In this Food Safety Guide for Butcher’s Shops
Meeting Food Hygiene Regulation in Butcher’s Shops
A couple of decades ago, every high street usually had an independent butcher. It won’t be a surprise to many that over the past 25 years, the number of independent butchers has reduced dramatically, by around 60%. According to the Agriculture and Horticulture Development Board (AHDB), the past few years have been more stable as consumers have an increased willingness to shop based on other factors as opposed to simply convenience and price.
The AHDB state that those who shop for red meat are more prepared now to invest time in shopping for their meat and want to become more informed about it. Quality is the top consideration followed closely by ethical production and origin. While 30% say that they try to buy local produce, such as from farm shops or farmers’ markets, 61% say they would be happy to pay more for meat of better quality.
Many independent butchers can deliver this, but they are always in competition with the big supermarket chains where convenience and reduced cost often tick the boxes for consumers. Supermarkets often have strict hygiene protocols that are a focus from the top down – so where does this leave your independent high street butcher?
This Food Safety and Hygiene Guide for Butcher’s Shops will provide guidance and advice on how to achieve the highest food safety and hygiene standards in both an independent butcher’s shop as well as a butcher’s counter in a larger store. Having stringent food safety practices in a butcher’s is essential when it comes to running a successful shop.
Food Safety and Hygiene Legislation to Follow for Butcher’s Shops
All food businesses in the UK, including butchers, must follow the food safety and hygiene legislation to ensure that their customers are safe when eating meat products. There are several enforceable laws in the UK to protect consumers.
- The Food Safety Act 1990 – This Act provides a framework for all food and drink businesses to follow. The Act ensures that butchers and other businesses do not put anything in food, remove anything from food, or treat food in ways that would mean it could be damaging to the health of those eating it. It also ensures that butchers sell food that is of the substance, nature and quality that customers should expect and that food is labelled, presented and advertised in a way that is not misleading or false.
- The Food Standards Act 1999 – This Act establishes the Food Standards Agency (FSA) as the body that oversees UK food safety laws and legislation. Its main goal is to protect public health when it comes to food and gives the FSA the power to act in the consumers’ best interests during all stages of food production, processing and supply.
- The Food Safety and Hygiene Regulations:
- The Food Safety and Hygiene (England) Regulations 2013
- The Food Hygiene Regulations (Scotland) 2006
- The Food Hygiene Regulations (Wales) 2006
- The Food Hygiene Regulations (Northern Ireland) 2006
- The Food Information Regulations 2014
- These regulations stipulate that businesses must provide allergen information if a food contains any of the 14 listed allergens.
- These were amended by the Food Information (Amendment) (England) Regulations 2019 to include Natasha’s Law.
Natasha’s Law
Natasha’s Law became official legislation in October 2021. This law is a legacy left in the wake of the death of Natasha Ednan-Laperouse, a young woman who died after suffering from an allergic reaction to a baguette she bought from Pret a Manger at Heathrow Airport.
Before Natasha’s Law was enforced, food establishments like butcher’s shops did not need to label any foods that were pre-packaged on the premises ready for sale. Such foods are commonly referred to as PPDS. Often, this type of food is not served in fish and chip shops as they tend to serve food that’s either raw and packaged upon request and purchase or made fresh for the customer.
However, it is still important legislation that butchers must be aware of, especially if they package up some of their foods for sale such as packs of sausages, pre-packaged chops or slices of bacon. Moreover, many butcher’s shops these days are diversifying by selling other goods such as pies, sandwiches and baked goods. If these goods are packaged before a customer requests them, they must also be labelled according to Natasha’s Law.
The labelling of these foods would need to include:
- Any of the 14 allergens that are required by law listed and emphasised on the packaging.
- The name of the food item.
- What ingredients it contains.
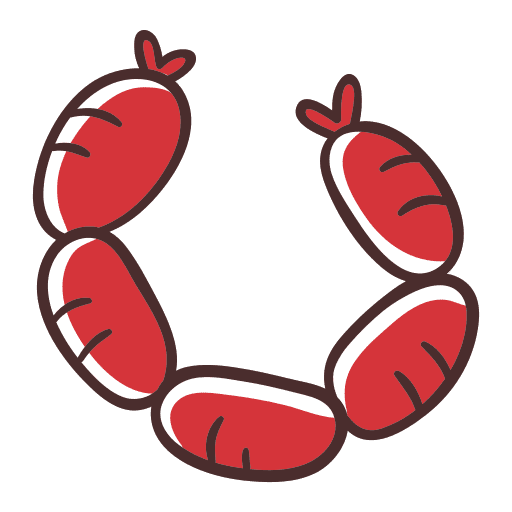
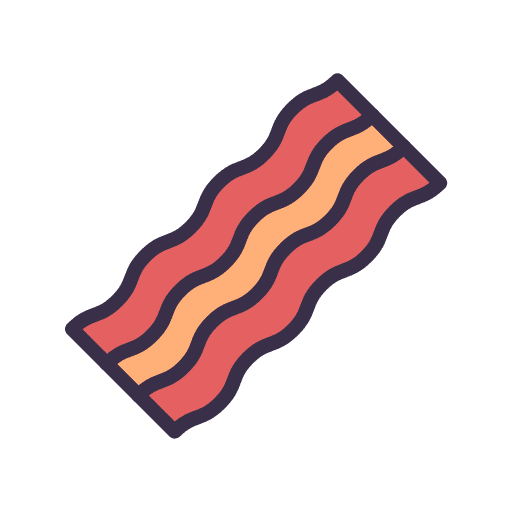
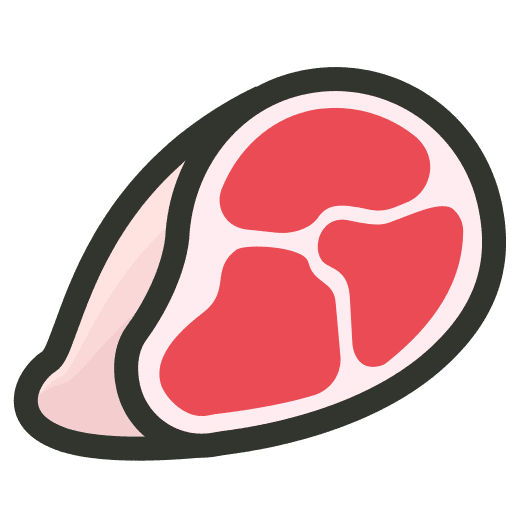
Other Regulations for Butcher’s Shops
In addition to the regulations and laws above, there is other legislation that is also applicable specifically to butchers and butcher’s shops. Whilst not always directly related to food safety and hygiene, butchers must also be aware of this legislation to avoid cross-contamination or incorrect labelling of products.
This includes:
Organic Produce
Organic produce must meet the requirements before it can legally be labelled as ‘organic’. To be labelled as such, it must be certified by an approved UK organic control body. This includes food that is prepared, imported, exported, stored or sold at the butcher’s shop. The requirements are:
- It must meet organic production rules.
- It must have at least 95% organic agricultural ingredients.
- All other ingredients, additives or processing aids must be listed as permitted within the organic regulations.
- The product, its labels and any suppliers must be certified by an approved body.
- Terms such as ‘organically grown’, ‘organically produced’ and ‘grown or produced using organic principles/methods’ must be used carefully. This also applies to business names. Butcher’s shops cannot use names such as ‘Andy’s Organic Butchery’ if non-organic products are also sold.
Meat Products
Of course, by their very nature, butchers tend to sell meat products. There are extensive laws regarding this. Meat products must comply with laws regarding their content and preparation:
- There is a maximum allowed total fat content for different meats. For mammals (other than rabbits and pigs) or mixtures of species where the majority is a mammal, there must be no more than 25% fat content. The collagen-to-meat ratio must also not exceed 25%. For pigs, the fat content and collagen-to-meat protein ratio must not exceed 30% and 25% respectively. For birds and rabbits, these figures are 15% and 10% respectively.
- Meat labelled as ‘fresh meat’ must not have had any preserving other than chilling or freezing. This includes vacuum-packed meat or meat packed in controlled atmospheres.
- Meat preparations are considered a food that has been made from fresh meat where the structure of the muscle fibre that makes up the meat has not been changed but other foods have been added. These could include seasonings and additives.
- Farm shops are not allowed to sell products that contain the following meat if the product is uncooked at sale:
- Feet
- Intestine (except as sausage skin)
- Lungs
- Oesophagus
- Rectum
- Spinal cord
- Spleen
- Stomach
- Udder.
- All meat products must be labelled if they contain added water if it makes up more than 5% of the product’s weight. This only applies if the meat looks like a cut, slice, portion, joint or carcase. It doesn’t apply to sausages. The name of the food must state that it has added water such as ‘chicken with added water’.
- Formed foods must be labelled as such. This applies if the product looks like it is one whole piece of meat when it is actually made up of more than one, such as a chicken breast or a slice of pork. It must have ‘formed meat’ next to its name.
- Added proteins must have the information on the label within the name of the food such as ‘pork escalopes with chicken egg protein’. This applies to proteins such as:
- Albumin
- Collagen
- Casein
- Milk protien
- Egg protien
- Minced meats must also meet certain standards:
- Lean means it contains less than 7% fat.
- Pure beef means it contains less than 20% fat.
- Minced meat containing pork must be less than 30% fat.
- Other minced meats must have less than 25% fat.
- It can be outside of these criteria if it is labelled ‘For UK market only’ followed by the national mark, which is a printed square.
- Frozen meat must show its date of freezing or first freezing.
- Certain products must have a minimum percentage of meat if they use one of the following names:
Sausage, chipolata, sausage meat, link.- Pastie/pasty.
- Sausage roll.
- Hamburger.
- Chopped.
- Luncheon.
- Pie.
- Game pie.
- Pudding.
- Scotch or Scottish pie.
- Bridie.
In addition to the above, there are specific requirements under the Food Hygiene Act on butchery. For example, butchers should have separate storage facilities for the storage of packaged and exposed meat. Cutting rooms should be equipped to ensure compliance with Annex III, Section I, Chapter V. This means that work on meat should be organised to prevent or minimise contamination.
In particular:
- Meat that is meant for cutting should be brought into the workroom as needed.
- During the cutting, boning, slicing, dicing and packing process, the meat must be maintained at no more than 3°C for offal and 7°C for other red meat. For white meat, this temperature is 4°C. This means the ambient temperature should be no more than 12°C.
- If the premises are approved for cutting different species of meat, there should be adequate precautions in place to avoid cross-contamination of different species by separating the operations by either time or in different spaces.
- Hand basins should have taps that are designed to prevent contamination for all staff who handle exposed meat.
- Hot water sterilisers should operate at a minimum temperature of 82°C.
What Happens if the Legislation is not Followed?
If a butcher does not follow the law when it comes to food safety and hygiene, there can be disastrous consequences. These can be life-threatening for those who consume unsafe products as well as damaging for businesses. One example of what happens when strict food safety laws aren’t met is the case of Bowring Butchers, owned by Robert Bowring. The former butcher was prosecuted after a listeria outbreak in the local area was linked to his butcher’s shop in Mansfield Woodhouse, Nottinghamshire. Mr Bowring was fined £25,000 and was also banned from operating any food-related businesses in the future. He also had to pay £40,000 in costs.
The investigation was launched by Mansfield District Council in April 2019 when Public Health England connected two cases of listeriosis to Bowring Butchers. The inspection at the high street butcher’s shop found listeria on equipment used in food production and in cooked meat products. The inspectors also found significant issues with use-by dates remaining unrecorded and dirty equipment in use as well as problems with cross-contamination. The shop was closed immediately before re-opening a month later after a deep cleaning process and new measures were put in place.
The local authority’s barrister spoke of the many failings of Robert Bowring to put in place issues highlighted on his premises’ previous food hygiene inspections. The risk of cross-contamination between cooked and raw meat was obvious and, what is more, there also appeared to be a deliberate attempt at concealing the failures and misleading the general public too.
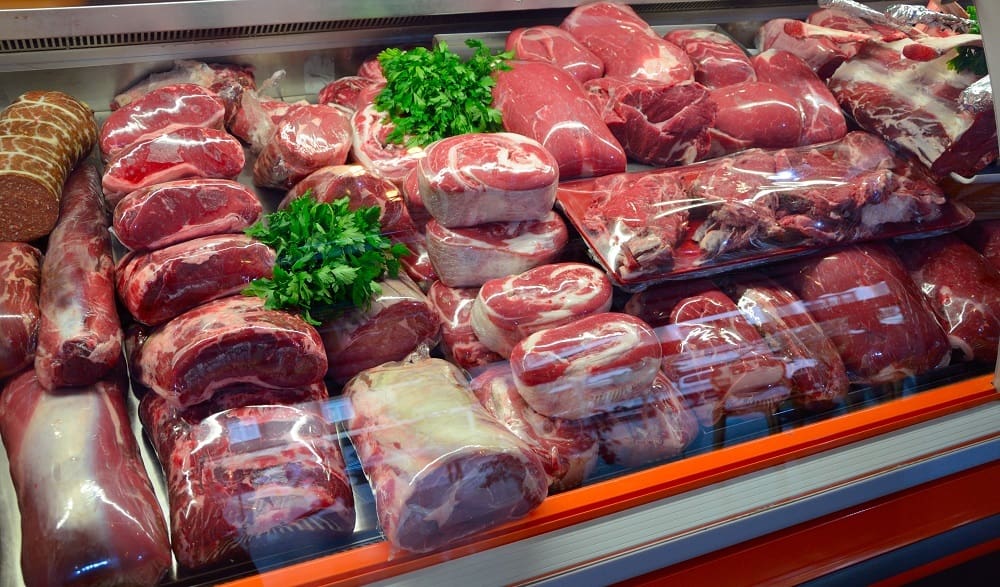
Staff Training on Food Hygiene for Butcher’s Shops
Staff training on food hygiene in butcher’s shops is a legal requirement. By law, all butchers and butcher’s shops must make sure that those who prepare, handle and sell food are trained and supervised in food hygiene. This does not mean that every worker in a butchery or butcher’s shop must have their own food hygiene certificate, however. But having food safety training and certification is the best way to show Environmental Health Officers (EHOs) as well as the shop’s customers that it is taking food safety and hygiene seriously. It also provides evidence of due diligence should there be an investigation for a breach in food safety legislation further down the line.
Butcher’s shop staff should have food hygiene training that is appropriate for their tasks, the area in which they work and relevant to their level of responsibility.
It should include training on:
- Personal hygiene – Staff should have training on the importance of handwashing, not working when ill and covering cuts and wounds.
- Storing ingredients, meat products, cooked goods etc. – Staff should have training on how to store ingredients correctly including separating raw and cooked ingredients, and temperature control.
- Preparing meat products and baked goods – Staff should be trained appropriately on how to avoid cross-contamination, handling raw meat, cooking and baking goods thoroughly if required, and ensuring that food is not left out at room temperature for too long. Training should include specifics for butchery including the temperatures required for preparing the different kinds of meat and avoiding preparing different meats at the same time.
- Cleaning and sanitising preparation areas, display areas and serving areas – Butcher’s staff should be trained on how to clean areas properly including how to clean different surfaces and equipment, and how to use cleaning products and cloths safely.
- Managing food safety – Butcher’s shop staff should know the principles of hazard analysis and critical control points (HACCP) – a systematic approach to identifying any hazards and controlling potential hazards in producing baked goods.
There are different levels of food safety and hygiene certification:
Level 1
Level 1 is an introduction to food hygiene practices. This training is typically for those who handle low-risk foods such as foods that are already in packaging or already pre-prepared on-site. This level of certification is useful for those working on tills selling pre-packaged meat and other products.
Level 2
Level 2 is a basic food hygiene certificate. This is a good choice of certification for staff who prepare and handle meat products and/or baked goods. Most butcher’s shop workers will need Level 2 certification, particularly those who work in the butchery environment or who package up meat products.
Level 3
Level 3 is classed as an intermediate food hygiene certificate. This is for those who have significant responsibilities within the butcher’s shop such as the owner, manager and supervisors as well as those involved in food safety management and HACCP systems.
Whilst this initial training is important, butcher’s staff should also ensure that they refresh their food safety and hygiene training every couple of years or so, especially if there have been any changes to the legislation, as with Natasha’s Law.
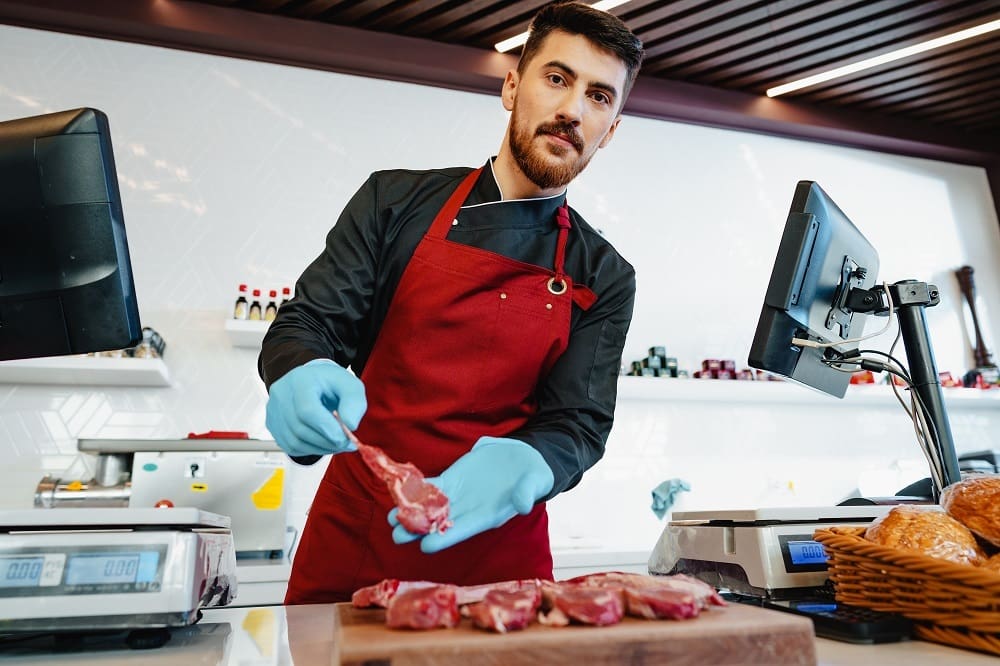
Food Hazards in a Butcher’s Shops
For most people, food hazards are something that we are naturally aware of in our day-to-day lives. However, the level of awareness of food hazards needed is different when you are working in a butcher’s shop. Given that they’re handling raw meat, butchers must have enhanced awareness of all hazards that may pose a risk to consumers. Raw meat often poses a greater risk by its very nature.
The FSA describes a food hazard as “something that could make food unsafe or unfit to eat”. The hazards can either be biological, chemical, physical or allergenic.
Biological
Biological food hazards are microorganisms or other living organisms. Some microorganisms can cause disease or illness in humans if they are consumed through contaminated food. The most common biological hazards in food include bacteria, viruses, parasites and fungi.
- Bacteria – Certain bacteria, such as salmonella, campylobacter, Escherichia coli (E. coli) and Listeria monocytogenes can cause food poisoning when they are present in contaminated food. This occurs when meat is not handled, stored or cooked properly. Listeria monocytogenes is a bacterium that can cause a serious foodborne illness called listeriosis, as was the case with the prosecution of Bowring Butchers mentioned above. It can contaminate meat during various stages of production including slaughter, processing, packaging and storage. It can also survive and even grow during refrigeration, making it a huge concern in the meat industry. Listeria poses a higher risk for certain groups of people including pregnant women, the elderly, newborns and those with weakened immune systems.
- Viruses – Viruses such as norovirus and hepatitis A can be spread through contaminated food including meat products and cause gastrointestinal illness. Bacterial contamination is generally more common, however.
- Parasites – Parasites in butchery, particularly in meat products are relatively uncommon in developed countries like the UK due to stringent regulations and control measures. However, it is still important to be aware of the potential risks and take the necessary precautions. Parasites like Trichinella spiralis (found in pork), Toxoplasma gondii and Taenia saginata (found in beef) can infect meat if animals were not properly raised, handled or inspected. However, it’s worth noting that the occurrence of these parasites in UK-produced meat is generally low due to effective farming practices and rigorous inspection systems.
- Fungi – Mould growth can occur on meat if it is not stored in appropriate conditions, leading to potential fungal contamination and the production of mycotoxins. Mycotoxins are toxic compounds produced by mould. Some common mycotoxins associated with food contamination include aflatoxins, ochratoxin A., fumonisins and zearalenone.
- Prions – Aside from the above, another potential biological hazard that is now extremely rare is prions. Prions are abnormal proteins that can cause severe neurodegenerative diseases, such as variant Creutzfeldt-Jakob disease (vCJD) in humans. Whilst the risk of prion contamination in butcher’s shops is extremely low, it is a concern when dealing with specific tissues like the brain and spinal cord of certain animals, such as cattle infected with bovine spongiform encephalopathy (BSE or ‘mad cow disease’). Strict regulations and practices are in place to prevent the spread of prion diseases. BSE was a significant issue in the UK in the 1980s and 1990s. Consuming BSE-infected meat was linked to the development of vCJD. Several strict control measures were put in place to protect public health as a result, and this includes removing high-risk meat products such as the brain, spinal cord and certain offal from the human food chain. As such, the occurrence of cases of BSE and vCJD is now extremely rare. However, it is still crucial to follow food safety guidelines, especially regarding the handling and consumption of specific tissues such as the brain and spinal cord.
Chemical
Chemical food hazards refer to harmful substances that can contaminate food and cause illness or disease when consumed. Chemical food hazard substances can occur naturally in the environment or be added to food either purposefully or accidentally. In a butcher’s shop, chemical hazards primarily arise from cleaning agents, pesticides, food additives and accidental contamination.
Some chemical hazards that pose a risk to foods from a butcher’s shop include:
- Cleaning agents – Butcher’s shops often use various cleaning products to maintain a clean and hygienic environment. Whilst necessary, these chemicals can lead to contamination of food surfaces and equipment when handled incorrectly. It is important to follow the manufacturer’s recommendations, dilute any chemicals correctly, and ensure thorough rinsing to prevent chemical residues on food contact surfaces.
- Pesticides – Pesticides are commonly used in agriculture to control pests and diseases in crops. If fruits and vegetables are stored and handled in a butcher’s shop, there is a possibility of pesticide residues. Proper sourcing and regular washing of produce can minimise this risk.
- Food additives – Certain food additives, such as artificial sweeteners, colours, preservatives and flavourings can cause adverse reactions in some people, particularly if they are used more than what is considered safe. In a butcher’s shop environment, there are added risks that include medicines and feed additives that are fed to livestock before slaughter. Butchers must follow legal requirements and usage guidelines when it comes to food additives to prevent excessive or unsafe levels in the final products.
- Contaminants from packaging – Chemicals from packaging materials such as plasticisers and bisphenol A (BPA) can migrate into foods and cause health problems.
Physical
Physical food hazards refer to foreign objects or materials that may contaminate food during the production process either accidentally or intentionally. These hazards can cause harm to customers such as choking, cuts, and causing damage to teeth.
Physical hazards include:
- Bone fragments – Meat products are prone to this physical hazard if they are not properly removed during processing. This is particularly relevant when processing meats that involve deboning.
- Glass or metal fragments – These can make their way into food during the production process such as if a glass jar or metal equipment is broken. Butcher’s shop owners should inspect machinery and utensils regularly for wear and tear. Regular maintenance should be carried out and any damaged items should be replaced.
- Stones, dirt and dust – These hazards can occur if food is not properly washed before preparing it or not properly sorted. Vegetables and salads are common places where these hazards occur. There may also be dust from animals, plants and poultry.
- Plastic or rubber materials – These hazards can be introduced during food packaging or equipment used during processing or handling. Plastic wrap or plastic ties are common in butcher’s shops and can pose a risk if accidentally left in or on the meat products.
- Wood splinters – Wooden surfaces or equipment that is damaged such as cutting boards may produce splinters that pose a physical hazard if they end up in meat products.
- Jewellery, hair or nails – If employees do not follow good food safety practices including good self-hygiene, hairnets, properly fitting clothing and removing jewellery before preparing food on a farm, these items can find themselves in the food being prepared.
Allergenic
Allergenic hazards in food are those which can cause an allergic reaction in people with food allergies. Allergens are typically proteins that are found in certain foods, and when someone with an allergy consumes them, their immune system reacts by releasing histamines and other chemicals that can cause mild to severe symptoms, including anaphylaxis which can ultimately lead to death.
Some of the most common allergenic hazards in food include:
- Peanuts and tree nuts.
- Milk and dairy products.
- Eggs
- Shellfish
- Wheat and gluten
- Soy
Butcher’s shops should be cautious when using pre-made seasonings, marinades or sauces that may contain allergens and ensure proper product ingredient labelling. As mentioned, food safety laws mean that certain allergens must be emphasised and clearly labelled on the packaging and that food establishments like butcher’s shops must also have allergy information available for customers on the items that they make and sell. There must also be proper allergen management controls in place.
The 4Cs
Butchers must follow the 4Cs of food hygiene to best prevent and avoid food hazards.
The 4Cs are:
- Cleaning
- Cooking
- Cross-contamination
- Chilling
Cleaning
According to the Food Standards Agency, a lack of proper cleaning is one of the most common reasons why a food business like a butcher’s shop is prosecuted. Cleaning is vital. It prevents harmful pathogens or cross-contact allergens from spreading, getting where they shouldn’t, and contaminating foods. Cleaning also discourages pests from making a home on the premises.
Cleaning in a butcher’s shop includes removing contaminants including blood, dirt, grease and other substances from surfaces, utensils and equipment. In a butcher’s shop, all food contact surfaces should be cleaned regularly including cutting boards, knives and counters. All equipment and machinery used in meat processing should also be cleaned and maintained properly. Floors, walls and storage areas must be cleaned regularly to prevent the build-up of dirt, bacteria or pests. Waste should also be managed well to prevent odours and minimise the risk of contamination.
Many butchers use a ‘clean as you go’ cleaning system whereby the workers clean up continually as they work before doing one final clean at the end of the day.
Cooking
Many butchers cook some of their goods on the premises. This often applies to baked goods such as sausage rolls or pies. Often, butchers cook samples of their products for customers to try before they buy too. This means that any baking and cooking must be done correctly before food is sold to customers. If food is undercooked, it can mean that it is not safe to eat and could cause illness such as food poisoning if someone eats it. Foods must be cooked or baked for the correct amount of time at the correct temperature to ensure that any harmful bacteria that are present in the food are killed. Butcher’s shops should also follow any food preparation guidelines on packaging (if present) and ensure that it is piping hot during cooking.
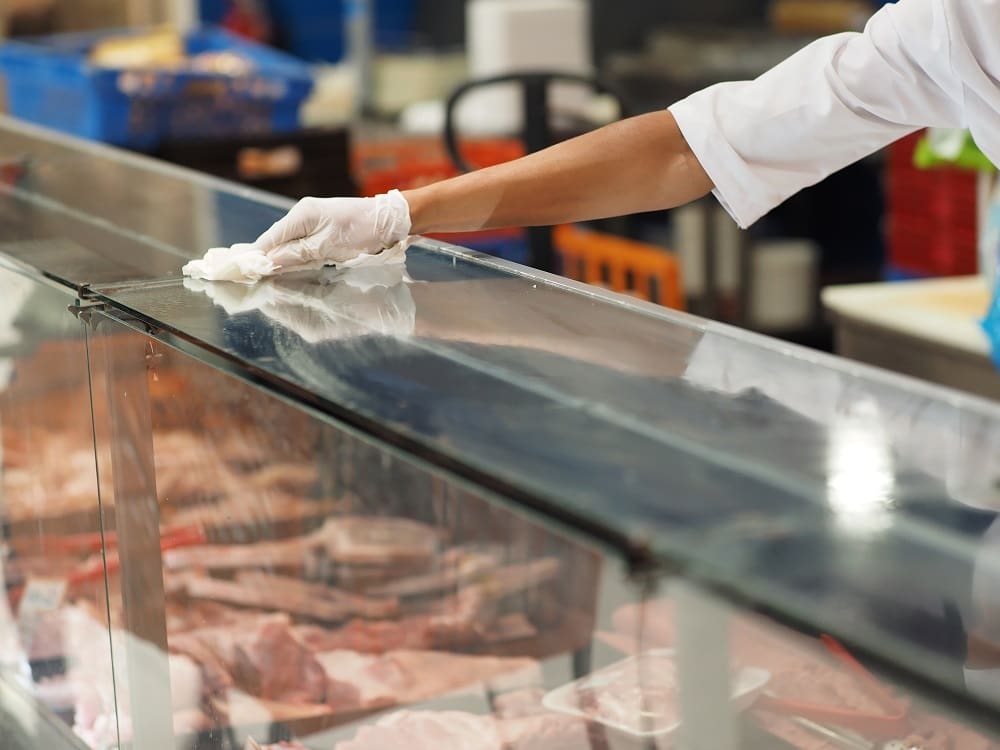
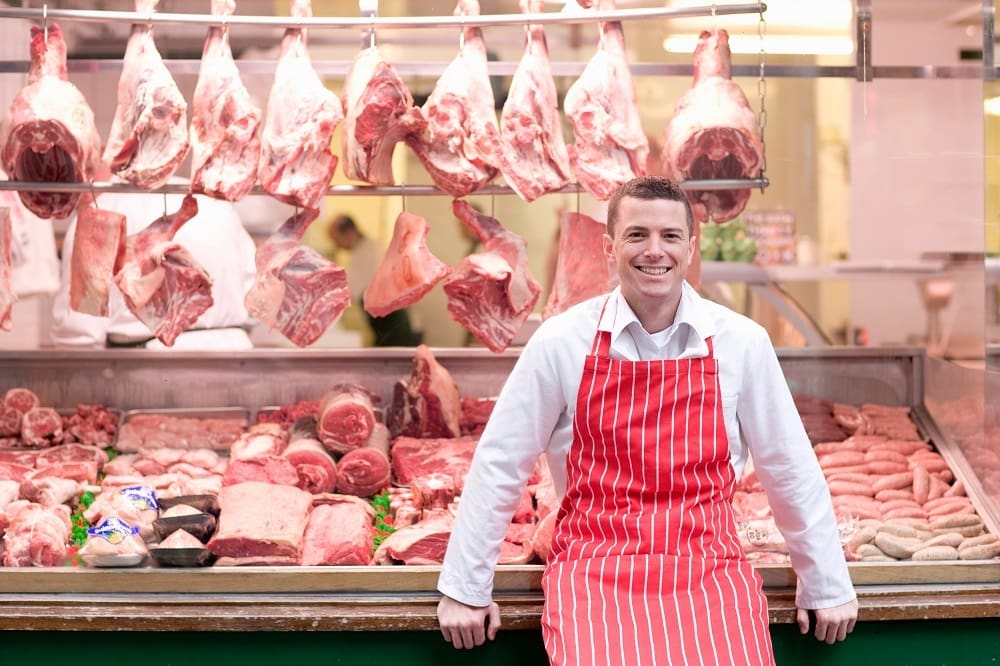
Cross-contamination
Nearly all foodborne illnesses happen as a result of cross-contamination when harmful allergens or pathogens are transferred into food from surfaces, utensils, between foods and from person to food. Cross-contamination of bacteria and viruses often results in what people call ‘food poisoning’. When referring to allergens, the term ‘cross-contact’ is more often used. It only takes a microscopic amount of allergen to cause an allergic reaction in some people.
Aside from pathogens and allergens, cross-contamination can occur with chemicals such as those used in cleaning, especially ones that are sprayed into the air where they can settle on food.
Staff working in a butcher’s shop must take cross-contamination and cross-contact extremely seriously. Butchers often pose a greater risk of cross-contact than some other food establishments due to their layouts.
Butcher’s shop owners should take the risks seriously and should have the following strategies in place:
- All workers must practise good personal hygiene.
- There should be separate areas for utensils and equipment if dealing with allergens.
- Equipment and utensils should be thoroughly cleaned between uses.
- Food should be stored correctly as per the guidance below.
- Cleaning should be consistent and cautious.
Chilling
When it comes to chilling meat in a butcher’s shop, the following guidelines and temperature regulations are recommended:
- Fridge temperature: The FSA advised that refrigerated storage areas should be set at a maximum temperature of 8°C. This is because this temperature helps slow down the growth of bacteria and helps maintain the quality and safety of perishable foods, including meat products.
- Chilled display cabinets: When displaying chilled meat products in cabinets, it is recommended that the temperature is between 0°C and 8°C. The meat should be easily visible and accessible to customers whilst being kept at a safe temperature.
- Storage duration: The FSA also recommends that fresh raw meat, including beef, lamb, pork and poultry, is stored in the fridge and used by its specified shelf-life or ‘use-by’ date. This means that the meat remains of good, safe quality.
- Temperature monitoring: The temperature of fridges and display cabinets must be monitored and recorded regularly using appropriate thermometers. This will help detect any unsafe fluctuation in temperature control.
- Rapid chilling: Rapid chilling is important for certain cooked or processed meat products. This includes ready-to-eat meat products such as sliced ham, deli meats, or prepared salads containing meat. These products are typically consumed without further cooking so it is important to cool them quickly to prevent the growth of harmful bacteria. Cooked meat dishes such as meat pies can take a long time to cool in a refrigerator – rapid chilling brings the temperature down more quickly. Rapid chilling can be achieved by using blast chillers or shallow containers in a controlled environment, bringing the temperature down to below 8°C as quickly as possible.
Whilst chilling does not kill harmful bacteria, it does slow down their growth, meaning they should not grow to unsafe quantities. When food isn’t chilled properly, it enters the ‘danger zone’. This encourages pathogens to grow and increases the risk of food poisoning.
Personal Hygiene in Butcher’s Shops
Personal hygiene is of the utmost importance in a butcher’s shop to ensure the safety and cleanliness of the working environment as well as for the customers who purchase the butcher’s products. Every worker in the butcher’s shop should be trained in proper personal hygiene, including:
- Training: Staff must be trained in personal hygiene and proper handwashing techniques and the role that they play in maintaining food safety. Refresher courses, regular reminders and posters on the premises should help reinforce good hygiene practices.
- Hand hygiene: Direction on how to wash hands thoroughly with warm water and soap before starting work, after using the toilet, after handling raw meat, and after any activities that may contaminate their hands. Hands should be washed for a minimum of 20 seconds. Hand sanitiser can be used as an additional measure (but not instead of handwashing). Proper handwashing prevents the spread of bacteria and other pathogens within the butcher’s shop.
- Protective clothing: Butcher’s shop staff should wear appropriate protective clothing including clean uniforms or aprons, hairnets or hats to cover hair, and disposable gloves when handling raw meat or ready-to-eat products. Gloves should be changed regularly (especially in between handling raw meat and ready-to-eat products) and should not be considered a replacement for washing hands.
- Illness and injuries: Employees with infectious illnesses such as stomach viruses or respiratory infections should not handle food and should report their illness to their supervisor. Cuts, wounds and skin infections should be properly covered with waterproof dressings before starting work. This helps reduce the transmission of any pathogens from staff to the butcher’s products.
- No eating, drinking or smoking: Doing any of these activities is not permitted in areas where meat is handled or processed. This helps prevent foreign substances from being introduced and reduces the contamination risk.
- Personal cleanliness: Employees in butcher’s shops should maintain high standards of personal cleanliness. This includes showering and bathing, keeping hair clean and tied back, and nails short and clean. Perfumes or strongly scented products should also be avoided as they could taint the meat products.
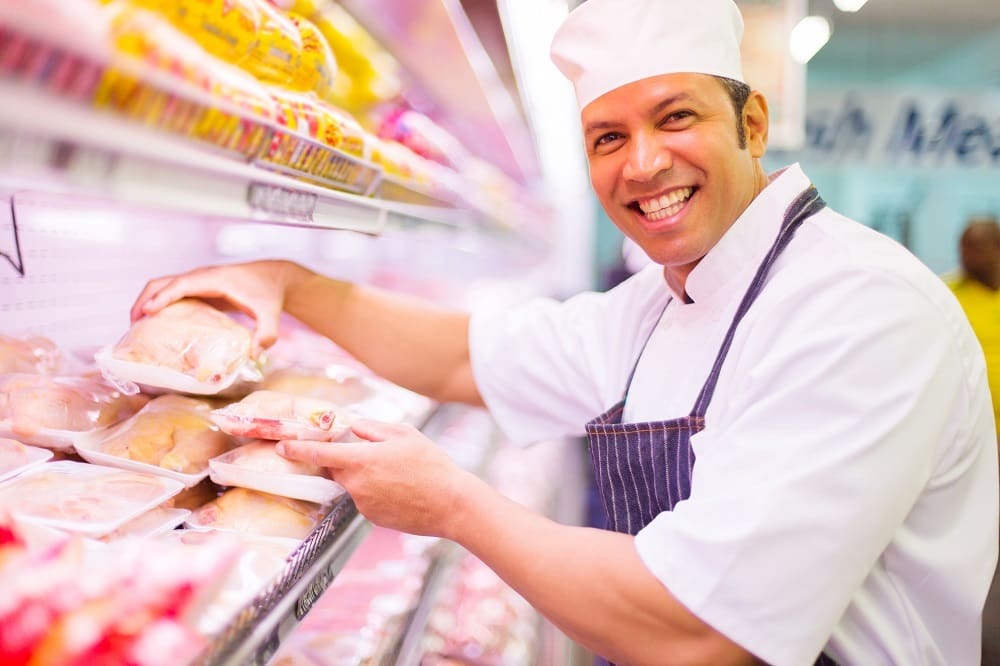
Food Allergens in Butcher’s Shops
In a butcher’s shop, many food allergens may be present, either in the raw meat itself or in the products made and sold in the shop. For those with allergies, coming across even a minuscule amount of allergen can be fatal. Many butchers may prepare their own food products such as pies, pastries, burgers, sausages and stir-fry mixes. This means that many allergens may be present near other products. Because of this, many butchers may state that although a product does not contain an allergen directly, they cannot guarantee that there hasn’t been any cross-contact.
By law, 14 allergens must be listed on ingredients for products sold.
These allergens are:
- Milk
- Celery
- Cereals containing gluten such as wheat, rye, barley and oats.
- Crustaceans, such as prawns, crabs and lobsters.
- Eggs
- Fish
- Lupin
- Molluscs such as clams, mussels and oysters.
- Mustard
- Nuts such as almonds, hazelnuts, walnuts, cashews, pecans, macadamia nuts, pistachios and Brazil nuts.
- Peanuts
- Sesame seeds
- Soybeans
- Sulphur dioxide and sulphites (at concentrations of more than 10mg/kg or 10mg/litre).
In a butcher’s shop, the most common allergens that are likely to be found are milk, wheat/gluten, soy and eggs. Milk is often present in processed meat products as an additive, in marinades or sausage casings. Some sausages, meatballs or other meat preparations may contain milk or milk derivatives so it is important to read and display ingredients labels carefully.
Wheat and gluten are also commonly found in breaded meat products such as escalopes. Wheat flour is also commonly used as a filler or binder in meatballs, sausages, burgers and meatloaf. Marinades and sauces also commonly contain wheat.
Soy is an allergen that is present in soy sauce and many additives are also soy-based. They could be used as binding agents or flavour enhancers in sausages, burgers, or meat-based sauces. Eggs are also used as emulsifiers, binders or in coatings for products such as burger patties, meatballs and sausages.
Information on all allergens in products should be readily available for customers and if the food is pre-packaged for direct sale (PPDS) then the ingredients must be clearly labelled on the packaging.
Workers should take precautions to avoid cross-contact when preparing food within the butcher’s shop.
This can be achieved by:
- Ensuring that allergenic hazards are included in HACCP systems and controls are put in place.
- Providing training on allergens for staff, including what to do in emergencies if a customer has an allergic reaction.
- Looking for allergenic ingredients on purchased products before using or supplying them (i.e. Worcestershire sauce contains anchovies which is a type of fish).
- Preparing products containing allergens in a separate area from non-allergenic products, for example, using different coloured chopping boards.
- Storing allergen-containing products separately from non-allergen-containing products.
- Cleaning surfaces and utensils thoroughly between uses where separate equipment is not possible.
- Labelling containers with any allergens stored within them.
- Recording information regarding allergens accurately, including on-shelf labels or ingredient labels and recipes.
Unlike pathogens such as bacteria, allergens are not affected by heating or cooling. As a result, butcher’s shop workers should be extra careful when handling any allergens and proceed with caution if a customer reports an allergy. Many butcher’s shops state that they handle all 14 allergens on the premises and cannot guarantee that their products are free from certain allergens to be on the safe side.
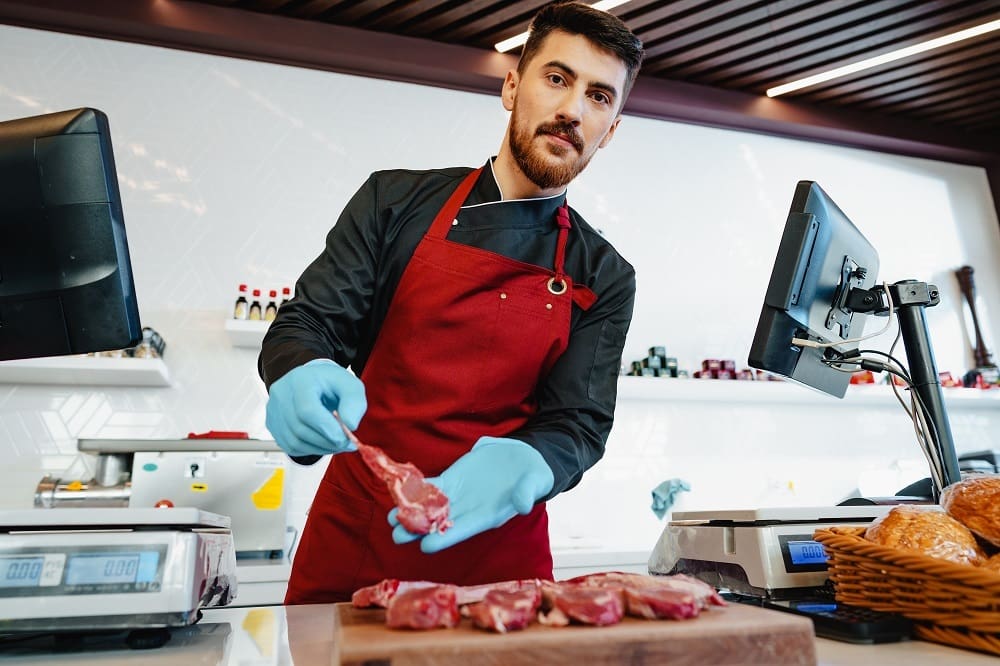
Safely Storing Food in a Butcher’s Shop
Food should be stored correctly in a butcher’s shop to maintain the quality of the food as well as prevent any foodborne illnesses.
There must be strict storage systems in place including:
- Dispose of any spoiled or out-of-date food promptly.
- Storing food at the right temperature. The refrigerator should be kept at or below 5°C and frozen food at or below -18°C. There are also specific rules in place for the temperatures that are needed when preparing different types of meat as mentioned above.
- The temperature of the fridge and freezer should be checked regularly to ensure that they are working correctly.
- Storage containers should be food-safe and should be labelled with the name of the food and the date it was stored as well as labelling any allergens within it to ensure proper and safe storage.
- Food should be stored in clean, dry and well-ventilated areas to prevent the growth of bacteria and mould.
- Advice for specific food storage should be followed.
- Rotate food regularly to ensure that older food is used up first. Have a system with first-in-first-out (FIFO) stock rotation.
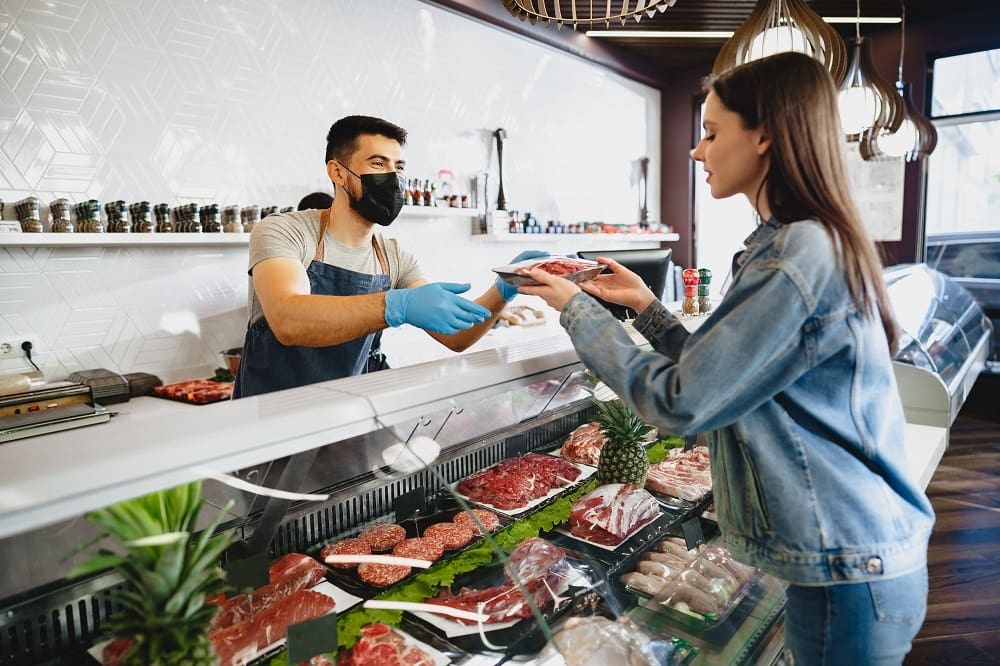
Safely Serving Food in a Butcher’s Shop
Whilst it’s not always common, some butcher’s shops have diversified further into hot food takeaways, sandwich bars, eateries or cafés where food is served. The food may be on display on counters or in hot holding areas before it is served to customers. The food mustn’t be contaminated during handling or packaging in the butcher’s shop. Any utensils used to handle foods should be cleaned thoroughly after each use. If utensils are not used, the staff handling foods should use disposable gloves and practise good hand hygiene.
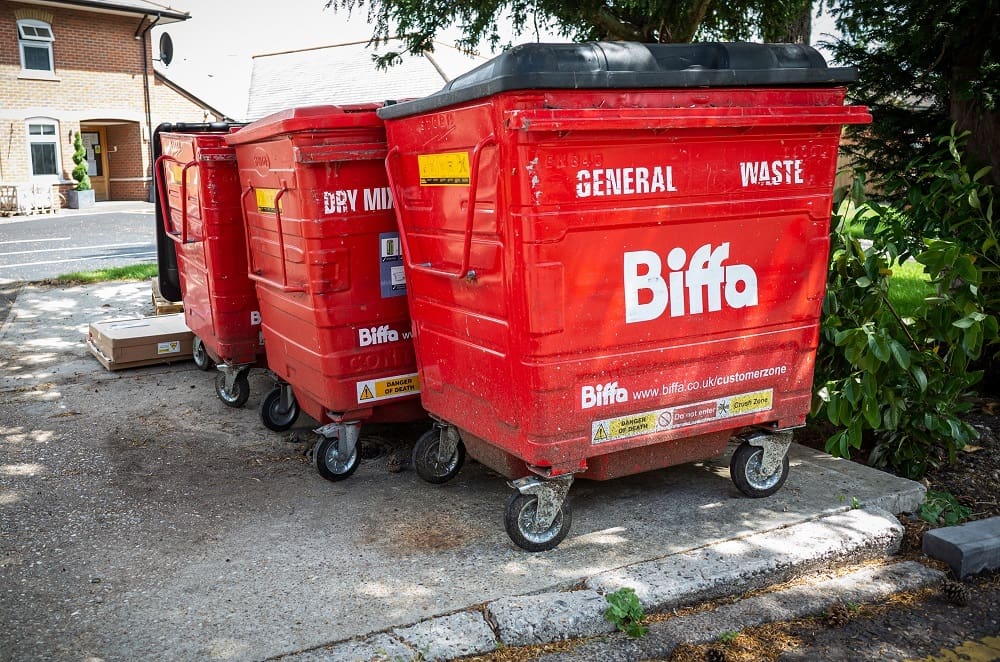
Waste Management in a Butcher’ Shop
Handling the waste effectively in a butcher’s shop is essential as, if it is poorly managed, it can result in problems with pests. Handling meat and animal carcases means that waste from a butcher’s shop is also hazardous.
Here are some best practices for water management in a butcher’s shop:
- Segregation: Proper segregation of different types of waste is vital. This means separating general waste, recyclable materials, food waste and potentially hazardous waste including animal remains, sharp objects and chemicals. Waste bins should be clearly labelled for their category and staff members should be trained on proper segregation practices.
- Food waste management: Measures to reduce food waste generation should be implemented. This includes accurately estimating customer demand so that there is not too much waste that needs to be disposed of. Excess food waste should be disposed of correctly, in tightly sealed containers to prevent odours and pests. Surplus edible food should be considered for charity to minimise waste and maximise use.
- Recycling: Butcher’s shops should ensure they are recycling as much as possible by having easily accessible, clearly labelled bins for different recyclable materials such as cardboard/paper, glass, plastic and tins.
- Hazardous waste: Waste such as animal waste should be disposed of properly. This type of waste is often collected by specialist disposal companies. In the UK, butchers must hold the appropriate licences to comply with the Animal By-Products Regulations (2013) that govern the handling, storage, transportation and disposal of animal by-products and hazardous waste.
- Waste collection and disposal: Butchers should engage with professional waste management services that are licensed and compliant with environmental regulations. Waste collections should be scheduled regularly to prevent bins from overflowing potentially causing hygiene issues. Records of waste collection and disposal should also be kept for auditing purposes.
- Cleaning protocols: Waste storage areas in a butcher’s shop should be cleaned and sanitised regularly to minimise odours, prevent pests and keep the environment as clean as possible. Staff should be trained on the importance of waste management to maintain overall food safety and cleanliness.
Aside from these, waste should also be removed regularly from food areas to avoid it accumulating. Bins should be easily accessible, both inside and outside, but should be lockable outdoors when not in use to prevent pests.
A butcher’s shop should foster a culture of waste management awareness among all workers in the team, making sure that everyone knows that they have a role to play in best waste management practices. By doing so, butcher’s shops can maintain a clean, hygienic environment that is fit for purpose as well as show their commitment towards being a responsible business.
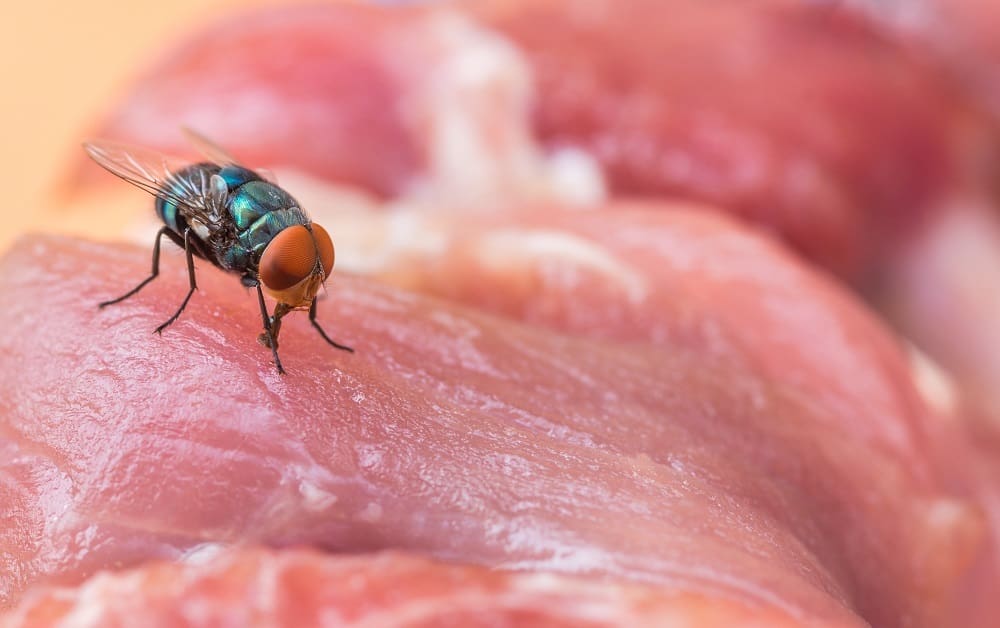
Pest Control in a Butcher’s Shop
Pests are a well-known hazard in many food establishments – and butcher’s shops are not immune!
The presence of food and waste easily attracts common pests, including:
- Rodents: Rats and mice are attracted to the food sources found in butcher’s shops. They can contaminate products, packaging and storage areas with their droppings, urine and hair, posing a significant risk to food safety.
- Flies: House flies, blow flies and fruit flies are attracted to organic waste and meat products. These pesky pests carry bacteria and can spread it around, causing foodborne illnesses.
- Cockroaches: Cockroaches tend to be nocturnal. They look for food and shelter in warm, moist environments. They contaminate food and surfaces with their droppings, exoskeletons and salvia. They are also known to transmit certain diseases.
- Stored product insects (SPIs): SPIs may not be a common pest for a butcher’s shop; however, given that they are often found in flour, spices and grains, it’s not too much of a leap to think that they might find themselves nestling in the ingredients for a burger or marinade that’s ready to be used or sold.
- Ants: Certain types of ants are attracted to spills, sweet things and crumbs. They can cause a nuisance in a butcher’s shop and can also contaminate food.
- Birds: Pigeons and seagulls are often attracted to butcher’s shops, especially if there are exposed or improperly stored products in outside yards or workshops. Bird droppings and feathers can contaminate surfaces, equipment and food itself, potentially, spreading diseases.
Preventing infestations of pests in a butcher’s shop is essential.
Butchers can try to prevent and control pests by:
- Keeping the butcher’s shop clean and tidy. This includes cleaning the floors, walls and counters. Food spills should be cleaned promptly.
- Disposing of waste correctly, particularly food waste as this is what attracts pests the most. Bins should be tightly sealed.
- Storing food correctly in tightly sealed containers. Containers should not be on the floor to prevent pests from entering them. When raw materials arrive from the farm, the contents should be inspected carefully to make sure no pests are being introduced to the butcher’s shop.
- Sealing any pest entry points such as cracks and gaps around windows, pipes, doors and floor. This will help to prevent pests from entering the butcher’s shop.
- Using products if pests are suspected to catch and/or eliminate them.
- Hiring professionals in to clear any pest infestations so that the job is done properly.
- Training the staff who work in the butchers to promote the importance of good practices within the shop and how to prevent pests.
By following such tips, the butchers and their customers can be sure to be as safe as possible.