In this article
Employers in the built environment, such as construction, demolition and engineering, have legal duties under health and safety legislation such as:
- Health and Safety at Work etc. Act 1974 (HASWA).
- The Management of Health & Safety at Work Regulations 1999 (MHSWR).
- The Provision and Use of Work Equipment Regulations 1998 (PUWER).
- The Lifting Operations and Lifting Equipment Regulations 1998 (LOLER).
- Working at Height Regulations 2005 amended 2007 (WAHR).
- Construction (Design and Management) Regulations 2015 (CDM).
To identify, eliminate, control and/or mitigate any significant risk.
When an employer has carried out the mandatory risk assessments of the health and safety risks to which employees and others may be exposed to, it is good practice to compile a method statement. Although not specifically a legal requirement, a method statement can help comply with legal requirements such as those listed above, as it helps to provide detailed information and instruction.
A method statement, as its name implies, is a clear explanation documented in a logical sequence of exactly how a job is to be carried out (the method). It describes the process, steps and resources required to carry out a task safely without risks to health. It may also be referred to as a safe work method statement or “SWMS” for short. The method statement can be in the form of a flowchart or a written step-by-step guide and often includes diagrams.
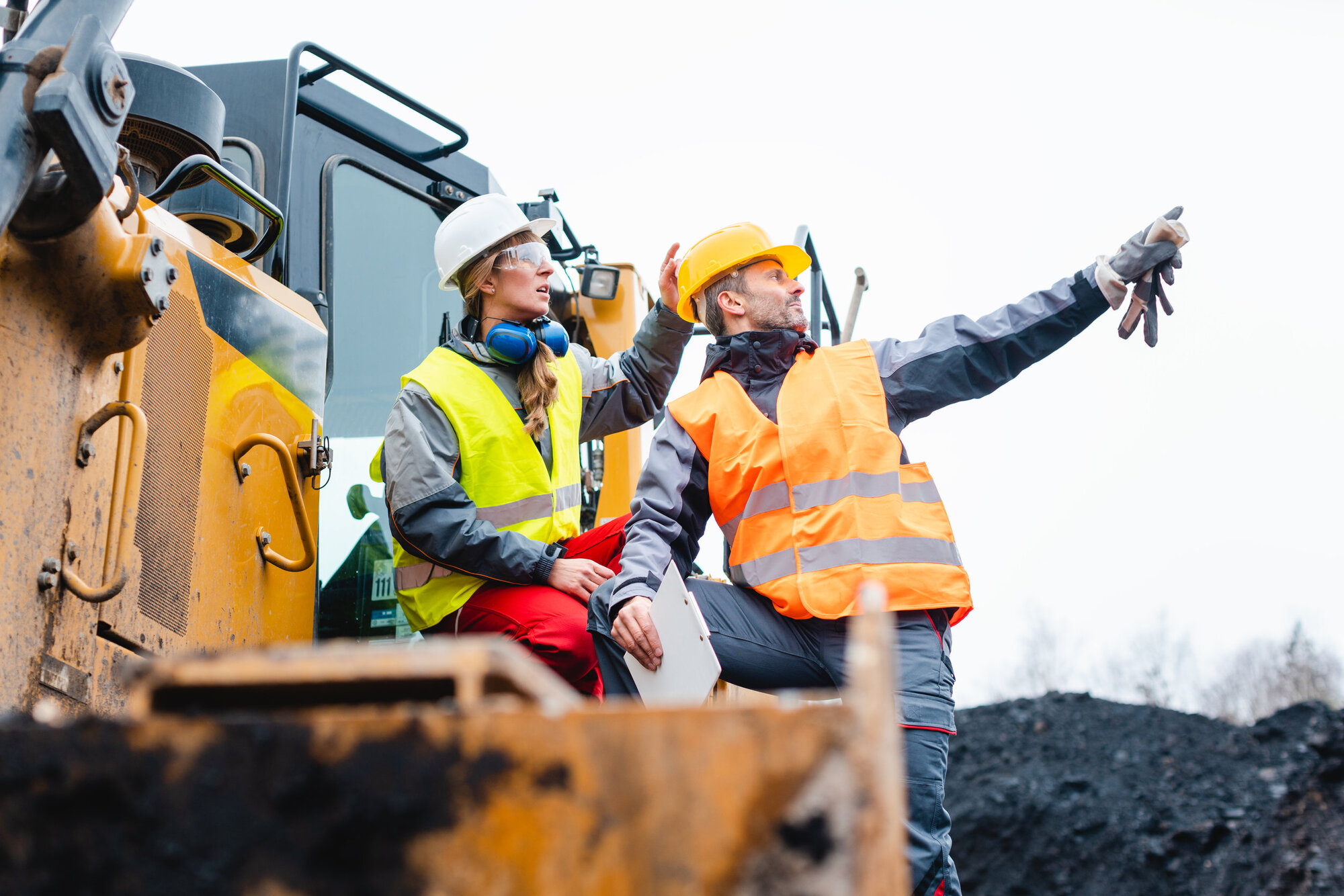
How is a method statement different from a risk assessment and a safe system of work (SSoW)?
Risk assessments and method statements are often mentioned within the same breath, as the two reports tend to be carried out side by side. However, they are separate documents that analyse different health and safety elements of the working environment. In the simplest terms, a risk assessment analyses the risk in the workplace, whilst a method statement outlines what is being done to prevent risk.
The method statement is just one part of the total SSoW, as is the risk assessment. A complete SSoW should also include emergency procedures and arrangements for monitoring and audit.
A method statement that included this much information would be unwieldy and unhelpful for the person asked to carry out a single task. A method statement doesn’t have to be a lengthy document, but it should contain all the information you need to communicate how to do the work safely. The information should be clear and concise.
What should be in a method statement?
A good method statement should state how a task is being carried out, and not just state what is being carried out.
Section 1 of a method statement might include information such as:
- The document title, for example Work Method Statement or Standard Operating Procedure.
- A brief description of the work to be carried out.
- The company details including name, address, contact details, registration number, logo etc.
- Project start date and completion date.
- Site address.
- Site contact details including emergency details.
- Document author.
- Health & Safety contact.
- Document number, issue date, revision date, revision number etc.
Section 2 of a method statement might include information such as:
- A summary of the main hazards that are present as identified in the risk assessment and the control measures that must be implemented as a result.
- A list of the Personal Protective Equipment (PPE) that must be worn, as identified in the risk assessment.
- Any environmental or quality procedures that must be undertaken during the task.
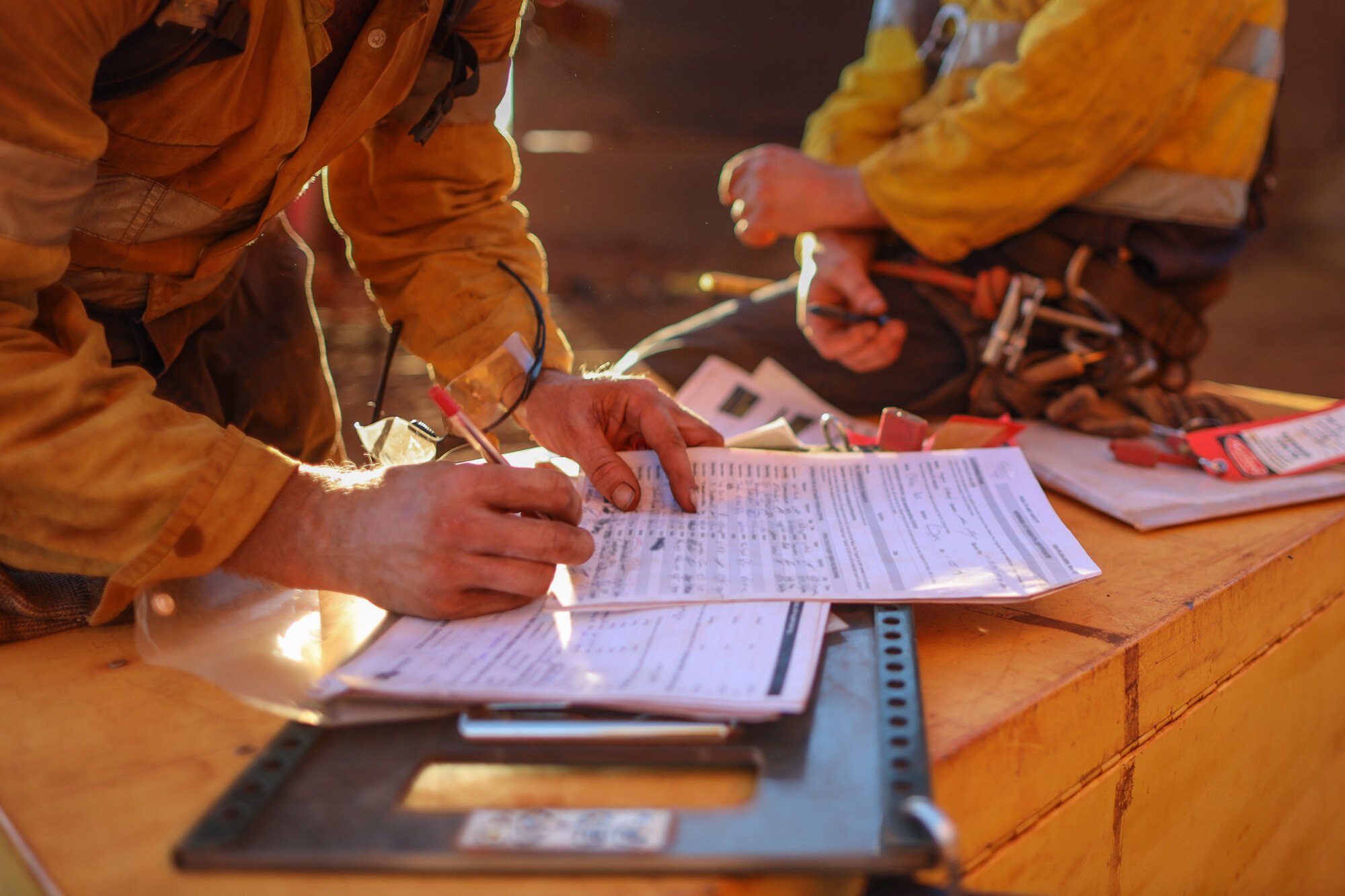
Section 3 of a method statement is used to describe the task in more detail such as:
- Staff, including:
– Managers.
– Team leaders.
– Supervisors.
– Workers.
– Technical staff.
– Sub-contractors. - Tasks and responsibilities.
- Training.
- Permits to work.
- Machinery shutdown and lock-off procedures.
- Site access, entrances and exits.
- Material handling.
- Scaffold and access to height.
- Background and preparation.
- Welfare and first aid.
Section 4 of a method statement is the step-by-step guide which may be a flowchart and can include diagrams that are used to explain in detail the steps that must be taken if the task is to be carried out safely. It’s important to include all relevant details in the order that you expect them to be carried out.
An example could be:
“The following method statement has been developed to provide a safe system of work and must be adhered to at all times. Any significant deviation from this system must first be authorised by your manager or safety representative. Please read the entire instruction sheet before beginning the procedure. If you have any questions please contact your manager or safety representative.”
- The main hazards to your safety and health are:
List all the main hazards. - The preventative measures you must take are:
List all preventative measures. - The Personal Protective Equipment (PPE) you must wear is:
List all PPE required for the task. - The environmental protection measures you must take are:
List all environmental protection measures. - Step-by-Step Process:
Preparation.
Activity methods of working. - Details of Site Management and Emergency Procedures:
List what to do if something goes wrong and who to contact.
The details provided in the above example method statement are intended as a guide only. When creating a method statement, be thorough and be sure to address all potential hazards and risks, even those that seem like common sense; never assume that even the most experienced worker will know or do what they should.
Include any aspect of a project that presents a risk for team members, site visitors, the public or the client. List steps clearly and articulately to avoid any confusion and consider providing important contact information and safety protocols that team members can use in the event of an accident.
Communicate clearly. Being clear and concise in a method statement can help reduce confusion and prevents assumptions from being made. Format the statement in a way that is easy to read and use simple language.
Abbreviations, construction jargon and nicknames can confuse the reader and may not be known by everybody. Try to ensure the tone is direct, the steps are easy to follow and the details apply to the current job; method statements should not be generic.
Pictures or diagrams can explain points more clearly and reduce confusion. Including site maps, for example, helps teams understand the site layout so they can quickly and safely get to where they need to be and easily locate site access points, waste disposal areas, PPE storage places and first aid locations.
The main aim of a method statement is to ensure that the right responsible person is appointed, and more importantly, the safety of anyone who could be affected by any work that is taking place is prioritised. It should also give a clear schedule to all those involved, including any special measures. For example, if any part of the building needs to be closed temporarily or if power needs to be isolated.
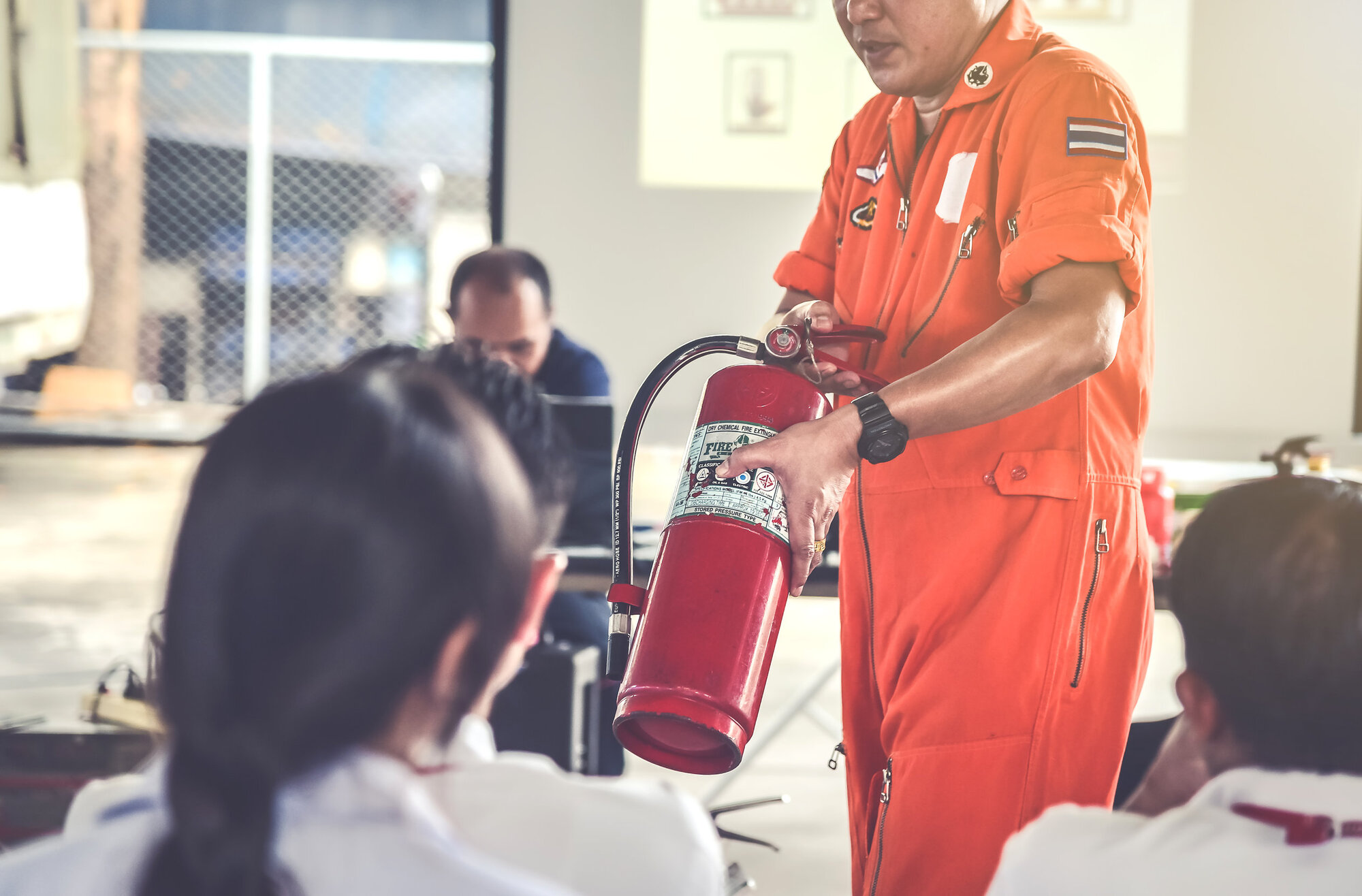
Who is responsible for writing a method statement?
Ultimately the employer is responsible for the provision of a method statement; however, as it is normally the supervisor who has responsibility to ensure the safe and accurate execution of each task, the responsibility to create a method statement is usually delegated to them. They should also make sure that all the workers have access to a copy.
Once they have created a method statement, the responsible supervisors (duty holders) must ensure that everyone is following the rules.
They should also:
- Keep records of the method statement throughout the duration of the project.
- Make sure that all the on-site workers are complying with the method statement.
- Stop any high-risk work if there is noncompliance with the method statement.
- Review the method statement from time to time and make amendments as and when required, for example if there is a change of location, staff, equipment etc.
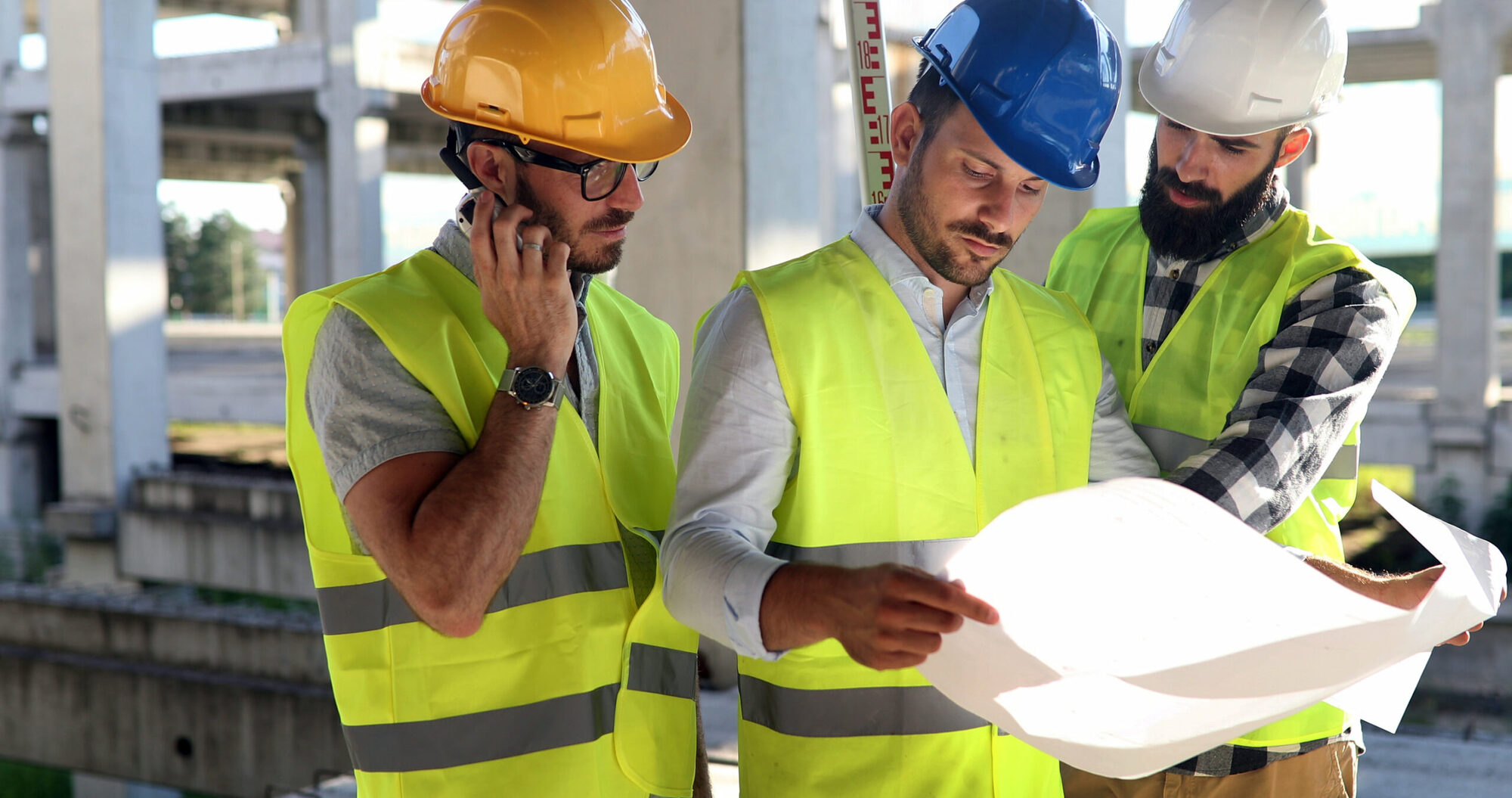
What a method statement is used for and when to use it
A method statement is usually necessary for higher risk work and it is commonly used within the construction, demolition and engineering sectors. It is quite common to be asked for the method statement in addition to the risk assessment before the start of a job. They are collectively known as “RAMS” – Risk Assessments and Method Statements.
If during a risk assessment it is noticed that a risk cannot be eliminated, then ideally a RAMS document should be in place. RAMS contain details of the hazard and a step-by-step guide to working around that hazard that all employees, contractors and others can easily follow.
Having a method statement helps with planning and it ensures that there are sufficient and appropriate resources allocated to carry out the task safely. The method statement is an effective way of providing information to employees about how an employer expects the work to be carried out and the precautions that should be taken.
It should explain what employees should do if something goes wrong, clarify the emergency procedures and detail what first aid arrangements will be available on site. It can also be a useful monitoring tool for checking that the working methods set out in the statement are actually put into practice on site.
All method statements are written after a risk assessment has been carried out, but it needs to be written before the job actually begins. Rather than repeating the information already in a risk assessment, a method statement enhances the information gathered for the risk assessment and goes further in planning the sequence for the activity.
Method statements can also help link together all the documents relating to the task. For example, it may reference a risk assessment, COSHH assessment, and permit to work for the activity.
Method statements are widely used as a means of controlling specific health and safety risks that have been identified following a risk assessment, such as lifting operations, demolition or dismantling, working at height, installing equipment, and the use of plant equipment.
The explicit safety measures should be included within the method statement; for example when using a ladder, although it may seem obvious to include items such as “check the ladder is stable before climbing”, include it to avoid any human error.
The method statement must be site specific, reviewed and revised for each job, and communicated to all who are required to work to it. Often in the construction industry, for example, one project finishes and a similar operation is repeated on the next job.
However, there may very well be significant changes such as a new location, a new team and a different set of circumstances such as the surrounding work activities and corresponding hazards, so a new method statement will be required.
Certain types of hazardous work always require a formal safety method statement, for example, but not limited to:
- Work in confined spaces.
- Work underground.
- Work at height.
- Work involving dangerous materials.
- Steel and framework erection.
- Demolition.
- Work with electrics including complex operations that involve installing, connecting, fitting or running a new supply.
- Work near or over water.
- Work with or near overhead power lines.
- Work over road or rail networks.
This list is not exhaustive as some tasks become hazardous because of their location or due to other specific factors relevant to that task.
When clients are planning projects and sourcing contractors, they will often insist that the contractors’ method statements are included with other health and safety documents in the tender submission. This enables them to assess the suitability of a contractor in terms of health and safety at the tender stage of a project before contracts are issued.
Contractors that demonstrate high levels of quality safety measures and provide method statements in their tender proposals are often viewed more favourably, and method statements are often a pre-requisite for any public sector tenders.
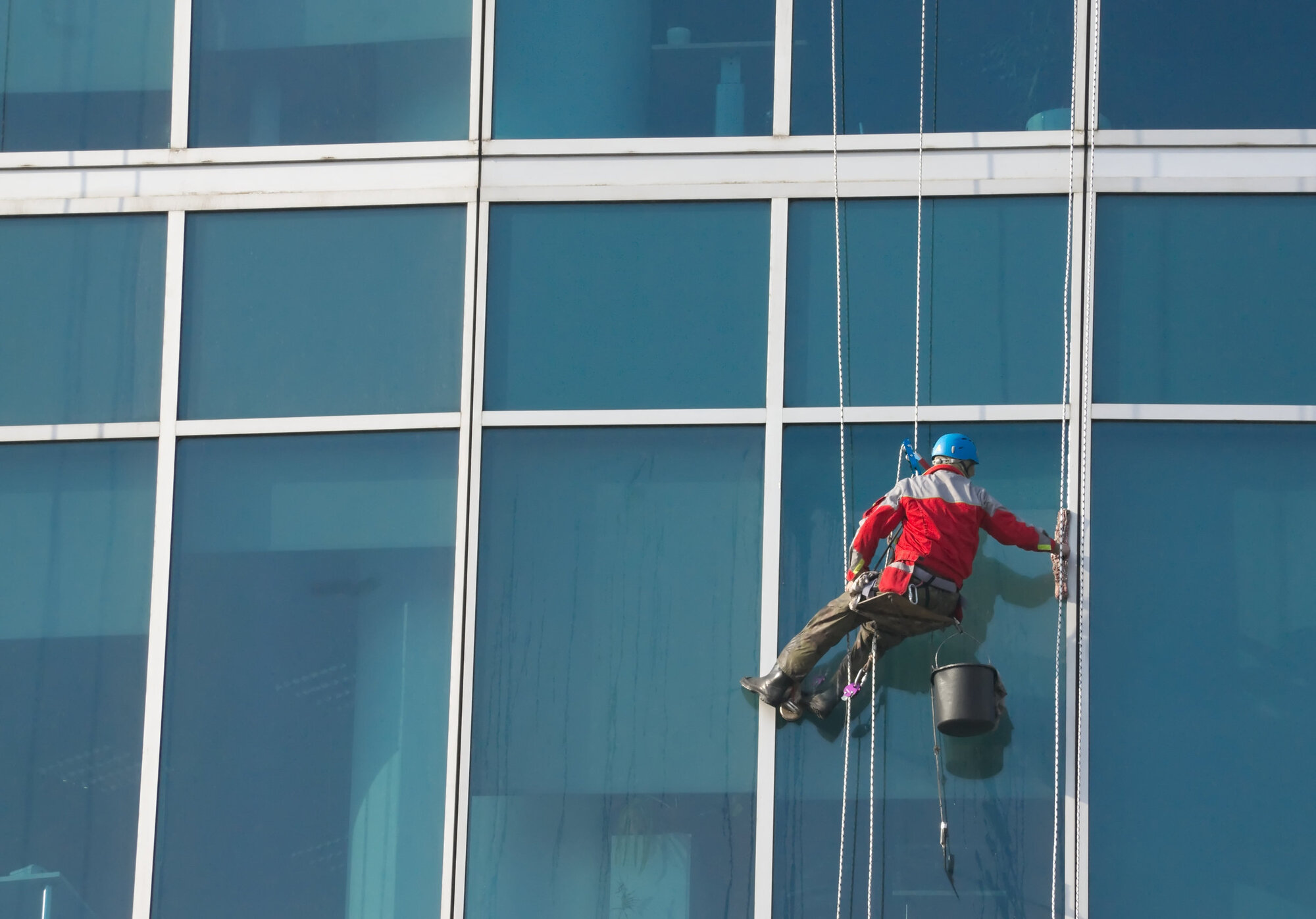
Why is a method statement needed?
According to HSE statistics, in 2019/20, 39 construction workers lost their lives at work. In the same year, for every 100,000 workers in construction, 2,760 (nearly 3%) were injured, and 3,520 (3.5%) suffered work-related illness.
The construction industry has a much higher injury rate of 2.8% than the average across all industries of 1.8%, and the types of injuries workers are at risk from in construction tend to be more severe.
In the five-year period from 2016/17 to 2020/21, 77% of all fatal injuries were accounted for by just five different accident kinds. Falls from a height, being struck by a moving vehicle and being struck by a moving object, including flying or falling objects, continue as the three main causes of fatal injury. In 2020/21, 60 members of the public were also killed as a result of a work-related accident.
Case law has made it clear it is not enough for employers to assume that an experienced employee will work out what to do to stay safe even if the risk in the activity they are carrying out is clear.
In the case law the Law Lords ruled that “It is the duty of an employer to give such general safety instructions as a reasonably careful employer who has considered the problem presented by the work would give to their workers.” Hence a good method statement fulfils this requirement.
In conclusion
Where risks are high, more detailed planning is needed to manage the hazards and control those risks. The method statement plans out the work in a logical sequence, providing information on the controls and precautions required at each step that have been identified in the risk assessments.
Think of the method statement as a detailed guide that explains the work that will be done and the plan of how to get it done safely. Anyone should be able to pick up the method statement and understand the risks, what they should do to mitigate those risks and work safely.