In this article
The impact of mismanagement of hazardous substances, poor safety and accidents can be fatal or result in serious injuries, with research indicating that up to a quarter of UK workers are exposed to a hazardous substance in some way in the workplace. Moreover, COSHH-related illnesses and conditions may not be apparent for several years, with small quantities of exposure to substances that are considered low risk over a long period of time potentially having a significant impact on the long-term health of workers.
In this article, we will examine the basics of COSHH and its relevance to a variety of industries. It will focus primarily on the storage of chemicals; in particular, how you store hazardous substances as part of the COSHH requirements. We will also discuss the relevant primary hazard symbols, as well as the various ways we can ensure that appropriate measures are put in place to control, prevent or minimise the risk.
What is COSHH?
COSHH stands for the Control of Substances Hazardous to Health, and it is an acronym used to refer to legislative measures put into place to ensure safety in the workplace. Ultimately, these regulations mean that employers have a duty to prevent or control exposure to hazardous substances.
Contact with such is dependent on your industry, but it is believed that some form of COSHH substance is used in virtually every workplace. A breach of the regulations is punishable by an unlimited fine, and there are a number of precautions that need to be taken. COSHH regulations were first created in 1999 and later amended in 2002 in line with EU directives. However, it should be noted that the regulations may be subject to change again in 2021 after the Brexit transition period.
What are COSHH substances?
COSHH covers substances that are hazardous to health, including:
- Chemicals.
- Products containing chemicals.
- Fumes.
- Dust.
- Vapours.
- Mists.
- Nanotechnology.
- Gases and asphyxiating gases.
- Biological agents – germs.
- Germs that cause diseases such as leptospirosis and germs used in laboratories.
Hazardous substances refer to individual chemical substances as well as preparations that include a mixture of one or more such as paint, cleaning materials and pesticides.
However, these regulations do not cover lead, asbestos or radioactive substances, with these being subject to their own specific regulations. As well as using chemicals, some manufacturing processes may also create substances which could be harmful to employees, contractors and other people.
What is classed as hazardous?
A hazardous substance is one which features one or more inherent hazardous properties, such as flammability, explosiveness, corrosiveness or toxicity.
This may mean that it has the potential to result in long-term damage to the health of employees, including injury to lungs, skin, nose, mouth, genes, eyes, the central nervous system and internal organs. There are three main routes of entry for a person to be affected by a harmful substance, including inhaling, absorption through the skin and ingestion.
Alternatively, the substance may pose a risk of combustion or explosion or due to its ability to oxidise. It is important to note that although there is a wide range of substances that have the potential to cause harm, when used properly and in line with the appropriate protocol, they rarely do.
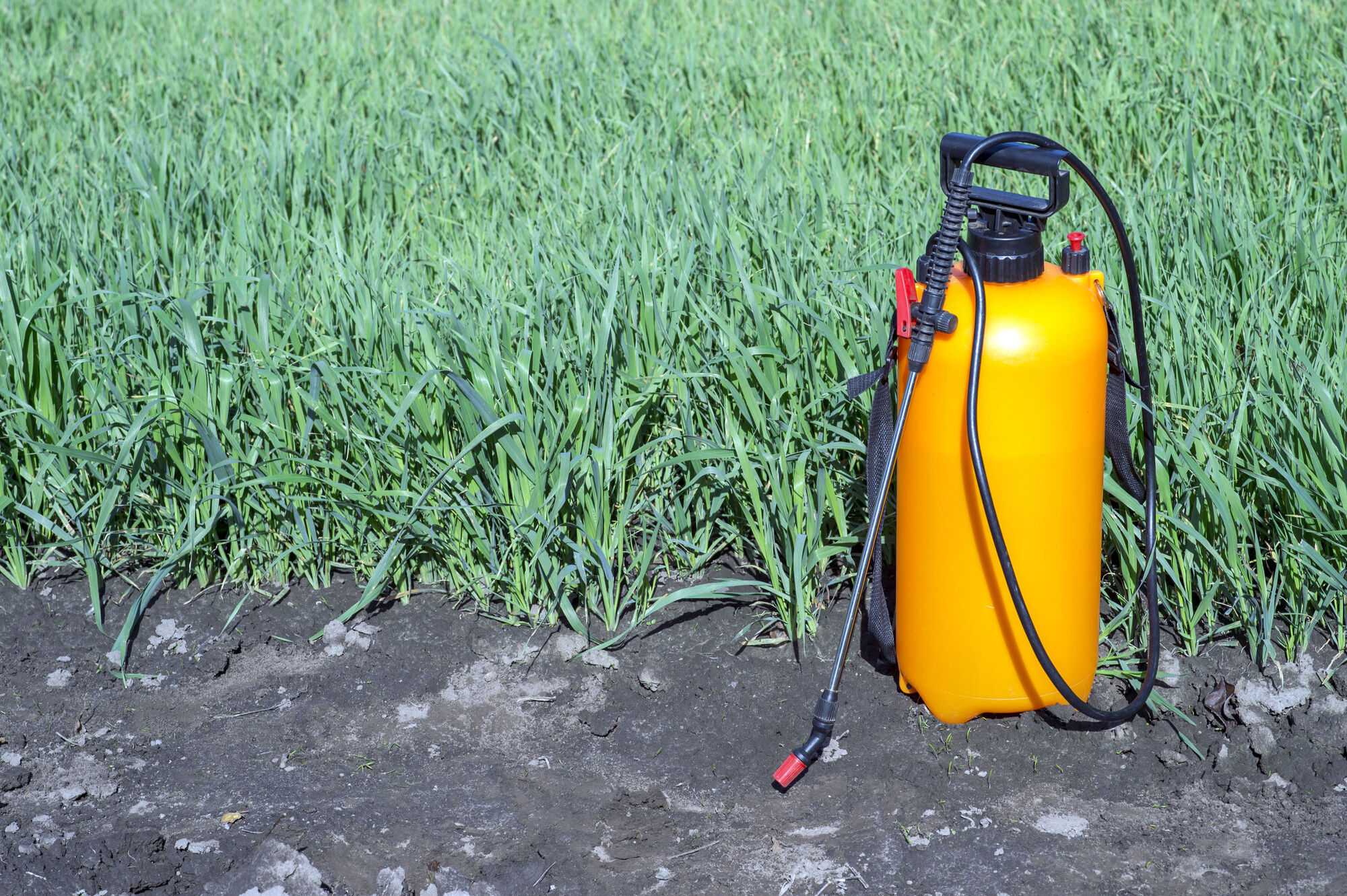
How are businesses responsible for COSHH?
In order to ensure compliance, employers must assess risks related to the COSHH substances used within the workplace.
They will then need to determine measures to prevent or adequately control exposure. Plus, they should be aware of the hierarchy of control measures that must be followed in relation to the risk associated with a specific substance.
In summary, chemical storage should be in accordance with the manufacturer’s instructions and safety data sheets. The storage area should include sufficient space, be tidy and well organised, well lit and well ventilated. It should also have a floor that is resistant to chemical damage and is easy to clean and maintain.
Ultimately, the organisation or employer is responsible for the implementation of COSHH, with obligations including:
Assessment
In order to identify potential hazards, businesses must complete regular COSHH and risk assessments. The assessment concentrates on the hazards and risks posed by the use or production of specific substances, with steps including:
1. Identify potential hazards.
2. Identify who could be harmed and how.
3. An evaluation of the risks.
4. Establish precautionary measures.
5. Record findings.
6. Implement changes.
7. Review and evaluate.
Depending on the type of COSHH substance and its particular properties, the assessment should include consideration of work circumstances including safe handling, storage, transportation of hazardous substances and appropriate waste removal.
Control
COSHH requirements mean that employers have a responsibility to control any substances that may be hazardous to health. If it is not possible to completely prevent exposure by using a different substance, measures could include checking for damage and leaks regularly, ensuring that damaged containers are replaced immediately and making sure that any spills are cleaned up immediately.
Waste should also be segregated from other substances and labelled appropriately. Furthermore, it is also essential for businesses to be aware of the applicable Workplace Exposure Limits (WELs) for the substances used. This refers to the limits of legal maximum exposure and is dependent upon the type of hazardous substance used for the work activity.
Monitor
Businesses are legally obligated to monitor and maintain the control measures that they have put in place as part of the COSHH assessment. This may include health surveillance, which refers to a regular system of ongoing health checks.
This approach is effective at ensuring any ill health is discovered early, at evaluating risk, and it is effective at reinforcing training and education. Moreover, health surveillance also provides a platform for employees to raise concerns about the use of hazardous substances in the workplace. Depending on your type of business, this may or may not be a legal requirement.
Protect
Businesses have a duty to protect workers from harm and to reduce the risks associated with the substances required for the work activity.
An example of a protective measure is the use of PPE, which stands for Personal Protective Equipment. Although this can add an extra layer of safety, it should be considered the last line of defence. The use of some hazardous substances may also require employees to wear Respiratory Protective Equipment.
Training
It is imperative for companies to ensure that all employees understand the necessary precautions related to the use, storage and transportation of COSHH substances.
As well as being aware of which substances are hazardous, it is also important for workers to know why they are hazardous and what damage they could cause. COSHH training can go some way to ensure that control measures are maintained, but it needs to be regularly updated to ensure that it is in line with current guidance.
Report
Businesses are also required to report and record accidents, spillage and breakages in line with the Reporting of Injuries, Diseases and Dangerous Occurrences Regulations (2015). Most incidents should be reported online, but there is a telephone service for reporting fatal and specified injuries only.
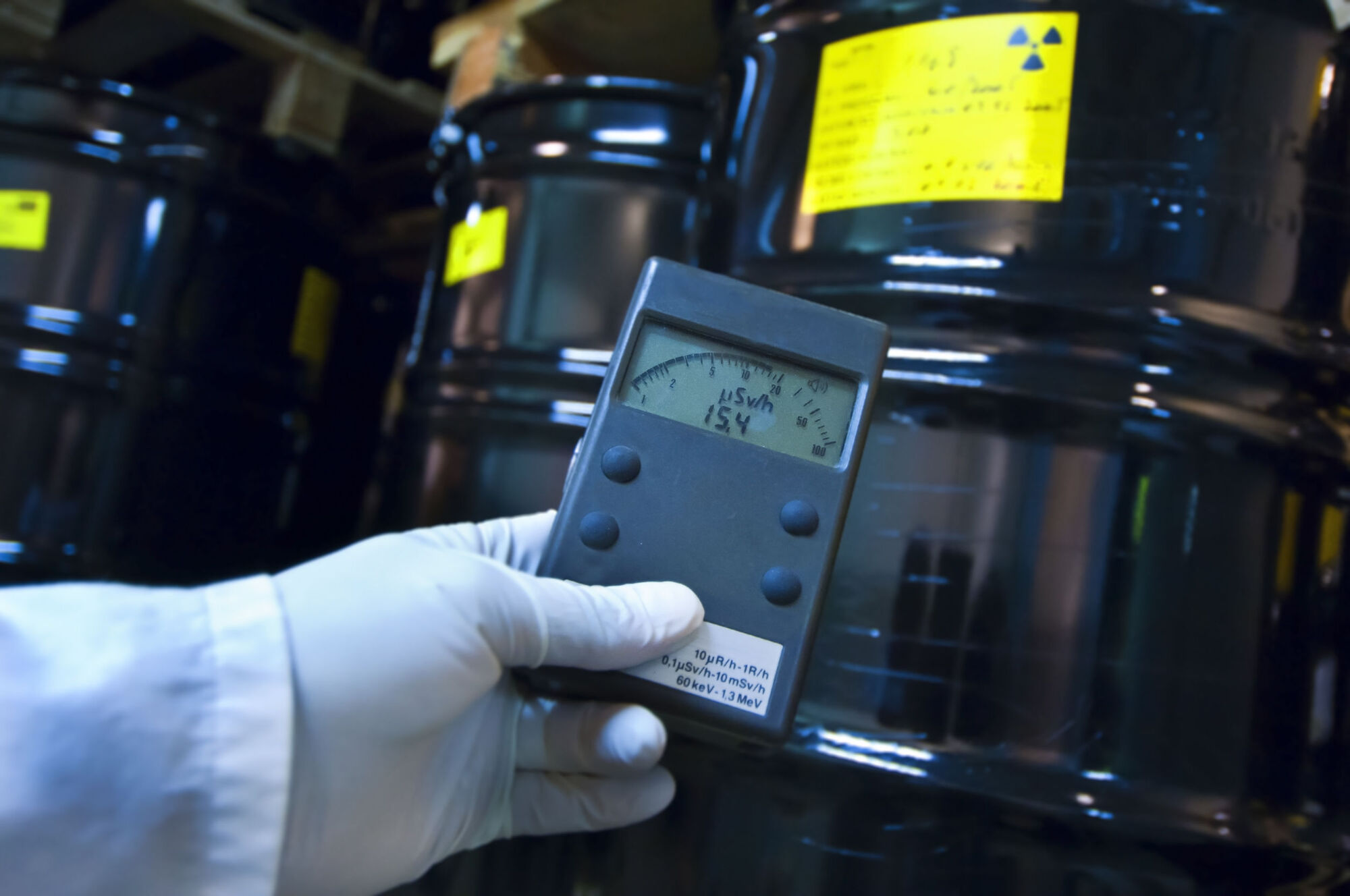
Where can COSHH substances be stored?
As part of COSHH regulations, you must store hazardous substances in a manner that minimises risk and limits exposure.
This helps to ensure the protection, health and safety of people on-site and protects the environment. COSHH substances should be stored in a designated storage area, such as process areas, workrooms and labs.
However, where and how you store them will depend on the specific type of substance.
Factors to consider include:
Safety Data Sheets (SDS): There is no singular way to store COSHH substances and the manner of storage will depend on the type of substance that is being used. As a result, it is important to ensure that the manufacturer’s instructions on the Safety Data Sheets (SDS) are strictly followed. Manufacturers and suppliers are legally responsible for supplying these, and a downloadable version should be available on the supplier’s website.
Location: When conducting your COSHH assessment, it is important to consider the layout of your workplace to ensure the most appropriate storage area. Hazardous substances should be stored in an area with a clear exit, and it is also advised that the storage area should be close to washing facilities. Substances may also need to be stored in appropriate COSHH cabinets, and should always be stored separately from any others. Furthermore, storage areas should be separate from process areas.
Maintenance: To ensure that control measures are successful, storage areas should be kept organised and well maintained. For example, container labels should be facing outwards, with heavier items on the lower shelves. Make sure that you dispose of materials when they are finished with and pay attention to use-by dates. Also, appropriate hazard signage should be displayed, which we will discuss in more detail below. With regards to regular maintenance, it is also important to ensure that containers are kept in good condition so that they remain suitable for the task.
Capacity: There are strict regulations regarding the capacity of containers, which is typically around 110% volume of the largest vessel. It is also important to be aware of the relevant storage limit, particularly with regard to flammable substances as these could have a large area of impact. For example, substances categorised as extremely flammable have a storage limit of 50 litres. Moreover, you should only store the minimum amount required for the work activity.
Ventilation: Storage areas should also be well ventilated, with different levels of ventilation required depending on the type of substances being stored. Ideally, COSHH substances should be kept in a secure outdoor location so that it can be appropriately dispersed with minimum risk of explosion. However, Local Exhaust Ventilation (LEV) may be required for the indoor storage of substances that produce airborne contaminants, especially when this release cannot be eliminated.
Temperature: You may also need to take the overall temperature of your storage area into consideration. For example, storage areas that are home to gas cylinders or cartridges must be kept below 50°C. There should also be no risk of ignition, such as a heater, especially when storing flammable substances.
What is of safe storage?
From a legal perspective, of safe storage would mean that all hazardous substances are stored in appropriate containers, which are appropriately labelled with correct signage and inaccessible to most. This is part of an organisation’s legal responsibilities, as proper storage can help to prevent exposure and reduce the risk of harm.
What are the primary hazard symbols?
Also known as hazard pictograms, there are primary hazard symbols related to the COSHH requirements. Employees should be aware of the meaning of such symbols and easily be able to recognise them.
Signage should be clearly displayed to indicate the presence of a potentially harmful substance. This is a requirement under the Health and Safety (Safety Signs and Signals) Regulations 1996. Classification Labelling and Packaging pictograms were implemented in 2015 to ensure similarities to international hazard symbol use, particularly with regard to the use of a distinctive red border with a white background.
The most frequently used hazard symbols include:
Toxic/Danger: Featuring a skull and crossbones, the toxic sign should be easily recognised. If it includes a T in the top left-hand corner, this means that the substance is particularly potent.
Serious/Long-term Health Hazard: Featuring a human silhouette with a white star in the centre, this sign indicates a potential risk to a person’s health. This label is used for substances that can cause severe and long-term health issues, such as cancer, respiratory diseases and genetic defects, amongst others.
Environmental Damage: The symbol of a dead tree and fish indicates danger to the environment, which could be either immediate or delayed. It is important to ensure that substances considered to be an environmental hazard are disposed of properly.
Flammable: With a symbol of a flame, this sign is featured on substances and products that are particularly high risk of catching fire. As a result, any product with the flammable symbol should be kept as far away as possible from any form of spark that could result in ignition.
Oxidising: Featuring a flame over a circle, an oxidising substance can react exothermically. This means that it has the potential to react violently with other substances and could cause or feed a fire.
Explosive: A sign used on explosive substances such as fireworks and various other types of ammunition. The exploding bomb signage indicates that there is a need for specialist care and they should always be kept away from any heat source.
Compressed Gas: An image of a gas cylinder. Substances that are gas could cause an explosion if heated. As a result, these need to be kept away from direct sunlight and sources of heat.
Harmful/irritant: This hazard label used to be a cross but it has been changed to an exclamation mark. This indicates that the container contains a hazardous substance which may be damaging to a person’s health.
When do you need to use a COSHH cabinet?
COSHH cabinets have been designed for secure chemical storage. While they are not able to remove the risk entirely, they can be an effective way of managing it.
COSHH cabinets should also be appropriately colour coded as well as clearly identified with the appropriate hazard symbol. They are leak-proof, secure, reinforced and specifically designed to contain various substances including the required sump to collect spillage.
The most frequently used COSHH cabinets are:
General COSHH Cabinet: Often yellow, these are designed to contain general hazardous substances.
Acids and Alkalis: Usually white and made from steel, these have been created to store acids and alkalis that are dangerous and corrosive. However, acids and alkalis should not be stored together.
Agrochemical and Pesticide: COSHH cabinets for agricultural and horticultural purposes; these are vented so that hazardous gases can escape.
Dangerous and Flammable: Suitable for a range of flammables such as petrol and paint thinners, these have a high melting point and have been designed to stop the spread of fire.
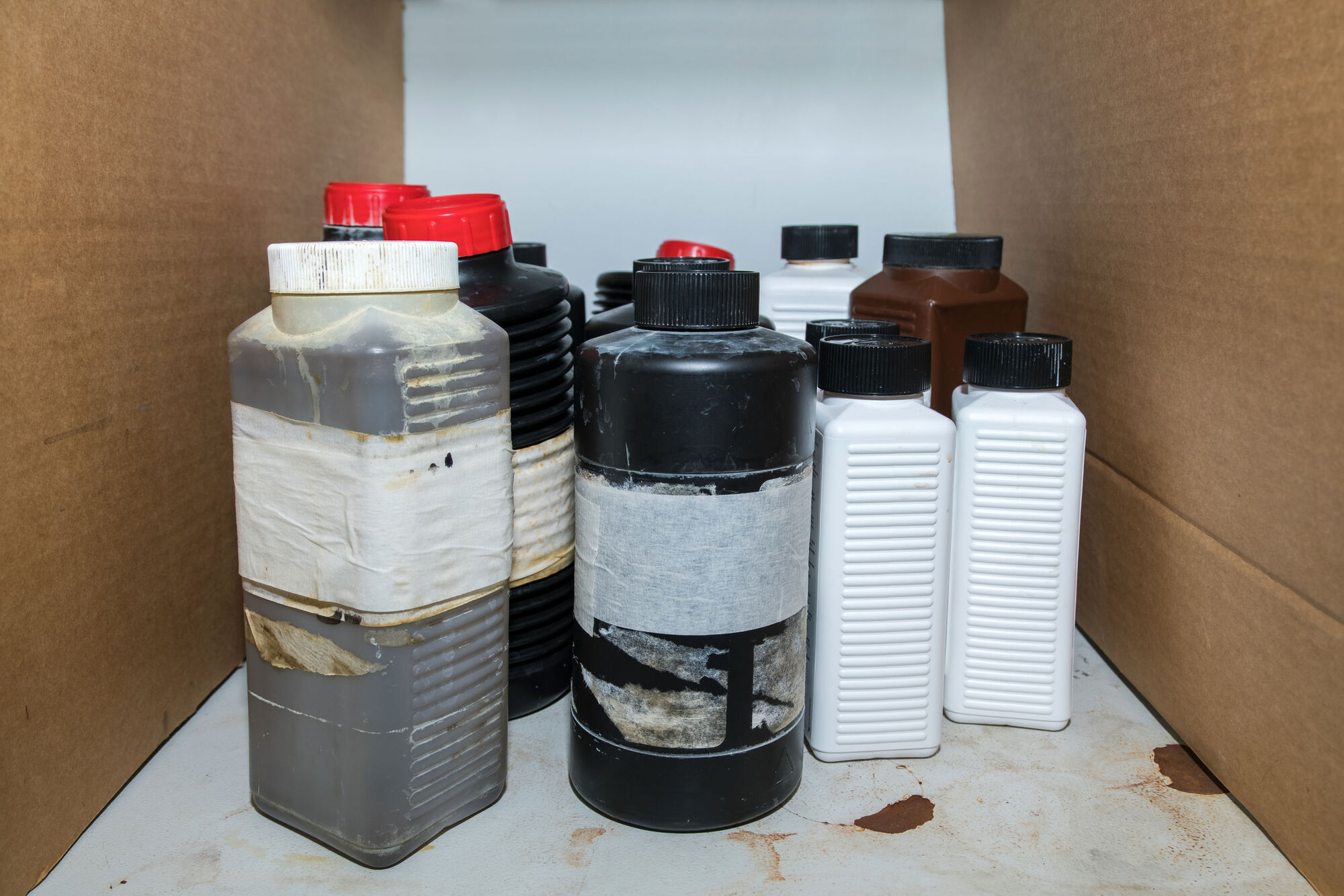
What are the requirements for fire-resistant cupboards and bins?
Fire is a common danger in a range of different workplaces and industries, and fire-resistant cupboards and bins are essential for appropriately storing flammable substances. These will not wholly contain or survive the fire but it will reduce the risk of a fire starting or spreading to prevent injury and to ensure that there is time for people to escape.
If substances have the potential to cause fire or explosion, storage of flammable or explosive substances must also comply with the Dangerous Substances and Explosive Atmospheres Regulations. Furthermore, they should always be stored separately from any other dangerous substances, and should never be stored near a source of ignition or heat.
Requirements include:
- The container should be made of a material such as steel so it is capable of the required fire resistance.
- Joints should be free from openings.
- Should include welded seams to prevent fire seeping through the gaps.
- The door must be reinforced and non-combustible and fit tightly to the frames.
- Hinges and fastenings must have a melting point which is greater than 750°C.
- Should feature liquid-tight sumps and multiple shelf levels.
How should businesses keep COSHH storage areas secure?
COSHH storage areas must be kept secure to prevent access to dangerous materials. This could be accidental access, but companies also need to take into account the potential for arson or vandalism.
As a result, storage areas containing COSHH substances should be kept locked at all times and not left unattended.
Security measures could include:
- Locks with only designated key holders.
- Metal fencing.
- Security alarms.
- Security patrols.
- Lockable covers.
- Welded mesh.
Summary
Demonstrating due care for the health and wellbeing of everyone in the workplace, COSHH regulations have been in place for more than 25 years and apply to a whole host of different businesses.
This article has broken down the multiple points businesses need to consider for the storage of chemicals.
In summary, businesses are responsible for:
- Learning about health hazards and knowing their impact.
- Deciphering how to prevent harm to health.
- Conducting risk and COSHH assessments.
- Providing control measures.
- Making sure controls are implemented.
- Keeping all control measures in good order.
- Ensuring employees are equipped with the necessary skills and knowledge to handle COSHH substances.
- Monitoring and health surveillance.
- Planning for emergencies.
- Ensuring secure and specific storage for hazardous substances covered under COSHH regulations.