In this Health and Safety Guide for Labourers
Labourer is a term given to workers that are usually just starting out in their career on a construction site. This is an entry-level position, and is where most construction workers get their first opportunity to work in the industry. To get on most construction sites in the UK, labourers will need a valid CSCS card for the role. These cards are the industry-wide standard which prove suitability to perform the job safely on site. CSCS cards are not a legal requirement, but most businesses will demand their workers have one to ensure safety on their site. These cards prove to employers, supervisors and managers that labourers have completed the necessary training and have suitable knowledge to perform their job safely. As there are countless safety hazards on construction sites that need to be overcome on a daily basis, labourers will need to maintain their own safety, as well as the safety of the area and the people around them.
What is The Role of a Labourer?
A labourer is a person who does manual work within the construction industry. A labourer performs various tasks on a construction site to complete a building project. Their duties include following instructions, carrying out manual jobs and ensuring safety on site. A labourer’s duties vary depending on the project, but they must be familiar with certain equipment and techniques that are common to various construction sites.
Some of their most common responsibilities include:
- Following instructions from supervisors to perform manual labour tasks such as digging, stacking up goods etc.
- Handling and transporting materials, e.g. cement etc. and equipment, e.g. drills and grinders etc.
- Helping with setting up and transferring temporary structures, e.g. scaffolding
- Assisting bricklayers, welders, carpenters, painters or other tradespeople on-site
- Putting up warning signs, signposts, cones etc. for vehicles and passers-by
- Directing traffic near building sites
- Performing set up and clean up tasks at the job site
- Climbing to heights and conducting work with proper safety restraints
- Maintaining tools and equipment
- Constructing roads and paths
- Driving forklifts
- Reporting issues with equipment or unsafe conditions
- Performing general maintenance of construction equipment and vehicles
- Lifting heavy loads and navigating construction job site terrain
- Digging pits, trenches and foundations in preparation for job site construction
- Providing labour as needed for a speciality crew
- Putting up panels to hold concrete in place
- Operating heavy machinery, such as excavators and dumper trucks
The above list is not exhaustive. Whatever the environment they work in, a labourer will be responsible for ensuring the safety of their work, tools and any equipment to protect the safety of themselves and other people.
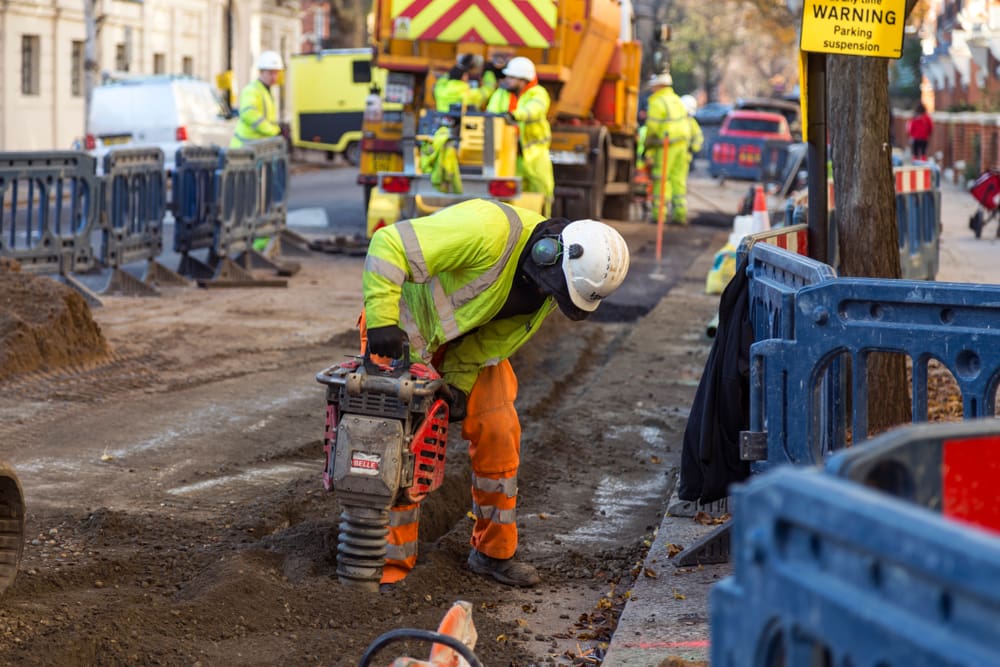
What Are The Main Health and Safety Risks Labourers Can Encounter?
Manual handling injuries have a major impact on all workplaces and sectors, costing the economy hundreds of millions every year. Manual handling encompasses a wide range of actions including lifting, lowering, pulling, pushing, and carrying awkward and heavy objects; the risks are endless for labourers whose role involves regularly lifting, carrying and handling material loads and equipment, and who may experience manual handling injuries such as:
- Back injuries
- Hernias
- Musculoskeletal disorders (MSDs) such as shoulder strain
- Repetitive strain injury (RSI) such as wrist strain
- Soft-tissue injuries to the wrists, arms, shoulders, legs or neck
- Long-term pain in the arms, legs or joints
The first step in reducing manual handling risk is to train staff to carry out their work safely. It means avoiding hazardous manual handling and using machines or equipment to move or lift loads.
Slips, trips and falls are one of the top three causes of non-fatal work injuries involving days away from work. Each year they cause thousands of preventable injuries, as they can cause various injuries such as bruises, sprains, scrapes, broken bones and head traumas. According to the Health and Safety Executive (HSE) several thousand construction workers are injured each year following a trip or slip whilst at work on a building site. Around 1,000 of these injuries involve someone fracturing bones or dislocating joints.
Key aspects of construction slips and trips include:
- Uneven surfaces
- Obstacles
- Trailing cables
- Wet or slippery surfaces
- Changes in level
Slips and trips affect the whole workplace, so everyone should work to eliminate them by cleaning up spills or debris, even if they did not cause them. Dispose of all debris safely in a skip, bin or designated areas for waste collection, as the debris may contain nails or other sharp objects. Keep work area floors clean, orderly, and dry and keep surfaces free of hazards such as sharp objects, loose boards, corrosions, leaks, spills, snow and ice. Signpost any slippery areas and make sure footwear with a good grip is worn; we will look at PPE later in this guide.
Labourers often have to perform a number of tasks at heights. Falling from height can cause serious or even fatal injury. Labourers should exercise every precaution when working at height. For those working on ladders, scaffolding or any other type of access equipment falls from heights are a risk that needs to be taken into consideration. Using framed scaffolds offer several advantages over using ladders by providing a wider, more stable work platform. Working from scaffolding with a wide work platform is much easier and safer than working from a ladder.
Working at height can also pose risks for others, as a worker falling from a height may injure anyone below when they fall. Avoid working directly underneath someone else where possible, and ensure that any tools or materials kept at a height are well secured so they can’t fall or cause harm.
When working at height, always change tools in secure areas where there is no risk of letting the tools fall, and don’t use tools without attaching them to a work belt when working at height. Tools being used at height should regularly be checked for damage and that there is no damage to lanyards, carabiners, attachment rings or belts.
Construction sites are places of constant movement of vehicles, machinery and equipment. As the building site develops the risks associated with it increase accordingly. Labourers should be trained to keep vigilant and aware of their surroundings and to avoid hazards.
Sources of risk from moving objects for labourers include:
- Working close to moving objects
- Poor working light
- Heavy-duty vehicles
- Overhead lifting equipment
- Little space to manoeuvre
Dust exposure including brick dust or silica is a major hazard to labourers and other workers on construction sites. Silica is a natural substance found in varying amounts in most rocks, sand and clay. For example, sandstone contains more than 70% silica, whereas granite might contain 15-30%. Silica is also a major constituent of construction materials such as bricks, tiles, concrete and mortar. Construction workers generate dust from these materials during many common construction tasks, which include cutting, drilling, grinding and polishing, and labourers working in the vicinity could be affected. Some of this dust is fine enough to get deep into the lungs. The fine dust is known as respirable crystalline silica (RCS) and is too fine to see with normal lighting. Silica is the biggest risk to construction workers after asbestos and the amounts needed to cause this damage are not large.
Heavy and prolonged exposure to RCS can cause lung cancer and other serious respiratory diseases such as:
- Silicosis – this can cause severe breathing problems and increases the risk of lung infections. Silicosis usually follows exposure to RCS over many years, but extremely high exposures can cause acute silicosis more quickly
- Chronic obstructive pulmonary disease – this is a group of lung diseases including bronchitis and emphysema. It results in severe breathlessness, prolonged coughing and chronic disability. It can be very disabling and is a leading cause of death. Around 4,000 deaths are estimated annually due to COPD resulting from workplace exposures in the past. Construction workers are a significant at-risk group within this.
HSE figures show that 800 people lose their lives to cancer every year because they inhale hazardous dust particles. A further 39,000 suffer from respiratory illnesses caused by the same particles.
Mortar is the material commonly used with bricks and blocks, to bond them together. Contact with wet cement products such as mortars is a major cause of skin health issues suffered by labourers in construction. Such contact with wet concrete, or other cement-based materials such as mortars and renders, can lead to skin diseases such as dermatitis and burns or rashes. Mortar also contains crystalline silica, mostly as quartz, which if breathed in as a very fine crystalline silica dust can lead to the development of silicosis.
Sanding and planing wood by carpenters on a construction site creates wood dust, and labourers working alongside carpenters risk breathing it in; it can cause nasal cancer, serious lung problems and asthma. Both hardwood and softwood dusts have a Workplace Exposure Limit (WEL) which must not be exceeded. The WEL for hardwood dust is 3mg/m3 (based on an 8-hour time-weighted average). The WEL for softwood dust is 5mg/m3 (based on an 8-hour time-weighted average). For mixtures of hardwood and softwood dusts the WEL for hardwood dust of 3mg/m3 applies to all wood dusts present in that mixture. Employers must provide dust extraction, also known as local exhaust ventilation or LEV, at woodworking machines to capture and remove dust before it can spread.
Wood dust, shavings, chips or slivers can also cause injuries to the eyes or skin through splinters. Labourers are at the most risk from flying debris from the chipping, chiselling, drilling, grinding, sanding and sawing of wood. Even a tiny splinter of wood can cause severe eye damage.
The Control of Substances Hazardous to Health Regulations 2002 (COSHH) adopts workplace exposure limits (WELs) that apply to the concentration of the hazardous substances in the air, averaged over a specified period of time and referred to as a time-weighted average (TWA). WELs are published regularly by the HSE, specifying the current limit values.
Irritant contact dermatitis is the most common cause of occupational contact dermatitis amongst labourers. Continual wetting and drying of the skin, as well as handling some particular substances, will cause the skin to dry out, flake, split and crack. This will occur more commonly in people with sensitive skin, especially those with a history of eczema.
Common irritants in the construction industry that can affect labourers include, but are not limited to:
- Cement/mortar
- Water, including washing hands frequently
- Abrasive hand cleaners
- Solvents
- Silica dust
- Dirt
- Putty and sealants
- Detergents
- Heat and sweating
- Friction, from using machinery
Asbestos was especially useful in insulation such as for pipe lagging and boilers, and can commonly be found in any building that was constructed before the year 2000, so labourers may encounter asbestos during the course of their work. According to the Health and Safety Executive (HSE) asbestos kills around 5,000 workers each year – this is more than the number of people killed on the road – and around 20 trades workers die each week as a result of past exposure.
When materials that contain asbestos are disturbed or damaged, fibres are released into the air. When these fibres are inhaled, they can cause serious diseases. These diseases will not affect you immediately as they often take a long time to develop, but once diagnosed, it is often too late to do anything.
Many cases of inadvertent, short-term exposure to asbestos will most likely have led to minimal exposure to fibres, with little likelihood of any long-term ill health effects. If you are concerned about possible exposure to asbestos from work activities, you are advised to consult your GP and ask for a note to be made in your personal record about possible exposure, including date(s), duration, type of asbestos and likely exposure levels, if known.
The Reporting of Injuries, Diseases and Dangerous Occurrences Regulations 2013 (RIDDOR) place duties on employers, the self-employed and people in control of work premises (the responsible person) to report certain serious workplace accidents, occupational diseases and specified dangerous occurrences (near misses). Exposure to asbestos is reportable under RIDDOR when a work activity causes the accidental release or escape of asbestos fibres into the air in a quantity sufficient to cause damage to the health of any person. Such situations are likely to arise when work is carried out without suitable controls, or where those controls fail.
Workers must be able to recognise asbestos-containing materials (ACMs) and know what to do if they come across them in order to protect themselves and others. Training for asbestos awareness is intended to give workers the information they need to avoid work that may disturb asbestos during any normal work which could disturb the fabric of a building, or other items which might contain asbestos. If a worker is planning to carry out work that will definitely disturb ACMs, further specific information, instruction and training will be needed. Asbestos awareness training is a requirement of regulation 10 of the Control of Asbestos Regulations (2012), and the supporting Approved Code of Practice L143 Managing and Working with Asbestos.
Repetitive vibration caused by power tools can severely damage workers’ nerves and blood vessels. Hand and Vibration Syndrome (HAVS) is a common injury in the construction industry. If untreated, it can affect dexterity and grasps.
Construction sites in particular can be problematic when it comes to hazardous noise levels. Excessive noise affects virtually all construction projects, and the louder an environment is, the harder it is to hear incoming hazards. Repeated exposure to loud noise can lead to permanent tinnitus and/or hearing loss.
The Control of Noise at Work Regulations 2005 and the Control of Vibration at Work Regulations 2005 apply to all construction sites.
Labourers can also sustain injury from poor, damaged or inadequate equipment. Ensuring tools are in proper working condition is key to ensuring safety on a job. Inspect all equipment before use and only use if in good working order. Keep cutting equipment sharp to ensure optimum use and cut away from the face and body to prevent injury. Store all equipment in a safe place to ensure it doesn’t fall into the wrong hands and doesn’t become a hazard in the workplace.
The Provision and Use of Work Equipment Regulations 1998 (PUWER) place duties on people and companies who own, operate or have control over work equipment. PUWER also places responsibilities on businesses and organisations whose employees use work equipment, whether owned by them or not.
PUWER requires that equipment provided for use at work is:
- Suitable for the intended use.
- Safe for use, maintained in a safe condition and inspected to ensure it is correctly installed and does not subsequently deteriorate.
- Accompanied by suitable health and safety measures, such as protective devices and controls. These will normally include emergency stop devices, adequate means of isolation from sources of energy, clearly visible markings and warning devices.
- Used in accordance with specific requirements.
Generally, any equipment which is used by an employee at work is covered by PUWER, for example hammers, knives, ladders, drilling machines, power presses, circular saws, photocopiers, lifting equipment (including lifts), dumper trucks and motor vehicles. Similarly, workers providing their own equipment will be covered by PUWER and it will need to comply.
Electricity has long been recognised as a severe health hazard in the workplace, and injuries can be caused by direct contact with the power source or indirectly through contact with live equipment or wiring. Using mechanical plant and any equipment in the vicinity of overhead or buried electrical cables, and underground gas mains, presents a very serious hazard of exposure to electricity via overhead and underground cables, and special precautions must be taken by all concerned.
Collapses are a familiar occurrence at construction and demolition sites due to the nature of the work. The risk of workers being injured or killed is serious. In the first quarter of 2019–2020, 15 deaths were due to collapses. Labourers working in and around excavations are particularly at risk, as several things can happen, such as the area around an excavation becoming unstable, resulting in collapse when extra loads are applied such as scaffolding or vehicles, the labourer could fall into the excavation or sustain injury from falling materials when the integrity of the excavation itself collapses or the integrity of nearby structures is undermined causing them to collapse.
Labourers are exposed to the elements during the course of their work. Too much sunlight, even on cool days, is harmful to the skin. In the short term, even mild reddening of the skin from sun exposure is a sign of damage. Sunburn can blister the skin and make it peel and longer-term problems can arise. Exposure to too much sun speeds up ageing of the skin, making it leathery, mottled and wrinkled. The most serious effect is an increased chance of developing skin cancer.
Labourers should use a high factor sunscreen of at least SPF15 on any exposed skin and, if possible, wear a hat with a brim or a flap that covers the ears and the back of the neck. They should also drink plenty of water to avoid dehydration. Dehydration is an issue for any construction project, and labourers should drink plenty of water to avoid dehydration and keep from working at midday when it is hottest, if possible. On hot, sunny days, workers should take frequent breaks to prevent overexertion and heat exhaustion.
Risk Assessments
Maintaining a safe work environment is important, particularly in the high-risk work environment faced by labourers. It is important that every hazard is met with elimination or, at the minimum, a control measure to mitigate any potential risk.
Under the Management of Health and Safety at Work Regulations (1999), the minimum a business must do is:
- Identify what could cause injury or illness in your business (hazards)
- Decide how likely it is that someone could be harmed and how seriously (the risk)
- Take action to eliminate the hazard or, if this isn’t possible, control the risk
Risk assessment requires making a judgement on Risk Severity. Risk Severity = probability of risk materialising x impact of risk on, for example, a person or people, a business, a property etc.
Probability may be understood as:
- Low (Level 1) – a reasonably informed person would think it very unlikely this risk would materialise in the foreseeable future.
- Medium (Level 2) – a reasonably informed person would think there is a significant possibility this risk would materialise in the foreseeable future.
- High (Level 3) – a reasonably informed person would think there is a very significant or even likely possibility the risk would materialise in the foreseeable future.
Impact may be understood as:
- Low (Level 1) – any impact that is minimal, having regard to the importance of interests affected, impairment of function and duration. Typically, the impact is isolated and short-lived.
- Medium (Level 2) – any impact that is significant, having regard to the importance of interests affected, impairment of function and duration. Typically, the impact is limited to one function or group, but there is a material operational impact and the effects may continue.
- High (Level 3) – any impact that is severe, having regard to the importance of interests affected, impairment of function and duration. Typically, the impact impairs a critical function and/or has a systemic impact and the effects may be long-lasting or permanent.
Labourers must ensure an assessment has been made of any hazards, which covers:
- What the potential hazard is – the risk assessment should take into consideration, for example, the type of equipment used, the way in which it is used and the environment it is used in
- Who, or what could be harmed by the hazard
- How the level of risk has been established
- The precautions taken to eliminate or control that risk
Managing risk is an ongoing process that is triggered when changes affect a labourer’s work activities; changes such as, but not limited to:
- Changing work practices, procedures or the work environment
- Purchasing new or used equipment or using new substances
- Workforce changes
- Planning to improve efficiency or reduce costs
- New information about the workplace risks becomes available
Risk assessments should be recorded and records regularly reviewed and updated whenever necessary. Should an accident occur, the Health and Safety Executive (HSE) will request copies of the risk assessments.
Why is PPE Important
Personal protective equipment (PPE) protects workers from hazards such as trips, burns, electrocution and falls. While there is some PPE that is universal to many trades, labourers have certain PPE which is specific to their job.
This includes:
- Bump caps – hard yet lightweight head covering to protect from knocks to the head. Head protection is required by law on all construction sites where there is a risk of head injury. It is also important to inspect the safety helmet on a daily basis to ensure that the structure and various components – that is, the outer shell, chin strap and visor – are in good condition to ensure adequate head protection.
- Face masks and respirators – prevent potentially inhaling substances, such as silica or mortar dust. For proper use and to ensure compliance, be sure to fit test the respirator, undergo formal training, always make sure it is clean and never borrow or use another worker’s respirator.
- Safety goggles/glasses – the use of eye protection can stop harmful debris from entering the eyes such as flying cement particles or mortar dust which can cause serious eye injuries or even blindness.
- Hearing protection – construction sites are loud and labourers are often exposed to much of this noise. Failure to wear dedicated hearing protection equipment such as noise-cancelling headphones, earplugs or earmuffs, either reusable or disposable, can lead to severe damage to the eardrum, tinnitus or even irreversible hearing loss in one or both ears.
- Gloves – wearing gloves helps ensure a stable grip when working. They also protect the hands against harsh chemicals.
- Footwear – it is common for labourers’ PPE requirements to include safety-toe footwear that protects against risks of collapsing walls or falling objects. PPE footwear should be slip-resistant and have puncture-resistant soles.
- Protective clothing – labourers should wear the correct protective clothing to match the working conditions and the potential risks of each situation. An example is trousers with removable knee pads which are highly recommended to protect joints and improve comfort when performing jobs involving kneeling.
- Highly-visible vests or reflective clothing – particularly important when working outside in low light and poor visibility conditions. Reflective workwear must fit properly and meet ISO EN 20471:2013 for high-visibility warning clothing. Hi-vis clothing should be comfortable, non-restrictive and provide good visibility during the day, at night, and in poor weather conditions.
- Fall protection – while the risk of falling is rare, it is not unheard of, so a labourer’s PPE should include fall protection equipment depending on the job site and the structures in place. When carrying out specific jobs where there is a risk of falling from a height, labourers might use, for example, a full harness, a retractable type fall arrester, a lanyard with shock absorber, anchor points and/or connectors.
- Sunscreen – labourers should use sunscreen with SPF minimum 30 UVA protection or higher, 20 minutes before going outside. It doesn’t matter if they are working in the heat or not, labourers still need to wear sunscreen for sun protection; the shade from a hard hat isn’t enough as UV radiation from the sun penetrates clouds and glass.
A full risk assessment must be undertaken before it is decided which PPE should be worn by the labourer.
What Training Should Labourers Take?
When labourers are trained to work safely, they should be able to anticipate and avoid injury from job-related hazards. Safety training is essential for all labourers appropriate to their role, and training should be directly applicable to the responsibilities and daily practices of the person being trained.
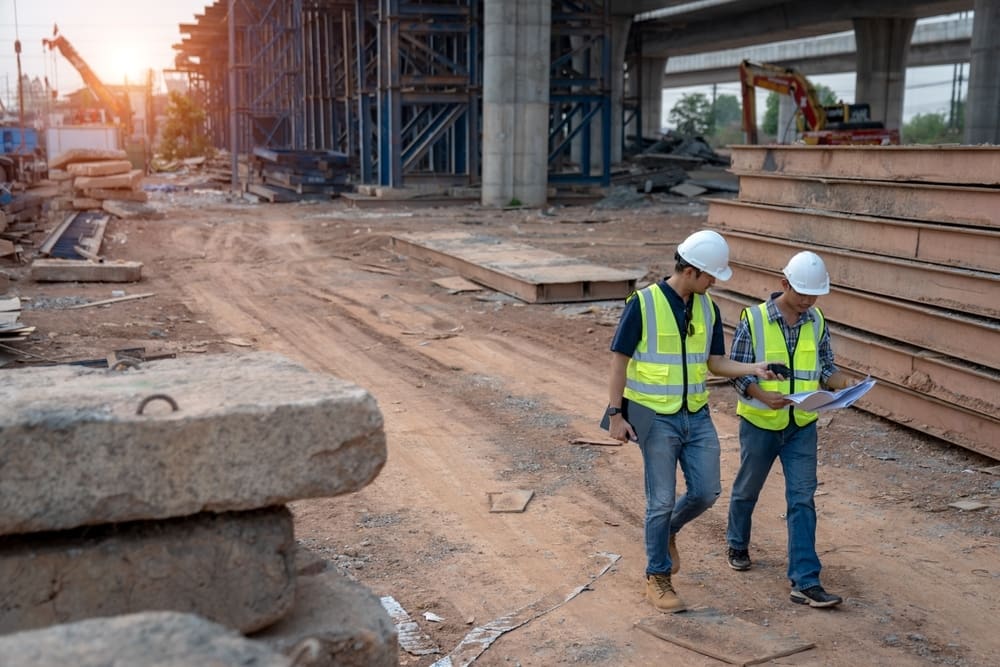
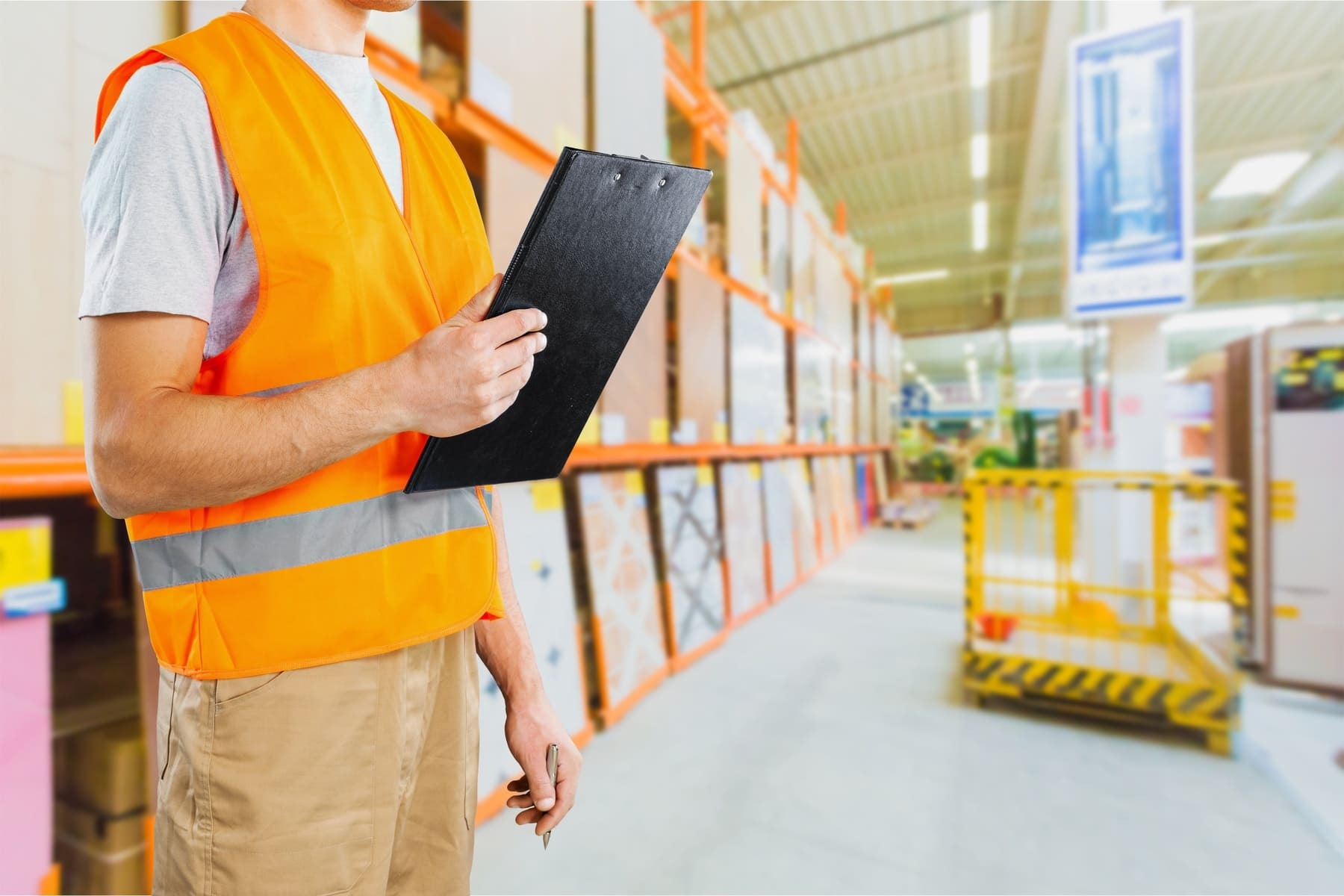
Training Courses
This training for labourers might include, but is not limited to:
- HAVS (Hand-Arm Vibration Syndrome) Training
- Health and Safety for Employees
- Manual Handling
- Workplace First Aid
- COSHH Awareness
- Working at height
- Slips, Trips and Falls
- Personal Protective Equipment (PPE)
- PUWER Awareness
- Noise Awareness
- Assessing Risk
- RIDDOR Awareness
- Electrical Safety Awareness