In this article
The Control of Substances Hazardous to Health (COSHH) Regulations represent the cornerstone of the UK’s efforts to protect workers and the public from the risks associated with hazardous substances in the workplace. Introduced as a regulatory framework, COSHH mandates employers to take systematic steps to assess, manage and reduce potential exposures to harmful chemicals, dusts, fumes, biological agents, and other hazardous materials. Ensuring COSHH compliance is not only essential for safeguarding health and safety, it is also a legal requirement that, if neglected, can lead to serious legal consequences, including fines, penalties, and even criminal liability for employers.
This article delves into the legal landscape surrounding COSHH, exploring both the regulatory responsibilities placed on employers and the potential ramifications of failing to meet these obligations. By examining the legal requirements and standards that underpin COSHH, as well as the penalties for non-compliance, this analysis aims to highlight the critical importance of adherence to COSHH for legal accountability and workplace safety.
Overview of COSHH Regulations
The Control of Substances Hazardous to Health (COSHH) Regulations 2002, as amended, are a key part of the UK’s framework for workplace health and safety, designed to protect workers and others from the risks associated with exposure to hazardous substances. These regulations are essential for managing workplace safety in relation to chemical and biological agents and are grounded in the broader legislative context provided by the Health and Safety at Work Act 1974 (HSWA).
According to the HSE, 138 workers were killed in work-related accidents in 2023/2024 and 561,000 working people sustained an injury at work according to the Labour Force Survey.
The Health and Safety at Work Act 1974 forms the overarching framework for health and safety in the UK, establishing general duties for employers to protect the health, safety and welfare of their employees and others. COSHH falls within this framework as a more specific regulation aimed at managing risks from hazardous substances. Since its implementation, COSHH has been updated to address changing risks in various industries, technological advancements, and improved understanding of hazardous substances. Under COSHH, employers are legally required to assess and control risks from substances that are hazardous to health. It requires practical steps and management practices to ensure worker safety across multiple sectors, including manufacturing, healthcare, construction, laboratories and agriculture.
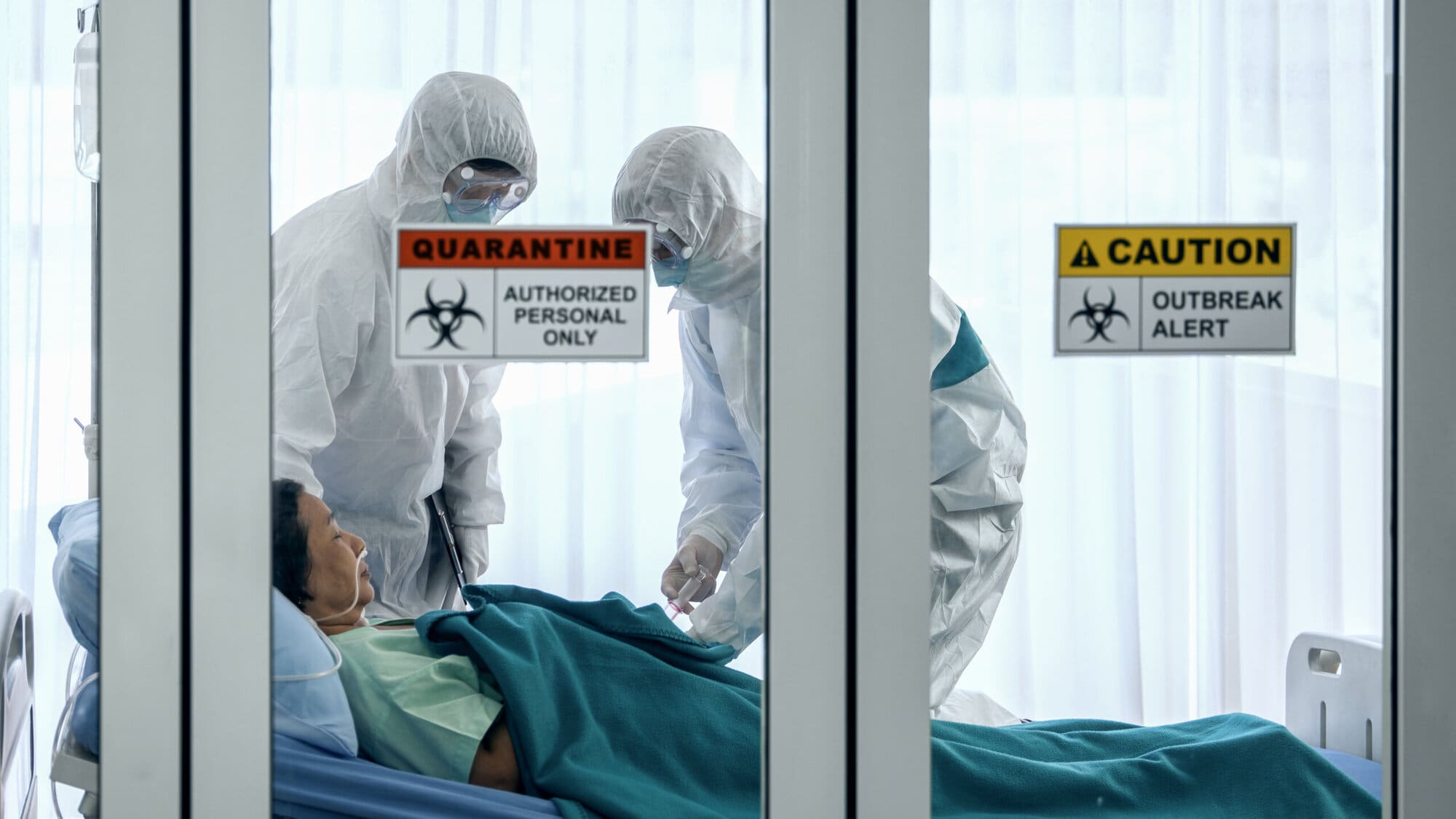
COSHH has three main objectives:
- Protection of workers and others – COSHH aims to safeguard employees and other individuals from the harmful effects of chemical and biological agents present in the workplace. This protection extends to anyone who may be affected by hazardous substances, including contractors, visitors and the general public.
- Control of exposure to hazardous substances – employers are required to identify, assess and control exposure to harmful substances. Control measures may include engineering controls like ventilation systems, administrative controls and personal protective equipment (PPE) to minimise risk.
- Prevention of harm from chemical and biological agents – COSHH is designed to prevent harm by promoting safe handling, storage and disposal of hazardous substances and ensuring that only those who are trained and equipped to handle such materials do so.
Under COSHH, employers have specific duties, including:
- Conducting COSHH risk assessments – employers must assess all hazardous substances used or generated during work activities to identify potential health risks. This involves understanding the nature of the substances, evaluating how workers might be exposed, and assessing the level of risk associated with this exposure.
- Implementing control measures – once risks are identified, employers must implement control measures to prevent or limit exposure. Control methods include ventilation systems to reduce airborne contaminants, and PPE such as gloves, masks and goggles.
- Providing employee training – employees must receive adequate training on COSHH-related procedures, including the safe use, storage and handling of hazardous substances. This training aims to help employees understand the risks, use control measures effectively, and know how to respond to potential exposure incidents.
- Ensuring ongoing health surveillance – for certain high-risk substances, employers must establish health surveillance programmes to monitor employees’ health and detect early signs of illness caused by hazardous substances. Health checks, biological monitoring and medical examinations may be required to track the effects of exposure on workers’ health over time.
- Monitoring and reviewing control measures – employers are responsible for regularly monitoring exposure levels and assessing the effectiveness of control measures. This may involve periodic air monitoring, reviewing work processes, and updating controls as necessary to ensure ongoing protection.
Employees also have responsibilities under COSHH Regulations, including:
- Following safe work procedures – employees are required to comply with safe work practices established under COSHH, such as proper handling of hazardous materials, correct usage of equipment, and adherence to operational protocols.
- Using PPE and other protective measures – employees must use personal protective equipment and other control measures provided by the employer as directed, ensuring their own safety and minimising the risk of exposure to hazardous substances.
- Reporting hazards or incidents – if employees identify potential hazards, incidents or failures in control measures, they must report these promptly to their employer or safety representative. This reporting is critical for ensuring swift responses to issues and for preventing further exposure.
COSHH applies broadly to any industry where hazardous substances are used or generated, covering diverse sectors such as:
- Manufacturing and engineering – managing exposure to chemicals like solvents, adhesives and cleaning agents.
- Healthcare – controlling risks from biological agents and chemical disinfectants used in clinical settings.
- Construction – reducing exposure to dust, cement and asbestos during building and demolition.
- Laboratories – handling potentially harmful chemicals, pathogens and radioactive substances.
- Agriculture – managing risks from pesticides, fertilisers and animal-based biological agents.
COSHH Regulations play a critical role in safeguarding health and safety by requiring employers to implement rigorous controls over hazardous substances, provide adequate training, and enforce the use of personal protective equipment (PPE) where necessary. Through these measures, COSHH supports a safer workplace environment across a range of high-risk industries.
Legal Implications of Non-Compliance with COSHH
Failure to comply with these regulations can result in serious legal, financial and reputational consequences for companies. This overview explores the criminal and civil liabilities, as well as the broader financial impacts of COSHH non-compliance.
Non-compliance with COSHH can result in criminal charges under the Health and Safety at Work Act (HSWA) 1974. The HSWA places a duty on employers to protect the health, safety and welfare of their employees and any others who may be affected by their work activities. Failure to control hazardous substances under COSHH is a breach of these duties, as inadequate measures can result in employee exposure to dangerous chemicals or materials.
Companies found guilty of breaching COSHH Regulations may face substantial fines. These penalties vary based on the severity of the breach, the degree of harm caused, and whether it was a repeated offence. Fines for large corporations can reach millions of pounds, especially when breaches are deliberate or due to gross negligence.
Employers and even individual managers may face prosecution for serious COSHH violations. Prosecutions are typically initiated when there is evidence of wilful neglect or gross failure to protect employees. Conviction in criminal courts is possible if the evidence demonstrates non-compliance and harm.
In the most severe cases, where breaches of COSHH have led to fatalities or significant health consequences for workers, company directors or responsible managers can be sentenced to imprisonment. The length of imprisonment depends on the severity and intentionality of the breach.
Examples of recent legal cases include:
- HSE v. Great North Eastern Railway Ltd – the railway company faced substantial fines for failing to protect workers from asbestos exposure. This case demonstrated the importance of COSHH Regulations and how a lack of compliance can expose companies to both fines and enforcement action.
- HSE v. Veolia ES (UK) Ltd. – this company was fined for multiple COSHH breaches due to failing to control employee exposure to hazardous dust and other toxic substances. The case illustrates how repeated non-compliance can result in more severe penalties.
These examples highlight the consequences of failing to control exposure to hazardous substances, underscoring the legal seriousness of COSHH non-compliance.
Employees who suffer injury, illness or chronic health issues due to hazardous substance exposure in the workplace may file civil lawsuits against their employer. Civil liability often focuses on employer negligence, where employers are held accountable for failing to prevent exposure risks effectively.
Employers are required under COSHH to identify hazardous substances and implement measures, for example PPE and ventilation systems, to control exposure. Failing to implement these can form a basis for a civil claim if exposure results in harm.
Employers must provide adequate training to workers handling hazardous substances. This training should cover the risks of exposure, proper handling procedures and emergency response actions. Claims can arise if inadequate training leads to exposure or injury.
COSHH mandates that employers carry out risk assessments to understand the potential hazards associated with substances in the workplace. Employees exposed due to incomplete or absent risk assessments may pursue claims based on this negligence.
The financial repercussions of COSHH non-compliance can be extensive including the legal fees associated with defending against criminal and civil cases, which can be substantial. Moreover, the fines imposed by regulatory authorities for COSHH non-compliance can be devastating, particularly for smaller businesses. If employees suffer harm and are successful in civil claims, companies may need to pay compensation for medical costs, lost wages and other damages. The cumulative financial impact can be significant, particularly when numerous employees are affected or if the health issues are long term.
Beyond financial costs, non-compliance with COSHH can damage a company’s reputation, including:
- Loss of employee trust – non-compliance can lead to employee mistrust, reduced morale and difficulty in retaining skilled workers. Workers are less likely to feel secure and valued if they believe their employer is neglecting their health and safety.
- Client and business partner relations – companies with a reputation for non-compliance may find that clients or business partners are reluctant to work with them. This could lead to a loss of business opportunities and difficulties in establishing new partnerships.
- Regulatory scrutiny – COSHH violations can lead to increased scrutiny from regulatory bodies like the HSE, which may conduct more frequent inspections and audits. This can disrupt operations and further strain company resources.
COSHH non-compliance carries serious consequences, including criminal prosecution, civil claims, financial losses and reputational damage. For companies, compliance is essential to protect both workers and the business from the legal and financial risks associated with hazardous substance exposure.
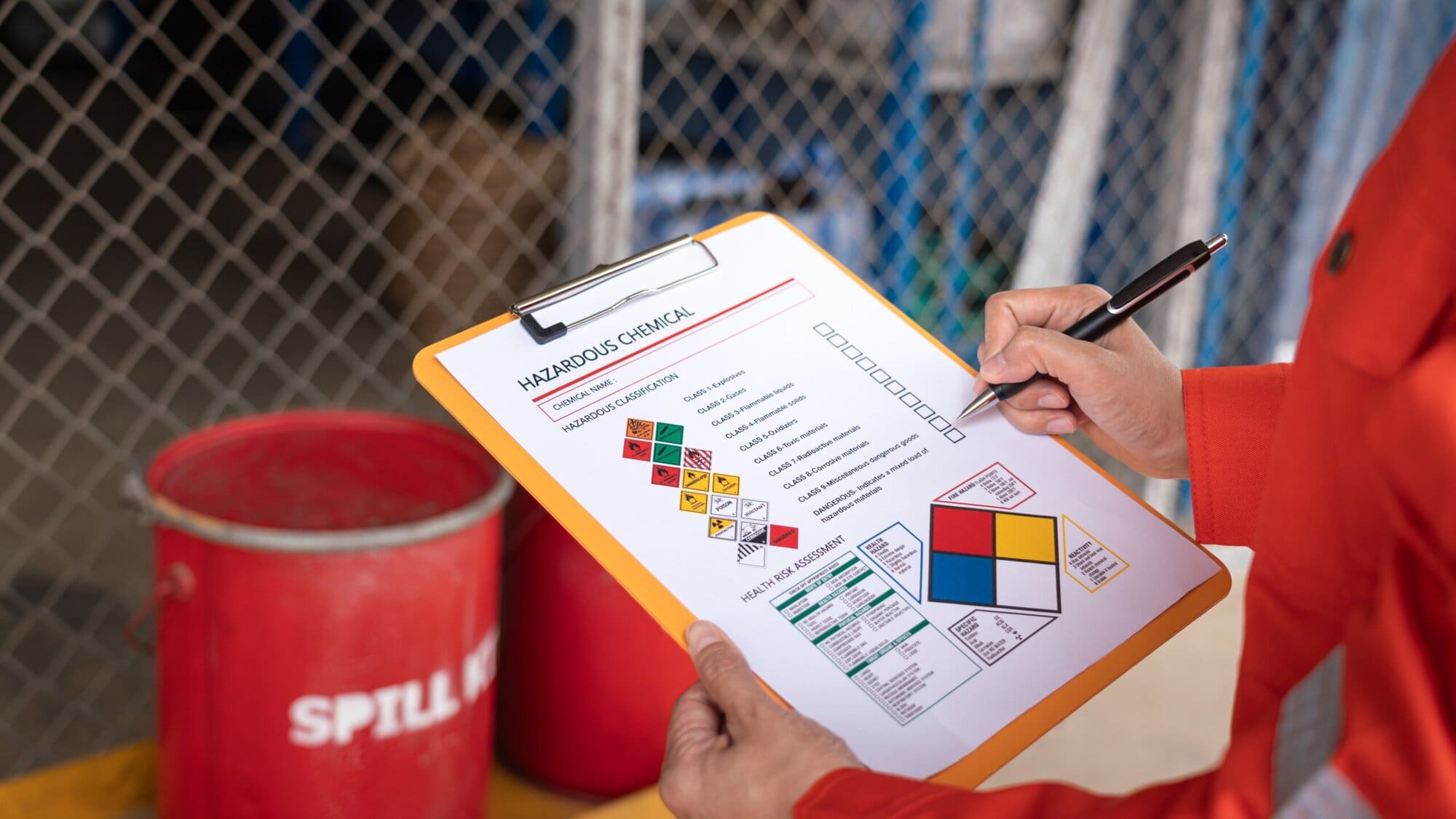
Key Regulations and Standards Related to COSHH
There are several key regulations and standards related to COSHH, including:
REACH (Registration, Evaluation, Authorisation and Restriction of Chemicals)
REACH is a European Union regulation that requires manufacturers and importers to register detailed information about chemicals produced or imported into the EEA. It complements COSHH by focusing on chemical safety and ensuring that hazardous chemicals are adequately assessed and regulated before they are used or sold. Under REACH, substances that pose significant health or environmental risks may be restricted or require specific authorisation, thus supporting COSHH’s objective of minimising chemical hazards in the workplace.
Globally Harmonised System (GHS)
The GHS is a global standard for the classification and labelling of chemicals, aimed at achieving consistency in chemical hazard communication worldwide. Through standardised labels, safety data sheets and classification criteria, GHS helps ensure workers understand the hazards associated with chemicals, regardless of where they are produced. The UK’s COSHH Regulations incorporate GHS principles to promote a clear understanding of chemical hazards, thus enhancing workplace safety through harmonised hazard communication.
OSHA Standards (U.S.)
The U.S. Occupational Safety and Health Administration (OSHA) sets regulatory standards for managing hazardous substances in the workplace, similar to COSHH. OSHA’s Hazard Communication Standard (HCS) aligns with GHS for consistent labelling and safety data sheets. Like COSHH, OSHA mandates risk assessments, employee training and control measures to prevent workplace exposure to hazardous substances, establishing a comparable framework for managing chemical risks.
In healthcare settings, COSHH is particularly relevant for managing biohazardous materials, including pathogens, biological samples and cleaning chemicals. Hospitals and labs must implement strict procedures to protect staff from infectious agents, body fluids and disinfectants. This includes sterilisation, containment of infectious agents, and use of PPE. Healthcare organisations must also ensure vaccination and regular training on biohazardous materials management as part of COSHH compliance.
In construction, COSHH regulates the handling of materials like asbestos and silica dust, both of which pose significant respiratory health risks. COSHH requires that employers implement dust control measures, such as dust suppression systems or respiratory protective equipment, to minimise worker exposure. Asbestos removal must follow strict guidelines to ensure safe handling and disposal, and any exposure must be managed through specific risk assessments and health surveillance procedures, as outlined by COSHH.
Personal Protective Equipment at Work Regulations 1992
These regulations work alongside COSHH to ensure that workers exposed to hazardous substances are provided with adequate PPE. Employers are required to provide suitable PPE that protects against specific risks identified in COSHH risk assessments. The PPE regulations mandate not only provision but also maintenance and training on proper usage to ensure PPE is effective against hazards like chemical splashes or inhalation of harmful particles.
Hazardous Waste Regulations 2005
The Hazardous Waste Regulations mandate safe disposal practices for substances classified as hazardous, aligning closely with COSHH’s focus on reducing exposure to hazardous substances. Under COSHH, businesses must prevent exposure to hazardous substances, and the Hazardous Waste Regulations require the correct labelling, storage and disposal methods to prevent environmental contamination. These regulations ensure that waste containing hazardous chemicals is managed to protect public health and the environment.
Steps for Ensuring COSHH Compliance
A COSHH risk assessment identifies hazardous substances, assesses the level of risk associated with them, and determines necessary control measures. Here are some important steps:
- Inventory check – list all chemicals and substances used, produced or encountered in the workplace.
- Safety Data Sheets (SDS) – obtain SDS for each substance, detailing potential hazards and handling procedures.
- Classify substances – identify which substances are hazardous and require COSHH assessment. This includes chemicals, dust, fumes, mists, vapours and biological agents.
- Assess the level of risk – determine the ways employees may be exposed to each substance, for example inhalation or skin contact. Evaluate how often and how long workers are exposed. Consider the potential health impact, ranging from minor irritation to chronic health conditions or fatal consequences. Identify any vulnerable groups, such as pregnant employees or those with existing health conditions.
- Decide on necessary control measures – based on the risk assessment, implement effective control measures to reduce exposure to an acceptable level.
Implementing control measures effectively minimises employees’ exposure to hazardous substances and protects health and safety. There are three primary types of control measures:
- Fume hoods and local exhaust ventilation (LEV) – capture hazardous fumes, dust or vapours at the source before they disperse into the work environment.
- Enclosures – use enclosed systems to contain hazardous materials, particularly in manufacturing or lab settings.
- Automation – automate processes to reduce the need for direct human contact with hazardous substances.
You should limit the amount of time workers spend exposed to hazardous substances and develop and implement procedures for safely handling, storing and disposing of hazardous substances. Clearly label hazardous substances and display hazard information prominently in work areas.
PPE should include:
- Respirators – for employees exposed to harmful dust, mists or fumes.
- Protective clothing – use gloves, gowns or aprons to protect against chemical splashes.
- Eye and face protection – use goggles or face shields as needed.
In environments where employees are exposed to significant health risks, COSHH requires employers to conduct health surveillance to monitor any impact of exposure on workers’ health. Surveillance is necessary if employees are exposed to:
- Substances that can cause cancer, asthma or dermatitis.
- Materials with known adverse health effects in prolonged or repetitive exposure.
Conduct regular health assessments, for example respiratory function tests, to detect early signs of health effects from exposure. Keep confidential records of each employee’s health surveillance data, ensuring it is regularly updated. If an employee shows early signs of exposure-related illness, adjust their work conditions or exposure levels to protect their health.
Training is essential to ensure all employees understand the hazards, proper handling of hazardous substances, and their role in maintaining COSHH compliance. Ensure all new employees receive training on COSHH Regulations, risks and safe work practices. Offer periodic refreshers or updates on new procedures, substances or equipment. Training should include straightforward guidance on handling hazardous substances, using PPE, and emergency procedures. Ensure that training materials, including SDS, COSHH assessments and emergency instructions, are easily accessible to all employees and provide training and materials in formats that are accessible for all employees, considering language and literacy needs.
COSHH requires employers to ensure employees understand their role in managing risks. Regularly involve employees in discussions about workplace safety and encourage feedback. Accurate record-keeping is essential for compliance and is a legal requirement under COSHH. Keep a record of all COSHH assessments, including details of identified hazards, assessed risks and implemented control measures. Record details of engineering, administrative and PPE controls. Include regular maintenance logs for equipment like LEV systems. Keep logs of all COSHH-related training sessions, including attendance records, topics covered and dates. Ensure that all records are complete, up to date and easily accessible for internal reviews and external audits. Non-compliance due to inadequate documentation could lead to legal penalties and affect worker safety.
By following these steps, employers can achieve full compliance with COSHH Regulations, reducing health risks to employees and fostering a culture of safety.
Future Trends in COSHH Legislation and Enforcement
The push for greater workplace safety and public health is likely to drive more stringent enforcement of COSHH Regulations. As awareness grows around the long-term health impacts of hazardous substances, regulatory agencies may increase the frequency of workplace inspections and enforce stricter compliance. This trend could involve:
- Tighter exposure limits – future COSHH legislation might further reduce permissible exposure limits for certain hazardous substances, particularly those known to have cumulative health effects, such as carcinogens or reproductive toxins. This approach is already seen in sectors like manufacturing and construction, where toxic exposures are common. Regulatory agencies might adjust these limits to reflect the latest research in toxicology and occupational health.
- Expanded substance coverage – as new chemical risks are identified, COSHH legislation may expand to include a broader range of substances, including newly classified nanomaterials and biotechnological agents. New testing methods and data may identify additional risks associated with previously overlooked substances.
- Higher penalties for non-compliance – penalties for failing to meet COSHH standards may become more severe, encouraging proactive risk management. New laws may also introduce liability for indirect exposures affecting local communities or ecosystems, which could further push companies to adopt stringent compliance practices.
- Technological advancements in compliance – the rise of digital tools and artificial intelligence has introduced new ways for businesses to manage and comply with COSHH requirements efficiently.
- The movement towards sustainability – this is influencing COSHH and similar regulations to emphasise the use of safer, more environmentally friendly chemicals. Legislation may require companies to replace hazardous chemicals with safer alternatives when available. This approach, known as ‘green chemistry’, aims to design chemical products and processes that reduce or eliminate the use and generation of hazardous substances. COSHH requirements might eventually mandate the substitution of certain substances or the use of chemicals with lower toxicity, persistence and bioaccumulation.
- Chemical management and lifecycle assessment – COSHH laws could evolve to encompass the entire lifecycle of chemicals, from production to disposal, ensuring that companies account for potential environmental and health impacts throughout a chemical’s use. Businesses may need to provide environmental impact reports and outline how they will responsibly manage waste.
COSHH Regulations are likely to become stricter, with a greater emphasis on real-time compliance, technological integration and sustainability. Future legislation will not only protect workers from immediate health risks but also consider the broader environmental impact of chemical use, pushing companies towards safer and more sustainable practices. These anticipated changes will require organisations to be agile, investing in both technology and green alternatives to remain compliant in an increasingly regulated landscape.
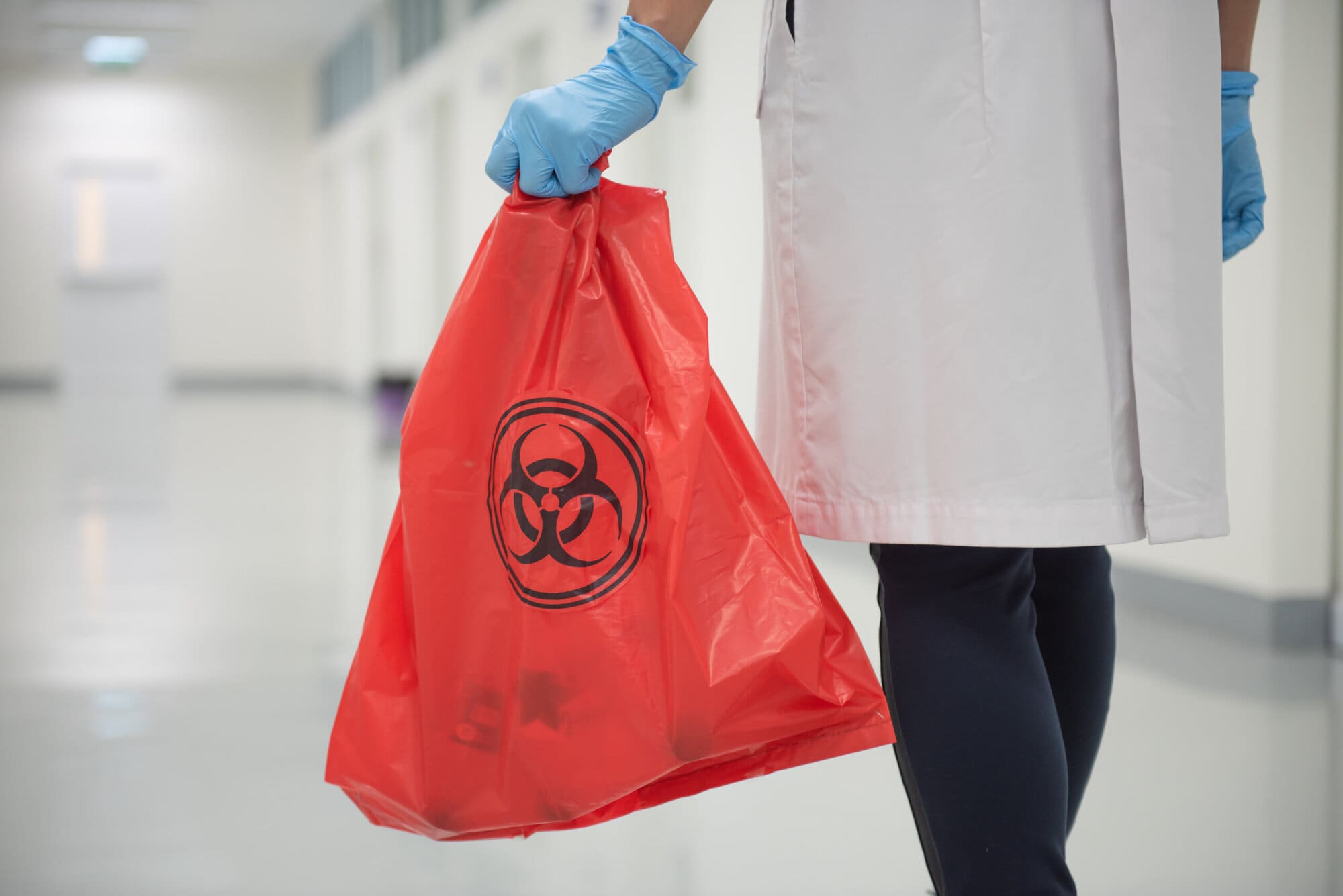
Conclusion
Understanding the legal implications and regulatory framework surrounding COSHH is essential for ensuring workplace safety, minimising health risks, and ensuring legal compliance. COSHH Regulations establish clear guidelines for assessing, managing and controlling exposure to hazardous substances, protecting both employees and the wider community from potential harm. Employers hold a critical responsibility to not only identify potential hazards but also to implement preventative measures, conduct regular risk assessments, and provide adequate training for all personnel involved. Non-compliance with COSHH Regulations can lead to severe legal repercussions, including fines, legal liabilities, and even criminal charges in cases of gross negligence.
By adhering to COSHH guidelines, organisations not only safeguard their workforce but also uphold their reputations and demonstrate a commitment to health and safety standards. Compliance encourages a proactive approach to risk management, creating a safer work environment and reducing the likelihood of accidents or health issues related to hazardous substances.
In an evolving regulatory landscape, staying updated with COSHH Regulations and implementing best practices remains a legal and ethical obligation, reinforcing a culture of safety and responsibility across industries.