In this Health and Safety Guide for PAT Testers
Portable appliance testing (PAT) plays a key role in the electrical safety of workplaces and protecting others from the dangers of electricity. A qualified PAT tester is an electrical testing engineer. They are responsible for inspecting electrical systems and equipment in homes and businesses to identify faults. PAT testers carry out work on or near electrical equipment. Working with electricity can be dangerous, therefore they should be able to anticipate and avoid injury to themselves and others from job-related hazards.
What is the Role of a PAT Tester?
Electrical PAT testers survey, test and inspect electrical installations in homes and businesses. They identify faults and complete test reports to confirm which equipment is working safely and efficiently and which is condemned as unsafe to use. Their role might involve carrying out quality checks on new buildings or conducting regular portable appliance (PAT) tests on frequently used machines.
The role of an electrical PAT tester might involve the following:
- Surveying, testing and inspecting electrical installations
- Carrying out portable appliance (PAT) testing
- Identifying faults or inefficiencies
- Fixing faults or arranging for them to be repaired
- Gaining quotes for repair jobs
- Completing testing reports and electrical certificates
- Working to health and safety standards
- Adhering to government and regulatory guidelines
- Liaising with clients and colleagues
The above list is not exhaustive. Whatever the environment they work in, an electrical PAT tester will be responsible for ensuring the safety of electrical equipment to protect the safety of themselves and other people.
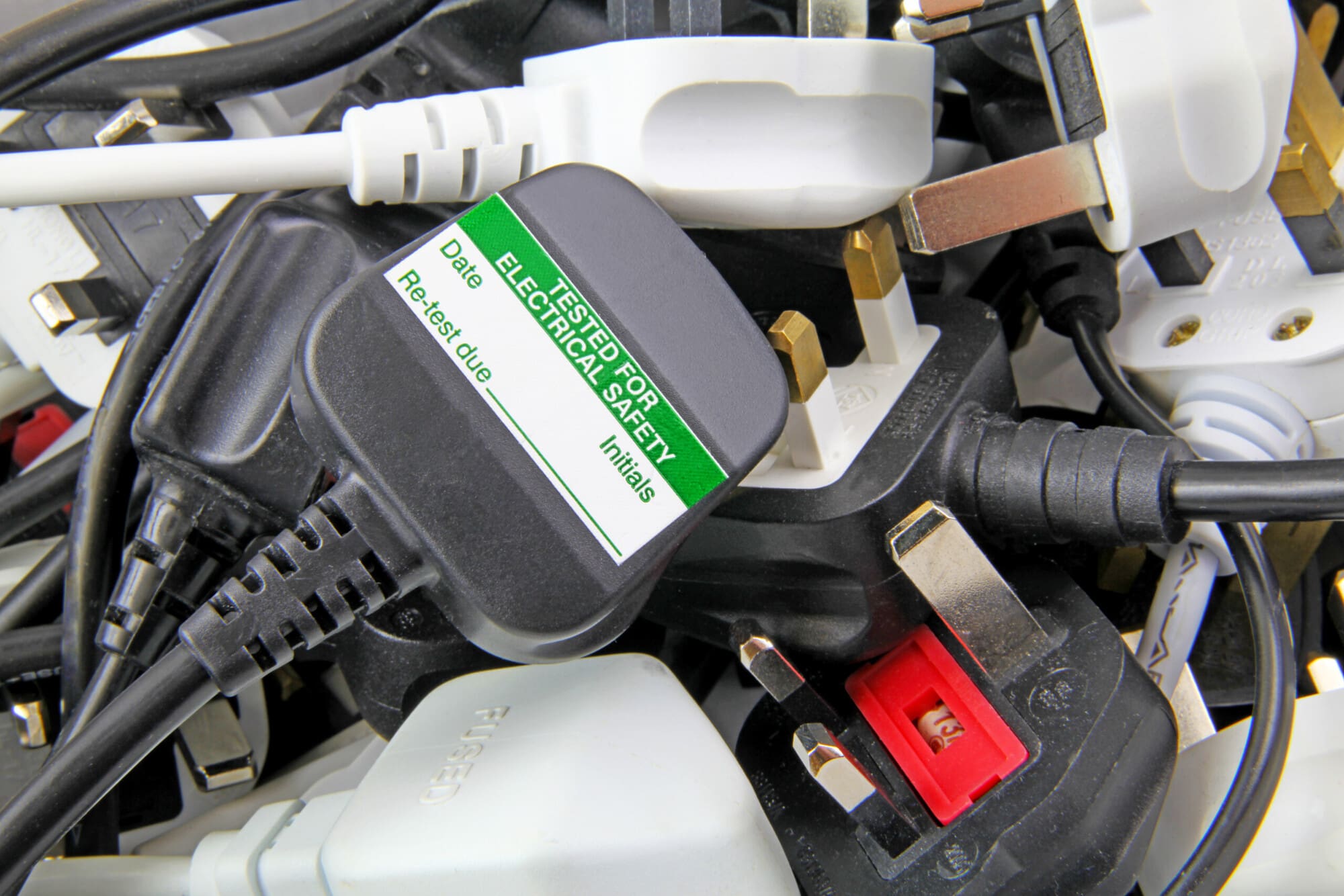
What are the Main Hazards of Working with Electricity?
There are many potential electrical hazards present in an electrical PAT tester’s work environment which could lead to severe injury or even death. Fatal electrocution is the main risk, but electrical shock, burns, and falls from elevations are also hazards. The wear and tear of equipment that results in insulation breaks, short-circuits and exposed wires can cause explosions or fire and can send current through the body, resulting in electrical shocks or burns, or death. The normal wear and tear on extension and flexible leads can loosen or expose wires, creating hazardous conditions. Additionally, if electrical equipment including extension and flexible leads, is used in ways for which it is not designed you can no longer depend on safety features built in by the manufacturer. This may damage the equipment and cause injuries.
The types of injury that may occur from faulty or mishandling electrical equipment include:
- Shock – if wiring or equipment is not properly grounded shocks can occur when a person makes direct contact.
- Burns – these have the potential to cause severe disfigurement and can be extremely serious and damaging. Burns injuries generally occur in the feet and hands as this is where the current enters and leaves the person’s body.
- Electrocution – electrocution can be fatal. If equipment is poorly installed or insulated it may result in electrocution.
- Falls – if a shock happens when installing, maintaining, testing or using electrical equipment at height, secondary injuries such as head injuries or broken or fractured bones may occur, and some falls may be fatal.
The risk of fire is also a potential hazard for those working with electrical equipment. Fire may occur from faulty electrical equipment or installations, explosions and/or fire may be caused by unsuitable electrical apparatus, or static electricity may ignite flammable vapours or dusts, for example in a spray-paint booth.
What Precautions Need to be Taken When Working with Electricity?
Electrical safety at work should be a concern to all businesses. It is vitally important for an electrical PAT tester to take safety precautions when working with electricity and electrical equipment. The first step of electrical safety is to avoid water at all times when working with electricity. Never touch or try repairing any electrical equipment or circuits with wet hands, as it increases the conductivity of the electric current.
An essential step when working with electricity to stay safe is to wear appropriate personal protective equipment (PPE). We will look at PPE recommended for electrical PAT testers later in this guide.
An electrical PAT tester should always use insulated tools while working. The electrical power should be turned off to allow you to do work safely, and it is essential that the power stays off until you have finished work. Doing this and testing to be sure the power is off is the only way to prevent being dangerously shocked. Even after shutting off the power, always act as if the wires are live. That way if someone accidentally turns on the power or a tester gives the wrong reading, you are still protected. Test for the presence of power using a voltage tester. To do this properly, follow the manufacturer’s instructions. It is good practice to test the tester, too. Touch the probes to a live circuit to make sure the indicator bulb lights are working properly. Test all wires; it is good practice to touch the bare end of a wire only with an insulated tool, not your fingers.
Risk Assessments
Under the Management of Health and Safety at Work Regulations (1999), the minimum a business must do is:
- Identify what could cause injury or illness in your business (hazards)
- Decide how likely it is that someone could be harmed and how seriously (the risk)
- Take action to eliminate the hazard or, if this isn’t possible, control the risk
Risk assessment requires making a judgement on Risk Severity. Risk Severity = probability of risk materialising x impact of risk on, for example, a person or people, a business, a property etc.
Probability may be understood as:
- Low (Level 1) – a reasonably informed person would think it very unlikely this risk would materialise in the foreseeable future.
- Medium (Level 2) – a reasonably informed person would think there is a significant possibility this risk would materialise in the foreseeable future.
- High (Level 3) – a reasonably informed person would think there is a very significant or even likely possibility the risk would materialise in the foreseeable future.
Impact may be understood as:
- Low (Level 1) – any impact that is minimal, having regard to the importance of interests affected, impairment of function and duration. Typically, the impact is isolated and short-lived.
- Medium (Level 2) – any impact that is significant, having regard to the importance of interests affected, impairment of function and duration. Typically, the impact is limited to one function or group, but there is a material operational impact and the effects may continue.
- High (Level 3) – any impact that is severe, having regard to the importance of interests affected, impairment of function and duration. Typically, the impact impairs a critical function and/or has a systemic impact and the effects may be long-lasting or permanent.
Electrical PAT testers must ensure an assessment has been made of any electrical hazards, which covers:
- What the potential hazard is – the risk assessment should take into consideration the type of electrical equipment used, the way in which it is used and the environment it is used in
- Who or what could be harmed by the hazard
- How the level of risk has been established
- The precautions taken to eliminate or control that risk
Managing risk is an ongoing process that is triggered when changes affect an electrical PAT tester’s work activity; changes such as, but not limited to:
- Changing work practices, procedures or the work environment
- Purchasing new or used equipment or using new substances
- Workforce changes
- Planning to improve efficiency or reduce costs
- New information about the workplace risks becomes available
Risk assessments should be recorded and records regularly reviewed and updated whenever necessary. Should an accident occur, the Health and Safety Executive (HSE) will request copies of the risk assessments.
The Importance of PAT Testing
There are a lot of reasons why PAT testing is important. One of the main reasons is because it helps to protect the safety of employees as well as everyone else. Electrical equipment can be hazardous if not used or maintained correctly, and faulty equipment can lead to electric shocks, fires, and other serious accidents. By carrying out PAT testing, businesses can ensure that their equipment is safe to use and minimise the risk of accidents occurring.
Ensuring that workplace and rental homes’ electrical equipment is safe and fit for purpose are legal requirements under the Health and Safety at Work Act etc.(1974), the Management of Health and Safety at Work Regulations (1999), the Electricity at Work Regulations (1989), the Provision and Use of Work Equipment Regulations (PUWER 1998), and the Housing Act (2004 England and Wales), Housing Act (2006 Scotland).
All equipment that uses a flexible wire or cable to connect to a power supply qualifies as a portable appliance and needs to be checked. Portable appliance testing (PAT) is the term used to describe the examination of electrical appliances and equipment to ensure that they are safe to use.
Most electrical equipment safety defects can be found by visual examination but some types of defect can only be found by testing. A PAT test involves a visual inspection to check the appliance casing and flex for wear or damage. Plugs are also checked for damage, correct wiring and to ensure that the correct fuse rating is used.
After the equipment has passed a visual inspection it will normally undergo a series of electrical tests using a fully calibrated electrical PAT tester. A label will be attached to each appliance indicating the test results. Any item failing the tests will be easily identifiable and should be removed from service until repaired. You should record and retain the results of all PAT testing in an appliance register for future reference. More specific detail of the PAT test is given below.
What are the Requirements of PAT Testing?
Electrical appliances are mainly categorised as Class 1, 2 or 3, with Class 1 being the most dangerous and Class 3 the least dangerous. Class 3 appliances include equipment such as laptops or mobile phones. These appliances are low voltage items, they are the safest class of electrical appliance and may not require PAT testing; however, their charging leads may need to be PAT tested. Class 2 appliances include items such as electrical drills, TVs or computer printers. This type of electrical equipment has extra insulation and so does not rely on an earth for protection, which makes it safer than Class 1 equipment. Class 1 appliances include equipment such as industrial machinery, office type equipment such as photocopiers and laptop leads, and many items of kitchen equipment such as microwave cookers, dishwashers or refrigerators.
The frequency of PAT testing is determined by several factors. This includes the type of equipment and its classification, the frequency it is used and/or moved and the environment in which it is operating. PAT testing should be carried out at the very least, every 2 years; however, in some environments and with some categories of equipment this may need to be done every time the equipment is moved.
The Health and Safety Executive (HSE) recommends taking the following into consideration as necessary:
- Manufacturer’s recommendations
- The age of the equipment
- Frequency of use of the equipment
- Foreseeable misuse of the equipment
- Effects of any modifications or repairs
- The history of the item
The Health & Safety Executive (HSE) advises that PAT testing should include three steps:
- User checks – all users of electrical equipment should have some basic training in how to use the equipment safely, as well as what danger signs to be aware of, as part of their induction. Users should feel confident in visually checking the equipment regularly for obvious signs of damage, as well as potential risks, such as cables trapped under desks or water hazards.
- A formal visual inspection – prior to the manual PAT test, a formal visual inspection of the equipment should be carried out. According to the HSE, this process usually flags up around 90% of problems. It is essential that the equipment is turned off and unplugged before beginning the visual inspection. The checklist should include:
- The plug – look for any signs of damage, including cracks, burns or bent pins, and check that the wiring is correct. The live, neutral and earth conductors should all be connected to their relevant terminals tightly.
- The cable – check the cable visually and physically for any damage, including fraying, cuts or abrasions. Any exposed wiring is an immediate fail.
- The appliance – check for any obvious damage, including cracks, burns, corrosion and casing wear and tear.
- The mains socket – although this is not part of a PAT test, it should be included in the visual inspection. The mains testing of sockets is done during a fixed wire test. Look for cracks, signs of over-heating and any loose fittings and check the shutter mechanism.
- Residual Current Device (RCD) checks – RCDs are fitted with a test button and will trip if the current flowing through the live conductor is different to that in the neutral. The inspection should look for signs of damage; check the operating current and test the ‘test’ button to ensure it’s in working order.
- Environmental check – check for trip hazards from cables, overloaded extension leads, water risks and fire hazards.
The manual PAT test using a portable appliance tester – the electrical PAT tester will carry out a visual inspection, as well as a manual electrical examination using a portable appliance tester device. This will test the appliance for earth continuity, lead polarity and insultation resistance, amongst other things, and will show if it has passed or failed the PAT test. The appliance will then receive a pass or fail sticker and the results should be recorded by the duty holder for future reference. Failed appliances must not be used and should be removed immediately, either to be repaired or replaced. If the item is repaired, it must pass another PAT test before it is safe to use again.
At present you don’t have to be a qualified electrician in order to PAT test; however, from 1st June 2020 the Landlord Electrical Safety Certificate Legal Requirement stated that all PAT testing in rental properties is checked by a qualified electrician to ensure that appliances are safe and that subsequent testing must then be carried out on a five-yearly basis.
When undertaking combined inspections and testing the tester will need:
- The right equipment to do the tests
- The ability to use this test equipment properly
- The ability to understand potential hazards and precautions to take when PAT testing
- The ability to properly understand the test results
A comprehensive checklist ensures that an electrical PAT tester follows strict rules during the PAT test. This ensures that all electrical appliances are PAT tested and covered by proper documentation.
What are the Benefits of PAT Testing?
Faulty electrical equipment can lead to unexpected downtime. This can be costly for businesses. By carrying out regular PAT testing, businesses can identify potential faults before they lead to equipment failure and address them before they cause any disruption.
With regular tests, PAT testing can help to improve the efficiency and performance of electrical equipment. Over time, electrical equipment can become less efficient due to wear and tear, but by carrying out PAT testing, businesses can identify any issues with their equipment and address them before they become unsafe. This can help to prolong the life of electrical equipment and make sure that it continues to perform effectively.
PAT testing is an essential part of ensuring electrical safety within the workplace. It helps to protect the safety of employees and ensure compliance with health and safety regulations and insurance requirements. A simple PAT test report is enough to show compliance with health and safety requirements and the absence of foul play in case of fire-related accidents, and enables the business to make a claim for damages through their insurance.
Why is PPE Important
Personal protective equipment (PPE) protects workers from hazards such as trips, burns, electrocution, and falls. While there is some PPE that is universal to many trades, electrical PAT testers have certain PPE which is specific to their job. The biggest risk posed to an electrical PAT tester is that they might come into contact with electricity; in these cases, electrical PPE clothing would be a great line of defence.
This includes:
- Safety trainers – an alternative to steel toe-cap boots, they offer greater sensations underfoot on ladders and steps, helping electrical PAT testers judge their step better while retaining the same insulation against electricity.
- Electricians glove – cut-resistant gloves through which the electrical PAT tester can still feel and grip through, while offering a reasonable amount of insulation against shocks.
- Safety glasses – specially made glasses are essential for long- or short-sighted electrical PAT testers.
- Hard hat – applicable to electrical PAT testers working in high-risk places.
- Voltage limiting devices – used for overloaded circuits or extension cords.
- Avoid wearing anything conductive such as metal bracelets or jewellery, especially since they could get caught inside machinery while they are being worn.
A full risk assessment must be undertaken before it is decided which PPE should be worn by the electrical PAT tester.
What Training Should PAT Testers Take?
Anyone wanting to qualify as a PAT tester should complete a PAT testing Certificate of Competence training course or complete the City & Guilds 2377-77 PAT training course. It is also recommended that you take regular refresher courses to keep up to date with regulations.
When electrical PAT testers are trained to work safely, they should be able to anticipate and avoid injury from job-related hazards. Safety training is essential for all electrical PAT testers appropriate to their role, and training should be directly applicable to the responsibilities and daily practices of the person being trained.
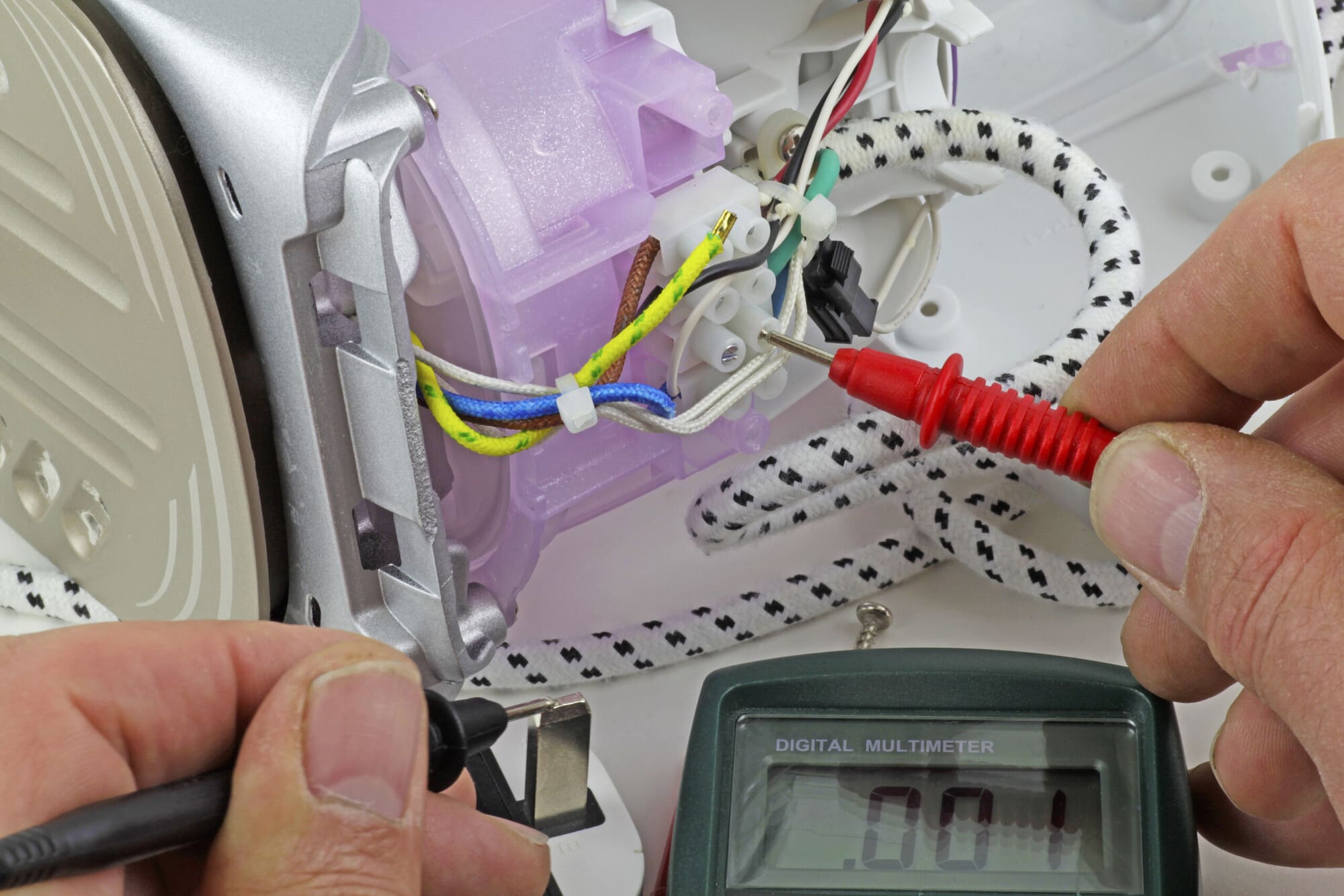
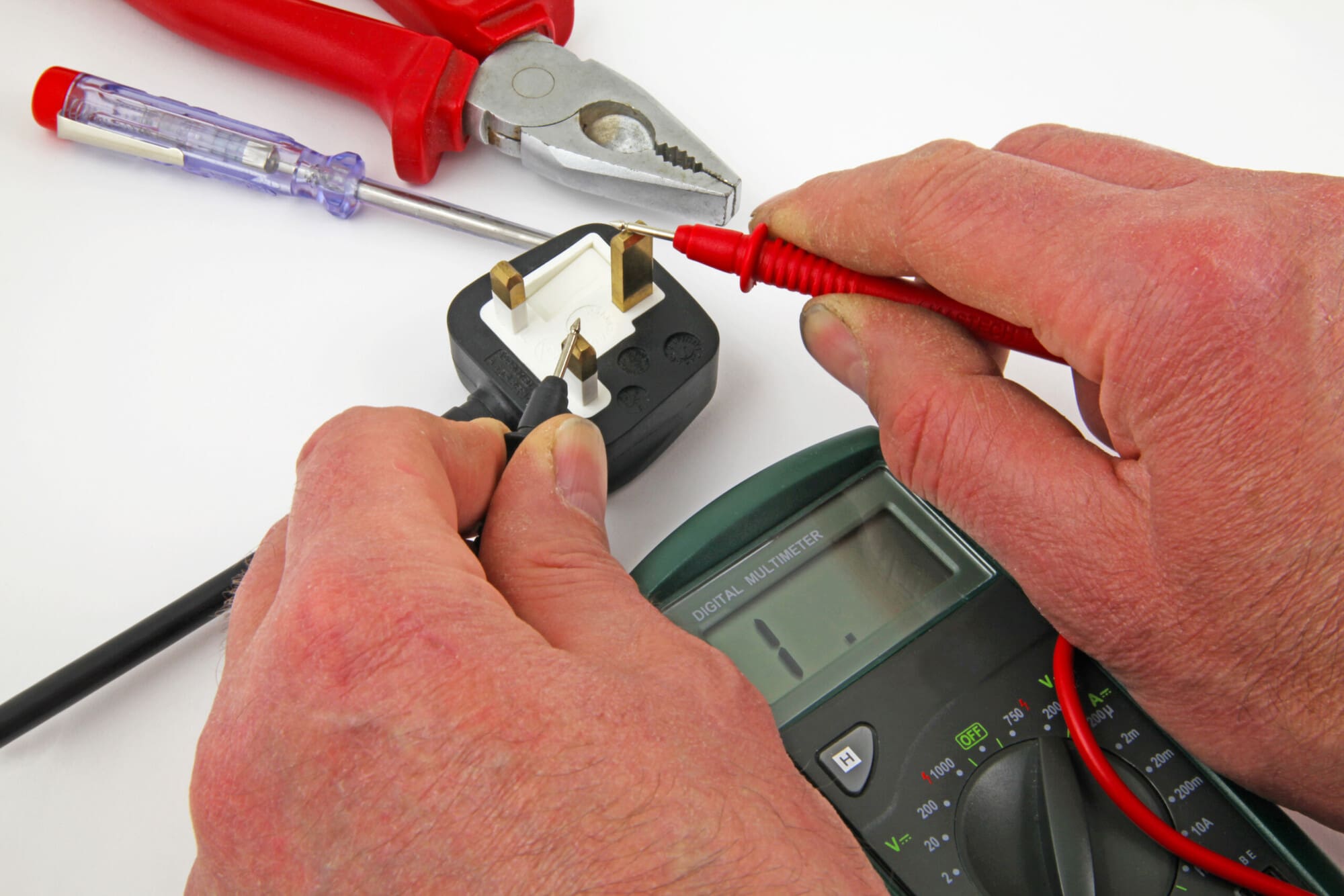
Training Courses
This training for welders might include, but is not limited to:
- Health and Safety for Employees
- Health and Safety for Managers
- Electrical Safety Awareness
- PAT Testing Awareness
- Assessing Risk
- Manual Handling
- Workplace First Aid
- Slips, Trips and Falls
- Personal Protective Equipment (PPE)
Electrical PAT testers should at a minimum refresh their safety training at least every 2 years and participate in continuing professional development (CPD).