In this Health and Safety Guide Warehouse Workers
The main function of a warehouse is to store products or goods before moving them to another location. Warehouses come in many shapes and sizes including those used for storage of raw materials, components or semi-finished products and finished products, and intermediate warehouses for distribution, etc. Warehouse buildings can be classified as open-air warehouses, industrial buildings, basements, depots, cold storage chambers, clad-rack warehouses etc.
An average of around 215,000 people are employed by warehouse and storage facilities in the UK, and the increase in online shopping during and post the COVID pandemic has increased the demand for warehouse staff. Recent data from the Office for National Statistics (ONS) has revealed that demand for warehouse workers rose by 43.2% at the end of 2022 when compared with pre-pandemic levels.
Warehousing and storage facilities in the UK cover a wide spectrum of sectors including, but not limited to:
- Chemical and pharmaceutical
- Building and construction
- Textiles and clothing
- Electronics
- Food and drink
- Other sectors such as furniture and homewares
Working in a warehouse is filled with potential workplace health and safety issues that need to be overcome on a daily basis, so to keep employees and others safe from danger or harm, warehouse workers will need to maintain their own safety, as well as the safety of the area and the people around them.
What is the Role of a Warehouse Worker?
Warehousing and storage facilities serve a great variety of industry sectors, as we have seen; however, irrespective of the sector a warehouse is serving, they tend to employ very similar roles, although specific role titles and duties may vary between individual settings.
Depending on where, and the type of work that they are doing, the role of employees and management in warehousing and storage facilities may involve, but is not limited to:
- Warehouse operative
- Warehouse picker
- Warehouse order packer
- Warehouse order dispatcher
- Warehouse manager
- Forklift operator/
- Industrial cleaner
- Support / Administrators – These roles often include, but are not limited to, customer support, shipping, sales, marketing, finance, HR, buyers, maintenance/facilities, senior management, security
Depending upon specific roles, their main tasks are varied and may include, but are not limited to:
- Taking in deliveries
- Assisting with the loading and unloading of vehicles using manual handling techniques
- Moving and storing products in the correct warehouse area
- Sorting and placing materials or items onto racks and shelves
- Processing, picking and packing orders in a timely manner, working to targets
- Ensuring all products are in good condition and free from damage, and reporting any discrepancies
- Cleaning and maintaining warehouse equipment to set standards
- Moving pallets and/or pallet-packed materials around the warehouse or storage facility using a forklift truck, checking loads are secure
- Performing equipment checks and basic forklift truck maintenance
- Using lifting equipment to move stock around the warehouse and/or onto or from storage racks
- Checking stock levels
- Making sure items are stored correctly
- Packing, wrapping and loading items to be dispatched
- Performing warehouse inventory controls via scanner and/or through a computer< /li>
- Stock counting and location checks
- Using computer systems to update necessary records and reports
- Managing the day-to-day operations of the warehouse
The above lists are not exhaustive and there is often a crossover of duties between roles. Generic to all roles is ensuring compliance with all relevant policies and procedures, and legal and regulatory requirements including health and safety. All warehouse staff may work both alone and also closely alongside other staff as part of a team. Whatever the environment they work in, warehouse and storage facilities staff and management will be responsible for ensuring the safety of their work and any equipment to protect the safety of themselves and other people.
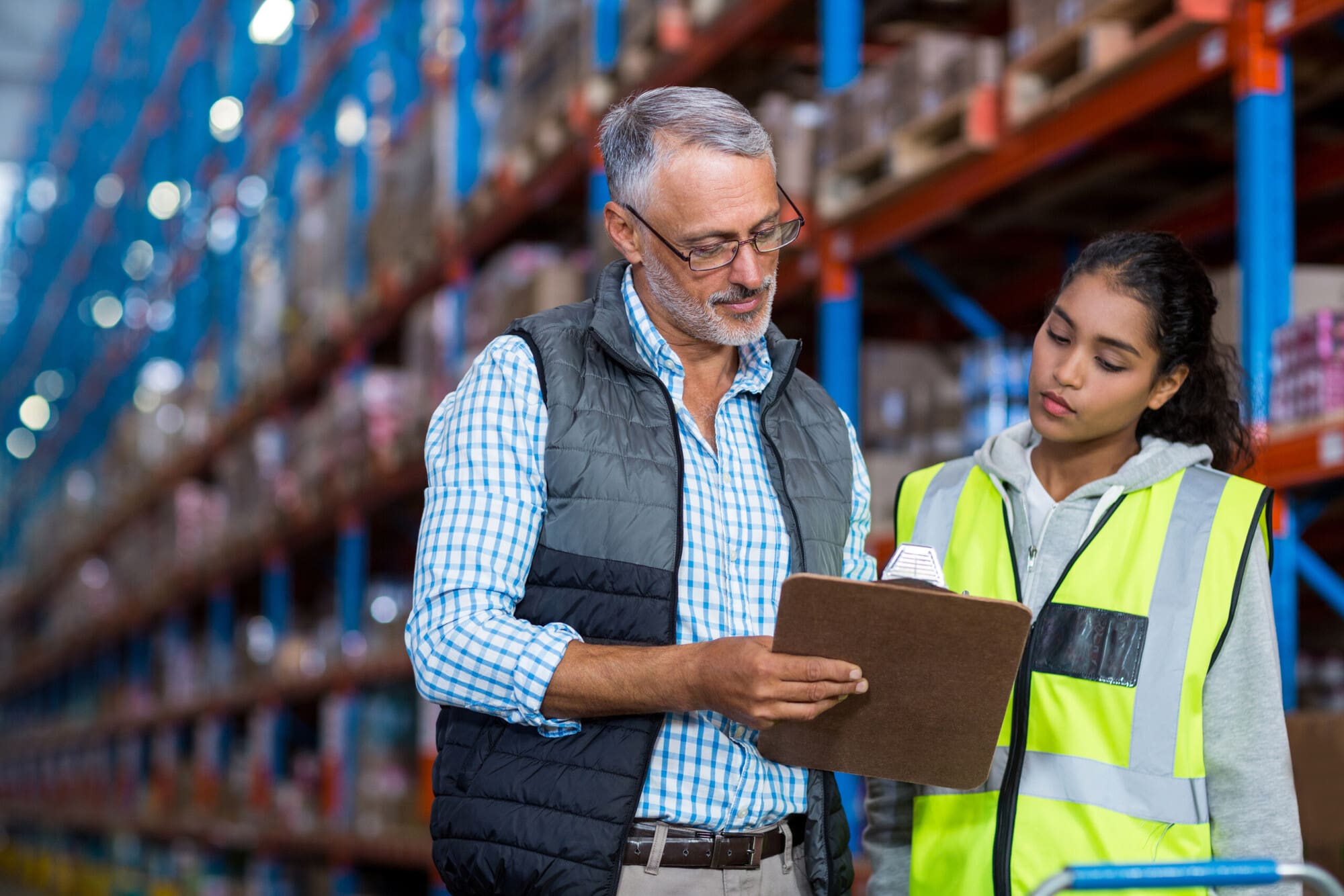
What are the Main Health and Safety Risks Warehouse Workers Can Encounter?
Warehouses or other large storage buildings pose many potential health and safety hazards and associated risks. The HSE (Health and Safety Executive) stopped reporting statistics for this sector in 2011; however, the last reported yearly figures show that there were 157 major injuries to workers in warehousing and storage facilities.
Slips, trips and falls are one of the top three causes of non-fatal work injuries involving days away from work. Each year they cause thousands of preventable injuries, and they can cause various injuries such as bruises, sprains, scrapes, broken bones and head traumas. Around 1,000 of these injuries involve someone fracturing bones or dislocating joints.
Key aspects of slips and trips include:
- Uneven surfaces
- Obstacles
- Trailing cables
- Wet or slippery surfaces
- Changes in level
Keep work area floors clean, orderly and dry, and keep surfaces free of hazards such as sharp objects, loose boards, corrosions, leaks, spills, snow and ice. Signpost any slippery areas and make sure footwear with a good grip is worn. We will look at PPE later in this guide. Warehouses should ensure that there is a good housekeeping regime to guarantee passageways are kept clear of clutter and obstacles and other trip hazards. This requires an effective cleaning schedule, adequate storage facilities and sufficient rubbish bins.
It is not unusual for warehouse workers to have to work above floor level, for instance stacking goods on high shelving, removing goods from high places, using ladders or mechanical pickers, or working on elevated walkways or flooring. Falls frequently occur while warehouse workers are over-reaching, attempting to access items, balancing on uneven surfaces, or working on mezzanines, elevated platforms, or loading bays. When working from a height, thorough and regular workplace inspections should be carried out, guardrail and fall arrest systems should be put in place and training should be provided. In particular, steps must be taken to ensure workers do not stand on forklift truck forks, or pallets mounted on forks, to access heights. This is a regular cause of fatal injury in warehouse and storage facilities.
Stock falling from racking or racking collapsing can cause serious injury and even death, so racking should be visually inspected at least once a month by a technically competent person. Load capacities should be obeyed and a damage log kept. Areas and specific activities in the warehouse where there is a risk of an object falling and striking someone should be clearly indicated to prevent entry by unauthorised persons.
Workers in warehouses can be struck by pedestrian operated pallet trucks, racks, trolleys, roller cages etc. Designated routes should be kept away from other workers where possible, and the person pushing/pulling the apparatus should have good visibility.
Manual handling injuries have a major impact on all workplaces and sectors, costing the economy hundreds of millions every year. Manual handling encompasses a wide range of actions including lifting, lowering, pulling, pushing, and carrying awkward and heavy objects; the risks are endless for warehouse workers who may experience manual handling injuries such as:
- Back injuries
- Hernias
- Musculoskeletal disorders (MSDs) such as shoulder strain
- Repetitive strain injury (RSI) such as wrist strain
- Soft-tissue injuries to the wrists, arms, shoulders, legs or neck
- Long-term pain in the arms, legs or joints
Overexertion is something that is easily done in any environment and can be difficult to avoid. Overexertion is usually caused by someone trying to lift or move something heavier than their capabilities or doing so incorrectly. Manual handling tasks should be avoided wherever possible. Where it isn’t possible to avoid handling a load, suitable safety measures should be introduced such as staff having the use of trollies or lifting equipment to move heavy items, and all staff should receive manual handling training to prevent and avoid injury.
Forklift trucks (FLTs) are widely used in warehouses as they can eliminate some or all manual handling. However, FLTs are dangerous vehicles and can cause serious life-changing injuries and fatalities. Consequently, action should be taken to ensure the safe use of FLTs in warehouses.
The racking in aisles must be organised to allow for safe access to goods and movement of FLTs. The aisles should be sufficiently wide, with adequate clearance room overhead. Staff should follow good housekeeping practices and ensure the aisles are kept free of obstructions. Pedestrians and vehicles must be able to circulate in a safe manner.
The areas in which FLTs operate should, if possible, be separated from the areas where pedestrians are likely to be. More than half of FLT accidents that seriously injure workers are caused to workers on foot. It is therefore essential to give pedestrians a warning when a truck is getting too close. There are now high-powered LEDs to cast bright bold red lines on the floor behind and to the side of a truck. These show those working in the area of the truck the distance that they must maintain to continue working safely.
Injuries that can be caused by FLT vehicles can range from minor to severe, with the root cause predominantly being improper use or insufficient training. These types of vehicles should only be operated by those with valid certifications and training, such as a forklift licence training course. Employers should enforce the use of seatbelts on forklift trucks and other vehicles, as around a quarter of all workplace transport accidents involve forklift trucks, with drivers being crushed after falling from a forklift truck.
Vehicle movement in and around warehouses requires careful and constant management to prevent accidents. This requires workplace traffic routes that allow pedestrians and vehicles to circulate safely. Where vehicles and pedestrians use the same traffic route, there should be adequate separation between them and, if possible, complete separation of vehicles and pedestrians. Nearly a quarter of all deaths involving vehicles at work occur during vehicle reversing. Warehouses need to be designed and operated to prevent such accidents. If possible, the need for reversing should be eliminated or, if this is not possible, minimised. Pedestrians should be kept out of areas where vehicles reverse.
Loading and unloading vehicles can be dangerous and needs safe systems of work to be in place. Goods should be securely packed and arranged so that they are safe for transport and unloading, shrink-wrapped on pallets, or in roller cages. Fall protection measures may be necessary for unloading goods or materials if there is a risk of injury from a fall.
In many warehouses, equipment such as forklift trucks, conveyors and compressors could give rise to potentially hazardous levels of noise. Industrial noise pollution caused by machinery and vehicles can have a detrimental effect on people’s mental and physical well-being. Prolonged exposure to noise can lead to:
- Stress and anxiety
- Productivity loss
- Fatigue
- Communication issues
- Tinnitus
- Cardiovascular diseases
- Deafness
- Nervous disorders
- Neurological problems
- Headaches
Warehouse workers participating in noise-heavy activities must wear protective equipment at all times.
In some warehouses there will be additional activities that will require their own precautions. These activities include storage of products that are classified as hazardous and that can cause harm to workers, and products that are flammable. Procedures need to be in place to prevent exposure to hazardous chemicals and to control the risk of damage to the environment caused by spillages. Handwashing should be second nature by now, but warehouse workers using any chemical substances must fully decontaminate themselves after using or coming into contact with hazardous materials. Good ventilation also proves an essential safety measure to stop the build-up of toxic vapours. All chemicals must be treated with caution, and employers must provide sufficient personal protective equipment (PPE) for employees that are required to use any chemicals, and ensure that all staff are sufficiently trained in categorising and handling them, as well as trained in providing first aid to immediately treat any injuries suffered to minimise the harm.
Warehouses can have a lot of open space, and often contain flammable materials such as shrink-wrap plastic, used to wrap the pallets, which makes them more flammable, conditions under which fire can spread extremely rapidly, leading to damage to the warehouse, harm to people, and loss of valuable resources and operation time. When a fire starts in a building, it can happen very quickly. Burns and respiratory damage can be caused by flammable materials or electrical equipment igniting. Fire safety is a serious subject and precautions must be taken by all workplaces. These precautions include checking all power cords are in good condition and that power outlets are not overloaded.
It is also vital to ensure that emergency lighting is installed and that staff know where fire extinguishers are located, where their nearest fire exit is, and that emergency exits are clear at all times. Regular fire alarm testing should take place as well as regular fire evacuation tests.
Employers and management need to be able to confirm that:
- Firefighting equipment is in place
- Fire evacuation procedures are clearly displayed
- All staff are aware of the evacuation drill, including arrangements for any vulnerable adults
In order to remain effective, fire risk assessments must be kept up to date. It is recommended that the responsible person completes a fire risk assessment at least once a year, and must conduct a review whenever there is a significant change in the environment.
Cold stores have very specific risks associated with them, for example those that arise from workers accidentally being locked in, over-exposure to cold conditions, slips and falls owing to ice build-up, and accidental release of refrigerant, a chemical cooling agent used in refrigeration. Freezing injuries include frostnip, frostbite, frost burn or skin damage when in contact with cold surfaces. Avoiding contact with metal and plastic surfaces with bare skin can help prevent these injuries. When there is prolonged exposure to temperatures of -20̊C or below, exposure to bare skin should be avoided.
Non-freezing and chronic injuries may be less obvious, but are usually marked by prolonged numbness, pain, swelling and sensitivity to the cold, in the hands or feet. They occur when tissues remain cold for many hours but do not freeze, and are best prevented by ensuring that cold stores warehouse workers warm up thoroughly during breaks, and by keeping their body warm, but not too hot. They should also report these problems early so they can be addressed. Hypothermia, which is a drop in body temperature, is unlikely in occupational circumstances; however, be aware that cold hands and feet indicate a drop in body temperature which could lead to hypothermia.
Cold exposure can be a trigger for certain diseases and aggravate the symptoms of prevailing chronic diseases. Warehouse workers working in cold stores should be physically fit for work.
Medical conditions that are likely to be adversely affected by the low temperature include:
- Asthma or other respiratory conditions, as freezer air is very dry. It may not be necessary to exclude people from cold-store areas who suffer from allergic asthma which is not cold induced.
- Cardiovascular and circulatory conditions such as angina, Raynaud’s disease etc.
- Hand-arm vibration syndrome (HVS).
- Arthritis.
- Musculoskeletal diseases.
- Skin diseases.
- Metabolic disorders, for example thyroid, and also diabetes whether controlled by tablets or injections.
It is of prime importance in such cold environments that all significant hazards are identified, the risk assessed and appropriate control measures put in place.
Risk Assessments
Maintaining a safe work environment is important, particularly in the high-risk work environment faced by those working in warehouses and storage facilities. It is important that every hazard is met with elimination or, at the minimum, a control measure to mitigate any potential risk.
Management of Health and Safety at Work Regulations (1999), the minimum a business must do is:
- Identify what could cause injury or illness in your business (hazards)
- Decide how likely it is that someone could be harmed and how seriously (the risk)
- Take action to eliminate the hazard or, if this isn’t possible, control the risk
Risk assessment requires making a judgement on Risk Severity. Risk Severity = probability of risk materialising x impact of risk on, for example, a person or people, a business, a property etc.
Probability may be understood as:
- Low (Level 1) – a reasonably informed person would think it very unlikely this risk would materialise in the foreseeable future.
- Medium (Level 2) – a reasonably informed person would think there is a significant possibility this risk would materialise in the foreseeable future.
- High (Level 3) – a reasonably informed person would think there is a very significant or even likely possibility the risk would materialise in the foreseeable future.
Impact may be understood as:
- Low (Level 1) – any impact that is minimal, having regard to the importance of interests affected, impairment of function and duration. Typically, the impact is isolated and short-lived.
- Medium (Level 2) – any impact that is significant, having regard to the importance of interests affected, impairment of function and duration. Typically, the impact is limited to one function or group, but there is a material operational impact and the effects may continue.
- High (Level 3) – any impact that is severe, having regard to the importance of interests affected, impairment of function and duration. Typically, the impact impairs a critical function and/or has a systemic impact and the effects may be long-lasting or permanent.
Workers in warehouses and storage facilities must ensure an assessment has been made of any hazards, which covers:
- What the potential hazard is – the risk assessment should take into consideration, for example, the type of equipment used, the way in which it is used and the environment it is used in
- Who or what could be harmed by the hazard
- How the level of risk has been established
- The precautions taken to eliminate or control that risk
Managing risk is an ongoing process that is triggered when changes affect a warehouse worker’s work activities; changes such as, but not limited to:
- Changing work practices, procedures or the work environment
- Purchasing new or used equipment or using new substances
- Workforce changes
- Planning to improve efficiency or reduce costs
- New information about the workplace risks becomes available
Risk assessments should be recorded, and records regularly reviewed and updated whenever necessary. Should an accident occur, the Health and Safety Executive (HSE) will request copies of the risk assessments.
There are a number of laws and regulations that apply to health and safety in warehouses and storage facilities including, but not limited to:
Health and Safety at Work etc. Act 1974 (HASWA) – This is the primary legislation that all businesses must abide by.
This Act sets out the general duties which:
- Employers have towards their employees and the members of the public
- Employees have to one another
- Self-employed have towards themselves and others.
The Lifting Operations and Lifting Equipment Regulations 1998 (LOLER). LOLER was created to ensure that all lifting operations conducted in the workplace that use lifting equipment are safe. LOLER requires that lifting operations are planned by a competent person. It stipulates that lifting operations must be supervised in an appropriate manner and performed by an employee who is able to complete the task safely.
The Dangerous Substances and Explosive Atmospheres Regulations 2002 (DSEAR) state the legal requirements for managing the risk of fire, explosion or similar events arising from dangerous substances at the workplace.
It is a requirement of the Control of Substances Hazardous to Health Regulations (COSHH) for employers to assess all exposures to hazardous substances in the workplace and implement necessary control measures in order to protect their workers’ health.
Health and Safety (First Aid) Regulations 1981 – These regulations require employers to provide the following:
- Adequate first aid equipment and facilities
- A sufficient number of first-aiders
- A first aid appointed person, for when a first-aider is unavailable.
The Workplace (Health, Safety and Welfare) Regulations 1992
The Manual Handling Operations Regulations 1992
The Provision and Use of Work Equipment Regulations 1998 (PUWER)
Why is PPE Important
Personal protective equipment (PPE) protects workers from hazards such as trips, burns, electrocution, infections and falls. While there is some PPE that is universal to many occupations, staff working in warehousing and storage facilities have certain PPE which is specific to their job.
This includes, but is not limited to:
- First aid kit — A first aid kit should be available in all workplaces, including warehouses and storage facilities. This is because accidents can happen at any time, and it is important to be prepared for them.
- Breathing masks — These can prevent breathing in toxic chemicals. Depending on the setting, a simple paper mask or a more complex respirator may be required. Wearing a mask at work will also prevent long-term respiratory problems.
- Hard hats — These are essential in some warehousing and storage environments where there is a risk of objects falling from above. They protect the head from impact and help to prevent serious injuries. Cold-store warehouse workers should wear a safety helmet with a thermal liner, thermal balaclava and thermal hood.
- Fall protection — When working at heights, there is a risk of falling. Wearing fall protection, such as a harness, will help to prevent serious injuries if a fall occurs.
- Hi-vis jackets – High visibility clothing is a must for anyone working in low-light areas of the warehouse but also for workers that are near to vehicles. For example, forklift drivers should be easily able to spot anyone close by so they can easily avoid them. Dark clothing makes it harder to see them and more likely for injuries to occur.
- Safety shoes – It is crucial that warehouse workers wear the right kind of shoes during shifts. Not only do safety shoes offer extra protection, but they also provide the wearer with the comfort and support they need to be on their feet all day. Cold-store warehouse workers should wear insulated safety boots with thermal socks.
- Gloves – These are needed to protect hands from harmful substances and to prevent cuts and blisters. Safety work gloves are available in different materials depending on the work that is being carried out. They allow the warehouse worker to get on with their tasks without worrying about their hands. Cold-store warehouse workers should wear cold-store gloves with thermal liners.
- Protective clothing — The type of clothing needed will depend on the nature of the work being done. Trousers with removable knee pads are highly recommended to protect joints and improve comfort when performing jobs involving kneeling. Cold-store warehouse workers should wear thermal undergarments to their personal preference, and jacket and salopettes, or all-in-one coveralls, both with knee protection.
- Ear protection – Warehouses and storage facilities can be noisy environments, so it is important to protect workers’ hearing. Earplugs or earmuffs will help to reduce the noise levels that they are exposed to.
- Fire extinguishers — Fire extinguishers are essential in any workplace, but they are especially important in warehouses and storage facilities. Having a fire extinguisher close at hand can help to prevent serious injuries or damage to property.
What Training Should Warehouse Workers Take?
Depending upon their role, staff and management working within warehouse and storage facilities will have completed training and qualifications specific to that role, for example forklift truck driving. In addition to their occupational training, warehouse and storage facilities staff will need to participate in adequate health and safety training to ensure that they are competent to do their work. When warehouse and storage facilities staff are trained to work safely, they should be able to anticipate and avoid injury from job-related hazards. Safety training is essential for all warehouse and storage facilities employees appropriate to their role, and training should be directly applicable to the responsibilities and daily practices of the person being trained.
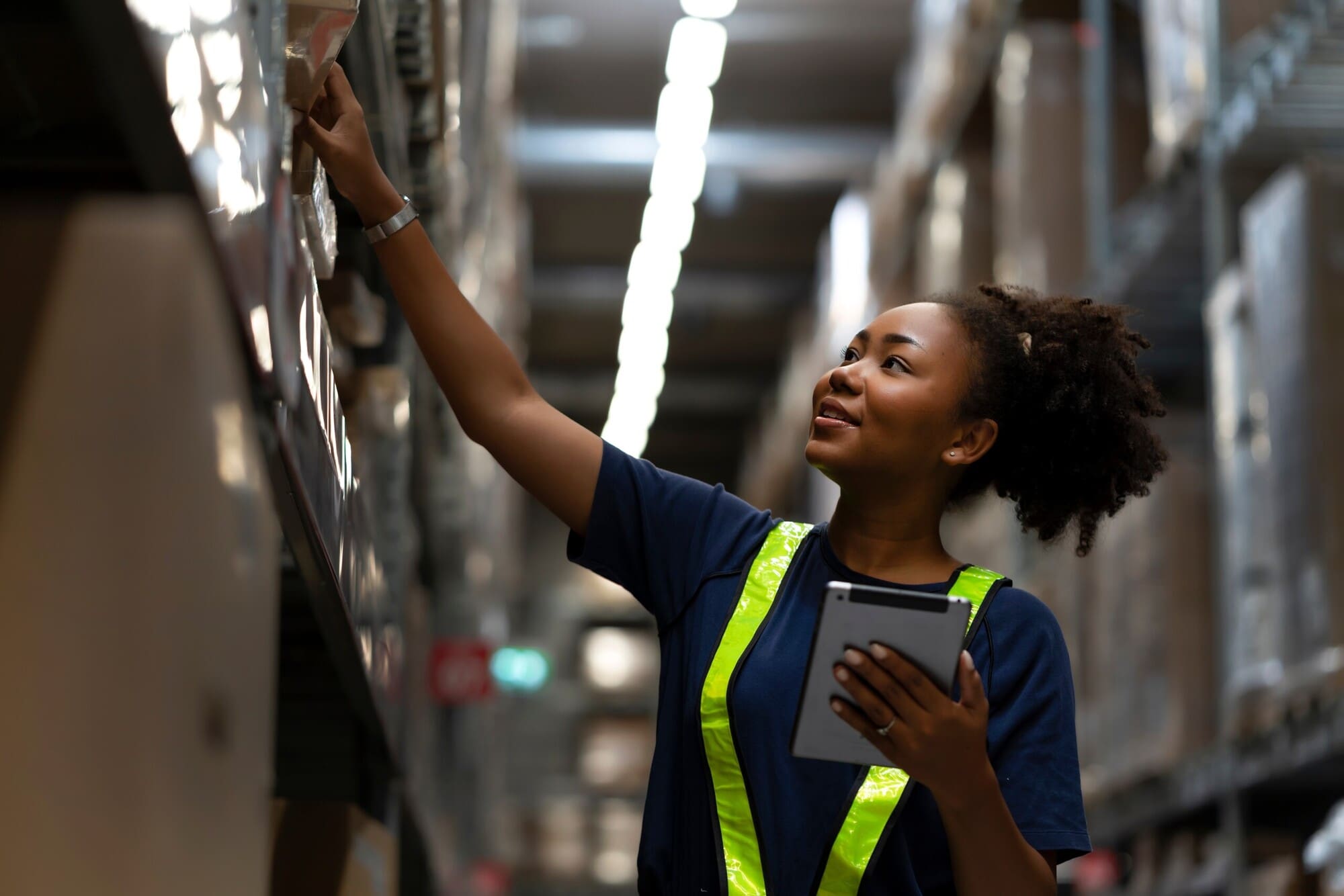
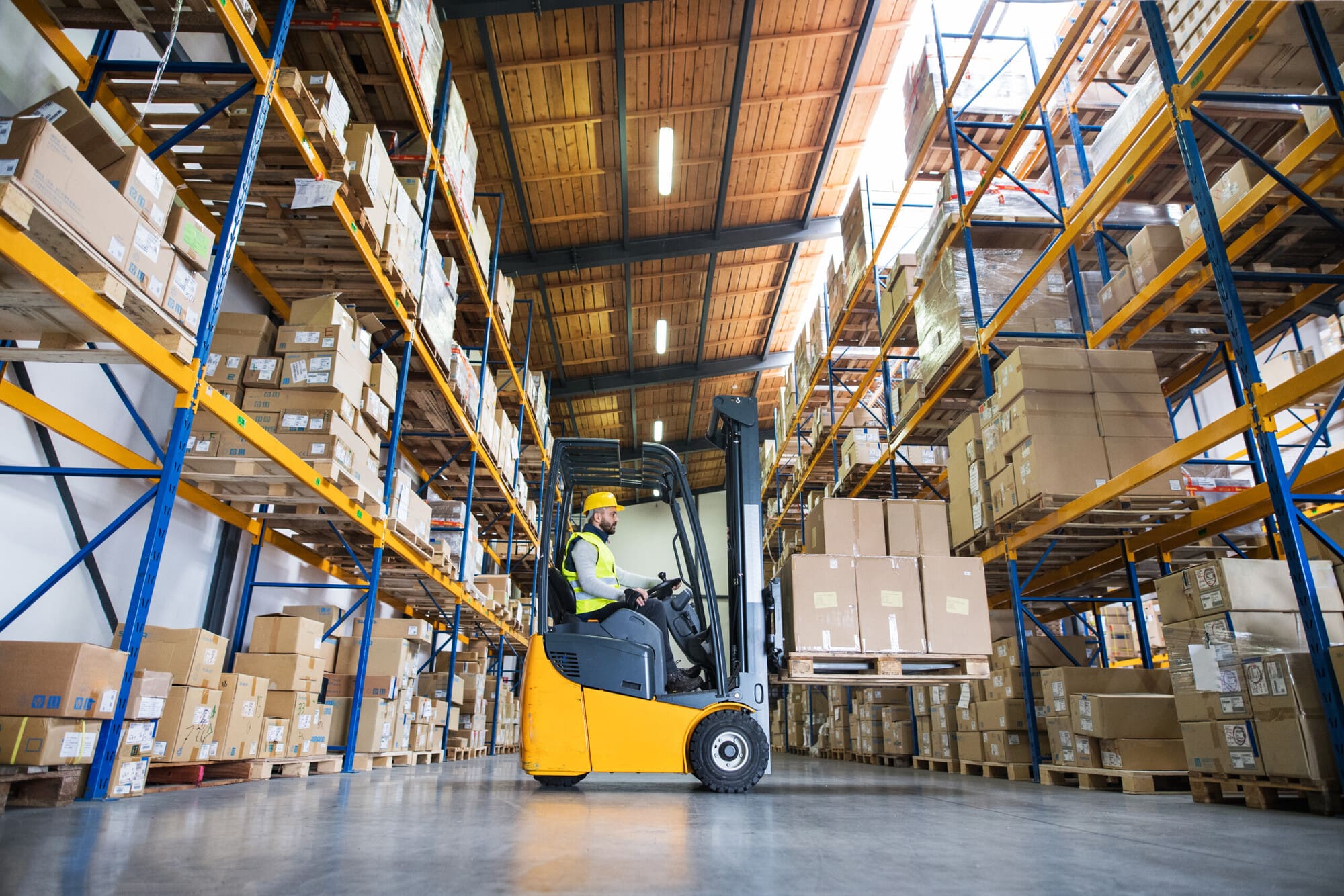
Training Courses
This training for warehouse and storage facilities staff might include, but is not limited to:
- Health and Safety for Employees
- Health and Safety for Managers
- Warehouse Safety Course
- Manual Handling
- Workplace First Aid
- Working at height
- Slips, Trips and Falls
- Personal Protective Equipment (PPE)
- PUWER Awareness
- Ladder safety
- Assessing Risk
- Electrical Safety Awareness
- DSEAR Awareness
- Fire Safety Awareness
- COSHH Awareness
- Fire Warden
- LOLER
Everyone working in warehouse and storage facilities should at a minimum refresh their safety training at least every 2 years and participate in continuing professional development (CPD).