In this article
Thousands of workers in industries such as construction, maintenance, utilities and manufacturing might encounter having to work in confined spaces during the course of their work. The Health and Safety Executive (HSE) defines confined spaces as: “…one which is both enclosed or largely enclosed, and has a reasonably foreseeable specified risk to workers of fire, explosion, loss of consciousness, asphyxiation or drowning”. This can be any place, including any chamber, tank, vat, pipe, sewer, or any other similar space which, by virtue of its enclosed nature, creates conditions that can give rise to a likelihood of an accident, harm or injury that requires emergency action.
The hazards associated with working in confined spaces include:
Oxygen deficiency-oxygen can be lacking in a confined space for the following reasons:
- Displacement of air by another gas
- Various biological processes or chemical reactions such as rotting of organic matter, rusting of metals, burning, etc.
- Absorption of air onto steel surfaces, especially where these are damp.
- Oxygen enrichment – an excess of oxygen, in the presence of combustible materials, results in an increased risk of fire and explosion. Some materials which do not burn in air, may burn vigorously or even spontaneously in an enriched oxygen atmosphere.
- Toxic atmosphere – this may cause various acute effects, including impairment of judgement, unconsciousness and even death. A toxic atmosphere may occur due to the presence or ingress of hazardous substances. These substances may be present in the confined space for various reasons such as:
- Remaining from previous processing or storage
- Arising from the disturbance of sludge and other deposits
- The presence of a fire or flames within the space
- Seepage from improperly isolated adjoining plant
- Formation during the work processes carried out in the space
- Being released from under scale and in brickwork as a result of the work process.
- Flammable or explosive atmospheres – a flammable atmosphere presents a risk of fire or explosion. Such an atmosphere can arise from the presence in the confined space of flammable liquids or gases or of a suspension of combustible dust in the air. If a flammable atmosphere inside a confined space ignites, an explosion may occur, resulting in the expulsion of hot gases and the disintegration of the structure.
- Excessive heat – the enclosed nature of a confined space can increase the risk of heat stroke or collapse from heat stress if conditions are excessively hot. The risk may be exacerbated by the wearing of personal protective equipment (PPE) or by lack of ventilation.
- Flowing liquid or free flowing solids – liquids or solids can flow into the confined space causing drowning, suffocation, burns and other injuries. Solids in powder form may also be disturbed in a confined space resulting in an asphyxiating atmosphere.
- Physical restrictions – these can cause difficulties for workers’ movements and may impede escape in any emergency situation.
UK fatal injury statistics from the Reporting of Injuries, Diseases and Dangerous Occurrences Regulations (RIDDOR) from 2014/15 to 2022/23 highlight that 36 people died because of drowning or asphyxiation, 43 from fire or explosion, 12 from contact with a harmful substance, and 123 from being trapped by something collapsing or overturning on them, including trench collapses. These are all specified risks under the Confined Spaces Regulations 1997.
Cutting-edge technologies and innovations are offering solutions set to transform confined space working and to improve the safety of those working in these environments. They aim to ensure better protection for workers, often drastically reducing the need for human presence in such hazardous environments, prioritising the well-being of workers while optimising operational processes.
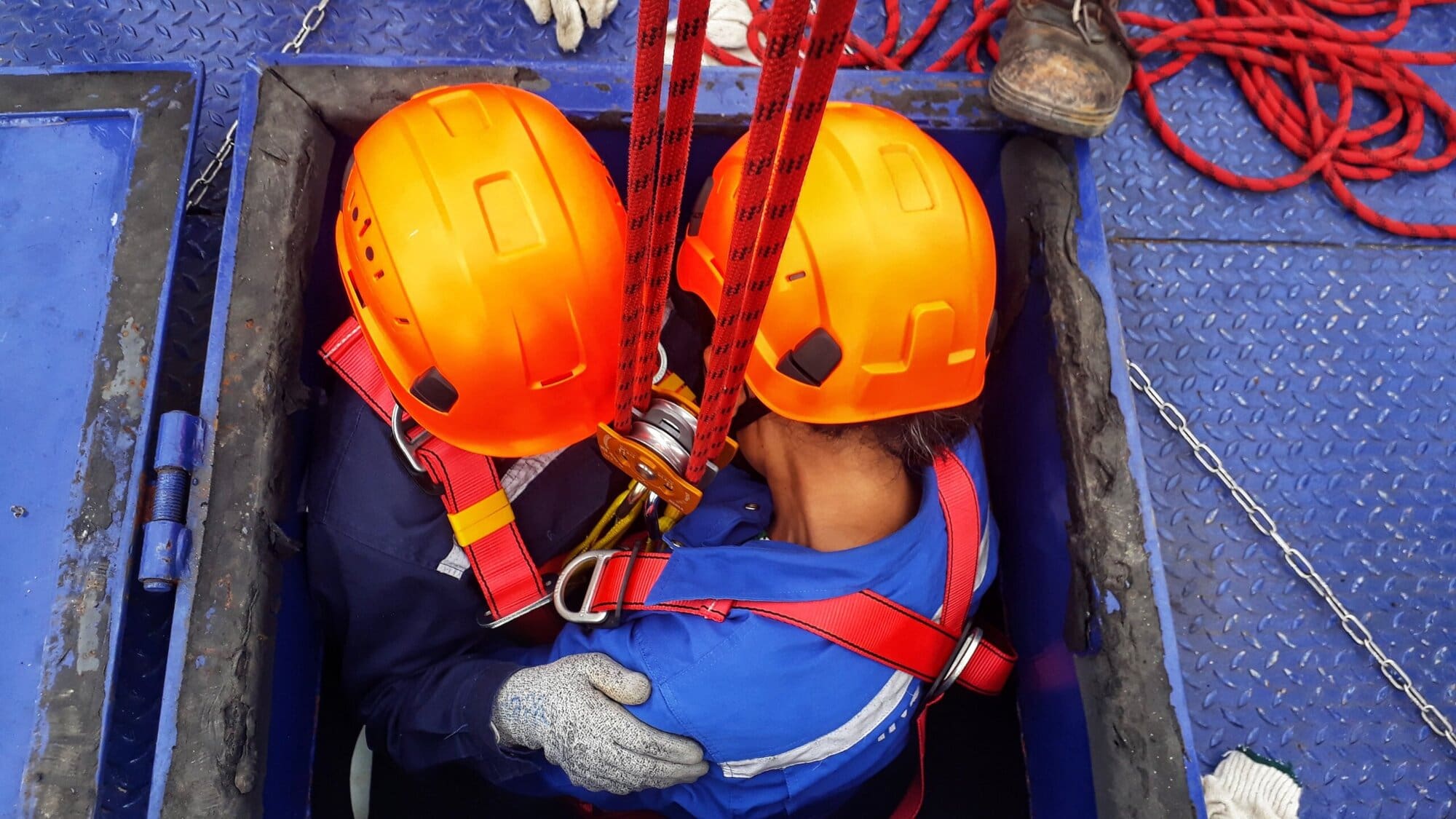
In this article we will look in more detail at some of the current challenges of confined space working and explore emerging technologies that aim to improve working practices and working environments.
Current Challenges in Confined Space Work
Risks and dangers can arise in confined spaces because of a variety of issues. Some of the most common include:
- One of the most common risks of working in a confined space is that air circulation can be limited. While oxygen levels within a confined space can be perfectly satisfactory at the beginning of the work, those levels can soon change once work commences, especially if the work is arduous in nature. Not only do oxygen levels reduce, but carbon dioxide levels increase, so a lack of oxygen can develop subtly and may initially go unnoticed.
- Whilst a lack of oxygen can be one consequence of poor air circulation in a confined space, that poor air circulation can also lead to a build-up of poisonous or noxious fumes. Examples of this can be from welding or the disturbance of materials already in the confined space, such as slurry or food waste.
- The risk of a gas explosion is greatly increased when considered in the context of confined spaces. One of the greatest culprits is methane, a highly combustible hydrocarbon-based gas that is heavier than air and can easily build up in a workplace environment. The classic environment where methane gas has been a historic killer has been down coal mines. The next three most common explosive gases are hydrogen, oxygen, and acetylene.
- Flooding is particularly dangerous in a confined space. As well as liquids such as water, there are certain solids that are just as dangerous as water when it comes to flooding in a confined space, including grain or flour in silos, and earthworks surrounding tunnels which can flood the space if the tunnel collapses.
- Dust can pose a dual threat when it comes to confined spaces. Firstly, it can cause severe respiratory problems and restrict breathing. Secondly, depending on the constituents of the dust, it can also have explosive properties; for example, not only is flour dust highly explosive, but dust from custard powder, instant coffee, sugar, dried milk, potato powder and soup powder are all highly explosive.
- Both excessive heat and cold in confined spaces can be dangerous. These conditions can give rise to a dangerous increase or decrease in the core body temperature. Gradual thermal build-up in a confined space can result in heat exhaustion.
- Restricted access is often one of the problems with working in confined spaces; having a limited means of entry and exit can make safety monitoring and escape or rescue difficult.
- Confined space entry often requires the use of breathing apparatus or respiratory protection equipment. By its very nature this equipment obstructs speech and creates a barrier to effective communication. In confined spaces such as tunnels or mines, wireless/radio signals may not easily penetrate, leading to signal loss or interference, and sound waves can bounce off walls, leading to echoes that make it hard to understand spoken words. In narrow, small or badly lit spaces, it may be difficult to maintain eye contact or to observe non-verbal cues, such as body language and facial expressions, which are important in communication.
There are several traditional solutions available to mitigate or counteract the risks and dangers of working in a confined working space environment; however, they often fall short in terms of efficiency, reliability, and worker safety. Some of these solutions and their limitations include:
Gas detection
This typically involves workers manually using handheld devices to check for hazardous gases such as oxygen deficiency, carbon monoxide, or methane. This is often done before entry and periodically during the work. However, the conditions in the confined space can change quickly, meaning that hazards might not be detected as they occur between checks as detectors can only sample the environment at a specific point in time and space. There is also the potential for human error occurring such as workers not properly using or maintaining the equipment, misinterpreting the data, or not consistently adhering to safety procedures or equipment operating manuals.
Restriction of movement
This can be either at the entry or inside the space that affects the restriction and poses a hazard to the worker. The most common problems are an inability to turn, or a restriction in the ability to reach or otherwise access a particular area within the space, and any personal protective equipment (PPE), including breathing apparatus, and tools or equipment that the worker will have to carry to ensure confined space safety, which may have an impact on their ease of movement and emergency escape routes.
Entry monitoring
This is traditionally carried out by a worker tracking who enters and exits the confined space either in person or via a monitoring system such as CCTV. However, this monitoring can be inconsistent, especially in busy environments where a worker’s attention may be drawn elsewhere and them possibly missing crucial details or failing to respond quickly enough in an emergency situation. In addition, the traditional paper-based permit system for working in confined spaces, where entry logs and safety checks are manually recorded, can be prone to errors and can cause delays in emergency response if the records are unclear or incomplete.
Communication – traditional communication equipment has its limitations in confined spaces; as mentioned previously, walls, metal structures, and other physical barriers can block or reflect communication signals, making it difficult to maintain clear communication.
These are just a few examples of why there is a growing need for technological advancements to address the limitations of these more traditional methods.
Emerging Technologies Enhancing Confined Space Work
Emerging technologies and technological breakthroughs for use in confined space working have introduced innovative tools and methods that significantly reduce risks and improve safety in these working environments. Robotics, drones, and advanced monitoring systems are at the forefront of this change, providing a safer alternative to manual entry. Let’s look at some of these in more detail:
Robotics and autonomous systems
Robots and drones equipped with high-definition cameras and sensors can now perform initial assessments of confined spaces. These devices can navigate through cramped and hazardous areas, capturing detailed images and data without putting human workers in danger. This remote inspection capability allows for thorough pre-entry evaluations, identifying potential hazards before any worker enters. One of the primary benefits of this technology is the ability to perform inspections remotely. Drones and robots can quickly and safely access confined spaces, providing real-time data and visual feeds to operators. This not only minimises the need for human entry but also speeds up the inspection process.
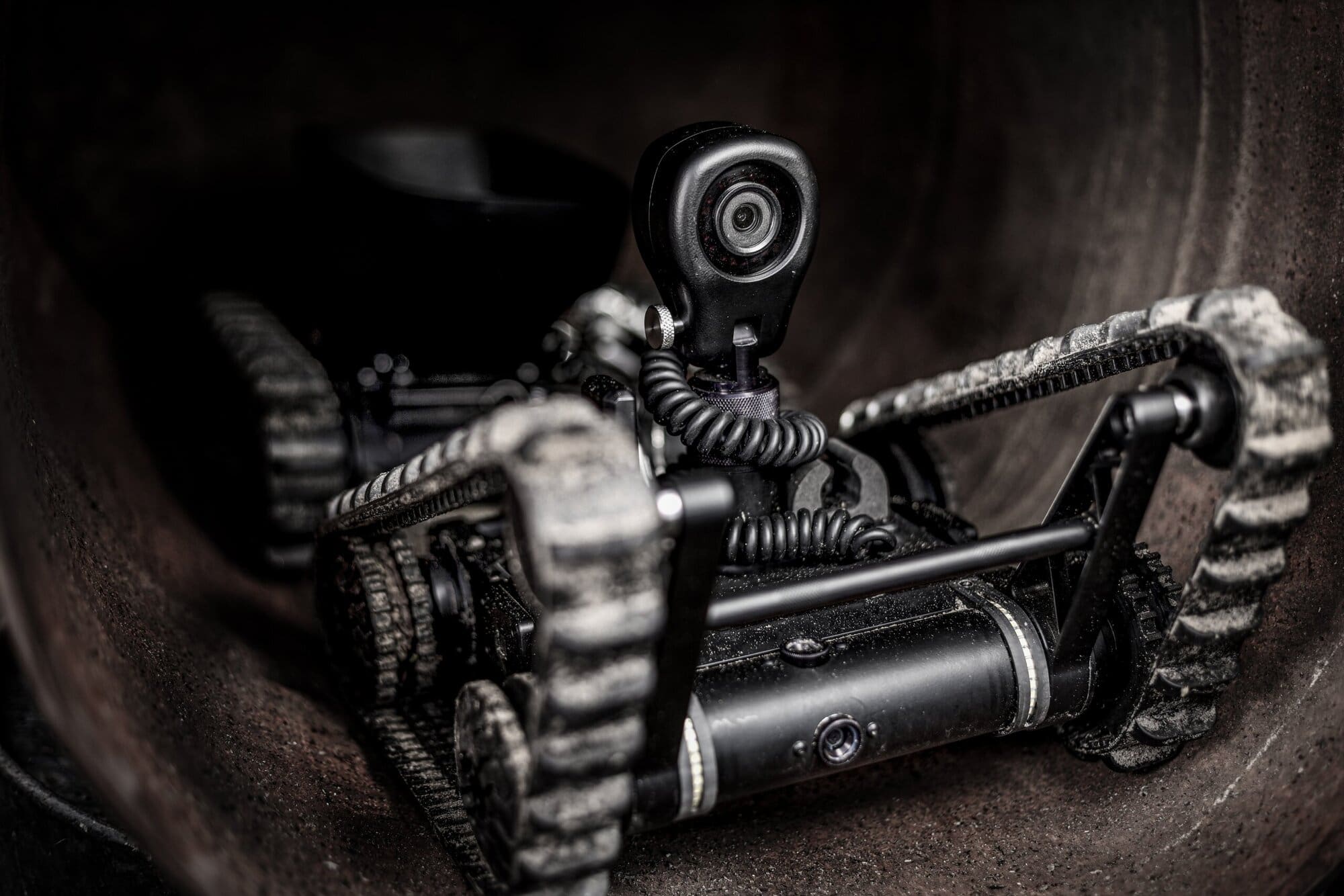
Advanced gas detection and monitoring systems
These are another critical technological development. These systems continuously monitor the atmosphere within confined spaces, detecting the presence of hazardous gases or insufficient oxygen levels. They can alert operators in real time, allowing for immediate action to be taken to mitigate any identified risks. This continuous monitoring ensures that the environment remains safe throughout the entire duration of the work. Internet of Things (IoT) environmental monitoring is a process that uses IoT technology to collect data about the environment, such as air quality, temperature and humidity levels.
This data can then be analysed to better understand the environment and make informed decisions about how to reduce the impact of negative aspects in the environment. In addition, wireless mesh technology embedded within some connected gas monitors enables the instruments to communicate with each other at a peer-to-peer level. Entrants inside the space carrying a gas detector enabled with peer-to-peer connectivity will share their readings with a connected area monitor or personal gas detector stationed with the gas tester or attendant outside the space, allowing them to “see” the readings and monitor the atmosphere through each of the entrants’ instruments.
Workers can respond to emergencies without putting themselves in danger. Smart PPE is being enhanced and developed that will integrate sensors into such things as helmets, or safety vests that monitor vital signs and environmental conditions, and which can trigger alerts for a swift response in the event of an accident, ensuring that workers remain safe and healthy during confined space operations.
Communications
Effective communication is crucial during confined space operations. Technological tools such as wireless communication devices and wearable technology have greatly improved the ability for teams to stay in contact. Workers can now use hands-free communication devices that integrate with their smart personal protective equipment (PPE), allowing for seamless communication with team members and supervisors outside the confined space. Additionally, real-time data sharing through cloud-based platforms enables better coordination and decision-making. Supervisors and safety officers can monitor operations remotely, accessing live data and video feeds. This connectivity ensures that any issues can be promptly addressed, and the overall safety of the operation is maintained.
Data analysis
This is another area where technology has significantly impacted safety in confined space working. By collecting and analysing data from past operations, companies can identify patterns and trends related to safety incidents and operational efficiency. This data-driven approach allows for continuous improvement of confined space entry protocols and procedures. Predictive analytics such as machine learning can also be used to anticipate potential risks based on historical data. By analysing factors such as environmental conditions, equipment performance, and worker behaviour, predictive models can forecast potential hazards and recommend proactive measures to prevent accidents.
Virtual reality (VR) and augmented reality (AR) training
These provide immersive and realistic simulations of confined space environments, and these realistic simulations allow workers to practise entry and emergency response procedures in a controlled, risk-free setting. This technology is revolutionising the training and preparedness of workers involved in confined space entry and working. Through VR and AR, trainees can experience various scenarios they might encounter in real-life confined spaces.
This hands-on approach enhances their understanding of potential hazards and the correct procedures to follow, improving their readiness and confidence when entering and working in confined spaces. One of AR’s major advantages in safety training is its ability to provide immediate feedback and assessment, helping trainees learn and improve in real time. AR systems can monitor user performance during simulations and offer instant corrections or suggestions, which is especially valuable in time-sensitive or hazardous situations. Augmented reality (AR) significantly reduces human error by offering clear, step-by-step instructions during training and it can also be used in real-life work situations providing real-time, hands-free guidance and instructions ensuring that workers are guided through each task in real time.
Benefits of Technological Innovations in Confined Space Work
Technological innovations are providing numerous benefits to all types of industries whose workers are involved in working in confined spaces. These include:
Enhanced safety
Technologies such as drones, robotics and remote sensors can inspect confined spaces without requiring workers to enter, reducing direct exposure to dangerous environments. IoT-enabled gas detectors and environmental monitoring systems provide continuous, real-time data on gas levels, temperature, humidity, and other hazardous conditions. This significantly reduces the risk of accidents due to changing environmental factors that might not be detected using more traditional methods. Workers’ health can be monitored using wearable smart technology offering immediate alerts if a worker’s health and/or safety is compromised. This enables faster interventions and rescue in emergency situations.
Fast emergency response
Confined space operations can be remotely monitored using advanced technologies such as IoT devices, reducing the time it takes to recognise hazards and for alerting rescue teams, enabling an immediate response if an emergency arises. Advanced technology communication tools such as two-way radios with integrated sensors, wearable devices, and automated alarm systems provide instant alerts in case of dangerous conditions, enabling supervisors and emergency teams to respond more quickly.
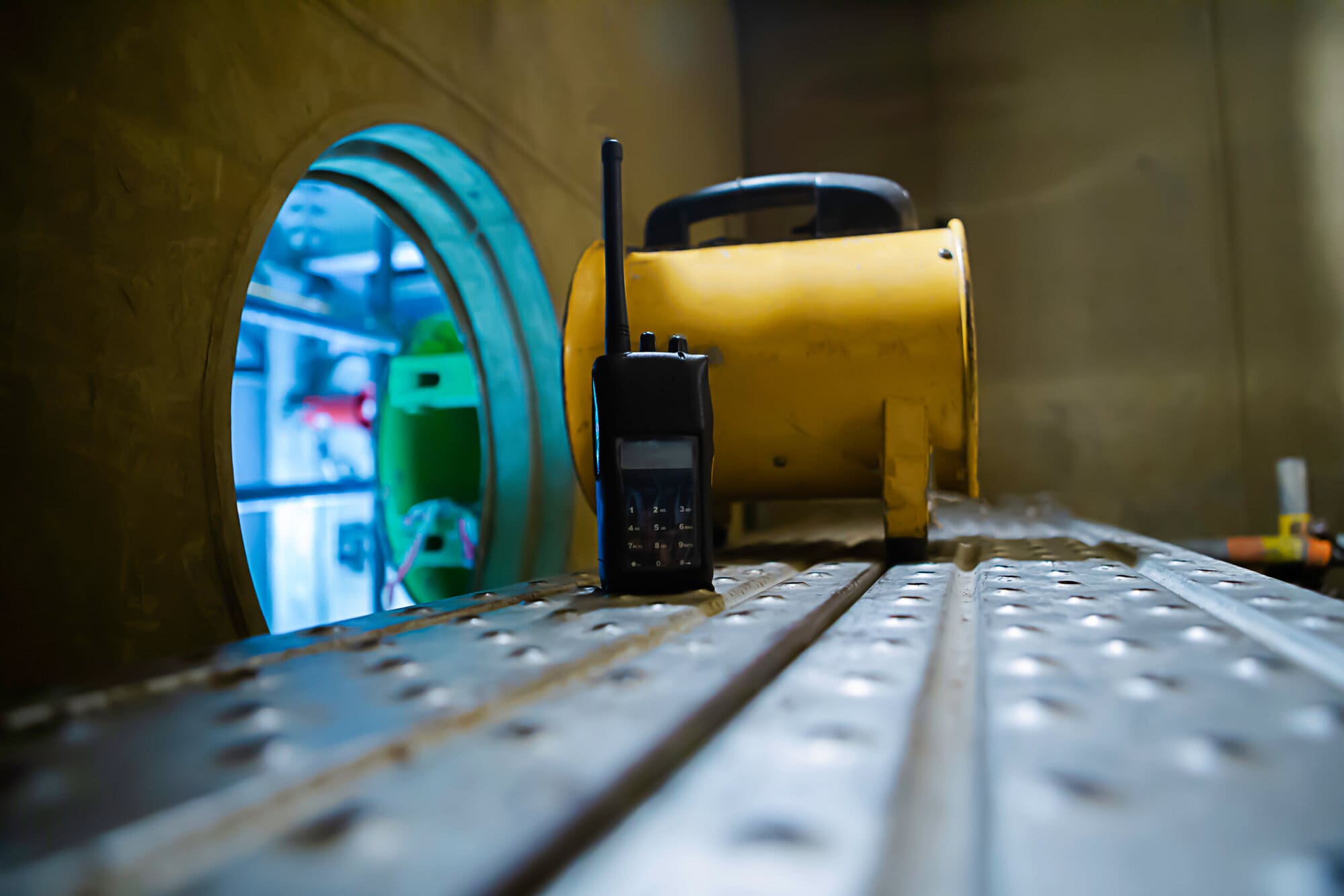
Increased efficiency
Routine inspections can be carried out by drones, robots and remote sensors, which speeds up the process, minimising downtime, and is also far more accurate than human inspections. The results of inspections can be used to monitor and inform future activities and decision-making. Digital platforms can be used to integrate safety monitoring with task management systems allowing for better coordination and planning of confined space work, optimising workflow and reducing unnecessary delays. Digital tools for confined space monitoring generate large amounts of data, which can be analysed to predict when conditions will become unsafe, and can help to inform risk assessments and to improve safety protocols.
Cost savings
Real-time monitoring allows for proactive maintenance and detection of issues before they become critical, preventing unplanned downtimes and costly disruptions to operations. As technology evolves, new tools can be easily integrated into existing safety systems, allowing companies to scale their safety measures in response to any changing operational demands or regulatory updates. Accident mitigation and reduction may also be reflected in reduced insurance premiums.
Regulatory compliance
Record keeping and administration can be both labour intensive and prone to inaccuracies. Technology automatically logs all entry and environmental monitoring data, ensuring accurate and up-to-date records are kept and easily available for HSE inspections and legislative compliance.
Case Studies or Examples of Technology Implementation
A report in the New Civil Engineer highlights the implementation by Scottish Water of state-of-the-art drones and lasers to improve its sewer network.
The hi-tech drones have been adapted for use in the waste water industry and are deployed to survey the sewers for potential problems, often flying to parts of the network that humans can’t reach. The initiative is a collaboration between Scottish Water, its alliance partner Caledonia Water Alliance (CWA), civil engineering trenchless specialist Environmental Techniques and drone manufacturer Good Friday Robotics.
Scottish Water has been able to reduce a job that normally takes a team of 15 to just two operatives using the drone and Light Detection and Ranging (LiDAR) scanning and measurement techniques, effectively replacing workers in dangerous underground conditions. This will also reduce carbon emissions from sewer surveys by as much as 80% by not using any plant and people resources unnecessarily.
Light Detection and Ranging (LiDAR) is a laser scanning tool that measures distances and the associated software creates an accurate computerised 3D point field output which can be viewed on-screen. The drone carries the LiDAR and camera on board as it flies inside the pipe. A worker controls or pilots the drone as it flies along the pipe and uses video for visual inspection and LiDAR for measurement. The outputs are then manually reviewed by operators to spot and code the defects, enabling more accurate assessments of sewer conditions.
Drones, when adapted for sewer surveys, can access parts of the network that are inaccessible to humans, thereby enhancing the accuracy of surveys. They reduce the need for human entry, which improves safety and mitigates the impact of factors like depth, flows, and debris on survey speed.
Employee training is one of the areas that is benefiting the most from the immersive revolution. BP uses virtual reality to train its employees in start-up and emergency exit procedures at its oil refinery in Hull, England. BP needed to train workers on how to safely enter and operate in confined spaces, such as refineries and pipelines, so they partnered with software company Immerse to create a series of new virtual reality training courses that give employees a safe place to practise their skills, no matter where they are located, reducing associated training costs.
The implementation of augmented reality (AR) training at BP has made the training more engaging and memorable, leading to better retention of safety protocols. Workers can practise responding to emergencies and navigating confined spaces without being exposed to actual risks.
By leveraging and successfully implementing advanced technologies such as drones and AR training, Scottish Water and BP have improved safety, reduced operational costs, and enhanced overall efficiency.
Future Trends and Predictions for Confined Space Technology
Technology has come a long way in recent years and continues to advance, bringing improvements to processes and safety at work. One of the great challenges facing robotics today is to improve work environments and achieve safe environments. In general, the automation of industrial processes such as working in confined spaces allows operators to work more safely, improves working conditions and removes them from hazardous environments.
Collaborative robots can take on tasks that are potentially dangerous and put people at risk, such as in confined space working. Robots can carry out repetitive and dangerous tasks, which cannot be carried out by humans or that involve high risk. They also allow workers to perform tasks within limited space or in extreme environments. There are still many challenges in dangerous environments that generate the need to be automated, or to be done autonomously due to the risk they entail. For this reason, robotic systems are being developed, both fully autonomous and tele-operated.
In many sectors such as energy or utilities where work is carried out in hazardous environments, such as in confined spaces, it is necessary to carry out repairs and maintenance with tasks that are a potential danger to workers. Operations must be carried out in hard-to-reach places that cannot be or are dangerous to be accessed by people. For this, autonomous robots with very diverse configurations that are able to move in dangerous environments and carry out tasks that would be a risk for workers are being introduced. These robots are capable of performing repair and maintenance tasks with a high degree of precision and flexibility.
One of the most famous developments of this type is Spot, the robotic dog from Boston Dynamics, which has already been used in real environments. Spot is designed to be used in potentially hazardous environments, such as conducting inspections at pump alert locations or detecting a chemical gas leak.
The adoption of AI-based solutions for confined space monitoring represents a significant advancement in industrial safety across the construction, manufacturing, oil and gas and mining sectors. By providing continuous, real-time surveillance, predictive analytics, and data-driven insights, AI enhances the ability to detect and respond to hazards, ensuring a safer working environment. Embracing AI technology will be essential to meet the growing demands for safety, efficiency and compliance in sectors where confined working is employed.
AI safety systems use real-time video monitoring that leverage high-definition cameras to provide continuous real-time video monitoring of confined spaces. These cameras can be strategically placed to cover all critical areas, ensuring that no blind spots exist. AI-powered analytics continuously process the video feeds to detect anomalies, such as PPE compliance, unusual worker behaviour, unauthorised entry, or environmental monitoring such as smoke or gas leaks. The systems can instantly alert safety personnel to potential hazards, allowing for swift action to prevent accidents by employing AI-powered safety monitoring systems with automated incident analysis and reporting.
These AI safety systems also enhance communication between workers in confined spaces and their supervisors. With real-time audio and video communication capabilities, workers can easily report issues or request assistance.
Earlier we mentioned that smart wearable technology is being developed to integrate with AI monitoring systems. These smart wearables are equipped with sensors to monitor vital signs such as heart rate, body temperature, and oxygen levels. If any readings indicate distress or unsafe conditions, the system can automatically raise an alert. This proactive approach ensures that workers are continuously monitored for health and safety, even in the most hazardous conditions. 5G technology will enable faster, more reliable data transmission from IoT devices in confined spaces. This will support the deployment of more connected sensors and wearables, ensuring real-time monitoring and communication between workers and safety teams.
Employee safety is a top priority for any organisation, which is why innovation in training methods for those working in confined spaces is so important. Immersive virtual environments offer new and exciting ways to train employees on safety procedures. By simulating real-life scenarios, employees can practise and learn in a safe and engaging environment.
Immersive virtual environments are computer-generated simulations that provide a realistic and interactive experience for the user. These environments can be accessed through virtual reality headsets or on a computer screen. They are designed to simulate real-life scenarios and allow users to interact with objects and people in the virtual world. Immersive virtual environments are being used in a variety of industries, particularly those whose work involves confined spaces for employee safety training.
One of the main concerns for organisations is the cost of implementing this technology, as it can require significant investment in hardware, software and training. However, as the technology evolves, costs are reducing, making the technology more accessible to a wider range of employers.
AR remote assistance is a cutting-edge technology that enables remote collaboration between experts and technicians using augmented reality (AR) tools. With AR remote assistance, a worker or technician at a physical location can receive guidance from an expert located elsewhere, without the need for the expert to be physically present. Teams can perform the task on dangerous equipment without putting workers’ lives in danger, and technicians can now successfully maintain machines they have never used before.
AR remote assistance helps to overcome on-site issues and get accurate and assertive instructions in real time. They can capture the content of images and recordings from service sessions while consulting with an expert. This saves lots of time, as well as fixing technical issues.
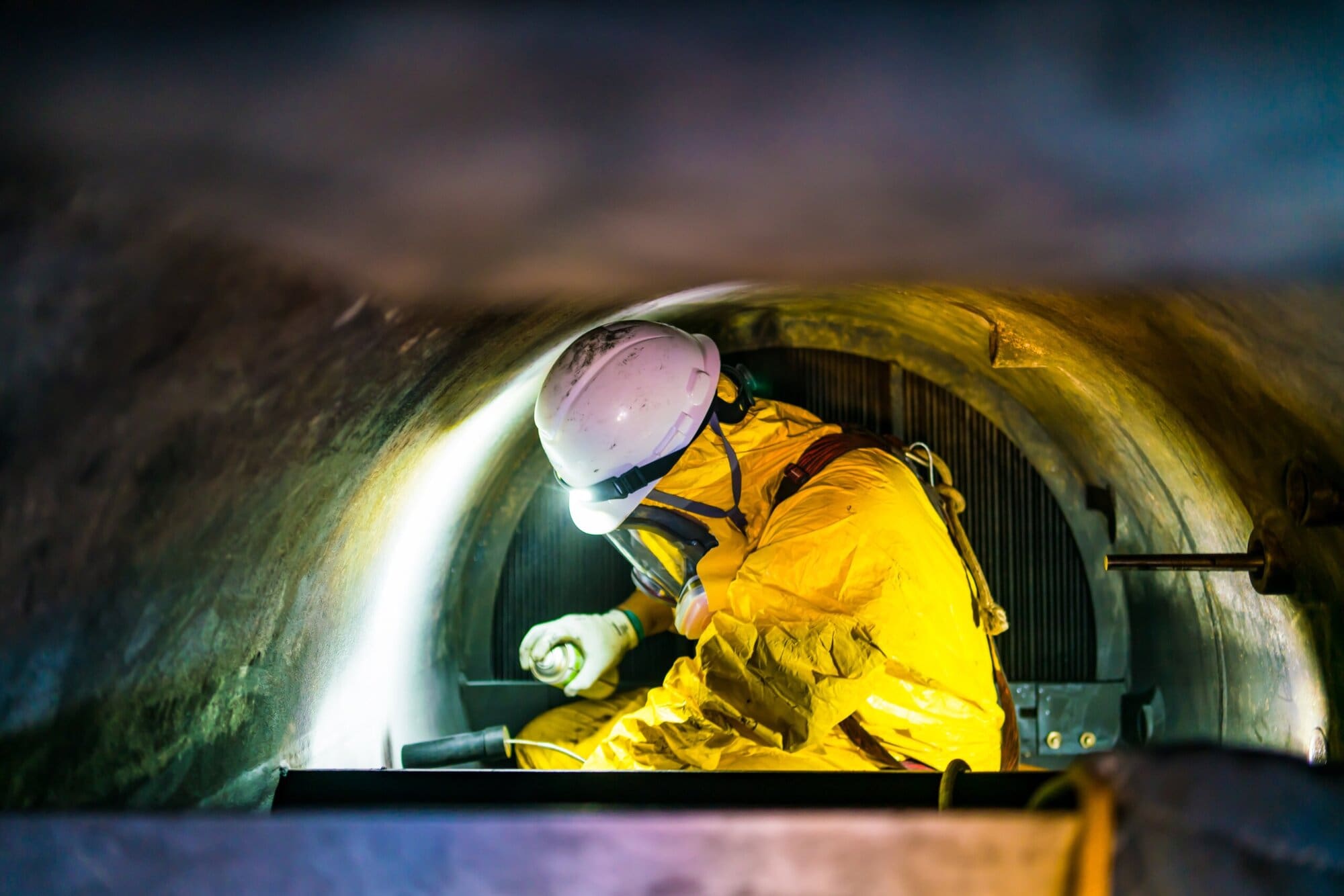
AR remote assistance makes it possible to collaborate with multiple users and receive or impart assistance to the worker, resulting in better decision-making. It helps quick and direct knowledge transfer between experts and workers.
Conclusion
The use of technology to improve safety systems and manage risk information is becoming more relevant and integrated than ever before. AI, IoT, drones, robotics, and virtual and augmented reality are already significantly enhancing safety and efficiency in industries that work in confined spaces. Training using immersive virtual and/or augmented reality or utilising drones and robotics are some of the most efficient ways of improving workplace safety. AI sensors, detectors and workers’ well-being tracking wearables not only contribute to workers’ safety and welfare, but they also improve efficiency by, for example, minimising downtimes.
However, the uses of some of these technologies are still in their infancy in the environments of heavy industries, and this may pose additional requirements to the technologies. For example, they need to be durable and usable in a wide variety of conditions from the deepest of mines to the highest of constructions and oil rigs, and they must comply with all statutory rules and regulations.
There are also still some significant barriers to workplace safety technology implementation across industries whose work involves working in confined spaces. Many lack information about the various technologies, including difficulties in finding information about companies that are successfully using these technologies. Also, costs can be a barrier to some businesses.
The case studies detailed in this article highlight how technologies such as remote confined space monitoring and immersive augmented reality training have emerged as safe, efficient, compliant, and cost-effective technological advancements for minimising hazards in these dangerous environments.
Integrating new technologies into workplace safety protocols is not just about compliance, but about creating an environment where workers feel valued and protected. Employers that embrace these technologies are seeing a positive shift in worker morale and engagement, and a decline in workplace accidents and emergency situations.