In this Health and Safety Guide for Electricians
Electricity has long been recognised as a serious workplace hazard and working with electricity can be dangerous. Electricians carry out work on or near electrical equipment therefore they should be able to anticipate and avoid injury to themselves and others from job-related hazards.
What is the Role of an Electrician?
Being an electrician can be a wide-ranging and varied job. Electricians can design, install, inspect, test and use electrical equipment, providing buildings with energy to light rooms, heat water and power devices, making sure they are working properly and safely. Some electricians install and maintain traditional systems in homes, shops and offices, whilst others work with renewable technology or fibre-optics; others service motors, transformers, street lighting or traffic systems, or work on engineering projects.
More specifically, an electrician might, for example, be involved in:
- Following technical plans
- Laying cables to connect equipment to power and computer networks
- Connecting sockets, switches, light fittings and appliances
- Fixing electrical faults or replacing parts
- Inspecting electrical systems, wiring and equipment to ensure they are safe and functioning properly
- Producing electrical designs
- Making and installing electrical control panels
- Installing security or data network systems
- Responding to emergency call-outs such as power cuts
- Maintaining electrical motors, transformers and machinery
- Working on construction sites, in domestic or commercial settings, or offshore
- Often working in cramped conditions or at height
- Adhering to strict safety regulations and adhering to electrical legislation
The above list is not exhaustive. Whatever the environment they work in, an electrician will be responsible for ensuring the safety of electrical equipment to protect the safety of themselves and other people.
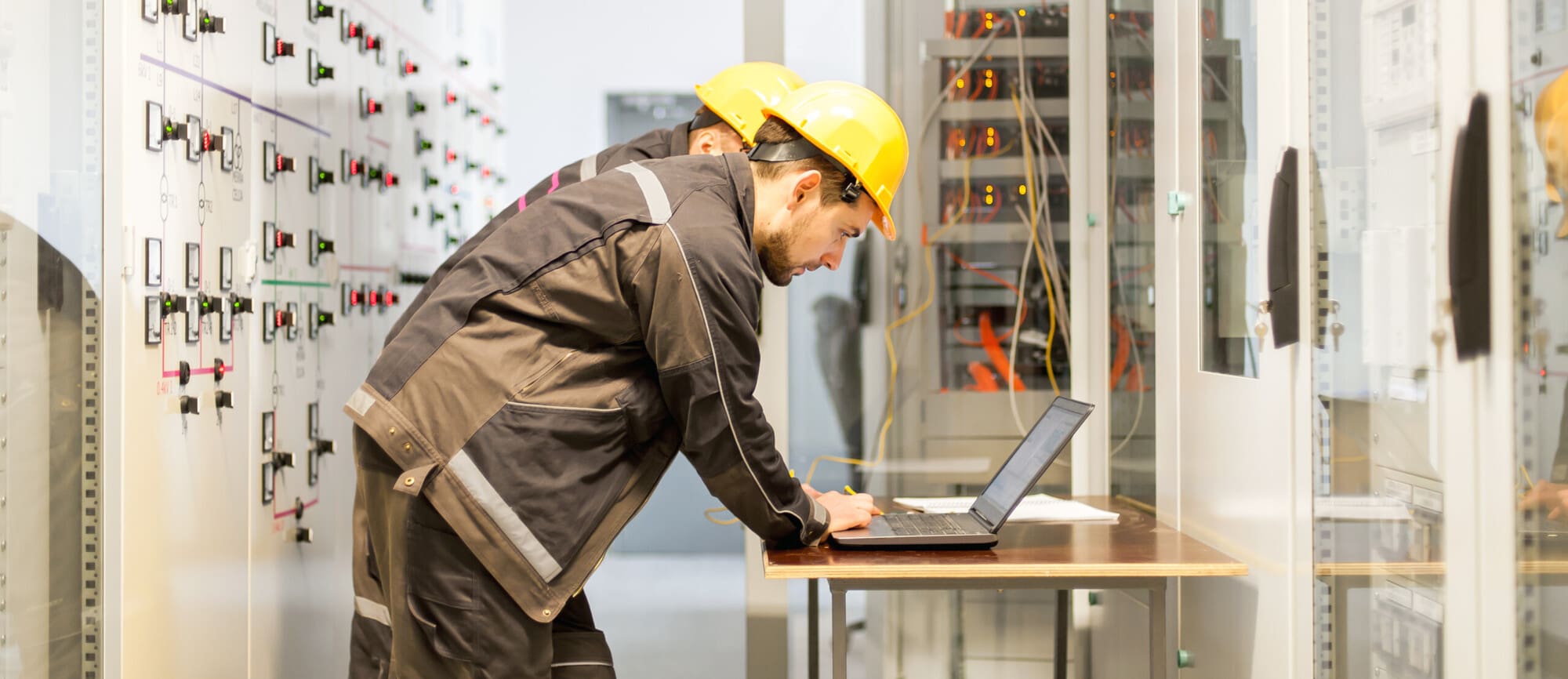
What are the Main Hazards of Working with Electricity?
There are many potential electrical hazards present in an electrician’s work environment which could lead to severe injury or even death. Electrical incidents may occur, for example, from contact with power lines. Overhead and buried power lines at a construction site are especially hazardous because they carry extremely high voltage. Fatal electrocution is the main risk, but burns and falls from elevations are also hazards. Using tools and equipment that can come into contact with power lines increases the risk. Additionally, there are risks of injury from exposure to arcing, which is when electricity jumps from one circuit to another.
The wear and tear of equipment that results in insulation breaks, short-circuits, and exposed wires can send current through the body, resulting in electrical burns, explosions, fire, or death. The normal wear and tear on extension and flexible leads can loosen or expose wires, creating hazardous conditions. Additionally, if electrical equipment, including extension and flexible leads, is used in ways for which it is not designed you can no longer depend on the safety features built in by the manufacturer. This may damage the equipment and cause injuries.
The types of injury that may occur from faulty or mishandling electrical equipment include:
- Shock – if wiring or equipment is not properly grounded shocks can occur when a person makes direct contact.
- Burns – these have the potential to cause severe disfigurement and can be extremely serious and damaging. Burns injuries generally occur in the feet and hands as this is where the current enters and leaves the person’s body.
- Electrocution – electrocution can be fatal. If equipment is poorly installed or insulated it may result in electrocution.
- Falls – if a shock happens when installing, maintaining or using electrical equipment at height, secondary injuries such as head injuries or broken or fractured bones may occur and some falls may be fatal.
The risk of fire is also a potential hazard for those working with electrical equipment. Fire may occur from faulty electrical equipment, installations, explosions, or unsuitable electrical apparatus, or static electricity may ignite flammable vapours or dusts, for example in a spray-paint booth.
What Precautions Need to Be Taken When Working with Electricity?
As with any job, the first and most essential step to staying safe is to wear appropriate PPE. We will look in more detail at the type of PPE recommended for electricians later in this guide.
Double-check the electricity/gas is turned off at the mains before starting work on the wiring, or a piece of equipment connected to it. With gas lines, the entire building’s supply must be turned off before proceeding. Put up danger notices where there are still live electrical circuits.
Don’t use steel ladders – if you get even the slightest shock of electricity, the whole current will pass through your body and you may risk death. So, make sure that you are using a wooden ladder or any other insulated ladder that won’t let the current pass through it.
Always use insulated tools while working.
Always use a cable locator to find buried or hidden services and permanently mark the position of the services you do find.
Never use broken equipment and never deal with frayed leads, broken plugs, and damaged insulations.
Never deal with electricity with bare or wet hands and make sure your body is also dry. Water is a good conductor of electricity and you might get an electric shock.
Risk Assessments
Under the Management of Health and Safety at Work Regulations (1999), the minimum a business must do is:
- Identify what could cause injury or illness in your business (hazards)
- Decide how likely it is that someone could be harmed and how seriously (the risk)
- Take action to eliminate the hazard or, if this isn’t possible, control the risk
Risk assessment requires making a judgement on Risk Severity. Risk Severity = probability of risk materialising x impact of risk on, for example, a person or people, a business, a property etc.
Probability may be understood as:
- Low (Level 1) – a reasonably informed person would think it very unlikely this risk would materialise in the foreseeable future.
- Medium (Level 2) – a reasonably informed person would think there is a significant possibility this risk would materialise in the foreseeable future.
- High (Level 3) – a reasonably informed person would think there is a very significant or even likely possibility the risk would materialise in the foreseeable future.
Impact may be understood as:
- Low (Level 1) – any impact that is minimal, having regard to the importance of interests affected, impairment of function and duration. Typically, the impact is isolated and short-lived.
- Medium (Level 2) – any impact that is significant, having regard to the importance of interests affected, impairment of function and duration. Typically, the impact is limited to one function or group, but there is a material operational impact and the effects may continue.
- High (Level 3) – any impact that is severe, having regard to the importance of interests affected, impairment of function and duration. Typically, the impact impairs a critical function and/or has a systemic impact and the effects may be long-lasting or permanent.
Electricians must ensure an assessment has been made of any hazards, which covers:
- What the potential hazard is – the risk assessment should take into consideration the type of electrical equipment used, the way in which it is used and the environment it is used in
- Who or what could be harmed by the hazard
- How the level of risk has been established
- The precautions taken to eliminate or control that risk
Managing risk is an ongoing process that is triggered when changes affect an electrician’s work activities; changes such as, but not limited to:
- Changing work practices, procedures or the work environment
- Purchasing new or used equipment or using new substances
- Workforce changes
- Planning to improve efficiency or reduce costs
- New information about the workplace risks becomes available
Risk assessments should be recorded and records regularly reviewed and updated whenever necessary. Should an accident occur, the Health and Safety Executive (HSE) will request copies of the risk assessments.
Making Sure Own Electrical Equipment is Safe
Electricity and the use of electrical equipment presents a significant risk, so electricians need to ensure that all tools and equipment that they use in the course of their job is fit for purpose. Electrical tools are tools used to work on an electrical system. These can include a wide range of tools such as wire and cable cutters, wire strippers, coaxial compression tools, telephony tools, cable tie tools, accessories, and even more. Speciality tools are designed for a very specific purpose. They are tools that are able to perform tasks that other tools cannot achieve, which includes things like heat tools and compression tools. It is imperative that all electrical equipment has been PAT tested and other tools are inspected regularly to ensure safety.
The Importance of PAT Testing
All equipment that uses a flexible wire or cable to connect to a power supply qualifies as a portable appliance and needs to be checked. Portable appliance testing (PAT) is the term used to describe the examination of electrical appliances and equipment to ensure that they are safe to use.
Most electrical equipment safety defects can be found by visual examination but some types of defect can only be found by testing. A PAT test involves a visual inspection to check the appliance casing and flex for wear or damage. Plugs are also checked for damage, correct wiring and to ensure that the correct fuse rating has been used.
After the equipment has passed a visual inspection it will normally undergo a series of electrical tests using a fully calibrated electrical PAT tester. A label will be attached to each appliance indicating the test results. Any item failing the tests will be easily identifiable and should be removed from service until repaired. You should record and retain the results of all PAT testing in an appliance register for future reference.
Electrical appliances are mainly categorised as Class 1, 2 or 3, with Class 1 being the most dangerous and Class 3 the least dangerous. Class 3 appliances include equipment such as laptops or mobile phones. These appliances are low voltage items, and they are the safest class of electrical appliance and may not require PAT testing; however, their charging leads may need to be PAT tested. Class 2 appliances include items such as electrical drills, TVs or computer printers. This type of electrical equipment has extra insulation and so does not rely on an earth for protection, which makes it safer than Class 1 equipment. Class 1 appliances include equipment such as industrial machinery, office type equipment such as photocopiers and laptop leads, and many items of kitchen equipment such as microwave cookers, dishwashers or refrigerators.
The frequency of PAT testing is determined by several factors. This includes the type of equipment and its classification, the frequency it is used and/or moved and the environment in which it is operating. PAT testing should be carried out, at the very least, every 2 years; however, in some environments and with some categories of equipment this may need to be done every time the equipment is moved.
The Health and Safety Executive (HSE) recommends taking the following into consideration as necessary:
- Manufacturer’s recommendations
- The age of the equipment
- Frequency of use of the equipment
- Foreseeable misuse of the equipment
- Effects of any modifications or repairs
- The history of the item
At present you don’t have to be a qualified electrician in order to PAT test; however, from 1st June 2020 the Landlord Electrical Safety Certificate Legal Requirement stated that all PAT testing in rental properties must be checked by a qualified electrician to ensure that equipment and appliances are safe and that subsequent testing must then be carried out on a five-yearly basis.
Ensuing Electricity is Turned Off Before Starting
The electrical power should be turned off to allow you to do work safely, and it is essential that the power stays off until you have finished the work. Doing this and testing to be sure the power is off is the only way to prevent dangerous shocks. Even after shutting off the power, always act as if the wires are live. That way if someone accidentally turns on the power or a tester gives the wrong reading, you are still protected.
Test for the presence of power using a voltage tester. To do this properly, follow the manufacturer’s instructions. It is good practice to test the tester, too. Touch the probes to a live circuit to make sure the indicator bulb lights are working properly. Test all wires; it is good practice to touch the bare end of a wire only with an insulated tool, not your fingers.
Communication
Electricians must be good communicators. They have to be able to listen, ask the right questions, and then communicate with their co-workers to chart out a course of action and ensure safety. They must be able to instruct them in precise and clear terms, so that they understand what needs to be done.
Good communication skills are also essential because electricians are often dealing with people who do not have a working knowledge of electrical systems. They must be able to understand what their customers are saying even if they do not say it in precise technical jargon.
Why is PPE Important
Personal protective equipment (PPE) protects workers from hazards such as trips, burns, electrocution and falls. While there is some PPE that is universal to many trades, electricians have certain PPE which is specific to their job. The biggest risk posed to an electrician is that they might come into contact with electricity; in these cases, electrical PPE clothing is a great line of defence.
This includes:
- Bump caps – a hard yet lightweight head covering to protect from knocks to the head, such as from items falling from service voids and ducts.
- Safety trainers – an alternative to steel toe-cap boots, they offer greater sensations underfoot on ladders and steps, helping electricians judge their step better while retaining the same insulation against electricity.
- Electricians’ gloves – cut-resistant gloves through which the electrician can still feel and grip through, while offering a reasonable amount of insulation against shocks.
- Safety glasses – specially made glasses are essential for long- or short-sighted electricians.
- Filtering dust mask – for protection against accidental asbestos exposure.
- Avoid wearing anything conductive such as metal bracelets or jewellery, especially since they could get caught inside machinery while they are being worn.
- For working with gas – a gas detection system will let you know when there is a gas leak before you smell it.
- If appropriate, wear clothing designed to protect against electric arc, or flame-retardant clothing.
A full risk assessment must be undertaken before it is decided which PPE should be worn by the electrician.
Identifying Cable Colours
In 2006, the wiring colour designations within the UK were harmonised with countries in mainland Europe to fulfil the specification of international standard IEC 60446 and to provide consistency and the avoidance of confusion. Wiring colour code changes mean that any fixed mains-powered and electrical cable following the introduction of the new wiring, and any flexible cabling, now feature identical colour wires.
Prior to 2006, the UK old wiring colour was:
- Black (neutral)
- Red (live)
- Green and yellow (earth)
Also note that prior to 1977, the earth wire was green. Since 2006, the UK wiring colour is:
- Blue (neutral)
- Brown (live)
- Green and Yellow (earth)
The neutral wire transfers electricity away from the appliance to avoid overloading. It is located at the circuit end to enable connection once electricity has flowed around the earth and live wires. It is highly unlikely that you will have an electric shock on contact with a blue wire. However, caution should be taken as the wire can run at very high heat.
The brown wire has the function of carrying electricity to the appliance. If the brown wire is live and not connected to the earth or neutral wires there will be a risk of electrocution. You must ensure that there is no power source connected with the live wire before working on the wiring.
The earth wire colour now features green and yellow stripes in accordance with the IEC regulations. It is vital for safety as it connects the metal casing of the electrical appliance with the ground. This means that the current of the live wire cannot be directly transmitted to the casing. Contact with the protective earth wiring should not result in an electric shock but exercising caution is always recommended.
It is also important to be aware of the difference between single-phase and three-phase wiring. The single-phase connection is formed of two wires, with the three-phase variety being formed of three or four wires. The single-phase connection allows for the relatively easy balancing of electrical loads via the network. Due to the increased power generation, the three-phase connection is better suited to connection within workplaces featuring a variety of electrical machines and equipment. You can identify either the single- or three-phase connection by counting the wires connected within the electrical service panel.
Cable Locating Devices
Cable locating devices are specialised tools used to detect the presence of an underground electric cable, underground pipe or utility. These pipe locator units are used to prevent injury or the damage caused by striking an underground cable while excavating.
A cable locator consists of two parts: a transmitter and a receiver. The transmitter sends out a signal into the soil. As the signal travels through the soil, it encounters an electrical current flowing along the path of the buried cable. The current creates an alternating magnetic field around the cable. The receiver detects the presence of the magnetic field created by the cable and displays the distance and direction of the cable. In some cases, you may use an electrical power quality analyser (PQA) to measure voltage, current, frequency, phase angle, harmonics, and waveforms to determine if there are any problems. Underground cable locators are able to locate any pipe or cable underground as long as there is current passing through the target.
Anyone who uses a cable locator should have received thorough training in its use and limitations.
Excavation and Underground Services
If you are digging or disturbing the earth you should take care to avoid damaging underground services. Underground electrical cables can be particularly hazardous because they often look like pipes and it is impossible to tell if they are live just by looking at them. Damage to underground electrical cables can cause fatal or severe injury and the law says you must take precautions to avoid danger.
Excavation work should be properly managed to control risks, including:
- Planning the work
- Using cable plans
- Cable locating devices
- Safe digging practices
Detecting underground services will require information from those who own the services. Anyone planning or undertaking work that may disturb underground services must contact the owners/operators of those services for information about the location and status of the services. </p
Damage to underground services can cause fatal or severe injury as well as significant disruption and environmental damage; it can also delay the project and incur considerable costs. Injuries are usually caused by the explosive effects of arcing current, and by any associated fire or flames that may result when a live cable is penetrated by a sharp object such as the point of a tool.
Asbestos
According to the Health and Safety Executive (HSE) asbestos kills around 5,000 workers each year, which is more than the number of people killed on the road, and around 20 trades workers die each week as a result of past exposure.
Asbestos might be present in any building built or refurbished before the year 2000. When materials that contain asbestos are disturbed or damaged, fibres are released into the air. When these fibres are inhaled, they can cause serious diseases. These diseases will not affect you immediately as they often take a long time to develop, but once diagnosed, it is often too late to do anything.
Many cases of inadvertent, short-term exposure to asbestos will most likely have led to minimal exposure to fibres, with little likelihood of any long-term ill health effects. If you are concerned about possible exposure to asbestos from work activities, you are advised to consult your GP and ask for a note to be made in your personal record about possible exposure, including date(s), duration, type of asbestos and likely exposure levels, if known.
The Reporting of Injuries, Diseases and Dangerous Occurrences Regulations 2013 (RIDDOR) places duties on employers, the self-employed and people in control of work premises (the responsible person) to report certain serious workplace accidents, occupational diseases and specified dangerous occurrences (near misses). Exposure to asbestos is reportable under RIDDOR when a work activity causes the accidental release or escape of asbestos fibres into the air in a quantity sufficient to cause damage to the health of any person. Such situations are likely to arise when work is carried out without suitable controls, or where those controls fail.
Workers must be able to recognise asbestos-containing materials (ACMs) and know what to do if they come across them in order to protect themselves and others. Training for asbestos awareness is intended to give workers the information they need to avoid work that may disturb asbestos during any normal work which could disturb the fabric of a building, or other item which might contain asbestos. If a worker is planning to carry out work that will definitely disturb ACMs, further specific information, instruction and training will be needed. Asbestos awareness training is a requirement of regulation 10 of the Control of Asbestos Regulations (2012), and the supporting Approved Code of Practice L143 Managing and Working with Asbestos.
Fire Safety
Electricians should be aware that they work in high-risk situations, including the risk of fire. In fact, electrically ignited fires are some of the most common. Dated and/or untested appliances, overloaded plug sockets and faulty wiring can quite easily cause devastating fires.
The fire triangle is a concept detailing the three components of any fire; that is fuel, heat and oxygen. To extinguish a fire, you must break the fire triangle, by taking away just one of these three elements.
To break the fire triangle:
- Take away the heat element by cooling it down. Obviously, electricity and water don’t mix, hence why grabbing any old fire extinguisher could make the situation far worse, as it might be water or foam-based. The electricity surging to an extension lead, for example, will be giving off heat energy, so, by disconnecting the lead, you take away both the fuel and the source of heat.
- Remove oxygen with fire equipment is the next angle of attack. A fire blanket could be a good idea, provided the fire is small enough, in order to starve the flames of oxygen. However, in the case of an electrical fire, you should use a CO2 fire extinguisher. The physical structure of a CO2 molecule means that it has no free electrons. Consequently, it can’t conduct electricity. Objects covered with this CO2 flame retardant can’t be used by the fire as a fuel source. If the flames are then properly extinguished, try again to remove the source of electricity, for security.
Fires can develop quickly. A potentially devastating blaze can form in 30 seconds, so if you can’t fight the electrical fire safely and/or successfully, as with any other fire, you must evacuate the building and call the emergency services. Follow fire exit signs calmly, use evacuation chairs to help people with disabilities and meet at a pre-designated fire assembly point.
The Dangerous Substances and Explosive Atmospheres Regulations 2002 (DSEAR) states the legal requirements for managing the risk of fire, explosion or similar events arising from dangerous substances at the workplace.
What Training Should Electricians Take
When electricians are trained to work safely, they should be able to anticipate and avoid injury from job-related hazards. Safety training is essential for all electricians appropriate to their role, and training should be directly applicable to the responsibilities and daily practices of the person being trained.
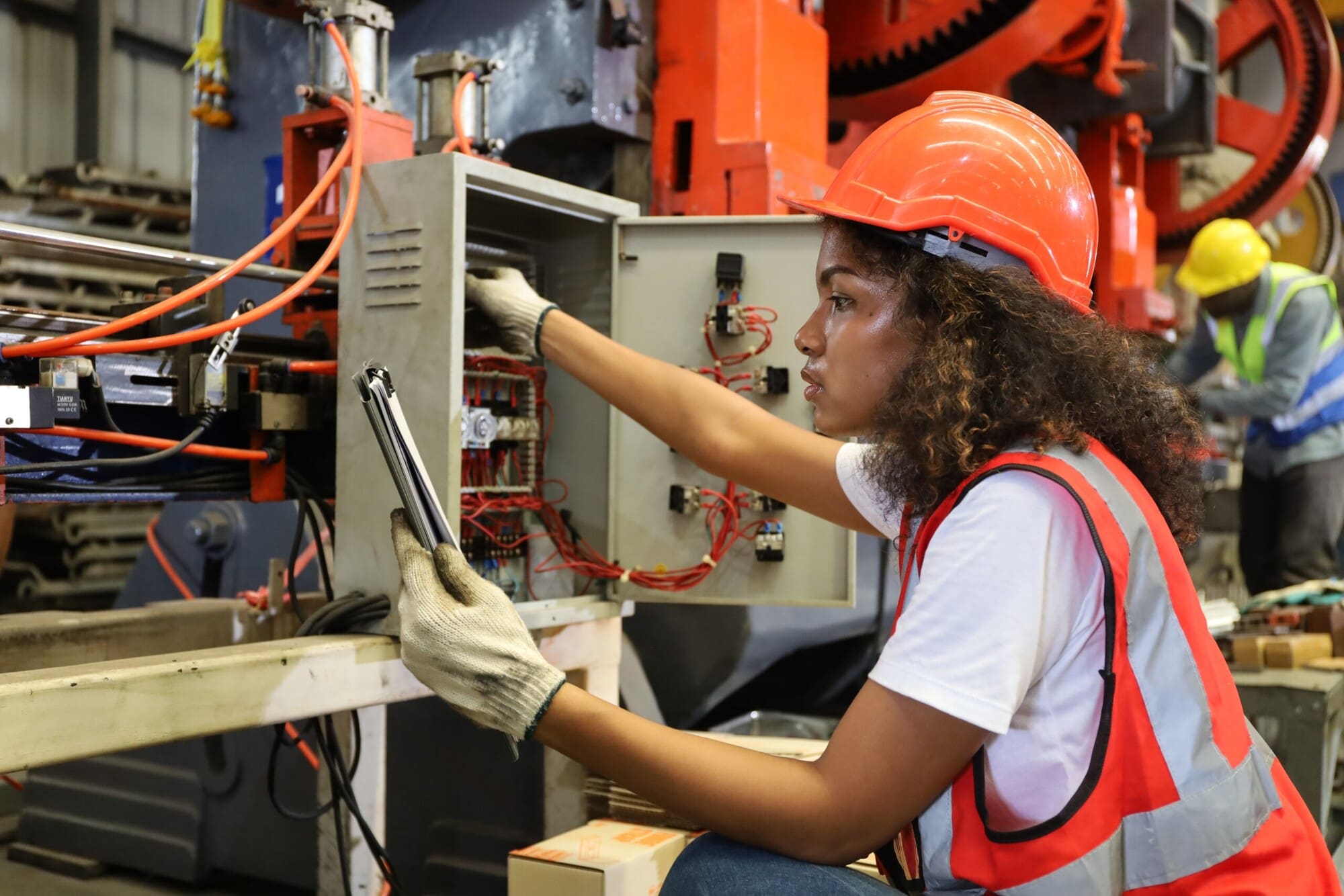
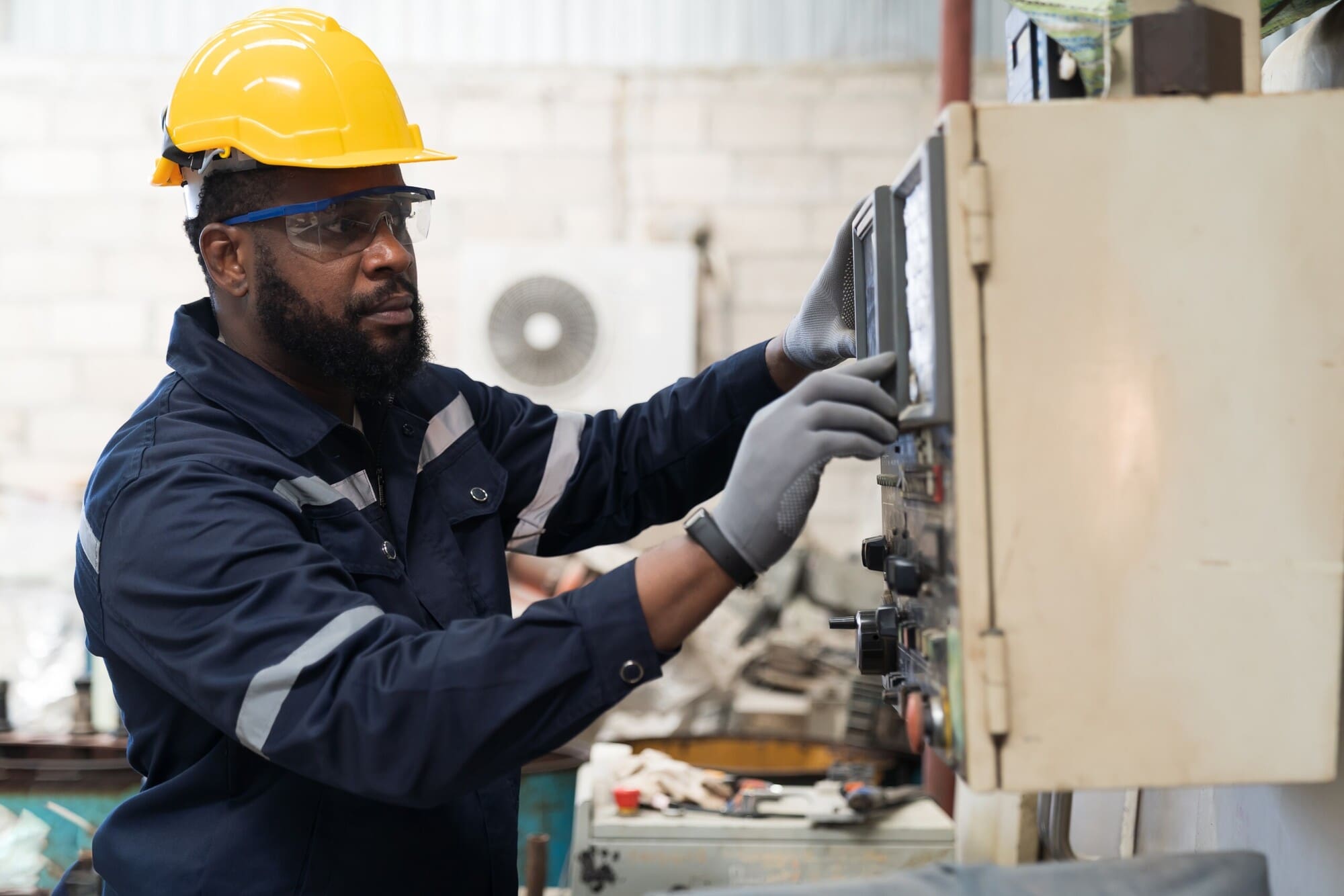
Training Courses
The training for electricians might include, but is not limited to:
- Health and Safety for Employees
- Health and Safety for Managers
- Electrical Safety Awareness
- PAT Testing Awareness
- Fire Safety Awareness
- Asbestos Awareness
- Working at height
- Ladder safety
- Assessing Risk
- Confined Spaces
- DSEAR Awareness
Electricians should at a minimum refresh their safety training at least every 2 years and participate in continuing professional development (CPD).