In this article
Employers have a duty to protect their workers from hazards in the workplace. The Control of Substances Hazardous to Health (COSHH) regulations set out what measures need to be taken in order to protect people from exposure to harmful materials.
To successfully implement COSHH guidelines, it is vital to provide essential protective equipment and take preventative measures, as well as provide training in the identification and control of hazardous substances.
COSSH training is important across a range of industries including healthcare, hospitality, construction and manufacturing. Failure to adhere to COSHH guidelines places workers in danger of disease, burns, breathing problems, skin issues and other work-related ill health.
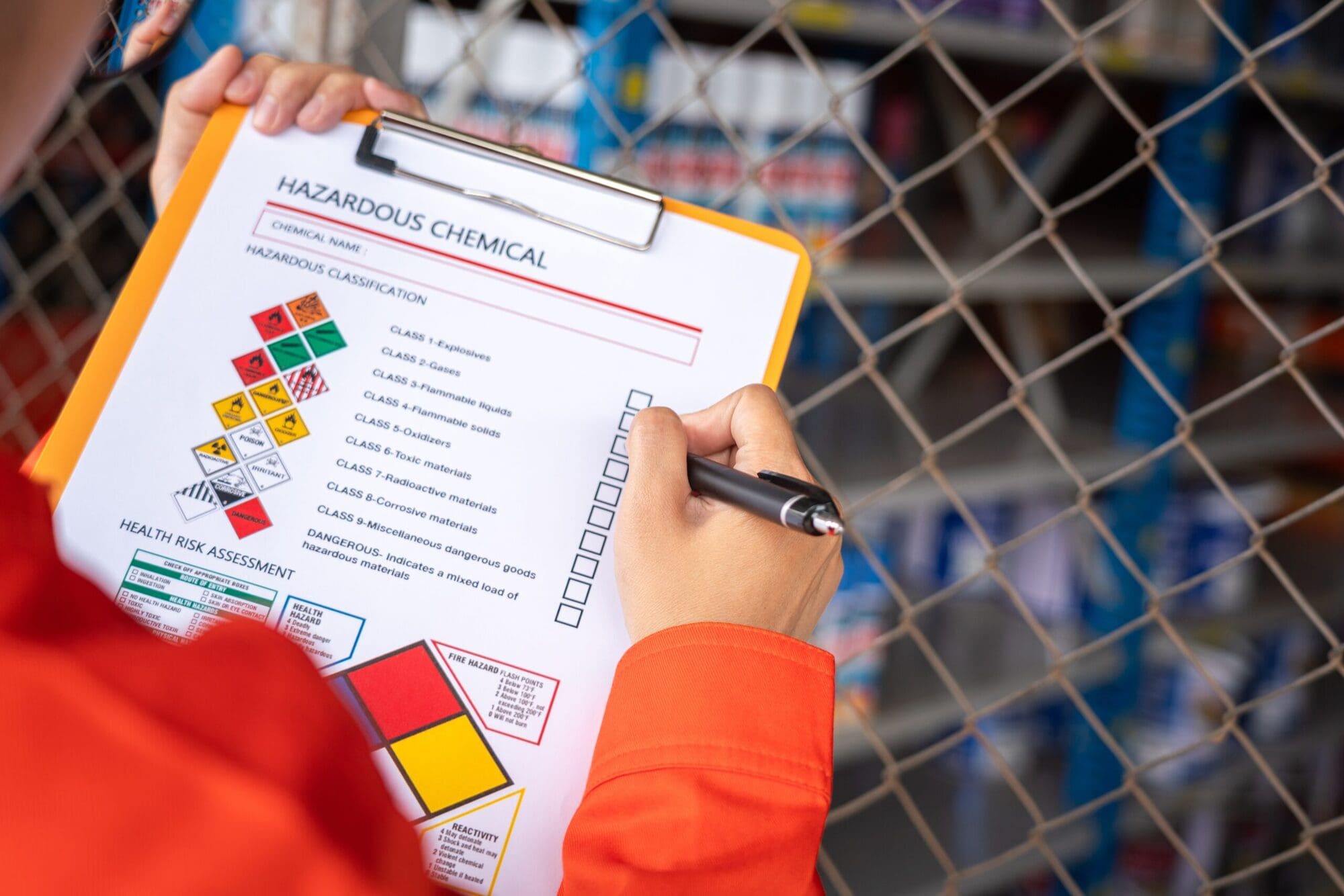
Understanding COSHH Regulations
The law requires us to take steps to control exposure to harmful materials and substances at work. A harmful substance or material is one that can cause harm to your health in some way. Some substances can cause immediate ill effects whereas others build up in the body and cause damage over a long period of time.
Harmful substances encountered at work include:
- Dust
- Gases or fumes
- Chemicals (including cleaning materials)
- Paint
- Microorganisms
- Body fluids
Some harmful substances are not covered by COSHH regulations because they have their own specific regulations. This includes asbestos, radioactive substances and lead.
When we routinely encounter substances at work it is vital that we take precautions to protect ourselves from harm. This requires a commitment from both employers and employees to follow COSHH guidelines, work safely and use protective equipment. If these precautions are implemented effectively, even though we encounter harmful substances at work, there is far less chance of them harming our health.
Essential Protective Measures
To determine the correct protective measures necessary, it is important to carry out a risk assessment. A COSHH risk assessment concentrates on the hazards and risks from hazardous substances in your particular workplace. The hazards and protective measures may vary significantly between workplaces.
The basic steps of a risk assessment are as follows:
- Identify the hazards
- Assess the risks
- Control the risks
- Record your findings
- Review your controls
Identify the hazards
To begin to identify which substances may be harmful you can:
- Look at the labels on any chemicals that you routinely use in your business for any warnings or precautions
- Read product data sheet ingredient lists (contact your suppliers if necessary)
- Think about harmful substances that are created due to the nature of your business (such as dust/fumes from cutting, grinding, sanding etc)
Workplace exposure limits (WELs) are in place to protect workers’ health. They indicate workplace exposure limits approved by the Health and Safety Executive (HSE). WELs are concentrations of hazardous substances in the air, averaged over a specific period of time:
- Any substances with WELs are considered harmful
- There are thousands of substances used in workplaces around the UK and approximately 500 of them have WELs
- EH40/2005 Workplace exposure limits is a publication that lists all current GB WELs
- The list linked above is legally binding under COSHH
Careful monitoring can check whether harmful substances are below their WEL in the air that workers breathe whilst performing a task. If substances are found to exceed safe limits, new controls will need to be put in place.
Assess the risks
To assess risks you need to decide who might be harmed and how. You should think about:
- The different ways substances may enter the body (through skin contact, being breathed in etc) and the effects of such exposure
- How often employees work with these substances and for how long
- Who else could be exposed (subcontractors, visitors, members of the public etc)
- What measures you are already taking to control the risks
- Any further action required to control the risks
- Who needs to carry out the action and when it needs to be done
Control the risks
After assessing and identifying risks, the next step is to think about the different measures that you can take to control them:
- Elimination: Can you eliminate the risks altogether by making substitutions or changing your processes to avoid the harmful substance being used/created at all?
- Containment: Can you contain the risks by using ventilation equipment, enclosing the process or minimising handling times?
- Systems of work: Can you improve your systems of work by restricting access to authorised personnel only or improving systems for storage/disposal of waste?
- Cleaning: Could you improve your cleaning methods to reduce exposure to hazardous substances and dust? Is your cleaning schedule as effective as possible? Could you redesign your systems or workplace to make cleaning easier and more efficient? Do you have the correct tools and equipment on hand to deal with spillages quickly and safely?
- Personal protective equipment (PPE): PPE (such as masks or other protective clothing and tools) should be provided to protect workers in conjunction with other protective measures and should never be considered as the only option.
- Information and training: All workers should be informed about the outcome of any risk assessments, what hazards and risks (including WELs) there are and how they should protect themselves and others. They should also be trained on how to use PPE and what to do in the event of an accident or incident.
Record your findings
You should make a written record of the findings of your COSHH risk assessment. If you employ more than five people you are required to record your findings; however, it is good practice for everyone to write down the steps they have taken to protect their workers and reduce risks, regardless of the size of their business.
Review your controls
You need to review your risk assessment periodically, especially in line with:
- Any legislative or policy changes
- When your systems of work change
- If you change the substances you use
- A significant change in staff
- An accident, incident or near miss
You should update your risk assessment with any changes that are made.
Essential protective measures under COSHH may include installing ventilation systems, performing air quality checks, implementing health surveillance systems to check workers are not suffering occupational ill health and providing personal protective equipment (PPE).
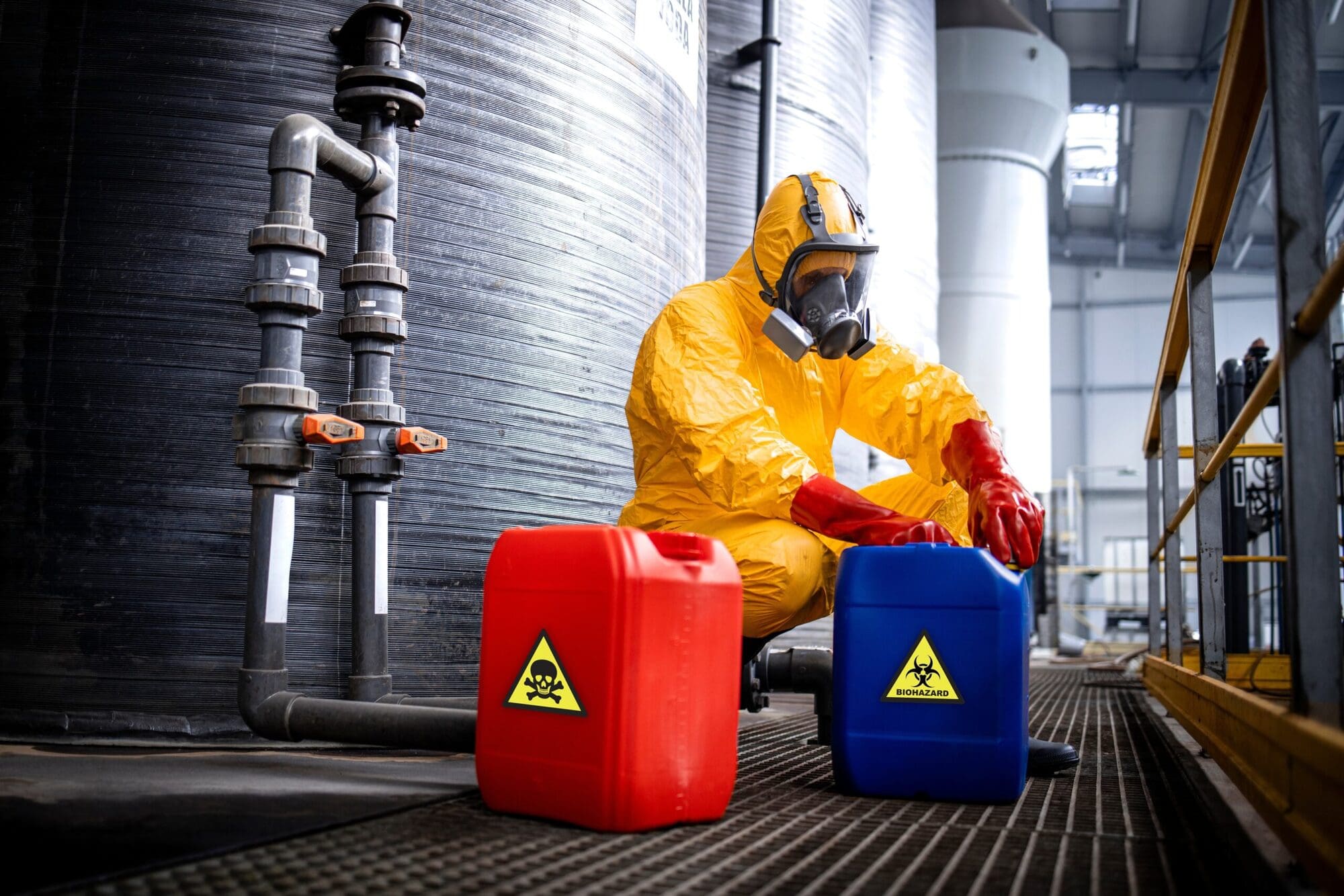
Personal Protective Equipment (PPE)
Personal protective equipment should be used as a last resort when all other measures are inadequate to control the risks at work. The Personal Protective Equipment at Work Regulations 1992 and the Personal Protective Equipment (Enforcement) Regulations 2018 are key pieces of legislation that relate to PPE at work.
Employers are responsible for providing, replacing and paying for PPE and should ensure that it is:
- Fit for purpose
- Safe and well maintained
- Hygienic
- Well fitting
- Complete with instructions
- Used correctly
Personal protective equipment is only effective whilst it is being used/worn, and if it fails or is misused, it will provide no protection at all.
Some common types of PPE that relate to COSHH include:
- Protective clothing (such as aprons, overalls)
- Gloves
- Eye protection (such as goggles)
- Masks
- Protective footwear
- Respirators
Employees need to know how to correctly use PPE, where it is kept and why/when they need it. Training in how to use PPE should include:
- Where in the workplace PPE is located
- Why and when it needs to be used
- Using the correct PPE for the job being done
- How to fit it correctly
- Does the PPE require cleaning/maintenance/replacement? How and when to do this and who is responsible for it
- Does it interfere with the task in hand? Does it introduce another potential health risk such as overheating or restricted vision?
- How to dispose of PPE safely and appropriately
Training and Education
Training and education for employees working with substances hazardous to health is necessary to ensure compliance and safe working practices.
Employers have a duty to provide appropriate training, education and information to all workers affected by COSHH. Training and education around COSHH can be done onsite by a manager/supervisor or an external instructor, offsite in a classroom setting (such as a local college) or as an online course.
Basic training and education should cover:
- What practices/products in the workplace pose a risk to health
- How to work safely to minimise the chance of harm (including using products correctly and using PPE)
- What to do in the event of an emergency
- Who the appointed first-aiders are
Employees should also be informed of any major changes (or planned changes) to working practices or substances, as well as any legislative changes.
COSHH training should also teach employees about the importance of safety data sheets, including:
Where safety data sheets are kept and why they are important
Safety data sheets contain all of the necessary information about products used. In the event of someone being exposed to a substance or chemical, the data sheet can provide information to emergency services or doctors at the hospital. This means that the right treatment can be given more quickly, meaning there is a greater chance of a full recovery. If someone has been in contact with a hazardous substance, time is of the essence. To save time, it is best practice to take the whole folder to the hospital rather than looking through for the right data sheet.
Emergency Procedures
Occasionally, even with robust training procedures in place, an accident or incident can occur. It is important that everyone at work is aware of the procedures for dealing with an emergency, such as:
- A spillage
- Accidental exposure to a hazardous substance
Training in emergency procedures relating to COSHH should clearly address:
- The correct equipment to use to deal with the emergency (e.g. a spill) including protective equipment and decontamination products
- The correct procedures to deal with a casualty
- Arrangements to deal with waste created
- How to call for help or call emergency services
Although emergencies at work are rare, the more prepared the workforce are for an emergency, the less likely they are to panic or react in an unhelpful way. Employers are also responsible for ensuring that there is at least one fully stocked first aid box on site and an appointed person to deal with first aid arrangements.
Case Studies
Case Study 1 – Solderer develops asthma at a large company in Gloucester
An employee working for a large multinational company in Gloucester for almost a decade developed occupational asthma. He was employed between 1995 and 2004 and was exposed to rosin-based colophony solder fume during his career as a solderer.
His health began deteriorating from 1999 onwards which caused him to take time off work due to breathing difficulties
A HSE investigation found that the company did not put adequate controls in place to protect workers from exposure to hazardous substances. The company failed to install fume extraction equipment to remove rosin-based fumes from the workroom air.
Furthermore, the company was directed to substitute their rosin-based solder with rosin-free solder in 1999 after an assessment but failed to implement this measure until 2003.
No employees (including the solderer with asthma) were placed under a health surveillance scheme by the company.
Due to their failure to protect workers, the company in question was fined £100,000 and had to pay £30,000 in costs. The case attracted media attention and the company incurred reputational damage as a result. If they had followed directions and used essential protective measures and equipment under COSHH this whole incident could have been avoided and their employee may not have developed occupational asthma.
Case Study 2 – Company fined for six separate breaches of COSHH
Workers at a company in Bristol were working with hazardous photographic chemicals associated over a four-year period. This led to at least three of them developing allergic contact dermatitis.
One worker developed symptoms including:
- Blistered skin
- Cracked skin
- Weeping
Two others developed symptoms of allergic dermatitis, including swollen and blistered hands and fingers. One of the two claimed that they could not even button up their shirt without their fingers splitting.
The company had to pay a £30,000 fine due to breaching the Health and Safety at Work Act 1974.
They also had to pay £10,000 for each of six separate breaches of Control of Substances Hazardous to Health (COSHH) Regulations for failing to:
- Make adequate risk assessments
- Prevent or control the exposure of employees to chemicals
- Provide any ‘health surveillance’ of employees at risk
They were also fined an additional £10,000 for not reporting a case of allergic dermatitis to the HSE.
If the company had used essential protective measures and equipment under COSHH they could have avoided being prosecuted and their workers would not have had to undergo the pain and suffering of developing allergic dermatitis.
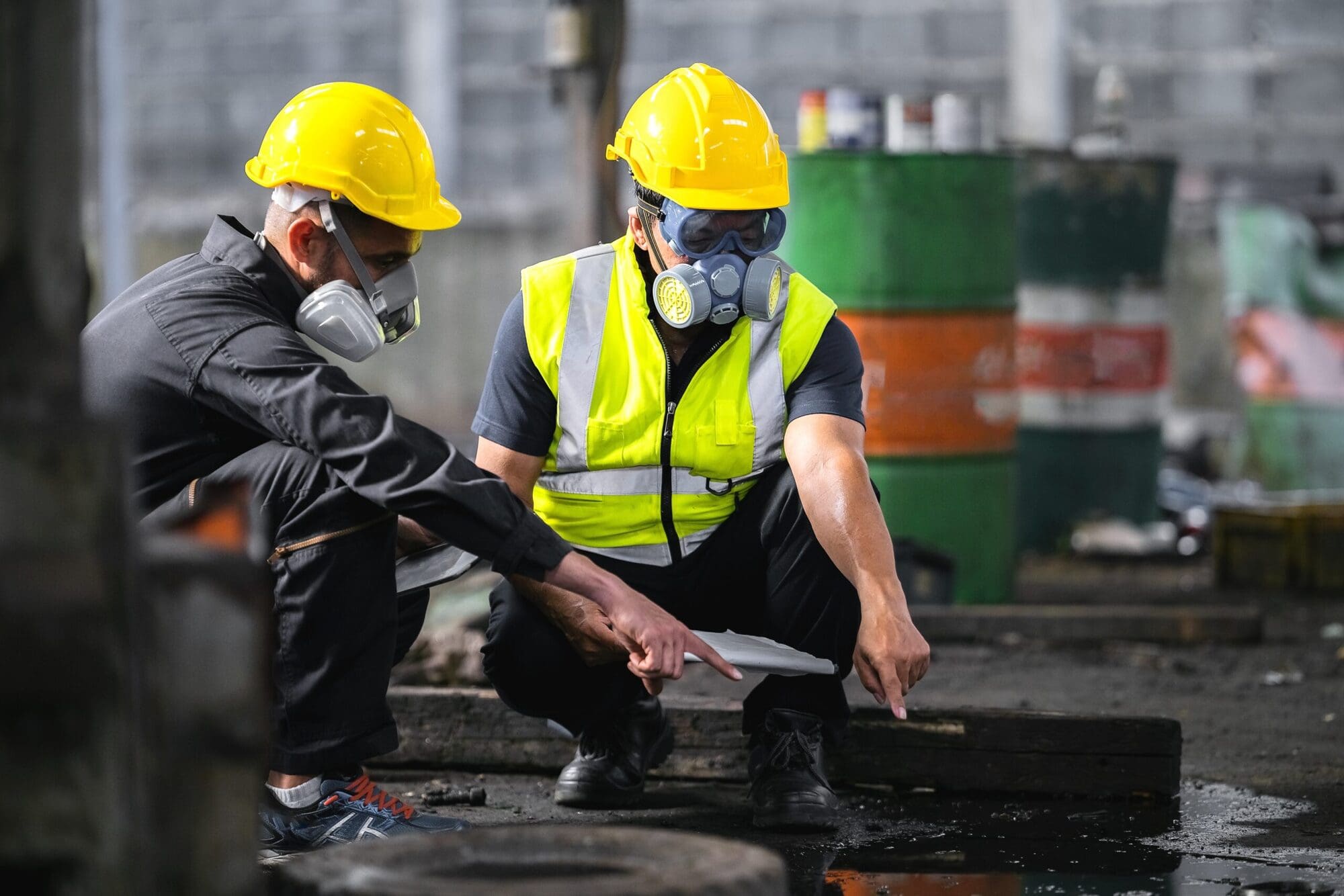
Conclusion
Effective implementation of COSHH regulations is essential for protecting workers from hazardous substances in the workplace. By understanding and employing the necessary protective measures and equipment, employers can ensure compliance with COSHH and promote a safe working environment.