In this article
According to the Health and Safety Executive (HSE), workplace injuries and work-related ill health cost approximately £20.7 billion a year in Great Britain. A significant cause of work-related injuries and illnesses is exposure to hazardous substances, including chemicals, fumes, dust, gases and biological agents. Compliance with the Control of Substances Hazardous to Health (COSHH) regulations can help to significantly reduce injuries and illnesses.
Ensuring a safe and healthy work environment is a fundamental responsibility for all employers, particularly when dealing with hazardous substances. The COSHH regulations provide a framework to manage these risks effectively. However, compliance with these regulations is heavily reliant on the proper training and education of employees. Without adequate training, even the most thorough plans for hazard control can fail and can lead to significant health risks and legal repercussions.
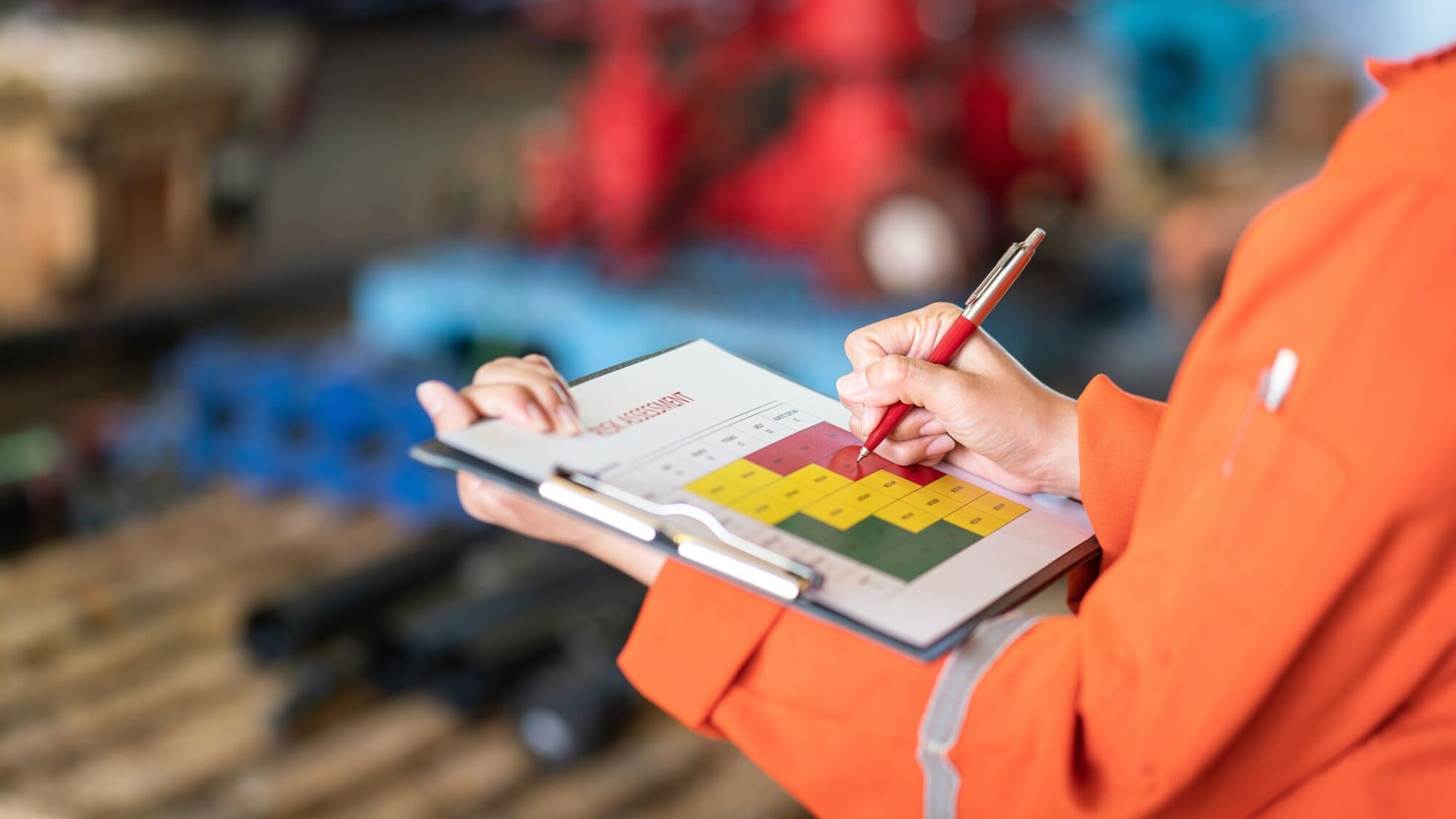
Importance of Training in COSHH Compliance
The Control of Substances Hazardous to Health (COSHH) is a set of regulations in the UK designed to protect workers from health risks associated with hazardous substances. Enforced by the Health and Safety Executive (HSE), COSHH regulations require employers to control substances that can harm workers’ health. The aim is to prevent or reduce workers’ exposure to hazardous substances by implementing measures such as risk assessments, proper storage and use of personal protective equipment (PPE).
The key elements of COSHH are:
- Risk assessments: Employers must conduct thorough risk assessments to identify potential hazards from substances used or generated in the workplace. This includes evaluating how substances are used, potential exposure routes and the severity of the risks.
- Control measures: Based on the risk assessment, employers must implement control measures to minimise exposure to hazardous substances. This can involve engineering controls, such as ventilation systems, and administrative controls, such as changing work practices and providing appropriate PPE.
- Information and training: Employees must be informed about the risks associated with hazardous substances and trained on how to handle them safely. This includes understanding labels, safety data sheets (SDS) and emergency procedures.
- Monitoring and health surveillance: In some cases, employers are required to monitor the levels of hazardous substances in the workplace and conduct health surveillance of employees to detect early signs of work-related ill health.
- Record-keeping: Employers must keep detailed records of risk assessments, any control measures that are implemented, monitoring results and health surveillance to ensure ongoing compliance and to provide evidence during inspections or audits.
Training is essential to ensure employees understand the fundamental principles of COSHH regulations. COSHH regulations require employers to prevent or control exposure to hazardous substances to protect workers’ health. Employees must understand the legal framework, which includes identifying potential hazards, conducting risk assessments and implementing control measures. Training programmes ensure that employees are aware of their responsibilities and the steps they need to take to comply with these regulations, which can help to create a safer and more compliant workplace environment.
One of the key components of COSHH training is educating employees on how to identify hazardous substances in their workplace. This involves understanding the different forms hazardous substances can take, such as liquids, gases, dust and fumes. Training helps employees recognise labels, safety data sheets and other indicators of hazardous substances, which is essential for assessing the associated risks. By being able to accurately identify these substances, employees can take appropriate precautions and implement necessary safety measures to protect themselves and their coworkers.
Effective risk assessment is essential for COSHH compliance and proper training equips employees with the skills to conduct these assessments accurately. Training programmes teach employees how to evaluate exposure levels, consider the potential health effects of different substances and identify who might be at risk. This knowledge enables employees to determine appropriate control measures, such as engineering controls, administrative controls and personal protective equipment (PPE). Regular and thorough risk assessments help in creating a safer workplace by proactively managing and mitigating risks associated with hazardous substances.
Components of Effective Training Programmes
When creating a COSHH training programme, there are several components you should include:
COSHH Awareness
COSHH awareness training is the foundation of an effective training programme and provides employees with essential knowledge about hazardous substances and their potential impacts. COSHH awareness should include:
- Recognition of hazardous substances: Employees should learn how to identify hazardous substances in their workplace through labels, safety data sheets and other indicators. This includes understanding the symbols and terminology used to denote various hazards.
- Routes of exposure: Training should outline the most common routes through which hazardous substances can enter the body, such as inhalation, ingestion, skin contact and injection. Understanding these routes helps employees take necessary precautions to prevent exposure.
- Potential health effects: Employees should be educated on the acute and chronic health effects associated with exposure to hazardous substances. This includes immediate effects like irritation and poisoning, as well as long-term effects like respiratory diseases and cancers.
Safe Handling Procedures
Training modules on safe handling procedures can help to minimise the risks associated with hazardous substances. These modules typically include:
- Safe handling: Instructions on how to safely handle hazardous substances to prevent spills, leaks and accidental exposure are necessary in COSHH training. This should include guidelines on the proper use of tools and equipment.
- Storage: Training should educate employees on best practices for storing hazardous substances to avoid accidental release and degradation. This involves understanding storage conditions such as temperature, humidity and the separation of incompatible substances.
- Disposal: An understanding of proper disposal methods for hazardous substances to prevent environmental contamination and ensure regulatory compliance is essential. This includes training on how to use disposal containers and procedures for disposing of different types of hazardous waste.
Use of Personal Protective Equipment (PPE)
Training employees on the correct selection, use and maintenance of personal protective equipment (PPE) is vital for mitigating exposure to hazardous substances. Effective PPE training includes:
- Selection: This includes guidance on choosing the appropriate PPE based on the type of hazardous substance and the level of exposure risk. This can involve different types of gloves, masks, goggles and protective clothing.
- Use: Training should provide detailed instructions on how to properly wear and adjust PPE to ensure maximum protection. This includes training on the correct procedures for wearing respiratory protection and ensuring a proper fit.
- Maintenance: Employees should be given information on how to inspect, clean and store PPE to maintain its effectiveness. Regular maintenance and proper storage of PPE are essential and ensure that equipment continues to provide the intended level of protection over time.
By incorporating these components into training programmes, organisations can effectively equip their employees with the knowledge and skills necessary to safely handle hazardous substances and comply with COSHH regulations. This not only improves workplace safety but also promotes a culture of proactive risk management and regulatory adherence.
Implementation and Delivery of Training
Effective COSHH training programmes must be tailored to the specific needs of different industry sectors and the types of hazardous substances present in each workplace. This customisation ensures that the training is relevant and directly applicable to the employee’s daily tasks and work environment.
Because different industries face unique hazards, tailored training programmes should include industry-specific content. For example, a chemical manufacturing plant will have different training needs compared to a healthcare facility. Tailored programmes address the specific types of hazardous substances and the particular risks associated with those substances in each industry.
Training programmes should also include role-specific training. Within an organisation, different roles may require different levels and types of training. For example, lab technicians might need in-depth training on handling and disposing of chemicals, while administrative staff may only need awareness training on emergency procedures. Additionally, tailored training often includes scenarios and case studies relevant to the specific workplace. This helps employees understand how to apply their training in real-world situations which can improve their ability to recognise and respond to hazards effectively.
Engaging employees in training sessions is essential for effective learning and retention. Interactive methods, such as quizzes, group discussions and hands-on activities, keep employees actively involved in the learning process. This not only makes training more engaging but also helps reinforce key concepts. It can also be helpful to include case studies of real incidents involving hazardous substances to help employees understand the practical implications of their training. Analysing these cases can provide valuable lessons and highlight the importance of following safety procedures. Conducting practical demonstrations of safe handling procedures, PPE usage and emergency response actions allows employees to observe and practise these skills in a controlled environment. This hands-on approach is particularly effective in building confidence and competence.
Ongoing training and regular updates are essential to ensure that employees remain informed and compliant with current COSHH regulations and best practices. This includes:
- Regulatory changes: COSHH regulations and guidelines can change over time. Regular updates ensure that employees are aware of the latest legal requirements and understand how to implement any new procedures or standards.
- Workplace changes: Changes in workplace practices, such as the introduction of new equipment or substances, necessitate updates to training programmes. Employees need to be trained on how these changes affect their safety protocols.
- Technological advancements: Advances in technology can lead to new methods for managing hazardous substances or improved PPE. Training programmes should incorporate these advancements to enhance safety and efficiency in handling hazardous substances.
- Refresher courses: Periodic refresher courses help reinforce knowledge and skills and ensure that employees do not become complacent. These courses can also address any emerging risks or trends in the industry.
By implementing tailored programmes, enhancing engagement and participation and providing regular updates, organisations can ensure their COSHH training is effective, comprehensive and up to date. This approach not only promotes a safer work environment but also supports ongoing compliance with COSHH regulations.
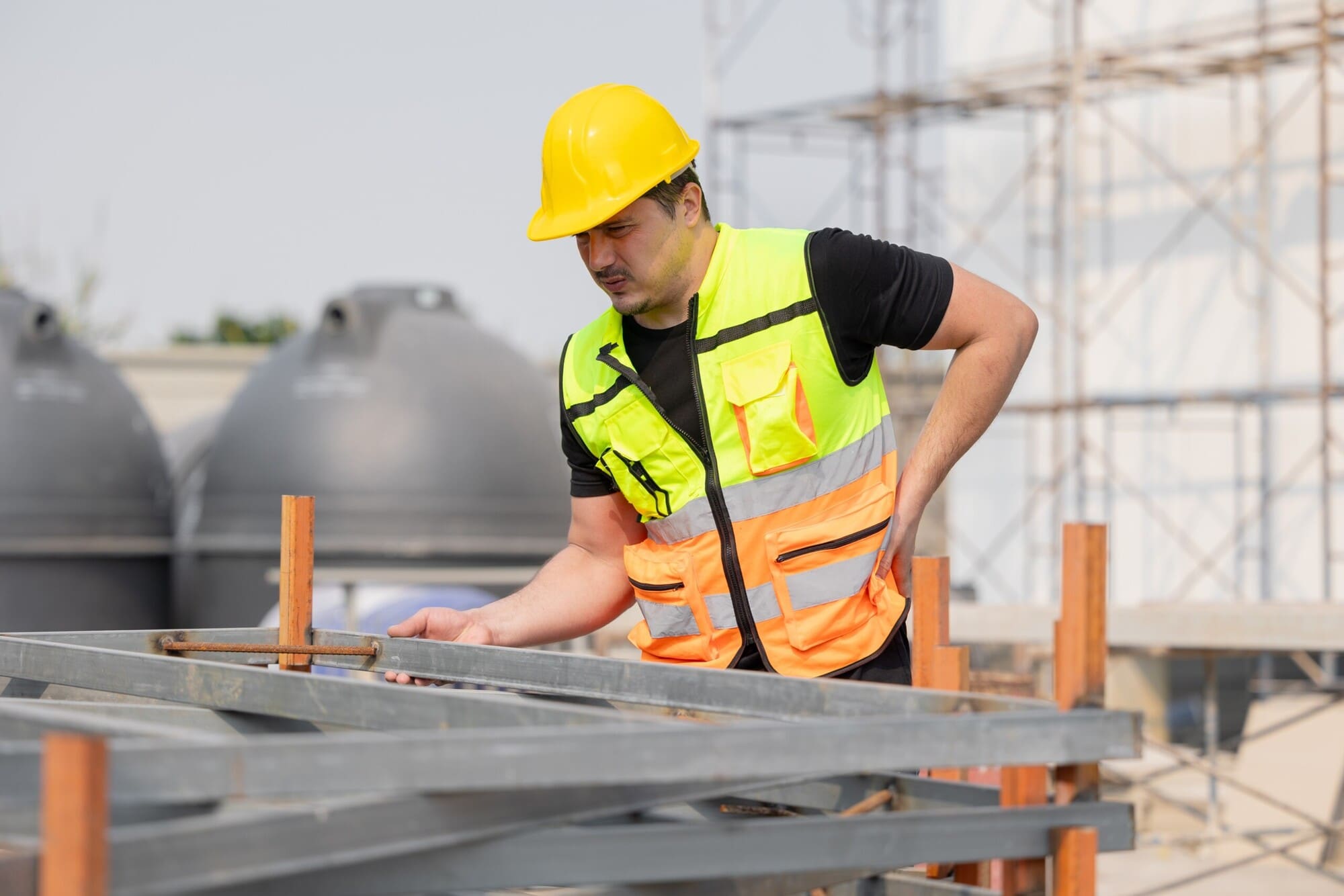
Benefits of Effective Training
Effective COSHH training has many potential benefits for both employers and employees, including:
Improved compliance
Effective training programmes are instrumental in ensuring that employees understand and adhere to COSHH regulations. Well-trained employees are more knowledgeable about the legal requirements and the specific procedures they need to follow to comply with these regulations. This increased awareness leads to:
- Accurate risk assessments: Employees who are well-versed in COSHH principles can conduct thorough and precise risk assessments, identify potential hazards and implement appropriate control measures.
- Proper handling and use: Trained employees are more likely to handle hazardous substances correctly, use PPE appropriately and follow safe disposal procedures, which can significantly reduce the risk of exposure incidents.
- Reduced penalties: By maintaining high standards of compliance, organisations minimise the risk of non-compliance penalties, legal actions and potential shutdowns imposed by regulatory bodies. This not only protects the organisation financially but also upholds its reputation.
Improved culture of safety
Comprehensive training programmes create a culture of safety within the organisation, where safety becomes a core value rather than just a compliance requirement. This culture of safety leads to:
- Fewer accidents and injuries: When employees are well-trained in recognising and managing hazards, the likelihood of accidents and injuries decreases. Safe work practices become second nature which leads to a safer work environment.
- Lower rates of occupational illnesses: Proper training ensures that employees are aware of the health risks associated with hazardous substances and know how to protect themselves, which typically results in lower rates of occupational illnesses and long-term health issues.
- Proactive risk management: A strong safety culture encourages employees to be proactive in identifying and addressing potential hazards before they lead to incidents. This continuous improvement mindset improves overall workplace safety.
Increased employee empowerment
Training empowers employees by equipping them with the knowledge and skills they need to maintain a safe and healthy work environment. This empowerment manifests in several ways:
- Increased vigilance: Empowered employees are more vigilant and attentive to potential hazards and more likely to take ownership of safety practices and actively contribute to hazard identification and mitigation efforts.
- Confidence in safety procedures: When employees are confident in their understanding of safety procedures and their ability to handle hazardous substances safely, they are more likely to follow protocols diligently and advocate for safety improvements.
- Active participation: Training encourages employees to participate actively in safety programmes, safety committees and workplace inspections. Their involvement ensures that safety measures are practical, effective and continuously improved based on frontline experiences.
By investing in effective training programmes, organisations not only improve compliance with COSHH regulations but also create a workplace culture of safety and empower their employees. This holistic approach to safety training leads to a safer, healthier and more productive work environment, benefiting both employees and the organisation as a whole.
Case Studies
Case Study: Nosmar Construction Company
Nosmar is a large construction company specialising in commercial and residential projects. The nature of their work often involves the use of hazardous substances such as solvents, paints and adhesives, and they often have to deal with dust and asbestos. Given these risks, the company recognised the necessity of a comprehensive COSHH training programme to ensure employee safety and regulatory compliance.
The training programme was meticulously tailored to meet the sector-specific needs of the construction industry. It included modules focused on various hazardous substances, from chemicals used in paints and coatings to asbestos management and dust control. Each module provided practical solutions and safety procedures relevant to the types of hazards encountered on construction sites.
To increase the effectiveness of the training, Nosmar Construction incorporated hands-on workshops. These workshops allowed employees to practise the correct use of PPE, such as respiratory protection for asbestos handling and safe techniques for managing and disposing of chemical waste. Real-life scenarios and case studies were integrated into the training to help employees understand the practical implications of their actions, which helped to reinforce the importance of following safety protocols.
Nosmar Construction also established a system for ongoing assessment and feedback. This included periodic quizzes, practical evaluations and anonymous surveys to gather employee feedback on the training’s relevance and effectiveness. The insights gained from these assessments were used to continuously refine and improve the training programme and ensure it remained up to date with evolving regulations and industry practices.
The implementation of this robust COSHH training programme had several positive outcomes. Tailoring the training to the specific hazards of the construction industry proved essential for addressing the unique risks faced by employees. Hands-on workshops facilitated the translation of theoretical knowledge into practical skills and resulted in improved confidence and competence in handling hazardous substances. Incorporating real-life scenarios made the training more relatable and emphasised the potential consequences of non-compliance, thereby reinforcing adherence to safety protocols.
Furthermore, the focus on continuous improvement through regular feedback and assessment allowed Nosmar Construction Company to keep the training programme relevant and effective. This commitment to ongoing learning promoted a strong safety culture within the organisation and led to a significant reduction in safety incidents and improved overall safety performance on construction sites.
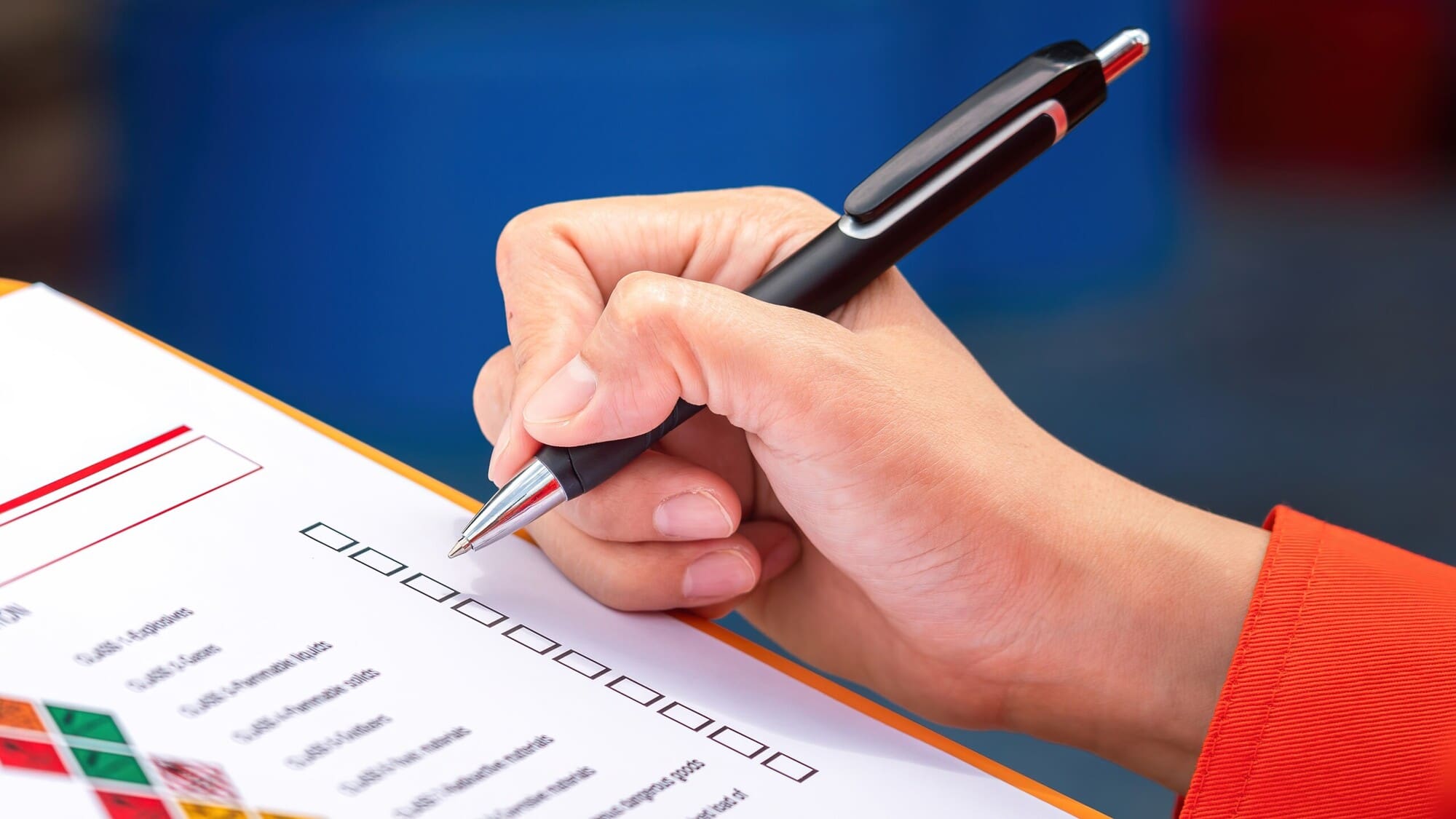
Case Study: EVM Food Processing Company
EVM Food Processing Company is a prominent business in the food manufacturing sector and handles various hazardous substances, including cleaning agents, preservatives and additives. To address the associated risks and ensure regulatory compliance, the company implemented a comprehensive COSHH training programme tailored to its specific operational needs.
The training programme at EVM was carefully customised to address the unique hazards encountered in different departments. For example, specialised modules were developed for production, maintenance and quality control teams, each focusing on the safe handling of relevant substances. The programme included interactive e-learning courses, virtual reality (VR) simulations and role-playing exercises to increase employee engagement. These immersive learning methods provided practical experience with hazardous scenarios and helped employees learn how to respond effectively to spills and accidents.
In addition to COSHH-specific training, EVM integrated health and safety workshops into their programme. These workshops combined COSHH training with broader topics such as emergency evacuation procedures and first aid to offer a more holistic approach to workplace safety. This integration ensured that employees understood how COSHH practices fit into the larger safety framework.
To ensure the effectiveness of the training programme, EVM also established a robust monitoring and evaluation system. This system included regular audits, employee feedback surveys and periodic refresher courses. The feedback collected was used to continuously update and refine the training content and delivery methods and ensure the programme remained relevant, engaging and effective.
The tailored approach to training proved essential in addressing the specific risks associated with different roles within the company. Interactive learning methods significantly improved employee engagement and retention and provided them with practical experience in managing hazardous situations. The holistic approach to safety, combining COSHH training with broader health and safety topics, contributed to a cohesive safety culture within the organisation.
Overall, EVM’s experience highlights the importance of customised, interactive training and continuous improvement. By focusing on these elements, the company successfully created a strong safety culture, reduced incidents related to hazardous substances and ensured a safer working environment for its employees.
Conclusion
In conclusion, training and education are essential components in achieving effective COSHH compliance, as they provide employees with the necessary knowledge, skills and awareness to manage the risks associated with hazardous substances. By prioritising and investing in robust training programmes, organisations can ensure that their employees are well-equipped to handle these substances safely and in accordance with regulatory requirements. This investment not only helps in meeting legal obligations but also creates a culture of safety within the workplace and promotes the overall well-being and health of the workforce. Ultimately, comprehensive training increases organisational safety, reduces the likelihood of incidents and non-compliance penalties and supports a proactive approach to workplace safety.