Amendments Regulations 2002). These regulations set out the steps needed to avoid, assess and reduce the risks from manual handling.
Workers also have a duty of care, which includes:
- Following safe systems of work that are in place to protect health and safety
- Use any equipment provided for their health and safety properly
- Work in a cooperative way
- Inform their employer of any changes or any unsafe working practices/ handling activities that they see
- Take care to make sure their work activities do not put others at risk
Training for manual handling
Manual handling training is crucial in any workplace where manual handling operations are required. When employees receive instruction and education in proper manual handling techniques and the risks associated with these activities, they are less likely to take risks and more likely to work safely and competently.
The benefits of manual handling training include fewer workplace injuries, increased workforce wellbeing, improved productivity and fewer days missed due to occupational ill-health.
Manual handling training at work should cover:
- Examples of manual handling activities
- Safe lifting
- Safe pushing and pulling
- How to safely use lifting aids
- Risks of poor manual handling
- Reporting of issues or injuries
- Legislation and legal requirements
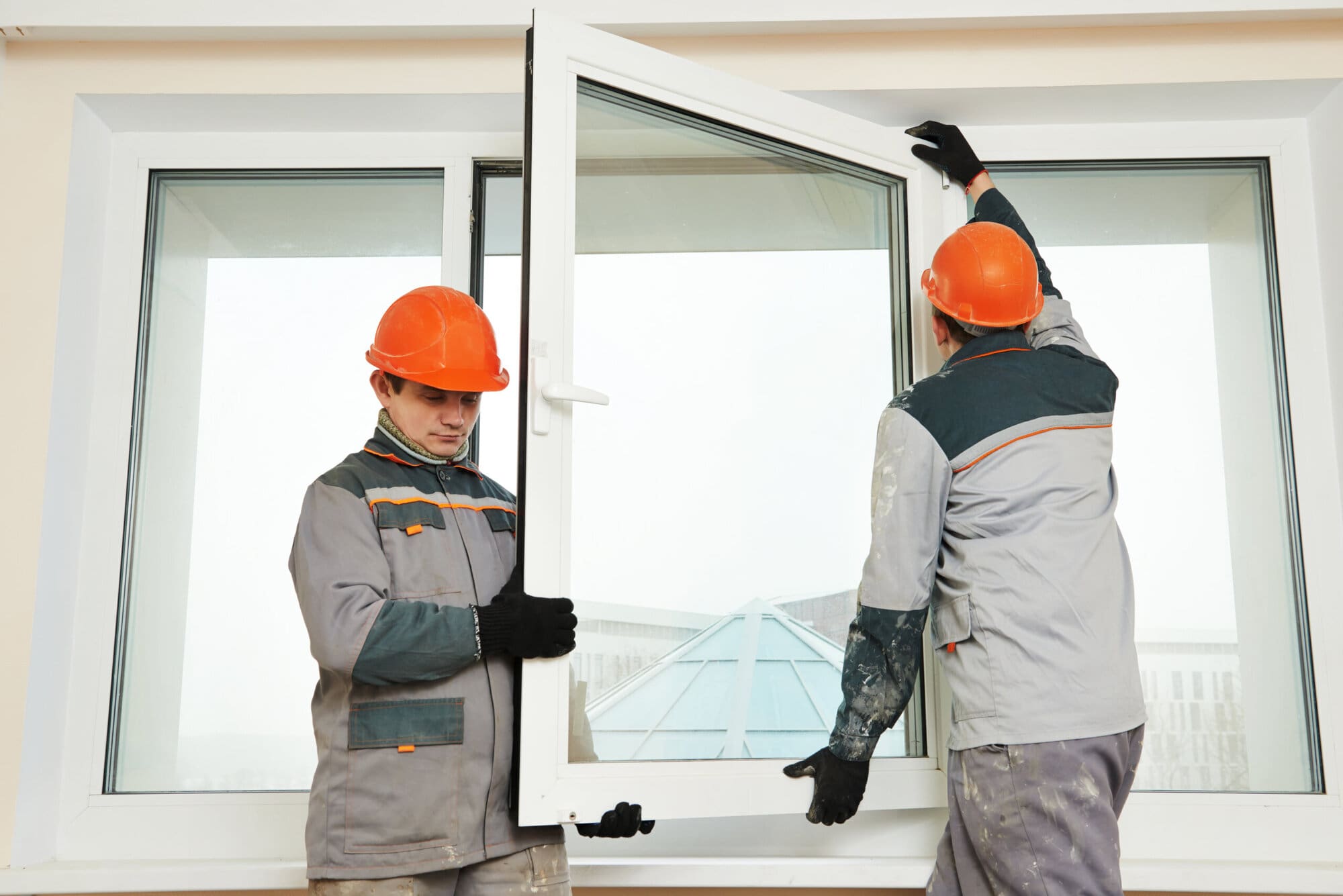
Training should be relevant to the type of work and tasks that employees routinely carry out. Effective training should include a mixture of instruction and practical, hands on examples.
Training in safe manual handling alone is not sufficient to control risks and should only be used in conjunction with other controls, including eliminating the need for manual handling if possible, making use of technology or methods for automation and reducing or rotating tasks to avoid repetition.