In this article
Electricity is an essential part of our everyday lives and is present in most, if not all, workplaces and homes. Despite its usefulness, it is dangerous, as contact with it can result in death or severe injuries. It can also cause damage to property from electrical-related fires and explosions.
Every year, approximately 1,000 accidents (30 of these fatal) at work involving electric shock or burns are reported to the Health and Safety Executive (HSE). Most fatalities are caused by contact with overhead or underground power cables. Even where electric shocks are not fatal, they can still result in permanent life-changing injuries.
Electrical-related fires are not uncommon either. In the Fire and Rescue Services statistics for England (2019/2020), there were:
- 14,308 fires in non-domestic premises
– 17 fatalities and 877 non-fatal casualties.
– 2,219 fires were caused by electrical distribution and 1,629 fires were caused by electrical appliances. - 28,494 fires in dwellings (homes)
– 199 fatalities and 5,152 non-fatal casualties.
– 3,081 fires were caused by electrical distribution and 3,145 fires were caused by electrical appliances.
Those who work directly with electricity, e.g. engineers, electricians and overhead lines staff, are at a higher risk. However, it is also a risk for other workers and the public who use electrical equipment and appliances at work and at home.
The dangers of electricity are often underestimated, especially in low-risk environments such as offices and when people are at home. The mains electrical supply in these types of environment is 230 volts, which may seem low. However, to put this into perspective, a voltage of just 50 volts is enough to cause the heart to stop and prevent breathing. Therefore, everyone must take electrical safety seriously, whether they are at work or at home.
If there is a risk of electrical injuries at work, employers have a legal duty to prevent, reduce or control the risks. It requires them to put precautions in place, e.g. providing employees with electrical safety training and information and instruction via safety signs and labels.
This article will look at electrical training, hazards and safety signs, and associated regulations and standards. It will also briefly look at PAT testing and labels.
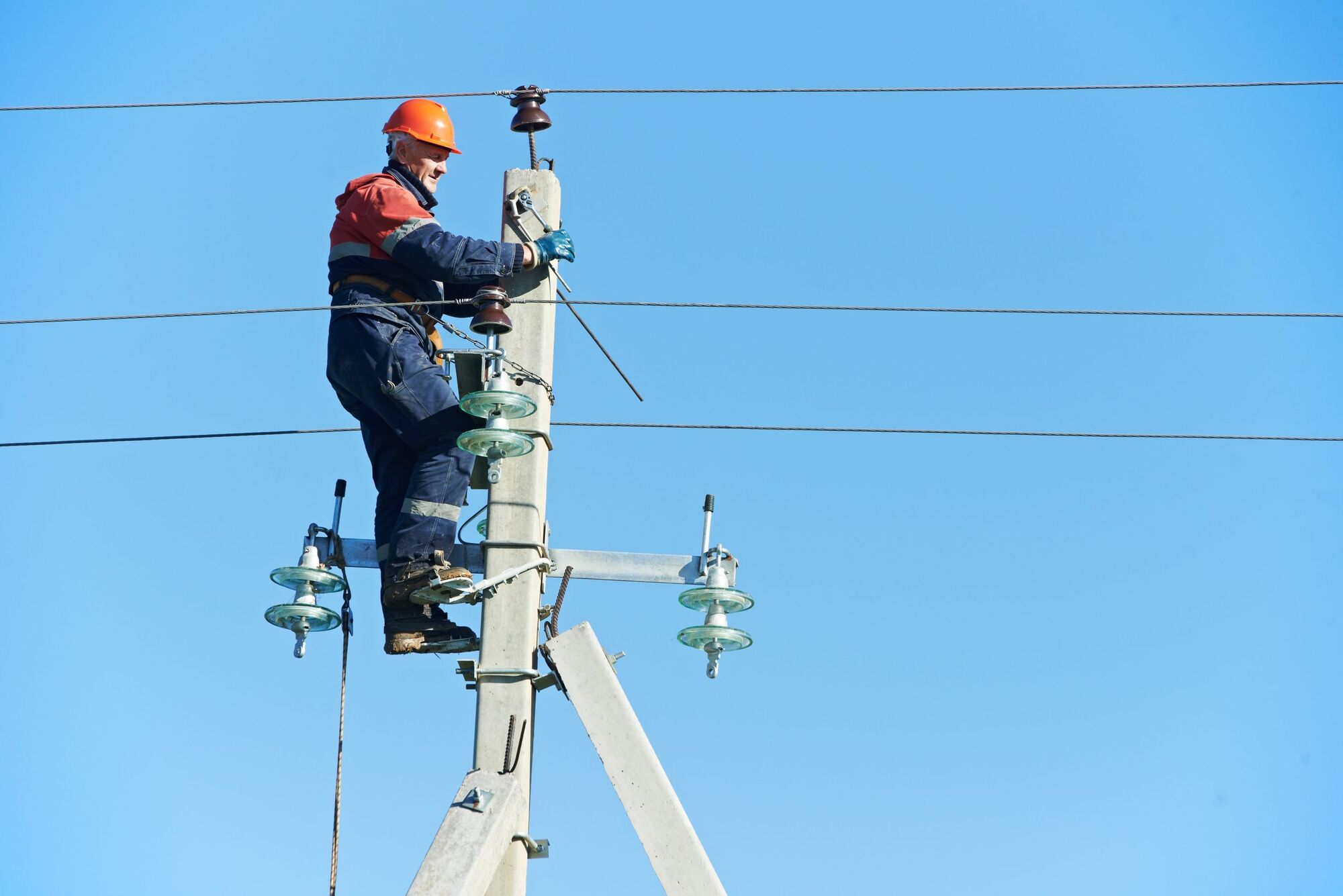
Electrical safety training
Anyone working near or on electrical systems or equipment must be competent. For a person to be deemed competent, they must have suitable training, skill and knowledge for the task to prevent injury to themselves and others (HSE). Training and competence are important in preventing and reducing the risk of electrical accidents.
The training and competence required will depend on the electrical work to be undertaken and the risks. For example, specialised work on high-voltage equipment will require additional training and a higher level of competence. Those who are undergoing training must also be supervised by a competent person.
According to the HSE, “a person can demonstrate competence to perform electrical work if they have successfully completed an assessed training course, run by an accredited training organisation, that included the type of work being considered. As part of that course, this person should have demonstrated an ability to understand electrical theory and put this into practice”.
Those who do not work on electrical systems or equipment may still be at risk from electrical hazards, e.g. users of appliances and equipment. Therefore, they should receive information, instruction and training on electrical safety. Our Electrical Safety Awareness Course can help employers and employees understand how dangerous electricity is and the precautions required to reduce the risks.
Avoiding electrical hazards
A hazard is something that has the potential to cause harm. Risk is the likelihood of harm occurring and the severity should it happen. Electricity is a hazard that can cause death, severe injuries and property damage, and it is a risk in almost all workplaces and homes.
The hazards present and the level of risk will depend on:
- The task, e.g. working on live electrical equipment will be a higher risk than using an electrical appliance in an office.
- The training and competence of workers, e.g. those in training will be more at risk than those with a higher level of competence.
- The electrical systems, processes or equipment involved, e.g. working with higher voltages will be more hazardous.
- The environment, e.g. using electrical equipment outdoors will be a higher risk than using it indoors.
Common electrical hazards
Some examples of common electrical hazards include:
- Electrocution, electric shock and burns, e.g. contact with live electrical parts.
- Eye damage and burns, e.g. from electricity arcing.
- Fire, e.g. from faulty, defective or damaged electrical equipment.
- Explosion, e.g. using unsuitable equipment that could be a source of ignition in an explosive atmosphere.
- Other hazards that can result in injury, e.g. an electric shock causing a fall from height
- Interruption of safety-critical equipment due to a loss of power.
Electrical accidents
Electrical accidents can occur for many different reasons, such as:
- Not isolating electrical installations and equipment properly before working on them.
- Working on or near live electrical systems that were assumed to be dead.
- Inadequate information and instruction provided on the risks.
- A lack of training and competence to undertake tasks involving electricity. Inadequate training is one of the main causes of electrical accidents.
- An unsafe safe system of work.
- Using the incorrect type of equipment, which is not suited to the environment, e.g. using electrical equipment in wet conditions.
- Using faulty, damaged and defective electrical systems and equipment.
- Poor design and construction of electrical installations and wiring.
- Overloading of electrical systems causing them to overheat.
- Inadequate maintenance, inspection and testing of electrical systems and equipment.
Minimising the risks
There are many precautions that can minimise electrical safety risks and far too many to mention in this article.
Some examples include:
- Ensuring the electrical installation is installed to a suitable standard and maintained by a competent person.
- Selecting the most suitable electrical equipment for the task and environment. Looking at safer alternatives where possible, e.g. low-voltage equipment.
- Using protective devices such as circuit breakers, fuses and residual current devices (RCDs).
- Ensuring people working with electricity are trained and competent. Those who are at risk from using the equipment should have an awareness of electrical hazards and precautions.
- Not misusing electrical equipment, using it for its intended purpose and storing it properly after use.
- Maintaining electrical equipment regularly, e.g. PAT testing.
- Completing a pre-use check of equipment to ensure that it is safe.
- Having enough sockets and not overloading them to prevent overheating and fire.
- Not routing electrical cables where they could be damaged or where someone could trip.
- Switching off electrical equipment and sockets before plugging in or unplugging, and during maintenance, cleaning, repairing or adjusting.
- Having procedures in place to deal with emergencies and adequate first aid provision to deal with electrical injuries.
- Switching off all non-essential electrical equipment at the end of the working day.
Further information on electrical hazards and precautions can be found on the HSE’s electricity webpage and in their electrical safety guidance.
There are many different measures to prevent, control or reduce the risks of electrical hazards. Those selected must reduce the electrical risks to the lowest possible level. One of the measures used is electrical safety signs.
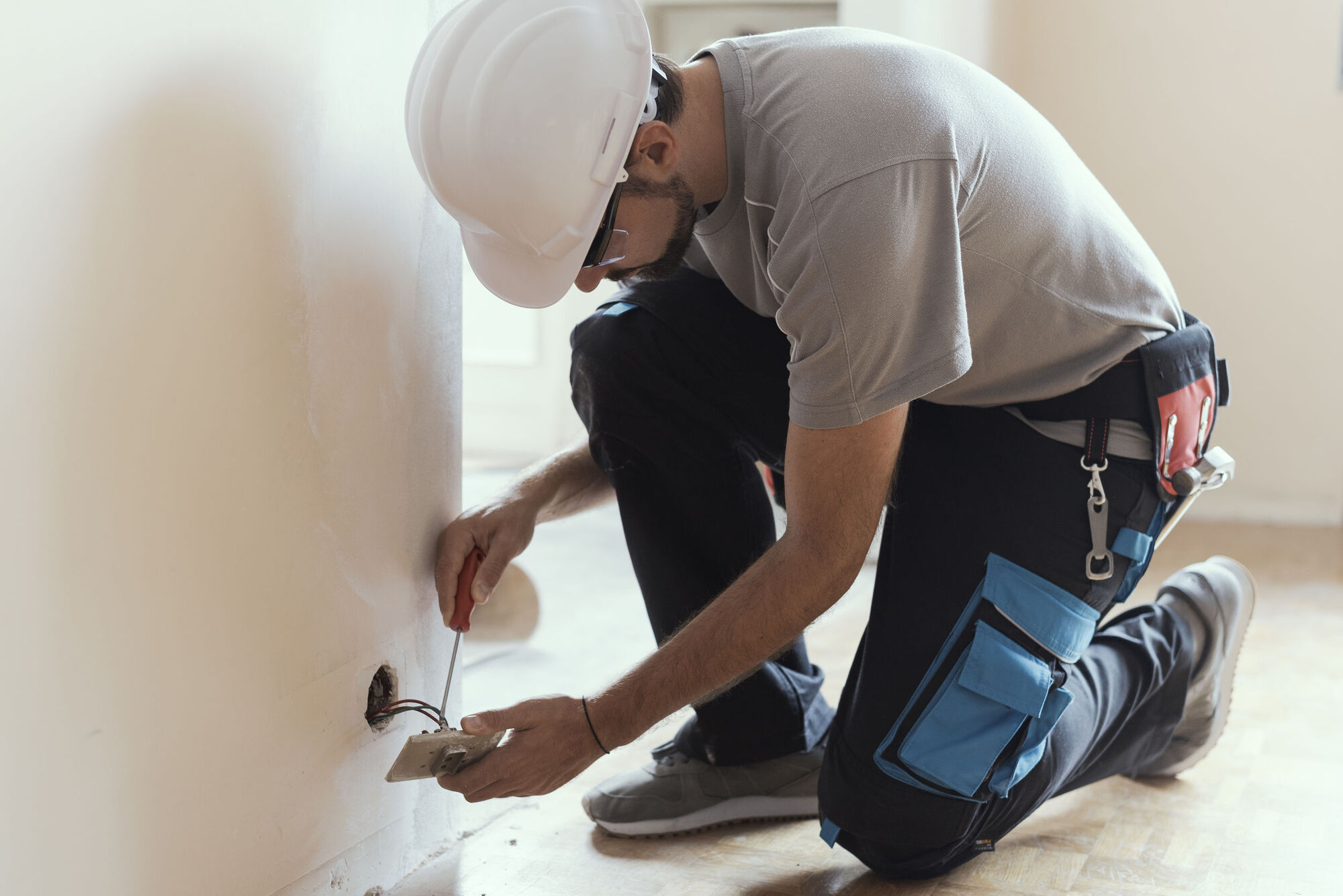
Electrical safety signs and symbols
Before providing safety signs, employers must first look at eliminating electrical hazards wherever possible, e.g. using non-electrical equipment. If it is not possible, they should then look at other means of avoiding or controlling the risk. For example, they can substitute higher voltage equipment for lower voltage or battery-powered equipment.
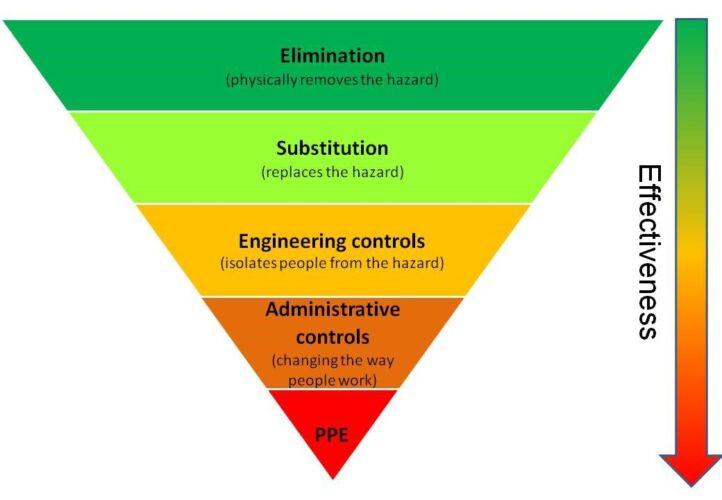
Electrical safety signs are examples of administrative controls. They are lower in the hierarchy as they do not remove the hazard. However, they are still important control measures. Safety signs can reduce the risk by providing information on the hazard and giving instructions on preventing exposure.
A safety sign is defined in the Safety Signs and Signals Approved Code of Practice as “a sign providing information or instruction about safety or health at work by means of a signboard, a colour, an illuminated sign or acoustic signal, a verbal communication or hand signal”.
The purpose of safety signs is to communicate health and safety information to workers and others at risk from the hazard.
There are five main categories of safety sign:
- Prohibition sign – Prohibits behaviour likely to increase or cause danger. They are circular-shaped and are RED with a white background, red band and crossbar.
- Warning sign – Gives a warning of a hazard or danger. They are triangular-shaped and are YELLOW with black symbols or text.
- Mandatory sign – Prescribes specific behaviour and what must be done. They are circular-shaped and are BLUE with white symbols or text.
- Safe condition sign – Gives information on emergency exits, first aid, or rescue facilities. They are rectangular-shaped and are GREEN with white symbols or text.
- Fire safety signs – Gives information on fire protection arrangements. They are square or rectangular-shaped and are RED with white symbols or text.
Some of the above are combined onto one sign to provide multiple messages, e.g.
Caution high voltage (warning sign).
Keep out (mandatory sign).
No entry (prohibition sign).
The most common electrical hazards signs are warnings. However, there are mandatory and prohibition signs relating to electrical safety.
Some examples that may be seen around the workplace or other areas include:
- Warning signs with a lightning bolt symbol, e.g.:
– Danger electric shock.
– Danger electrocution risk.
– Danger live electrical equipment.
– Danger high voltage.
– Main switch.
– Mains voltage.
– Danger 400 volts.
– Danger overhead cables.
– Danger buried cables.
– Danger switchgear. - Warning signs with a lightning bolt symbol striking a collapsed person on the ground, e.g.:
– Danger of death. - Mandatory signs with an exclamation mark in the blue circle, e.g.:
– Isolate for safe working or if fault occurs.
– Keep out.
– Keep locked.
– Disconnect mains plug from electrical outlet. - Prohibition signs with a hand stopping an activity, e.g.:
– No admittance, authorised personnel only.
– No entry.
– No unauthorised access.
All safety signs should have the appropriate universal symbols or pictograms to account for those who have difficulty reading and limited English skills. Signs displaying just text will not be compliant. Some have supplementary text (usually at the bottom) with further information on the hazard or instructions. If text is used, it must meet the category of the sign.
PAT labels
Faulty, damaged and defective electrical equipment is a common cause of accidents and is often due to a lack of maintenance. Electrical appliances and equipment should be subject to regular maintenance to identify any issues that could create a risk to users or others. Portable appliance testing (PAT), also known as PAT testing, is an example of an effective maintenance method.
According to the HSE, PAT testing is “the term used to describe the examination of electrical appliances and equipment to ensure they are safe to use”. The Institution of Engineering and Technology (IET) refer to it as the in-service inspection and testing of electrical equipment.
PAT testing involves a combination of visual inspections and electronic tests. After an electrical item has been PAT tested, labels are often attached to indicate the test date and whether it is safe or not.
They usually contain the following information:
- The appliance identification number or asset number.
- The signature or initials of the person who carried out the PAT test.
- The date of the PAT test.
- Whether it has passed, failed or being inspected. Failed equipment must be removed from use immediately.
- Some labels also have a re-test date. The HSE does not recommend this, as the tester is not responsible for determining the frequency of tests; the duty holder is. However, a re-test date can be added to the label if they have been informed of the necessary frequency.
PAT labels do vary, and there are many different types, for example:
- Passed labels are usually green but can be blue, purple or black to account for different periods before the next test.
- Failed labels tend to be red but are sometimes amber.
- Some have barcodes that can be scanned by certain PAT testing equipment, which gives a maintenance history for the appliance.
- Some are circular or rectangular-shaped.
- Some can be personalised with the company details.
There is not a specific requirement for PAT labels to be a particular colour, size or shape. However, PAT labels are covered in the IET Code of Practice for In-Service Inspection and Testing of Electrical Equipment. The Code of Practice is widely accepted, and many PAT label suppliers will follow the requirements within.
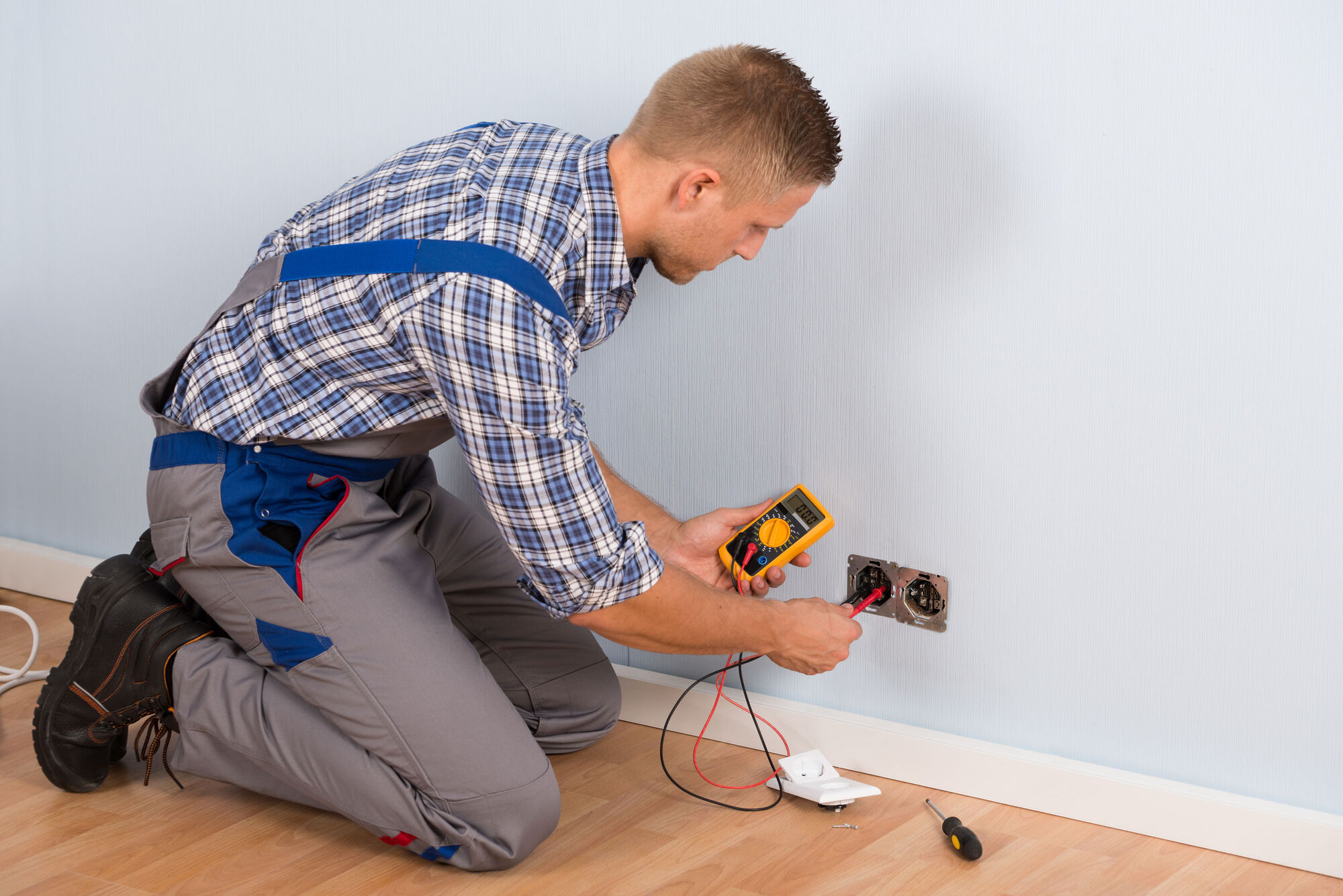
Regulations and standards
The Electricity at Work Regulations 1989
The main law relating to electrical safety is the Electricity at Work Regulations 1989. These regulations place duties on employers, the self-employed and employees. It aims to prevent and reduce the risk of death and injury from electricity in the workplace.
The main requirements of the regulations are as follows:
- Electrical systems must be of good construction and maintained to prevent danger.
- The strength and capability of electrical equipment must not be exceeded.
- Electrical equipment must be protected if used in adverse or hazardous environments, e.g. in wet conditions.
- Electrical conductors must be protected and insulated if dangerous.
- Precautions such as earthing and other protective measures should be provided where required.
- Electrical systems and equipment should have a means of isolation and supply cut-off in dangerous situations. It also covers working on dead equipment once isolated.
- Workers shouldn’t work on or adjacent to live conductors unless there is no other way. Further precautions will be required for live working.
- There should be adequate space, access and lighting around electrical equipment when working on it.
- People must be competent or supervised to work on electrical systems and with electrical equipment.
The Health and Safety (Safety Signs and Signals) Regulations 1996
The requirement for electrical safety signs comes under the Health and Safety (Safety Signs and Signals) Regulations 1996. Where there is a significant electrical risk that cannot be eliminated or controlled by other methods, employers must provide safety signs and maintain them by law. The Safety Signs and Signals Approved Code of Practice provides further guidance on the requirements of the regulations.
When and where to use safety signs should be based on the findings of the risk assessment. They should only be used where they can further reduce the risk. They should be clear and legible, and employers should avoid using too many signs, as it can confuse people.
To comply with the regulations, employers must also provide employees with suitable and sufficient instruction and training in the meaning of safety signs, including the measures to take in connection with them.
BS EN ISO 7010
BS EN ISO 7010 is an international standard. According to the British Standards Institution (BSI), BS EN ISO 7010 standardises the look of safety signs and their meaning for international use and for the purposes of accident prevention, fire protection, health hazard information and emergency evacuation. The shape and colour of each safety sign and the design of the graphical symbols is according to ISO 3864 series.
ISO 7010 was introduced so that safety signs were consistent across Europe. In 2013, it became a European Normative (EN), which meant it was adopted by European Law. As a result, all member states had to adopt the standard, which included the UK. The UK has now left the EU, but BS EN ISO 7010 is the British version of the standard and still applies.
It is important to note that British Standards are not law. However, BS EN ISO 7010 is referred to in the Safety Signs and Signals Approved Code of Practice (ACOP), which provides guidelines on complying with the Health and Safety (Safety Signs and Signals) Regulations 1996. An ACOP is a legal series publication, and the HSE can use it as evidence of non-compliance with the regulations. Therefore, it is wise for employers to follow the standard with regards to their safety signs.
PAT testing and labels
There is no legal requirement to carry out PAT testing, but it is an effective way of showing that electrical equipment has been effectively maintained. Maintenance is a legal requirement under the Electricity at Work Regulations 1989 and the Provision and Use of Work Equipment Regulations (PUWER) 1998. The frequency of PAT testing should always be based on the findings of a risk assessment.
There is also no legal requirement to use PAT labels, but it is recommended as it shows that the equipment has been tested, the result and the date of the test. It also provides evidence that an effective maintenance regime is in place.
There are guidelines for PAT testing, including labels, in the IET’s Code of Practice for In-service Inspection and Testing of Electrical Equipment, 5th Edition.
Summary
Electricity can kill people. It can also cause severe injuries and damage to property. Therefore, electrical safety must be taken seriously by all those who may be directly or indirectly exposed to electricity.
Electrical signs and symbols provide workers and others with information on electrical hazards and instructions on preventing harm. Labels, such as those used in PAT testing, inform people that electrical equipment and appliances are safe to use or not. Signs, symbols and labels are a useful way of communicating health and safety information to employees and others, which can reduce the risks.
Employers have many legal duties regarding electrical safety in the workplace. They should use the top options in the hierarchy of control to prevent and reduce the risks in the first instance. If this isn’t possible, safety signs can be used where the remaining risks are significant. If safety signs are used as a control measure, employers must ensure they comply with the relevant laws and standards. It is also vital to ensure that those at risk from electricity understand the message to keep themselves and others safe.