In this article
Lockout/tagout (LOTO) procedures are crucial safety protocols aimed at protecting workers during the maintenance and servicing of machinery. According to the Health and Safety Executive (HSE), there are around 1,000 electrical accidents at work each year and 25 individuals die because of their injuries.
In the United Kingdom, adherence to rigorous LOTO practices is vital in preventing accidents and ensuring workplace safety across various industries. These procedures help mitigate the risks associated with hazardous energy sources, emphasising the need for comprehensive understanding and implementation within organisational safety frameworks.
What is Lockout/Tagout?
Referred to either as lockout/tagout or lock out tag out, LOTO is a safety procedure implemented in industries to ensure the proper shutdown of machinery and equipment during maintenance, repair or servicing activities. The core objective of LOTO is to prevent the accidental startup or release of stored energy, which could lead to serious injuries or fatalities.
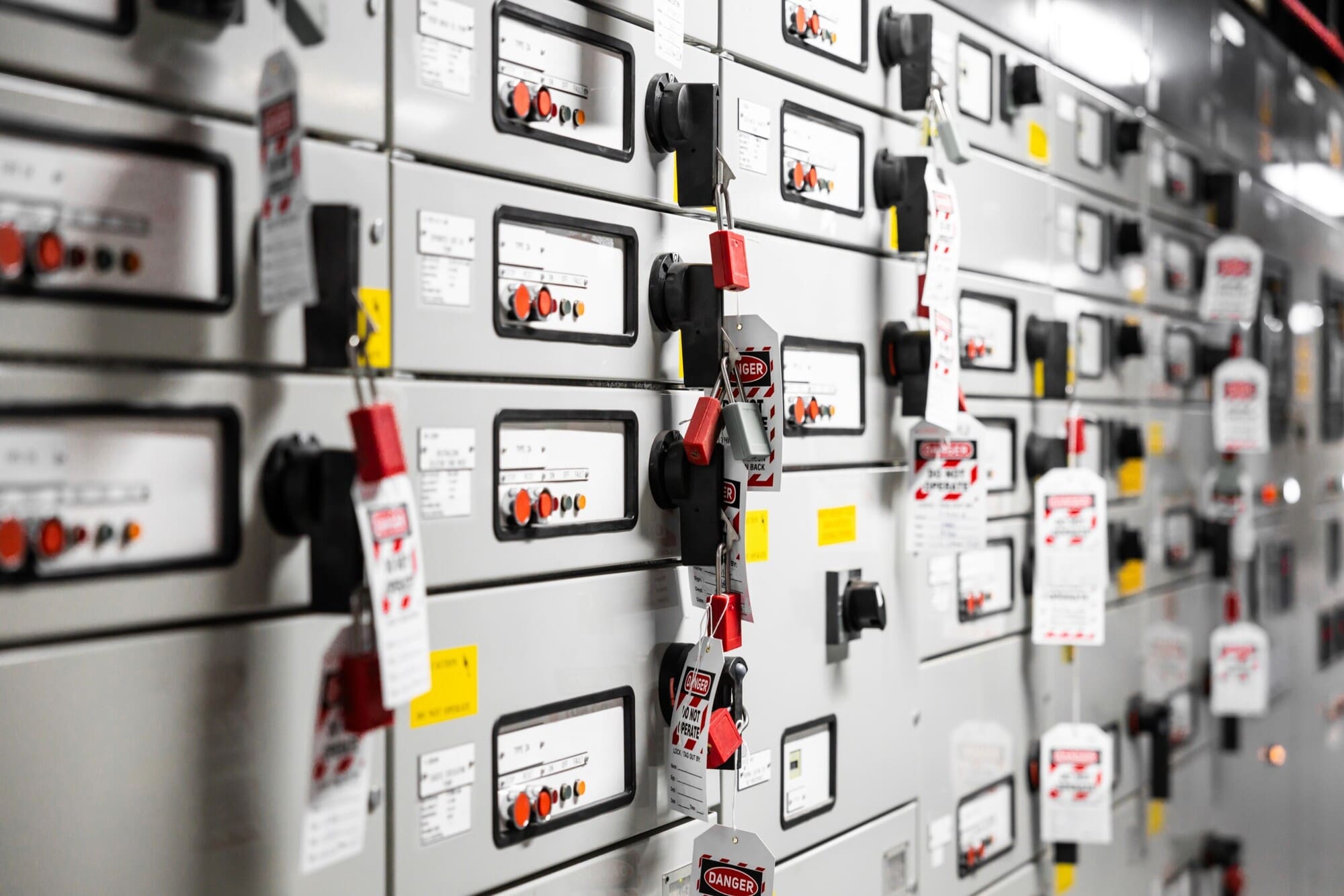
Key Components of Lockout/Tagout
The two key components refer to the following:
Lockout: This involves physically isolating the energy-isolating devices of machinery by using lockout devices such as padlocks, valve covers or electrical circuit breakers. These locks are designed to prevent the machinery from being energised or started up.
Tagout: In addition to lockout, tagout involves attaching prominent tags or labels to the energy-isolating devices. These tags provide clear visual warnings indicating that the equipment must not be operated until the tags are removed by authorised personnel after the completion of maintenance work.
Ultimately, the primary purpose of LOTO is to protect workers from hazardous energy sources, including electrical, mechanical, hydraulic, pneumatic, chemical, thermal or other energy sources. By effectively implementing LOTO procedures, employers can ensure the safety of their employees by preventing accidental contact with energised equipment, thus reducing the risk of workplace accidents and injuries.
Who Does Lockout/Tagout Apply To?
Lockout/tagout (LOTO) procedures apply to any individual involved in maintenance, repair or servicing activities where the unexpected startup or release of hazardous energy could occur. This includes:
- Maintenance Personnel: Employees directly responsible for performing maintenance tasks on machinery or equipment.
- Service Technicians: Workers tasked with repairing or servicing machinery in various industrial settings.
- Operators and Line Workers: Individuals operating or working near machinery that requires maintenance or repair.
- Contractors: External contractors or third-party service providers engaged in maintenance work on-site.
- Supervisors and Managers: Personnel overseeing maintenance operations and ensuring compliance with safety protocols.
- Safety Officers: Professionals responsible for implementing and enforcing safety regulations within the workplace.
LOTO procedures are essential for anyone involved in activities where the unexpected energisation or startup of machinery could lead to serious injury or even death. By adhering to LOTO protocols, employers and workers alike ensure a safer working environment by mitigating risks associated with hazardous energy sources.
What is the Purpose of Lockout/Tagout?
Lockout/tagout (LOTO) serves several critical purposes aimed at protecting workers from the hazards of unexpected energisation or startup of machinery during maintenance, repair or servicing activities. The primary objectives include:
- Worker Safety: The foremost purpose of LOTO is to safeguard the well-being of employees. By effectively implementing LOTO procedures, employers prevent accidental contact with energised equipment, thereby reducing the risk of injuries such as electrocution, burns, crushing or amputation.
- Prevention of Accidents: LOTO helps prevent workplace accidents that can result from the release of stored energy. This includes mechanical, electrical, hydraulic, pneumatic, chemical, thermal or other forms of hazardous energy that can pose significant risks if not properly controlled during maintenance or repair.
- Compliance with Regulations: LOTO procedures come under the Health and Safety at Work Act 1974 and the Provision and Use of Work Equipment Regulations 1998 (PUWER). Compliance with these regulations ensures that organisations adhere to standardised safety practices to protect workers’ health and safety rights.
- Risk Mitigation: LOTO mitigates risks associated with unexpected equipment startup. It ensures that machinery remains in a safe or neutral state during maintenance activities, preventing potential damage to equipment and facilities.
- Enhanced Workplace Safety Culture: Implementing robust LOTO procedures fosters a culture of safety within organisations. It promotes awareness among employees about the dangers of hazardous energy and encourages proactive measures to prevent accidents.
- Legal and Financial Implications: Failure to adhere to LOTO regulations can result in legal consequences and financial liabilities for organisations. Accidents due to inadequate LOTO procedures may lead to lawsuits, fines, increased insurance premiums and damage to the company’s reputation.
- Worker Empowerment: LOTO procedures empower workers by giving them the knowledge and tools to protect themselves from workplace hazards. It promotes collaboration between employees and management in ensuring a safe working environment.
Overall, the purpose of lockout/tagout is to establish a systematic approach to energy control during maintenance activities, emphasising the importance of safety, compliance and risk management within industrial workplaces.
What is the Difference Between Lockout and Tagout?
Lockout and tagout are complementary safety procedures. While they share the common goal of preventing accidental startup or energisation, there are distinct differences between the two:
Lockout
- Definition: Lockout involves physically securing energy-isolating devices with lockout devices such as padlocks, chains or valve covers.
- Purpose: The primary purpose of the lockout is to prevent the equipment from being energised or started up inadvertently.
- Mechanism: Lockout devices are placed on energy-isolating devices (e.g., switches, valves, circuit breakers) to ensure they remain in a safe or off position throughout maintenance activities.
- Effectiveness: Lockout devices physically prevent the operation of machinery, providing a higher level of protection against accidental startup.
Tagout
- Definition: Tagout involves attaching prominent tags or labels to energy-isolating devices to provide a clear warning that the equipment must not be operated.
- Purpose: Tagout serves as a visual warning to inform employees that maintenance work is being performed and that the equipment should not be operated until the tags are removed.
- Mechanism: Tagout devices are typically durable tags or labels that are securely attached to the energy-isolating device using fasteners or adhesive.
- Limitations: Unlike lockout devices, tagout devices do not physically prevent the operation of equipment. They rely on the discipline and compliance of workers to avoid accidental activation.
Key Differences Summarised
Lockout physically prevents machinery from being energised or started by physically disabling energy-isolating devices. Tagout provides a visual warning not to operate machinery, relying on tags or labels attached to energy-isolating devices.
Both lockout and tagout are crucial components of a comprehensive energy control programme. Depending on the circumstances and specific risks involved, organisations may use lockout, tagout or a combination of both to ensure the safety of personnel conducting maintenance activities.
What is a Lockout Device?
A lockout device is a physical mechanism used to secure energy-isolating devices in a safe or off position, thereby preventing the inadvertent startup or release of hazardous energy during maintenance, repair or servicing activities. These devices play a crucial role in the implementation of lockout procedures as part of a comprehensive energy control programme.
Key Characteristics and Components of Lockout Devices
The primary purpose of a lockout device is to ensure that energy-isolating devices (such as electrical circuit breakers, valves, switches or hydraulic lines) cannot be operated while maintenance work is being performed. As such, there are varying types:
- Padlocks: These are commonly used to lock out electrical switches, valve handles or circuit breakers. Padlocks can be keyed differently or have unique keyways to prevent unauthorised removal.
- Lockout Hasps: Used to secure multiple padlocks to an energy-isolating device, allowing multiple workers to apply their own padlocks, ensuring collective safety.
- Valve Lockouts: Specifically designed to fit over valve handles to prevent them from being turned.
- Circuit Breaker Lockout: Clamp around circuit breaker toggles to prevent them from being switched on.
- Cable Lockout: Used to secure devices with a flexible cable that can be cinched tightly around an energy source.
Design and Durability
Lockout devices are typically made from durable materials such as hardened steel or non-conductive plastic to withstand harsh industrial environments and ensure long-term reliability.
Colour and Visibility
Lockout devices are often brightly coloured (commonly red) for high visibility and may include labels or markings indicating the purpose of the lockout and the identity of the authorised personnel.
Key Control
Some lockout devices can accommodate multiple keys, allowing each authorised worker to apply their own lock and ensuring that only those with the corresponding keys can remove them.
Compatibility
Lockout devices are designed to fit specific types and sizes of energy-isolating devices, ensuring a secure and effective lockout procedure without interfering with the normal operation or integrity of the equipment.
The Importance of Lockout Devices
Safety: Lockout devices prevent accidents and injuries by ensuring that machinery cannot be energised or started inadvertently.
Compliance: They help organisations comply with regulatory requirements and standards related to workplace safety.
Risk Mitigation: Using lockout devices minimises the risk of equipment damage and ensures a safe work environment for employees performing maintenance tasks.
Incorporating appropriate lockout devices as part of a lockout/tagout programme is essential for enhancing workplace safety and preventing accidents associated with hazardous energy sources. Proper training and adherence to procedures ensure effective use of lockout devices to protect personnel and maintain operational safety.
What is a Tagout Device?
A tagout device is a prominent tag or label affixed to an energy-isolating device to provide a clear visual warning that the equipment must not be operated. Tagout is an essential component of lockout/tagout (LOTO) procedures and is used in conjunction with lockout devices to enhance safety during maintenance, repair or servicing activities.
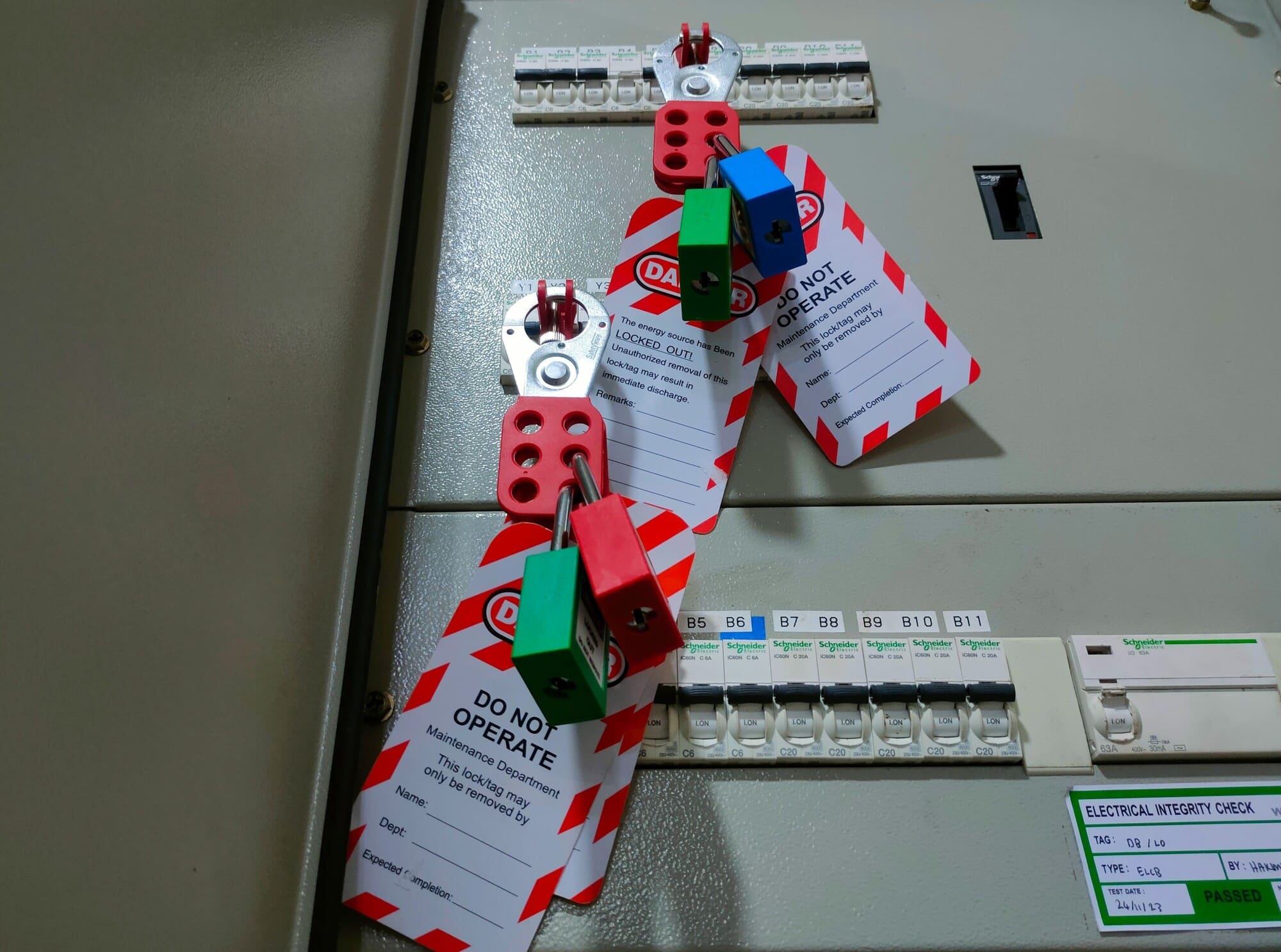
Key Characteristics and Components of Tagout Devices
The primary purpose of a tagout device is to communicate critical safety information to personnel working on or near machinery or equipment. Tags indicate that energy-isolating devices are locked out and should not be operated until the tags are removed by authorised personnel.
Design and Material
Tagout devices are typically made from durable materials such as plastic, cardstock or vinyl to withstand environmental conditions and remain securely attached to energy-isolating devices. They may be pre-printed with standardised warnings, instructions and identification fields.
Colour and Visibility
Tags are usually brightly coloured (commonly red or orange) for high visibility in industrial settings. This ensures that workers can easily identify equipment that is under maintenance and avoid accidental operation.
Information Provided
Tags include essential information such as:
- Warning Statements: Clear statements indicating that the equipment is locked out and should not be operated.
- Identification: Details about the specific equipment or machinery undergoing maintenance.
- Date and Personnel: Information about the authorised personnel responsible for the lockout/tagout procedure and the date/time of application.
- Attachment Method: Tagout devices are attached securely to energy-isolating devices using fasteners such as zip ties, chains or adhesive strips. This prevents easy removal or tampering by unauthorised individuals.
- Limitations: Unlike lockout devices, tagout devices do not physically prevent the operation of equipment. They serve as a supplementary warning system and rely on the diligence and compliance of workers to ensure safety.
The Importance of Tagout Devices
Visual Warning: Tagout devices provide a clear visual indication that equipment is inoperable and under maintenance, helping to prevent accidental startup or energisation.
Communication: Tags convey critical safety information to employees, contractors and other personnel working in the vicinity, promoting awareness and adherence to safety protocols.
Compliance: Incorporating tagout devices into a LOTO programme ensures compliance with regulatory standards and enhances workplace safety practices.
Supplementary to Lockout: Tagout devices complement lockout procedures by providing additional safety measures and reinforcing the importance of maintaining equipment in a safe state during maintenance activities.
Effective use of tagout devices, alongside lockout devices, is essential for mitigating risks associated with hazardous energy sources and preventing workplace accidents. Proper training and adherence to procedures ensure that tagout devices are used effectively to protect personnel and maintain a safe working environment.
What is a Lockout/Tagout Box?
A lockout/tagout (LOTO) box, also known as a lock box or safety box, is a secure container used to store lockout devices, tagout tags and keys during maintenance, repair or servicing activities. It plays a crucial role in ensuring that only authorised personnel have access to energy-isolating devices, thereby preventing accidental startup or energisation of machinery or equipment.
Key Features and Components of a Lockout/Tagout Box
The primary purpose of a LOTO box is to centralise and secure lockout devices, tagout tags and keys used during the lockout/tagout procedure. It ensures that these essential components are readily accessible to authorised personnel and prevents unauthorised tampering or removal.
Construction
LOTO boxes are typically made from durable materials such as metal or sturdy plastic to withstand industrial environments. They are equipped with a hinged lid and may include slots or compartments to organise and store multiple lockout devices, tags and keys securely.
Colour Coding
LOTO boxes are often colour-coded for easy identification and compliance with safety standards. Red is commonly used for LOTO boxes to signify danger and indicate the presence of lockout devices and tags inside. This colour choice aligns with the high-visibility safety standards in industrial settings.
Lockout Locks and Tags
Lockout locks used in conjunction with LOTO boxes are typically colour-coded (commonly red) to match the box and indicate that equipment is locked out for maintenance. These locks are secured to energy-isolating devices to prevent operation.
Tagout Tags
Tagout tags stored in the LOTO box are also colour-coded (often red or orange) for visibility and to indicate that equipment is under maintenance. Tags provide critical information and warnings to personnel about the status of energy-isolating devices.
Key Control
LOTO boxes include designated hooks, slots or compartments to organise and securely store keys to energy-isolating devices. Each key is typically labelled or tagged to indicate the specific lockout point it corresponds to, ensuring controlled access during maintenance activities.
Usage and Access
Only authorised personnel trained in lockout/tagout procedures should have access to the LOTO box. Keys to energy-isolating devices are released only after all maintenance work is completed and the lockout/tagout procedure is verified and signed off.
The Importance of Lockout/Tagout Boxes
Security: LOTO boxes enhance security by centralising lockout devices, tagout tags and keys, reducing the risk of unauthorised access or tampering.
Organisation: They promote organisation and efficiency during maintenance activities by providing a designated storage space for essential LOTO components.
Compliance: LOTO boxes help organisations comply with regulatory requirements and safety standards related to energy control procedures, ensuring a safe working environment for employees.
Incorporating a LOTO box into a comprehensive lockout/tagout programme enhances safety practices and reinforces the importance of controlling hazardous energy sources during maintenance operations. Proper training and adherence to procedures are essential to maximise the effectiveness of LOTO boxes in preventing workplace accidents.
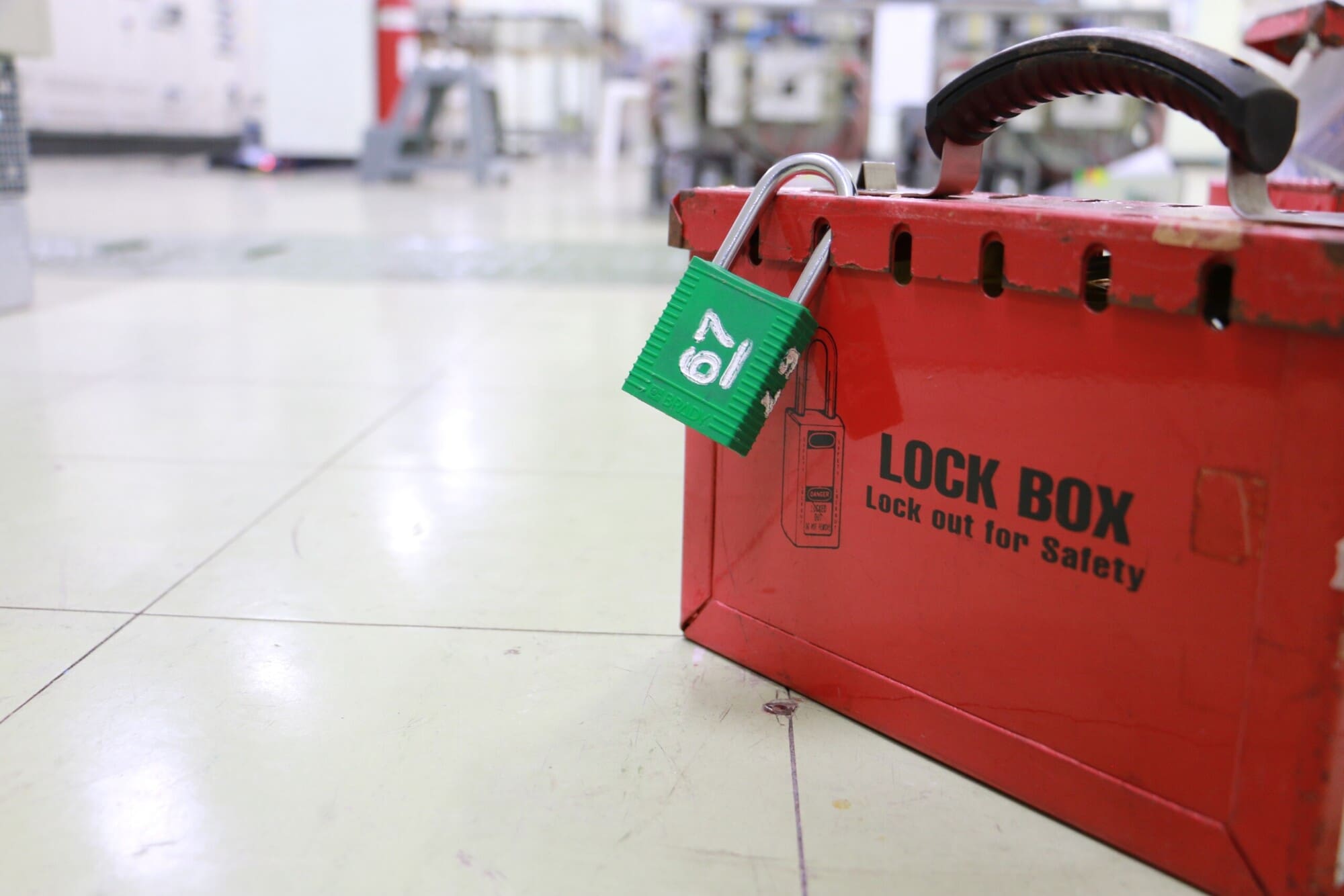
What are the Lockout/Tagout Requirements?
In the United Kingdom, lockout/tagout falls under the HSE PUWER 1998. These regulations ensure that work equipment doesn’t lead to incidents and risk health and safety.
Key Processes of LOTO Standard
Preparing for Shutdown
This should take place in advance. However, if a machine has failed or needs repairs, this might not be possible. It’s a good idea to use a computerised maintenance management system (CMMS) to record everything like who is going to carry out the work, what the work involves, who will need access to machinery and how long it will take.
Notifying Employees
If a planned shutdown of machinery is required, employees should be notified in advance. Anyone who is affected needs to be notified. Ideally, this will be in a face-to-face meeting or conversation to ensure they don’t miss the message.
Machinery Shutdown
Machinery needs to be turned off by an authorised technician that understands the potential hazards. There should be an established procedure to do this to minimise risk.
Isolate Equipment
After shutting down, equipment should be isolated from its source of energy. This might require a line valve, block or circuit breaker. There could be safety blocks, blank flanges, special disconnects or valves to isolate the equipment.
Dissipate Residual Energy
Residual or stored energy is energy that stays within the machinery or system after it’s been turned off. If this were to be released without control, it could cause injuries; for example, being struck by moving parts or objects or by being crushed. This is a huge hazard. Whether it’s pressure in gas, water or steam, it is crucial to drain it in the LOTO process.
Apply LOTO Devices
Lockout tagout devices can now be applied. The lockout device will ensure that the machinery is isolated from its energy source. The tagout device will be a visual warning to show the machinery is out of operation. These processes happen together. To put a tag on machinery without locking it out is dangerous and vice versa.
Check the Equipment is Isolated
It is vital to check that all machinery is disconnected. This final step ensures that the servicing can be done.
By adhering to strict lockout/tagout procedures, employers can effectively protect workers from the dangers of hazardous energy and create a safer work environment conducive to productivity and employee well-being.