In this article
Electrical safety is a critical concern in both domestic and commercial settings, with significant legal and regulatory frameworks in place to protect individuals and businesses in the UK. The potential hazards posed by electrical systems underscore the necessity for stringent safety measures.
According to Electrical Safety First there are about 19,300 accidental domestic fires in the UK each year with an electrical-related cause, whether this may be down to faulty leads or misuse of appliances.
Electrical safety is crucial for preventing accidents and ensuring the longevity of appliances. Electrical accidents can result in:
- Electrical shocks – improper handling or faulty wiring can result in electrical shocks, which can cause severe injury or even death.
- Burns – electrical faults can lead to burns if appliances overheat or short circuit.
- Fires – faulty electrical appliances or wiring are a major cause of residential and commercial fires. Ensuring electrical safety can prevent these catastrophic events.
The common risks associated with electrical appliances include:
- Overloading – plugging too many devices into a single outlet can cause overheating and increase the risk of electrical fires.
- Short circuits – faulty wiring or damaged insulation can lead to short circuits, causing sparks, fires or damage to the appliance.
- Water exposure – water conducts electricity, and exposure can result in severe electrical shocks or damage to the appliance.
- Damaged cords and wires – frayed or damaged cords are a common risk, as they can expose live wires and cause shocks or fires.
- Improper grounding – appliances that are not properly grounded can lead to electrical shocks. Grounding provides a safe path for electricity to travel back to the ground.
- Misuse of extension cords – using extension cords as permanent wiring solutions can lead to overheating and increased fire risk. They should be used only temporarily and with the correct load capacity.
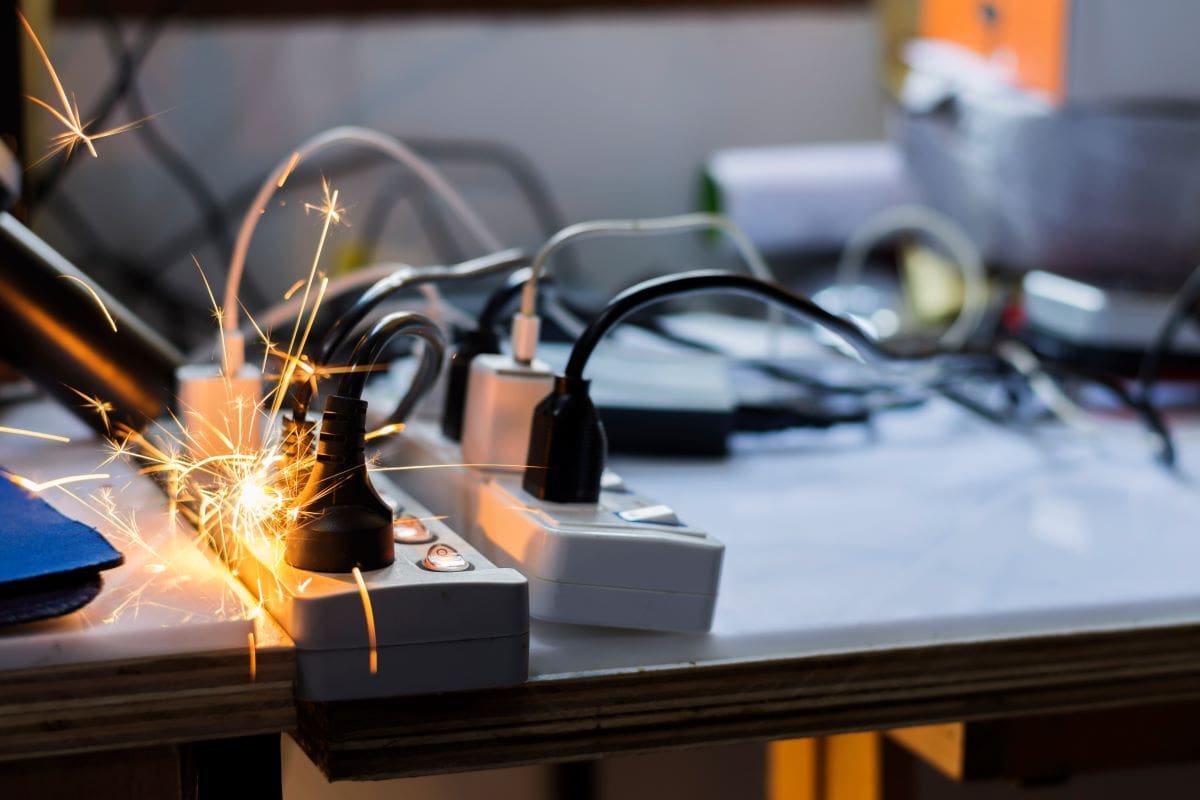
Prioritising electrical safety is essential for protecting lives and property. Understanding the common risks associated with electrical appliances and taking preventative measures can significantly reduce the likelihood of accidents and extend the useful life of electrical equipment. Regular inspections, proper usage and adherence to safety standards are key practices in maintaining a safe electrical environment.
The UK’s approach to electrical safety is governed by various laws and regulations that ensure installations, maintenance and usage are conducted safely. Key legislation, such as the Electricity at Work Regulations 1989 and the Building Regulations, along with standards like the British Standard BS 7671, establish the legal obligations for electrical work. These regulations are designed to mitigate risks and ensure compliance with safety practices, offering protection to workers, consumers and property. Understanding these legal implications is essential for electricians, employers and property owners to avoid penalties, prevent accidents and safeguard lives.
Overview of Key Regulations and Standards
OSHA (Occupational Safety and Health Administration) Standards (U.S.)
The Occupational Safety and Health Administration (OSHA) is a U.S. government agency under the Department of Labor, responsible for ensuring safe and healthy working conditions for employees. OSHA achieves this through setting and enforcing standards, offering training, outreach and education.
Key components of OSHA standards include:
- Employers must provide a workplace free from recognised hazards that are likely to cause death or serious harm.
- OSHA has industry-specific standards that address hazards across sectors such as construction, maritime and agriculture.
Common OSHA standards include:
- Hazard communication – requires informing workers about chemical hazards via labelling, safety data sheets and training.
- Personal Protective Equipment (PPE) – this mandates the use of protective clothing for dangerous jobs.
- Machine guarding – this ensures protection from machinery hazards.
- Fall protection – this requires systems to prevent falls in construction and other industries.
- Confined spaces – regulations for entering hazardous enclosed areas.
- Record-keeping – employers must maintain records of work-related injuries and illnesses.
- Enforcement and inspections – OSHA conducts workplace inspections, and employers can face penalties for non-compliance.
NFPA 70E (National Fire Protection Association) Standard (U.S.)
NFPA 70E is a U.S. standard published by the National Fire Protection Association (NFPA) that focuses on electrical safety in the workplace. Its main purpose is to protect workers from electrical hazards, such as shock, electrocution, arc flash and arc blast. The standard provides guidelines for safe work practices, PPE and maintenance requirements.
The key components of NFPA 70E include:
- Hazard risk assessments – it requires employers to assess potential electrical hazards and determine the level of risk associated with electrical tasks.
- Safe work practices – provides rules for de-energising electrical equipment before work and outlines procedures for working on live equipment if absolutely necessary.
- PPE – it specifies the necessary PPE for workers exposed to electrical hazards, including clothing, gloves and face shields, based on the risk level.
- Arc flash boundary – this defines the distance within which workers are at risk of injury from an arc flash and the required protective measures.
- Training – it mandates regular training for workers to ensure they are aware of potential electrical hazards and understand safe work practices.
IEC (International Electrotechnical Commission) Standards
The International Electrotechnical Commission (IEC) is a global organisation that develops and publishes standards for electrical, electronic and related technologies. IEC standards are widely used to ensure the safety, reliability and performance of various electrical products and systems.
IEC standards cover a wide range of technologies, including power generation, transmission, electronics, communication, renewable energy and electromagnetics. The goal is to harmonise practices globally, making trade easier and ensuring products and systems are safe and interoperable.
Their key areas of focus include:
- Electrical equipment and machinery – standards for electrical safety, performance and environmental considerations.
- Power and energy – standards for power generation, transmission, renewable energy and smart grids.
- Electromagnetic compatibility (EMC) – ensuring devices work without causing or being affected by electromagnetic interference.
- Cybersecurity – standards for data security and communication protocols in smart grids and industrial systems.
- Global impact – IEC standards are recognised internationally, facilitating global trade by creating common criteria for product quality and safety. They are often adopted by national standard organisations, forming the basis of many national regulations.
- Collaboration – IEC works with other organisations, like the ISO (International Organisation for Standardisation) and ITU (International Telecommunication Union), to create joint standards where there is overlap in technology fields.
European Union Directives
European Union (EU) Directives are legislative acts that set goals or standards for all EU member states to achieve, while giving them the flexibility to choose how to implement them within their national laws. Unlike regulations, which are immediately binding in their entirety, directives require member states to transpose the directive into their own legal systems, usually within a set deadline.
Its purpose is to harmonise laws across the EU, ensuring consistent outcomes while respecting national legal systems. It covers various policy areas, such as environmental protection, consumer rights, digital services, labour laws and public health.
Each member state decides how to incorporate the directive into its national legislation, adapting it to local circumstances. The European Commission monitors the transposition and can take legal action against states that fail to implement directives correctly or on time.
Local and National Regulations
There are various other regional or country-specific regulations, including the Canadian Electrical Code (CEC), officially known as CSA C22.1, a standard published by the Canadian Standards Association (CSA). It sets out the safety requirements for electrical installations across Canada. The CEC is intended to protect people and property from electrical hazards by outlining how electrical systems should be installed, maintained and operated.
The AS/NZS 3000 is the Australian/New Zealand Standard for electrical installations, commonly known as the Wiring Rules. It sets out requirements for the design, construction and verification of electrical installations to ensure their safety and efficiency. The standard is jointly published by Standards Australia and Standards New Zealand and applies to all types of electrical installations, including residential, commercial and industrial.
Industry-Specific Regulations
In the UK, several industry-specific regulations apply to electrical safety in addition to general standards:
- Construction industry – the Construction (Design and Management) Regulations 2015 (CDM) focus on the safe design and management of construction projects, including electrical installations. BS 7671 Wiring Regulations govern electrical installations in construction, ensuring safety in temporary and permanent set-ups.
- Healthcare sector – the Health Technical Memoranda (HTM 06-01) outlines standards for electrical services in healthcare facilities to ensure patient safety, particularly for life-critical systems like medical equipment.
- Energy sector – the Electricity Safety, Quality and Continuity Regulations (ESQCR) 2002 specify requirements for energy suppliers to ensure the safe distribution of electricity. The Electricity at Work Regulations 1989 also apply, with a particular focus on the safe operation and maintenance of high-voltage equipment.
Legal Implications of Non-Compliance
Penalties and Fines
Failure to comply with electrical safety regulations in the UK can lead to serious financial consequences, including fines, penalties and legal fees including:
- Magistrates’ court fines – breaching electrical safety regulations can result in significant fines. In the Magistrates’ Court, fines can go up to £20,000 per offence, depending on the severity and nature of the breach.
- Unlimited fines (Crown Court) – if the case escalates to the Crown Court, fines are unlimited, meaning there is no cap on the financial penalties. Serious breaches, particularly those resulting in injury or death, may incur very high fines.
- Landlord penalties (for Residential Properties) – landlords are specifically required to ensure that electrical installations and equipment in rented properties are safe. Under the Electrical Safety Standards in the Private Rented Sector (England) Regulations 2020, landlords who fail to comply may face fines of up to £30,000 per breach.
Defending against electrical safety violations can lead to significant legal fees. This includes the cost of hiring solicitors, barristers and any associated legal professionals. Legal costs can escalate quickly, especially if the case progresses to higher courts. There are also associated court fees, which vary based on the court in which the case is heard and the complexity of the case. These can include filing fees, hearing fees and other procedural costs.
In cases where a failure to comply with electrical safety regulations leads to property damage or personal injury, the company or individual could face civil claims for compensation. The compensation claims could include damages for injury, property loss or loss of life, which can amount to substantial sums.
The Health and Safety Executive (HSE) can issue prohibition notices that require unsafe electrical work to stop immediately. Failure to comply with a prohibition notice is a criminal offence, which can result in additional fines. If the HSE issues an improvement notice and the entity fails to make the necessary corrections, this can also lead to further penalties and additional legal scrutiny.
Enforcement actions, including prohibition or improvement notices, can lead to significant business disruption. This can result in lost revenue, especially if operations are halted until the issue is resolved. Non-compliance with safety regulations can result in higher insurance premiums or, in some cases, void insurance coverage altogether. This adds an ongoing cost burden.
If equipment, systems or installations are found to be non-compliant, the cost of bringing them up to standard can be significant. This includes hiring qualified electricians, replacing faulty wiring, and ensuring all systems are safe and compliant with regulations.
In extreme cases where breaches result in serious injury or death, individuals responsible (such as directors or landlords) may face criminal prosecution, which could lead to imprisonment. Although not a direct financial penalty, imprisonment can devastate a business financially.
Company directors found liable for significant breaches of safety regulations may also face disqualification from serving as directors, which could have long-term financial implications for their personal careers and the business.
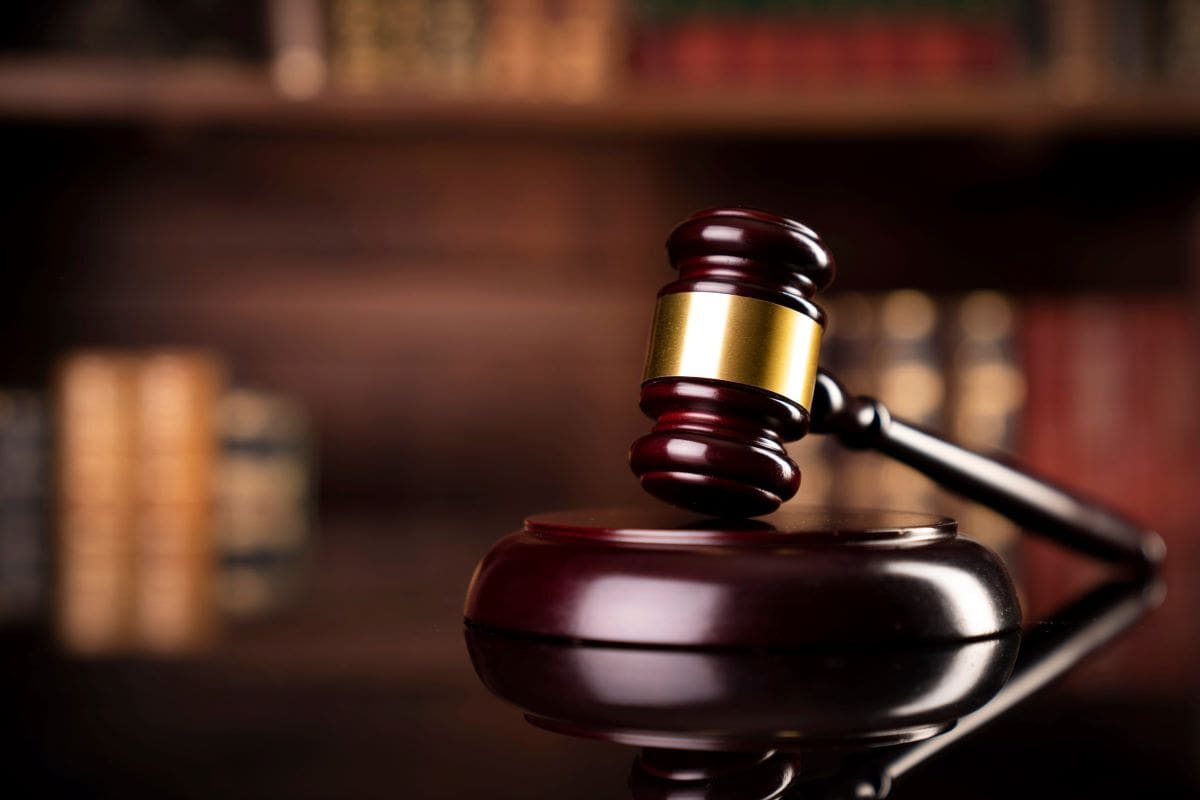
Criminal and Civil Liability
Criminal charges can be brought against individuals and companies under various statutes, with the key ones being the Health and Safety at Work Act 1974, the Electricity at Work Regulations 1989, and the Corporate Manslaughter and Corporate Homicide Act 2007.
Employers or duty holders can be prosecuted if they fail to take reasonable steps to prevent risks from electrical hazards, such as faulty wiring, non-compliant installations, or failure to maintain electrical equipment. If gross negligence leads to the death of an individual, a company can be prosecuted for corporate manslaughter. This charge applies when the company’s activities, policies or management lead to a gross breach of the duty of care owed to individuals, resulting in a fatal accident.
In addition to criminal proceedings, victims or their families can pursue civil lawsuits for damages, focusing on compensation for losses or injuries suffered as a result of the negligence. A civil lawsuit for negligence requires proving that the company or individual:
- Owed a duty of care to the injured party and breached that duty.
- The breach directly caused injury or damage.
- The injury or damage was reasonably foreseeable.
If these elements are met, the injured party can claim compensation for:
- Medical expenses
- Loss of earnings
- Pain and suffering
- Property damage.
Insurance Implications
If an insurance provider becomes aware that a property or business is not adhering to electrical safety standards, the perceived risk of fire or electrical hazards increases. As a result, the insurer may raise premiums to compensate for the heightened risk. Non-compliance may also signal to insurers that regular inspections and maintenance are not being carried out. This increases the likelihood of electrical accidents, which, in turn, leads to higher premiums to cover the increased risk.
Most insurance policies, particularly for property and business insurance, have specific clauses that require compliance with local safety regulations, including electrical safety. If non-compliance is discovered after an electrical fire, shock incident or equipment damage, insurers may deny claims, citing a breach of policy terms.
If an incident such as a fire is found to have been caused by faulty or non-compliant electrical systems, insurers can argue that the negligence led to the loss. As a result, they can refuse to cover the costs of damages, repairs or liability claims.
In extreme cases, insurers may void a policy altogether if there is a persistent or blatant failure to comply with electrical safety regulations. This can happen if the insurer finds out that the policyholder intentionally disregarded safety regulations, putting the property and occupants at significant risk.
Business Reputational Damage
Companies that fail to meet electrical safety standards may suffer reputational damage, leading to a loss of clients, contracts or tenants. The long-term financial impact of reputational damage can be substantial.
A strong business reputation is essential for long-term success, sustainability and growth in a competitive market.
Best Practices for Maintaining Compliance
Conduct Regular Risk Assessments
Risk assessments are a legal requirement ensuring that employers prioritise the safety of their employees and others who might be affected by their activities. Regular assessments ensure compliance and avoid potential penalties.
Regular assessments help maintain system performance by identifying faults before they escalate. This reduces downtime, equipment damage, and the cost of emergency repairs. Preventative maintenance resulting from risk assessments helps extend the lifespan of electrical systems, improving reliability and operational efficiency.
Develop and Implement Safety Programmes
Developing a comprehensive electrical safety programme is essential for reducing risks, preventing accidents and ensuring legal compliance. Implementing clear electrical safety policies provides the foundation for safe working practices.
These policies should include:
- Risk assessment procedures to identify and evaluate electrical hazards.
- Permit-to-work systems for tasks involving high-voltage equipment.
- Lockout/Tagout policies to ensure equipment is properly de-energised before any maintenance or repair.
- Reporting mechanisms for incidents and near misses to continually improve safety.
Establishing well-documented Standard Operating Procedures (SOPs) ensures that all employees understand how to work with or around electrical systems safely. These procedures should cover:
- Safe use of electrical tools and equipment.
- Proper handling of cables, switches and other electrical components
- Instructions for working in environments with high electrical risks, e.g. wet areas or confined spaces.
- Specific guidelines for qualified vs. unqualified employees regarding who can handle certain tasks.
Provide Training and Certification
An effective electrical safety programme must include regular training to ensure that all employees, regardless of their role, are aware of the risks and the safety measures in place. Key elements include:
- Initial training for all new employees on electrical hazards, safe practices and emergency procedures.
- Refresher training to update employees on new policies, equipment or regulations.
- Tailored training for workers who are exposed to higher risks, e.g. electricians or maintenance staff, on safe work practices, the use of protective equipment, and emergency procedures.
Use Compliant Equipment and Tools
Using tools and equipment that meet current safety standards and regulations is crucial for several reasons:
- To ensure user safety.
- To ensure legal compliance.
- Prevents malfunctions and breakdowns.
- Protects others and the environment.
- Enhanced productivity and efficiency of equipment.
- Maintains reputation and trust.
By investing in tools and equipment that meet current safety regulations, businesses not only protect their workforce and assets but also align themselves with best practices that promote long-term success and sustainability.
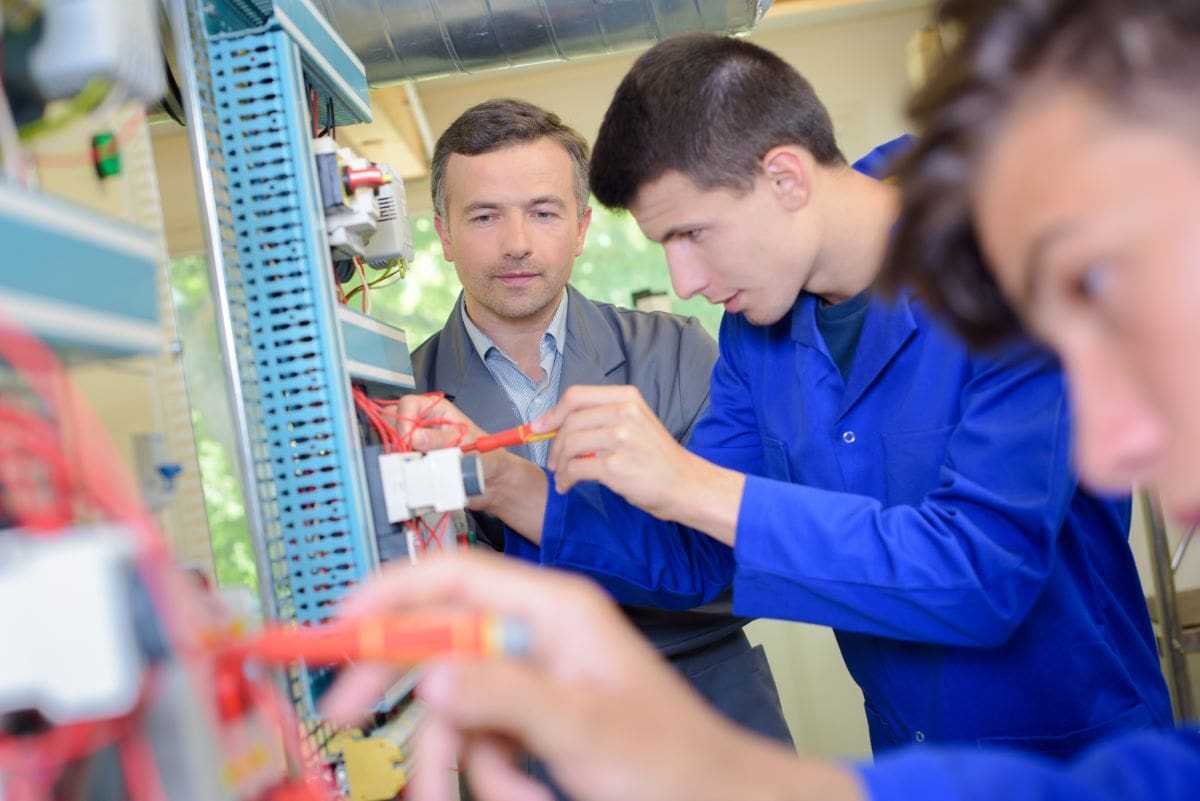
Maintain Documentation and Record-Keeping
Maintaining detailed records of safety inspections, training sessions, incident reports and compliance checks is critical for demonstrating adherence to UK electrical safety regulations. In the event of an accident or incident involving electrical equipment, organisations may be required to prove they have taken reasonable steps to prevent harm. Records of training sessions, inspections and safety audits serve as proof that employees were properly trained, equipment was regularly inspected, and safety standards were actively maintained. This can help reduce liability and demonstrate that the organisation has acted responsibly.
Detailed incident reports allow for effective analysis of accidents or near-miss events, helping organisations identify potential root causes of electrical hazards. This data supports proactive measures to improve safety standards and prevent future incidents. These records can be used to assess trends and develop targeted safety interventions, thereby improving the overall safety culture.
Records of training sessions and competency assessments ensure that employees are adequately trained and qualified to perform their roles safely. Keeping detailed training logs allows organisations to track which employees have received electrical safety training, making it easier to identify gaps in knowledge and ensure that all staff remain compliant with required safety standards.
Insurance companies often require detailed records as part of their risk assessments. In the event of a claim related to an electrical incident, these records demonstrate that the organisation has followed best practices and complied with all legal and safety obligations. This can reduce the risk of claims being rejected and may also contribute to lower insurance premiums by demonstrating effective risk management.
Case Studies and Examples
Example of a Compliance Success
General Motors (GM), one of the largest automotive manufacturers in the world, operates numerous production plants across the globe. With a highly automated production process and extensive use of electrical equipment, GM recognised the potential hazards associated with electricity in its facilities. Electrical hazards posed a risk not only to employee safety but also to the continuity of operations and compliance with regulatory requirements.
Prior to implementing its comprehensive electrical safety programme, GM faced several issues:
- Frequent electrical incidents – a number of minor electrical shocks, arc flashes and near misses had occurred across multiple facilities.
- Non-compliance with standards – audits revealed gaps in compliance with electrical safety regulations.
- Lack of employee training – many employees lacked formal training on electrical hazards, which contributed to unsafe practices and lack of awareness.
- High risk of legal and financial liabilities – without proper safety measures, GM risked substantial fines, compensation claims and other legal repercussions.
To address these challenges, GM implemented a detailed electrical safety programme across all its manufacturing plants globally. The key elements of the programme included:
- Electrical risk assessments – GM began conducting thorough risk assessments of all electrical systems, identifying high-risk areas, equipment and processes. This allowed them to prioritise safety improvements.
- Training and awareness programmes – GM launched extensive training programmes tailored to different roles, such as electricians, maintenance personnel and machine operators. The training covered lockout/tagout (LOTO) procedures, arc flash safety and appropriate PPE, safe operation and maintenance of electrical systems, and awareness of standards and regulations.
Within two years of implementing the electrical safety programme, GM saw a dramatic improvement in workplace safety and compliance. The company reported a 50% decrease in electrical incidents, including arc flashes and electric shocks. No serious injuries related to electrical hazards were reported during this period. Regular audits showed that the company consistently met or exceeded safety requirements.
Employee surveys indicated that workers felt significantly safer performing their jobs, especially those who worked directly with electrical equipment. The training programmes and new safety protocols instilled confidence in the workforce.
By avoiding electrical incidents, GM reduced potential legal liabilities, workers’ compensation claims, and downtime from electrical-related injuries. In addition, the company avoided hefty fines for regulatory non-compliance. GM’s electrical safety programme was recognised as a best practice within the manufacturing industry. The company shared its approach with other manufacturers and contributed to industry-wide improvements in electrical safety.
General Motors’ implementation of a comprehensive electrical safety programme demonstrates how proactive measures, including risk assessments, training, standardised procedures and regular audits, can lead to significant improvements in workplace safety and regulatory compliance. By focusing on continuous improvement, GM not only protected its workers from electrical hazards but also minimised operational disruptions and legal risks, ultimately creating a safer and more efficient work environment.
This case is an example of how a large organisation can successfully implement an electrical safety programme, align with industry standards, and see measurable benefits.
Example of Non-Compliance Consequences
A significant real-life example from the UK where failure to comply with electrical safety regulations led to a tragic accident and legal action, occurred in 2015, involving a company called Celtic Recycling Ltd in Newport, South Wales.
Allan Currie was working on a high-voltage transformer when he was electrocuted. The transformer had not been properly isolated from the power supply, violating critical safety regulations for handling live electrical systems. The failure to implement the appropriate safety measures resulted in Currie being exposed to an electric shock of 33,000 volts, leading to his death.
The Health and Safety Executive (HSE) conducted an investigation and found several breaches of electrical safety regulations. The power supply to the transformer was not isolated, and there were no clear safety protocols in place for working with high-voltage equipment. The company failed to create and implement safe working procedures that ensured equipment was fully de-energised before any work was done. The investigation revealed insufficient supervision and training for workers handling electrical equipment.
In 2017, Celtic Recycling Ltd was prosecuted under the Health and Safety at Work Act 1974 and the Electricity at Work Regulations 1989. They pleaded guilty to the safety breaches and were fined £450,000 for their role in the fatal accident. They were also ordered to pay £71,000 in legal costs. The company was criticised for its failure to prioritise electrical safety, which directly led to the tragic incident.
This case serves as a stark reminder of the importance of complying with electrical safety regulations in the workplace. Failure to ensure proper isolation of electrical equipment, inadequate training and lack of supervision can result in severe legal consequences and, more tragically, the loss of life.
This incident reinforced the need for stringent adherence to safety protocols, particularly when working with high-voltage systems, to prevent such accidents and legal repercussions.
Future Trends in Electrical Safety Regulation
Emerging Regulations and Standards
The landscape of electrical safety standards in the UK is rapidly evolving in response to the proliferation of new technologies such as EVs, renewable energy, smart homes and battery storage systems.
The IET Wiring Regulations (BS 7671), in particular, are expected to undergo several amendments, ensuring that electrical systems remain safe as they integrate with advanced technologies and renewable energy sources.
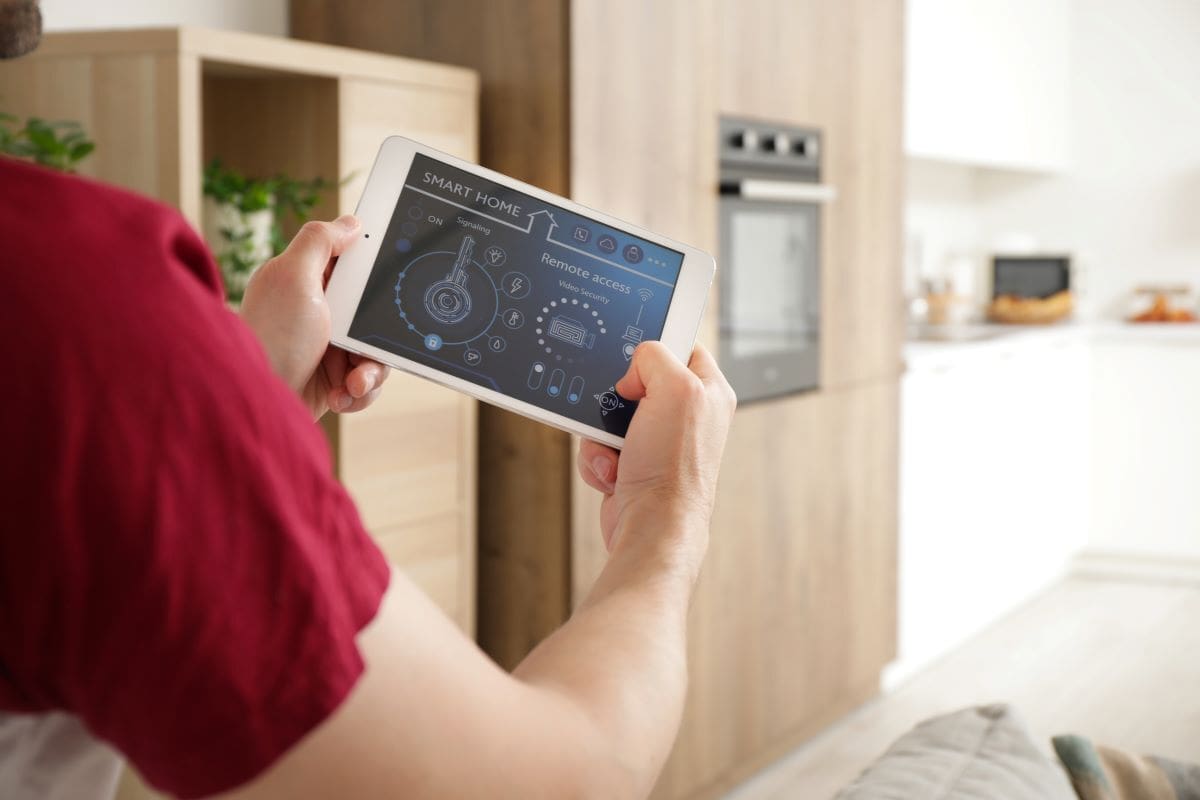
Global Harmonisation Efforts
The harmonisation of electrical safety regulations across countries and regions is essential for facilitating international trade and ensuring safety compliance. Different countries have varying standards for electrical safety. This diversity can complicate compliance for manufacturers and hinder trade.
Benefits of harmonisation include:
- Facilitating trade – unified regulations can reduce the barriers to entry for manufacturers, streamline certification processes, and lower costs associated with compliance.
- Enhancing safety – a common set of standards can improve product safety globally, ensuring that products meet high safety requirements regardless of their origin.
- Simplifying compliance – manufacturers can avoid the need to redesign products for different markets, reducing time to market and fostering innovation.
Challenges to harmonisation include:
- Regulatory differences – differences in national regulations can be based on local safety concerns, environmental factors or market needs, making uniformity challenging.
- Resistance to change – established practices and standards may face resistance from stakeholders who are accustomed to existing systems.
- Economic factors – the cost implications for countries in adopting new standards or aligning with international norms may deter progress.
Potential strategies for harmonisation include:
- International collaboration – establishing collaborative efforts among international standards organisations, governments and industry stakeholders to develop common standards.
- Mutual recognition agreements (MRAs) – countries can enter agreements that recognise each other’s certification processes, allowing products certified in one country to be accepted in another.
- Regional standards bodies – developing regional standards that can serve as a bridge between global standards and national regulations to facilitate alignment.
Conclusion
In conclusion, the legal implications and regulations surrounding electrical safety in the UK are essential for protecting both individuals and properties from electrical hazards. Compliance with established standards, such as the Wiring Regulations (BS 7671), the Electricity at Work Act 1989, and the Health and Safety at Work Act 1974, is crucial for ensuring safety in both residential and commercial settings. The regulatory framework not only mandates proper installation and maintenance of electrical systems but also emphasises the need for ongoing training and certification for electricians.
As technology evolves and new challenges arise, continuous updates to legislation and safety standards will be necessary to address emerging risks associated with electrical safety. Stakeholders, including regulatory bodies, businesses and consumers, must remain vigilant and proactive in adhering to these regulations to foster a culture of safety.
Ultimately, the effective enforcement of electrical safety laws will contribute to minimising risks, promoting public confidence, and safeguarding the well-being of everyone in the UK.