In this Health and Safety Guide for Manufacturers
There are around 2.7 million people employed in UK manufacturing across these sectors. The Office for National Statistics (ONS) Labour Force Survey estimates that an average of 33,000 manufacturing workers per year suffer from illnesses that have been caused or made worse by their job in the manufacturing industry.
The manufacturing industry is filled with potential workplace health and safety issues that need to be overcome on a daily basis, so to keep employees and others safe from danger or harm, manufacturing workers will need to maintain their own safety, as well as the safety of the area and the people around them.
Manufacturing in the UK covers a wide spectrum of sectors including, but not limited to:
- Chemical and Pharmaceutical
- Defence
- Electronics
- Aerospace
- Automotive and Transport
- Food and Drink
- Nuclear
- Construction
- Steel
- Rubber, Plastics and non-metallic Minerals
- Textiles and Clothing
- Energy
- Other production sectors such as furniture production
What is the Role of a Manufacturer?
Manufacturing is carried out in factories, plants, mills and even at home. It involves the creation of new products directly from raw components and materials. For example:
- The food manufacturing sector transforms agricultural and livestock products into goods for intermediate or final consumption; that is, producing goods for retailers and wholesalers, who then distribute them to consumers.
- The textile, leather and apparel sectors transform leather, cloth or other materials such as plastic, rubber or leather substitutes into functional products such as footwear and garments.
- Electrical equipment, appliances and components manufacturers produce a variety of goods such as lighting fixtures, light bulbs, transformers, generators, electric motors, batteries, electric outlets, light switches and fuse boxes. This industry is usually plant-based.
The manufacturing industry is quite broad and, as we have seen, serves a great variety of industry sectors. However, irrespective of the sector a manufacturer is working in, they tend to employ very similar roles, although specific role titles and duties may vary between individual settings.
Depending on where, and the type of work that they are doing, the role of employees and management in manufacturing may involve, but is not limited to:
- Technical Manager – The technical manager is responsible for ensuring that all products meet quality criteria, liaising with regulatory authorities, ensuring good standards of housekeeping and hygiene are maintained, managing health and safety systems, enforcing performance KPIs, reviewing and maintaining programmes, dealing with customer complaints, making sure hygiene and all other audits are carried out, as well as other reasonable duties.
- Production Line Supervisors – Duties include the successful running of a busy production environment, KPI reports, supervising a team of around 25 staff and assuring that all health and safety processes are adhered to.
- Manufacturing Supervisors – Responsible for planning and organising staff rotas, reporting machinery breakdowns, stock control and ordering supplies, making sure the team meets production targets, carrying out quality control checks and writing reports, updating paperwork such as holiday requests and sick leave and organising staff training.
- Engineers – Manufacturing engineers usually work inside factories or other production sites. They develop efficient systems, processes and machines that result in high-quality products. They may also take into account how manufacturing processes impact the environment.
- Production Operatives – Responsible for measuring, grading and feeding batches of raw materials into production machinery, operating production line equipment, assembling goods on a production line, reporting equipment faults to maintenance staff, finishing products, monitoring the production process and carrying out basic testing and quality checks, storing goods and raw materials in the factory or warehouse, using lifting equipment and forklift trucks, packing goods ready for shipment, and cleaning and maintaining work areas and machinery.
- Machinists and Operators – Machinists and operators set up, maintain and operate both computer and mechanically-operated machinery used in the manufacturing process. They also review drawings, instructions, blueprints or samples to ensure accurate manufacturing and production and select appropriate machines and settings for a given task.
- Assemblers – Assemblers work in factories, often on assembly lines, putting parts together to form completed products or parts of other products. Duties include adding components in the right order, following diagrams and instructions, using tools such as spanners, pliers, tweezers, drills and electric screwdrivers, using microscopes for detailed work, testing items and checking quality, and packing products or putting them in the correct area for collection.
- Quality Assurance Technicians – Responsible for monitoring each stage of the production process, a quality assurance technician uses statistical analysis to make sure that machined parts are within tolerance limits, inspects materials and products for defects, using methods like non-destructive testing, deals with customer feedback and complaints, assesses suppliers, reviews policies, and produces reports for quality managers.
- Packing Operatives – Packing operatives pack products to protect them during transportation, give them an identifiable and desirable appearance for display, and preserve any goods that are perishable. Duties include picking orders, packing boxes, checking stock, goods in and out, assembly and cleaning within the warehouse.
- Forklift Truck Operatives – The role will include loading and unloading, and moving materials around the warehouse. Duties will include operating a reach forklift truck in a safe and successful manner, palletising and other general warehousing duties as required.
- Industrial Cleaners – Industrial cleaners work in factories, plants etc., and their duties can include washing out boilers, tanks and vats, removing dust and ash, decontaminating work areas and machinery, mixing cleaning chemicals in the correct amounts, sandblasting the outside of buildings and structures, disposing of hazardous waste, and reporting potential hazards to supervisors.
- Delivery and/or HGV Drivers – Drivers work from depots, distribution centres and warehouses, driving, carrying goods, planning delivery schedules, supervising or helping to load and unload goods, making sure loads are safely secured, following traffic reports and changing routes if necessary, and completing delivery paperwork and logbooks.
- Support / Administrators – These roles often include, but are not limited to, customer support, shipping, sales, marketing, finance, HR, research and development, buying, maintenance/facilities, senior management.
Generic to all roles is ensuring compliance with all relevant policies and procedures, and legal and regulatory requirements including health and safety. All staff will be working closely alongside other staff to deliver high-quality manufacturing production. The above lists are not exhaustive and there is often a crossover of duties between roles. Whatever the environment they work in, manufacturing staff and management will be responsible for ensuring the safety of their work and any equipment to protect the safety of themselves and other people.
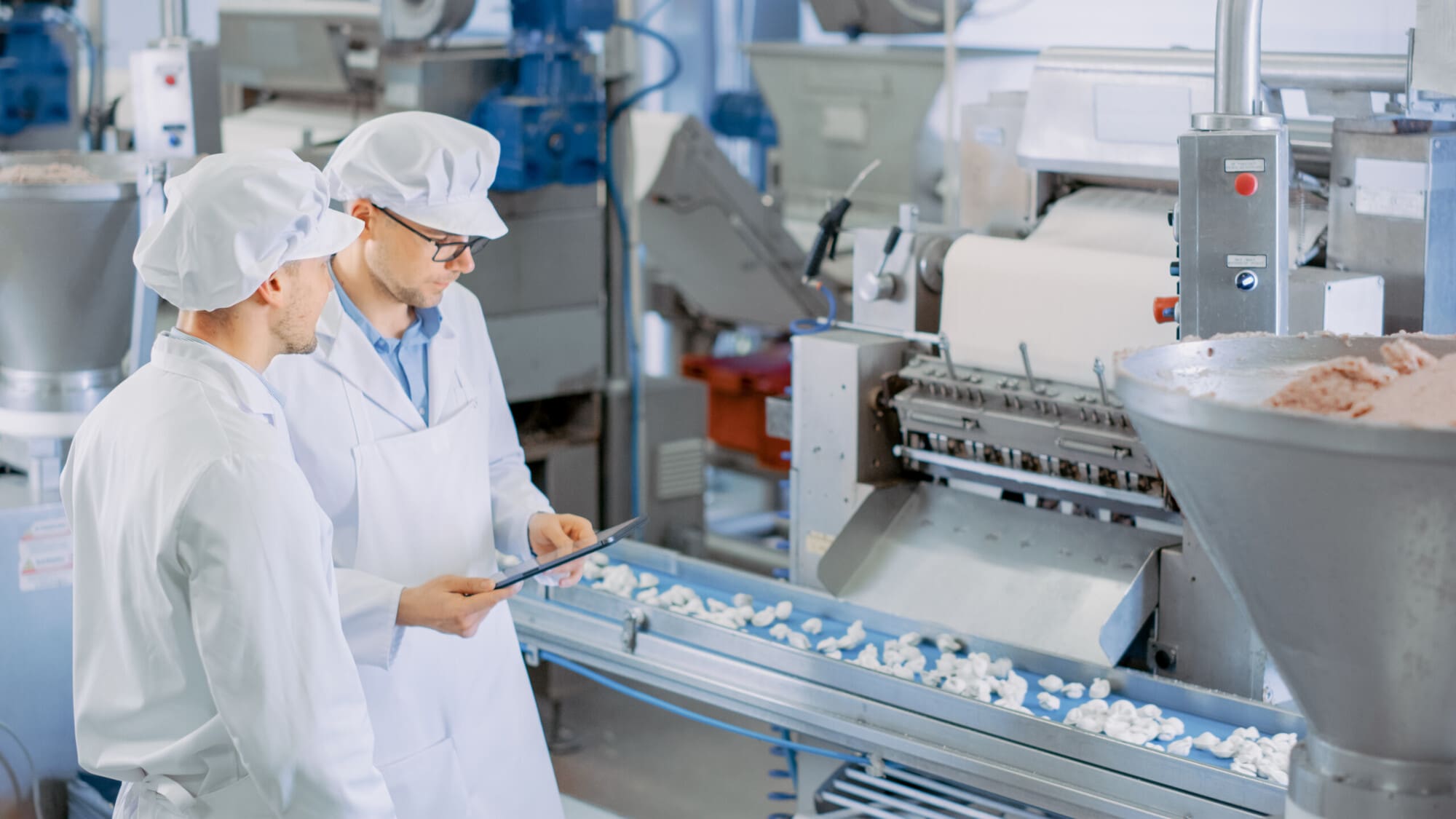
What are the Main Health and Safety Risks Manufacturers Can Encounter?
Workers in manufacturing may encounter numerous hazardous situations as part of their role; the types of manufacturing hazards can vary from disruptive to catastrophic and severe. According to the Health and Safety Executive (HSE), the manufacturing sector saw 22 fatal injuries in 2021/22, out of a total of 123 workers involved in fatal workplace accidents.
Workers in the manufacturing industry are frequently exposed to and work with electricity. In a manufacturing environment, electrical hazards can come in numerous forms such as faulty electrical equipment, damaged tools, damaged insulations and even explosions. Electrical equipment can gradually become unstable over time after repeated wear and tear, or it can react when exposed to water sources, or when circuits are overloaded. Additionally, if electrical equipment, including extension and flexible leads, is used in ways for which it is not designed you can no longer depend on the safety features built in by the manufacturer. This may damage the equipment and cause injuries.
The types of injury that may occur from faulty or mishandled electrical equipment include:
- Shock – if wiring or equipment is not properly grounded shocks can occur when a person makes direct contact.
- Burns – these have the potential to cause severe disfigurement and can be extremely serious and damaging. Burns injuries generally occur in the feet and hands as this is where the current enters and leaves the person’s body.
- Electrocution – electrocution can be fatal. If equipment is poorly installed or insulated it may result in electrocution.
- Falls – if a shock happens when installing, maintaining or using electrical equipment at height, secondary injuries such as head injuries or broken or fractured bones may occur and some falls may be fatal.
The risk of fire is also a potential hazard for those working with electrical equipment. Fire may occur from faulty electrical equipment or installations, explosions and/or unsuitable electrical apparatus, or static electricity may ignite flammable vapours or dusts, for example in a manufacturing environment. Mitigating this risk involves ensuring all electrical equipment is properly installed, configured, insulated, operated and maintained. It is also vital to ensure that all employees are properly trained in electrical safety and risk management.
The Provision and Use of Work Equipment Regulations 1998 (PUWER) place duties on people and companies who own, operate or have control over work equipment. PUWER also places responsibilities on businesses and organisations whose employees use work equipment, whether owned by them or not.
PUWER requires that equipment provided for use at work is:
- Suitable for the intended use.
- Safe for use, maintained in a safe condition and inspected to ensure it is correctly installed and does not subsequently deteriorate.
- Accompanied by suitable health and safety measures, such as protective devices and controls. These will normally include emergency stop devices, adequate means of isolation from sources of energy, clearly visible markings and warning devices.
- Used in accordance with specific requirements.
Generally, any equipment which is used by an employee at work is covered by PUWER, for example hammers, knives, ladders, drilling machines, power presses, circular saws, photocopiers, lifting equipment (including lifts), dumper trucks and motor vehicles. Similarly, workers providing their own equipment will be covered by PUWER and it will need to comply.
Slips, trips and falls are one of the top three causes of non-fatal work injuries involving days away from work. Each year they cause thousands of preventable injuries, and they can cause various injuries such as bruises, sprains, scrapes, broken bones and head traumas. Around 1,000 of these injuries involve someone fracturing bones or dislocating joints.
Key aspects of slips and trips include:
- Uneven surfaces
- Obstacles
- Trailing cables
- Wet or slippery surfaces
- Changes in level
Keep work area floors clean, orderly and dry, and keep surfaces free of hazards such as sharp objects, loose boards, corrosions, leaks, spills, snow and ice. Signpost any slippery areas and make sure footwear with a good grip is worn. We will look at PPE later in this guide.
Falls frequently occur while manufacturing workers are over-reaching, attempting to access machinery, balancing on uneven surfaces, or working on mezzanines, elevated platforms, or loading bays. When working from a height, thorough and regular workplace inspections should be carried out, guardrail and fall arrest systems should be put in place and training should be provided. Stock falling from racking or racking collapsing can cause serious injury and even death, so racking should be visually inspected at least once a month by a technically competent person. Load capacities should be obeyed and a damage log kept.
Poorly installed machine guarding. Machines are a non-negotiable aspect of manufacturing, providing far greater efficiency than manual operations. Yet, accidents can occur, machinery can malfunction, and humans can make mistakes. Machine guards are typically physical barriers that prevent direct worker contact with the machinery and help minimise risk. If these guards are not put in place correctly, workers become vulnerable to hazardous motions and pinch points and can lead to accidental injuries, including:
- Abrasions
- Cuts
- Fractures
- Amputations
Management should always ensure that machinery and machine guarding is inspected for maximum operational efficiency, and also ensure all workers are up to speed with correct procedures for safe operation.
Manual handling injuries have a major impact on all workplaces and sectors, costing the economy hundreds of millions every year. Manual handling encompasses a wide range of actions including lifting, lowering, pulling, pushing, and carrying awkward and heavy objects; the risks are endless for manufacturing workers who may experience manual handling injuries such as:
- Back injuries
- Hernias
- Musculoskeletal disorders (MSDs) such as shoulder strain
- Repetitive strain injury (RSI) such as wrist strain
- Soft-tissue injuries to the wrists, arms, shoulders, legs or neck
- Long-term pain in the arms, legs or joints
Overexertion is something that is easily done in any environment and can be difficult to avoid. Overexertion is usually caused by someone trying to lift or move something heavier than their capabilities or doing so incorrectly. Manual handling tasks should be avoided wherever possible. Where it isn’t possible to avoid handling a load, suitable safety measures should be introduced such as staff having the use of trollies or lifting equipment to move heavy items, and all staff should receive manual handling training to prevent and avoid injury.
Powered industrial vehicles are commonly found in manufacturing settings. These vehicles include forklifts and lift and reach trucks, and extend to include vehicles used for the delivery of manufactured products and goods. Workers will use these vehicles to raise, lower or move goods and materials, typically in large quantities. Injuries that can be caused by these vehicles can range from minor to severe, with the root cause predominantly being improper use or insufficient training. These types of vehicles should only be operated by those with valid certifications and training, such as a forklift licence training course. Employers should enforce the use of seatbelts on forklift trucks and other vehicles, as around a quarter of all workplace transport accidents involve forklift trucks, with drivers being crushed after falling from a forklift.
Many manufacturers use chemical products in several ways. Some are used in industrial product manufacturing, whilst others are used to clean and maintain workplace premises. Many of these chemicals are poisonous or highly corrosive chemicals, which can cause severe and sometimes irreparable damage or injury. Workers may have to work with chemicals such as caustic cleaners, flammable substances such as ethanol, and even products containing bleach.
Physical and health hazards associated with toxic chemicals include, but are not limited to:
- Irritation
- Carcinogenicity
- Respiratory
- Flammability
Handwashing should be second nature by now, but manufacturing workers using any chemical substances must fully decontaminate themselves after using hazardous materials. Good ventilation also proves an essential safety measure to stop the build-up of toxic vapours. All chemicals must be treated with caution, employers must provide sufficient personal protective equipment (PPE) for employees that are required to use any chemicals, and ensure that all staff are sufficiently trained in categorising and handling them, as well as trained in providing first aid to immediately treat any injuries suffered to minimise the harm.
Industrial noise pollution caused by machinery and vehicles can have a detrimental effect on people’s mental and physical well-being. Prolonged exposure to noise can lead to:
- Stress and anxiety
- Productivity loss
- Fatigue
- Communication issues
- Tinnitus
- Cardiovascular diseases
- Deafness
- Nervous disorders
- Neurological problems
- Headaches
Manufacturing workers participating in noise-heavy activities must wear protective equipment at all times.
Fire safety is an essential part of any workplace environment and is especially important in manufacturing, where highly inflammable materials are being used or manufactured. When a fire starts in a building, it can happen very quickly. Burns and respiratory damage can be caused by flammable materials or electrical equipment igniting. Fire safety is a serious subject and precautions must be taken by all workplaces. These precautions include checking all power cords are in good condition and that power outlets are not overloaded.
It is also vital to ensure that emergency lighting is installed and that staff know where fire extinguishers are located, where their nearest fire exit is, and that emergency exits are clear at all times. Regular fire alarm testing should take place as well as regular fire evacuation tests.
Employers and management need to be able to confirm that:
- Firefighting equipment is in place
- Fire evacuation procedures are clearly displayed
- All staff are aware of the evacuation drill, including arrangements for any vulnerable adults
In order to remain effective, fire risk assessments must be kept up to date. It is recommended that the responsible person completes a fire risk assessment at least once a year, and must conduct a review whenever there is a significant change in the environment.
Fatigue or dehydration are significant risks within the manufacturing industry, with both having considerable impacts on health and safety. Fatigue is characterised by a chronic decline in physical and cognitive function. Dehydration is characterised by reductions in mental performance, mood, cognition and physical work rates. It is important to recognise that although sweating is a significant contributor to dehydration for those working long periods in hot environments, dehydration can occur at any time when a fluid deficit is allowed to develop. This can include during long shifts in low-humidity, air-conditioned environments, and can even occur in winter when hydration is often overlooked. Ensure adequate, structured rest breaks; not only does this allow time for recovery, but it also allows for regular drinking, whereby the individual consumes fluid consistently over their shift rather than in large doses at limited intervals.
Risk Assessments
Maintaining a safe work environment is important, particularly in the high-risk work environment faced by those working in manufacturing. It is important that every hazard is met with elimination or, at the minimum, a control measure to mitigate any potential risk.
Under the Management of Health and Safety at Work Regulations (1999), the minimum a business must do is:
- Identify what could cause injury or illness in your business (hazards)
- Decide how likely it is that someone could be harmed and how seriously (the risk)
- Take action to eliminate the hazard or, if this isn’t possible, control the risk
Risk assessment requires making a judgement on Risk Severity. Risk Severity = probability of risk materialising x impact of risk on, for example, a person or people, a business, a property etc.
Probability may be understood as:
- Low (Level 1) – a reasonably informed person would think it very unlikely this risk would materialise in the foreseeable future.
- Medium (Level 2) – a reasonably informed person would think there is a significant possibility this risk would materialise in the foreseeable future.
- High (Level 3) – a reasonably informed person would think there is a very significant or even likely possibility the risk would materialise in the foreseeable future.
Impact may be understood as:
- Low (Level 1) – any impact that is minimal, having regard to the importance of interests affected, impairment of function and duration. Typically, the impact is isolated and short-lived.
- Medium (Level 2) – any impact that is significant, having regard to the importance of interests affected, impairment of function and duration. Typically, the impact is limited to one function or group, but there is a material operational impact and the effects may continue.
- High (Level 3) – any impact that is severe, having regard to the importance of interests affected, impairment of function and duration. Typically, the impact impairs a critical function and/or has a systemic impact and the effects may be long-lasting or permanent.
Workers in manufacturing must ensure an assessment has been made of any hazards, which covers:
- What the potential hazard is – the risk assessment should take into consideration the type of equipment used, the way in which it is used and the environment it is used in
- Who or what could be harmed by the hazard
- How the level of risk has been established
- The precautions taken to eliminate or control that risk
Managing risk is an ongoing process that is triggered when changes affect a manufacturer’s work activities; changes such as, but not limited to:
- Changing work practices, procedures or the work environment
- Purchasing new or used equipment or using new substances
- Workforce changes
- Planning to improve efficiency or reduce costs
- New information about the workplace risks becomes available
Risk assessments should be recorded, and records regularly reviewed and updated whenever necessary. Should an accident occur, the Health and Safety Executive (HSE) will request copies of the risk assessments.
There are a number of laws and regulations that apply to health and safety in the manufacturing sectors including, but not limited to:
Health and Safety at Work etc. Act 1974 (HASAWA) – this part of the legislation is the primary regulations that all businesses must abide by. This Act sets out the general duties which:
- Employers have towards their employees and the members of the public
- Employees have to one another
- Self-employed have towards themselves and others.
The Lifting Operations and Lifting Equipment Regulations 1998 (LOLER). LOLER was created to ensure that all lifting operations conducted in the workplace that use lifting equipment are safe. LOLER requires that lifting operations are planned by a competent person. It stipulates that lifting operations must be supervised in an appropriate manner and performed by an employee who is able to complete the task safely.
The Dangerous Substances and Explosive Atmospheres Regulations, 2002 (DSEAR) state the legal requirements for managing the risk of fire, explosion or similar events arising from dangerous substances at the workplace.
It is a requirement of the Control of Substances Hazardous to Health Regulations (COSHH) for employers to assess all exposures to hazardous substances in the workplace and implement necessary control measures in order to protect their workers’ health.
Health and Safety (First Aid) Regulations 1981 – these regulations require employers to provide the following:
- Adequate first aid equipment and facilities
- A sufficient number of first-aiders
- A first aid appointed person, for when a first-aider is unavailable
Why is PPE Important
Personal protective equipment (PPE) protects workers from hazards such as trips, burns, electrocution, infections and falls. While there is some PPE that is universal to many occupations, staff working in manufacturing have certain PPE which is specific to their job.
This includes, but is not limited to:
- Breathing masks — These can prevent breathing in toxic chemicals. Depending on the setting, a simple paper mask or a more complex respirator may be required. Wearing a mask at work will also prevent long-term respiratory problems.
- Hard hats — These are essential in some manufacturing environments where there is a risk of objects falling from above. They protect the head from impact and help to prevent serious injuries.
- Fall protection — When working at heights, there is a risk of falling. Wearing fall protection, such as a harness, will help to prevent serious injuries if a fall occurs.
- Safety gloves – These should be specific to the manufacturing sector that workers are working in; for example, gloves used for food processing and production applications must be manufactured in such a way that any substances released pose no human health risk.
- Protective clothing — Many manufacturing sites require workers to wear protective clothing. This could include items such as gloves, head coverings, aprons, overalls, boots, non-slip footwear, footwear covers etc. and, in some sectors, can include full-body suits. The type of clothing needed will depend on the nature of the work being done.
- Face shields — Face shields provide additional protection for the face, eyes and mouth. They are often used in conjunction with safety glasses or goggles when manufacturing facilities are especially dangerous.
- Ear protection – Manufacturing facilities can be noisy, so it is important to protect workers’ hearing. Earplugs or earmuffs will help to reduce the noise levels that they are exposed to.
- Water bottles or easy access to water – This will ensure that workers are able to remain hydrated.
- Fire extinguishers — Fire extinguishers are essential in any workplace, but they are especially important in manufacturing facilities. Having a fire extinguisher close at hand can help to prevent serious injuries or damage to property.
- First aid kit — A first aid kit should be available in all workplaces, including manufacturing facilities. This is because accidents can happen at any time, and it is important to be prepared for them.
- Mobile phone – Delivery drivers require a method to maintain contact whilst working on the road.
A full risk assessment must be undertaken before it is decided which PPE should be worn by workers in the manufacturing industry.
What Training Should Workers in Manufacturing Take?
Depending upon their role, staff and management working within manufacturing will have completed training and qualifications specific to that role. In addition to their occupational training, manufacturing staff will need to participate in adequate health and safety training to ensure that they are competent to do their work. When manufacturing staff are trained to work safely, they should be able to anticipate and avoid injury from job-related hazards. Safety training is essential for all manufacturing employees appropriate to their role, and training should be directly applicable to the responsibilities and daily practices of the person being trained.
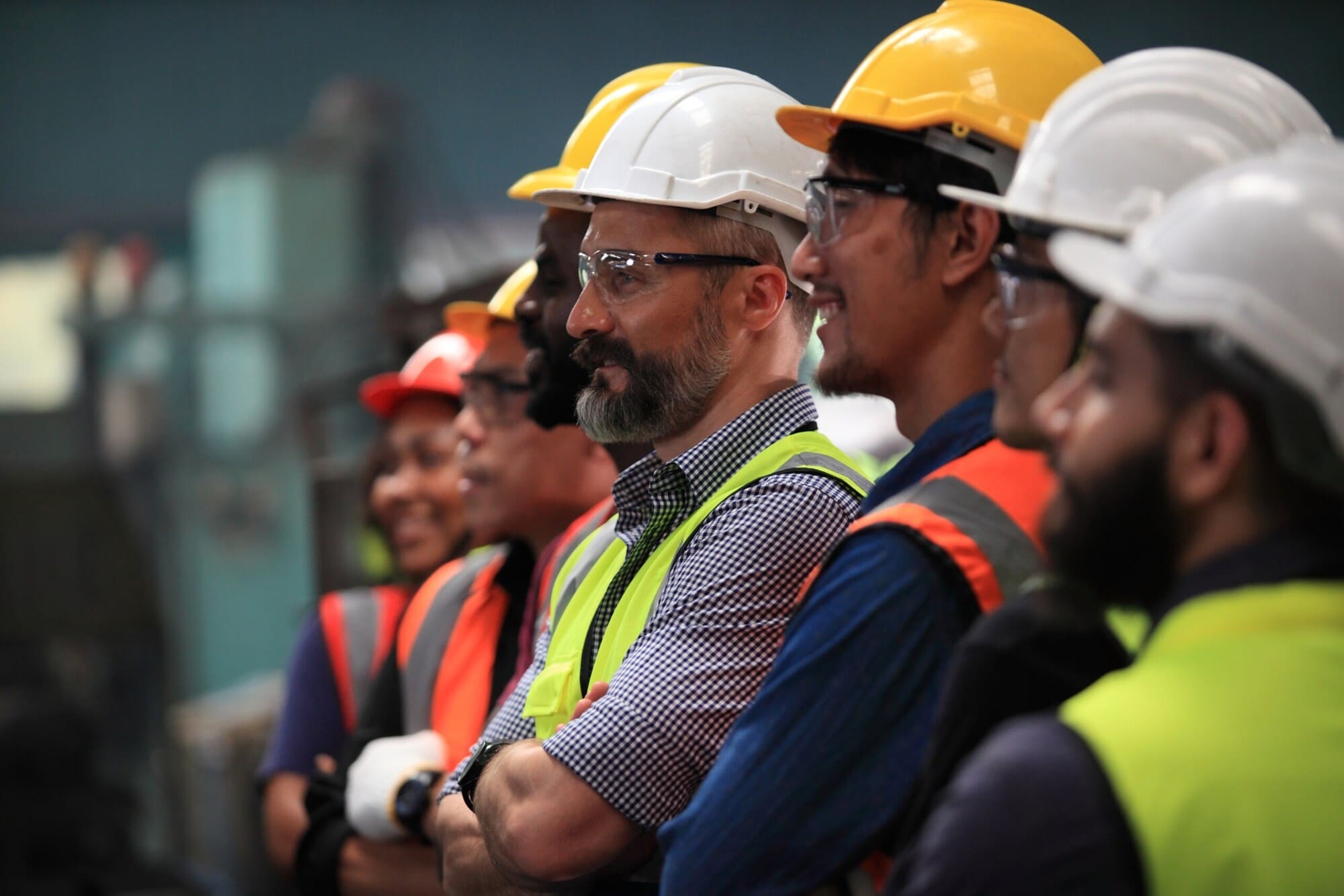
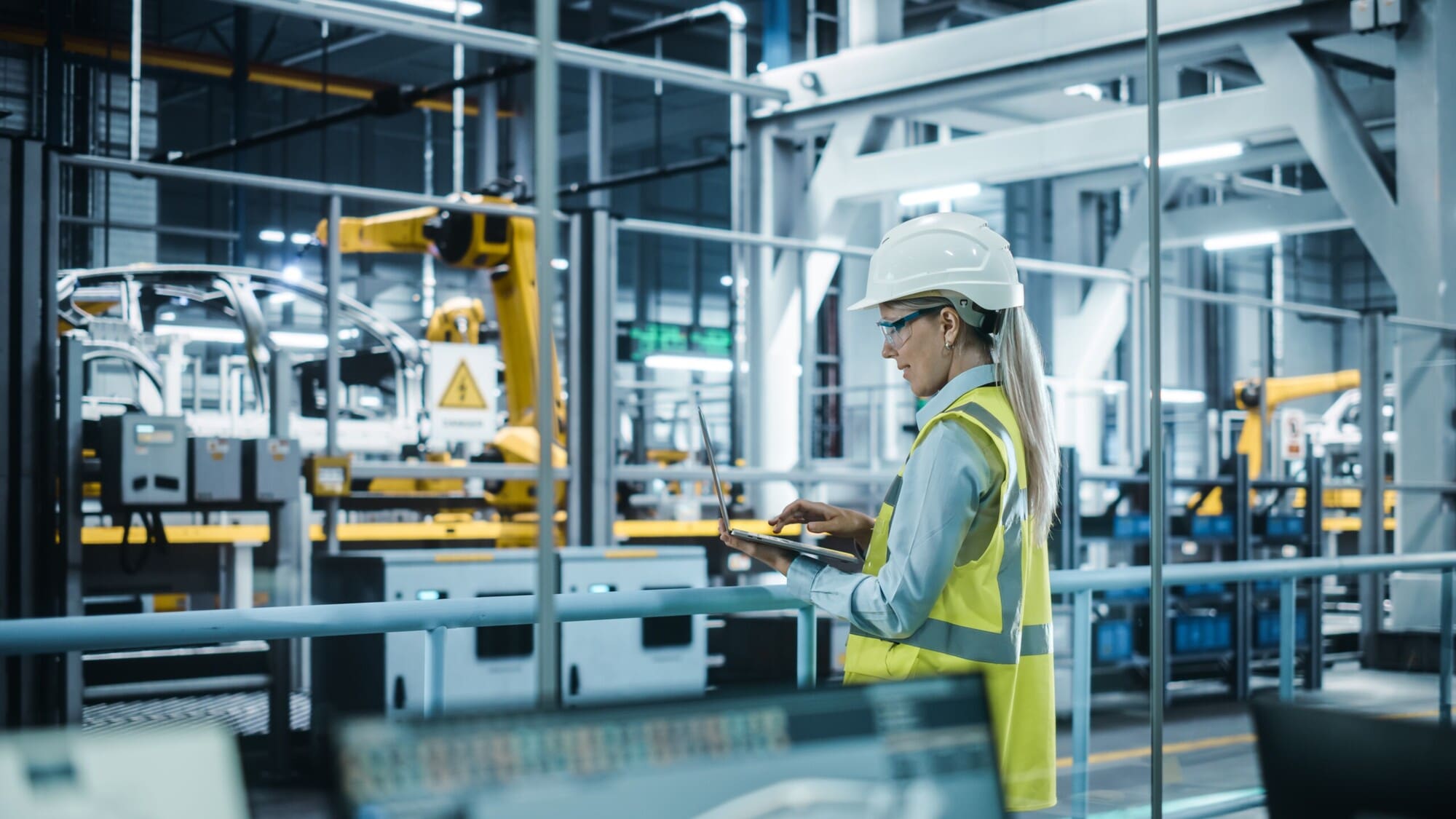
Training Courses
This training for manufacturing staff might include, but is not limited to:
- Health and Safety for Employees
- Health and Safety for Managers
- Manual Handling
- Workplace First Aid
- Working at height
- Slips, Trips and Falls
- Personal Protective Equipment (PPE)
- PUWER Awareness
- Ladder safety
- Assessing Risk
- Electrical Safety Awareness
- DSEAR Awareness
- Fire Safety Awareness
- COSHH Awareness
- Fire Warden
- LOLER
Everyone working in the manufacturing industry should at a minimum refresh their safety training at least every 2 years and participate in continuing professional development (CPD).