In this article
Lifting operations are defined under Regulation 8(2) of LOLER and refer to the processes and activities involved in moving heavy objects or loads from one place to another using mechanical equipment, and are a crucial and common activity in many industries such as, but not limited to:
- Construction
- Manufacturing
- Warehouses
- Retail locations
- Logistics
- Docks and shipping facilities
- Transportation
A lifting operation denotes any activity that involves the use of lifting equipment to lift, lower, or move loads. It includes tasks such as hoisting objects with cranes, operating forklifts, or using other types of lifting machinery. Most types of lifting equipment are designed for specific types of material handling processes and they also have different weight capacities. Some of the more complex machines may even require specialised training.
Lifting equipment provides a safer way to move heavy objects and selecting the right types of lifting equipment can improve the efficiency and safety of material handling processes. There are strict rules and regulations governing the use, inspections, certification, and maintenance of lifting equipment and tools.
These rules are designed to ensure the safety of both those using equipment, and those nearby. The Lifting Operations and Lifting Equipment Regulations 1998 (LOLER) regulations cover any lifting equipment used at work. In this article we will examine LOLER in more detail and in particular the importance of record keeping to ensure compliance with the LOLER regulations.
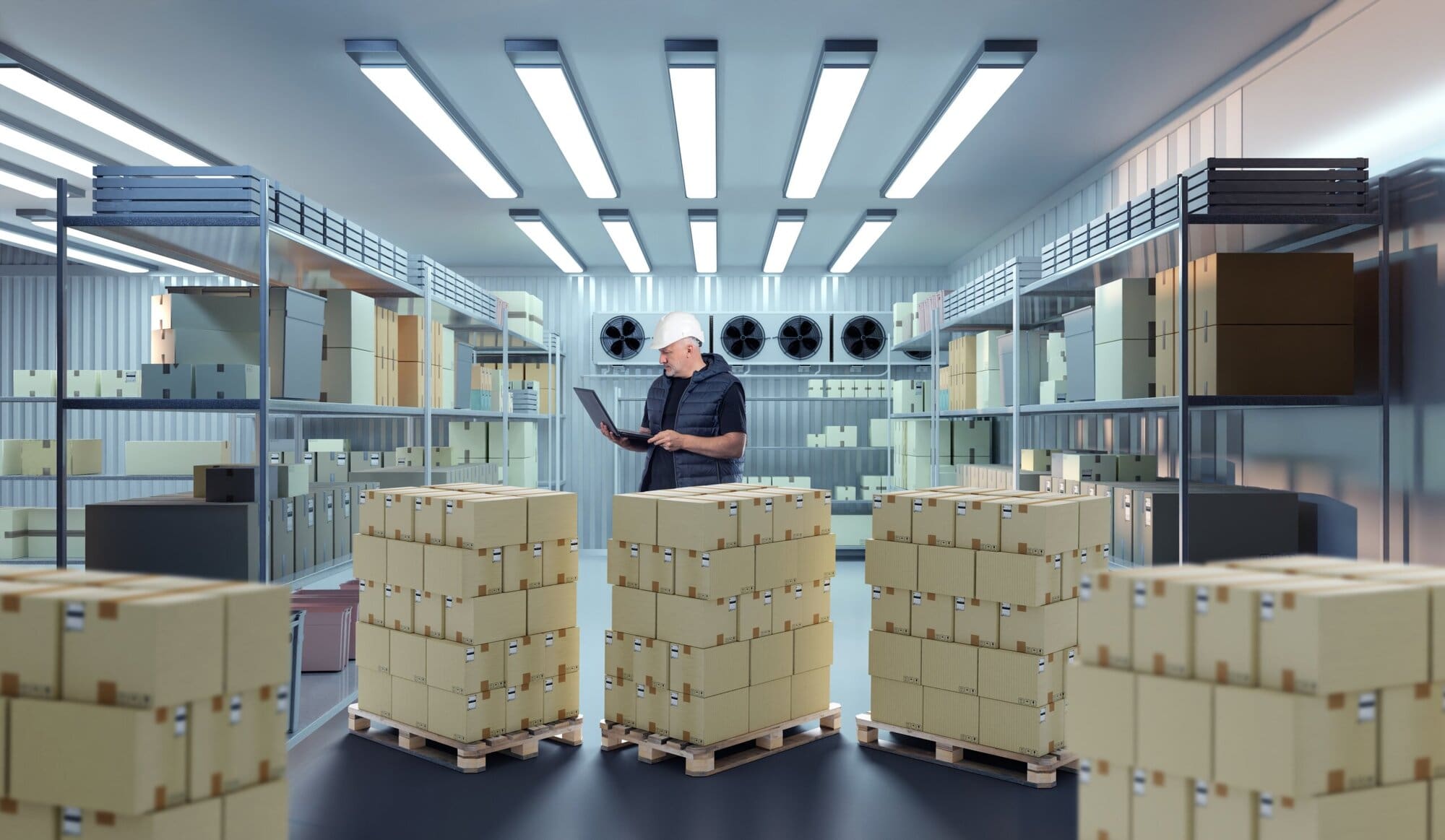
What is LOLER?
The Lifting Operations and Lifting Equipment Regulations 1998 (LOLER) was created to ensure that all lifting operations conducted in the workplace that use lifting equipment are safe. LOLER requires that lifting operations are planned by a competent person. It stipulates that lifting operations must be supervised in an appropriate manner and performed by an employee who is able to complete the task safely.
LOLER also requires that all equipment used for lifting is fit for purpose, appropriate for the task and suitably marked, with evidenced inspection and maintenance records, and that any defects are documented and reported. This not only includes the lift equipment itself, but also includes any lifting accessories used.
Lifting accessories are the pieces of equipment used to attach the load to lifting equipment, providing a link between the two. The LOLER regulations place responsibilities on various parties involved in lifting, including employers, self-employed individuals, equipment owners, and those responsible for planning and supervising lifting operations. Examples of lifting equipment and accessories covered under LOLER include but are not limited to:
- Cranes, which are used during construction, this also includes their support runways
- Goods and passenger lifts, as well as dumbwaiters or other service lifts, and stair-lifts
- Car lifts, which can be seen in mechanics and auto-repair settings
- Lorry lifts, such as for unloading and loading pallets of heavy goods
- Hoists for patients, which are used in hospital beds and care homes and includes bath lifts
- Telescopic handlers, which are used in agricultural work to move bales of hay and other work that reaches to high areas
- Scissor lifts, which is a mobile scaffold platform that raises people and materials safely and securely
- Vehicle cranes and hoists, such as those used for heavy construction or repairs
- Forklifts, used in warehouses to lift goods to sometimes very high levels
- Eyebolts, which are used to secure slings and ropes within a lifting system
- Slings for use in hoists, either hoist goods or people in healthcare settings – sometimes slings are used in veterinary medicine and conservation too
- Hooks, which are part of many types of lifting systems
- Spreader beams, which support wide loads of timber, piping and other heavy loads at each side to prevent them from swinging
- Ropes, pulley systems rely on the integrity of ropes, as do many lifting systems, so they are subject to LOLER regulations.
However, it is important to note, that whilst a particular piece of equipment may not be covered by LOLER, it is still most likely that they are covered by the Provision and Use of Work Equipment Regulations 1998 (PUWER) which enforces similar responsibilities for equipment selection, inspection, maintenance, and training.
Also, the Health and Safety at Work Etc. Act 1974 (HASAWA) places a responsibility on employers and the self-employed for the safety of anybody potentially affected by their work, this includes employees, customers, and members of the public. LOLER compliance is a legal requirement under the Health and Safety at Work Etc. Act 1974.
Under LOLER, lifting equipment has to be carefully checked in a range of circumstances, such as:
- Prior to its initial use (if no declaration of conformity was made during the previous year).
- If it needs to be installed, or re-installed, at a different location.
- In addition, if it has exposure to corrosive conditions, which could compromise its safety.
A LOLER inspection sheet template should be used to record details of examinations such as this example from the Construction Industry Training Board (CITB).
If faults are discovered during inspection then the appropriate authority, either the HSE for industrial premises, or local authorities for other premises, should be informed. In addition the people using the machinery, and those who rent it out to others, should also be notified.
Regulations for Record Keeping
Regulation 11 of LOLER refers to the keeping of information and to maintaining a secure and easily accessible record-keeping system for inspection reports. Detailed records of thorough examinations, inspections, and maintenance activities must be maintained to demonstrate compliance with LOLER regulations.
The main feature of LOLER is the undertaking of a thorough examination of lifting equipment at least every six months, or in accordance with a written scheme. LOLER regulations mandate regular and thorough examinations to identify and address faults, wear and tear, and overall operational standards.
The thorough examination should be undertaken by a competent person. A competent person is defined within the LOLER Approved Code of Practice (ACoP) as someone who “has such appropriate practical and theoretical knowledge and experience of the lifting equipment to be thoroughly examined as will enable them to detect defects or weaknesses and to assess their importance in relation to the safety and continued safe use of the lifting equipment”.
Under LOLER, the term thorough examination includes, where necessary, testing. During a thorough examination it is the competent person who has to decide whether a test is necessary. The competent person must provide a written report of thorough examination and any inspections or tests that they do, and Schedule 1 of LOLER sets out what information must be in the report. Records of all thorough examinations and inspections for all lifting equipment must be kept as follows:
- Thorough examination before first use – Records should be held for lifting equipment, until the employer ceases to use the lifting equipment, for lifting accessories, records should be held for two years.
- Thorough examination before use – Records should be held until the equipment is no longer in use where the safety of the equipment at the place where it was installed / assembled depends on the installation conditions.
- In-service thorough examination (6-monthly, 12-monthly or examination scheme) – Records should be held until the next report is made or two years, whichever is the later.
- In-service inspections / tests – Records should be held until the next report is made
- Periodic maintenance checks – Records should be held until the next test or inspection of the equipment occurs.
In addition to this, it is recommended to also keep detailed records of all equipment checks and repairs. After a LOLER inspection, records and certificates should be stored securely to maintain compliance.
One of the key aspects that the LOLER regulations cover is the planning and organising of lifting operations, this is specified in Regulation 8. Before any lifting operation, LOLER requires that any foreseeable risks involved in the work are identified, and that the appropriate resources including people, necessary for safe completion are appropriately allocated.
There are defined circumstances when a Lifting Plan must be written these circumstances can be found in the LOLER Approved Code of Practice and guidance, but for good practice, a written plan is recommended for all but the simplest, routine lifts.
Like safety checks, inspections and risk assessment and planning, record-keeping is part of a legal obligation for duty holders who own, operate, or have control over lifting equipment. If records cannot be located, or are outdated, this could be breaching compliance with LOLER.
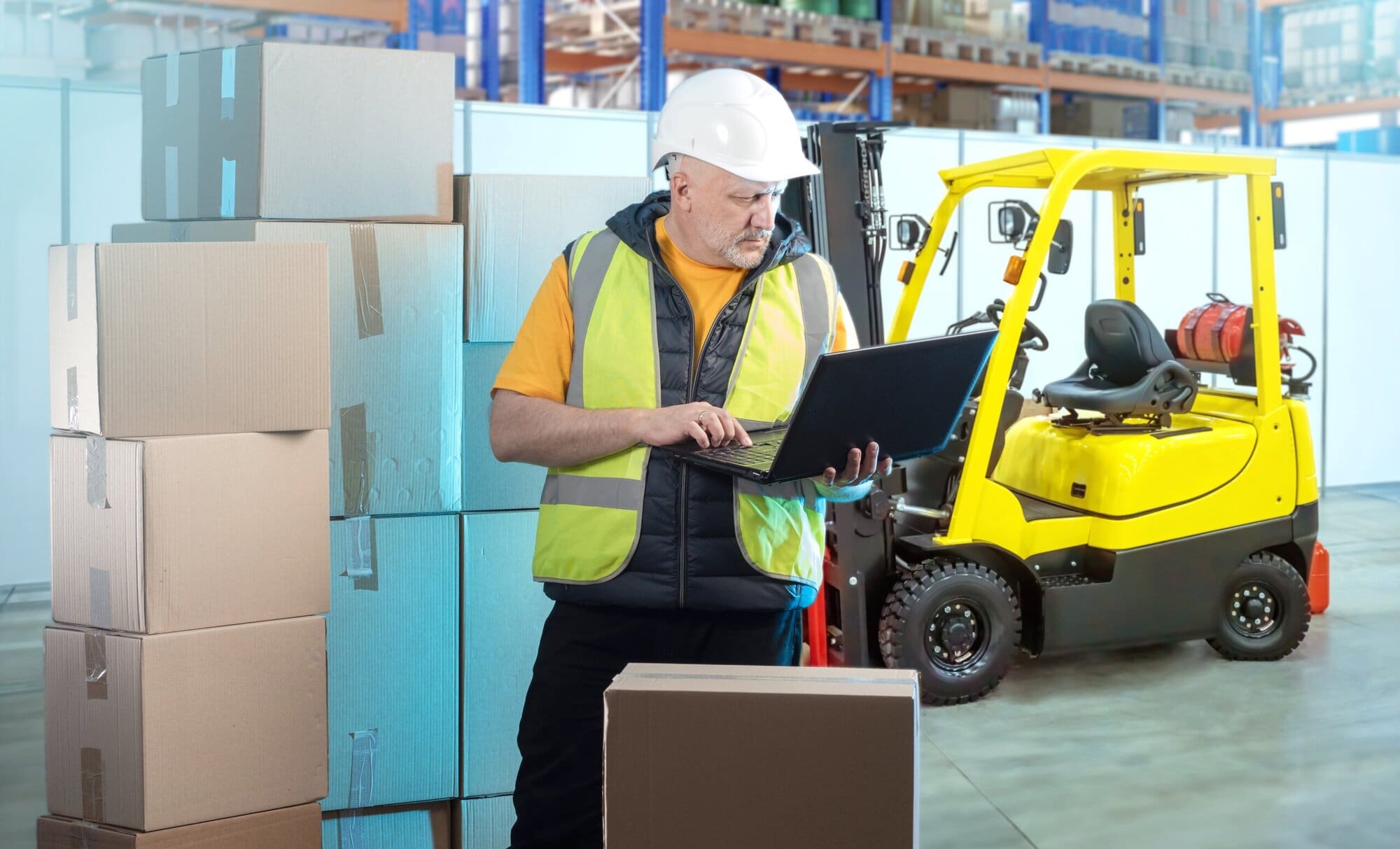
Why Keep LOLER Records?
Record-keeping under LOLER is critical for ensuring that equipment inspections, examinations, maintenance, repairs, training, and usage have been carried out in line with the LOLER regulations to maintain safety standards, and that they are properly documented to evidence that all the necessary steps have been taken to ensure that lifting equipment is safe to use, and that it is being used safely. These records and documentation assist in demonstrating legal compliance with LOLER.
Keeping detailed records of inspections, examinations, maintenance and repairs ensures that workers are using equipment that has been verified as safe and properly maintained. These records of inspections can highlight any potential faults or wear in the lifting equipment, and document any action taken helping to reduce the risk of accidents or injuries.
Record-keeping also helps to provide a clear audit trail showing who was responsible for examining and / or maintaining the lifting equipment. This is important particularly in the event of an accident as these records can be used to show that the necessary inspections and maintenance had been carried out, and by whom should an investigation take place, or should an insurance claim need to be submitted.
Maintenance records help to ensure that lifting equipment is serviced at the right intervals and continues to be in good condition, helping to prevent malfunctions and reducing replacement costs. These records can also assist the appointed competent person in scheduling regular inspections and maintenance.
Records of any repairs undertaken are important to confirm that the lifting equipment has been restored to safe working order. Accurate records provide evidence that the necessary repairs were completed to meet safety standards.
Training records help to promote a safe and efficient work environment. They provide evidence that certain employees have completed appropriate training and obtained any relevant certifications that meet occupational needs and / or regulatory compliance requirements.
It is an employer’s responsibility to take the necessary steps to train, direct and instruct workers who may be inspecting, maintaining, planning the use of, and using lifting equipment on maintaining and / or operating the equipment safely and within regulatory boundaries. In the event of any accidents or incidents involving lifting equipment, training records will be requested by investigatory authorities.
Health and safety inspectors have the role to enforce LOLER and this can happen during a health and safety audit or inspection at any time. This means you must keep all documentation related to your thorough LOLER inspections, examinations, maintenance, repairs, and training properly filed, easily accessible and available for inspection if requested by the authorities.
What should LOLER records include?
Under LOLER, employers have a legal responsibility to ensure that lifting operations are properly planned, supervised, and carried out by competent individuals. The LOLER regulations and supporting LOLER Approved Code of Practice and guidance outline specific requirements that employers must adhere to. These include conducting thorough risk assessments, providing adequate training and supervision, and maintaining equipment in a safe condition. Failure to comply with LOLER can result in serious consequences, including fines and legal action.
Most lifting operations must have an associated lift plan. This plan should ensure that the correct risk assessments have been carried out and documented, detail which piece of equipment is appropriate for the task and stipulate the method for lifting, and should mitigate any conditions that could endanger the employee or others in the area. The risk assessment should assess all the potential risks involved and identify who could be harmed by them and could include:
- The location where the operation takes place
- Pre-use check(s)
- Other hazards nearby
- Limited visibility
- How loads are attached and / or detached
- Whether people will be lifted
- The potential for overloading
- Actions taken to prevent or mitigate the risk
The lift plan needs to clearly set out the actions involved at each stage of the operation and identify the responsibilities of those involved. The degree of planning and complexity of the plan will vary and should be proportionate to the foreseeable risks involved in the work. More complex tasks need more in-depth and sophisticated planning, and these can typically include expert input, constant monitoring and supervision.
This type of planning is usually undertaken by a specially trained member of the team. To be compliant with LOLER, an individual plan must be made for each situation to fit the circumstances. A record of this lift plan and associated risk assessment should be kept and be made available during HSE audits or inspections.
LOLER records should also be kept listing every equipment inspection and details of any defects found, along with evidence that any defects have been reported to the right authorities and to the responsible people. The competent person who completes the inspection is responsible for recording all tests performed and their results.
If any defects are identified they then need to be presented in a report to the responsible person, usually the business owner, whose responsibility is to address them, rectify them and to keep a record as proof of the actions that they have taken to manage the risks.
After every LOLER inspection, all lifting equipment, including accessories, must be clearly marked with a label. This is to indicate their safe working loads (SWL) that is the maximum load the equipment can safely lift the safe working load. Lifting equipment and accessories should also carry a label highlighting any factors that could make the equipment unsafe. If the lifting equipment will be used to lift people, the number of people it can carry should also be marked clearly.
Anyone who uses or requires lifting equipment must have been given suitable and sufficient instruction and training to carry out these functions, and the training records must be kept for inspection. It is essential to keep precise records of all training offered together with details of those who have participated, the dates of the training, and dates of when refresher training may be required.
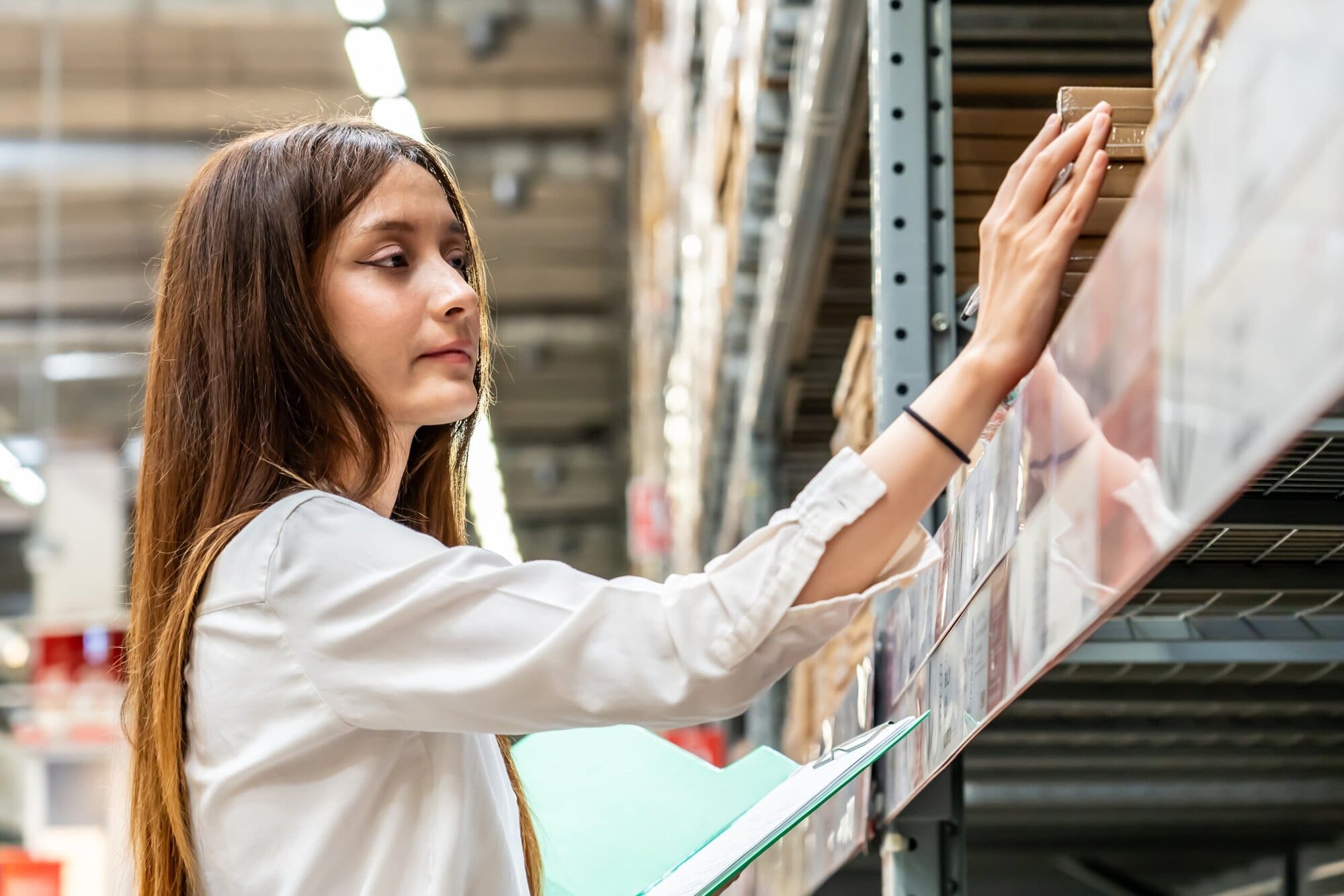
Conclusion
Not complying with the LOLER regulations including not keeping comprehensive records is a criminal offence under UK law, which can result in legal action against employers for gross misconduct. This can lead to heavy penalties, including substantial fines and even imprisonment. Although fines are proportional to the LOLER breach, a well-known car manufacturer was fined £200,000 and ordered to pay costs of £17,218 for breaching LOLER by using faulty lifting equipment, and although no one was actually harmed, it could well have been a very different outcome.
In another case, a construction site manager was fined for a number of breaches of LOLER including non-compliance with record keeping by not providing a thorough examination certificate for a piece of faulty equipment that injured a worker.
LOLER is designed to prevent harm, this is why it is extremely important to strictly follow the LOLER Approved Code of Practice and guidance, and to keep up-to-date, complete LOLER records in order to not only comply with the regulations, but also to ensure that all safety measures taken are documented, not to do so is a direct violation of LOLER regulations.