In this article
What is LOLER?
The Lifting Operations and Lifting Equipment Regulations 1998 (LOLER) are the UK government’s regulations designed for the safe use of lifting equipment in workplaces. LOLER applies to individuals and businesses who own, operate or have control over any type of lifting equipment in the UK. LOLER is designed to ensure that lifting equipment is safe for use, fit for purpose, well-maintained and used correctly.
The key points of LOLER include:
Safe use of equipment
Equipment must be suitable, properly installed and used safely to prevent injury.
Thorough examination and inspection
Lifting equipment must be regularly inspected by a competent person, typically every 6 months for lifting equipment used to lift people (e.g., passenger lifts or hoists) and every 12 months for other lifting equipment (e.g., cranes or forklifts), depending on usage. Equipment should also be inspected after any significant repairs or modifications. The regulations state that a LOLER certificate must be issued after any inspections.
Marking of equipment
Lifting equipment must be clearly marked with its Safe Working Load (SWL). If equipment has multiple lifting configurations, each separate SWL must be stated.
Planning of lifting operations
All lifting operations should be properly planned by a competent person, supervised appropriately and carried out safely.
Record keeping
Inspection reports and maintenance records must be documented and kept on record for at least two years. Employers must ensure workers are properly trained in using lifting equipment safely.
LOLER defines lifting operations as operations concerned with the lifting or lowering of loads. Loads can be objects, people or animals. Under LOLER, lifting equipment is defined as the work equipment, lifting accessories, anchors, fixes and supports that are used to lift and lower loads. Each type of equipment has specific inspection, maintenance and operational requirements to prevent accidents and maintain compliance.
LOLER applies to a wide range of lifting equipment and ensures safe lifting operations across various industries, including:
- Construction
- Manufacturing
- Warehousing
- Agriculture
- Healthcare
- Vehicle mechanics and vehicle recovery services.
Because the majority of lifting equipment covered under LOLER is used in the workplace or installed in a professional capacity, the Provision and Use of Work Equipment Regulations 1998 (PUWER) often apply in conjunction with LOLER.
LOLER 1998
The Lifting Operations and Lifting Equipment Regulations 1998 (LOLER) apply to any person or company that owns, operates or has control over lifting equipment. LOLER is supported by the Health and Safety Executive (HSE) and the Health and Safety at Work etc Act 1974.
LOLER covers multiple duties related to lifting, including:
Choosing the correct equipment
LOLER specifies that all lifting equipment must be appropriately strong and stable for the load and the task. Additionally, any lifting equipment must be positioned and installed in a way that reduces the risk to as low as is reasonably practicable. This includes ensuring that the load does not:
- Strike a person
- Drift
- Fall freely
- Release unintentionally
Safe lifting by machine
LOLER requires that lifting machines (e.g., cranes, hoists, forklifts, etc.) be:
- Suitable for the task: Machines must be capable of safely lifting the intended load and only used for the intended purpose.
- Properly maintained: Regular servicing and thorough inspections must be carried out.
- Used within Safe Working Load (SWL) limits: Equipment must be clearly marked with its SWL.
- Stable and securely positioned: The machine must be placed on firm ground or properly anchored.
- Controlled by trained personnel: Only competent operators should use lifting machines.
Marking of lifting equipment
Every piece of lifting equipment must be correctly and clearly marked to show the safe working loads (SWL). The SWL is the maximum load that each piece of equipment can safely lift.
Some pieces of equipment can be configured in multiple ways (e.g., an anchor that can be angled in different positions). The marking must specify the SWL for each possible configuration to ensure safe lifting operations in every situation. The marking must also include any characteristics that could affect the SWL (e.g. if different parts are attached).
If the equipment is used to lift people, the marking must include the SWL and the number of people that can be lifted at one time. For example, it could specify that the maximum weight is 500kg and that a maximum of five people can be lifted at one time. For equipment NOT designed to lift people, but which could mistakenly be used to lift people, the marking must indicate that it is not intended to lift people.
Planning, organising and carrying out lifting operations
LOLER specifies that lifting operations must be:
- Planned by a competent person (e.g., someone with knowledge and training of lifting risks and safety procedures).
- Risk assessed, including identifying potential hazards (e.g., unstable loads or overhead power lines).
- Supervised appropriately by trained personnel.
- Carried out safely, considering factors like wind speed, equipment condition and weight distribution.
LOLER also differentiates between simple lifts and complex lifts when it comes to planning the lift. Simple, routine lifts which need basic lift control require minimal planning to manage potential risks whereas more complex lifts need more detailed planning with input from experts, strict monitoring and supervision by specially trained individuals and detailed records.
Planning also includes planning logistical aspects not directly related to the lifting action. For example, a busy factory should have designated walkways to keep workers clear of suspended loads.
Thorough examination of lifting equipment
LOLER specifies that a competent person must conduct thorough examinations at the following intervals:
- Before the first use (unless the equipment has a valid Declaration of Conformity from the last 12 months).
- Every 6 months, for lifting equipment used for people.
- Every 12 months, for lifting equipment NOT used for people.
- After significant repairs or modifications.
- If the equipment is exposed to conditions that could cause deterioration.
- If the equipment needs to be installed, reinstalled or assembled at another location.
The examination process should include:
- Checking structural integrity (e.g., cracks, rust or wear).
- Verifying safety mechanisms (e.g., brakes and limit switches).
- Ensuring correct labelling (e.g., that the equipment is labelled with the Safe Working Load).
- Records of the examination.
Safe Lifting
Safe lifting under LOLER ensures that lifting operations and equipment are carried out and used in a way that minimises the risk to workers and others. It applies to all industries where lifting equipment is used.
The key principles of safe lifting under LOLER include:
Use suitable and well-maintained equipment
Lifting equipment must be fit for purpose and capable of handling loads safely. Equipment must also be well-maintained, with regular servicing and inspections and clearly marked with the SWL.
A thorough risk assessment
LOLER requires employers to assess the risks involved in lifting operations. The risk assessment should include:
- Weight and stability of the load.
- Ground conditions (e.g., avoiding soft or uneven surfaces).
- Nearby hazards (e.g., power lines, other workers and obstacles).
- Weather conditions (for outdoor lifting operations).
Proper planning and supervision of lifting operations
Under LOLER, a competent person must plan and oversee lifting operations. Additionally, lifting must be done in a safe area with barriers to keep people away from suspended loads. Operators must be trained and authorised to use lifting equipment and equipment must be used according to manufacturer instructions.
Correct use of lifting accessories
LOLER also applies to lifting accessories such as chains, slings, shackles, hooks and eyebolts. Safe lifting requires:
- Choosing the right lifting accessory for the load type.
- Checking accessories for damage before use.
- Ensuring correct attachment to the load and lifting equipment.
- Proper storage of accessories when not in use to avoid wear and tear.
Ensuring the stability of loads
Loads must be securely attached before lifting and balanced and stable positioning is essential to prevent tipping. Handlers should avoid sudden movements that could shift the load dangerously and use supporting equipment and accessories, such as spreader bars, slings or lifting beans, if necessary.
Keeping people safe from suspended loads
It is essential that people are not allowed to walk under or near a suspended load. To prevent this, workers should erect barriers or exclusion zones around lifting operations and use signals or radios to clearly communicate lifting and coordinate movements.
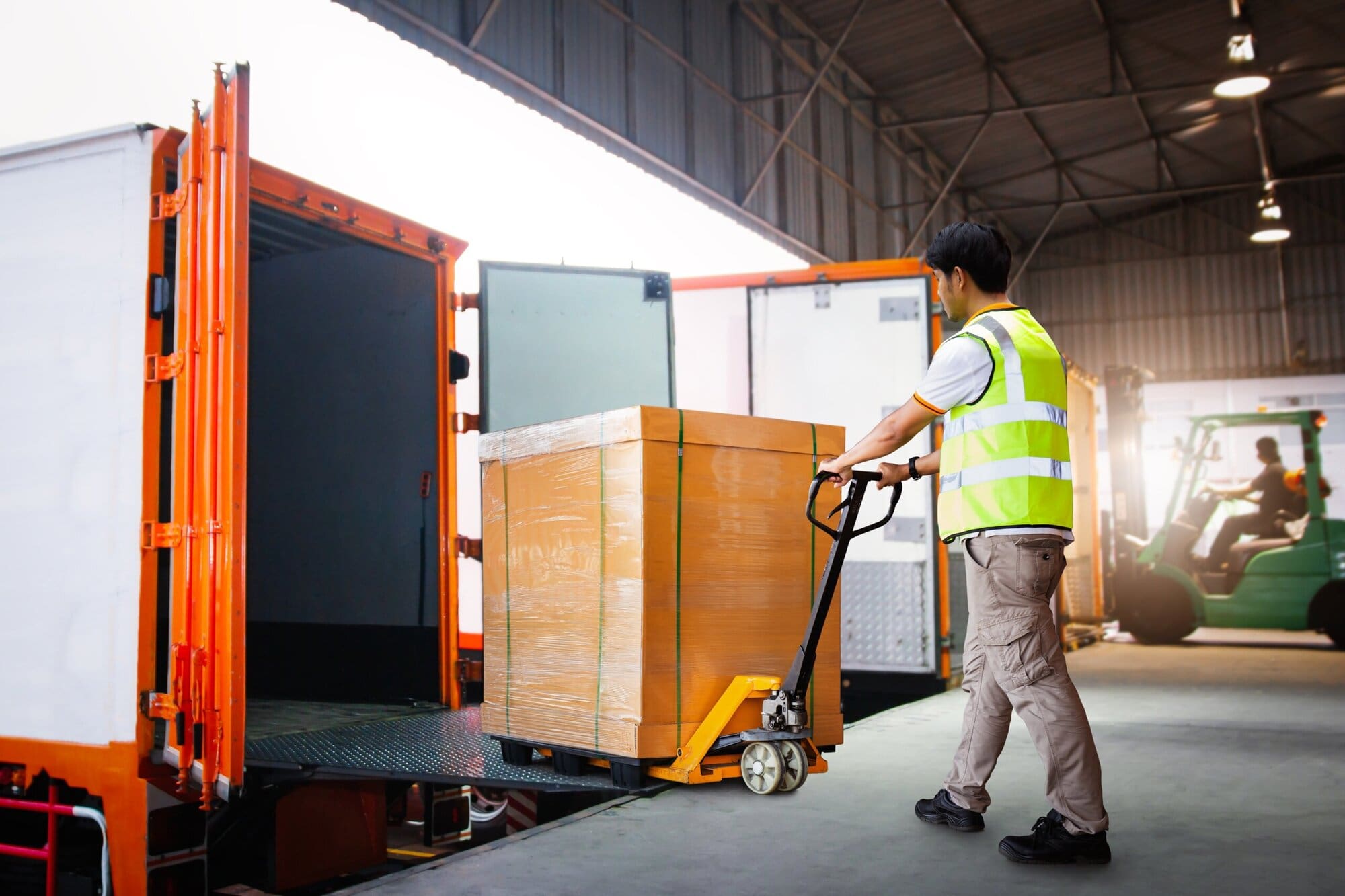
Lifting Equipment Covered in LOLER Regulations
LOLER applies to all lifting equipment and accessories used at work for lifting and lowering loads, including:
Lifting machines and devices
Lifting machines and devices are used for lifting and lowering loads. Common examples include:
- Cranes: Tower cranes, mobile cranes and overhead cranes.
- Forklifts and telehandlers: Including attachments used for lifting.
- Hoists and winches: Passenger and goods hoists and scaffold hoists.
- Lifts and elevators: Passenger lifts, goods lifts and stairlifts.
- Vehicle lifting equipment: Vehicle tail lifts, car lifts and recovery truck cranes.
- Construction lifting equipment: Excavators used for lifting and gantry cranes.
- Patient hoists: Used in healthcare to lift patients.
- MEWPs (Mobile Elevating Work Platforms): Cherry pickers and scissor lifts.
Lifting equipment for lifting people
Lifting people requires higher safety standards under LOLER than other types of lifting equipment and has additional safety features, including:
- The equipment must be specifically designed for lifting people (e.g., passenger lifts, hoists or mobile elevating work platforms).
- Safety measures must be in place, e.g., emergency stop buttons and fall protection.
- Thorough examination every 6 months: Lifting people equipment requires more frequent inspections than standard lifting equipment.
- Secure and stable platforms: This includes no gaps where people could fall
For example, a cherry picker that allows workers to perform maintenance work must have additional safety features such as guardrails and harnesses to prevent falls.
Common types of lifting equipment for transporting people include
- Passenger Lifts: Found in buildings, hotels and offices.
- Stairlifts: Used in care homes and private properties.
- Patient hoists: Used in hospitals and nursing homes.
- MEWPs (Cherry pickers and scissor lifts): Used in construction and maintenance work.
- Cage lifts and suspended platforms: Used for window cleaning or construction work at height.
Vehicle-mounted lifting equipment
This type of equipment includes:
- Tail lifts: Fitted to vans, lorries and delivery vehicles.
- Vehicle recovery lifts: Winches and lifting arms used by tow trucks.
- Loading cranes: Truck-mounted cranes used for heavy lifting.
Passenger lifts and escalators
Passenger lifts and escalators must comply with both LOLER and PUWER. Key LOLER requirements include:
- Thorough examination every six months, as passenger safety is a priority.
- Regular maintenance by a competent engineer and immediate action is required for faults.
- Emergency procedures should be in place. For example, lifts must have alarm systems and emergency exit options.
- Load capacity must be clearly displayed as this prevents overloading accidents.
Vacuum lifting equipment
Vacuum lifting equipment uses suction to lift objects, such as glass panels or metal sheets. Under LOLER, individuals or businesses using vacuum devices must ensure:
- Regular checks for leaks or loss of suction to prevent load drops.
- Emergency fail-safes, for example, systems must have backup power or alarms for suction loss.
- Clearly marked lifting capacity, as this prevents exceeding the Safe Working Load (SWL).
- Operator training to ensure employees understand how to use vacuum lifters correctly.
Magnetic lifting devices
Magnetic lifters use electromagnets or permanent magnets to lift metal objects (e.g., steel plates and pipes). LOLER compliance includes:
- Testing of magnet strength to ensure it can hold the required load safely.
- Backup safety systems: In case of power failure, backup safety systems must ensure that the load does not drop.
- Operator training on correct usage to prevent unintended load release.
- Clear SWL markings must be displayed on the equipment.
Lifting accessories
Lifting accessories are attachments that help lift loads. For example:
- Slings and chains: For example, wire rope slings, chain slings and fibre slings.
- Shackles and hooks: For example, Bow shackles, D shackles and lifting hooks.
- Eyebolts and lifting points: These are fixed anchor points used for lifting.
- Spreader beams and lifting frames: Used to distribute load weight.
- Lifting Magnets: Including electromagnetic and permanent lifting magnets.
- Cranes Attachments: For example, clamps, grabs and lifting beams.
Some equipment is not covered by LOLER, including equipment used for private or domestic purposes (such as home stairlifts), agriculture loaders that are used only for pushing and pulling loads and pallet trucks that don’t have a lifting function.
LOLER Inspections
LOLER inspections (also called thorough examinations) are mandatory checks carried out by a competent person to ensure that lifting equipment and accessories are safe to use and compliant with the Lifting Operations and Lifting Equipment Regulations 1998 (LOLER). LOLER inspections ensure that lifting equipment is safe, legal and properly maintained and help prevent accidents, equipment failures and legal penalties by identifying potential hazards before they cause harm.
A LOLER inspection should cover
- Structural Integrity: For example, checking for cracks, corrosion or wear.
- Safe Working Load (SWL) verification: Ensuring the equipment is not overloaded.
- Mechanical and electrical components: Inspecting components such as brakes, gears, hydraulics and limit switches.
- Safety Mechanisms: For example, testing emergency stops, interlocks and alarms.
- Correct installation and stability: For example, checking that equipment is positioned securely.
- Labelling and markings: Ensuring SWL and identification plates are clear.
- Lifting Accessories: The inspection of accessories, such as slings, chains, hooks and eyebolts for wear or damage.
Inspections must be carried out by a competent person who has
- Sufficient knowledge of lifting equipment.
- Training and experience in identifying faults.
- Independence from daily operations (individuals should not inspect their own work).
A competent person could be a LOLER-certified engineer, a lifting equipment specialist or a qualified maintenance professional.
If the equipment is determined to be safe, it will pass the inspection. If defects are found, the equipment will fail the inspection. If serious defects are found, the equipment must be removed from use immediately, until it is repaired or replaced. The inspector must issue a written report once the inspection is complete. The report should include:
- Equipment details (e.g., type, serial number and location).
- Inspection findings (e.g., pass or fail and any defects found).
- Recommendations for repairs or further checks.
- The inspector’s name and signature.
LOLER reports for equipment must be kept for the lifespan of the machinery and LOLER reports for lifting accessories should be kept for at least two years or until the next report is issued. Failure to carry out LOLER inspections can result in equipment failure, costly damage, serious injuries or fatalities, legal action and the forced closure of businesses.
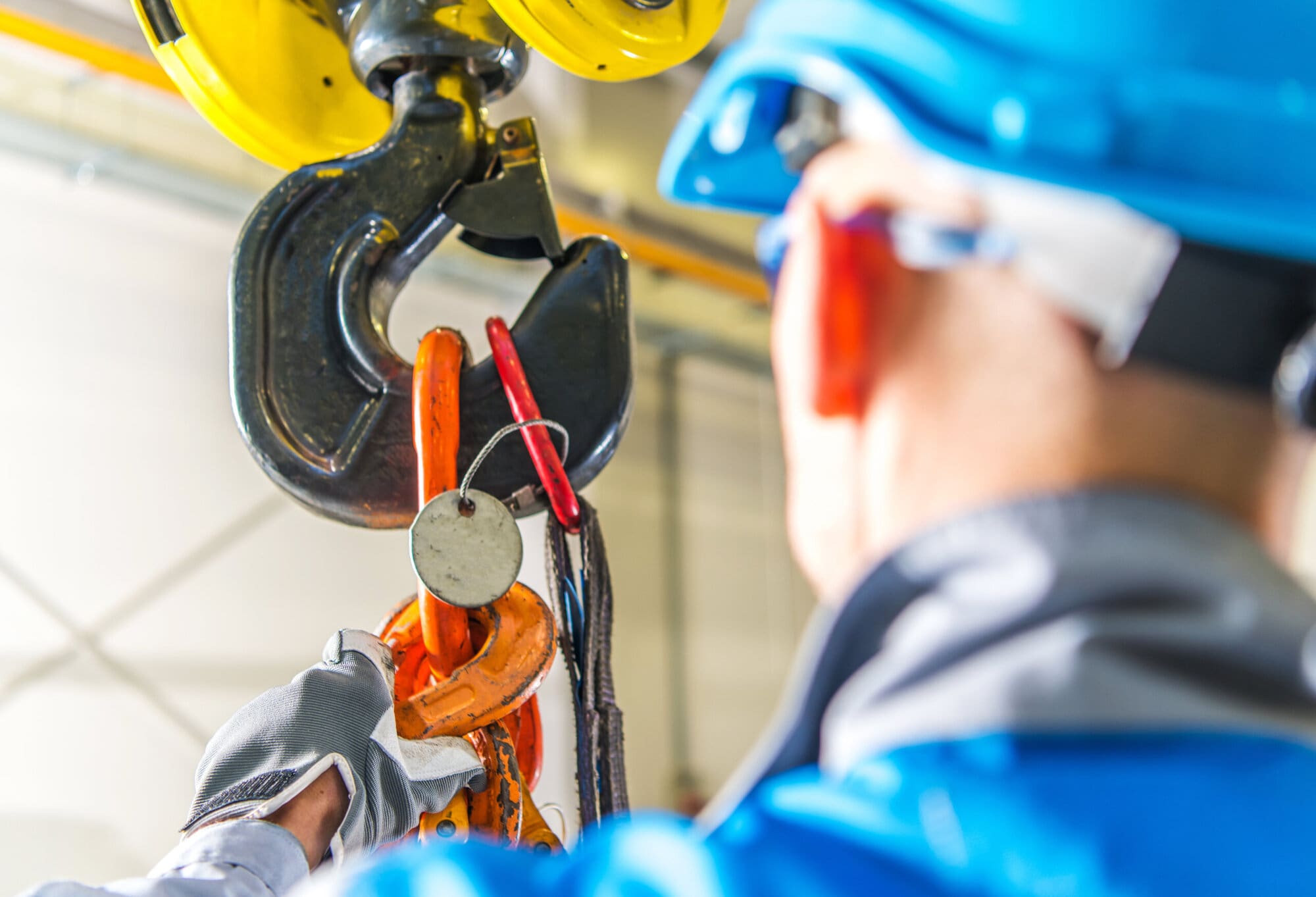
Safety Regulations
There are several pieces of key health and safety regulations that work alongside LOLER to ensure lifting operations are carried out safely, including:
Health and Safety at Work etc Act 1974
The Health and Safety at Work etc Act is the main piece of legislation covering workplace health and safety in the UK. It places a legal duty on employers to ensure the health and safety of employees and others affected by their work. The Act:
- Requires employers to assess and control risks associated with lifting operations.
- Covers training, maintenance and safe use of equipment.
- Specifies that employees must follow safety procedures and report any defects in equipment.
Provision and Use of Work Equipment Regulation 1998 (PUWER)
PUWER applies to individuals, companies and organisations who own, operate or have control over work equipment. PUWER specifies that lifting equipment in the workplace should be:
- Suitable for the task.
- Safe, well-maintained and inspected.
- Used only by individuals who have the relevant information and training.
- Labelled with the relevant safety markings.
Management of Health and Safety at Work Regulations 1999
The Management of Health and Safety at Work Regulations require risk assessments for all workplace activities, including lifting operations. The regulations specify that:
- Employers must identify hazards related to lifting.
- Competent persons should oversee lifting operations.
- Emergency procedures should be created for lifting accidents.
The Work at Height Regulations 2005
The Work at Height Regulations apply if lifting equipment is used at height or to lift people. The regulations specify that individuals and companies must ensure that lifting operations prevent falls from height and that lifting equipment used at height or to lift people requires proper safety harnesses, guardrails, platforms or other safety features. The regulations cover equipment such as MEWPs (Mobile Elevated Work Platforms), cherry pickers and scaffolding hoists.
LOLER Violation Risks
Failing to comply with LOLER can have serious consequences, including injuries, fatalities, legal action and financial penalties.
Risk of accidents and injuries
When lifting equipment is not properly inspected, maintained or used correctly, serious accidents can occur, for example:
- Falling Loads: Falling loads can occur due to worn-out slings, broken chains or mechanical failures and can cause significant injuries or even death.
- Crush Injuries: Workers can become trapped between loads or machinery and excessive force or pressure can result in bleeding, bruises, broken bones, nerve injuries, traumatic amputations and neurological injuries.
- Equipment Collapse: Overloaded or poorly maintained cranes, forklifts or hoists may collapse and cause injury to the people working on the equipment or in the vicinity.
- Falls from Height: If MEWPs (cherry pickers, scissor lifts) or passenger lifts fail, the worker may fall from height.
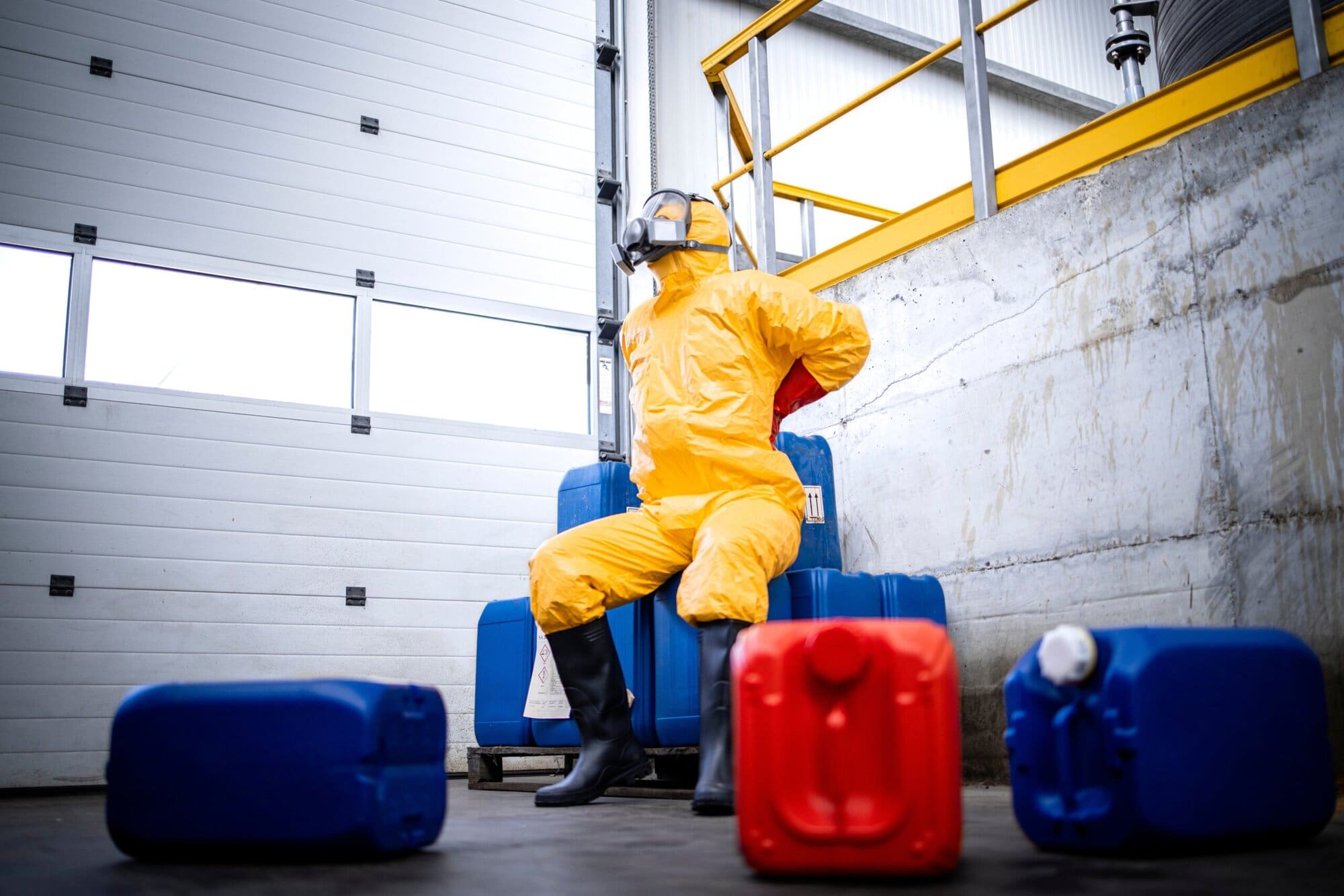
Fatalities from unsafe lifting operations
LOLER violations can result in fatal accidents, especially in high-risk industries like construction, warehousing and manufacturing. Causes of fatal accidents can include:
- Unstable loads if lifting plans are not properly followed.
- Unsafe lifting of people.
- Improper use of equipment (e.g., from untrained workers).
Legal penalties and prosecution
The Health and Safety Executive (HSE) enforces LOLER and if a company or individual fails to comply, the HSE can pursue legal consequences, such as:
- Prohibition notices: Immediate shutdown of dangerous lifting operations.
- Improvement notices: Companies are given a deadline to fix safety breaches.
- Prosecution in court: If violations lead to serious injury or death.
- Heavy fines: Courts can impose unlimited fines for non-compliance.
- Prison sentences: Company directors and managers can be jailed.
Equipment failure and breakdowns
Without regular LOLER inspections and maintenance, lifting equipment is more likely to fail unexpectedly. This could result in expensive repairs and delays in production, delivery or construction work. Additionally, by not properly maintaining equipment and performing regular inspections, businesses may find themselves needing to replace entire lifting systems instead of making minor repairs.
Financial losses and business disruption
Not complying with LOLER can have financial consequences, such as:
- Fines.
- High legal fees after HSE investigations.
- Compensation claims from injured workers.
- Cost of replacing damaged equipment.
- Project delays due to damaged equipment or prohibition notices.
- Loss of reputation and trust from clients resulting in a loss of business.
- Higher insurance premiums for future projects.
To avoid LOLER violations, individuals and companies should:
- Schedule regular LOLER inspections (every 6 or 12 months).
- Ensure all lifting equipment is safe, marked and maintained.
- Train employees on safe lifting procedures and LOLER compliance.
- Create proper lifting plans and risk assessments.
- Keep inspection reports for the specified amount of time.