In this article
What is Welding?
Welding is a type of fabrication process where materials (usually metals) are joined together using high temperatures. Heat is applied to the edges of each material to melt them and then a filler material is typically added to the joining. The parts are then left to cool and fully fuse together, which creates a strong permanent join.
There are several different types of welding processes, including:
- Arc Welding: Using an electric arc to melt the metals.
- Gas Welding: Using a flame to heat and melt the metals.
- Laser Welding: Using a laser beam to melt the metals (this method offers more precision and is often quicker).
Although heat is the most common method for fusing materials, there are also types of welding that don’t use heat, including:
- Solvent Welding: Using chemicals to fuse materials together (usually thermoplastics).
- Solid-state Welding: Applying pressure, or pressure in combination with heat, to fuse materials.
- Diffusion Welding: The materials are heated to a temperature that is not high enough to melt them but where atomic diffusion occurs and the welded together.
Welding is used in a huge number of industries, including construction, aerospace, manufacturing, making and repairing vehicles, underwater welding (e.g., ships, submarines and offshore platforms), welding pipes, tanks and pressure vessels, making heavy equipment (e.g., farming, mining and earth-moving equipment) and repair and maintenance.
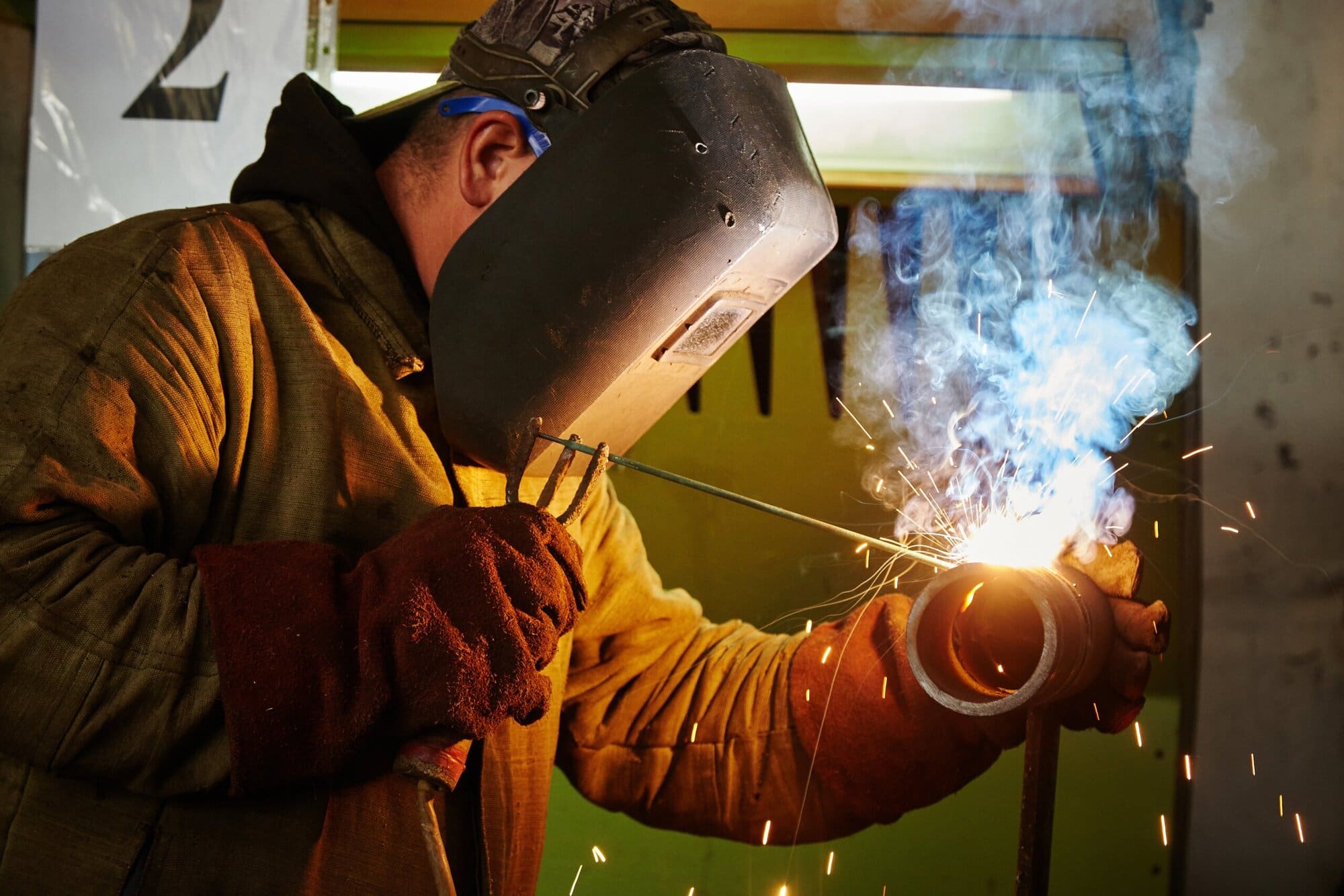
What are the Health and Safety Risks When Welding?
There are many potential health and safety risks when welding, several of which can cause significant harm and even be life-threatening. The main risks are:
Welding Fumes
Welding fumes are a complex mixture of airborne particles and gases that are produced when metals are heated during the welding process. These fumes may be visible as smoke or mist or may be invisible and require specialised equipment to detect them.
One of the most significant health and safety risks associated with welding is the risks associated with welding fumes. The effects of being exposed to welding fumes can be immediate, with the welder experiencing negative effects soon after exposure. This could include irritation to your throat and lungs, skin irritations or infections, irritant-induced asthma, metal-fume fever (a flu-like illness) or pneumonia.
The effects of being exposed to welding fumes can also be long-term and potentially life-threatening. This could include lung cancer and chronic obstructive pulmonary disease (COPS). These illnesses are more likely to occur if there is repeated exposure to welding fumes. The Health and Safety Executive (HSE) estimates that between 40 and 50 welders are admitted to hospital every year because of exposure to welding fumes.
UV Radiation
Welding using electrical arcs and laser welding produces UV (ultraviolet) radiation. As the UV light reflects off surfaces, this can be hazardous to a person’s eyes and skin. It can cause immediate symptoms, such as burns and arc eye (also known as welder’s flash), which is a painful inflammation of the cornea caused by short-term exposure to UV radiation that causes symptoms such as eye pain, tearing and light sensitivity.
The severity of the effects of UV exposure depends on the intensity of the radiation, the length of exposure and the distance from the welding activity. There are also long-term risks of exposure to UV radiation, including cataracts, ocular melanoma (a rare type of eye cancer that has been linked to UV radiation from welding) and skin cancer. Because UV reflects off surfaces, it is not only the welder who is at risk but anyone else in the vicinity.
Working in a Confined Space
In a lot of cases, welding happens in confined spaces, for example, in tanks, pipes, vessels or tunnels where either the object being welded cannot be moved or it is the confined space itself that is being welded (e.g., welding the inside of a pipe or tank). There are many potential hazards associated with welding in a confined space, including the risks of fire and explosions, exposure to toxic fumes and gases and electrical hazards.
Working in a confined space is dangerous as the small space can trap oxygen. Welding gases, such as argon, carbon dioxide and nitrogen, can shift the air inside the space and displace oxygen or generate other gases, such as carbon dioxide. This can lead to suffocation or asphyxiation.
There is an additional risk from inert gases (noble gases), which are sometimes pumped into confined spaces to reduce the fire risk or prevent oxidation when welding. If inert gases build up and the amount of gas in the space becomes too high, you can pass out with no warning and no time to evacuate and die from asphyxiation. Lower levels of inert gases (which are still over the safe limit) can cause you to feel weak, shaky, drowsy and confused. This confusion can make it difficult for the welder to safely evacuate themselves, which can cause them to pass out and potentially die from gas exposure.
Welding can also produce harmful fumes and gases that can accumulate in confined spaces, causing respiratory irritation, dizziness, nausea and potentially long-term health issues like lung damage or cancer.
As well as the risks associated with the gases in confined spaces, welding can also ignite flammable materials and the confined nature of the space can trap these fires, which can increase the risk of an explosion. Confined spaces can also increase the risk of electrical shock due to the close proximity of equipment and the potential for accidental contact with energised parts.
Electrical Hazards
Some types of welding, specifically arc welding, involve a live electrical circuit, which poses a risk of electric shock. A live electrical circuit is used in welding to create a molten metal pool to fuse the two metals together. Electric shocks can happen when a welder makes contact with live parts, such as the electrode holder or grounded metal or when two metal objects have a different voltage. The voltage can then make a circuit through their body and cause an electric shock.
Additionally, electric shock can be caused by improperly wired machines and stray currents (e.g., when the electrical current does not run along the welding return cable but along a different path). Electric shock injuries can range in severity from minor burns and muscle spasms to more serious injuries such as heart problems, permanent nerve damage, seizures, loss of consciousness, internal organ damage (e.g., to the lungs and kidneys), cardiac arrest and even death.
There is a higher risk of electrical shock if the welding is done in damp or wet conditions or in contact with other metal surfaces, such as inside a metal tank or on a metal platform.
Thermal Hazards
Thermal hazards are the hazards associated with working with high levels of heat. This could include thermal burns from direct contact with hot metal, molten splatter or contact with the welding torch. The welder can also be burnt if they are exposed to the intense heat and radiation from the welding arc.
Prolonged exposure to heat can lead to heat exhaustion, characterised by fatigue, weakness and dizziness. It can also lead to dehydration and heat syncope, which is a sudden loss of consciousness because of a drop in blood pressure caused by heat exposure.
Exposure to thermal hazards also increases the risk of fire and explosion. Ignition sources, such as sparks, hot slag and the welding flame, can ignite flammable materials and cause fires or explosions. If there are any other flammable substances in the welding environment, such as paper, wood, chemicals or dust, this can significantly increase the risk of fire.
Noise Hazards
A noise hazard in the workplace is any noise above 85 dB(A) and the noise exposure limit is 87 dB(A). Exposure to noise hazards, particularly if you are repeatedly exposed, can damage your hearing. Welding processes, including flame cutting and arc gouging, can produce noise levels above 100 dB(A).
Prolonged or excessive exposure to these loud noises can lead to temporary or permanent noise-induced hearing loss, tinnitus (ringing in the ears) and other health issues. The severity of a noise hazard depends on factors like the loudness, duration and frequency of exposure. Welding in a confined space can also increase the risk of hearing damage as the sound may be amplified.
Ergonomic Strain
Ergonomic strain is the physical stress on your body when welding. It can be caused by welding in an awkward position (e.g., bending, twisting or welding above your head), repetitive movements, staying still for too long (e.g., crouching down for an extended period which can cause muscle fatigue and stiffness) and poor workplace set-up (e.g., welding too high or too low without proper support). It usually affects the neck, back, shoulders, wrists, hands and knees.
Why is Welding Safety Important?
Welding safety is essential because welding can be highly dangerous and has many potential risks. Welding combines intense heat, electricity, bright light, fumes and heavy equipment, all of which can be dangerous if not handled properly. If workplaces do not follow safety hazards, welding can pose a serious risk to short-term and long-term health.
Welders work with extremely high temperatures, molten metal, intense light (including ultraviolet and infrared radiation) and potentially harmful fumes and gases. Without proper safety precautions, these elements can cause severe injuries such as burns, electric shock, eye damage and respiratory issues. Over time, repeated exposure to toxic fumes can lead to chronic illnesses, including lung disease or even certain types of cancer.
As well as protecting the personal health and safety of workers, welding safety is essential for preventing workplace accidents that could endanger others. A single spark can ignite a fire or cause an explosion if flammable materials or gases are present nearby. Equipment failures, structural collapses or improper use of tools can also lead to serious injuries not just for the welder but for anyone else in the vicinity. Following safety protocols, including wearing flame-resistant clothing, using proper ventilation and checking electrical equipment can help to significantly reduce these risks.
As well as the health and safety concerns, workplaces must also consider the legal requirements. There are several laws in the UK that apply to employers, employees and any person who is responsible for managing or supervising welding operations, including:
- The Health and Safety at Work etc. Act 1974: This is the primary legislation covering occupational health and safety in the UK. It requires employers to ensure (as much as is reasonably practicable) the health, safety and welfare of their employees. Additionally, employees must take reasonable care of themselves and others and cooperate with their employer on health and safety matters.
- The Management of Health and Safety at Work Regulations 1999: These regulations require employers to carry out risk assessments for all work activities, including welding, implement necessary control measures to minimise the risks and provide training and information to employees to help them work safely.
- The Control of Substances Hazardous to Health (COSHH) Regulations 2002: COSHH applies to welding because of the exposure to fumes, gases and dusts. Under COSHH, employers must assess the risks from hazardous substances, prevent or adequately control exposure, provide proper ventilation (e.g., a fume extraction system) and offer health surveillance where appropriate.
- The Personal Protective Equipment at Work Regulations 1992: Under these regulations, employers must provide suitable PPE to anyone involved in welding, such as welding helmets, gloves, protective clothing and respiratory equipment. They must also ensure PPE is maintained, stored correctly and replaced when necessary and train workers on how to use PPE properly.
- The Electricity at Work Regulations 1989: These regulations apply to any electrical welding equipment and specify that equipment must be installed, maintained and used safely by competent, trained individuals. Equipment must also be regularly inspected and tested to ensure it is safe to use.
- The Provision and Use of Work Equipment Regulations (PUWER) 1998: PUWER requires workplaces to ensure that all tools and machinery that are used in welding tasks are suitable for the intended task, maintained and in a safe condition and only used by trained and authorised personnel.
Employers and workers who ignore these regulations can face fines, shutdowns or legal action.
Ensuring safety in the workplace also contributes to higher-quality work. When a welder is properly protected and working in a safe, well-organised environment, they are less likely to rush or make errors. This means cleaner welds, stronger joints and fewer defects, which can ultimately save time and resources in the long run. Additionally, promoting welding safety builds a culture of responsibility and respect in the workplace. It shows that workers value their own well-being and that of their team.
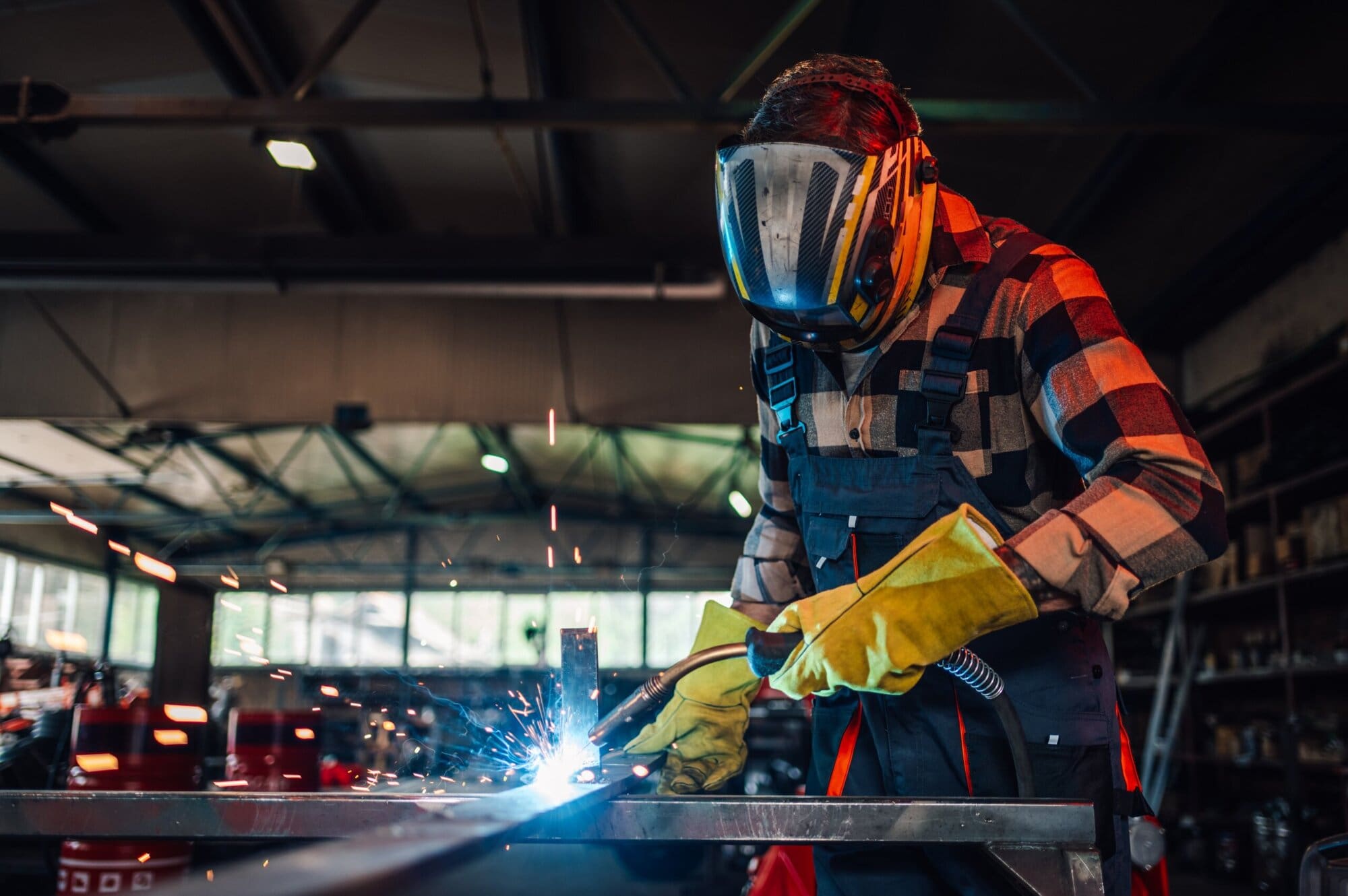
Welding Safety Precautions
Welding safety precautions are the safety practices and protective measures that help prevent accidents, injuries and long-term health issues. It doesn’t matter whether you are welding in a fabrication shop, on a construction site or at home, safety precautions can create a safer working environment and help protect the health and safety of you and others.
Some safety precautions to implement include:
Ensure adequate ventilation and fume control
Welding produces harmful fumes and gases, especially when working with metals like stainless steel or galvanised steel. To protect the health and safety of anyone working in a welding area, not just welders, workplaces should use local exhaust ventilation (LEV) or fume extraction systems. Where possible, welders should work outdoors or in well-ventilated spaces. If ventilation isn’t sufficient, anyone with an exposure risk should wear appropriate respirators.
Check equipment before use
Before starting any welding job, it is essential to check cables and connections for any wear or damage, welding machines for leaks or malfunctions and gas cylinders and hoses to ensure secure fittings and no leaks. It is also important to make sure that all equipment is grounded properly and the settings are correct for the job at hand.
Prevent fire and explosion hazards
Welding creates sparks and high heat that can easily ignite flammable materials. To reduce the risk of fire, clear the area of any flammable materials, liquids or vapours and use welding screens to protect other people and contain any sparks. It is also recommended to keep a fire extinguisher or fire blanket nearby. If you are welding near flammable structures, protect them using fire-resistant blankets or barriers.
Follow safe working practices
Safe work practices can make a big difference in welding safety. Recommended practices include:
- Never weld in confined spaces without proper ventilation or a safety attendant.
- Use a welding positioner or adjustable table to avoid awkward positions and postures.
- Let hot materials cool before handling them and clearly mark them as hot.
- Keep your work area clean and organised to avoid tripping hazards or accidental burns.
Be properly trained and informed
Only trained and competent individuals should perform welding tasks. It is important to stay up to date with safety standards, manufacturer instructions and legal requirements, including guidance from the Health and Safety Executive (HSE). Welders, employers and anyone overseeing welding activities should attend regular safety briefings or refresher training to ensure their knowledge and training are up to date.
Protect others
Protecting others is a key part of welding safety. This could be other employees or the general public. It is important to use welding screens or curtains to protect other people from UV light and flying sparks, particularly when other people may not be wearing the appropriate PPE. Before beginning any welding task, post warning signs or completely restrict access to the welding area. It is also recommended to inform nearby workers before starting welding to ensure they take the appropriate precautions as well.
Controlling the Risks from Welding
Controlling the risks from welding requires you to identify the hazards and put control measures in place to eliminate or reduce the risks of these hazards. An important way of doing this is by conducting a risk assessment. Before any welding job, it is important to identify ALL the potential hazards. You should then assess who is at risk of harm and how this harm could happen. The risk assessment should consider things like:
- The type of welding process being used.
- The amount of welding that is being done.
- The level of fumes being produced.
- The size of the parts being welded.
- The type of metal that is being welded.
As part of the risk assessment, the assessor must determine how likely and severe those risks are. All findings from the risk assessment should be properly documented with a clear plan of how to control the risks. Some people may be at higher risk than others and it is important to document this in a risk assessment. For example, a worker with asthma, a worker who is pregnant or a worker who has previously inhaled fumes may be at higher risk from welding fumes than other workers and may, therefore, require more stringent control measures.
In some cases, it may be possible to eliminate the risks completely by using an alternative process (not welding). For example, you could use a cold joining technique, such as mechanical fasteners and adhesives. Alternatively, it may be possible to automate or mechanise the process to remove the risks to the worker. When this is not possible, it is essential to control the risks as much as possible to protect the health and safety of everyone involved.
Recommendations of how to control the risks from some of the main welding hazards include:
Welding Fumes
Exposure to welding fumes poses short-term and long-term risks to anyone exposed to them. These risks can be significantly reduced by implementing the following controls:
- Use local exhaust ventilation (LEV) or fume extraction systems at the source of the fumes.
- Wear respiratory protective equipment (RPE) when ventilation isn’t enough.
- Clear any coated, painted or dirty materials before welding.
- Switch to low-fume welding techniques or consumables if possible.
- Limit the amount of time you are exposed to welding fumes and rotate tasks where practical.
- Follow COSHH regulations and carry out proper fume risk assessments.
- Use a different consumable or a welding process that generates less fumes.
UV Radiation
To reduce the risk of ultraviolet radiation, some controls you can implement include:
- Always wear a welding helmet with the correct shade filter.
- Use auto-darkening helmets if you frequently stop and start when welding.
- Cover all parts of your skin with flame-resistant PPE (no exposed skin).
- Use welding curtains or screens to protect nearby workers.
Working in a Confined Space:
Although working in a confined space can be high risk for welders, there are some ways to control the risks, including:
- Consider if there is a way to complete the welding without going into the confined space.
- Ensure there is an emergency rescue plan in place and that all necessary personnel are aware of the plan.
- Use forced ventilation to keep air fresh and remove fumes.
- Test the air for oxygen levels and toxic gases before and during work.
- Ensure a trained confined space attendant is stationed outside the confined space for the entire duration the welder is inside.
- Ensure a permit-to-work system has been obtained before entering the space.
- Use the necessary PPE, including respirators, gas detectors, atmospheric monitors and a full-body harness.
Electrical Hazards:
If electrical hazards are not controlled, this can result in shocks, burns, electrocutions or fires. To control the hazards, it is important to:
- Inspect all cables, electrode holders, connectors and plugs regularly (e.g., is the insulation intact, are the leads undamaged).
- Make sure all electrical equipment complies with the British (BS) standards.
- Ensure welding machines are properly grounded.
- Ensure any fixed welding equipment is installed by a qualified person and installation complies with the manufacturer’s instructions.
- Keep gloves and hands dry and insulated and avoid welding in wet conditions.
- Never touch live parts with bare hands or wet PPE.
- Turn off and unplug equipment during maintenance or electrode changes.
- Use an insulating mat so you are not in contact with wet or conductive surfaces.
Thermal Hazards, Fire and Explosion:
To reduce the risks of thermal hazards, workers should:
- Wear heat-resistant gloves, boots and flame-resistant clothing.
- Use welding screens to contain sparks.
- Mark or cordon off hot materials after welding.
- Avoid loose clothing that can catch fire.
- Allow parts to cool before handling them or use tongs or tools to handle them.
- Clear away any flammable materials, such as wood, cardboard and fabrics, before beginning welding.
- If the area is not 100% clear (e.g., if some flammable materials cannot be removed), maintain a fire watch during the welding and for at least 30 minutes afterwards.
- Clear away any flammable liquids before beginning welding.
Noise Hazards:
Grinding, plasma cutting or certain welding processes can exceed safe noise levels, which can lead to hearing damage over time. The controls below should be implemented to reduce the risk:
- Conduct a noise risk assessment.
- Use hearing protection (e.g., earplugs or earmuffs) when levels exceed 80 dB(A).
- Rotate tasks or limit time in noisy areas.
- Use noise-dampening mats or panels where practical.
- Maintain equipment to reduce unnecessary noise.
Ergonomic Strain:
Repetitive movements, awkward postures, heavy PPE and prolonged static positions can lead to muscle fatigue, joint pain and long-term injuries. To reduce the risk, it is important to:
- Use welding positioners or adjustable tables to bring the welding work to a better height.
- Take breaks regularly to stretch and move.
- Wear properly fitting PPE to reduce any unnecessary strain.
- Plan the setup before welding to avoid awkward postures.
- Use ergonomic tools and anti-fatigue mats if you are standing for long periods.
- Rotate tasks to give different muscle groups a rest.
Personal Protective Equipment
Personal protective equipment (PPE) is essential in welding and is the last line of defence between the welder and a number of hazards. PPE can protect you from burns and heat, UV radiation, harmful fumes, nose hazards and electrical shocks. The type of PPE required will depend on the type of welding that is being done, the equipment being used, the potential hazards and the environment (e.g., is the environment wet, are flammable materials present).
Common PPE used by welders includes:
Welding helmet
A welding helmet protects the welder’s face and eyes from ultraviolet or infrared radiation, sparks and molten spatter. The helmet should have a properly rated filter lens (whether a shade is required depends on the type of welding). If possible, an auto-darkening helmet should be worn as this can increase comfort and visibility.
Safety glasses or goggles
Safety glasses or goggles should be worn under the helmet to protect the welder’s eyes from dust, grinding particles and flash. The glasses or goggles must meet impact protection standards.
Flame-resistant clothing
Welders should wear flame-resistant clothing that protects their skin from sparks, spatter and heat. They should avoid any synthetic materials which can melt and fuse to the skin and should wear welding jackets, aprons and trousers made from leather or treated cotton. It is important to wear long sleeves and closed collars to protect from sparks and UV rays.
Welding gloves
Heavy-duty leather gloves that are insulated and heat-resistant can help protect your hands when welding. Welding gloves are specifically designed to allow dexterity while protecting the hands from burns and electric shock.
Safety boots
Steel-toe, heat-resistant boots can protect your feet from dropped metal and hot surfaces. The boots should have metal guards for added protection.
Respiratory protection
Respiratory protective equipment (RPE) is required when ventilation is inadequate. The most effective respirator is a power air respirator or a supplied air respirator that has an APF (assigned protection factor) of at least 20. Alternatively, a tight-fitting respirator (either disposable or re-usable) can be used, although these can be uncomfortable if worn for a long time.
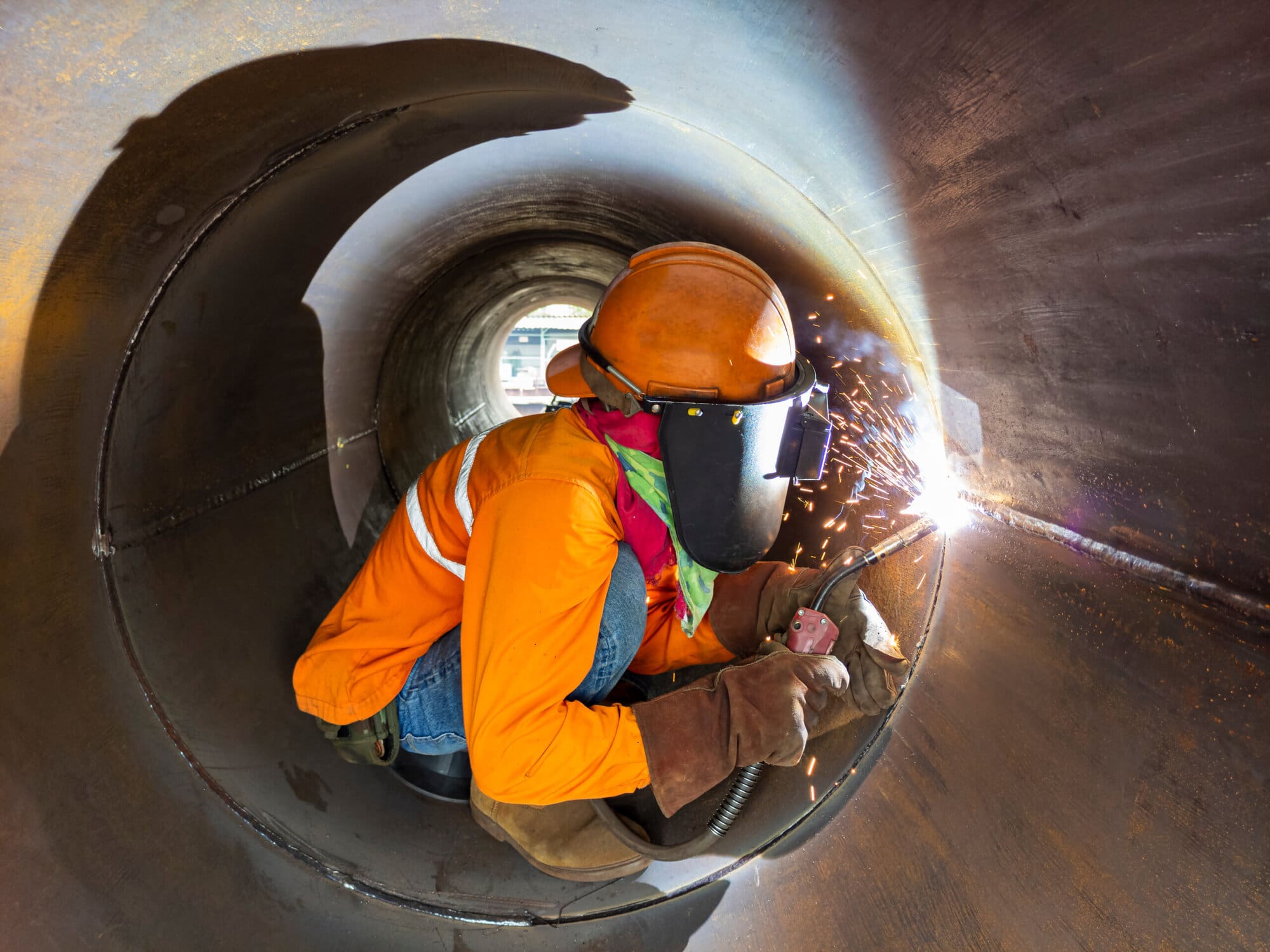