In this article
Electrical safety is a fundamental aspect of maintaining safe living and working environments, as electrical hazards pose serious risks that can lead to fires, electric shocks, injuries and costly equipment damage. In the UK, electrical incidents are a major cause of workplace accidents and household fires, with statistics showing that 53.4% of accidental domestic fires have an electrical origin and approximately 1,000 workplace accidents and 30 fatalities involving burns or electrical shocks are reported every year. Recognising these risks is essential, as is understanding the role of regular inspections and maintenance in mitigating them.
The primary risks associated with electrical systems include:
- Faulty wiring: Improper or deteriorated wiring can lead to short circuits, overheating and, ultimately, fire hazards. This is common in older buildings or properties that have undergone multiple renovations without updated electrical assessments.
- Overloaded circuits: When circuits are forced to handle excessive electrical loads, they can overheat and create significant fire risks, often without obvious warning signs.
- Damaged equipment: Worn-out, broken or malfunctioning equipment can lead to electric shocks or even cause circuit failures, which can pose dangers both to users and to the integrity of the system.
- Outdated systems: Older electrical systems may not meet current safety standards and are often incompatible with modern electrical loads. This increases the risk of faults or dangerous failures.
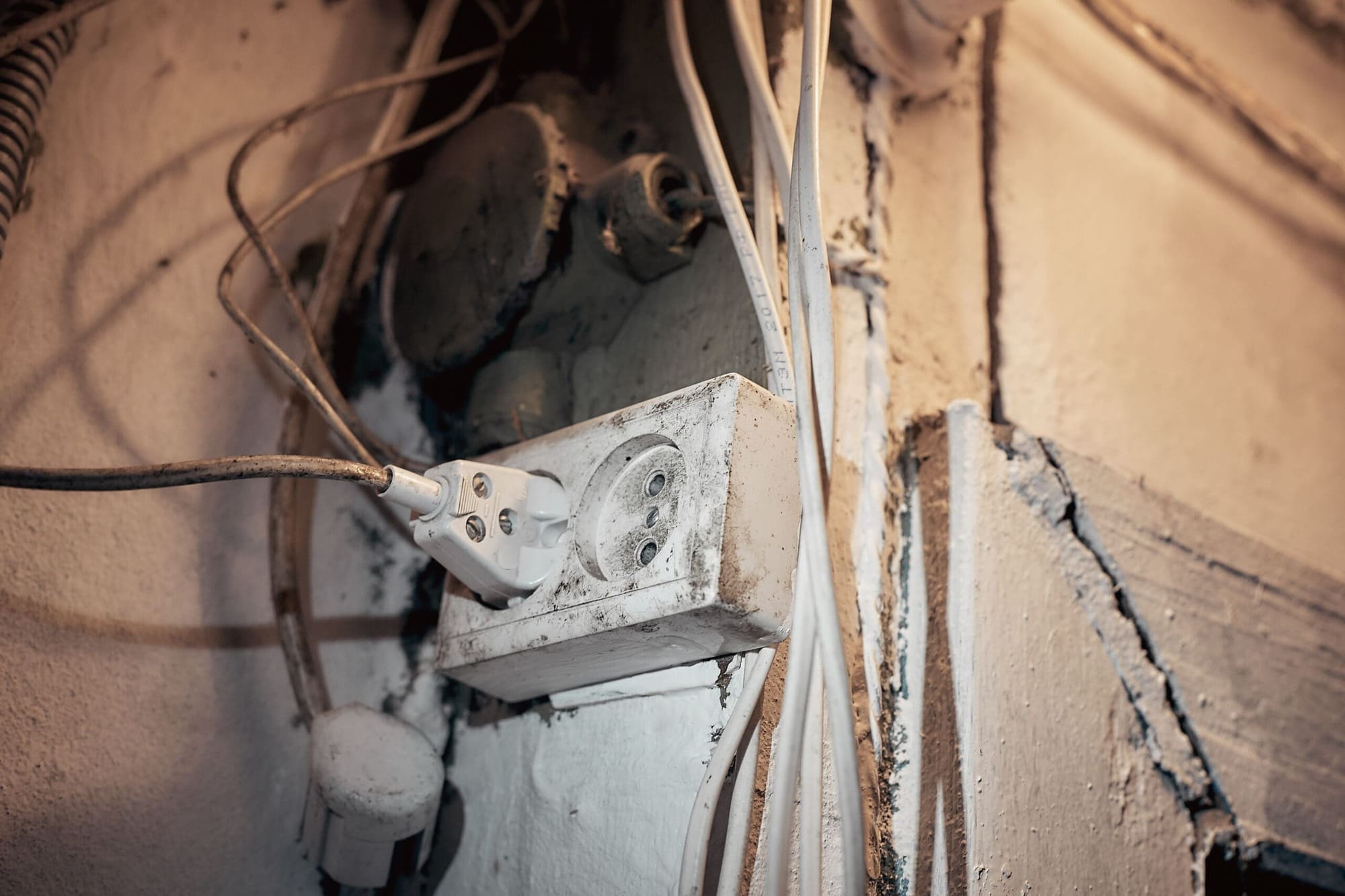
Electrical safety refers to the practices, guidelines and measures designed to prevent electrical hazards such as shocks, burns, fires and explosions. Because electrical hazards can result from faulty electrical systems, equipment malfunctions or improper handling of electrical devices, electrical safety involves a range of actions designed to address these risks, from safe equipment handling and maintenance to the regular inspection of electrical systems. Electrical safety aims to protect individuals and property from the dangers posed by electricity.
Regular inspections and maintenance are essential in identifying these issues early and addressing them proactively. This not only protects people from harm but also ensures compliance with UK safety standards, maintains equipment longevity and prevents costly emergencies.
Why Regular Electrical Inspections are Crucial
Regular electrical inspections are essential for maintaining safe, efficient and long-lasting electrical systems in both residential and commercial settings. Electrical inspections can have multiple benefits, such as:
Preventing major accidents
One of the primary reasons for regular electrical inspections is accident prevention. Electrical faults, such as worn wiring, loose connections and overloaded circuits, can lead to severe incidents like fires, electrocution or power outages if left unaddressed. Routine inspections allow certified electricians to detect potential hazards before they escalate, thereby preventing accidents and ensuring a safer environment for occupants.
Compliance with safety regulations
In the UK, laws and regulations mandate that electrical installations be maintained to prevent hazards. Compliance with these laws requires regular inspections to verify that all electrical systems are functioning safely and effectively. Regular inspections ensure compliance with these standards and help property owners avoid penalties and legal liabilities. Compliance is especially critical for business owners, who are legally responsible for maintaining a safe working environment. Regulations to be aware of in the UK include:
Electricity at Work Regulations 1989
These regulations mandate that electrical systems must be maintained to prevent danger and that employers must ensure that work involving electrical systems is done safely. This applies to all workplaces and requires regular maintenance and inspection of electrical systems to prevent accidents such as electric shocks, burns and fires.
The IET Wiring Regulations (BS 7671)
These regulations set out standards for electrical installations in the UK. This code of practice, published by the Institution of Engineering and Technology (IET), is not legally binding by itself but is widely used to comply with other legal requirements. The regulations specify safe wiring practices and the necessary technical requirements for electrical installations in homes, workplaces and public spaces.
The Building Regulations 2010: Electrical Safety – Dwellings Approved Document P
Approved Document P requires that all electrical installations in homes meet certain safety standards to protect occupants from fire and electric shock risks. Electrical work that falls under Part P, such as adding new circuits or working in high-risk areas like kitchens and bathrooms, must either be performed by a registered electrician or certified by a building control body.
Health and Safety at Work etc. Act 1974
The Health and Safety at Work etc. Act (HSWA) is a broader regulation that covers various safety aspects in the workplace, including electrical safety. Employers are required to provide a safe working environment, which includes managing electrical risks. Compliance with the HSWA means that employers must identify potential electrical hazards and take measures to control or eliminate these risks.
Provision and Use of Work Equipment Regulations 1998 (PUWER)
PUWER mandates that all work equipment, including electrical devices and installations, must be safe for use and maintained in good condition. Employers must ensure that equipment is inspected regularly, that it is suitable for the task and that employees using it are trained and informed about potential risks.
The Regulatory Reform (Fire Safety) Order 2005
This is the primary legislation governing fire safety, including the risks posed by electrical systems. It requires a responsible person, such as an employer, landlord or building owner, to conduct fire risk assessments that include the inspection of electrical systems as a potential source of fire hazards. It mandates that appropriate preventative and protective measures are in place.
The Management of Health and Safety at Work Regulations 1999
These regulations require employers to conduct risk assessments, including those for electrical hazards, to ensure a safe work environment. These regulations require employers to implement and maintain health and safety management systems that assess and mitigate risks from electrical installations.
Prolonging equipment lifespan
Regular inspections can extend the life of electrical systems and appliances. By catching issues early, such as minor wear, potential overloads or loose connections, property owners can address small problems before they lead to major failures. This preventative approach minimises wear and tear on electrical components, reduces the need for expensive replacements and extends the lifespan of both systems and equipment.
Energy efficiency
Electrical faults, such as poor grounding or failing circuits, can lead to unnecessary power consumption, which can raise energy costs. Regular inspections identify these faults and improve system efficiency, which helps to reduce waste and ensures that systems use only the power they need. By promoting energy efficiency, inspections not only lower energy bills but also contribute to a reduced environmental footprint.
What an Electrical Inspection Involves
An electrical inspection is a thorough assessment conducted by a certified electrician to ensure that an electrical system is functioning safely, efficiently and in compliance with relevant standards.
During an electrical inspection, various key components are thoroughly examined to detect any potential hazards or faults. These include:
- Wiring: Inspectors check the condition of wiring throughout the property, looking for signs of wear, damage or outdated materials that may pose risks of overheating or fire.
- Outlets and switches: Outlets and switches are tested to ensure proper function and safety, particularly looking for loose connections, exposed wires or signs of melting.
- Electrical panels and circuit breakers: Panels are inspected to verify that they are not overloaded and that all circuits are functioning correctly. Circuit breakers are checked to ensure they are correctly rated and operational to prevent dangerous overloads.
- Grounding systems: Proper grounding prevents electrical shocks and helps stabilise electrical currents. Inspectors check grounding systems to confirm they’re functioning as designed, especially in areas with higher moisture levels or where equipment requires grounding.
- Residual Current Devices (RCDs): RCDs or Ground Fault Circuit Interrupters (GFCIs), are critical for preventing shocks. Inspectors check that RCDs are correctly installed and functioning to shut off power in the event of a ground fault.
A visual inspection is the initial phase of any electrical inspection, focusing on easily observable signs of deterioration or damage, which may indicate underlying issues. Inspectors look for frayed wires, discolouration or cracked insulation, which can indicate ageing or damage that requires attention. Components that are exposed to moisture, such as those near plumbing fixtures or in damp areas, are checked for signs of corrosion or rust, which can lead to compromised connections. Plug sockets, switches and breakers are examined for any loose or faulty connections that can create sparks, which pose serious fire risks.
Beyond visual inspection, electrical systems are tested with professional tools to measure performance and identify hidden issues. Some common tools and techniques include:
- Voltage meters: Voltage meters are used to measure the voltage levels in circuits and verify that all components are receiving the correct power levels and that there are no issues such as voltage drops.
- Thermal imaging cameras: These cameras detect overheating by identifying temperature variations, which can indicate poor connections, overloaded circuits or malfunctioning equipment. This technology is particularly useful in identifying issues that could lead to fires.
- Insulation resistance testers: Insulation testing is done to ensure wires are properly insulated to reduce the risk of short circuits or electric shock. This test measures the resistance of insulation and helps inspectors determine if wiring is still safe for continued use.
A crucial part of an inspection is ensuring that the electrical system meets UK regulatory standards. To do this, electrical inspections should be conducted by certified electricians. Certified inspectors are trained to understand and apply current regulations and ensure that every aspect of the system meets safety codes and standards. Additionally, after completing an inspection, professionals issue an Electrical Installation Condition Report (EICR) if the system meets standards. This report is essential for both property owners and insurers, as it provides official documentation that the system has been evaluated and deemed safe. If an issue is identified, inspectors will provide recommendations for repairs or upgrades needed to bring the system up to standard to help property owners address risks proactively.
Benefits of Regular Electrical Maintenance
Regular electrical maintenance is essential in all settings, including in homes and businesses. One of the most significant safety benefits of regular maintenance is the prevention of electrical fires. Faulty wiring, loose connections and overloaded circuits can lead to overheating, which, if undetected, can spark fires. Maintenance ensures that these potential hazards are addressed early, which helps to reduce the risk of fires and protect both occupants and property.
Electrical maintenance can also help to prevent electrical shocks. Electrical shocks can occur when systems are improperly grounded or when outlets and appliances are not functioning correctly. Regular maintenance checks the integrity of grounding systems and plug sockets, ensures that they are safe to use and reduces the risk of shocks to anyone interacting with the electrical system. This is especially important in areas where individuals might use electrical devices near water or in high-traffic areas.
Electrical maintenance can also be a cost-saving measure. Proactive maintenance can save property owners from costly repairs by identifying and addressing minor issues before they turn into emergencies. For example, a small problem like a loose connection can escalate into significant damage or a total circuit failure if left unchecked, requiring more extensive repairs or even system replacements.
Regular maintenance keeps costs down by preventing these avoidable issues. Additionally, in commercial and industrial environments, unexpected equipment failure can lead to downtime which can interrupt business operations and incur revenue losses. Routine maintenance helps keep all electrical components functioning reliably and reduces the likelihood of unexpected failures. This is particularly beneficial for businesses where continuous power supply is critical, as well-maintained systems ensure fewer interruptions.
Many insurance providers require proof of regular electrical maintenance as part of their coverage criteria. If an electrical fault results in a fire or injury, insurers may deny claims if there is no record of proper maintenance, potentially leaving property owners with significant liabilities. Regular inspections and maintenance provide essential documentation that electrical systems are safe, ensure that insurance coverage remains valid and avoid issues with claim denials.
Electrical maintenance also ensures legal compliance. In the UK, laws like the Electricity at Work Regulations 1989 and the Health and Safety at Work etc. Act 1974 impose a legal obligation on business owners, landlords and property managers to provide a safe environment for employees, tenants and visitors. Regular electrical maintenance helps fulfil these obligations by ensuring that systems are inspected, safe and compliant with current regulations. Failing to meet these standards can result in legal repercussions, including fines or liability in the event of an accident.
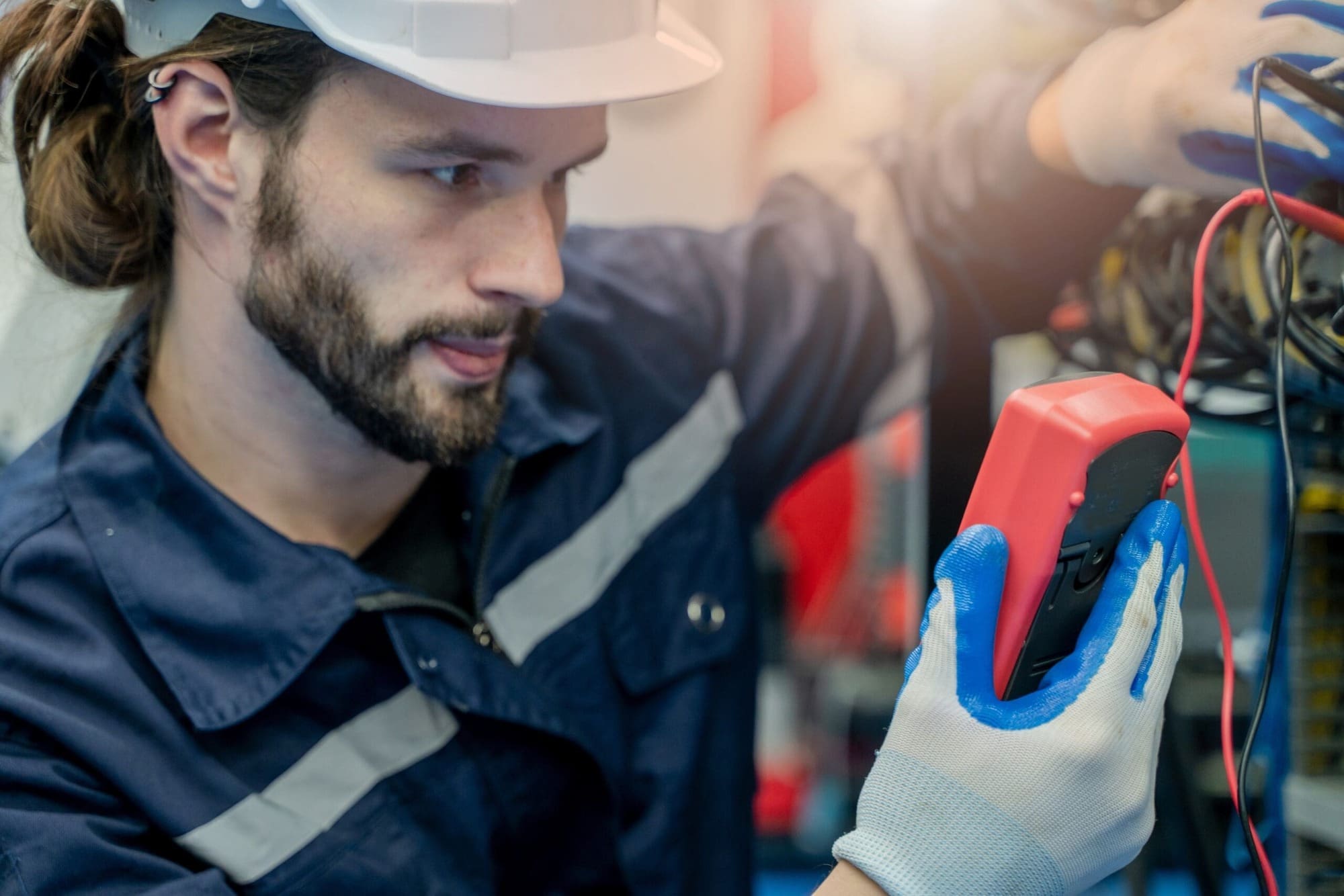
Frequency of Inspections and Maintenance
To maintain safety and efficiency, the frequency of electrical inspections and maintenance depends on the type of building, its usage and other influencing factors.
Residential Properties
- Homeowners: Electrical inspections are generally recommended every 10 years for owner-occupied homes.
- Rental properties: In England and Wales, landlords are required to arrange electrical inspections every 5 years or at the start of a new tenancy, as required by UK regulations for rental property safety.
Commercial Properties
For commercial buildings like offices, retail spaces and public facilities, an inspection is generally recommended every 5 years. However, specific requirements vary depending on the nature of business activities within the building.
Industrial Properties
Industrial properties, such as factories, warehouses and manufacturing facilities, typically require annual inspections due to higher energy demands, more complex equipment and an increased risk of wear and damage from heavy machinery.
Educational and Public Buildings
Facilities such as schools, hospitals and other public buildings generally require inspections every 3-5 years. Because these buildings often experience high traffic and diverse electrical demands, regular inspections are critical for maintaining safety. Many public buildings, such as hospitals and medical clinics, should also conduct routine checks between more detailed inspections.
Several factors may necessitate more frequent electrical inspections and maintenance, regardless of the building type. These can include:
Age of the building
Older buildings (typically those over 30 years old) tend to have ageing wiring and outdated electrical systems. If the electrical infrastructure hasn’t been upgraded, more frequent inspections are recommended to ensure these systems are safe and to identify any need for rewiring or replacement.
High energy usage
Properties with high energy demands, such as data centres, factories or commercial kitchens, often experience greater electrical stress. Frequent inspections help ensure these systems are not overloaded and remain safe under heavy use.
Environmental conditions
Properties located in areas prone to moisture, dust or corrosive environments, like coastal areas or industrial zones, require more frequent inspections. Moisture and dust can lead to corrosion or compromised wiring insulation, which increases fire and shock risks.
History of electrical issues
Buildings with a history of frequent electrical faults, such as tripping breakers, power surges or overloaded circuits, should be inspected more often. This is especially important in properties that have experienced electrical fires or equipment failures, as it may indicate underlying issues with the system.
Building modifications or new installations
Renovations, the addition of new electrical equipment or significant changes to electrical demands (such as switching to high-powered equipment) often necessitate an immediate inspection to ensure the system can handle the additional load safely.
Who Should Perform Electrical Inspections and Maintenance?
Electrical inspections and maintenance require a high level of expertise and knowledge of safety standards. In the UK, only licensed and certified electricians should perform electrical inspections and maintenance. Certified professionals are trained to meet rigorous safety standards which ensures the work complies with legal requirements and best practices. Qualified electricians are knowledgeable about complex systems, regulations and emerging safety protocols, making them essential for ensuring comprehensive and compliant inspections.
Certified professionals can identify subtle signs of wear, faulty wiring, overloaded circuits and other potential hazards that may not be obvious to untrained individuals. This skill is crucial for preventing fires, shocks and equipment failures. Additionally, licensed electricians have access to specialised tools like thermal imaging cameras, insulation testers and voltage meters that aid in accurately diagnosing and addressing issues.
Also, only licensed professionals can issue the necessary safety certifications, such as the Electrical Installation Condition Report (EICR), required for property rentals, insurance compliance and certain business types. Hiring a certified electrician ensures that the work not only meets safety standards but is also documented correctly for regulatory purposes.
Attempting electrical maintenance without proper qualifications can be extremely dangerous. DIY electrical work can lead to improper wiring, which increases the risk of electrical shocks, short circuits and fires. Furthermore, a lack of knowledge in handling high-voltage systems can result in serious injury or even fatal accidents.
Additionally, homeowners or property managers lack the specialised equipment and training required to accurately test and diagnose electrical systems. Standard household tools are not adequate for detecting deeper issues such as insulation breakdown, voltage irregularities or temperature variations in wiring that may indicate future problems. Professional tools and techniques provide the accuracy and depth needed to ensure long-term safety and efficiency.
Many insurance providers and regulatory bodies require proof of maintenance performed by certified electricians. DIY maintenance may not be recognised as legitimate, potentially voiding insurance coverage if an accident occurs. Additionally, for landlords and business owners, hiring an unqualified person for electrical work can result in legal liability in the event of an accident, as UK law requires electrical work to be conducted by certified individuals.
Given the potential risks, the benefits of professional inspections and the legal requirements involved, hiring a licensed and certified electrician is essential for maintaining a safe and compliant electrical system. It ensures thorough, accurate inspections and maintenance, minimises risks and provides peace of mind to property owners, tenants and users alike.
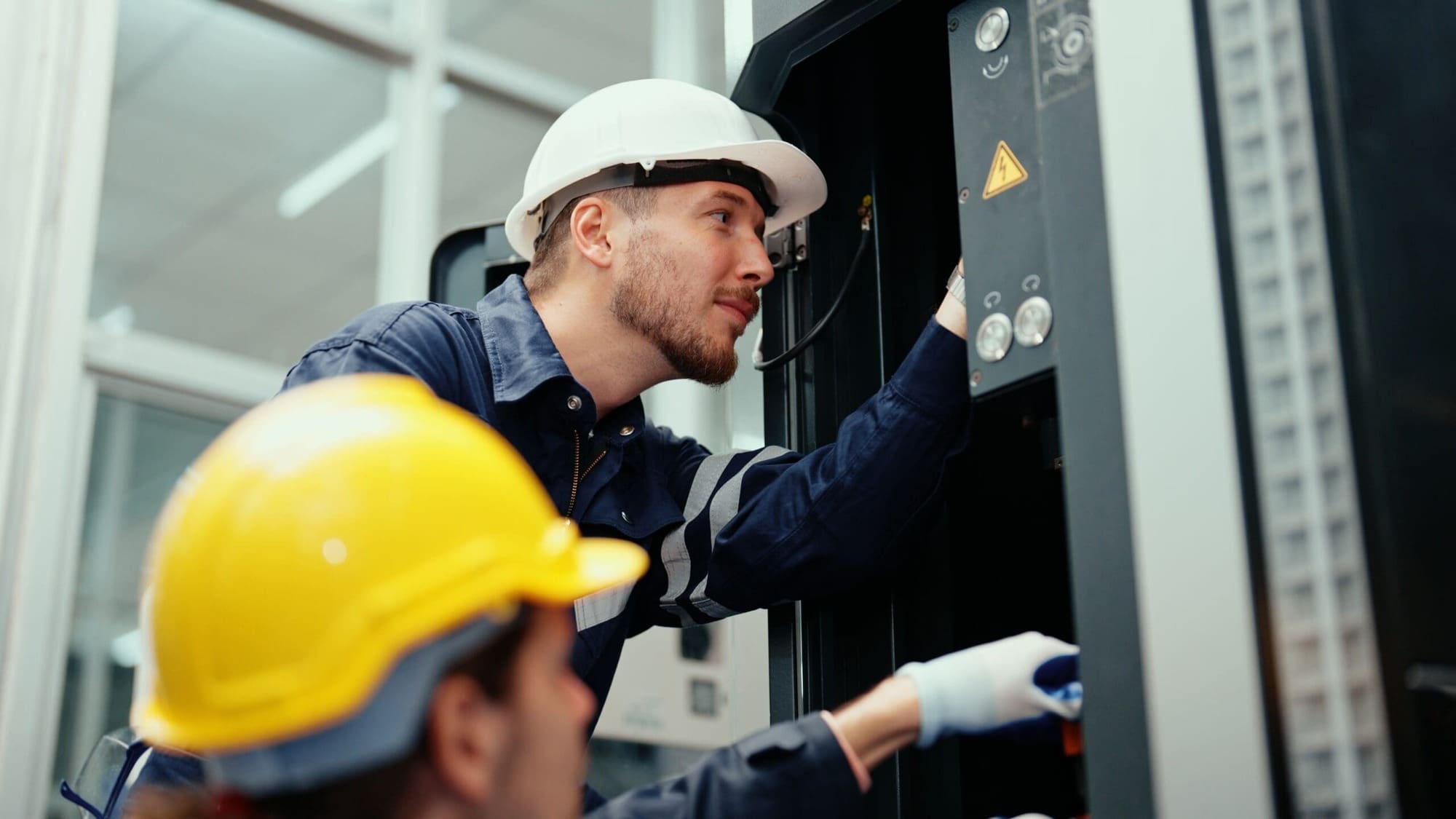
Case Studies and Examples
Real-life cases highlight the critical importance of regular electrical inspections and maintenance in preventing accidents and avoiding costly repairs. Below are three examples that showcase the consequences of proactive maintenance and the risks of neglecting electrical safety protocols:
Case Study 1: Proactive Maintenance Prevents a Major Incident
In a mid-sized commercial building used for office space, regular electrical inspections were conducted as part of the company’s maintenance plan. The building housed a large number of computers, servers and office equipment, putting high demands on its electrical system.
During a routine inspection, an electrician discovered that several outlets were showing signs of overheating and the insulation on some wiring near the circuit breakers had started to deteriorate. Using thermal imaging cameras, the inspector identified hot spots where cables were overloading due to excessive demand from outdated wiring and insufficient breakers. The electrician recommended the immediate replacement of outdated breakers and rerouting of circuits to balance the electrical load. They also installed additional surge protection to safeguard equipment from power surges.
By addressing these issues before any failures occurred, the building avoided what could have been a severe fire hazard or an equipment failure, saving the business from potential equipment replacement costs, data loss and significant disruption. Proactive maintenance also ensured that the company continued to meet regulatory safety standards, helped to protect employees and ensured a safe work environment.
Case Study 2: Electrical Fire in an Ageing Residential Building
In an older residential block of flats, routine electrical inspections were not prioritised due to budget constraints. Over the years, the wiring in the building had aged and the insulation was beginning to wear. Residents had reported occasional flickering lights and minor shocks from outlets, but no maintenance was scheduled.
One evening, faulty wiring caused a short circuit in the wall of one of the flats, sparking an electrical fire. The fire spread quickly, causing severe property damage to three flats and displacing residents. The property owner was held liable for not conducting regular inspections and was subject to fines and costly repairs, as well as higher insurance premiums in the future. The residents were left homeless for more than six months while repairs were made and had to be placed in temporary accommodation.
Case Study 3: Equipment Failure in a Manufacturing Facility
In a large manufacturing plant, regular electrical inspections were overlooked in favour of cost savings. The facility used multiple heavy-duty machines that placed significant demands on its electrical system. The company relied heavily on these machines to meet production deadlines, but with no maintenance the electrical system was not monitored for potential overload.
One of the machines overloaded a circuit due to unbalanced loads and outdated breakers, resulting in a breakdown. The equipment required extensive repairs and downtime and this caused production delays and financial losses. Furthermore, emergency repairs were costly and the company incurred additional losses due to missed production targets. Following this incident, the company had to invest heavily in rewiring and maintenance to prevent future occurrences. This highlights the cost-saving benefits of preventative maintenance.
Steps for Implementing an Electrical Maintenance Plan
Establishing an effective electrical maintenance plan involves systematic scheduling, thorough documentation and preparation for emergencies. The essential steps for implementing an electrical maintenance plan are listed below:
Scheduling inspection
It is essential to set a regular inspection schedule based on factors such as the type and age of the building, the building’s function (e.g. factory or residential) and the type and amount of electrical usage. When creating the schedule, consider seasonal timings, for example, by scheduling inspections during times when demand is lower, such as after business hours for commercial properties or during school holidays for educational institutions, as this minimises disruptions to normal operations. It can be beneficial to use digital tools (like calendar apps or project management software) or physical planners to document scheduled inspections. These should include:
- Dates of previous inspections.
- Upcoming inspection dates.
- Any recommended follow-up actions.
- Contact information for licensed electricians or inspection services.
Once the schedule has been created, it is essential that it is followed. If there are any electrical concerns and an inspection is not due, one should be performed anyway.
Documenting and Tracking
Keep a detailed log of all inspections, maintenance activities and repairs. This log should include:
- Date of inspection or maintenance.
- Name and qualifications of the professional conducting the work.
- Summary of findings and any issues identified.
- Recommended actions and follow-up dates.
- Dates when actions were completed and by whom.
Retain inspection logs and documentation for a minimum of 5 years or as required by local regulations. This documentation is crucial for proving compliance with safety standards and for insurance purposes. Consider using maintenance management software to streamline tracking and documentation. Many platforms allow for reminders, reporting and easy access to historical data, which is beneficial for compliance and audit purposes.
Emergency response plan
Prepare for potential electrical issues identified during inspections by creating an emergency response plan. This plan should outline:
- Immediate actions: Steps to take if a serious electrical problem is found during an inspection (e.g. shutting off power and evacuating personnel).
- Contact information: List of emergency contacts, including licensed electricians, local emergency services and safety personnel.
- Safety procedures: Specific protocols for employees or residents to follow in case of electrical hazards, such as fire or electric shock. This might include training on the proper use of fire extinguishers for electrical fires.
- Regular training: Conduct regular training sessions for employees or building occupants to familiarise them with the emergency response plan. Include practice drills for scenarios such as electrical fires or equipment failure to ensure that everyone knows how to respond effectively.
- Review and update the plan: Periodically review and update the emergency response plan to reflect any changes in building layout, electrical systems or personnel. It is also important to ensure that new staff are trained on emergency procedures.
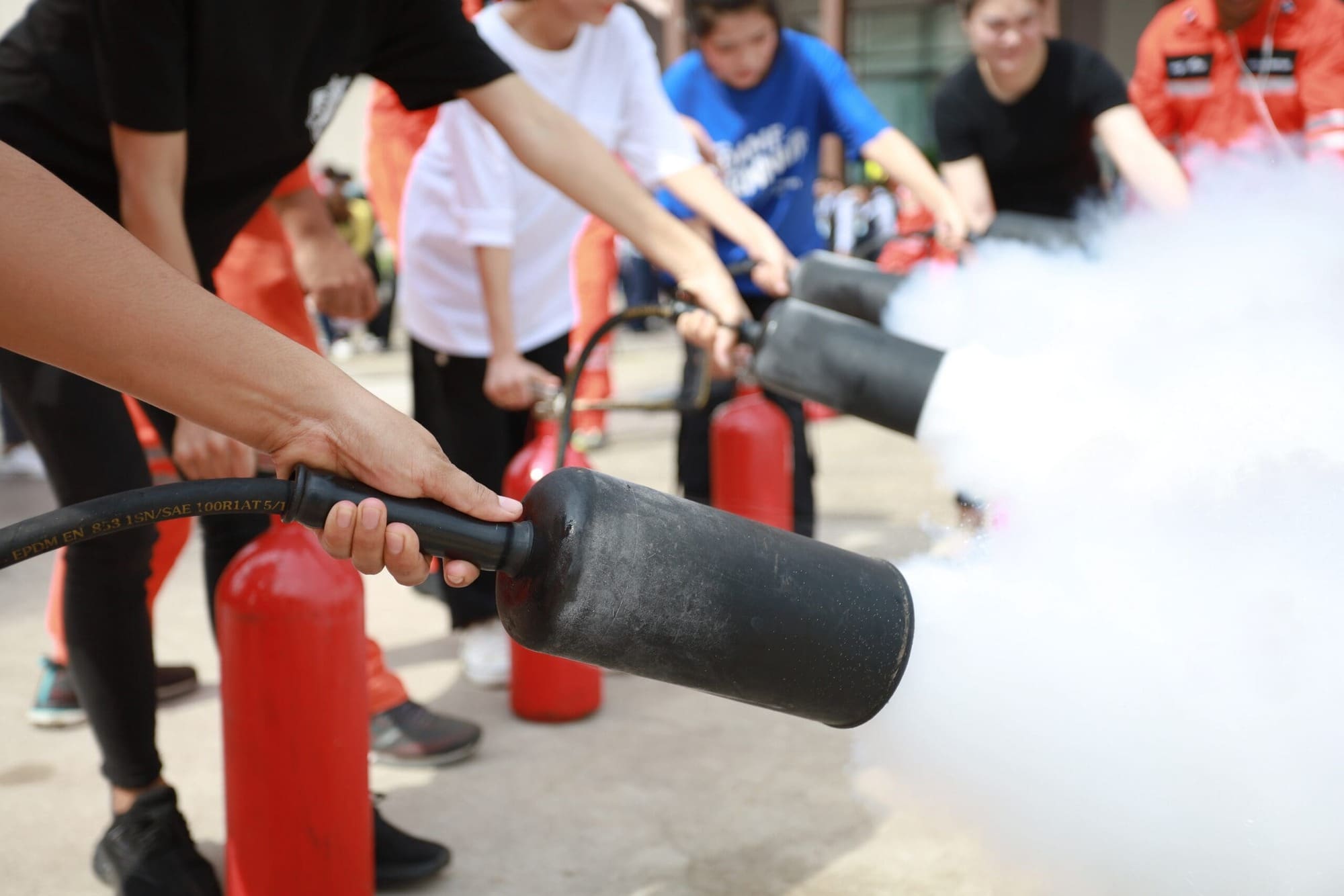
Conclusion
In summary, regular electrical inspections and maintenance are vital components of a comprehensive safety strategy for any property. They not only protect lives and property from the dangers of electrical hazards, such as fires, shocks and equipment failures, but also offer significant cost savings in the long run. By identifying and addressing potential issues before they escalate, property owners can extend the lifespan of their electrical systems and appliances, improve energy efficiency and ensure compliance with legal regulations and safety standards.
It is recommended that property owners schedule a comprehensive electrical inspection with a certified professional to ensure the safety and reliability of their electrical systems. Additionally, implement a regular maintenance routine to stay ahead of potential issues and promote a secure environment. Instead of waiting for an emergency to happen, prioritise electrical safety now for peace of mind and to protect your property and the health and safety of everyone involved.