In this article
Moving and handling can cause serious injuries to people. An estimated 581,000 workers were reported to have sustained an injury in the workplace during 2018/19 according to the Labour Force Survey – with industries such as agriculture, construction and wholesale coming out on top as the highest risk for workplace injuries. So, understanding the dangers of your workplace environment has never been so important – but, how in the know are you?
There is no getting away from the fact that moving and handling plays a part in almost every role, in every industry, making the risk of a workplace injury high if you’re not up to speed with the best practice techniques. But if you work in an industry that relies heavily on moving and handling, whether that be manually or using moving and handling equipment – the risks are much greater.
So, whether your role involves a lot of lifting and carrying, or you’re looking to improve your basic knowledge of health and safety in the workplace, you’ve come to the right place. Today we’re looking at some of the most common workplace injuries, how they occur – and what you can do to prevent injuries and reduce risks in the workplace.
What is a workplace injury?
A workplace injury can cover a number of things, including physical injury or illness and is a direct result of the work environment. This can be an injury or illness caused, contributed or significantly aggravated by events or exposures in the workplace environment.
Whilst some industries pose a higher risk than others, it is possible to sustain a workplace injury in any occupational role.
What are the most common types of workplace injury and how do they occur?
There are a wide variety of illnesses and injuries that can come as a result of the work environment, and these may differ vastly from one industry to another. However, a 2018/19 RIDDOR report showed that 20% of all non-fatal workplace injuries came as a result of handling, lifting and carrying, making this the second highest cause of work injuries after slips, trips and falls (accounting for 29% of injuries). With this in mind, let’s take a closer look at three of the most common injuries caused as a result of moving and handling.
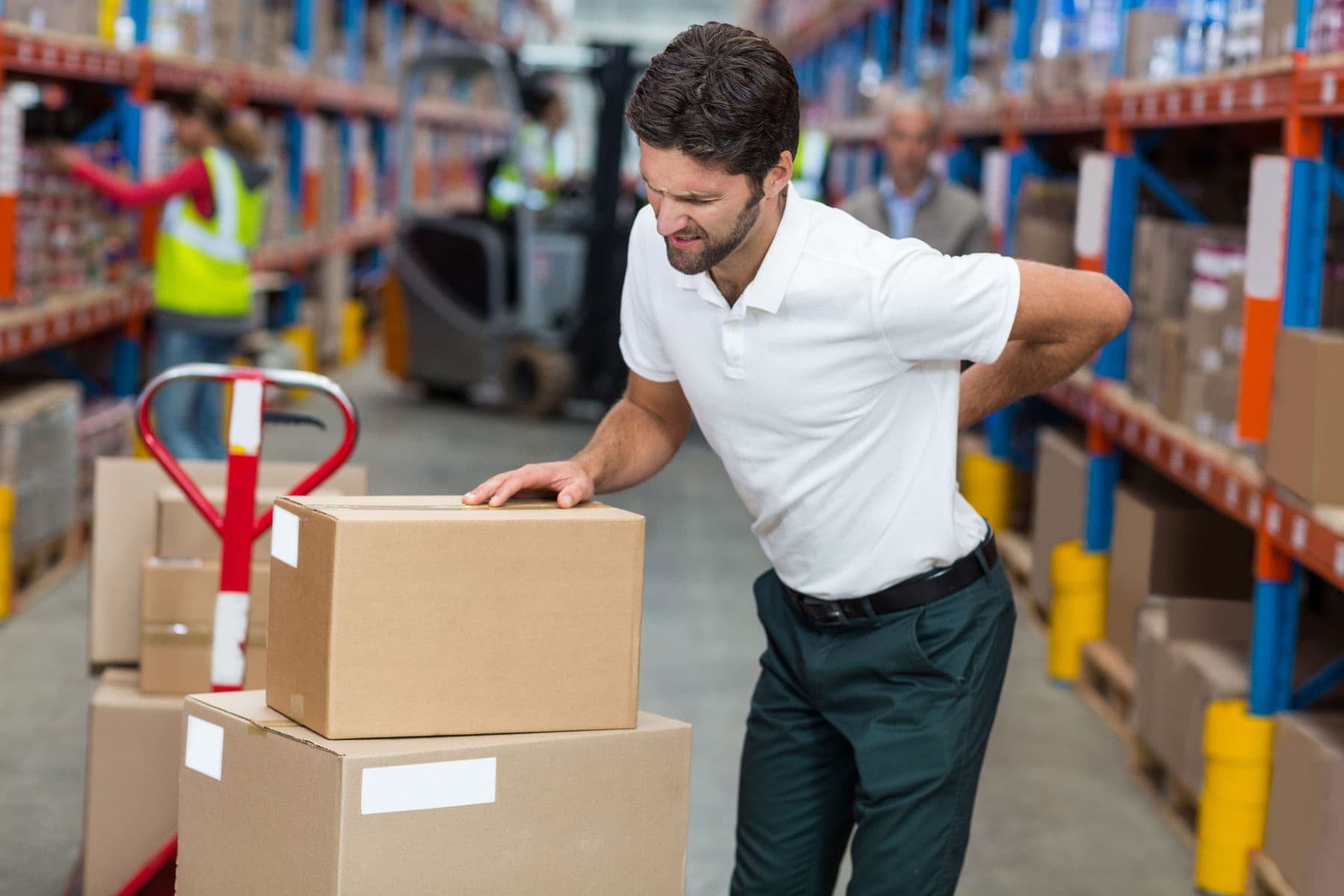
Musculoskeletal disorders
Musculoskeletal disorders are by far the most common injuries to occur as a result of the workplace and are mostly associated with the construction industry where manual handling is part of everyday life.
Musculoskeletal disorders can encompass a range of injuries, and can include muscles, joints and tendons in any part of the body. This type of injury is most often associated with long-term damage, and often has a huge impact on not only the work life, but also the personal life of the sufferer.
According to the Health and Safety Executive, there were 498,000 workers suffering from work-related musculoskeletal disorders (either new or long-standing) in 2018/19, with 203,000 of these suffering with upper limb or neck injuries, 40% suffering from back problems and 19% with lower limb injuries.
How do musculoskeletal injuries occur?
Unlike more superficial and short-term workplace injuries, musculoskeletal disorders usually occur as a result of repetitive movements over a long period of time. It doesn’t always necessarily occur as a result of heavy trauma either, as the HSE state that manual handling, lifting and repetitive keyboard typing are the prime causative factors behind work-related musculoskeletal disorders.
Musculoskeletal disorders can occur from gradual wear and tear, repetitive movements or sudden movements, including some of the following:
- Twisting.
- Awkward movements that occur regularly over a long period of time.
- Lifting heavy items regularly.
- Lifting an item that is too heavy.
- Bending down regularly.
- Sitting or standing with bad posture.
- Stretching to reach high areas.
- Working in a cramped environment.
- Working on unstable or uneven flooring.
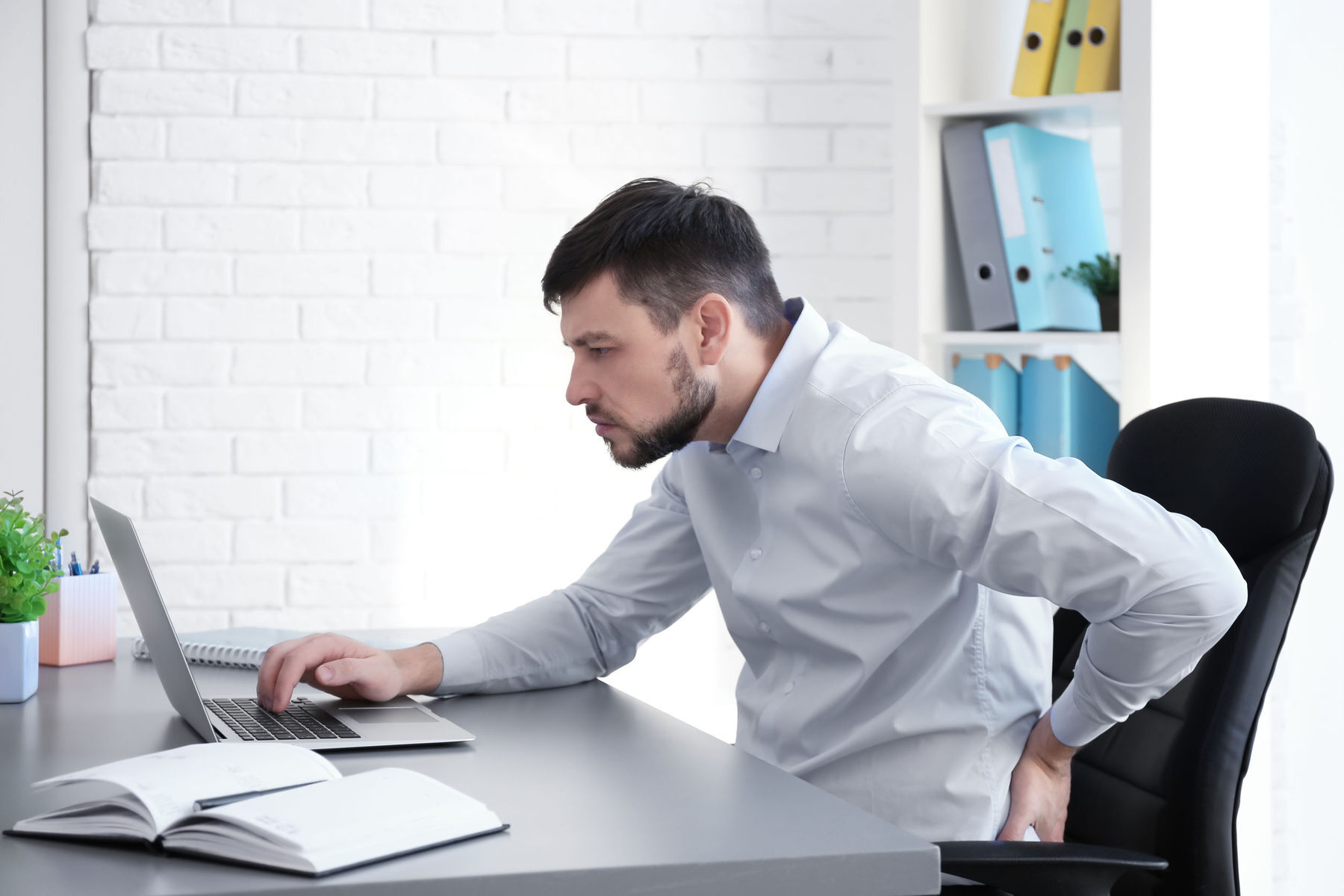
What are the symptoms of a musculoskeletal disorder?
There are a number of symptoms that come as a result of a musculoskeletal disorder which can be incredibly debilitating – including:
- Pain in the affected area.
- Minimal mobility or range of movement.
- Widespread pain.
- Dull aches.
- Swelling.
- Tightness in muscles.
- Stiffness.
- Numbness or tingling.
- Disturbed sleep.
- Burning muscles.
- Muscle spasms.
- Muscle fatigue.
Superficial injuries
Superficial or short-term injuries encompass a wide range of things, including cuts and lacerations, sprains, tears, small fractures and muscle strains. Superficial injuries are amongst the most common type of work place injury, and if you work in a high-risk environment, the chances are you’re even more exposed to these potential injuries.
How do superficial injuries occur?
Short-term and/or superficial injuries can be caused by a range of things, and are most commonly associated with sudden, unexpected movements. Here are some of the most common causes of superficial injuries:
- Dropping a load.
- Suddenly losing grip of a load.
- Lifting excessive amounts of weight.
- Falling whilst carrying a load.
- Tripping whilst carrying a load.
- Awkward movements whilst lift or carrying.
- Unsafe or incorrect use of a handling equipment.
What are the symptoms of a superficial injury?
The symptoms of short-term or superficial injuries really depends on the type of injury sustained. However, below are some of the most common types of symptoms relating to superficial injuries through manual handling:
- Sudden onset pain.
- Cuts.
- Bruises.
- Lesions.
- Swelling.
- Limited mobility.
- Loss of consciousness.
Mental health issues
Often overlooked, mental health issues are common in those who have sustained long-term injuries in the workplace. Although physical injuries are more readily addressed, a large proportion of those who sustain an injury at work find it difficult to cope with the treatment, long-term side effects and overall impact it can have on their personal lives.
According to the Health and Safety Executive, approximately 6.6 million working days were lost in 2018/19 as a result of work related musculoskeletal disorder. This alone would have a serious impact on finances and home life, causing further strain and potentially leading to an increase in mental health issues.
Who is at risk of sustaining an injury from incorrect moving and handling?
If you partake in any kind of moving and handling, then there is a chance that you could sustain a workplace injury. Whether you’re a manager or an employee, it is important to follow moving and handling best practice techniques in order to reduce the risk of injuries occurring.
What factors increase the risk of workplace moving and handling injuries occurring?
Risks of moving and handling injuries occurring are naturally higher in certain industries such as construction and agriculture where there are more potential risk factors at play. However, in many cases there are preventative factors that may contribute to the risk of accidents happening that we can be aware of, and in many cases that we can rectify before injuries are sustained.
There are a number of things to be considered when it comes to the risk of injury during moving and handling tasks, including not only environmental factors, but also relating to the individual and the resources made available. Let’s take a look at some of these in more detail:
Environmental factors
- Lack of appropriate space to carry out the task at hand can lead to injury through maintaining inappropriate and awkward body posture.
- The environment may not be properly maintained for safe working i.e. it may be cluttered with multiple obstructions in place
- The environment may be too warm or too cold, impacting the effectiveness of the work carried out i.e. making it hard to grip tools, making the worker lethargic and tired
- Improper lighting can have a direct impact on safety in the work place, particularly when moving and handling goods. A dark environment could lead to trips or falls over obstacles, or lead to repeatedly bad posture if the worker is straining to see what they are doing
Resources
- If a role requires a lot of heavy lifting and carrying, but workers are not supplied with efficient working equipment to carry out the task, it can quickly lead to injuries occurring through trying to tackle the loads manually.
- Equipment that hasn’t been routinely maintained could pose a risk to the user, especially if there are faults which have previously gone undetected or ignored.
- Lack of policy enforcement in place could mean that workers feel isolated and unsure how to approach management about potential workplace risks.
Individual
- Lack of experience in the industry can quickly lead to an increase in risk as the worker may not know best practice moving and handling techniques, or how to effectively make use of equipment.
- Insufficient training, whether that be in the industry, the role or in the necessary moving and handling equipment can lead to a higher risk of injury as the worker is underqualified to safely carry out the tasks.
- Physical health also can contribute to the level of risk in the workplace. There may be a history of back injuries for example, where manual roles could quickly irritate conditions leading them to flare up and potentially heightening the risk of injury in work.
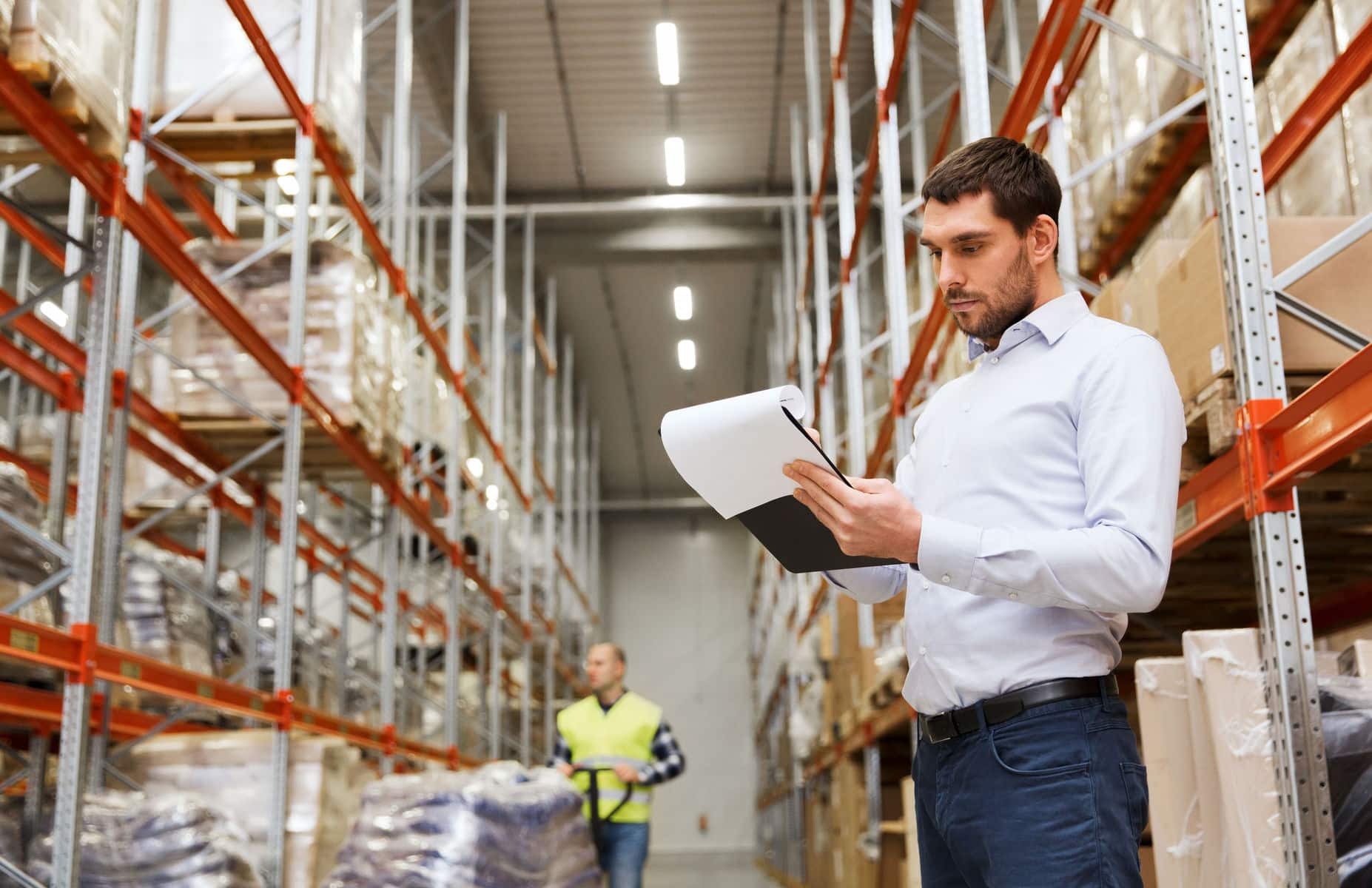
Ways to prevent risks occurring in the workplace
As with any physically demanding role, completely removing all risk may not be possible – but, there are things that can be done to drastically reduce the risk of injury occurring.
According to the Health and Safety Executive, a huge part of controlling risk in the workplace is through conducting routine risk assessments. This means the following are carried out:
- Hazards are identified.
- Those at risk are identified.
- The level of risk is assessed, and precautions are put in place.
- Significant findings are recorded.
- The risk assessment is reviewed and updated routinely.
When it comes to safe manual handling activities, it is generally expected that every employee carries out regular risk assessments as and when things change in the workplace. Through this regular maintenance, and ownership on all workers to take responsibility, the chances of injuries occurring through manual handling are significantly reduced.
Posture
Poor or incorrect posture is up there as one of the main causes of injury during moving and handling. This is usually just as common in workers who have been in the job for many years and have become complacent as it is with new employees who are unfamiliar with best practice techniques.
Ensuring your posture is correct at all times can protect you from unnecessary injury significantly. This includes ensuring you lift, push, pull and carry goods the appropriate way to avoid strain or tension on your neck and back. If you are unfamiliar with the best techniques to use, you should consult your management who are legally obligated to ensure training is provided under the Health and Safety at Work Act 1974.
Alternatively, you can improve your skills and knowledge whilst on the job with one of our online courses, such as the manual handling programme designed to leave you with all the information you need to carry out your role safely and efficiently
Personal Protective Equipment (PPE)
We have discussed the importance of using appropriate PPE in the workplace before, but having appropriate clothing and workwear can make a huge difference when it comes to preventing the risk of injury during moving and handling.
Employers are obligated under the Health and Safety at Work Act to provide appropriate workwear to employees so that they are able to safely carry out the tasks at hand. So, if you’re workwear is old and damaged, or you feel there are pieces you could benefit from, speak with your management.
Test your knowledge on moving and handling safety knowledge
Wherever you are in your career, it is important to continue your personal development, which means staying on top of the newest techniques and best practice ways to stay safe during moving and handling tasks.
Why not take our moving and handling quiz to see how savvy you are? Or check out our affordable online courses in health and safety to see where you could improve.