In this article
What is HAVS?
Hand-arm vibration syndrome (HAVS) is a medical condition that is caused by prolonged exposure to vibration, usually from power tools and machinery. HAVS affects the nerves, blood vessels, muscles and joints of the hand and arm and can cause numbness, permanent changes in the sensation of the fingers and muscle weakness.
HAVS is a serious workplace health issue in the UK, particularly in industries such as construction, manufacturing and forestry. It is most common in people who have been working with power tools for more than ten years. Occasional use of power tools and equipment is unlikely to lead to HAVS.
HAVS can cause significant pain, injury and ill health and can even result in disability. Even if you regularly use power tools, HAVS is completely preventable. However, once the nerves, blood vessels and joints are damaged, the damage is permanent. It is estimated that 2 million people in the UK are at risk of HAVS.
Awareness of hand-arm vibration syndrome has been growing since power tools were first introduced but the Control of Vibration at Work Regulations were not introduced until 2005. It then took another 15 years for HAVS to be added to the Industrial Injuries Disablement Benefit (IIDB) system in 2020. This gives individuals access to disability benefits because of an accident, injury or illness obtained at work.
Even with more awareness of the risks of prolonged exposure to vibration and better safety features being in place, HAVS is still a big issue in the UK. In 2023, the Health and Safety Executive (HSE) reported 215 new cases of hand-arm vibration syndrome (HAVS). These statistics only account for HAVS injuries severe enough for a referral to IIDB, so the real statistics are likely significantly higher.
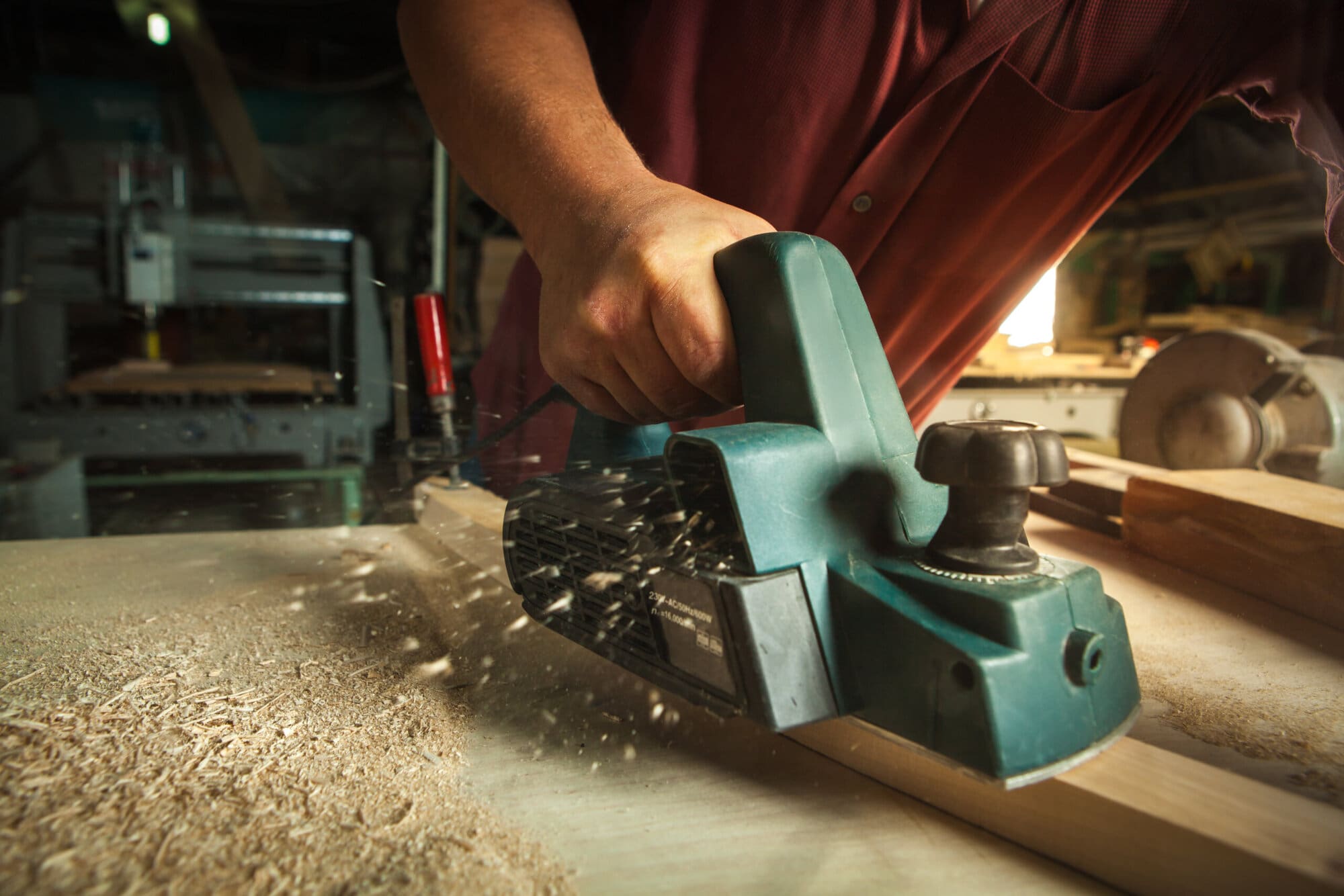
Symptoms of HAVS
There are several different symptoms associated with Hand-arm vibration syndrome (HAVS). The symptoms usually develop slowly over time and affect the nerves, blood vessels, muscles and joints in the hands and arms. The severity of symptoms usually increases with continued exposure to power tools.
Early symptoms:
- Numbness and tingling in the fingers
- Loss of feelings and reduced touch sensitivity.
- Blanching (pale or white fingers in the cold) similar to Raynaud’s disease.
- Loss of grip strength
- Hands feeling weak after using vibrating tools
- Mild finger stiffness.
Once these symptoms begin to develop, this means permanent damage has already been done. If the individual continues to work with vibrating tools, their symptoms are likely to progress and become more severe. For example, the numbness and tingling may become permanent and can lead to more serious muscle weakening and wastage. While symptoms can be managed, the underlying damage to the vascular, nervous and musculoskeletal systems has already been done.
Some people develop symptoms of HAVS after years of using power tools, while others develop symptoms much more quickly. Several factors influence how quickly HAVS develops. The intensity of vibration the person is exposed to plays a significant role, with higher intensity leading to faster damage. The duration of exposure is also relevant, as using power tools daily increases the risk. Additionally, the way a tool is gripped matters and holding a power tool too tightly can worsen symptoms.
For people who regularly work outside or in cold environments, this can worsen circulation problems as the cold can constrict blood vessels. Individual health factors also contribute, such as smoking, which narrows arteries and restricts blood flow. Other circulation issues, as well as medications like beta-blockers, decongestants and certain migraine treatments, may also impact circulation to the fingers and hands and increase the likelihood of developing HAVS.
Tools and Machinery Linked to HAVS
HAVS is primarily caused by prolonged use of handheld or hand-guided vibrating tools and machinery. Power tools vibrate and, over time, can damage nerves, blood vessels and joints in the hands and arms. The most common tools and machinery associated with HAVS are those used in construction, demolition, carpentry, metalwork, manufacturing, gardening and landscaping. Examples include:
- Jackhammers (Pneumatic and hydraulic breakers)
- Concrete vibrators
- Compactors (wacker plates, rammers and vibratory rollers)
- Impact wrenches
- Drills (rotary and hammer drills)
- Chainsaws
- Hand sanders (orbital and belt sanders)
- Jigsaws and reciprocating saws
- Planers and routers
- Angle grinders
- Needle scalers
- Bench and hand-held polishers/buffers
- Riveting guns
- Hedge trimmers
- Brush cutters and strimmers
- Hand-guided lawnmowers
The vibrations from these types of tools can very small, repetitive injuries to the small nerves and blood vessels in the fingers which can build up over time and result in permanent damage.
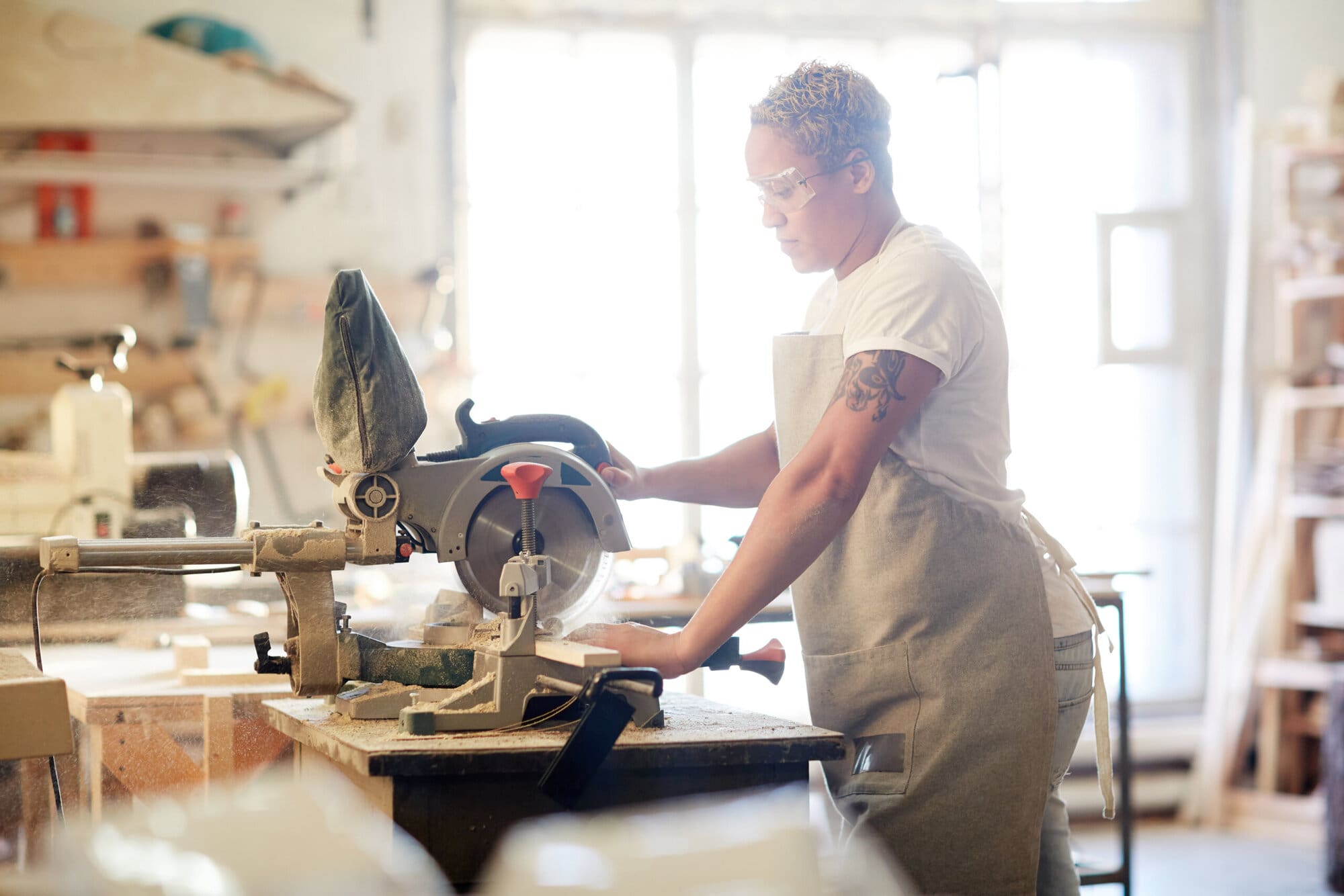
Reducing the Risk of HAVS
It is essential to put practices into place to reduce the risk of HAVS, especially for people who use vibrating tools regularly. Risk reduction strategies are designed to reduce exposure to vibrations and minimise the likelihood of developing HAVS but may not completely eliminate the risk. This is because while they make power tools safer to use, they still allow some level of vibration exposure.
Some ways to reduce risks are:
Performing risk assessments
Risk assessments can help to identify any tasks and activities could that expose workers to harmful vibrations. A risk assessment can also identify the most high-risk activities and recommend ways to reduce or eliminate the risks.
Choosing tools with low-vibration exposure
Only choosinglow-vibration tools can help to reduce the risk of HAVS. Workplaces should specify a maximum vibration level in their policy and stick to this when purchasing power tools and equipment. If you aren’t sure about the vibration level of some of your equipment, manufacturers can provide vibration ratings. It is also recommended to check how efficient the tool is. A power tool with a low vibration setting that takes much longer to do the same job can actually be more harmful and can result in the same or higher exposure to harmful vibrations.
Thinking about the power tool’s features and design
If you regularly use power tools choose tools that are well-balanced and designed for reduced vibration. When choosing tools and equipment, consider:
- How heavy is it?
- Is it efficient?
- Is the handle easy to grip and comfortable to hold?How much force/ strength is needed to hold the tool?
- How easy it is to use?
Ensuring the tool is suitable for the task
When using power tools, it is essential to ensure it is:
- Suitable for the task you are doing.
- Suitable for the conditions it will be used in (e.g., cold weather or rain).
- Used only for tasks it was intended for (consult the manufacturer’s guide if you are unsure).
- Designed to reduce the impact of vibrations and the risk of HAVS.
Ensuring tools are regularly cleaned and maintained
Properly cleaning and maintaining power equipment can help to ensure power tools are working effectively and the vibration performance is functioning as it should be. Tools should be kept sharp (where applicable), as dull or damaged tools typically create more vibration. Workplaces must regularly check for worn-out parts and replace them.
Limiting exposure time
Any workers handling vibrating tools must take regular breaks. Workplaces should implement the five-minute rule – for every 30 minutes of tool use, workers should take a five-minute break, as this can help to reduce the risk of long-term damage. It can also be helpful to rotate tasks so workers can avoid using vibrating tools for long, continuous periods. Implementing a job rotation policy can ensure tasks requiring power tools are shared among workers.
Staff training
Power tools should only be used by workers who are properly trained. It is important that workers are educated on the risks of HAVS and any prevention methods. Workers should also be trained on safe handling techniques and safe exposure limits.
Improving grip and handling
Power tools should be held loosely (while still ensuring the grip is strong enough that the tool won’t slip or fall). A firm grip increases vibration impact so it is important to avoid excessive force. Let the tool do the work rather than forcing it and, if possible, use tools with ergonomic handles for better control and comfort.
Using protective equipment
Anti-vibration gloves can help to reduce some of the impact of vibrations, although wearing them doesn’t completely prevent HAVS. Using power tools with padded grips and shock absorbers can also help to reduce the impact of the vibrations. Improving workplace design can also be beneficial. Workstations can be designed to reduce the load on employee’s hands, wrists and arms when they are using power tools.
Avoiding cold, damp conditions
Being exposed to the cold and damp can restrict blood flow and increase the likelihood of HAVS. It is important that anyone who works with power tools keeps their hands warm and dry. For example, if you are using power tools in cold weather, wear warmer clothing and gloves to prevent the cold from worsening the impact of the vibrations on your blood vessels.
Monitoring and controlling vibration exposure
All companies and individuals need to follow the Exposure Action Value (EAV) and Exposure Limit Value (ELV) under the Control of Vibration at Work Regulations 2005:
- EAV: 2.5 m/s² A (8) → Action must be taken.
- ELV: 5.0 m/s² A (8) → Legal limit (must NOT be exceeded).
Checking the health of employees
Employers should provide regular health checks for workers using vibrating tools and monitor them for any emerging symptoms. All workers should be aware of the symptoms of HAVS and be encouraged to report any early symptoms, such as numbness, tingling or white fingers. Workers should seek medical advice as soon as possible if symptoms appear as early intervention can prevent permanent damage.
HAVS Prevention Strategies
Prevention strategies aim to completely stop HAVS from occurring by removing or controlling exposure to harmful vibrations. These strategies focus on completely eliminating or fully controlling vibration exposure, so HAVS cannot develop. Preventing HAVS requires a combination of tool selection, workplace practices and personal protective measures.
Effective prevention strategies include:
Changing work processes to eliminate vibrating tools
Workplaces should look for alternative working methods that would eliminate the use of power tools. Redesigning work processes can help workers avoid tasks that require vibrating tools, for example, if laying concrete, companies can utilise pre-cast concrete that has existing holes to eliminate the need for a drill. Additionally, using pre-cut materials rather than requiring workers to cut them themselves can eliminate the need for power tools.
Automating tasks
Where possible, workplaces should automate tasks to protect workers from HAVS. For example, they could use robotic arms, CNC machines or remote-controlled equipment instead of manual tools. They could also opt for machine-assisted cutting, drilling and grinding rather than handheld work.
Job design changes
Redesigning jobs so workers don’t need to use vibrating tools and shifting to processes that don’t require handheld vibration exposure can help prevent HAVS. Workplaces can also choose alternative materials, where possible, that don’t require cutting, grinding, excessive shaping or other activities that would require the use of power tools. Alternatively, they can focus on changing manufacturing and construction methods to eliminate vibration exposure.
Modify the work environment
Modifying the work environment and changing how tasks are performed can reduce exposure to vibrations. For example, workplaces can introduce clamping or support systems to eliminate handheld vibration exposure or use automation, remote controls or robotics to replace manual work. Workplaces can also implement anti-vibration engineering solutions, for example, by installing vibration isolation systems in workstations and vehicles and using mechanical dampening methods to eliminate excessive vibrations.
Prevention is always better than risk reduction, but in many industries, eliminating vibration exposure is not always practical. To achieve the safest possible practices, many workplaces focus on a combination of prevention (where possible) and risk reduction (where necessary).
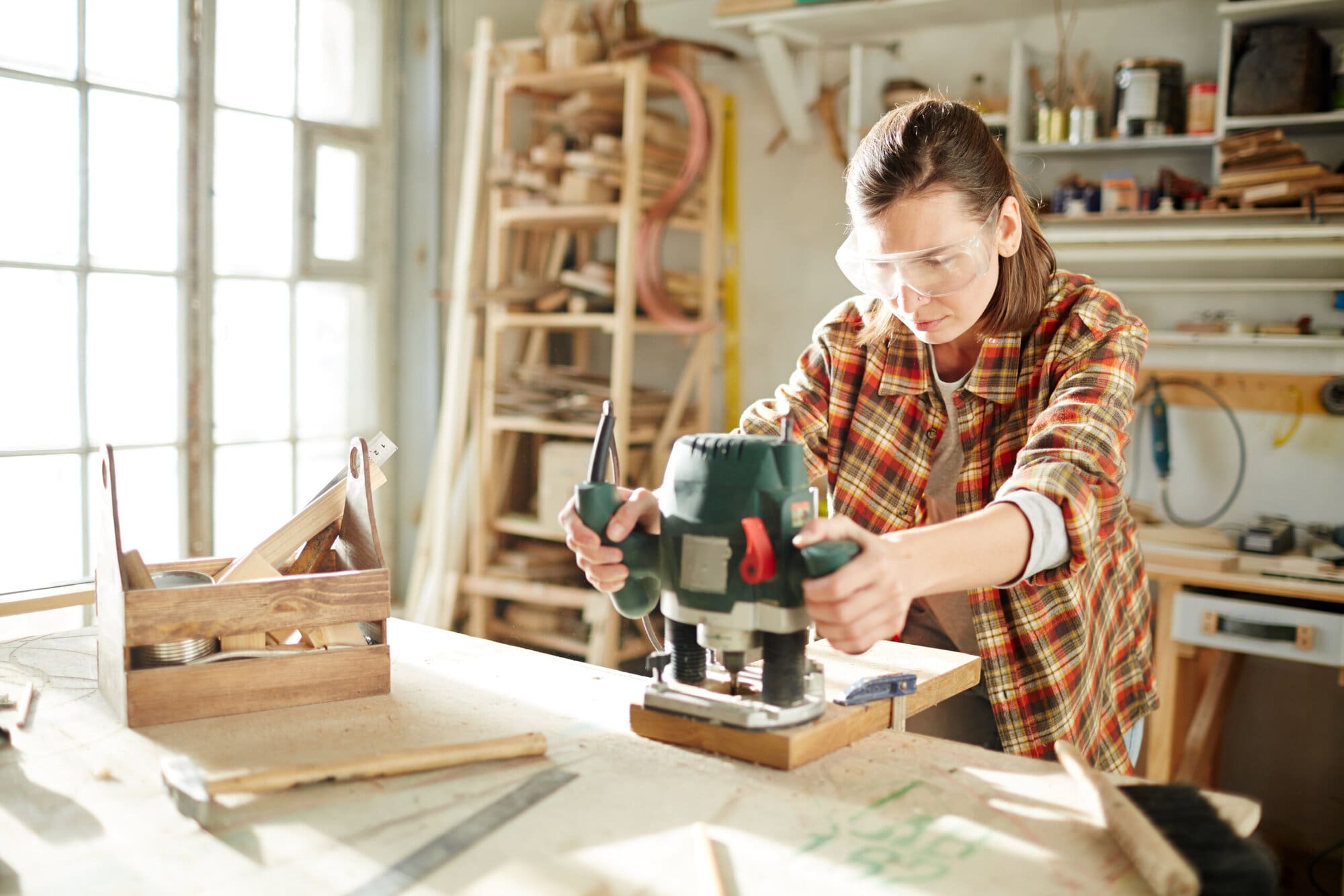
HAVS Regulations
In the UK, HAVS and the use of power tools and equipment are regulated under several laws designed to protect workers from excessive vibration exposure and other work-related hazards and risks. If you don’t comply with these regulations you may receive a fine, legal action or the business may be closed.
Control of Vibration at Work Regulations 2005
The Control of Vibration at Work Regulations is the main law covering HAVS in the UK. It sets the legal limits for daily vibration exposure and requires employers to assess, control and monitor vibration risks. Under these regulations, employers must:
- Measure the vibration levels of tools and equipment and ensure workers do not exceed limits.
- Assess worker exposure and the overall risk.
- Never exceed the exposure limit value (ELV)
- Take action if exposure reaches the limit.
- Provide health surveillance.
- Train employees in reducing vibration exposure.
Health and Safety at Work etc. Act 1974
The Health and Safety at Work etc. Act is the main law covering general health and safety in the workplace. It applies to all workplace hazards, including vibration exposure and covers risk assessments. The Act states that it is the responsibility of the employer to provide safe working conditions.
Management of Health and Safety at Work Regulations 1999
These regulations state that employers are required to perform risk assessments to identify and evaluate the risks of being exposed to vibrations. Employers are then required to take preventative action to reduce or eliminate exposure. They must also regularly monitor, review and update the risk assessment, based on new tools and processes.
Provision and Use of Work Equipment Regulations (PUWER) 1998
PUWER applies to all work equipment that is used by employees, including handheld power tools, machinery and vibrating equipment. It requires employers to ensure that all equipment is:
- Safe to use: Tools must be properly maintained and not pose unnecessary risks.
- Suitable for the task: Employers must choose the right tool for the job to minimise vibration exposure.
- Properly maintained: Regular checks and servicing must be carried out to prevent excessive vibration.
- Used by trained workers: Employees must be trained in safe handling techniques to reduce HAVS risk.
- Fitted with safety measures: Equipment must include vibration-dampening features where possible.
Reporting of Injuries, Diseases and Dangerous Occurrences Regulations (RIDDOR) 2013
Under RIDDOR, notify the HSE when a worker is diagnosed with HAVS. Employers must also investigate what happened and take action to prevent further cases. Failure to report HAVS cases is a criminal offence under RIDDOR.