In this article
People are killed or seriously injured in the UK each year working in confined spaces across a range of industries, including mining, sewage and working on the docks. Those killed in accidents include people working within the confined space and those people attempting a rescue operation from confined spaces without the proper equipment or training.
A confined space is a specific type of work environment with distinct characteristics that pose unique challenges and hazards to workers. The defining characteristics of a confined space include:
- Limited entry and exit points – confined spaces have restricted means for entry and exit, which can complicate emergency escape and rescue operations. These limited openings may require special entry and exit procedures, often involving ladders or narrow passages.
- Inadequate ventilation – the natural ventilation in confined spaces is often poor, leading to the potential accumulation of hazardous substances. This lack of adequate airflow can cause dangerous atmospheres due to the build-up of toxic gases, lack of oxygen, or flammable vapours.
- Potential atmospheric hazards – confined spaces can contain or produce hazardous atmospheres, which may include oxygen deficiency. These are oxygen levels below 19.5%, which can impair physical and mental functioning and can be fatal. Oxygen enrichment is oxygen levels which are above 23.5%, which can increase the risk of fire and explosion. Toxic gases and vapours include the presence of substances such as carbon monoxide, hydrogen sulphide, or other chemicals that can cause poisoning or respiratory problems. Flammable gases and vapours include the presence of substances that can create a risk of explosion or fire.
- Not designed for continuous occupancy – these spaces are not intended for continuous worker occupancy. They are usually designed for occasional access for maintenance, repair, cleaning, inspection or similar activities.
Confined spaces may contain other hazards such as unguarded machinery, exposed live wires, extreme temperatures, or loose materials that can pose risks to workers.
Examples of confined spaces include:
- Storage tanks – including chemical tanks, water tanks and fuel tanks.
- Vessels – pressure vessels, reactors and boilers.
- Ducts and HVAC (heating, ventilation and air conditioning) systems – including air ducts and exhaust ducts.
- Pipelines – sewage pipes, water pipes and gas pipelines.
- Vaults – including electrical vaults and utility vaults.
- Crawl spaces – these are areas under floors or in attics.
- Hoppers – these are used in industrial processes for holding and dispensing materials.
- Utility tunnels – underground tunnels for utilities such as steam, water or electrical lines.
- Bunkers – storage bunkers for materials like coal, sand or grains.
- Septic tanks – used for waste disposal.
- Boiler rooms – rooms where boilers are housed, often cramped and poorly ventilated.
- Ship holds – cargo holds in ships.
- Trenches – deep excavations for laying pipes and cables.
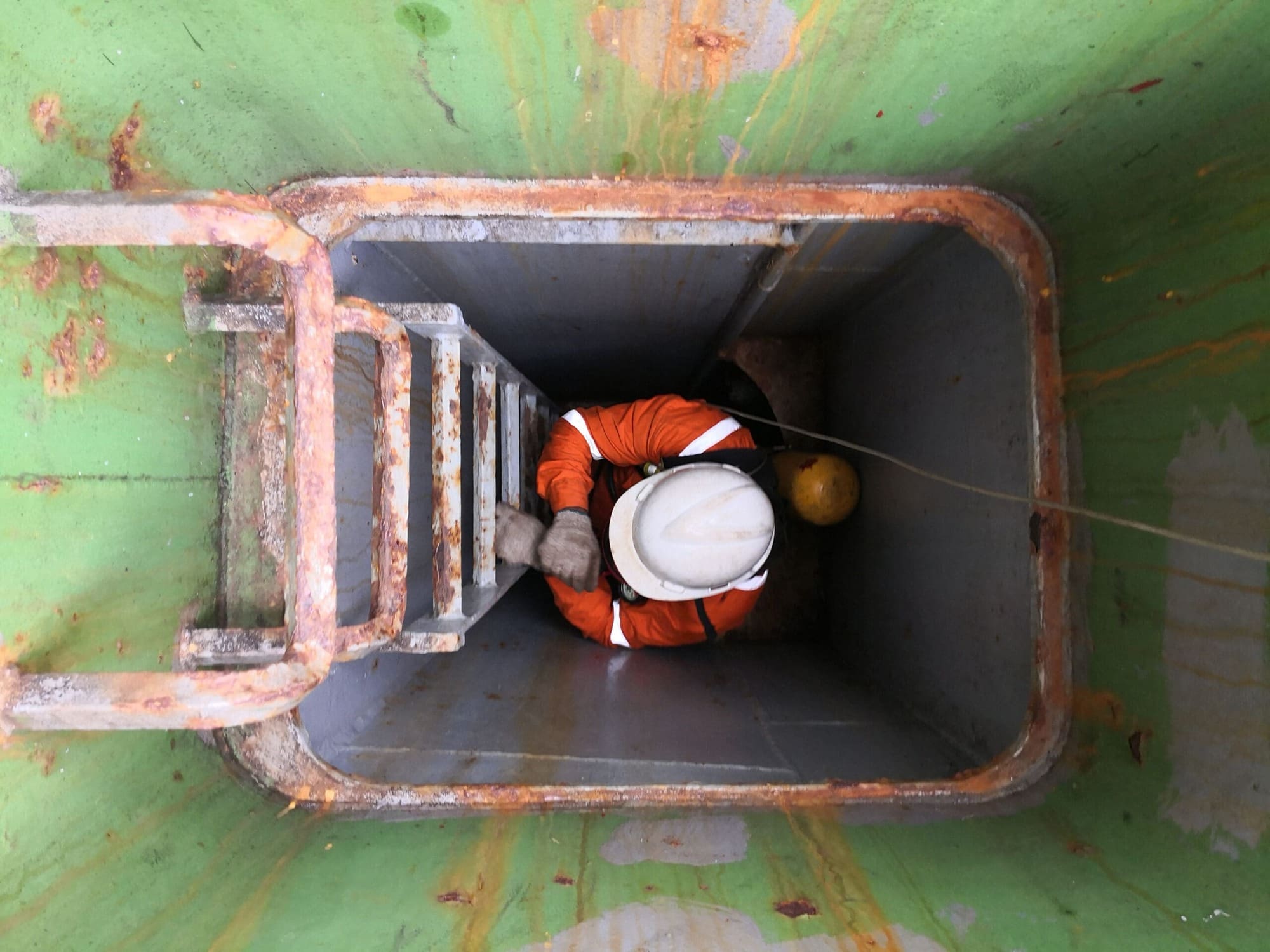
Confined spaces are among the most challenging and hazardous environments in the industrial world and require not only rigorous safety protocols but also advanced equipment designed to meet the unique demands of these high-risk areas. Innovations in confined space safety equipment have transformed how industries approach these environments, incorporating cutting-edge technology to enhance monitoring, communication and personal protection.
From sophisticated air quality sensors and real-time monitoring systems to wearable tech and improved rescue gear, these innovations aim to minimise risks and respond swiftly to emergencies. This exploration of new developments in confined space safety equipment highlights the critical technologies and strategies that are setting new standards for worker protection, efficiency and compliance in industries worldwide. As confined spaces continue to present complex safety challenges, these innovations along with effective risk assessments are paving the way for safer, smarter and more responsive approaches to managing confined space operations.
The Need for Innovation in Confined Space Safety
Confined spaces present numerous risks and hazards that can endanger the health and safety of individuals working within them. These hazards can be broadly categorised into atmospheric, physical and psychological hazards. Understanding these risks is crucial for effective safety management and prevention measures.
Atmospheric hazards
Oxygen deficiency can result from the consumption of oxygen by chemical reactions, e.g. rusting, displacement by other gases, or biological processes such as fermentation. Symptoms of oxygen deficiency include dizziness, shortness of breath, confusion, loss of consciousness and, in severe cases, death. Also, exposure to toxic gases can cause a range of health issues from mild irritation to severe poisoning, respiratory failure and death.
Hydrogen sulphide, for instance, can cause rapid unconsciousness and death at high concentrations. Other toxic gases include hydrogen sulphide, carbon monoxide, ammonia and methane. Flammable vapours can form explosive mixtures with air, posing fire and explosion risks. A spark or static discharge can ignite these vapours, leading to catastrophic consequences. Flammable vapours include methane, propane and gasoline vapours.
Physical hazards
Engulfment can occur in environments like grain bins, sand, gravel, or other loose materials. Engulfment can lead to suffocation, crushing injuries, and death as the individual is buried and pressure from the material prevents breathing. Entrapment occurs when a person is trapped in machinery, between objects, or in narrow passages. It can result in injuries or death due to compression, inability to escape, or delays in rescue efforts. Slippery surfaces, unguarded edges, uneven flooring, and the confined nature itself can cause people to have falls. Falls can lead to fractures, head injuries and other serious trauma. The confined space complicates rescue operations, increasing the risk of prolonged entrapment and further injury.
Psychological hazards
These include claustrophobia which is a fear of confined or enclosed spaces. Individuals may experience intense anxiety, panic attacks, sweating, rapid heartbeat and difficulty breathing. This can impair their ability to function safely and effectively within the space. Panic can be triggered by the confined nature of the space, lack of visibility or a sudden hazardous event, e.g. gas release or equipment failure. Panic can lead to irrational behaviour, compromised decision-making, and potentially exacerbate the situation. In extreme cases, it can cause the person to hyperventilate, freeze or attempt dangerous escape manoeuvres.
Safety equipment is vital in minimising these risks, reducing accident rates, and ensuring compliance with strict safety regulations like OSHA in the United States and HSE in the UK. Essential safety equipment includes:
- Gas detection devices – portable gas monitors and fixed sensors continuously check air quality, detecting hazardous gases and low oxygen levels, allowing workers to respond before a situation becomes life-threatening.
- Personal Protective Equipment (PPE) – respirators, helmets, gloves and protective clothing shield workers from harmful chemicals, dust and physical impacts, providing crucial layers of protection.
- Ventilation and exhaust systems – ventilation systems help circulate fresh air, diluting harmful substances and maintaining safe oxygen levels within confined spaces. These systems are essential to prevent the build-up of toxic or explosive gases.
- Rescue equipment and emergency communication tools – rescue harnesses, tripods and communication devices enable safe evacuation in emergencies and facilitate timely communication between confined space workers and supervisors outside the confined area.
- Compliance and monitoring technology – modern compliance tools and safety management systems help organisations track real-time data and adhere to safety regulations, reducing the likelihood of accidents and ensuring adherence to global standards.
The confined space safety landscape is rapidly evolving as new safety regulations, advanced technology and heightened worker safety demands drive innovation. Key drivers include:
- Stricter safety regulations – regulatory bodies are constantly updating safety standards in response to incident data and technological advancements. Regulations require companies to adopt newer, more effective safety measures, motivating continuous improvements in equipment and protocols.
- Advances in technology – innovations in robotics, Internet of Things (IoT) and artificial intelligence (AI) are transforming safety. For example, remote-controlled drones and robotic inspection devices are increasingly used to assess confined spaces before workers enter, minimising human exposure to hazards. Similarly, IoT-enabled gas monitors and wearable devices track air quality and worker location, enabling real-time monitoring and early warnings.
- Demand for worker safety and accountability – as companies prioritise worker safety and seek to attract talent, there’s greater demand for innovative, proactive safety solutions. Modern workers are more aware of their rights and the safety risks they face, driving companies to adopt better safety practices and technology.
- Focus on real-time data and predictive analytics – innovations in data collection and analytics allow companies to predict and mitigate risks before they occur. For example, historical data can identify patterns of hazards, enabling proactive safety planning and reducing incidents in confined spaces.
- Automation and remote monitoring – new technologies allow for remote inspection and monitoring of confined spaces, reducing the need for workers to physically enter these hazardous environments. Robots, cameras and remote sensors can perform inspections, drastically reducing exposure to danger.
Innovation in confined space safety is essential to meet the demands of modern industries and ensure worker safety. By understanding the inherent risks, utilising advanced safety equipment, and embracing cutting-edge technology, companies can mitigate hazards, comply with regulations, and prioritise the wellbeing of their workforce. With continuous advancements in technology and stricter regulations, the future of confined space safety will likely see even greater improvements in risk management and worker protection.
Latest Innovations in Confined Space Safety Equipment
Recent advancements in safety technologies have significantly improved the protection and monitoring capabilities available to those working in these environments. Key innovations include:
Advanced Gas Detection Systems
Modern multi-gas detectors have evolved to offer real-time monitoring of several critical gases, including oxygen (O₂), carbon monoxide (CO), hydrogen sulphide (H₂S) and combustible gases. These detectors use advanced sensor technology to provide continuous readings, enabling quick identification of hazardous gas levels and alerting workers instantly to any dangerous fluctuations. The detectors are now equipped with digital displays and user-friendly interfaces, allowing workers to easily read and understand gas levels in real time.
Wireless-enabled gas detection systems now allow safety officers to monitor confined space environments remotely, reducing the need for physical presence in potentially hazardous spaces. These systems transmit data wirelessly to central monitoring stations or mobile devices, allowing for real-time supervision from a safe distance. This innovation not only enhances safety but also supports quicker response times in the event of an emergency.
Wearable gas detection devices have become more compact and versatile, incorporating personal health monitoring functions alongside air quality measurements. These sensors continuously monitor vital signs, such as heart rate and temperature, while also detecting harmful gases in the vicinity. They are often connected to smartphones or monitoring software that can send alerts to workers and supervisors if dangerous conditions arise, enhancing situational awareness and enabling timely evacuations.
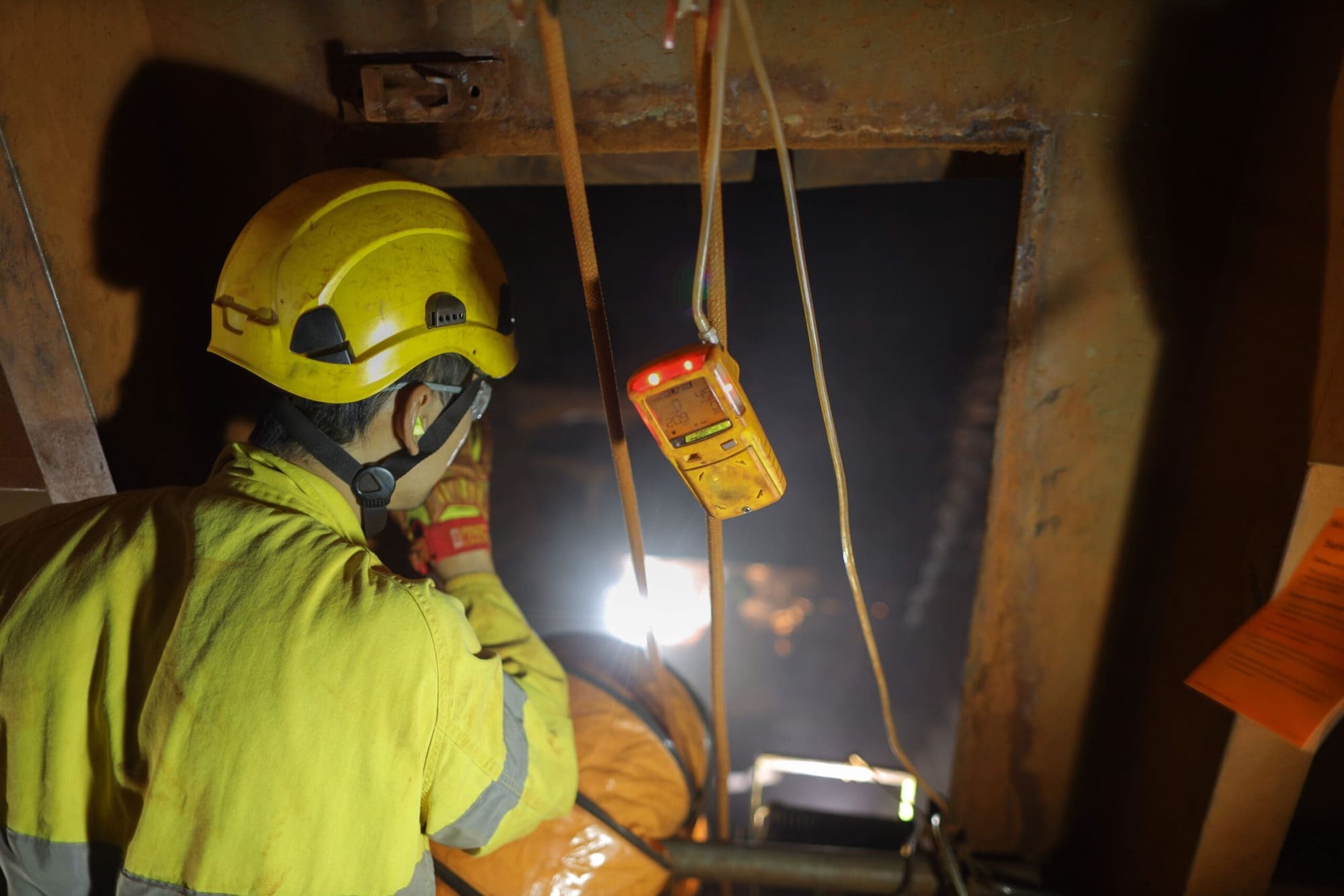
Robotics and Drones for Remote Inspections
Robotics technology has introduced inspection robots that can be remotely operated to enter confined spaces, reducing the need for workers to be physically present in potentially dangerous areas. These robots are equipped with sensors, cameras and manipulators, allowing them to assess conditions, measure gas levels and even perform certain tasks. This minimises human exposure to hazards and streamlines inspection processes.
Drones equipped with high-definition cameras and sensors are increasingly used for confined space inspections. Their small size and agility allow them to access hard-to-reach or narrow areas, providing live video feeds and collecting environmental data without risking human safety. This innovation is particularly useful in large industrial sites, such as tanks, silos and sewers, where manual inspection would be challenging and hazardous.
Confined Space Entry Monitoring Systems
Entry monitoring systems now use wireless communication and cloud-based platforms to track worker location, movement, health metrics and environmental data in real time. These connected systems enable safety managers to monitor multiple confined spaces simultaneously, making it possible to assess workers’ wellbeing continuously and respond quickly to any concerning trends or sudden health changes.
‘Man-down’ detection systems are designed to automatically detect when a worker becomes motionless or is in distress, immediately sending alerts to supervisors and triggering alarm systems. Automated rescue mechanisms, such as remotely activated retrieval winches, have also been developed to facilitate rapid extraction of a worker in emergencies, minimising the time between an incident and rescue.
Personal Protective Equipment (PPE) Enhancements
Smart helmets have been introduced, integrating features such as cameras, sensors and communication tools to provide workers with improved visibility and connectivity in confined spaces. Equipped with real-time video capabilities and environmental sensors, these helmets allow workers to stay connected with supervisors, who can monitor conditions and provide guidance remotely. Enhanced lighting and augmented reality (AR) functionalities are also incorporated to improve visibility and situational awareness.
Respirators have become lighter and more ergonomically designed, allowing workers greater mobility and comfort without compromising on protection. Advanced materials and filters provide effective protection against toxic gases and particulates, while being more breathable and less obtrusive. This evolution in respirator technology supports extended wear and reduces worker fatigue.
New fall arrest and protection harnesses offer superior support, comfort and flexibility, which are essential for workers navigating vertical or inclined confined spaces. These systems often include built-in suspension relief straps and padded harnesses to minimise the impact of extended use, improving both safety and comfort for workers operating at heights or in awkward positions.
Ventilation and Air Purification Systems
Portable ventilation units have been enhanced for greater efficiency and ease of use, effectively circulating fresh air and reducing the concentration of hazardous gases in confined spaces. These units are designed to be lightweight and easy to transport, allowing for flexible deployment. With better airflow management, they can maintain safer conditions by removing stagnant air and replenishing oxygen levels.
Innovative Air Purifiers and Scrubbers
Advanced air purifiers and gas scrubbers have been introduced to confined space safety equipment, offering the ability to filter out dangerous particulates and remove toxic gases from the environment. These systems use advanced filtration and chemical absorption techniques to purify the air, reducing the exposure risk for workers and improving overall air quality. Some models are portable and battery-operated, enabling flexible placement in confined spaces without the need for continuous external power sources.
Benefits of These Innovations
Confined spaces present unique risks that require specialised safety equipment and procedures. Advances in technology have made confined space operations safer, more efficient and cost-effective. Below are some of the key benefits of the latest innovations in confined space safety equipment.
Real-time monitoring technology in confined space safety equipment, especially through advanced data and gas detection systems, has transformed how companies manage risks. Devices can now detect hazardous gases, changes in air quality and other potential dangers in real time, allowing workers and supervisors to respond to issues immediately. This immediate feedback loop reduces response times drastically, which is critical in emergencies, helping mitigate injuries and potentially save lives.
Human error is one of the most common causes of accidents in confined spaces, often due to stress, fatigue or limited visibility. Automated systems and robotics can significantly reduce these risks by handling repetitive, hazardous or complex tasks with precision. For example, robotic devices can perform inspections or repairs, ensuring a level of accuracy that reduces the chance of oversight or mistakes. This automation not only improves safety but also allows human workers to focus on oversight and analysis rather than direct exposure to risks.
The introduction of drones, robots and remote-controlled equipment into confined space operations has significantly reduced downtime associated with manual inspections and repairs. Drones can inspect hard-to-reach areas, identify potential hazards, and gather data faster than humans could with conventional methods. This minimises the need for complete shutdowns, as robots can often operate without disrupting other activities, ensuring continuous productivity and minimising time losses.
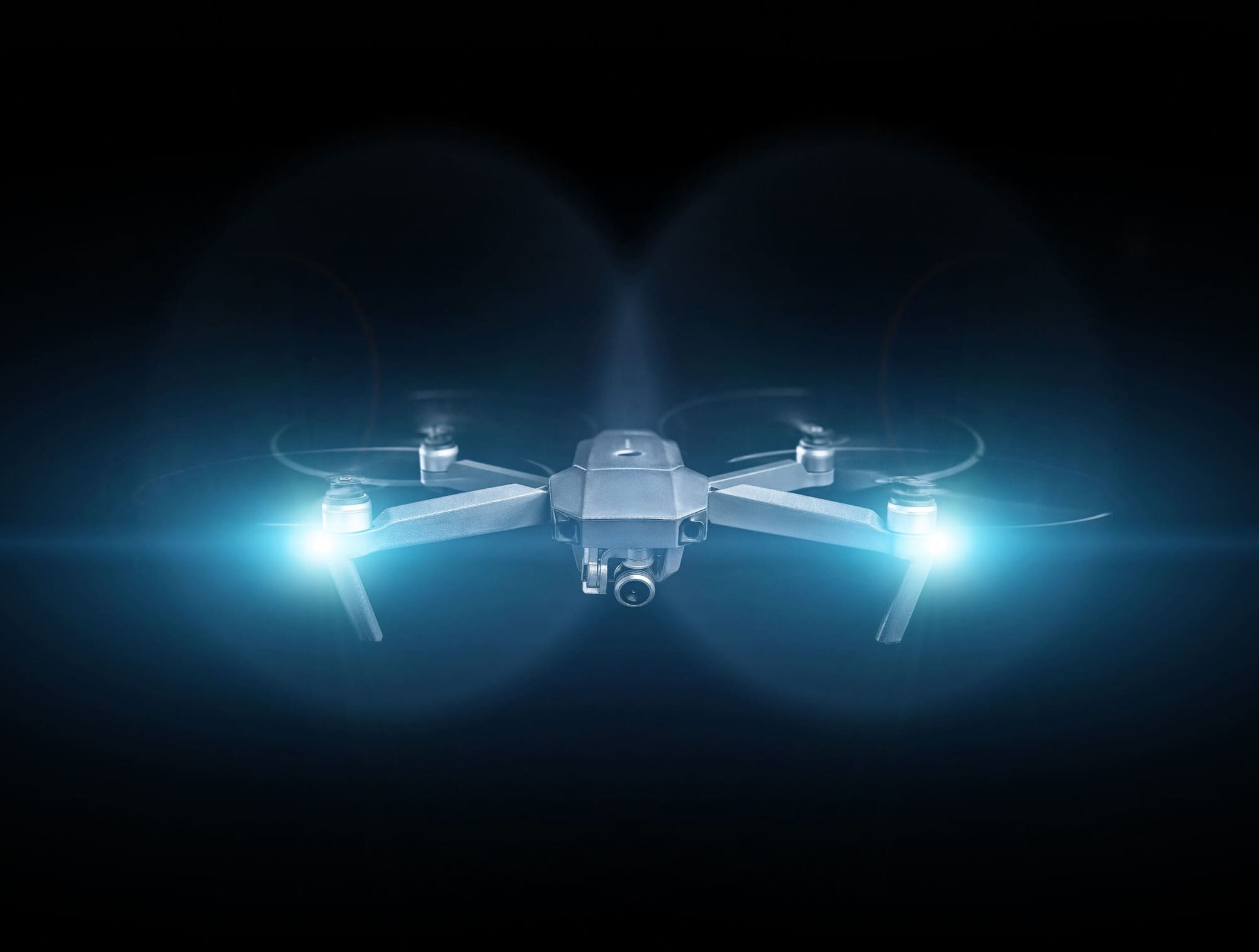
Compliance with safety regulations is essential but can be complex. Modern confined space safety equipment is now designed with built-in compliance features, including automated data logging, inspection checklists, and pre-installed alerts for regulatory thresholds. This allows companies to easily meet safety standards, as they can quickly document and verify adherence to industry regulations. Equipment with built-in compliance also reduces the need for extensive safety audits, saving both time and resources.
Fewer accidents and incidents mean significant financial savings for companies. When accidents are minimised, companies avoid the associated costs of medical expenses, legal fees, insurance premiums and lost productivity. With advanced safety equipment that detects and mitigates risks, businesses can maintain a safer working environment, ultimately resulting in lower costs related to employee health and accident liability.
Innovations in durable and reliable equipment designed specifically for confined spaces lead to lower maintenance and replacement costs. High-quality robotics, sensors and monitoring devices are built to withstand harsh conditions, reducing the need for frequent repairs or replacements. This durability translates to longer service life for safety equipment, reducing ongoing maintenance expenses and providing a better return on investment over time.
The latest innovations in confined space safety equipment provide substantial benefits across safety, efficiency and cost savings. From real-time monitoring and automation to compliance-focused designs, these advancements support safer operations, improved productivity and financial benefits for companies. Investing in these new technologies not only helps companies remain compliant and efficient but also enhances worker safety and reduces operational risks.
Regulations and Standards Impacting Safety Equipment
When it comes to confined space safety equipment, regulations and standards play a crucial role in guiding the requirements for design, implementation and usage to ensure worker safety. Here’s a breakdown of key regulatory frameworks and standards that influence confined space safety equipment:
In the United States, the Occupational Safety and Health Administration (OSHA) sets regulations for permit-required confined spaces. OSHA’s standard, 29 CFR 1910.146, applies to industries outside of construction and establishes requirements to protect workers from hazards such as toxic atmospheres, engulfment and oxygen deficiency. OSHA mandates that employers implement a written programme for confined spaces, which includes testing the atmosphere, providing continuous monitoring, having a rescue plan in place, and ensuring adequate ventilation. Safety equipment must include gas detection devices, fall protection, ventilation systems and retrieval devices. OSHA also addresses confined space safety in the construction sector under 29 CFR 1926 Subpart AA. This standard emphasises the identification of confined spaces and the implementation of a Permit-Required Confined Space (PRCS) programme for any work that may expose workers to confined space hazards in construction. Similar to general industry standards, construction standards require gas detection, monitoring, ventilation and retrieval systems for safe entry and exit.
In the United Kingdom, the Health and Safety Executive (HSE) has published the Confined Spaces Regulations 1997, which outline requirements for working safely in confined spaces. The HSE requires companies to assess confined space risks and eliminate entry if possible, with entry only permitted when essential and with comprehensive controls in place. Required safety equipment includes ventilation systems, gas detectors, breathing apparatus and suitable lighting. The HSE advocates a risk-based approach, requiring thorough training, planning and monitoring to prevent confined space incidents.
ISO 45001 is an international standard for occupational health and safety management systems, designed to prevent workplace injuries and ill health. Although it does not focus specifically on confined spaces, it sets a framework that applies to all workplace hazards, including those associated with confined spaces. ISO 45001 encourages organisations to proactively identify, assess and control health and safety risks, which would encompass confined spaces hazards. By following ISO 45001, organisations commit to continuous improvement in safety management practices, which include establishing procedures and controls for confined space entry and using compliant safety equipment like gas detectors, personal protective equipment (PPE) and rescue devices.
The EN 140 and EN 149 standards apply to respiratory protective devices used in confined spaces and other environments where inhalation hazards are present. EN 140 covers requirements for half masks and quarter masks, while EN 149 addresses particle-filtering half masks. These standards ensure that respiratory protection meets performance, filtration and fit requirements, providing adequate protection in confined spaces with limited or hazardous atmospheres.
These standards shape the design and implementation of confined space safety equipment by mandating certain performance specifications, inspection protocols and operational guidelines.
Case Studies and Examples of Successful Equipment Use
Confined space work is common in industries like utilities, water treatment, oil and gas, and construction, where maintenance and repairs must occur in tight, enclosed environments. UK companies are continually seeking innovative equipment and strategies to improve safety and operational efficiency in these high-risk settings. Below are some industry examples and lessons learned from UK companies that have successfully implemented new confined space safety equipment.
Anglian Water: Implementing Robotics for Pipe Inspections
Anglian Water, a large water utility company in the UK, implemented robotic technology for inspecting sewage pipes, which are classified as confined spaces due to limited access, lack of ventilation, and potentially hazardous gases. The company used remote-controlled robots equipped with cameras to inspect ageing infrastructure without needing human entry into the confined space.
It reduced the need for workers to enter confined and hazardous environments, thereby minimising exposure to risks and allowed inspections to be conducted more frequently and quickly, providing real-time data to engineers and preventing potential failures.
The use of robotics highlights the effectiveness of remote-operated solutions in confined spaces, showing that eliminating direct human entry can significantly reduce risk and enhance inspection efficiency.
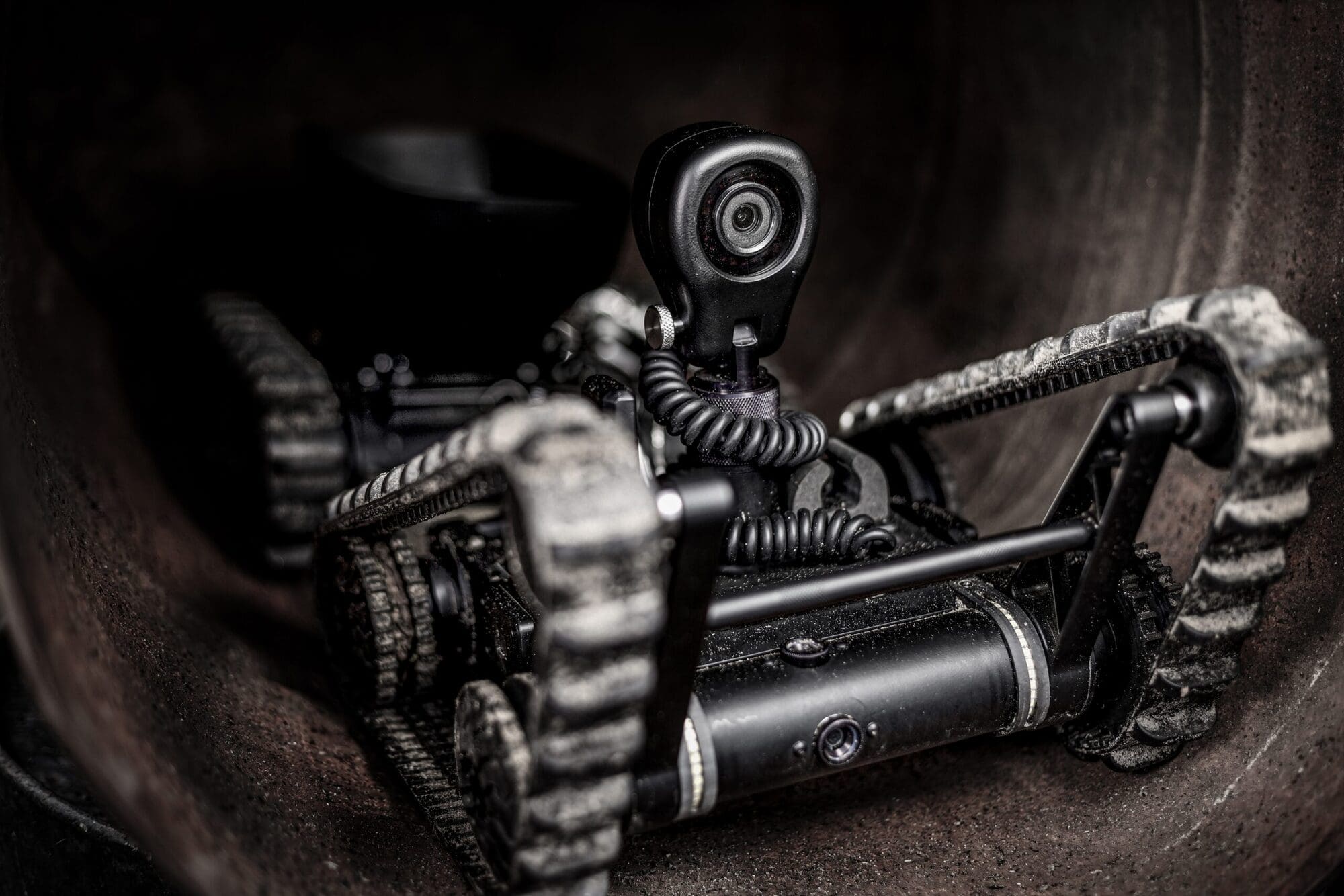
Scottish Power: Utilising Gas Detection Wearables
Scottish Power equipped their maintenance teams with wearable gas detection devices during work in confined transformer rooms and underground spaces. These devices provide real-time monitoring of toxic and combustible gases and alert workers if levels become unsafe.
This improved incident prevention by providing immediate warnings about dangerous gas concentrations, allowing workers to evacuate or take protective measures and reduced downtime by enabling continuous monitoring without needing periodic equipment checks. Workers could focus on their tasks while relying on the device for gas detection.
This case demonstrates the value of wearable technology for real-time monitoring, empowering workers to detect threats early and respond promptly, ultimately reducing the likelihood of accidents in confined spaces.
Network Rail: Confined Space Ventilation Systems
Network Rail adopted portable ventilation systems to improve air quality in confined workspaces such as underground tunnels and maintenance shafts. These systems included high-power fans and air purifiers that maintained a steady airflow, diluting toxic gases and lowering temperature, which is critical for worker safety and comfort.
Enhanced air quality prevented hazardous gas accumulation and kept oxygen levels within safe limits, reducing risks of hypoxia or toxic exposure and the ventilation systems allowed extended work hours in confined spaces by maintaining suitable environmental conditions, thereby improving productivity.
Effective ventilation is essential in confined spaces. Portable ventilation systems show that maintaining optimal air quality can reduce health risks and increase the time workers can safely spend in confined areas, improving overall operational efficiency.
BP: Use of Autonomous Drones for Tank Inspections
BP introduced autonomous drones for the internal inspection of oil storage tanks, a high-risk confined space. Traditionally, workers had to enter tanks to inspect for corrosion, but drones equipped with high-definition cameras and sensors now carry out these inspections autonomously.
This eliminated the need for human entry into tanks, reducing exposure to hazardous conditions such as gas leaks, low oxygen or chemical residues. Drones significantly reduced inspection time from days to hours, allowing more frequent inspections and minimising tank downtime.
This case highlights the potential for autonomous technologies to eliminate the need for human presence in confined spaces, offering a safer, more efficient alternative to traditional inspection methods.
The Future of Confined Space Safety Equipment
The future of confined space safety equipment is set to be reshaped by emerging technologies, innovative equipment and data-driven insights. Advances in technology, particularly in AI, IoT and wearable devices, are poised to significantly enhance safety in these settings. Here’s an in-depth look at technological trends and potential future innovations:
Artificial intelligence and machine learning for predictive safety
- Predicting hazards in real time – AI algorithms, trained on historical data, can predict potential hazards in confined spaces by recognising patterns in environmental data, such as gas levels, temperature or airflow changes, and alerting workers before situations escalate. By learning from prior incidents, machine learning models can identify early warning signs that might go unnoticed by human supervisors.
- Adaptive hazard response – machine learning systems are increasingly being designed to adapt based on specific environmental conditions. For example, if gas levels rise, the AI system can respond by activating ventilation systems or alerting personnel in real time. These adaptive responses can drastically reduce incident response times and help mitigate risks proactively.
Wearable technology for health and environmental monitoring
- Vital sign monitoring – wearables equipped with sensors to monitor vital signs, such as heart rate, oxygen saturation and body temperature, can provide real-time health data on workers in confined spaces. If a worker’s health metrics fall out of safe ranges, automated alerts can trigger, signalling a need for immediate intervention. Wearables can even include stress detection or hydration levels, addressing both physical and mental wellbeing.
- Gas detection and environmental sensors – smart helmets and wearables that include sensors for toxic gas detection and air quality monitoring provide another layer of security. Devices can detect dangerous gas levels, triggering alarms and facilitating evacuation before exposure becomes dangerous.
- Connectivity with emergency systems – wearables connected to IoT systems can communicate with control centres and emergency responders, providing location tracking and environmental data in real time. This connectivity is essential for coordinating fast, informed responses during emergencies.
IoT and real-time data collection
- Connected confined space monitoring systems – IoT-enabled sensors collect and relay environmental data including temperature, humidity and gas levels to central systems that can analyse this information for potential hazards. This data is critical in confined spaces where risks can evolve quickly, providing insights to safety managers in real time.
- Automated ventilation and temperature control – IoT systems can automate essential safety functions like ventilation, reducing human intervention. These systems can adjust airflow or temperature based on data from connected sensors, maintaining safe conditions and adapting quickly to environmental changes.
Enhanced communications systems
- Hands-free communication devices – with voice-activated communication devices, workers in confined spaces can communicate without needing to manually handle equipment, ensuring they remain focused on their tasks while maintaining the ability to reach out for help if necessary.
- Smart radio and Bluetooth-integrated systems – Bluetooth and radio integration allow for seamless communication between personnel inside and outside confined spaces, ensuring constant contact even in complex, hazardous work environments. This minimises response time and increases situational awareness across teams.
Fully automated confined space entry and monitoring systems
- Robotic entry and monitoring – future confined space safety may see the rise of autonomous or remote-controlled robots that can perform inspections, take environmental readings, and conduct basic maintenance without the need for human entry. By minimising the need for direct human exposure to high-risk areas, automated systems can reduce accident rates and enhance safety.
- Drone-assisted inspection systems – drones equipped with cameras and environmental sensors may assist in inspecting confined spaces that are challenging for humans to navigate. These drones could fly into spaces, relay real-time video and environmental data, and identify issues that might need attention, thus improving the accuracy and safety of inspections.
AI-driven risk assessment and incident management
- Automated risk assessment tools – AI-based tools could assess confined spaces and create risk profiles before human entry. By analysing past data, sensor readings and predictive modelling, these tools can offer detailed risk assessments, suggesting optimal entry strategies and safety measures tailored to specific conditions.
- Integrated safety command centres – an AI-driven command centre could monitor multiple confined space entries simultaneously, assessing each environment’s real-time data and ensuring compliance with safety protocols. It could dispatch alerts, recommend actions, and coordinate responses across multiple sites, enhancing situational awareness and crisis management.
Smart exoskeletons and robotics for worker assistance
- Exoskeletons for confined spaces – as exoskeleton technology advances, specially designed exoskeletons could assist workers in confined spaces by providing support, stability and strength, reducing physical strain and injury risk in demanding environments. This could be especially useful in confined spaces that require prolonged physical labour in awkward postures.
- Collaborative robots (Cobots) as safety partners – cobots, designed to work alongside humans, may soon play a role in confined spaces. They could be tasked with carrying equipment, managing waste, or providing support during entry and exit, effectively reducing the physical demands on human workers and enhancing operational efficiency.
Digital twin technology for simulation and training
- Virtual environment training and simulation – digital twins, virtual replicas of confined spaces, allow workers to train in simulated conditions identical to the real spaces they will enter. This provides hands-on practice in a risk-free environment, enabling workers to familiarise themselves with potential hazards, evacuation routes and emergency procedures before they physically enter the confined space.
- Predictive maintenance through digital twins – using a digital twin, safety managers could monitor and predict equipment wear and environmental degradation in confined spaces. This helps in planning maintenance proactively, reducing unplanned shutdowns and ensuring that spaces remain as safe as possible.
Biometric access and real-time compliance monitoring
- Biometric access control – advanced biometric systems, such as facial recognition or fingerprint scans, could be used to ensure that only authorised and adequately trained personnel enter confined spaces. These systems would improve accountability and enhance compliance with safety protocols.
- Compliance monitoring through Augmented Reality (AR) – AR devices could overlay safety instructions, compliance checklists and evacuation routes onto workers’ field of vision in real time, enhancing adherence to safety protocols and guiding workers step-by-step through complex confined space tasks.

As technology advances, the landscape of confined space safety will transform, blending automation, AI and real-time monitoring to create safer work environments. From AI-powered risk assessment to robotic entry systems, each innovation contributes to a future where confined space entry becomes less reliant on direct human intervention, mitigating risk while increasing operational efficiency. The evolution of safety equipment will not only safeguard human lives but also streamline industrial operations, making confined space safety smarter, faster and more reliable.
Conclusion
Advancements in confined space safety equipment are significantly enhancing the protection and efficiency of workers in hazardous environments. Emerging technologies, such as improved ventilation systems, wearable sensors and real-time monitoring devices, are minimising risks and enabling faster responses to potential threats.
Robotics and drones are reducing the need for human entry into confined spaces, while augmented reality (AR) and virtual reality (VR) training tools are preparing workers to handle these environments more effectively. As these innovations continue to evolve, they promise to not only improve safety standards but also increase regulatory compliance and operational productivity. By investing in modernised safety solutions, industries can foster a safer work environment and demonstrate a commitment to the wellbeing of their workforce, ensuring that confined spaces become significantly less dangerous.