In this Care Certificate Guide Standard 13
After reading this Care Certificate Standard 13 – Health and Safety, you should be able to:
- Have an understanding of how health and safety applies in care roles
- Understand what your responsibilities are
- Understand workplace stress and how to tackle it.
The Care Certificate Standards detail what you must achieve and be assessed against to meet these learning outcomes.
If you have any concerns or queries, you should discuss these with your employer and/or assessor.
What do we Mean by Health and Safety?
Ultimately, it means keeping employees, visitors, patients and members of the public and others free from injury/harm and free from illness/disease. We all want to stay safe and healthy at the end of each working day and we all have a duty to prevent injury/ill health to one another.
Why do we Need Health and Safety?
All individuals and companies should prioritise other people’s health, safety and wellbeing from a moral perspective. People should be able to go to work without being injured, suffer ill health or worse; society also expects this. Unfortunately, some individuals and companies do not see a need for health and safety or they believe it to be costly. This usually results in poor health and safety management, which is the main cause of accidents, incidents, damage and ill health.
Accidents and ill health cost businesses, individuals and society as a whole, and millions of working days are lost as a result. These costs can outweigh the costs of good health and safety management. However, as the costs of accidents/ill health can be difficult to calculate, the emphasis tends to be put on how much good health and safety management costs. This is morally wrong and also inaccurate.
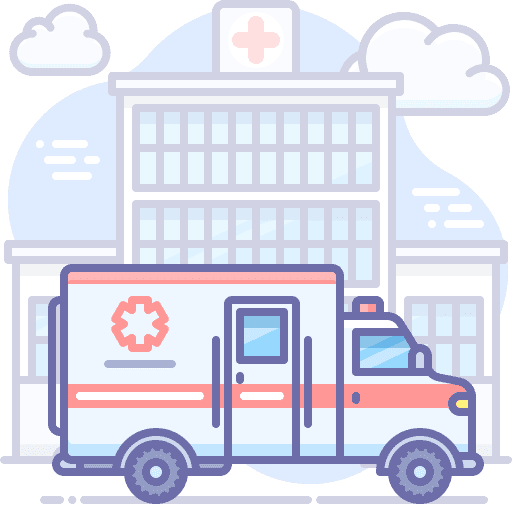
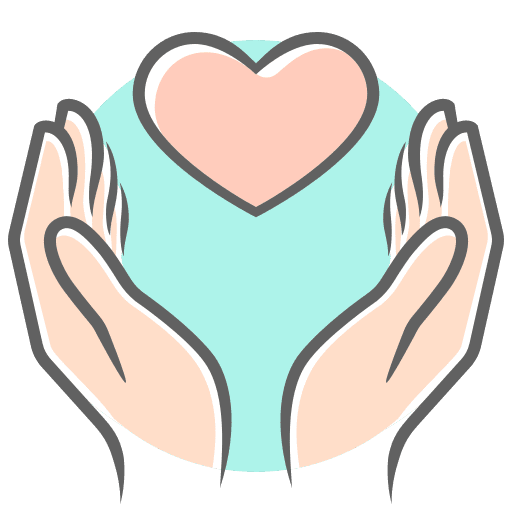
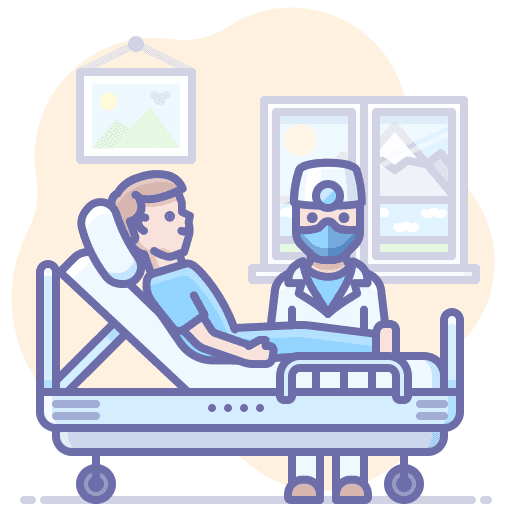
Why is Health and Safety Needed?
There are strong reasons for good health and safety management:
- Reduces injuries and ill health.
- Good staff retention.
- Increased productivity and high morale amongst employees.
- Lower insurance costs.
- Good reputation/image which could increase business/customers and therefore turnover.
There are consequences of no/poor health and safety management:
- Increased accidents, incidents and near misses. This can result in injuries and damage to buildings/equipment.
- Reduced productivity.
- Increased sickness absence.
- High staff turnover and low morale amongst employees.
- Fines, prosecutions, civil claims (compensation claims).
- Tarnished reputation and loss of business.
- High insurance premiums. Insurance companies can also refuse insurance cover if a business/individual is deemed too high risk.
Health and safety is a legal requirement.
Health and Safety Statistics
According to the HSE
- 65,427 non-fatal injuries to employees reported by employers in 2019/2020.
- 38.8 million working days lost due to non-fatal workplace injuries and ill health
- 0.5 million work-related musculoskeletal disorders

Key Definitions You Need to Know
- Hazard – Hazards are anything in the workplace that have the potential to cause harm.
- Legislation – A set of laws that have been passed by Parliament.
- Policy – A system of principles adopted by an organisation.
- Procedure – An established way of doing something.
- Risk – The likelihood of the hazard causing harm.
- Risk Assessment – Used to identify hazards and risks .
- Stressors – Something that can cause the state of tension or stress.
NHS England 6Cs
To ensure you are keeping individuals in your care as safe as possible, you should follow the 6Cs.
- Care
- Compassion
- Competence
- Communication
- Courage
- Commitment.
Relevant Legislation
The Health and Safety at Work etc. Act 1974 (HSWA) is the primary occupational health and safety legislation in Great Britain and, as previously mentioned, it is one of the most important pieces of health and safety legislation.
In Northern Ireland, the primary occupational health and safety legislation is the Health and Safety at Work (Northern Ireland) Order 1978 where similar provisions are made. As there are similarities, for the purposes of this unit, you will focus on the HSWA.
The HSWA applies to all industries and workplaces in Great Britain and can also include offshore installations such as oil rigs.
The HSWA is an enabling Act which means that other health and safety regulations, also known as Statutory Instruments or delegated legislation, can be made under the Act – think of it as umbrella legislation (HSWA is the umbrella and the health and safety regulations are underneath it).
Reporting of Injuries, Diseases and Dangerous Occurrences Regulation 2013
If hazards are not properly controlled, there is the potential for injuries, diseases and near misses (dangerous occurrences). If these are of a certain type, then there is a duty to report them to enforcement agencies under the Reporting of Injuries, Diseases and Dangerous Occurrence Regulations (RIDDOR) 2013.
Records must be kept for:
- RIDDOR reportable injuries/diseases/incidents.
- Injuries that result in over three-day absences.
The Management of Health and Safety at Work Regulations 1999
The Management of Health and Safety at Work Regulations (MHSWR) 1999 places a duty on employers, employees and others. The general requirements are on providing suitable and sufficient risk assessments and implementing appropriate risk controls.
Employers should also have access to competent health and safety assistance, have procedures for imminent danger and should provide training for employees. This regulation also covers young persons and pregnant workers.
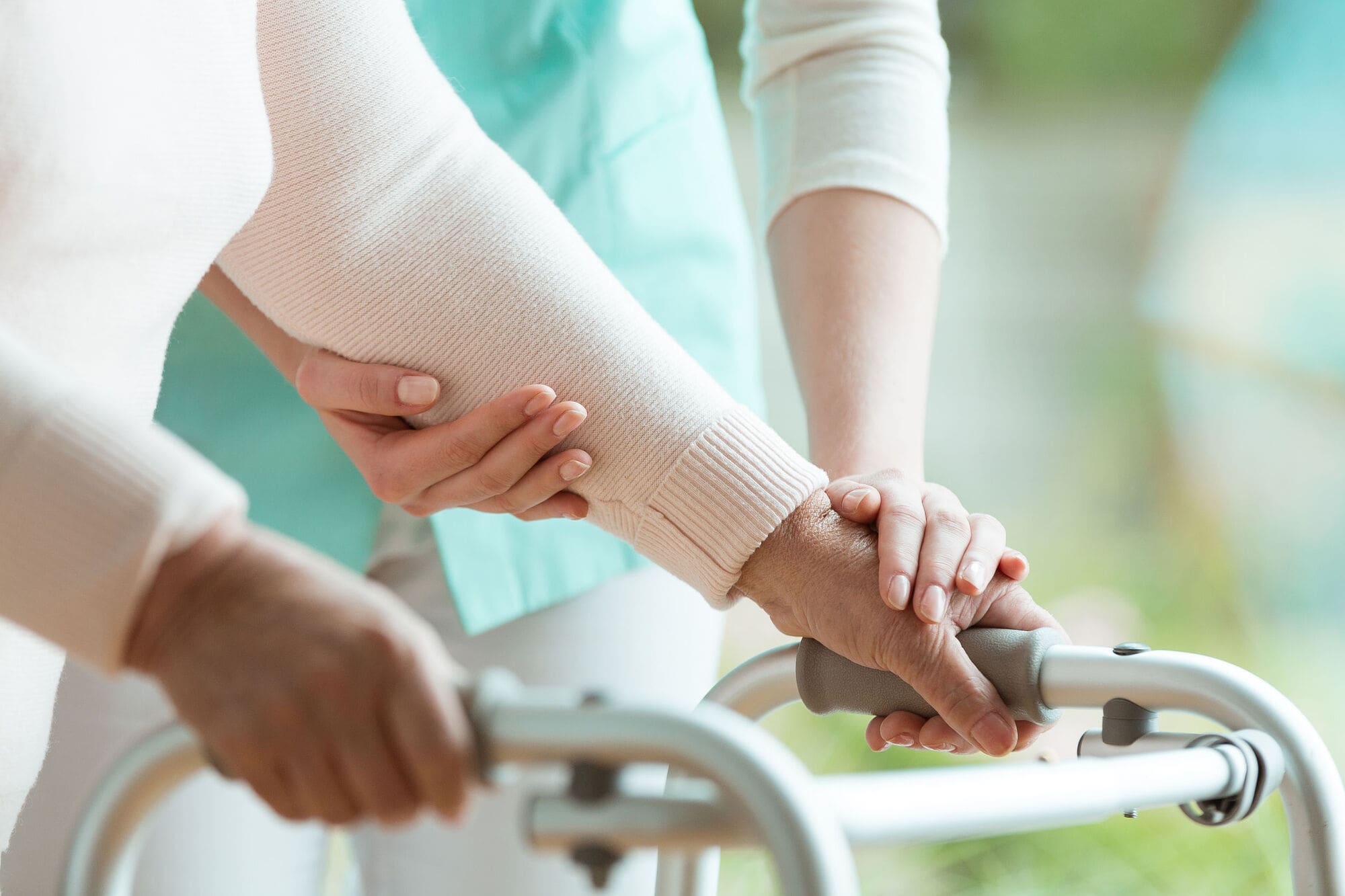
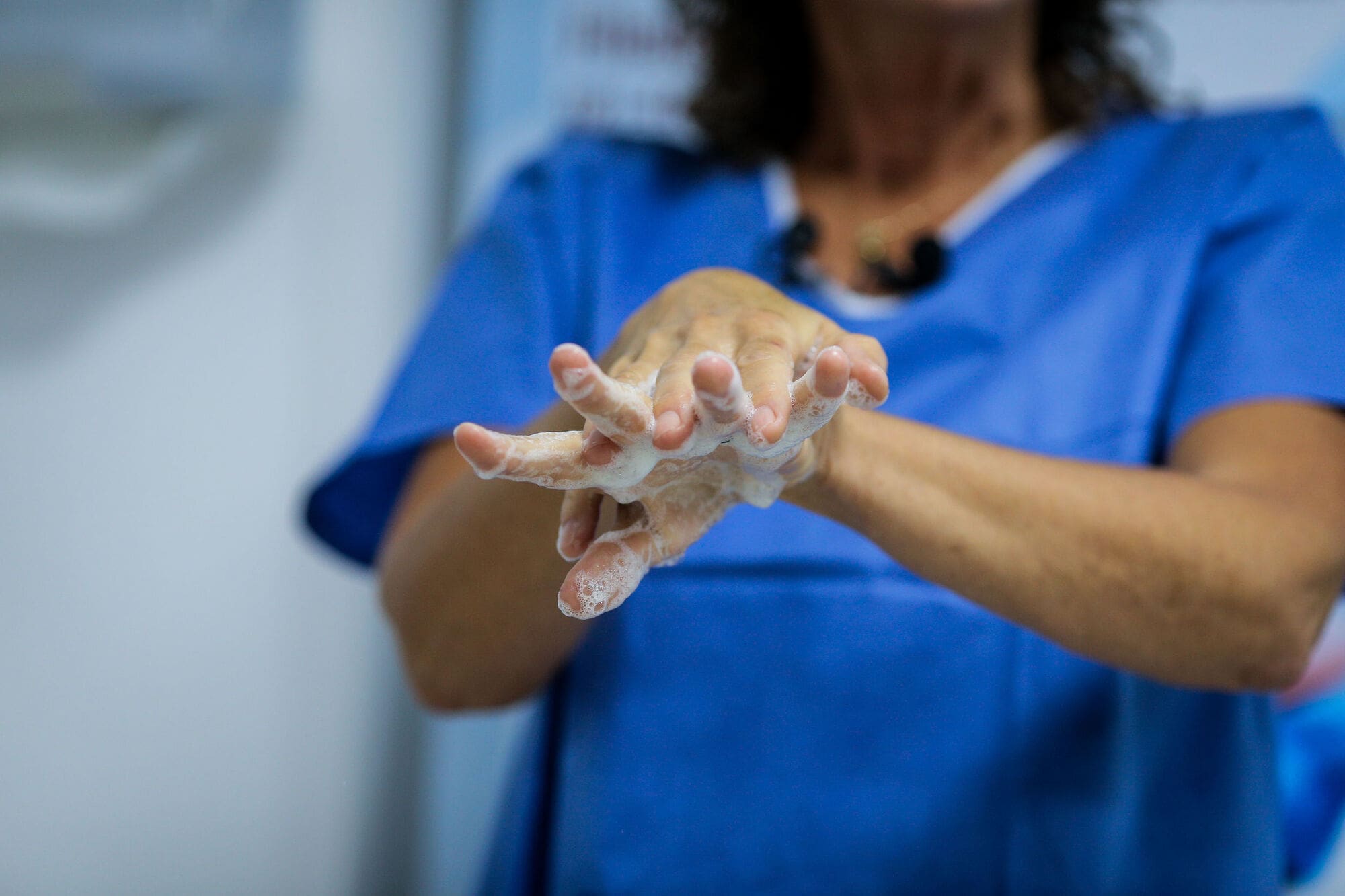
The Regulatory Reform (Fire Safety) Order 2005
The Fire Safety Order (2005) was designed to outline the responsibilities of different people with relation to fire safety. The FSO replaced over 70 different laws in England and Wales to bring together the legalities of fire safety.
With the introduction of the FSO, the responsibility of inspecting buildings went to the building owner, occupier or employer. This responsibility used to be with the fire service. This means that each business must have a ‘responsible person’ who is tasked with fire safety.
Control of Substances Hazardous to Health Regulations (COSHH) 2002
The COSHH Regulations were last consolidated in 2002 and were last amended in 2004. They are known as the COSHH Regulations 2002 (as amended).
The regulations apply in Great Britain (England, Wales and Scotland). In Northern Ireland, the regulations are the Control of Substances Hazardous to Health Regulations (Northern Ireland) 2003. The principles are the same as the Great Britain Regulations, so for the purposes of this unit you will focus on the COSHH Regulations 2002.
The aim of the regulations is to protect the health of workers, and others, who could come into contact with hazardous substances in the workplace. The regulations place duties, not just on employers, but also on the self-employed and employees. You will look at these duties later in the unit.
The Manual Handling Operations Regulation 1992
Manual handling should be avoided. Where it can’t be avoided, employees should know the weight of the load.
It should be controlled and the risk reduced i.e. using mechanical aids such as trolleys.
The Provision and Use of Work Equipment Regulations 2002
Work equipment must be suitable and well maintained. The risks of the equipment should be known and dangerous parts guarded, users should be trained in the maintenance/use of equipment provided.
The Protective Equipment (PPE) Regulations 1992
PPE must be provided if there is a risk of injury/ill health, and there is no other way of controlling the risks.
It should be of a suitable standard, clean, provided with instruction, employees trained on its use/cleaning/inspection and should be replaced when faulty/damaged.
The Lifting Operations and Lifting Equipment Regulations 1998 (LOLER)
LOLER applies to all workplaces in Great Britain where HSWA applies. It applies to all lifting equipment used for work purposes.
Employer and Employee Responsibilities
Employer Responsibilities
- To provide a safe place to work.
- Ensure staff have the correct training.
- To ensure legislation and policies are followed.
- Ensure risk assessments are completed and up-to date.
Employee Responsibilities
- Do not carry out any tasks that will put yourself or others at risk.
- Follow policies and procedures that are set out.
- Ensure you act in the correct way, which will not cause an accident
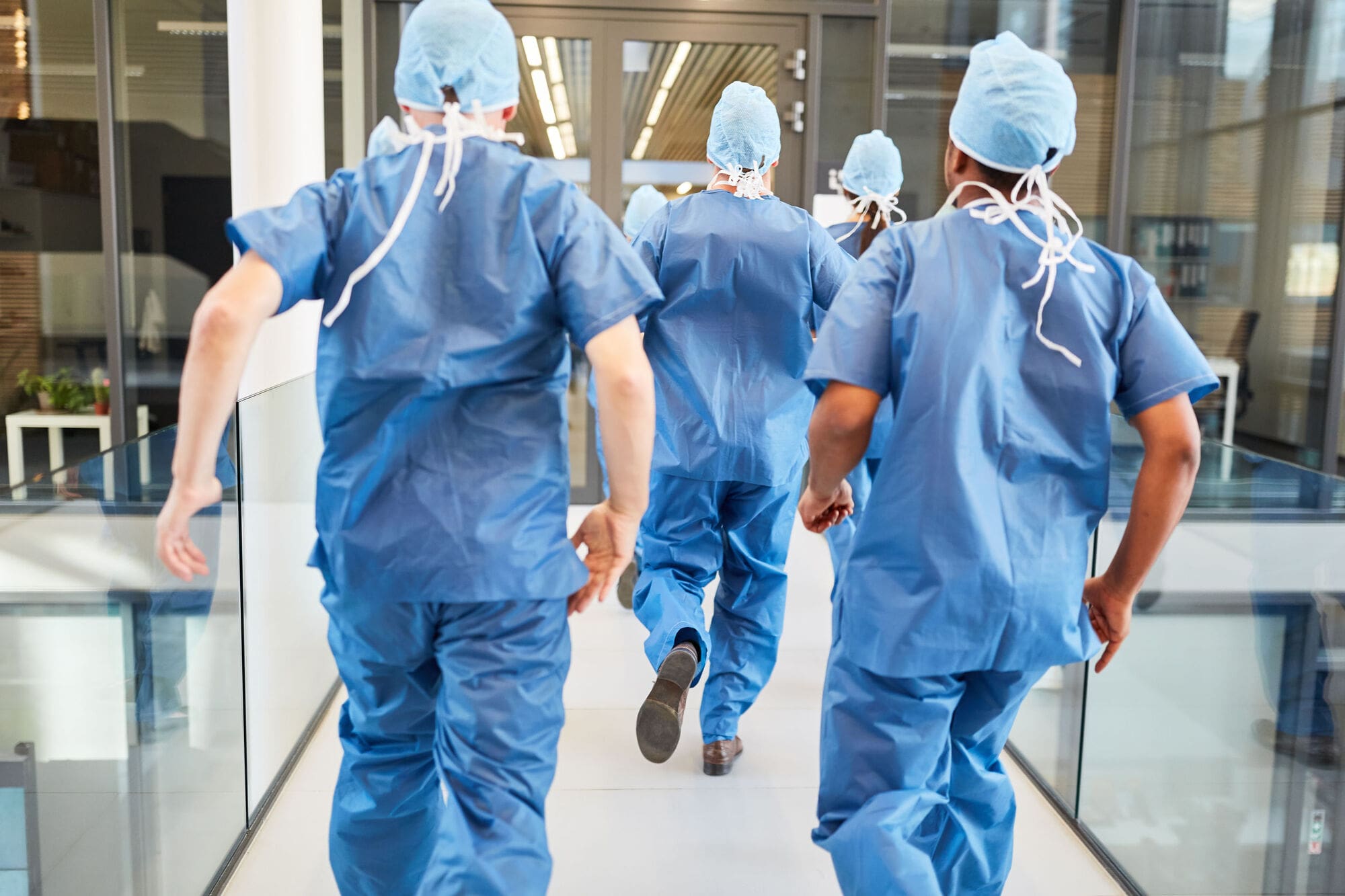
What are Risks and Hazards?
- Hazard – Hazards are anything in the workplace that have the potential to cause harm.
- Risk – The likelihood of the hazard causing harm. (Likelihood x Consequence).
What is a Risk Assessment?
Every day of your life, you are assessing risk; whether you are aware of it or not. When you come to cross a busy road, you make a decision on whether it is safe to cross. You inadvertently know when it is safe to cross and when it isn’t.
You know the consequences of crossing when it isn’t safe and you make decisions based on what you see at the time. You know that if you try to cross a busy road without a crossing, there is a likelihood of being hit by a vehicle.
There are, of course, those who would take a chance by running across a busy road, and you have probably seen some near misses, or even accidents, previously. However, for most people they know what is safe and what isn’t – they are conducting a risk assessment before crossing the road.
A risk assessment in the workplace is very much like the risks we assess in everyday life. However, in the workplace, risk assessments are a legal requirement under the Management of Health and Safety at Work Regulations 1999 (regulation 3).
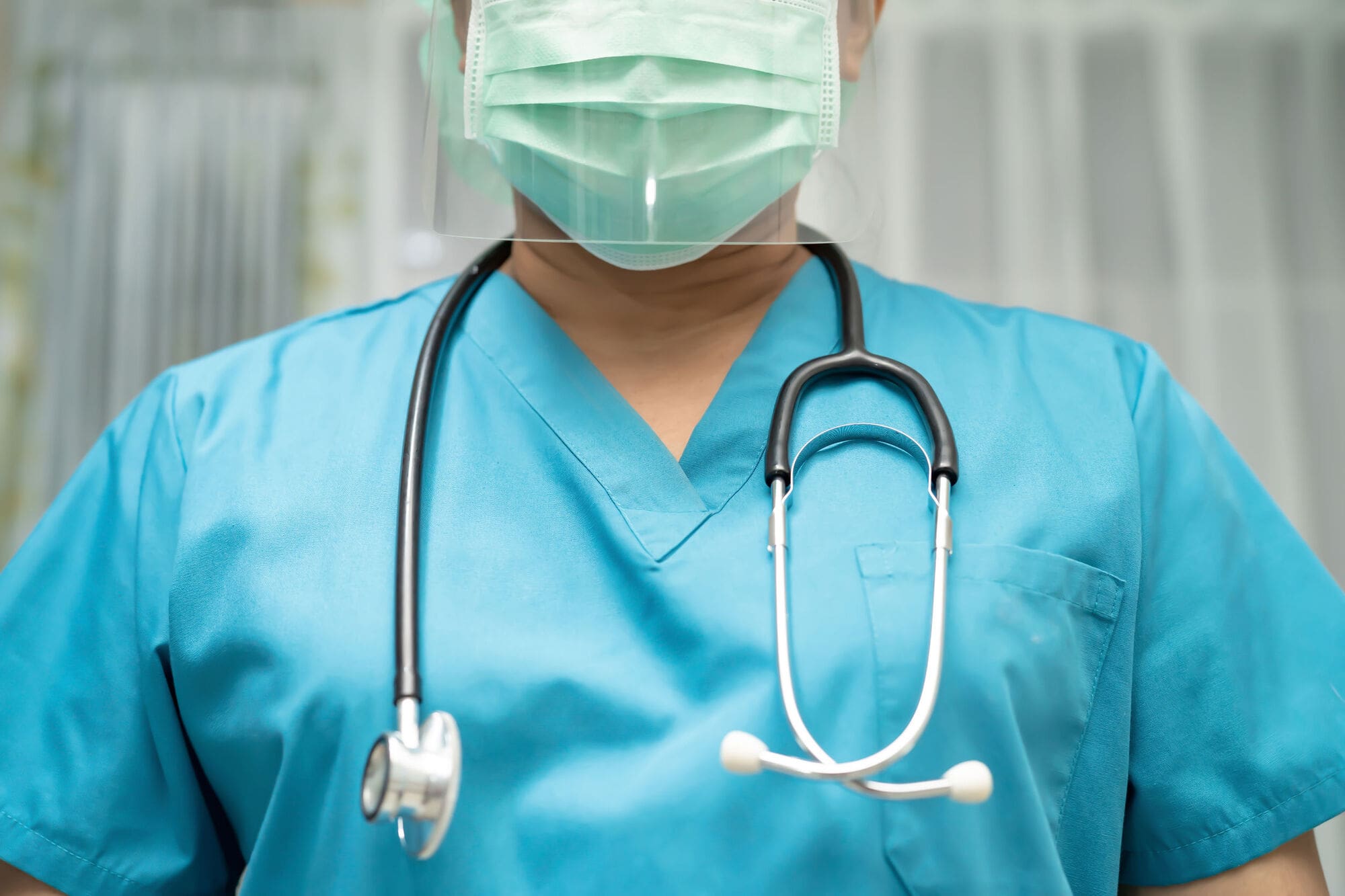
Risk Assessment Requirements
Overall, it is business owners and senior management who have the overriding responsibility for the risks associated with work activities and the workplace (if owned). It is part of their risk management, and their duty cannot be passed to another.
The regulations also state that risk assessments shall be suitable and sufficient. Suitable and sufficient means:
- Workers are involved in the risk assessment. This is very important as people who do the work should be aware of the hazards involved. They are also more likely to take ownership of the assessment if they are involved in its creation
- The activity being assessed was properly checked
- The assessment takes into account all those whose health and safety could be affected by the risk(s). This is not just looking at employees, but other people who could be affected. You will look at this later on in the unit
- The risk assessment identifies foreseeable, significant hazards and looks at the number of people who could be affected
Foreseeable – is a hazard/risk that should be anticipated when carrying out a certain activity/action
Significant – likely risks that could result in serious consequences (death/disability/serious injury/ill health). You wouldn’t expect paper cuts to be assessed in detail whilst leaving out hazards that could result in, for example, a fracture or a serious burn - The precautions (controls) put in place are enough to lower the risk to an acceptable level
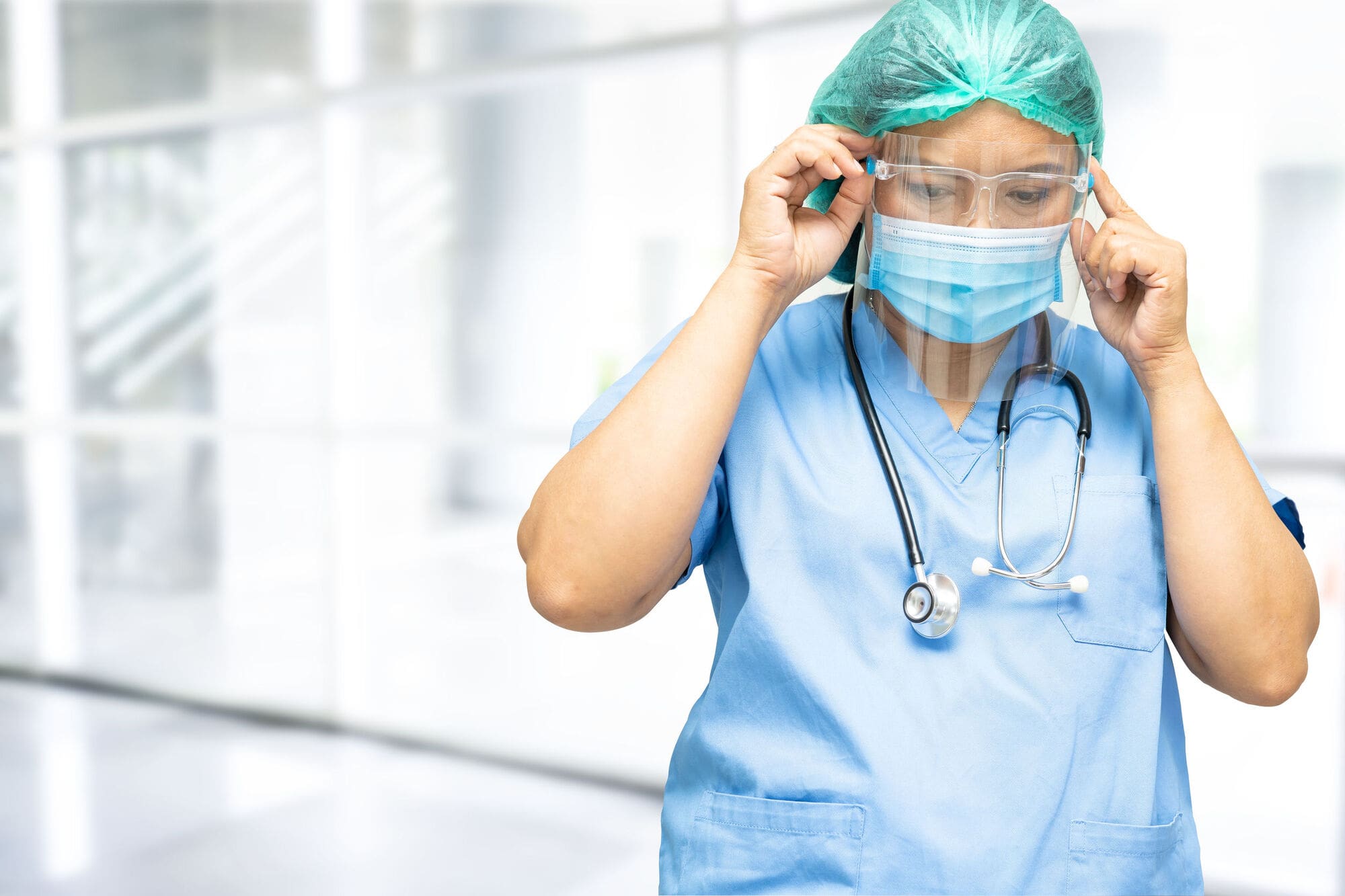
Steps to Risk Assessment
A risk assessment is an examination of workplace hazards that could cause injury or ill health to employees and others. It doesn’t need to be complicated, but it does need to be proportionate to the risks and have adequate precautions, as to avoid injury and ill health.
A risk assessment should be carried out before a work activity starts or before starting in a new work location.
A risk assessment is completed in five steps (although you may come across other methods).
The five steps are:
- Reviewing and updating the risk assessment where necessary.
- Identification of hazards.
- Deciding who could be harmed by the hazard and how.
- Evaluating the risks identified and deciding what precautions are necessary.
- Recording the findings of the risk assessment.

Essential Workplace Practices
Administering Medication
Correct procedures for storing medication
A key part of making sure that medication remains safe for use is consideration for how it is stored. Each healthcare setting should have strict policies that are written in line with legislation, showing how medication should be stored safely so that it remains fit for purpose and so that it is not accessible by people who may not use it for its intended purpose.
Care workers should be familiar with all policies that relate to how medication is stored so that they know how to do this correctly. Consideration should also be given to those individuals who are able to take their own medication within a setting and how easy it is for them to access the medication that they need.
Needles and Sharps
Where the use of sharps cannot be avoided, the regulations maintain that employers are to provide alternatives to traditional unprotected medical sharps with ‘safer’ sharps, wherever this is possible.
Safer equipment is designed specifically to minimise or prevent the risk of accidental injury, which is widely associated with the use of traditional medical sharps. Safer equipment examples include syringes and needles, which are fitted with a shield that covers the needle automatically once it has been used.
Health and Safety Executive guidance when using safer sharps recommends that healthcare providers consider the following factors before going ahead with their use:
- The use of a safer sharp should not compromise effective care of individuals.
- The safer sharp should be reliable.
- The healthcare provider should have complete control over the procedure.
- The possibility that using the safer sharp may mean that other safety hazards become apparent or that other sources of blood exposure might be presented.
- How easy the safer sharp is to use.
- How suitable the safety mechanism is.
The Health and Safety Executive also reminds employers that safe sharps do not eliminate all risks and that injuries can still occur.
As with any practice that has the potential for a higher level of risk to employees, only those who have been properly trained in the use of a sharp device may carry out procedures which involve them.
Training will be both corporate and departmental and includes instructions on the correct assembly of sharps bins and on all aspects of how to manage an incident where there has been exposure to a sharp that has resulted in injury or illness.
Employees must be aware of their responsibilities in terms of reporting any incidents that occur and to try and ensure within reasonable measures that they avoid incidents from happening in the first place, which includes the safe disposal of any sharp that has been used for a procedure.
Any employee who has not received the relevant training to carry out a procedure that involves the use of a sharp should not be asked to use or dispose of one, nor should they take it upon themselves to do so, as they put themselves and others at risk.
Moving and Handling
The responsibilities of the employee with regard to moving and handling
The responsibilities of employees are equally important to those of the employer as employees are those people who are more likely to be working on a one-to-one basis with individuals when moving and handling procedures take place.
The main focus of their responsibilities concerns:
- Taking reasonable care for their own health and safety and those who may be affected by how they carry out their role.
- To cooperate with their employer and with other employees to make sure that legislation is correctly and lawfully adhered to.
- Not intentionally or recklessly interfering with or misusing anything that is provided to them in the interests of health and safety.
- Ensuring that they remain competent in their role such as keeping up to date with appropriate training when using specific pieces of equipment.
Hand Washing
Effective handwashing
The use of basic hygiene procedures is one of the most robust ways of helping to lessen the possible spread of infection. However, this will only be possible if staff are aware of what their responsibilities are in terms of personal hygiene and handwashing procedures.
All organisations should have a policy in place about hygiene procedures and how these are best followed. It should be easily accessible to all staff who can refer to it if they have any doubts about what their own responsibilities are in lessening the risk of infection spreading within their setting.
The NHS has a standard practice for the best way to wash hands to ensure that they no longer potentially contain harmful bacteria and this should be done both before and after sharps have been used with individuals.
You should wash your hands for the amount of time it takes to sing ‘Happy Birthday’ twice (around 20 seconds)
- Wet your hands with water
- Apply enough soap to cover all over your hands. You can use alcohol-based handrub if you don’t have immediate access to soap and water
- Rub hands palm to palm
- Rub the back of your left hand with your right palm with interlaced fingers. Repeat with other hand
- Rub palms together with fingers interlaced
- Rub the backs of your fingers against your palms with fingers interlocked
- Clasp your left thumb with your right hand and rub in rotation. Repeat with your left hand and right thumb
- Rub the tips of your fingers in the other palm in a circular motion, going backward and forwards. Repeat with the other hand
- Rinse hands with water
- Dry thoroughly, ideally with a disposable towel
- Use the disposable towel to turn off the tap.
Aprons and Gowns
Disposable aprons and gowns are designed to protect uniform from being soiled whilst carrying out activities within the healthcare setting. In most cases, plastic aprons will be used for standard procedures. However, where there is increased risk of infection transmission or in places where there may be heavy soiling, a long-sleeved, fluid repellent gown will be more appropriate.
Aprons and gowns should not be worn routinely and only worn when activities are taking place. They must be changed after working with each individual or they may need to be changed between procedures with the same individual.
Care should be taken when putting them on and taking them off and the outer surface should not come into contact with the employee’s uniform before they are disposed of. They should be discarded immediately after use and the employee should apply thorough hand hygiene before undertaking any further tasks.
In some settings, aprons may be colour coded, for example some are used when performing surgical tasks and some when serving food. It is the responsibility of the employer to train the employee to know which apron they should use for the task they are carrying out.
Dealing with Spillages
Spills of body waste may occur, for example, if an individual does not get a receptacle for vomit in time or if they enter an A&E department bleeding profusely from a wound. Employees are also responsible for dealing with the contents of bottles, bedpans and commodes, where there is a greater potential for spillages to occur. When a spill occurs, it should be dealt with immediately and appropriately with suitable cleaning materials by employees who are trained in their use.
Recommended methods of dealing with spillages
It is important that employees are wearing PPE when dealing with any type of body fluid spillage so as to reduce the risk of infection. This means wearing a minimum of an apron and gloves, which should be disposed of immediately after use.
After PPE has been put on, employees should clear the spillage as quickly as they can, ensuring that no one else comes into contact with it wherever this is possible, so making others aware of the spill by use of a sign or by simply telling them to avoid the area if they can.
The area that is in and around where the spillage has occurred should then be cleaned using specific cleaning materials and equipment, which the Health and Safety Executive makes clear recommendations about:
- Cleaning materials and equipment for removing spilled body fluids must be used for no other purpose; they must be specifically for body waste and nothing else
- A hypochlorite solution, which contains chlorine releasing disinfectant, is most suitable for this type of spillage
- Bags and bins for the waste which comes from the cleaning up of body waste must be clearly labelled and employees must know which one to use
- Employees must ensure that they dispose of their own PPE in the correct place and thoroughly wash and dry their hands after dealing with spillages – they should not come into contact with anyone else before washing their hands.
Fire Prevention
Protection is about reducing damage and saving lives when a fire occurs. This can be done using a lot of methods which we will explore in this section of the course. Protection measures can be split into active and passive.
Active control measures are a safety measures that requires action from a person or situation. This means that active protection measures are either used or react when a fire takes place. Examples include fire extinguishers and blankets which are used by people. Other examples include sprinkler systems and emergency lighting as these are triggered when a fire happen.
Passive control measure are physical features that do not require any action in protecting life. They are usually built into a building and are no different when a fire takes place to any other day. They include fire exits, signs leading to the nearest exits and any special fire safety equipment built into the location (such as fire resistant walls and doors).
Fire Protection
General tidiness
Making sure that areas are kept tidy is an essential part of preventing fires as well as reducing the risk of injuries if a fire does occur. General tidiness refers to keeping areas free from hazards that could burn or else be in the way when people are trying to use exits.
General tidiness involves:
- Keeping exit routes clear – you should never leave boxes or any other materials blocking fire exits. These doors and windows could be needed at a moment’s notice and should be clear at all times.
- Storage – ensuring that things are not left lying around will reduce the chances of fires starting or additional fuel being burnt. Things like paper and cardboard are in every office and these items can easily ignite or help to spread flames. Ensuring that materials are safely stored will help to stop this issue.
- Waste management – rubbish should be removed from the premises regularly. This will ensure that any flammable materials are far from the building and cannot be in the way should a fire start.
Smoking
One common way for fires to start is through people smoking. Despite the UK bans on smoking in the workplace, many people do still smoke and they should understand where they can and cannot smoke cigarettes.
Despite the law, some people still break the rules around smoking at work so it is important that a designated smoking area is provided that is a safe distance from the building.
Work-related Stress
Stress and mental ill health
Stress and mental ill health are commonly linked because when someone feels overwhelmed with stress, their ability to carry out day-to-day functions is compromised.
These can include functions such as:
- Cognition (thinking) – the ability to think about information and make decisions in a sound manner.
- Perception – the ability to accurately understand events that are going on around you.
- Emotions and mood – the ability to express how you are feeling in an appropriate fashion, including the way in which you respond to the feelings of others.
Stress can affect an individual in two ways, dependent upon how long the thing(s) that is causing the stress continues.
The two types of stress are:
- Acute – which is a one-off stressful event
- Chronic – one or more stressful events that are ongoing.
Dealing with Experiences
Someone who cannot deal effectively with life experiences and events is likely to deal with the same situation very differently.
They are more likely to have a longer period of recovery from any injuries because their mental state is unlikely to be positive. Additionally, they may encounter some kind of post-traumatic stress and relive the accident persistently, causing them further mental trauma each time this happens.
Finally, they may not be able to speak about what has happened to them and so they keep their emotions inside; this can lead to severe emotional outbursts, which can add to existing problems.
Employers and Work-life Balances
The Mental Health Foundation notes that employers should have measures in place to ensure that their employees remain mentally well.
In terms of work-life balance, this may include:
- Promoting the message about a good work-life balance within the workplace.
- Developing effective policies about the link between stress and poor mental health.
- Encouraging a culture of openness about well-being.
- Giving appropriate training to managers who may be able to identify signs of stress amongst employees.
- Ensuring that employees do not work beyond their contracted hours.
- Enabling employees to attend appointments relating to their health and well-being.