In this article
Lifting equipment plays a critical role in a wide range of industries—from construction and manufacturing to logistics and warehousing. Whether it’s a crane moving heavy steel beams or a forklift transporting pallets, lifting equipment is essential for efficiency and productivity.
However, the very nature of lifting operations also introduces serious safety risks. Faulty equipment, improper use or neglected inspections can lead to accidents, injuries and even fatalities. Not to mention legal and financial consequences for businesses. In 2023-2024, 138 workers were killed in work-related accidents. There were also 87 members of the public killed in work-related accidents in the same year.
That’s why lifting equipment safety isn’t just a box-ticking exercise. It’s a legal obligation under UK law, and more importantly, a fundamental part of protecting workers and ensuring smooth operations. Regular inspections, carried out by a competent person, help identify potential hazards before they escalate and ensure all equipment meets required safety standards.
This guide is intended for everyone responsible for the use, inspection or maintenance of lifting equipment. That includes business owners, site managers, health and safety officers and anyone tasked with ensuring compliance under the Lifting Operations and Lifting Equipment Regulations 1998 (LOLER).
What is lifting equipment?
Lifting equipment refers to any work equipment used for lifting or lowering loads, including any accessories used to anchor, fix or support the equipment. Under the Lifting Operations and Lifting Equipment Regulations 1998 (LOLER), this definition covers a broad range of tools and machinery commonly used across industries such as construction, manufacturing, warehousing and logistics.
Common Examples of Lifting Equipment
Here are some example:
- Cranes: Tower cranes, mobile cranes and overhead gantry cranes used to lift heavy materials vertically and move them horizontally.
- Hoists: Manual or powered devices used to raise and lower loads vertically. They’re often used in garages and workshops.
- Forklifts: Industrial trucks used to lift and move loads over short distances. They’re often fitted with forks, clamps or platforms.
- Lifting platforms: Including scissor lifts and cherry pickers. They’re used for raising personnel or equipment to higher levels.
- Vehicle tail lifts: Fitted on lorries and vans to load goods safely into the vehicle.
- Winches and jacks: These are typically used for raising vehicles or machinery during maintenance or recovery operations.
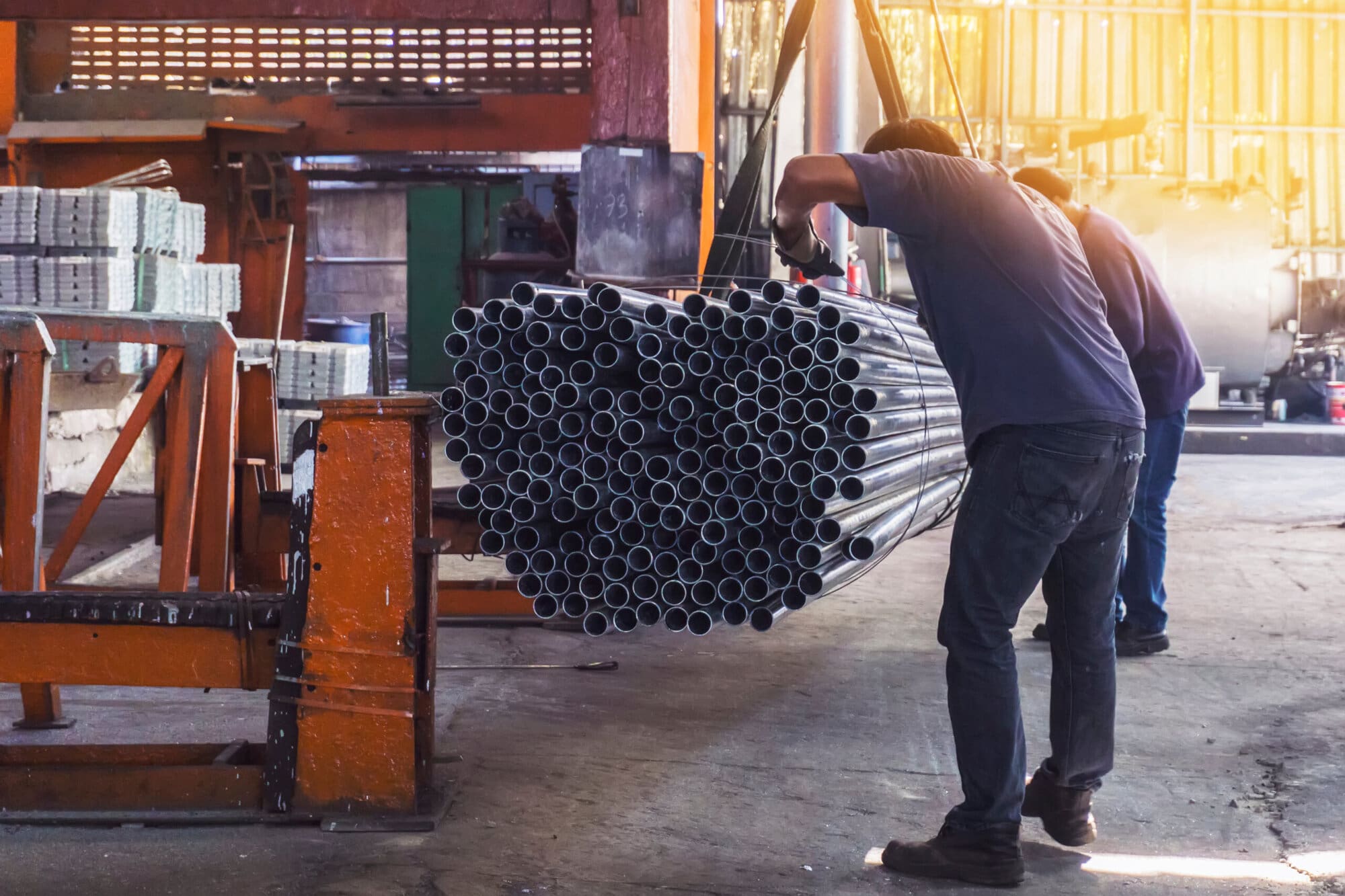
Lifting Accessories vs Lifting Equipment
It’s important to distinguish between lifting equipment and lifting accessories. As both fall under LOLER but have slightly different roles and inspection requirements.
Lifting accessories are items used to attach the load to the lifting equipment. These include:
- Slings (chain, rope or webbing)
- Shackles
- Eyebolts
- Hooks
- Lifting beams and spreader bars
While they don’t lift loads on their own, accessories are critical to the safe use of lifting systems. Any failure in these components can result in dropped loads or serious injury, so they are subject to the same rigorous inspection standards as the primary equipment. Understanding what qualifies as lifting equipment and accessories ensures the correct inspection protocols are followed and helps maintain compliance with UK safety legislation.
Regulations around lifting equipment
Two key sets of regulations apply for lifting equipment safety in the UK. These are the Lifting Operations and Lifting Equipment Regulations 1998 (LOLER) and the Provision and the Use of Work Equipment Regulations 1998 (PUWER). These laws set out the minimum legal requirements for the safe use, maintenance and inspection of lifting equipment in the workplace.
Overview of LOLER 1998
LOLER was introduced to ensure that lifting operations we properly planned, supervised and carried out. LOLER applies to any workplace using lifting equipment. There are specific responsibilities for employers, the self-employed and people in control of lifting equipment.
The Key LOLER requirements include:
- All lifting equipment must be suitable for the task. It must be marked with its safe working load (SWL) and positioned or installed to minimise risks.
- Thorough examinations must be carried out at regular intervals by a competent person.
- Equipment must be clearly labelled, properly maintained and only used by trained individuals.
- Records of inspections and repairs must be kept and made available to enforcing authorities.
How LOLER Links with PUWER
While LOLER deals specifically with lifting operations, PUWER is a broader set of regulations that applies to all work equipment and lifting equipment. PUWER requires that:
- Equipment is maintained in a safe condition and inspected where necessary to ensure safety.
- Only people who have received adequate training and instruction can use work equipment.
- Equipment is used in accordance with manufacturer’s instructions and risk assessments.
In essence, PUWER ensures the equipment itself is safe, while LOLER governs how it is used during lifting operations.
Duties of Employers and Employees
Under LOLER and PUWER, both employers and employees have clear responsibilities:
Employers must:
- Ensure lifting equipment is safe and suitable for the task.
- Arrange regular inspections and maintenance.
- Appoint a competent person to carry out thorough examinations.
- Provide training and supervision to anyone operating or using lifting equipment.
- Keep up to date with inspection records.
Employees must:
- Use equipment correctly and safely, following any training or instructions.
- Report defects or concerns immediately.
- Avoid lifting equipment they are not trained or authorised to use.
Insurance and Legal Liability
Failure to comply with LOLER and PUWER can have serious consequences. If an accident occurs due to unsafe lifting equipment or neglected inspections, employers may face prosecution by the Health and Safety Executive (HSE), fines, imprisonment, invalidated insurance policies (particularly if inspection records are incomplete or missing), civil claims for injury or loss.
Lifting equipment competent person
One of the core requirements of LOLER is that the equipment must be thoroughly examined by a competent person at regular intervals. This role is vital for ensuring the ongoing safety, reliability, and compliance of lifting operations.
Who qualifies as a competent person under LOLER?
LOLER does not define a specific qualification for a competent person. The Health and Safety Executive outlines that they must have:
- Practical and theoretical knowledge of lifting equipment
- Experience in assessing safety-critical components
- The ability to identify defects, assess risk and determine whether continued use is safe.
The competent person must be sufficiently independent and impartial to make objective decisions. In many cases, this means someone who is not directly responsible for the maintenance or operation of the equipment, in order to avoid conflicts of interest.
Internal vs External Inspections
Businesses can appoint either an in-house competent person or an external inspection body, depending on their needs and resources.
Internal competent persons are typically used by larger companies with dedicated health and safety teams or engineering departments. They must still meet the competency requirements and have no vested interest in the continued use of the equipment.
External inspectors are often third-party inspection firms or insurers. They are widely used by SMEs and are usually certified by recognised bodies like the Lifting Equipment Engineers Association (LEEA) or the Safety Assessment Federation (SAFed).
The key is ensuring that the competent person—internal or external—is qualified, impartial and appropriately experienced.
Training and Qualifications Required
There’s no legal requirement for a specific qualification or certificate. However, formal training and certifications are strong indicators of competency. Relevant qualifications could include LEEA diplomas or certification, IOSH and NEBOSH courses (with lifting equipment components) and engineering or mechanical qualifications with practical lifting knowledge.
Ongoing professional development is also essential to stay current with changing regulations and equipment standards.
Role in Risk Assessments and Inspections
A competent person’s duties go beyond checking for defects. Their responsibilities include:
- Carrying out thorough examinations of lifting equipment and accessories at legally required intervals.
- Assessing the risk associated with any identified defects and advising on actions needed (e.g. repair, replacement, withdrawal from service).
- Determining whether lifting equipment can continue to be used safely until remedial action is taken.
- Providing a written report of examination that includes findings, recommendations and deadlines for any corrective action required.
They may also support or inform lifting risk assessments. For example, if they identify mechanical or structural vulnerabilities in the equipment setup.
Types of Inspections
Regular and appropriate inspections of lifting equipment is essential for the safe operation and legal compliance under LOLER and PUWER. Different types of inspections are required at various stages of an equipment’s use. Each has a distinctive purpose in identifying wear, damage or other safety risks.
Pre-Use Checks
These are quick visual and functional assessments carried out by the equipment operator before each use. These checks help spot obvious defects that could pose an immediate danger like frayed or damaged slings and ropes, leaks in hydraulic systems, missing safety guards or locking pins and signs of corrosion, wear or distortion.
Ongoing In-Service Inspections
These are routine or interim inspections. They’re more detailed than a pre-use check and usually happen weekly or monthly depending on the intensity and environment of use. They focus on:
- Signs of mechanical wear
- Stability and structural integrity
- Functionality of limiters, brakes and controls
- Lubrication and moving parts.
These inspections should be recorded. Any defects should be addressed before the equipment is used again. These inspections don’t replace formal examinations, but they do help to identify emerging issues early.
Thorough Examinations
A thorough examination is a detailed and systematic inspection. It is carried out be a competent person, as required by LOLER. These examinations are legally mandated. They must take place:
- Before first use (unless the equipment has an EC Declaration of Conformity issues in the last 12 months).
- Every 6 months for lifting accessories and equipment used to lift people.
- Every 12 months for all other lifting equipment.
- After exceptional circumstances (e.g., modifications, damage or prolonged storage).
The examination may include disassembly, functional testing and measurements of wear. There must be a formal written report of examination. This must have defects and remedial actions listed with deadlines.
Testing vs inspections – what’s the difference?
Although the terms are often used interchangeably, there is a clear distinction between testing and inspection.
Inspection involves visually and manually checking equipment to assess its condition and functionality. It focuses on identifying defects, damage or deterioration.
Testing involves applying a load or operating the equipment under controlled conditions to assess its performance or strength. This could include a load test to confirm a crane can safely lift its rated load.
Testing may be required as a part of a thorough examination, after installation or major repairs or when recommended by the manufacturer.
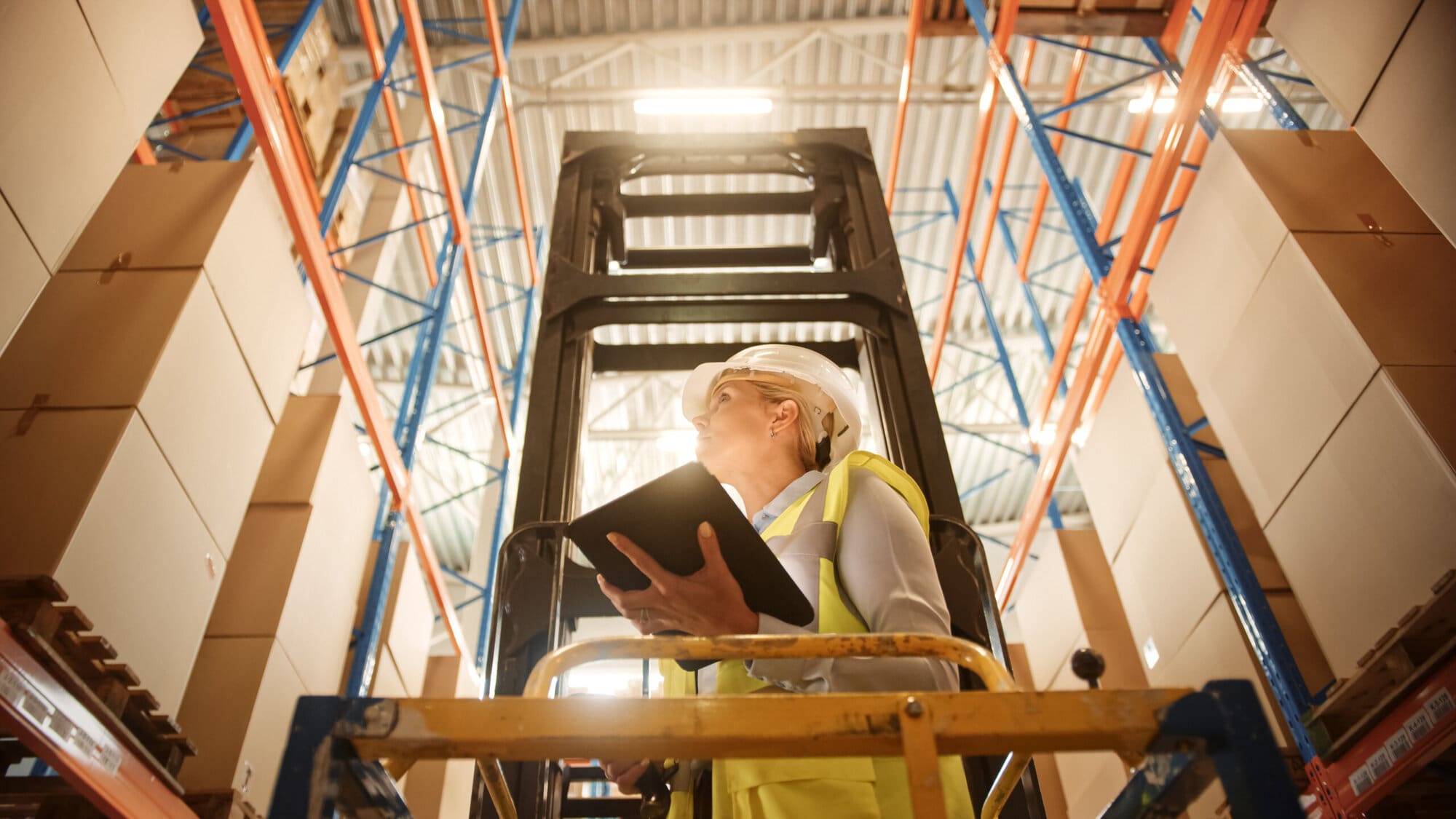
What to check for lifting safety
Ensuring lifting equipment remains safe for use means checking for both mechanical issues and environmental factors that could compromise performance. These checks should be carried out during pre-use inspections, in-service check and thorough examinations. This depends on the situation and frequency of use.
Load capacity and clear labelling
All lifting equipment must be clearly marked with its Safe Working Load (SWL)—the maximum it can lift safely. Accessories like slings and shackles must also display relevant load limits. Checks should confirm that:
- Load ratings are visible, legible and appropriate for the task.
- There’s no evidence of tampering or mismatched components.
- The equipment in use is suitable for the lifting plan and working environment.
Overloading or using equipment with unclear ratings is a major cause of lifting incidents and a breach of LOLER regulations.
Wear and Tear
Regular use, especially in hard environments, can lead to degradation of components.
Inspect for:
- Frayed or cut slings and ropes.
- Cracked or worn hooks, shackles and chains.
- Corrosion on metal surfaces or inside joints.
- Distortion or elongation of load-bearing elements.
- Loose or missing pins, bolts or retaining clips.
Even minor signs of damage should be investigated and, if necessary, equipment removed from service until assessed by a competent person.
Functionality of brakes, limit switches and safety devices
Lifting equipment often includes mechanical and electrical safety features to prevent accidents. These must be tested regularly to ensure correct operation. Items to check include:
- Brakes that hold loads securely without drift or slippage.
- Upper and lower limit switches to prevent over-travel.
- Emergency stop functions and safety cut-offs.
- Warning alarms, sensors or indicators (where fitted).
Structural Integrity
A close inspection of the frame and load-bearing structures is essential. This will catch signs of fatigue or failure before they escalate. Look for:
- Cracks or fractures, especially around welds.
- Rust or pitting on metal surfaces.
- Loose fasteners, rivets or joints.
- Bent or twisted structural members.
These issues often indicate overloading or long-term wear. They should always be assessed by a competent person before further use.
Environmental Risks
Lifting equipment performance can be affected by external conditions. This is especially true on construction sites or warehouses with varying climates. Risks include:
- Moisture and water ingress. This can lead to rust or electrical hazards.
- Extreme temperatures. This can affect hydraulic systems, metal strength and lubrication.
- Dust, grit or chemical exposure. This can clog or corrode moving parts.
- Wind or unstable ground. Particularly during outdoor lifts.
Equipment should be selected and maintained with environmental factors in mind. For example, stainless steel accessories may be more suitable for corrosive environments and hydraulic systems may need specific fluids for cold temperatures.
When should inspections be carried out
Timely inspections are essential for maintaining the safety and reliability of lifting equipment. The frequency and timing of checks are defined in part by LOLER, but they can also vary depending on how the equipment is used, its environment and manufacturer guidelines.
Before First Use
New lifting equipment (or equipment brought into use for the first time in the UK) must be:
- Thoroughly examined by a competent person if no valid EC Declaration of Conformity exists within the previous 12 months.
- Tested, if required, to confirm its suitability for safe operation.
This ensures that the equipment is installed correctly and functions as intended before being used in lifting operations.
Regular Intervals (LOLER Schedule)
Under LOLER, lifting equipment must undergo thorough examinations at specific intervals:
Every 6 months for:
- Equipment used for lifting people.
- All lifting accessories (sling, shackles, eyebolts, etc.).
Every 12 months for:
- All other general-purpose lifting equipment (e.g. cranes, hoists, forklifts).
These time frames are the maximum period between inspections. More frequent checks may be necessary depending on use intensity or environmental risks.
After Exceptional Circumstances
In addition to scheduled inspections, a thorough examination is also required:
- After installation or relocation to ensure correct setup.
- Following an accident, overload or failure.
- After modifications or significant repairs.
- Following long periods out of use.
Any of these events could compromise the integrity or safe function of the equipment. It’s the employer’s duty to ensure it is re-validated before being put back into service.
According to the Manufacturer’s Instructions
Most lifting equipment comes with manufacturer-specified maintenance and inspection schedules. These should always be followed in addition to legal requirements, especially if the equipment is highly specialised or used in extreme conditions.
Daily and Weekly Checks
Although not legally required under LOLER, daily pre-use checks and weekly in-service inspections are considered best practice. They help catch minor issues early, reducing the risk of serious incidents and prolonging equipment life.
These checks should be:
- Carried out by trained operators.
- Documented, especially for high-risk operations.
- Followed up promptly if there are any identified issues.
Record-Keeping and Documentation
Keeping accurate records (and keeping them up to date) is a legal requirement under the LOLER regulations. Proper documentation provides evidence of compliance. It also supports safe operations. In the event of an incident or audit, these records are crucial.
The Legal Requirements for Maintaining Records
LOLER requires employers:
- Keep a record of all thorough examinations and tests carried out on lifting equipment.
- Make records available to enforcing authorities like the HSE upon request.
- Ensure the records are retained for a specified period, depending on the equipment and the type of inspection.
Failure to comply can result in enforcement action, fines or liability in the event of an accident.
What Needs to Be Reported
You must include the following on your inspection and examination records:
- Date of inspection.
- Identification of the equipment (e.g., serial number or asset tag).
- Name and qualifications of the competent person conducting the examination.
- Details of the inspection (scope, method, conditions).
- Findings (including any defects or wear observed).
- Assessment of risk posed by any defects.
- Recommendations for remedial action, if required.
- Confirmation of whether the equipment is safe to continue in use.
- Date of the next due examination.
Where defects pose a serious and immediate risk, the competent person must report it immediately to the duty holder. They must submit a written report to the relevant authority (e.g. HSE or local authority)/
How Long to Keep Records
The minimum retention period under LOLER is at least 2 years from the fate of the thorough examination or until the next report is made, whichever is longer.
In some industries or for internal compliance purposes, businesses can choose to keep records for longer. Particularly when the equipment has a long service life of is critical to operations.
Paper vs Digital Records
Both are acceptable as long as they’re legible, secure and easily retrievable. Digital records are popular because they allow for centralised management and automatic reminders for upcoming due inspections. They also reduce the risk of loss or damage compared to paper copies.
However, businesses should make sure their digital systems are properly backed up and comply with data protection laws if they contain personal details. Regardless of the format, they should be stored in a structured way and be reviewed regularly to ensure they remain compliant.
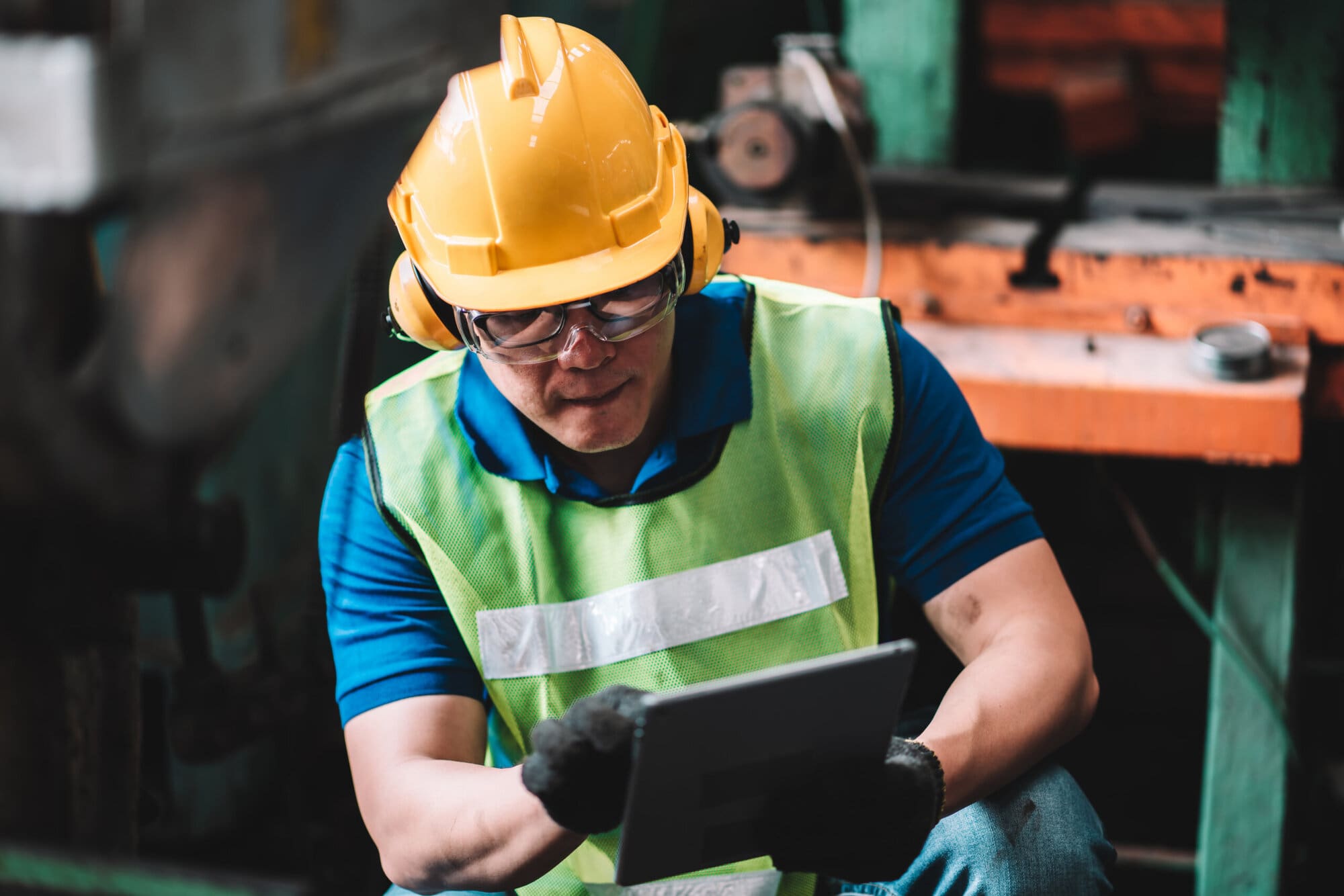
Reporting defects and issues
Spotting a defect in lifting equipment is only part of the responsibility. Acting on issues promptly and correctly is just as important. Under LOLER and general health and safety law, both employers and workers have duties when it comes to reporting, documenting and resolving equipment issues.
If any fault, damage or deterioration is found during a check or inspection:
- Stop using the equipment immediately if there’s any risk to safety.
- Tag or isolate the item clearly to prevent further use.
- Report the issue to a manager, supervisor or responsible person straight away.
- Record the defect in maintenance logs or defect reports.
For high-risk defects (those that could cause injury), you should seek a formal report from the competent person. This should be shown to the employer and the enforcing authority.
The competent person’s role includes writing a written report of their examination and outlining the nature and severity of issues. If the issue poses a serious and imminent danger, a copy of the report should be sent to the enforcing authority within 28 days, but it should be as soon as possible.
The report must specify whether the equipment can continue to be used (possibly with conditions) or whether it should be taken out of service immediately.
Employers must act on all reported defects without delay. They should ensure that the defective equipment is repaired, re-tested or replaced as necessary. There should also be a clear audit trail of actions taken to address the issue. Finally, all resolutions or ongoing risks should be communicated to affected staff. Delaying action or reusing defective equipment without proper clearance is a serious breach of LOLER. It could lead to prosecution if an incident then occurs.
Workers have a legal duty under the Health and Safety at Work Act 1974 to:
- Take reasonable care for their own safety and that of others.
- Use equipment according to training and instructions.
- Report defects promptly to prevent harm.
This means all staff operating lifting equipment should be trained to identify basic faults and know how to escalate concerns.
Conclusion
Lifting equipment plays a critical role in many industries. But with it comes the responsibility to ensure it is used and maintained safely. By understanding the legal requirements under LOLER and by conducting regular inspections, businesses can reduce the risk of accidents and legal liability.