In this article
Safety helmets (also known as hard hats) can prevent or minimise injuries to the head and brain, protecting against falling objects or debris, impact with other objects, electric shock and rain. Most head injuries can be avoided if the proper head protection is selected, used and maintained.
The history of head protection
Helmets were invented around 2500 BC to protect soldiers’ heads during battles. The first mass-produced versions were worn by Assyrian soldiers around 900 BC and were mainly made from bronze, protecting the wearer from sword blows and arrow strikes.
In the Victorian era, workers such as miners would wear only a canvas cap in the mines, giving them no protection from falling objects. Similarly, a boom period for construction, shipping and engineering at that time, shipbuilders, dock and construction workers had no protective headwear to protect them when working, despite the dangerous work they were doing, although many employers were beginning to consider the wellbeing of their workforces.
For example, contractors William Arrol were noted at the time, as making every effort to look after the welfare of the “Briggers” (construction workers) working on the construction of the Forth Rail Bridge in the 1880s.
However, a description of the clothing worn by the men included “old tweed jackets, mufflers and caps” which although helping to keep out the worst of the Scottish weather, offered little or no protection against falling tools or red-hot metal. Seventy-three fatalities were recorded on that project, many from head injuries.
It was not until the late 1800s, that the Patent Pulp Manufacturing Co Ltd of Thetford in Norfolk, produced the first ever mass-produced hard hat to protect workers; documents from this company are held in the National Archives at Kew. The Patent Pulp Manufacturing Co Ltd manufactured a helmet from pulp which was mixed with lime and fed into formers.
The formed hat was left to dry and then lacquered giving a smooth, if slightly textured, finish and then a steel plate was riveted to the inside of the helmet to give further protection. Although these helmets were groundbreaking, they were somewhat uncomfortable to wear due to the lack of a cradle inside the helmet. The cradle was not invented until about 30 years later in 1919, by an American.
Shipbuilding appears to be the first industry where hard hats were used, as dock workers were in constant danger of being hit by falling objects. The use of hard hats, later to be known by the term safety helmets, then moved into the construction industry.
They were first recorded as a mandatory requirement for construction workers on the Hoover Dam and Golden Gate Bridge projects in the US in the 1930s. They are now a standard piece of safety equipment worldwide.
In Britain, following the death of TE Lawrence (Lawrence of Arabia) in a motorcycle accident, neurosurgeon Sir Hugh Cairns realised that his life might have been saved had he been wearing a helmet. He began to research and campaign for the use of motorcycle helmets in the UK.
This all led to the first motorcycle standard in 1952 which was followed 2 years later by the first hard hat standard (The Light Duty Safety Helmet Standard) in 1954; both were British Standards.
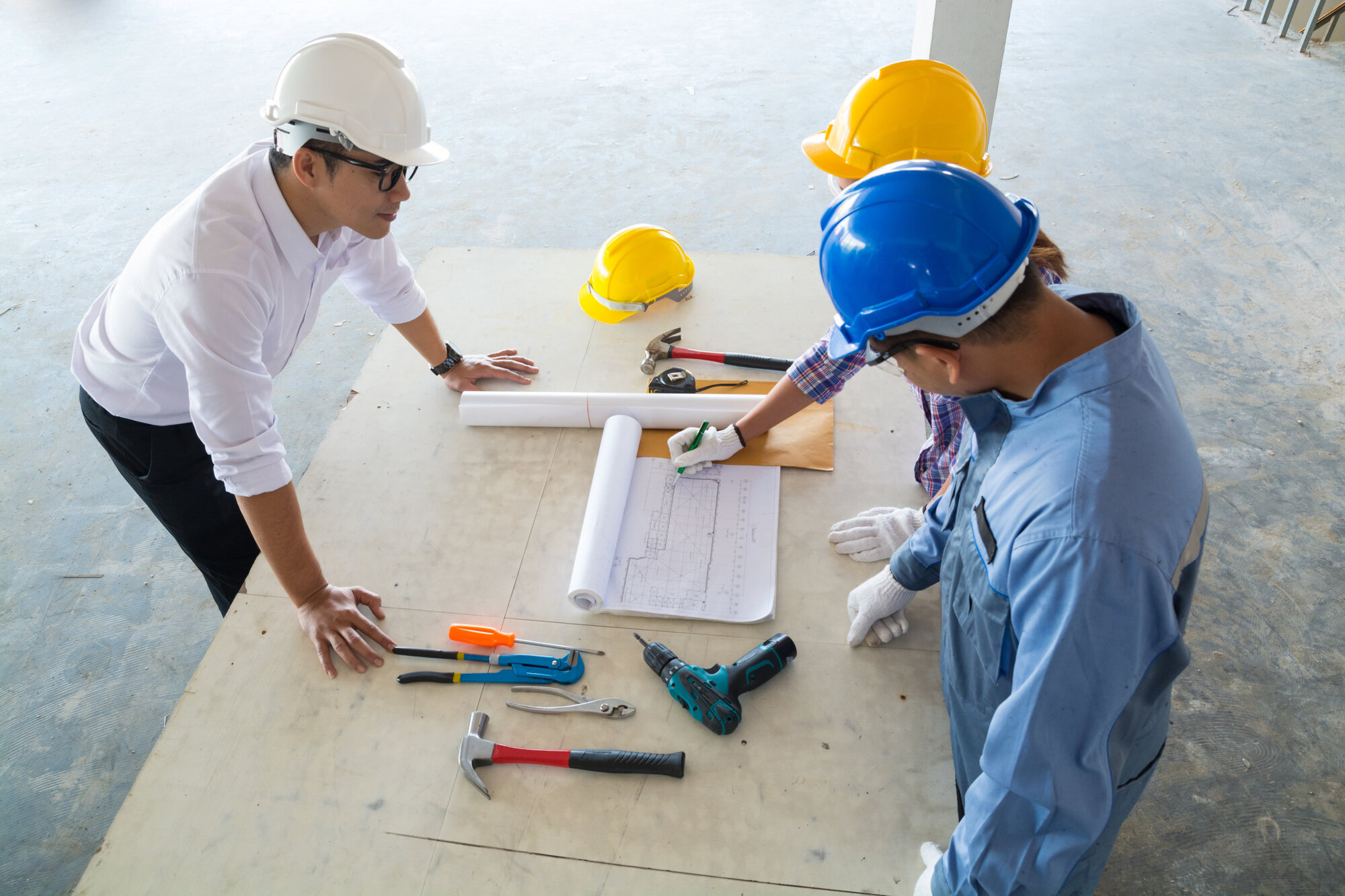
Some statistics
According to the Health and Safety Executive (HSE), 47% of estimated annual average injuries in the construction industry for the years 2017/18–2019/20, were from falls from a height and a further 12% of injuries were caused by being struck by moving, flying or falling objects.
Over all industries, of the 142 workers killed in work accidents in 2020/21, 35 were killed by falls from a height and 17 fatalities were caused by being struck by moving, flying or falling objects.
What is a safety helmet?
Safety helmets are crucial and mandatory on almost all work sites and manual working environments. Industrial safety helmets are the most common and basic form of PPE.
They will have the following components aimed at good protection for the head:
- Shell.
- Harness.
- Headband.
The outer shell is usually made from polyethylene, with the inner harness having a system of strips made from polyethylene or woven bands. The headband has adjustment mechanisms that can change its wearing height and its length to increase stability when worn.
Choosing the right safety helmet
Safety helmets are only required on an as-needed basis, so if a risk assessment does not identify any risks of head injuries, then they need not need be worn. However, different construction sites may operate their own rules, and if a risk assessment has identified the possibility of head injury, then safety helmets are mandatory, regardless of the nature of the construction work, or the size of the project.
Safety helmets used on UK construction sites must be manufactured to British Standard (BS) EN 397, which includes rigorous tests for impact resistance and flame retardance, among others. Any employee or visitor to a construction site should be provided with a safety helmet by either their employer or the main contractor, but self-employed workers (including subcontractors) may need to provide their own.
It is important to take several factors into account when choosing a safety helmet. It is first necessary to identify the task to be carried out by the worker as well as the constraints and risks of the activity that need to be provided for. The level of protection required from a safety helmet varies according to the activity. For example, a construction helmet cannot be used for demolition work because it does not offer the same protection.
No one helmet is perfect for everybody and there are several trade-offs to consider when deciding which is right for a work environment. First is the trade-off between performance and comfort.
High-performance helmets are relatively heavy, and though they offer maximum protection, unsupervised wearers may be tempted to remove the more cumbersome designs, leaving them with no protection at all, so there may be a need to balance protection with comfort to ensure compliance.
The different types of safety helmet
Helmet | Protection | Accessories | Applications | Applicable standard |
---|---|---|---|---|
Bump cap | A close-fitting baseball cap style offering the lowest level of protection. As the name suggests, its function is to provide padded protection against knocks from static objects. | Chinstrap which fits under the chin to help secure the bump cap on the head. Can be equipped with an LED light. | Vehicle manufacture and maintenance.Loft insulation.Plumbing.Removals.Loft insulation.Warehouse. | The EN 812 |
Safety helmet – lightweight | In recent years, lightweight helmets have become more popular. Being light, there is less material in them, so they are useful when there is a very low risk of anything falling on the head, such as in low-rise construction, utilities and highway maintenance. For someone working on the side of the roadway, or telephone or electrical engineers inspecting a cabinet, or a worker lifting a duct cover in the road, there is no actual danger of anything falling, but a helmet is needed in case a stone or another loose object flies up and hits their head. | Many applications include helmet attachments, and these often bring different performance characteristics from the “stand alone” item to be attached. An example of this might be earmuffs, whereby a headband version and a helmet-attachment version are offered. The different mountings result in differing noise attenuation performance. These are generally covered by the standard for the attachment type, e.g. hearing, eyewear etc. | Low-rise construction.Highway maintenance.Utilities.Warehouse. | The EN 397 lightweight |
Safety helmet – standard | This will be suitable if a falling object could hit the head, and is the most common type of helmet used in the workplace. | As above. | Construction.Manufacturing.External telecoms. | The EN 397 standard |
Safety helmet – Industrial | The more traditional model usually weighs around 400g to 500g with a robust shell of uniform thickness. This is ideal for applications such as workers excavating foundations in a hole, where there is a chance that something may fall on them from the side as well as the top and hit them on the head. | As above. | Construction.Manufacturing.External telecoms. | The EN 397 industrial |
Climbing helmet, also known as mountaineering helmet | This type of helmet has become popular with scaffolders to protect them from hazards such as swinging pieces of tube. | They also have a secure chinstrap, which will keep the helmet on the head should the wearer fall from height. | Rigging.High-rise construction.Building sites.Tower climbing.Energy and networks sites. | The EN 12492 These can also meet the EN 397 impact protection requirements, in some cases having extra padding for side-impact loads. |
High-performance industrial safety helmet | This is intended for use on sites where objects and debris are likely to fall, such as in mining and quarrying. | Safety visors and ear defenders. | High-rise construction.Mining.Demolition.Heavy construction.Tunnelling.Refinery, oil and gas.Offshore / Marine. | The EN 14052 |
Anti-static | For use in potentially explosive environments. | As above. | Demolition.Mining. | The EN13463-1 |
Motorcycle helmet | For use on British roads by motorcyclists and moped riders. | Goggles or visor. | Couriers.Delivery riders. | British Standard BS 6658:1985 and carry the BSI Kitemark |
EN 397 is the British and European standard that specifies physical and performance requirements (including testing) for industrial safety helmets.
It comprises of mandatory and optional tests: Mandatory Tests:
- Shock Absorption Test – The 5kg rounded striker is dropped on the crown of the helmet from 1m. The force transmitted to the head form cannot exceed 5000N (5kN).
- Resistance to Penetration Test – 3kg pointed striker dropped on the crown region, striker not allowed to contact the head form.
- Resistance to Flame Test – When exposed to a flame for 10 seconds and then removed, the shell must not set alight or self-extinguish within 5 seconds.
- Markings – Every helmet which complies to the standard must have the following information moulded or impressed into the shell somewhere visible:
– Number of the European Standard (in this case EN 397).
– Name or identification mark of the manufacturer.
– Year & quarter of manufacture (date stamp).
– Type of helmet (manufacturer’s designation): this should be marked on both the shell & harness.
– Size or size range (in cm), marked on both the helmet & harness.
– Shell material abbreviation (e.g. ABS, HDPE).
EN 12492 shock absorbance tests involve extra impacts at the front, side and rear of the helmet using 5kg flat and hemispherical strikers, each weighing 5kg. The transmitted force through the head form cannot exceed 10kN. The penetration test is similar to that for EN 397 but the strike test is applied to a bigger area of the helmet.
Impact tests on the crown of the helmet under EN 14052 use a 5kg mass dropped from about 2m, or 1m for off-crown impacts. For penetration, a 1kg blade is dropped onto the helmet from 2.5m (crown impacts) or 2m (off-crown impacts) and no contact with the head form is permitted.
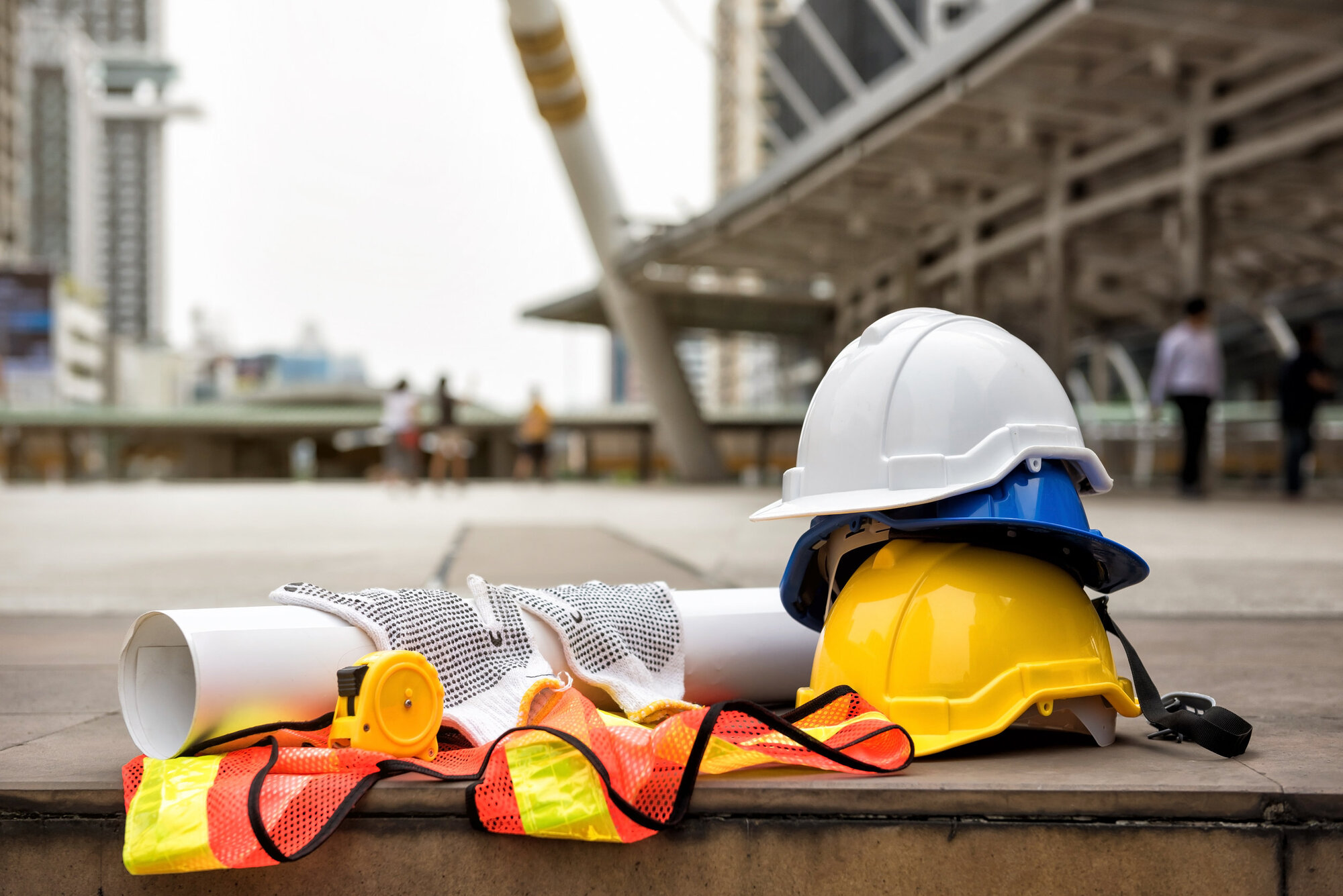
Safety helmet colours from January 2017
Construction sites and UK Highways should adhere to the following colour scheme on all new (and existing, where practicable) sites:
- White – For site managers, competent operatives and vehicle marshals (distinguished by the wearing of a different coloured high-visibility vest).
- Black – For site supervisors.
- Orange – For slingers and signallers.
- Blue – For all other site visitors.
Network Rail’s PPE standard requires only white and blue safety helmets to be used on site. Workers with additional responsibilities, such as a trained first aider or fire marshal, will be denoted by the use of stickers. On smaller sites a safety helmet colour standard may be impractical; in these cases, it is advised that a default colour of white is used as a general current practice.
The colours before January 2017 were:
- White – For managers, foremen, engineers or supervisors.
- Green – For safety inspectors, new or probationary workers.
- Yellow – For general labourers or earth-moving operators.
- Brown – For those involved in high-heat applications such as welders.
- Blue – For carpenters, electricians and other technical operators.
- Orange – For road crews.
- Grey – For site visitors.
The above colour safety helmets may still be being used on some long-term construction sites where work began before the 2017 changes, although change to the 2017 scheme is recommended where practicable. The ‘traditional’ yellow safety helmet is missing from the list of colours from January 2017.
The reason for the colour changes is to apply consistency across all industries. This is because there is such a range of different approaches to safety helmet colours, with sites and contractors having their own, often conflicting, approaches documented in their PPE standards. These inconsistencies are confusing and potentially dangerous.
This 2017 standard aims to make site visitors and other non-team members easily identifiable. All other roles (such as vehicle marshal) are now identifiable through the use of coloured high-visibility vests. Reflective markings and role-specific decals are permissible. All safety helmets are required to meet the requirements of British Standard EN 397.
Helmet life
Helmets are intended to provide an in-use lifespan of up to 5 years from date of first use or removal from storage. It should be noted that mobile workers who keep their helmet on the rear parcel shelf of their vehicles in direct sunlight should be aware that this constitutes use (the sunlight causes progressive brittleness). If the helmet is used in an aggressive environment or incurs excessive wear and tear then the lifespan will be shortened.
Employers should determine what sort of lifespan is appropriate for the different applications across all work environments, and ensure that a suitable replacement policy is published and applied. In the event that a helmet survives an instance of impact from a falling object, the helmet should be replaced immediately, as it may have been weakened without any faults being visible.
Safety helmet user’s checklist
Below are some of the things you should check before relying on your head protection. This is not an exhaustive list.
- Have the hazards present in the environment been reduced, isolated and controlled as far as reasonably practicable?
- Is the head protection suitable for the task you are going to undertake? For example, if the employee will be bending forward, ensure there is a chinstrap or ratchet wheel to keep it in place, and check if there is sufficient electrical protection.
- Is the safety helmet free from damage such as cracks, scratches or impact strikes?
- Is the safety helmet free from chemicals and solvent-based paint?
- Has the helmet been stored correctly?
- Has the helmet been used to carry items in it?
- Does the helmet fit properly?
- Has the helmet been adjusted to ensure it stays on your head?
- Have any accessories to the helmet been adjusted?
- Do you know what the colour of the other hard hats being worn on site mean?
The dangers of not wearing a safety helmet
The results of not wearing safety helmets or wearing those that have exceeded their service life can be devastating.
Head injuries can result in short- and long-term effects such as:
- Concussions.
- Memory loss.
- Ongoing physical symptoms such as headaches, visual difficulties, light sensitivity.
- Ongoing emotional and cognitive symptoms such as sleep difficulties, depression and anxiety, aggression and other personality changes.
- Brain damage.
- Degenerative brain diseases such as Alzheimer’s.
- Paralysis.
- Fatality.
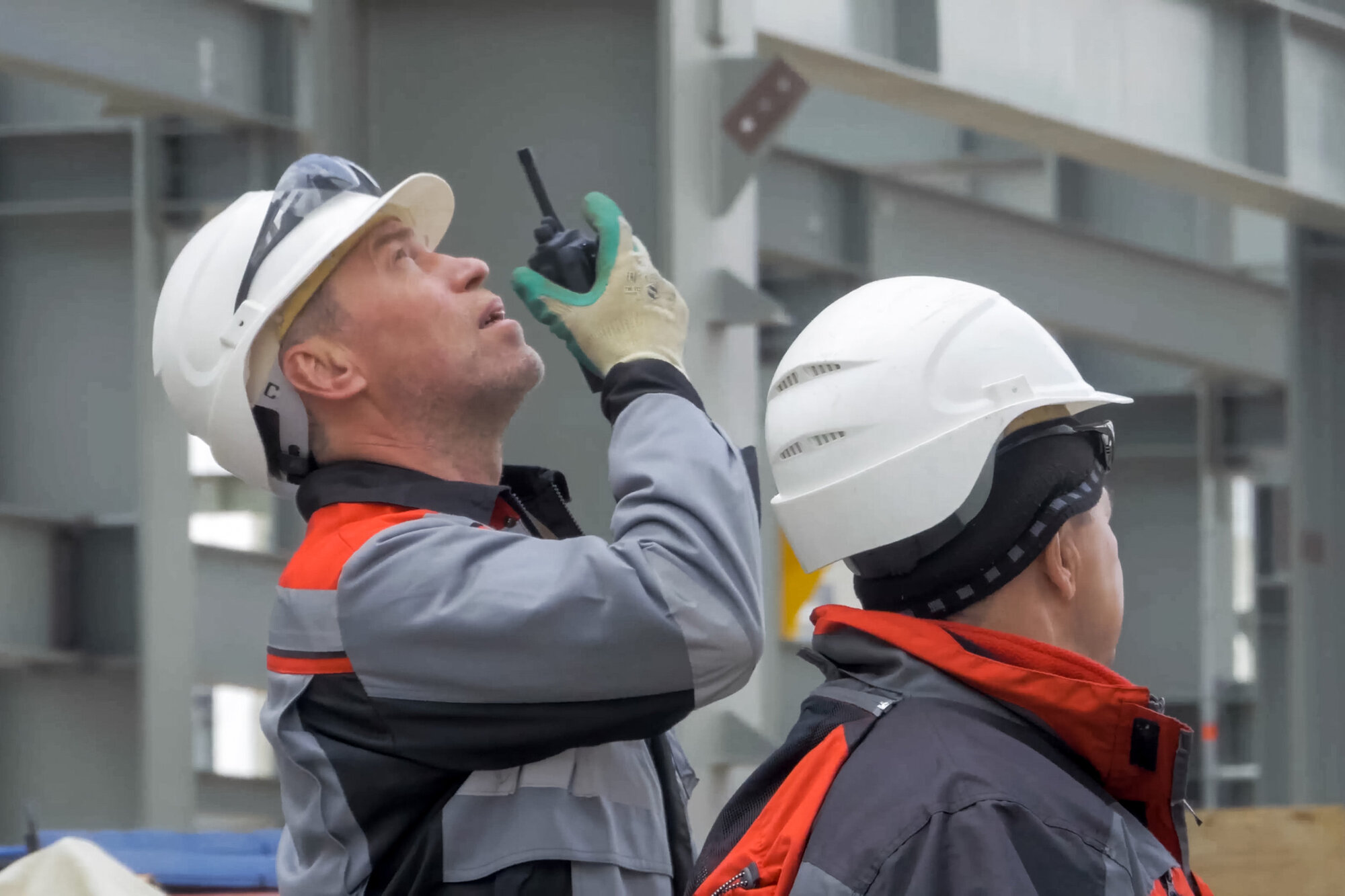
The law
The main laws that apply to the use of safety helmets are:
- The Personal Protective Equipment at Work Regulations 1992 (as amended 2013 to apply to the provision and use of hard hats on construction sites).
- The Personal Protective Equipment Regulations 2002.
The Motor Cycles (Wearing of Helmets) Regulations 1973 (as amended 1998) applies in addition to the above to those using a motorcycle at work.
These laws are enforced by the Health and Safety Executive (HSE).
Employers must, by law, provide adequate and suitable head protection and ensure it is worn if there is a risk of injury to the head, which will be the case on many work sites. Regulation 4 of the 1992 Act states:
“Every employer shall ensure that suitable personal protective equipment is provided to his employees who may be exposed to a risk to their health or safety while at work except where and to the extent that such risk has been adequately controlled by other means which are equally or more effective.”
Section 9 of the Act makes it clear that under no circumstances should there be any charge to an employee requiring PPE equipment, and that the employer should provide all the necessary equipment for free. The equipment must also be regularly checked for damage and effectiveness, with special attention being paid to specific requirements, such as the use-by dates of safety helmets.
There is an exemption for Sikhs who wear a turban, but not for Sikhs who do not wear turbans or for any other religious groups. Section 11(1) of the Employment Act 1989 as amended by s.6 of the Deregulation Act 2015 exempts turban-wearing Sikhs from any legal requirement to wear a safety helmet in a workplace, including a construction site.
Employees’ duties in law are:
- Employees are required to use PPE including safety helmets in accordance with the employer’s instructions, based on the manufacturer’s instructions for use.
- Employees must also report any defects or loss of PPE.
Safety standards and Brexit
Following Brexit, safety helmets by law should be now be UKCA (UK Conformity Assessment) marked; this is the new UK product marking that will be required for certain products being placed on the market in Great Britain (England, Wales and Scotland).
It covers most products that previously required the CE mark. The CE mark is still required if PPE is offered for sale within the European Union including Northern Ireland; this is an EU legal requirement for any item of personal protective equipment including safety helmets.